Cuando exploré por primera vez el mundo del moldeo por inyección, me sorprendió mucho cómo este método convierte las materias primas en piezas complejas. Parece un truco de magia que necesita talento y precisión.
Los elementos esenciales del moldeo por inyección incluyen la preparación de las materias primas, el proceso de inyección en sí y el posprocesamiento. Estos pasos garantizan la calidad y precisión de las piezas moldeadas mediante el control de la temperatura, la presión y el tiempo.
Ya has visto un vistazo de estos importantes pasos. Ahora, explora cada uno más de cerca. Descubra cómo cada sección del método conecta con detalles técnicos que garantizan que el resultado final sea perfecto.
La preparación afecta la calidad del moldeo por inyección.Verdadero
Una planificación minuciosa produce artículos impecables al manipular los materiales con cuidado y ajustar las herramientas correctamente.
¿Cómo afecta la preparación antes del moldeo a la calidad?
Prepararse antes de darle forma es importante para lograr productos impecables y de alta calidad en el moldeo por inyección. Sienta las bases para un proceso de producción fluido y eficiente.
La preparación antes del moldeo afecta la calidad al garantizar que las materias primas se traten adecuadamente y el equipo esté configurado correctamente. Esto incluye secar plásticos hasta niveles de humedad específicos, precalentar inserciones, limpiar maquinaria y seleccionar agentes desmoldantes adecuados.
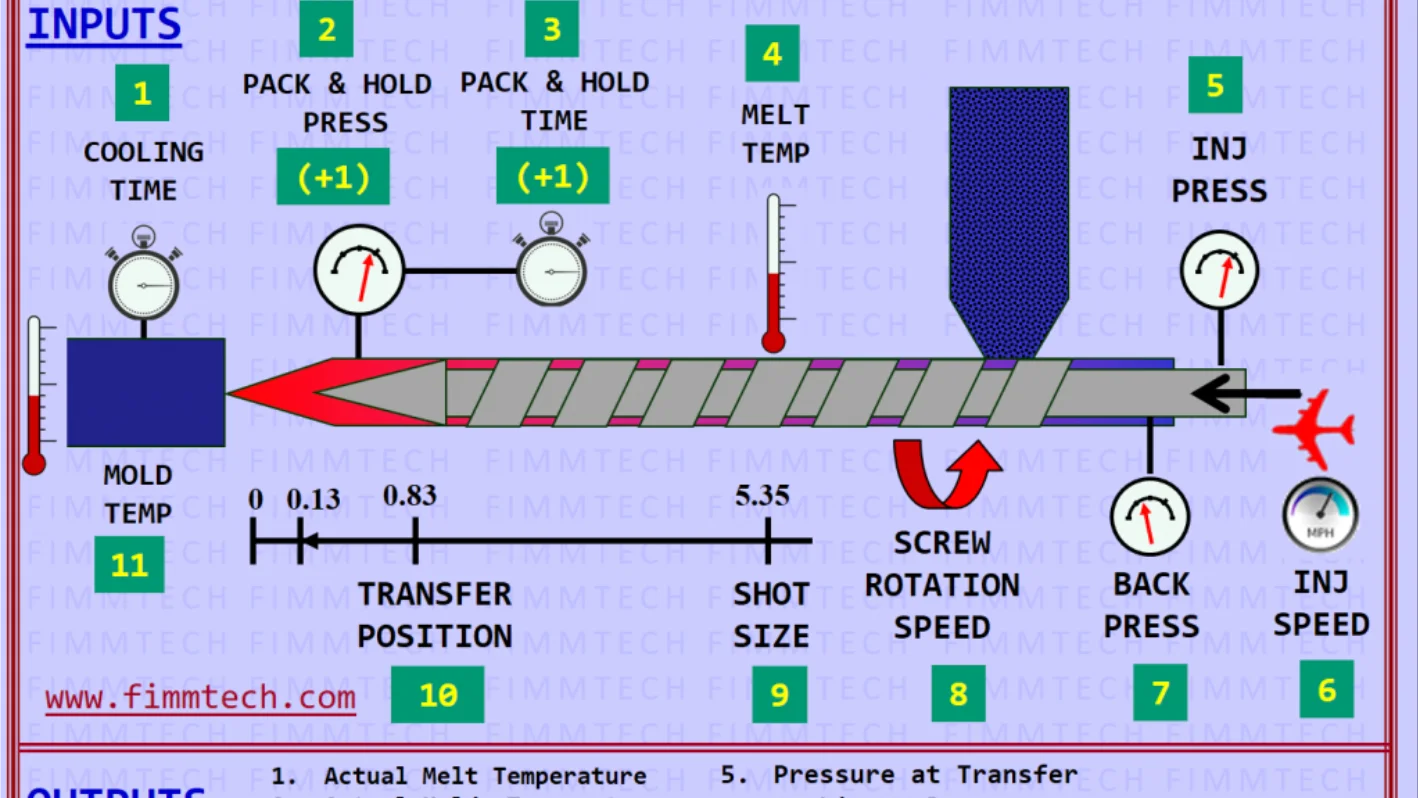
Preparación de Materia Prima
Una buena preparación comienza con los materiales. El tratamiento de estos materiales es crucial para reducir los problemas en el producto final. Los plásticos como el ABS o el policarbonato requieren niveles de humedad específicos antes de darles forma. El uso de un horno de secado al vacío 1 ayuda a secar estos plásticos según los estándares necesarios, como por ejemplo por debajo del 0,2% para el policarbonato, para evitar problemas de humedad. Agregar color puede implicar ciertos agentes o aditivos de color.
Insertos de precalentamiento
