Resolver problemas de falta de llenado en el diseño de moldes a veces se parece a resolver un rompecabezas muy complejo. Las estrategias adecuadas convierten los desafíos en oportunidades para mejorar.
Para solucionar problemas de llenado insuficiente en el diseño de moldes, estudie la ubicación y el tamaño de la puerta. Compruebe también los sistemas de guías. Es muy probable que una buena colocación mejore el flujo de fusión. El tamaño adecuado ayuda a llenar la cavidad por completo. Mejore también el control de los gases de escape. Estos cambios disminuyen los defectos en el moldeo por inyección. Un mejor flujo significa menos problemas.
Estas estrategias crean una base muy sólida. Observar de cerca cada detalle revela aún más potencial para mejorar tanto la eficiencia como la calidad. Es similar a ajustar un instrumento musical; cada ajuste armoniza su proceso de fabricación. Consulte estos consejos de expertos. Vea cómo cambia su línea de producción.
La ubicación de la puerta afecta el flujo de fusión en el moldeo por inyección.Verdadero
Ajustar la posición de la compuerta puede mejorar el llenado en áreas de paredes delgadas.
La longitud del canal no tiene impacto en la eficiencia del flujo de fusión.FALSO
Los canales más cortos reducen la resistencia, mejorando la eficiencia del flujo de fusión.
- 1. ¿Cómo puede la ubicación de la puerta afectar el llenado del molde?
- 2. ¿Cómo afecta el diseño del sistema de canales a la prevención del llenado insuficiente?
- 3. ¿Por qué es crucial el diseño de los gases de escape en el moldeo por inyección?
- 4. ¿Qué materiales mejoran la ventilación del molde?
- 5. ¿Cómo afecta la calidad de la superficie del molde al resultado del producto?
- 6. Conclusión
¿Cómo puede la ubicación de la puerta afectar el llenado del molde?
¿Alguna vez has pensado por qué es tan importante la colocación de las puertas en los moldes? ¡Parece que el objetivo es conseguir que el flujo sea perfecto!
La posición de la compuerta afecta la forma en que se llena el molde al controlar la ruta del flujo, la distribución de la presión y el riesgo de defectos. Las compuertas correctamente ubicadas permiten un llenado uniforme. Esto reduce las bolsas de aire y los problemas de llenado incompleto.
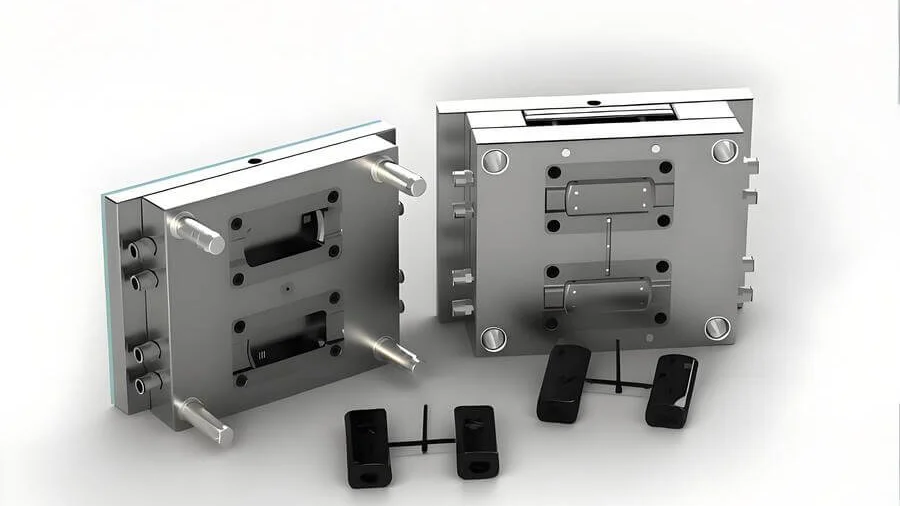
Optimización del diseño de la puerta
Ajuste de la ubicación de la puerta
Descubrí que la ubicación de la puerta afecta significativamente el proceso cuando se trabaja con formas complejas como un recipiente de plástico con un asa delgada. Colocar la compuerta cerca de la manija ayudó a evitar problemas de llenado insuficiente causados por recorridos largos de fusión. Pequeños cambios pueden cambiarlo todo, similar a dirigir un barco.
