Résoudre les problèmes de sous-remplissage dans la conception de moules ressemble parfois à résoudre un casse-tête très complexe. Les bonnes stratégies transforment les défis en opportunités d’amélioration.
Pour résoudre les problèmes de sous-remplissage dans la conception du moule, étudiez l'emplacement et la taille des portes. Vérifiez également les systèmes de coureurs. Un bon placement améliore très probablement l'écoulement de la matière fondue. Une taille appropriée aide à remplir complètement la cavité. Améliorez également le contrôle des gaz d’échappement. Ces changements diminuent les défauts du moulage par injection. Un meilleur flux signifie moins de problèmes.
Ces stratégies créent une base très solide. Un examen attentif de chaque détail révèle encore plus de potentiel d’amélioration de l’efficacité et de la qualité. C'est comme ajuster un instrument de musique ; chaque ajustement harmonise votre processus de fabrication. Consultez ces conseils d’experts. Voyez votre ligne de production changer.
L'emplacement de la porte affecte l'écoulement de la matière fondue dans le moulage par injection.Vrai
Le réglage de la position de la porte peut améliorer le remplissage dans les zones à parois minces.
La longueur des canaux n'a aucun impact sur l'efficacité de l'écoulement de la matière fondue.FAUX
Les canaux plus courts réduisent la résistance, améliorant ainsi l'efficacité de l'écoulement de la matière fondue.
- 1. Quel est l'impact de l'emplacement de la porte sur le remplissage du moule ?
- 2. Comment la conception du système de glissières affecte-t-elle la prévention du sous-remplissage ?
- 3. Pourquoi la conception des gaz d’échappement est-elle cruciale dans le moulage par injection ?
- 4. Quels matériaux améliorent la ventilation des moisissures ?
- 5. Comment la qualité de la surface du moule affecte-t-elle le résultat du produit ?
- 6. Conclusion
Quel est l'impact de l'emplacement de la porte sur le remplissage du moule ?
Avez-vous déjà réfléchi à la raison pour laquelle le placement des portes dans les moules est si important ? Il semble que l’objectif soit d’obtenir un flux parfait !
La position de la porte affecte la façon dont le moule se remplit en contrôlant le chemin d'écoulement, la répartition de la pression et le risque de défauts. Des portes correctement positionnées permettent un remplissage uniforme. Cela réduit les poches d'air et les problèmes de remplissage incomplet.
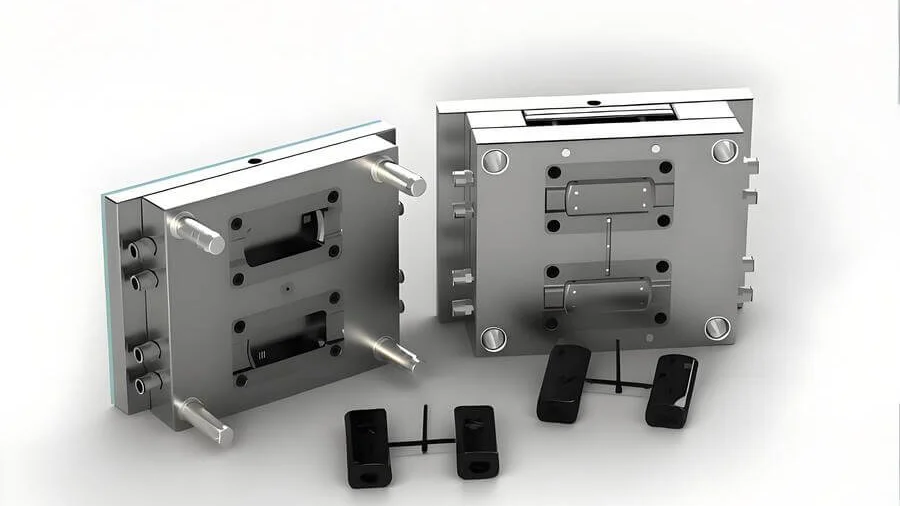
Optimisation de la conception des portes
Ajustement de l'emplacement de la porte
J'ai découvert que le placement des portes a un impact significatif sur le processus lorsque l'on travaille avec des formes complexes comme un récipient en plastique avec une poignée fine. Le fait de placer la porte près de la poignée a permis d'éviter les problèmes de sous-remplissage causés par les longs trajets de fusion. De petits changements peuvent tout changer, comme diriger un navire.
La symétrie joue également un grand rôle. Le moulage d’une figurine avec une porte latérale a donné un résultat inégal. L'alignement de la porte le long de l'axe de symétrie a permis à la matière fondue de s'écouler correctement, équilibrant les deux côtés. C'est comme s'assurer que tout le monde à la table reçoive une part égale.
Pour les formes complexes, il est indispensable de placer les portes à proximité des zones à parois fines ou 1 difficiles à remplir .
Modification de la taille et du nombre de portes
La taille du portail est importante. Travailler sur de grands plateaux en plastique m'a montré qu'augmenter le diamètre de la porte de 3 mm à 5 mm améliorait considérablement les performances. Plus de fusion entraînait moins de défauts, voire moins de frustration.