Incluyendo piezas metálicas necesita precalentamiento. Esto reduce la tensión en el interior debido a la diferente contracción entre el metal y el plástico. Recoger metales con alta expansión térmica y calentarlos ayuda a reducir la tensión y a lograr una conexión uniforme con el plástico circundante.
Preparación del equipo
Limpiar la cámara de la máquina de inyección es un paso importante que no debe omitir. Las máquinas nuevas o aquellas que cambian de materiales o productos necesitan una limpieza a fondo. El uso de materiales reciclados o polietileno de baja densidad ayuda a la limpieza sin dañar las partes sensibles.
Selección de agentes de liberación
Elegir el agente desmoldante adecuado es muy importante. El estearato de zinc es adecuado para los plásticos en general, mientras que la parafina líquida funciona mejor con las poliamidas. Es importante aplicar la cantidad adecuada para mantener intactos el aspecto y el color del producto.
Tabla: Plásticos comunes y sus necesidades de tratamiento previo
Tipo de plástico | Necesidad de contenido de humedad | Método de secado adecuado |
---|---|---|
ABS | Por debajo del 0,2% | Horno de secado al vacío |
PA (nylon) | Por debajo del 0,1% | Circulación de aire caliente |
PC (Policarbonato) | Por debajo del 0,03%-0,05% | Horno de secado al vacío |
Estos pasos preparan el proceso de moldeo por inyección para un funcionamiento fluido y productos de calidad libres de los problemas habituales como huecos o deformaciones. Conocer estos pasos ayuda a los fabricantes a mantener su producción estable y precisa.
El precalentamiento de las inserciones metálicas reduce la tensión interna.Verdadero
El calentamiento iguala los niveles de contracción, lo que reduce la tensión en las piezas moldeadas.
El estearato de zinc es ideal para todo tipo de plástico.FALSO
Varios plásticos necesitan agentes desmoldeantes particulares para obtener mejores resultados.
¿Qué sucede durante el proceso de inyección?
El método de inyección es la parte principal del moldeo por inyección. Las materias primas se transforman en piezas finales. Conocer cada paso es importante para una buena producción.