La simetría también juega un papel importante. Moldear una figura de juguete con una puerta lateral dio como resultado un resultado desigual. Alinear la compuerta a lo largo del eje de simetría permitió que la masa fundida fluyera adecuadamente, equilibrando ambos lados. Es como asegurarse de que todos en la mesa reciban una porción igual.
es esencial colocar puertas cerca de áreas de paredes delgadas o zonas difíciles de llenar 1
Cambiar el tamaño y la cantidad de puertas
El tamaño de la puerta es importante. Trabajar con bandejas de plástico grandes me demostró que aumentar el diámetro de la puerta de 3 mm a 5 mm mejoraba drásticamente el rendimiento. Más derretimiento conducía a menos defectos y, de hecho, a menos frustración.
Agregar más puertas a veces resuelve los problemas. Esto me lo enseñó una caja de herramientas con muchos compartimentos. La colocación de puertas adicionales cerca de cada sección llenó los compartimentos de manera uniforme e hizo que el proceso fuera tan fluido como mi café de la mañana.
Ajustar el tamaño de la compuerta según la complejidad del producto es vital para artículos grandes o aquellos con paredes gruesas; aumentar el tamaño de la compuerta puede mejorar el flujo de fusión.
Aumentar el número de puertas para estructuras complejas 2 garantiza una distribución uniforme.
Mejora del sistema de corredores
Ajuste de la longitud y el diámetro del corredor
Subestimé la importancia de acortar los corredores hasta que me ocupé de los problemas de pérdida de calor. Como un atajo en la carretera, los corredores más bajos enfrentaron menos resistencia y permitieron un flujo más fácil. En proyectos grandes, el aumento del diámetro del corredor aseguró un movimiento suave.
Acortar la longitud de los canales reduce la pérdida de calor y la resistencia a la fusión al rediseñar los canales para que sean más directos, como en los moldes para piezas pequeñas, se mejora la eficiencia.
Aspecto del corredor | Ajuste | Impacto |
---|---|---|
Longitud | Acortar | Menos resistencia |
Diámetro | Aumentar | Mejor flujo |
Mejora del diseño de los gases de escape
Agregar ranuras de escape funcionó como abrir ventanas en un día caluroso. Las trampas de aire dejaron de ser un problema. En el caso de estructuras intrincadas, los materiales respirables como el acero permeable al aire eran cruciales; ayudaron a combatir el llenado insuficiente debido al aire atrapado.
Agregar ranuras de escape en cavidades profundas y otras áreas 3 propensas a la retención de aire permite el escape del aire, evitando problemas de contrapresión.
La ubicación de la puerta afecta la eficiencia del llenado del molde.Verdadero
Ajustar la ubicación de la compuerta mejora el flujo hacia áreas de paredes delgadas, mejorando el llenado.
La longitud del canal no afecta la resistencia al flujo del material fundido.FALSO
El acortamiento de la longitud del canal reduce la resistencia al derretimiento y la disipación de calor.
¿Cómo afecta el diseño del sistema de canales a la prevención del llenado insuficiente?
Algunos moldes de inyección se llenan por completo, mientras que otros no. El diseño del sistema de guías es la razón clave.
Un buen diseño de sistema de canales da forma al moldeado controlando la facilidad con la que el material fundido se mueve hacia el molde. Este control de flujo es muy importante. Una tasa de llenado y una distribución de presión optimizadas ayudan a evitar problemas de llenado insuficiente. Esta práctica eleva la calidad del producto. La calidad es clave.