L'ajout de portes supplémentaires résout parfois des problèmes. Une boîte à outils avec de nombreux compartiments m'a appris cela. Placer des portes supplémentaires près de chaque section a rempli les compartiments de manière uniforme et a rendu le processus aussi fluide que mon café du matin.
L'ajustement de la taille de la porte en fonction de la complexité du produit est vital pour les articles volumineux ou ceux à parois épaisses. L'augmentation de la taille de la porte peut améliorer l'écoulement de la matière fondue.
L'augmentation du nombre de portes pour les structures complexes 2 garantit une répartition homogène.
Amélioration du système de coureurs
Ajustement de la longueur et du diamètre des coureurs
J'ai sous-estimé l'importance de raccourcir les coureurs jusqu'à ce que je fasse face à des problèmes de perte de chaleur. Comme un raccourci sur la route, les coureurs plus courts faisaient face à moins de résistance et permettaient une circulation plus facile. Sur les grands projets, l’augmentation du diamètre des glissières garantissait un mouvement fluide.
Le raccourcissement de la longueur des canaux réduit les pertes de chaleur et la résistance à la fusion en redessinant les canaux pour qu'ils soient plus directs, comme dans les moules pour petites pièces, vous améliorez l'efficacité.
Aspect coureur | Ajustement | Impact |
---|---|---|
Longueur | Raccourcir | Moins de résistance |
Diamètre | Augmenter | Meilleur flux |
Amélioration de la conception des gaz d'échappement
L'ajout de rainures d'échappement a fonctionné comme l'ouverture de fenêtres par une journée chaude. Les pièges à air sont devenus moins problématiques. Avec des structures complexes, les matériaux respirants comme l’acier perméable à l’air étaient cruciaux ; ils ont aidé à lutter contre le sous-remplissage dû à l'air emprisonné.
L'ajout de rainures d'échappement dans les cavités profondes et dans d'autres zones sujettes à la rétention d'air permet à l'air de s'échapper, évitant ainsi les problèmes de contre-pression.
L'emplacement de la porte affecte l'efficacité du remplissage du moule.Vrai
L'ajustement de l'emplacement de la porte améliore le flux vers les zones à parois minces, améliorant ainsi le remplissage.
La longueur des canaux n’a pas d’impact sur la résistance à l’écoulement de la matière fondue.FAUX
Le raccourcissement de la longueur des canaux réduit la résistance à la fusion et la dissipation thermique.
Comment la conception du système de glissières affecte-t-elle la prévention du sous-remplissage ?
Certains moules à injection se remplissent complètement, d’autres non. La conception du système de guidage en est la principale raison.
Une bonne conception du système de canaux façonne le moulage en contrôlant la facilité avec laquelle le matériau fondu se déplace dans un moule. Ce contrôle de flux est très important. Un taux de remplissage et une répartition de la pression optimisés aident à éviter les problèmes de sous-remplissage. Cette pratique améliore la qualité du produit. La qualité est la clé.
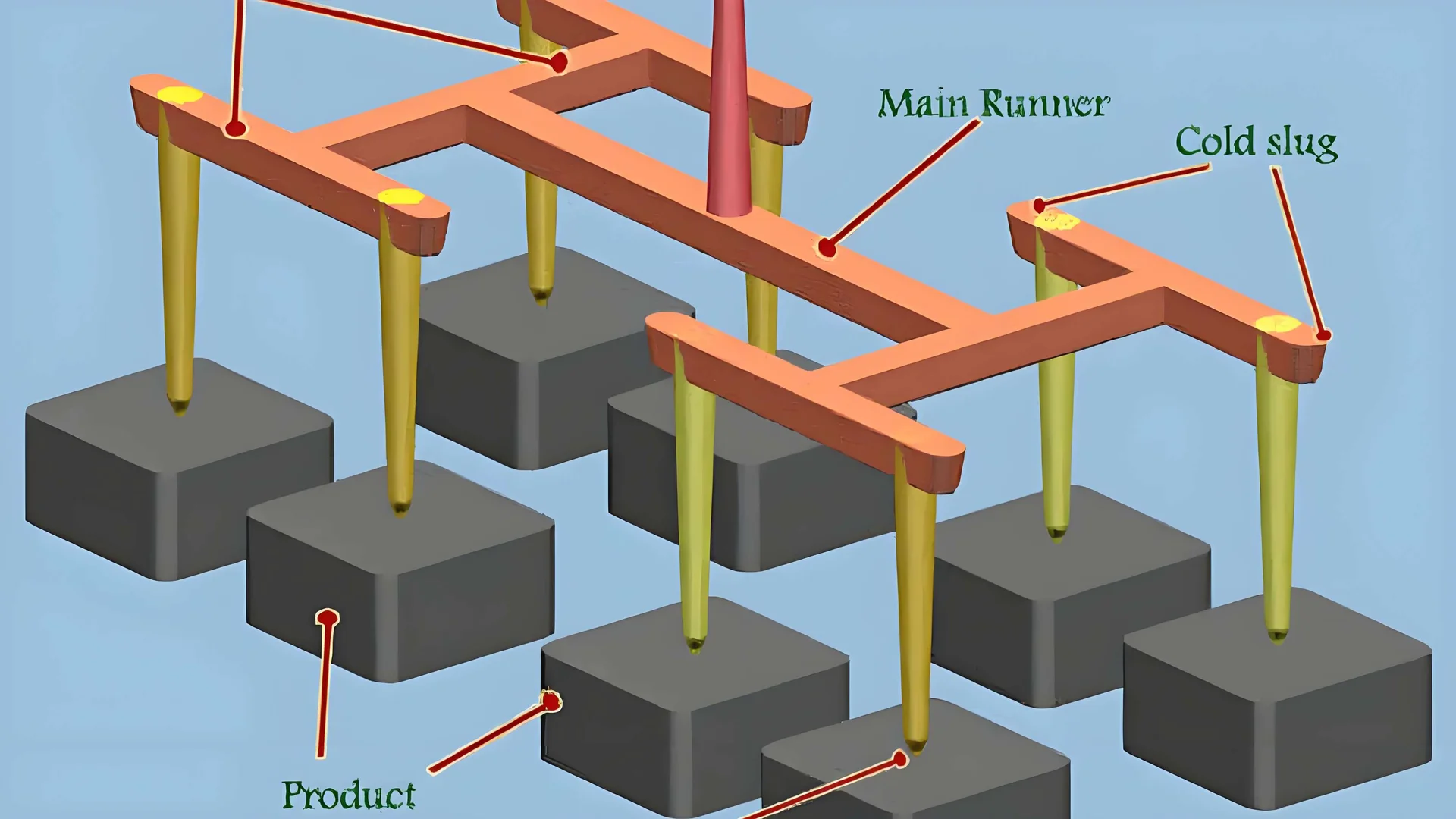
Parlons de la longueur et du diamètre des coureurs