Durante el proceso de inyección, el material plastificado se inyecta en la cavidad de un molde, pasando por fases como carga, plastificación, inyección, enfriamiento y desmolde. Cada fase requiere un control preciso de la temperatura, la presión y el tiempo para garantizar productos de alta calidad.
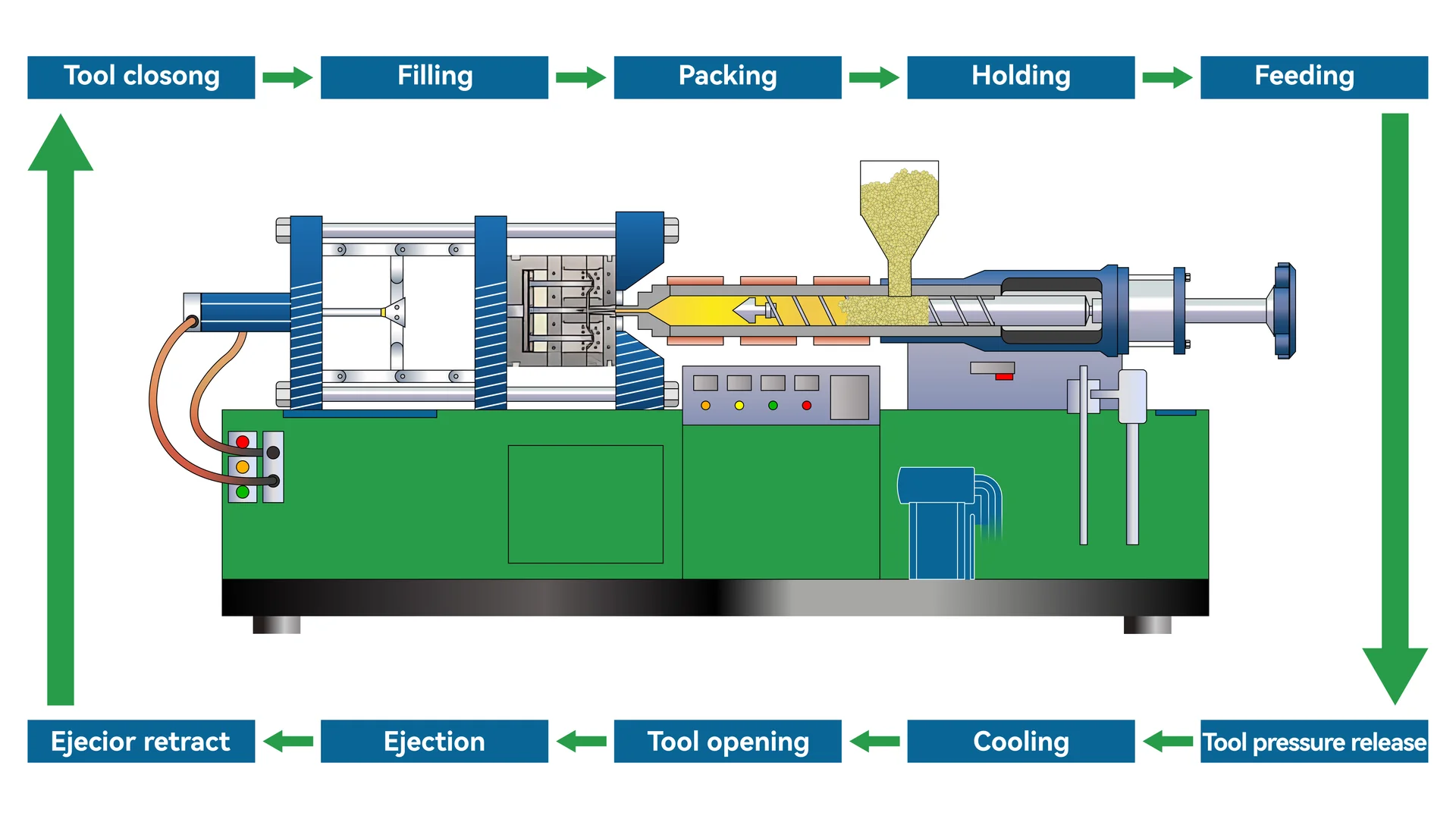
Carga: Balance de materiales
En esta fase, la máquina necesita una cantidad concreta de material para un buen funcionamiento. Usar demasiado o muy poco puede causar problemas como encogimiento o formas incompletas. Es importante seleccionar la cantidad correcta según los detalles del producto y la capacidad de la máquina.