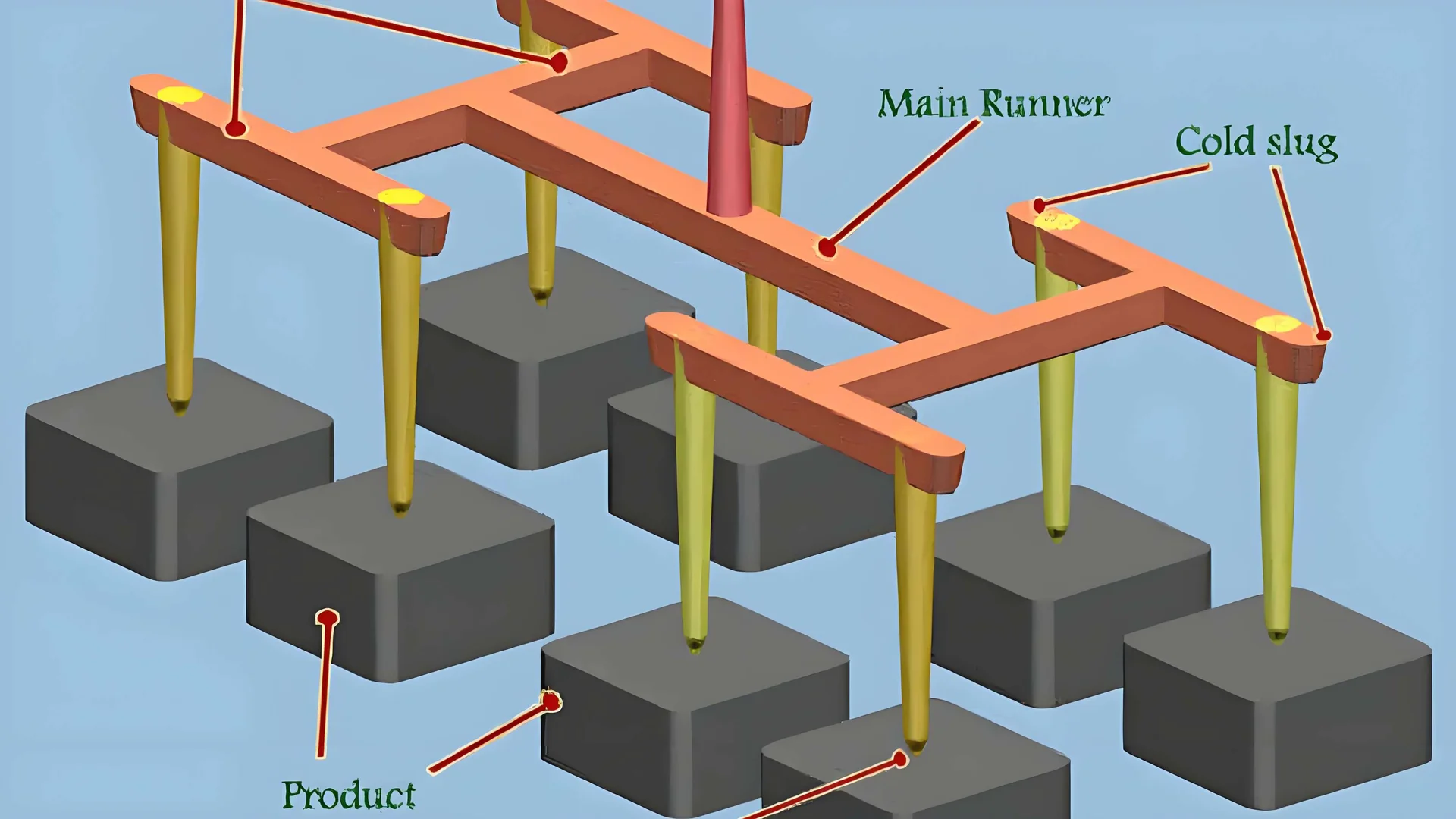
Hablemos de la longitud y el diámetro del corredor
Imagine que está trabajando en un proyecto de moldeo por inyección y el producto no se llena correctamente. Quizás la razón sea la longitud y el diámetro del corredor. Recuerdo que una vez los cambié en un proyecto: ¡realmente cambió todo! Los corredores cortos reducen la pérdida de calor y la resistencia. La masa fundida fluyó mejor. Aumentar el diámetro de 8 mm a 10 mm fue como abrir grandes puertas, especialmente para productos gruesos. Realmente ayudó.
Factor | Impacto |
---|---|
Longitud del corredor | La manteca reduce la disipación de calor. |
Diámetro del corredor | Los diámetros más grandes mejoran el caudal de fusión |
La magia de una superficie lisa
Una vez pulí una superficie rugosa del corredor y el flujo mejoró enormemente. Era casi como si el fundido estuviera feliz de tener un camino más fácil. Una rugosidad de la superficie inferior a Ra0,8μm reduce mucho la fricción. Menos fricción significa menos problemas de llenado. Realmente ayuda.
Diseño de puerta: el héroe anónimo
¡A menudo se pasa por alto el diseño de la puerta! Vi cómo mover puertas a mejores lugares puede cambiarlo todo, especialmente con diseños complejos. En un proyecto, mover la puerta sobre el eje de simetría de una figura de juguete cambió mucho la distribución del material fundido. Fue una gran victoria.
- Ubicación de la puerta : cerca de áreas de paredes delgadas.
- Tamaño/Número de puerta : Haga coincidir la complejidad y el tamaño del producto.
Explore más sobre la optimización del diseño de puertas 4 para formas complejas.
Respirar tranquilo con sistemas de escape
Los buenos sistemas de escape le dan aire fresco al molde. Utilicé acero respirable en un molde resistente y funcionó de maravilla. Las ranuras u orificios de escape dejan salir el aire atrapado. Menos aire significa menos problemas de llenado insuficiente. Conozca las mejoras al sistema de escape 5 para un mejor llenado del molde.
Conocer estos elementos del sistema de canales realmente ayuda a la calidad del producto. Hace que el material fluya mejor y corta defectos.
La ubicación de la compuerta afecta el flujo de fusión en formas complejas.Verdadero
Ajustar la ubicación de la puerta ayuda a llenar áreas de paredes delgadas de manera eficiente.
La rugosidad de la superficie del canal no afecta el flujo de fusión.FALSO
Los canales más suaves reducen la fricción, mejorando la eficiencia del flujo de fusión.
¿Por qué es crucial el diseño de los gases de escape en el moldeo por inyección?
¿Alguna vez ha pensado en cómo las pequeñas elecciones de diseño pueden afectar la calidad de un artículo moldeado? Exploremos por qué la planificación de los gases de escape es tan importante en el moldeo por inyección.
En el moldeo por inyección, el diseño de los gases de escape es muy importante para evitar defectos como disparos cortos y marcas de quemaduras. Este diseño permite que el aire atrapado escape bien. Este escape de aire ayuda a mantener estable la calidad del producto. También ayuda a que el molde funcione mejor.
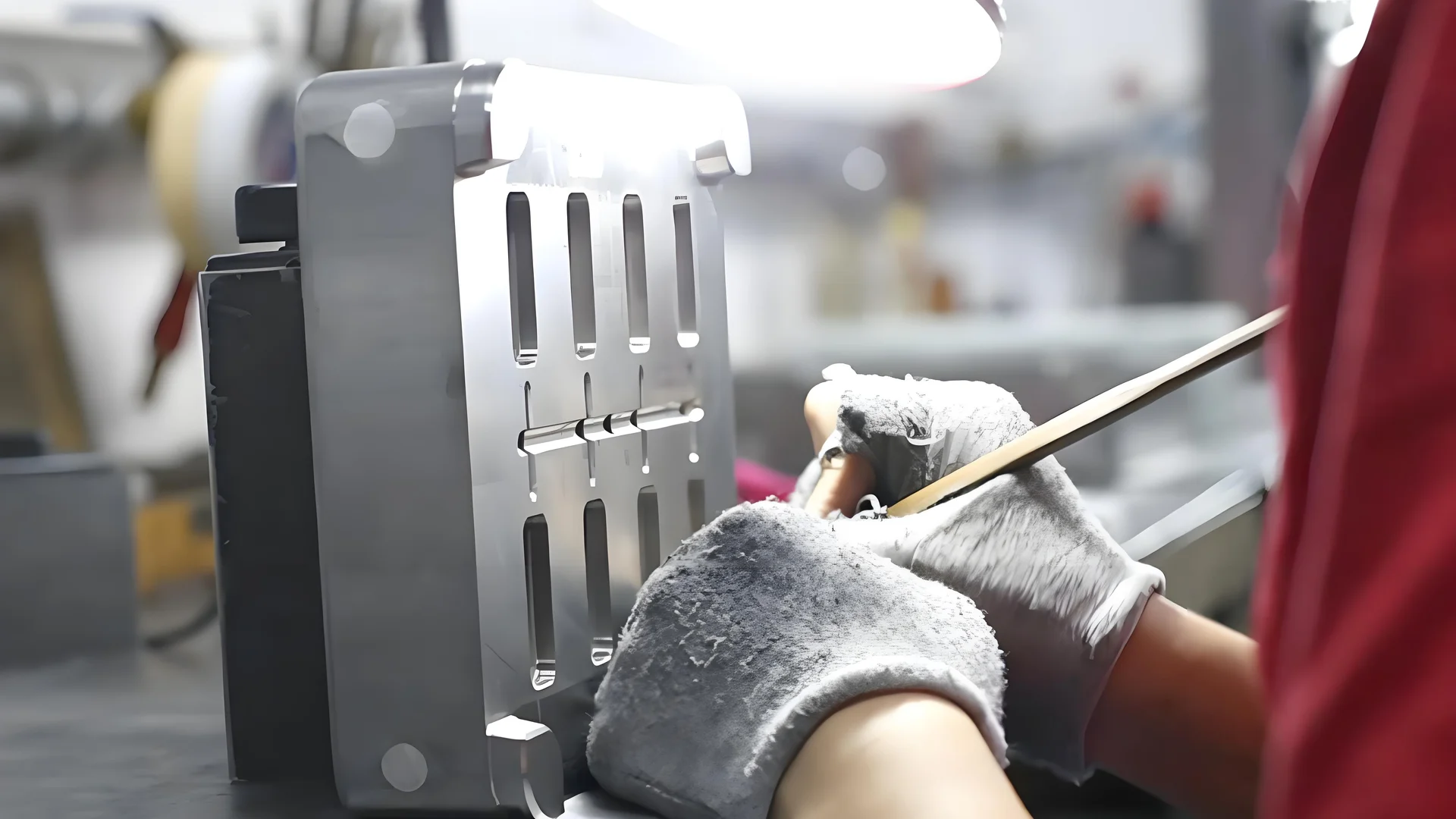
Comprensión de los gases de escape en el moldeo por inyección
Imagínese intentar llenar un molde complejo con plástico derretido, pero las molestas burbujas de aire siguen bloqueando el camino. Estas burbujas atrapadas pueden causar disparos cortos, donde el plástico no llena completamente el molde, o pueden causar marcas de quemaduras cuando el aire se incendia bajo presión. Por eso, un sistema de escape inteligente es muy importante.
Métodos de diseño de gases de escape.
Ranuras y orificios de escape
Las ranuras o agujeros de escape realmente cambian el juego cuando se colocan en los lugares correctos. Por ejemplo, en un proyecto con cavidades de molde profundas, agregar ranuras de escape de solo 0,03 mm de ancho y 0,2 mm de profundidad permitió que el aire escapara fácilmente. Alrededor de los pasadores expulsores, los orificios de escape ayudaron a que todas las piezas funcionaran sin problemas y redujeron significativamente los defectos.
Materiales transpirables