Plastificación: creación de una masa fundida uniforme
La plastificación convierte piezas sólidas de polímero en una masa fundida suave mediante calor y mezcla. Este paso es importante para la uniformidad y la calidad del producto. Los ajustes como el calor del cilindro, la velocidad del tornillo y la contrapresión deben gestionarse cuidadosamente para mantener la masa fundida constante. Por ejemplo, algunos plásticos necesitan temperaturas superiores a cierto punto para fundirse correctamente.
Inyección: llenado del molde
Durante esta fase, el plástico fundido ingresa al molde a alta presión. Se divide en pasos como llenado de flujo, retención y reflujo. En el llenado por flujo, los materiales se mueven rápidamente hacia el molde, ajustándose a la velocidad y el espesor. Mantener la presión garantiza que el molde se llene por completo, lo que realmente ayuda con la resistencia y la densidad.
Enfriamiento: mantener la forma y el tamaño
Después del llenado, el molde se enfría con un medio especial, endureciendo el plástico y fijando su forma y características finales. El tiempo de enfriamiento cambia según el tamaño y el material. Un enfriamiento adecuado es clave para mantener la forma y evitar deformaciones.
Desmoldeo: extracción de piezas
Cuando se enfría lo suficiente, la pieza sale del molde utilizando una herramienta de empuje. Este paso debe realizarse con cuidado para evitar dañarse o pegarse. Los sistemas eyectores y los agentes de liberación bien fabricados realmente ayudan a una eliminación sin problemas.
Estos pasos muestran cómo cada parte del proceso de inyección 2 ayuda a la calidad y exactitud. Al gestionar eficazmente el calor, la fuerza y el tiempo, las fábricas probablemente produzcan piezas estables y fiables. Obtenga más información sobre las configuraciones de moldeo por inyección 3 para profundizar su conocimiento de este complicado proceso.
La fase de carga determina la cantidad de material.Verdadero
El paso de carga garantiza la cantidad correcta de material para una excelente fusión del plástico.
El enfriamiento afecta las dimensiones finales de la pieza.Verdadero
El enfriamiento endurece el plástico, decidiendo el tamaño y las características de la pieza.
¿Por qué el posprocesamiento es crucial para el moldeo por inyección?
El posprocesamiento en moldeo por inyección garantiza que el producto final alcance las normas de calidad y rendimiento. Elimina defectos y mejora las características del material.
El posprocesamiento es vital para el moldeo por inyección porque reduce las tensiones residuales, mejora la estabilidad dimensional y mejora el acabado superficial. Técnicas como el recocido y la hidratación son cruciales para lograr estos resultados.

El papel del recocido en la reducción del estrés residual
Durante el proceso de moldeo por inyección, los materiales a menudo enfrentan problemas de fusión, endurecimiento, conformación y enfriamiento desiguales dentro del molde. Además, las piezas metálicas o un procesamiento adicional inadecuado pueden introducir tensión dentro de las piezas moldeadas. Para abordar estos problemas, a menudo se utiliza el recocido posteriormente.
El recocido implica colocar las piezas moldeadas en un horno o líquido tibio durante un tiempo determinado. Esto permite que las piezas dentro del plástico se relajen, reduciendo las tensiones sobrantes. Por lo general, la temperatura del horno se establece entre 10 y 20 °C por encima de la temperatura a la que normalmente se utilizan las piezas de plástico o entre 10 y 20 °C por debajo de su temperatura de deformación por calor. Es necesario tener cuidado para evitar deformaciones evitando temperaturas excesivamente altas.