¿Qué pasa si las ranuras y los agujeros no funcionan? El uso de materiales transpirables, como el acero transpirable, podría muy bien salvar el día. Este acero permite que el aire circule a través de sus diminutos poros, ofreciendo una solución inteligente cuando las técnicas habituales no funcionan.
Optimización de los sistemas de ventilación: una tabla comparativa
Método | Ejemplo de aplicación | Beneficios |
---|---|---|
Ranuras de escape | Cavidades profundas en moldes. | Previene la compresión del aire y la contrapresión. |
Orificios de escape | Alrededor de los pasadores expulsores | Garantiza un funcionamiento suave y reduce los defectos. |
Materiales transpirables | Estructuras internas complejas | Resuelve el llenado insuficiente cuando el aire no puede escapar |
Impactos en el rendimiento del moldeo por inyección
El diseño correcto de los gases de escape no solo mejora el rendimiento del molde 6 , sino que también mejora la calidad del producto y reduce los residuos y los costos de producción. Con menos defectos que manejar, el tiempo del ciclo se vuelve más rápido. ¡Realmente acelera!
Consideraciones relacionadas en el diseño de moldes
Para ajustar el diseño de los gases de escape es necesario pensar en otras cosas, como la ubicación de la puerta y los sistemas de corredor. Cambiar el tamaño de la puerta 7 también puede ayudar a distribuir el material de manera uniforme, evitando posibles defectos.
La incorporación del diseño de los gases de escape a estas consideraciones más amplias permite a los fabricantes alcanzar un alto nivel de éxito en el moldeado.
Ajustar la ubicación de la puerta reduce el riesgo de llenado insuficiente.Verdadero
La colocación de compuertas cerca de áreas de paredes delgadas garantiza un flujo uniforme del material fundido.
El aumento del diámetro del canal disminuye la resistencia al flujo de fusión.Verdadero
Los diámetros más grandes permiten que pase más masa fundida sin problemas, mejorando el llenado.
¿Qué materiales mejoran la ventilación del molde?
Explorar materiales de ventilación con moho ayuda a crear aire más fresco y saludable. Las decisiones correctas mantienen su espacio libre de moho.
El acero transpirable y los plásticos porosos brillan en la ventilación del molde. Estos materiales ayudan a que el aire se mueva por el espacio. La reducción de la humedad se produce de forma eficaz. Las posibilidades de crecimiento de moho probablemente disminuyen significativamente. Los riesgos de moho siguen siendo muy bajos. Esto es importante. Los riesgos de moho siguen siendo muy bajos.

Acero transpirable
El acero transpirable es un material innovador utilizado en la fabricación de moldes para mejorar la ventilación. Su naturaleza porosa permite que el aire escape a través del propio acero, lo que resulta especialmente útil en estructuras complejas 8 donde las soluciones de escape tradicionales no son viables.
Recuerdo una época trabajando en un proyecto con juguetes de plástico detallados para niños. Los juguetes debían ser perfectos tanto en apariencia como en seguridad. El acero respirable se convirtió en un sorprendente salvador. Sus pequeños agujeros dejan escapar el aire, especialmente en zonas difíciles donde los métodos habituales a menudo fallan. Una vez resolvió un problema de aire duro en la naricita de un juguete. Salvó el proyecto y mi cordura. Fue un verdadero alivio.
Por ejemplo, al moldear productos plásticos complejos, el acero respirable se puede colocar estratégicamente en áreas propensas a la retención de aire, lo que permite un flujo de aire perfecto.
Plásticos porosos
Los plásticos porosos son otra excelente opción para mejorar la ventilación. Estos materiales están diseñados con microagujeros que permiten el paso del aire manteniendo la integridad estructural.
Los plásticos porosos fueron útiles durante la remodelación de mi cocina. Estos materiales se adaptaban muy bien a las molduras con espacios profundos. Tienen pequeños agujeros que permiten el paso del aire mientras se mantienen fuertes. Esto fue fundamental para evitar que las burbujas de aire arruinaran mis nuevos gabinetes.
Una aplicación común es la fabricación de productos con cavidades profundas, donde estos plásticos ayudan a evitar que se formen bolsas de aire durante el proceso de moldeo.
Material | Ventajas |
---|---|
Acero transpirable | Permite el escape de aire en estructuras de moldes complejas. |
Plásticos porosos | Previene bolsas de aire y mantiene la forma del producto. |
Caucho de silicona
El caucho de silicona es conocido por su flexibilidad y resistencia a la humedad. Se puede utilizar en moldes para crear sellos que impidan la entrada de aire y humedad no deseados, controlando así los niveles de humedad de forma eficaz.
El caucho de silicona fue clave cuando necesitaba flexibilidad y resistencia a la humedad. Actuó como una ayuda invisible, equilibrando entre mantener la humedad afuera y dejar entrar el aire. Ideal para moldes que necesitan cambios frecuentes, el caucho de silicona proporcionó la flexibilidad que aseguró que el proceso se desarrollara sin problemas.
Además, las cualidades inherentes del caucho de silicona lo hacen ideal para moldes que requieren ajustes o modificaciones frecuentes.
Incorporación de materiales avanzados
Explorar materiales avanzados 9 como resinas compuestas o metales tratados también puede contribuir a mejorar la ventilación. Las resinas compuestas son livianas pero resistentes y brindan un excelente equilibrio entre resistencia y permeabilidad.
Probar materiales avanzados fue como descubrir nuevas oportunidades. Las resinas compuestas y los metales tratados se convirtieron en herramientas esenciales para mí:
- Resinas compuestas : ligeras pero resistentes, ofrecen la combinación perfecta para diseños complejos.
- Metales tratados : reduzca la fricción mejorando el flujo de aire mediante una fricción superficial reducida, perfecto para diseños de moldes detallados.
Seleccionar estos materiales cuidadosamente no solo mejoró mis diseños sino que también aumentó mi confianza para diseñar proyectos de manera más eficiente y al mismo tiempo reducir los defectos causados por el mal movimiento del aire.
El tamaño de la puerta debería aumentar para productos más grandes.Verdadero
Los productos más grandes requieren un mayor tamaño de puerta para mejorar el flujo de fusión.
Las superficies rugosas de los canales mejoran el flujo de fusión.FALSO
Los canales suaves reducen la fricción, mejorando la eficiencia del flujo de fusión.
¿Cómo afecta la calidad de la superficie del molde al resultado del producto?
¿Alguna vez te has preguntado cómo los detalles más pequeños deciden el éxito o el fracaso de un producto?
La calidad de la superficie de un molde afecta en gran medida la apariencia, el tacto y el funcionamiento del producto final. Un molde liso ayuda a que el material fluya uniformemente. Esto reduce los defectos. También mejora la apariencia y la fuerza. Esto es crucial. Esto es muy importante para crear artículos de alta calidad.