El tiempo necesario para el recocido varía según factores como el tipo de plástico, la temperatura del medio de calentamiento, la forma y el grosor de las piezas. Por ejemplo, piezas más gruesas o con requerimientos muy precisos pueden requerir tiempos más largos.
Hidratante para formas estables y fuerza.
La hidratación es importante más adelante, especialmente en materiales como la poliamida. Las piezas recién moldeadas se sumergen en agua caliente para mantenerlas alejadas de la exposición al aire. Esto previene la oxidación y les ayuda a absorber la humedad más rápido, manteniendo su estabilidad de forma y fortaleciéndolos.
Normalmente, este proceso ocurre a temperaturas entre 100°C y 120°C. Para plásticos que se doblan a temperaturas más altas, se prefiere el límite superior. El tiempo de hidratación depende del tipo de plástico, la forma de la pieza, el grosor de la pared y cómo se empaquetan las piezas en su interior.
Con un remojo rápido en agua, las piezas moldeadas se vuelven más duras y fuertes. Este tratamiento no sólo mantiene las piezas libres de aire sino que también mejora sus características de rendimiento.
Importancia de los pasos correctos de posprocesamiento
La forma en que se ejecutan los pasos de posprocesamiento afecta en gran medida la calidad final de los artículos moldeados por inyección. Un recocido deficiente puede dejar tensiones residuales que los debiliten con el tiempo. Del mismo modo, una hidratación insuficiente puede provocar cambios dimensionales y reducción de la resistencia.
Al implementar planes integrales de posprocesamiento de manera efectiva, los fabricantes pueden abordar bien estos problemas. Pasos como el recocido y la hidratación mejoran el rendimiento del producto y al mismo tiempo satisfacen las necesidades de diseño.
El posprocesamiento es clave para el éxito del moldeo por inyección. Al seguir los pasos correctos, los fabricantes aumentan la resistencia, la precisión y la calidad de los productos, lo que los hace útiles en industrias que van desde la automoción hasta la electrónica. Para obtener más información sobre los detalles del moldeo por inyección y explorar nuevas mejoras en los resultados a través de técnicas avanzadas de posprocesamiento 4 .
El recocido reduce las tensiones residuales en las piezas moldeadas.Verdadero
El recocido calma las macromoléculas y reduce la tensión sobrante.
La hidratación es innecesaria para las piezas de poliamida.FALSO
Agregar humedad equilibra el tamaño y fortalece la poliamida.
¿Cómo afectan la temperatura y la presión al moldeo por inyección?
La temperatura y la presión son aspectos importantes que afectan directamente la calidad y el éxito del moldeo por inyección. Conocer su impacto probablemente conduzca a mejores resultados del producto.
La temperatura y la presión en el moldeo por inyección afectan el flujo de material, la calidad del producto y la eficiencia. Un control adecuado garantiza una plastificación óptima, reduce los defectos e influye en las velocidades de enfriamiento.

Uso del papel de la temperatura en el moldeo por inyección
La temperatura es muy importante en el moldeo por inyección. Afecta a lo bien que se mueve el plástico y a su calidad final. Se consideran dos temperaturas clave: temperatura del material y temperatura del molde .
-
Temperatura del material: El cilindro de la máquina controla esto. El fuego debe ser alto para que el plástico fluya bien sin romperse. Por ejemplo, el policarbonato 5 necesita una temperatura del cilindro entre 260°C y 300°C para mantenerse estable.
- Ejemplo: al fabricar productos delgados, como fundas para teléfonos móviles, se puede aumentar la temperatura del cilindro de los plásticos ABS para ayudar a que el plástico llene el molde por completo.