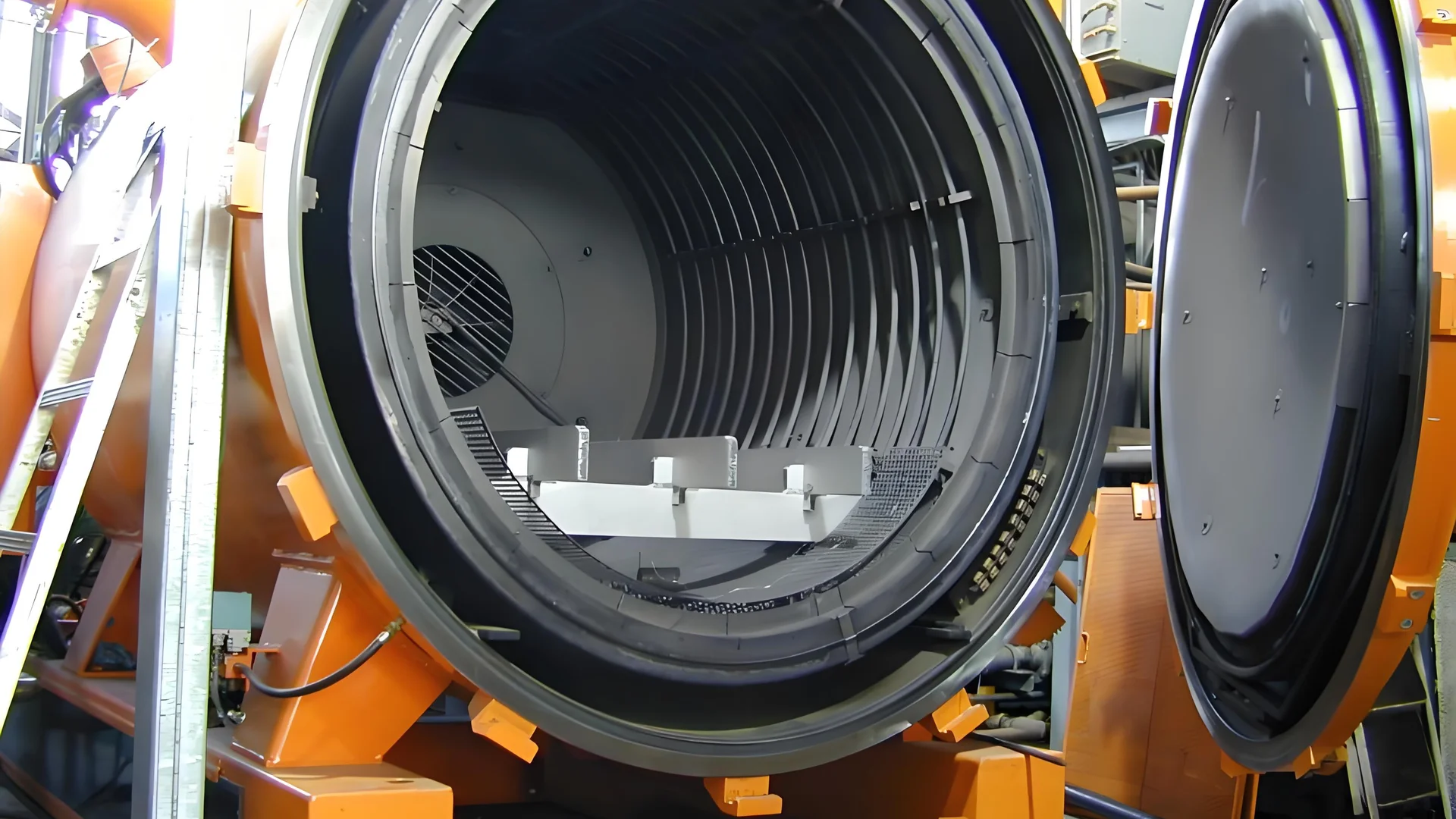
El papel del acabado superficial en la estética y la funcionalidad
La primera vez que noté el impacto de un molde pulido fue inolvidable. Se sintió como magia: ver el material fundido deslizarse en cada esquina sin ningún problema. Con menos fricción, una superficie lisa permite que la masa fundida se mueva fácilmente 10 , dando un acabado tan uniforme que los defectos casi desaparecen. Mire los gabinetes electrónicos, por ejemplo. Un acabado brillante no sólo luce elegante sino que también actúa como un escudo, manteniendo la suciedad alejada y su brillo intacto durante mucho tiempo.