-
Temperatura del molde: Se gestiona mediante sistemas de refrigeración, normalmente con agua. Afecta la rapidez con la que se enfría la masa fundida, lo que afecta la apariencia de la superficie, la velocidad de trabajo y la contracción. Si la temperatura del molde aumenta, podría ayudar a cristalizar ciertos plásticos como la poliamida 6 , lo que resulta en una mejor densidad y resistencia.
Dinámica de presión en el moldeo por inyección
La presión es importante para la calidad del artículo moldeado al influir en el calor y el movimiento de la masa fundida. Las presiones clave son la presión de plastificación, la presión de inyección y la presión de la cavidad.
-
Presión de plastificación: También conocida como contrapresión, controla la mezcla de la masa fundida dentro del barril. Una mayor presión puede aumentar el calor derretido y ayudar a plastificar, pero puede ralentizar el flujo si es demasiado alto.
- Ejemplo: para materiales como el polietileno (PE), la alteración de la presión de plastificación afecta en gran medida la calidad de la masa fundida.
-
Presión de inyección: Importante para llenar el espacio del molde. Debe equilibrarse con la temperatura del material para evitar problemas como el desbordamiento o el llenado insuficiente.
- Ejemplo: en el caso de piezas de automóviles, la presión de inyección correcta es clave para alcanzar la precisión necesaria.
-
Presión de la cavidad: La presión final después de las pérdidas a través de las aberturas afecta la calidad del producto. El control es crucial para piezas precisas.
Interacción de temperatura y presión
Ambos factores se conectan; los cambios en uno pueden necesitar ajustes en el otro. Por ejemplo, las temperaturas más altas del material reducen las presiones de inyección requeridas, pero se deben vigilar de cerca para evitar daños.
Conocer estos vínculos es crucial para perfeccionar el moldeo por inyección, garantizando buenos productos con pocos defectos. Los productores deben ajustar estos elementos en función de las características del material y las necesidades del producto para obtener mejores resultados.
Una temperatura más alta del molde mejora la cristalización en poliamida.Verdadero
El aumento de la temperatura del molde favorece una mejor cristalización, lo que aumenta la densidad y la resistencia.
El aumento de la presión de plastificación reduce la temperatura de fusión.FALSO
El aumento de la presión de plastificación eleva la temperatura de fusión, mejorando la plastificación.
Conclusión
Conocer estos elementos mejora sus habilidades en moldeo por inyección, aportando precisión y calidad en la producción. Piense en estos aprendizajes para mejorar sus procesos de fabricación.
-
Los hornos de secado al vacío garantizan niveles óptimos de humedad, evitando defectos.: Tiempos de proceso significativamente reducidos... Ciclos de vacío controlados digitalmente, en los que la cámara de trabajo se ventila a intervalos cortos,... ↩
-
Explore las fases detalladas para mejorar la comprensión de las etapas del moldeo por inyección: Los pasos del proceso de moldeo por inyección · 1. Sujeción · 2. Inyección · 3. Alojamiento · 4. Enfriamiento · 5. Apertura del molde · 6. Expulsión. ↩
-
Comprender los parámetros clave para optimizar la calidad del moldeo por inyección: Se pueden argumentar múltiples variables (equilibrio de llenado, tiempo de llenado, presión de inyección, presión de la cavidad) como las más importantes. ↩
-
Descubra métodos para optimizar la calidad de los productos moldeados por inyección: Opciones populares de posprocesamiento para moldeo por inyección · Texturas Mold-Tech · Tampografía · Serigrafía · Insertos de estacas térmicas · Soldadura ultrasónica. ↩
-
Descubra cómo las propiedades térmicas del policarbonato afectan su procesamiento: Un policarbonato puede mantener su dureza a temperaturas de hasta 140 °C, lo que significa que las piezas de policarbonato pueden soportar esterilizaciones repetidas. ↩
-
Descubra cómo la temperatura del molde influye en la cristalización de la poliamida: La temperatura del molde debe estar entre 55 y 80 grados Celsius para el moldeo por inyección de PA6 y el moldeo por inyección de PA66, que es el rango de temperatura aceptable... ↩