Calidad superficial e integridad estructural
Nada frustra más que ver un diseño arruinado por desniveles o puntos débiles. Descubrí, a través de desafíos, que estos problemas a menudo provienen de superficies rugosas del molde. Al mejorar cuidadosamente la suavidad mediante el pulido, mantenemos el equilibrio del enfriamiento y protegemos la forma y la resistencia del producto. Es como colocarle una armadura a su producto.
Mejoras en el diseño de puertas y corredores
Optimización del diseño de la puerta:
- Ajuste de la ubicación de la puerta: Tuve que mover la puerta por las manijas de los contenedores de plástico una vez y ¡guau, qué cambio! Este pequeño cambio logra un relleno uniforme, especialmente en áreas difíciles de paredes delgadas.
- Ajustes de tamaño y número: para moldes más grandes, aumentar el tamaño de la puerta ayuda mucho. Agregar puertas adicionales en partes complejas también puede marcar una gran diferencia.
Tipo de producto | Ajuste de la puerta |
---|---|
Contenedores de paredes delgadas | Cerca de áreas delgadas |
Bandejas grandes | Mayor diámetro de puerta |
Cajas de herramientas complejas | Puertas auxiliares adicionales |
Mejoras en el sistema de corredores
Ajuste de longitud y diámetro de los corredores:
Intenté acortar los corredores para disminuir la pérdida de calor. En artículos más grandes, aumentar el diámetro del canal ayuda a que la masa fundida fluya más suavemente.
- Calidad de la superficie: ¿Corredores pulidos? ¡Absolutamente! Reducen enormemente la fricción, lo que significa menos problemas de llenados incompletos: un verdadero salvavidas en la producción.
Mejora del diseño de los gases de escape
Implementación de ranuras de escape:
las cavidades profundas se benefician de las ranuras de escape, lo que evita el molesto aire atrapado que provoca la acumulación de presión. Los orificios de escape bien ubicados son muy importantes para que el aire salga limpio.
Característica del molde | Diseño de escape |
---|---|
Cavidades profundas | Ranuras de escape |
Superficies de separación | Orificios de escape regulares |
Concentrarse en la calidad de la superficie del molde es como perfeccionar un arte: mejora significativamente los resultados del producto. Este enfoque no sólo hace que los productos luzcan mejor, sino que también garantiza que se mantengan firmes y funcionen bien. Aquellos interesados en aprender más deberían explorar más recursos sobre mejoras de moldes 11 para obtener información valiosa sobre cómo mejorar las estrategias de producción.
La ubicación de la puerta afecta la eficiencia del llenado del molde.Verdadero
La colocación de compuertas cerca de áreas de paredes delgadas garantiza un flujo uniforme del material fundido.
La calidad de la superficie del canal no afecta el llenado del molde.FALSO
Los canales más suaves reducen la fricción, mejorando la eficiencia del flujo de fusión.
Conclusión
Este artículo explora soluciones efectivas de diseño de moldes para problemas de llenado insuficiente, centrándose en la optimización de la compuerta, las mejoras del sistema de canales y el diseño de los gases de escape para mejorar la eficiencia y la calidad del producto.
-
Explore cómo las diferentes ubicaciones de las puertas afectan el llenado del molde en formas complejas, mejorando sus diseños. ↩
-
Descubra por qué múltiples puertas pueden optimizar el llenado de moldes para productos complejos. ↩
-
Comprenda cómo el diseño del escape mejora el llenado del molde al permitir que escape el aire atrapado. ↩
-
Explore estrategias para la ubicación y el tamaño de las puertas que mejoren la eficiencia del llenado en moldes complejos. ↩
-
Descubra métodos para mejorar la evacuación de aire de los moldes, reduciendo defectos como el llenado insuficiente. ↩
-
Conozca los beneficios de un sistema de escape bien diseñado para mejorar la eficiencia del molde y la calidad del producto. ↩
-
Comprenda cómo ajustar el tamaño de la compuerta puede mejorar la distribución del material y complementar las estrategias de gases de escape. ↩
-
Este enlace explica cómo las propiedades únicas del acero respirable mejoran el flujo de aire y previenen la retención de aire. ↩
-
Explore cómo los materiales avanzados, como las resinas compuestas, optimizan el diseño del molde al mejorar el flujo de aire y la resistencia. ↩
-
Descubra cómo las superficies más lisas facilitan un flujo eficiente del material fundido, reduciendo los defectos. ↩
-
Descubra métodos para mejorar la calidad del molde, garantizando un rendimiento superior del producto. ↩