Imaginez que vous travaillez sur un projet de moulage par injection et que le produit ne se remplit pas correctement. Peut-être que la longueur et le diamètre du coureur en sont la raison. Je me souviens de les avoir modifiés une fois dans un projet – cela a vraiment tout changé ! Les coureurs courts réduisent les pertes de chaleur et la résistance. La fonte coulait mieux. Augmenter le diamètre de 8 mm à 10 mm revenait à ouvrir de grandes portes, surtout pour les produits épais. Cela a vraiment aidé.
Facteur | Impact |
---|---|
Longueur du coureur | Le raccourcissement réduit la dissipation thermique |
Diamètre du coureur | Des diamètres plus grands améliorent le débit de fusion |
La magie d'une surface de roulement lisse
J'ai poli une fois une surface rugueuse et le débit s'est considérablement amélioré. C'était presque comme si le fondu était heureux d'avoir un chemin plus facile. Une rugosité de surface inférieure à Ra0,8 μm réduit considérablement la friction. Moins de friction signifie moins de problèmes de remplissage. Cela aide vraiment.
Conception de la porte : le héros méconnu
Le design des portails est souvent négligé ! J'ai vu comment déplacer les portes vers de meilleurs endroits peut tout changer, en particulier avec des conceptions complexes. Dans un projet, déplacer la porte sur l'axe de symétrie d'une figurine de jouet a considérablement modifié la distribution de la matière fondue. C'était une grande victoire.
- Emplacement de la porte : Près des zones à parois minces.
- Taille/numéro de porte : faire correspondre la complexité et la taille du produit.
Découvrez-en davantage sur l’optimisation de la conception des portes 4 pour les formes complexes.
Respirer facilement grâce aux systèmes d'échappement
De bons systèmes d’échappement donnent de l’air frais à votre moule. J'ai utilisé de l'acier respirant dans un moule résistant et cela a fait des merveilles. Les rainures ou les trous d'échappement permettent à l'air emprisonné de s'échapper. Moins d’air signifie moins de problèmes de sous-remplissage. Découvrez les améliorations du système d'échappement 5 pour un meilleur remplissage des moules.
Connaître ces éléments du système de guidage contribue réellement à la qualité du produit. Cela améliore le flux des matériaux et réduit les défauts.
L'emplacement de la porte affecte l'écoulement de la matière fondue dans les formes complexes.Vrai
L'ajustement de l'emplacement de la porte permet de remplir efficacement les zones à parois minces.
La rugosité de la surface des canaux n'a pas d'impact sur l'écoulement de la matière fondue.FAUX
Des canaux plus lisses réduisent la friction, améliorant ainsi l'efficacité de l'écoulement de la matière fondue.
Pourquoi la conception des gaz d’échappement est-elle cruciale dans le moulage par injection ?
Avez-vous déjà pensé à la façon dont de petits choix de conception peuvent affecter la qualité d'un article moulé ? Voyons pourquoi la planification des gaz d'échappement est très importante dans le moulage par injection.
Dans le moulage par injection, la conception des gaz d'échappement est très importante pour éviter les défauts tels que les projections courtes et les marques de brûlure. Cette conception permet à l’air emprisonné de bien s’échapper. Cette fuite d’air contribue à maintenir la qualité du produit stable. Cela aide également le moule à mieux fonctionner.
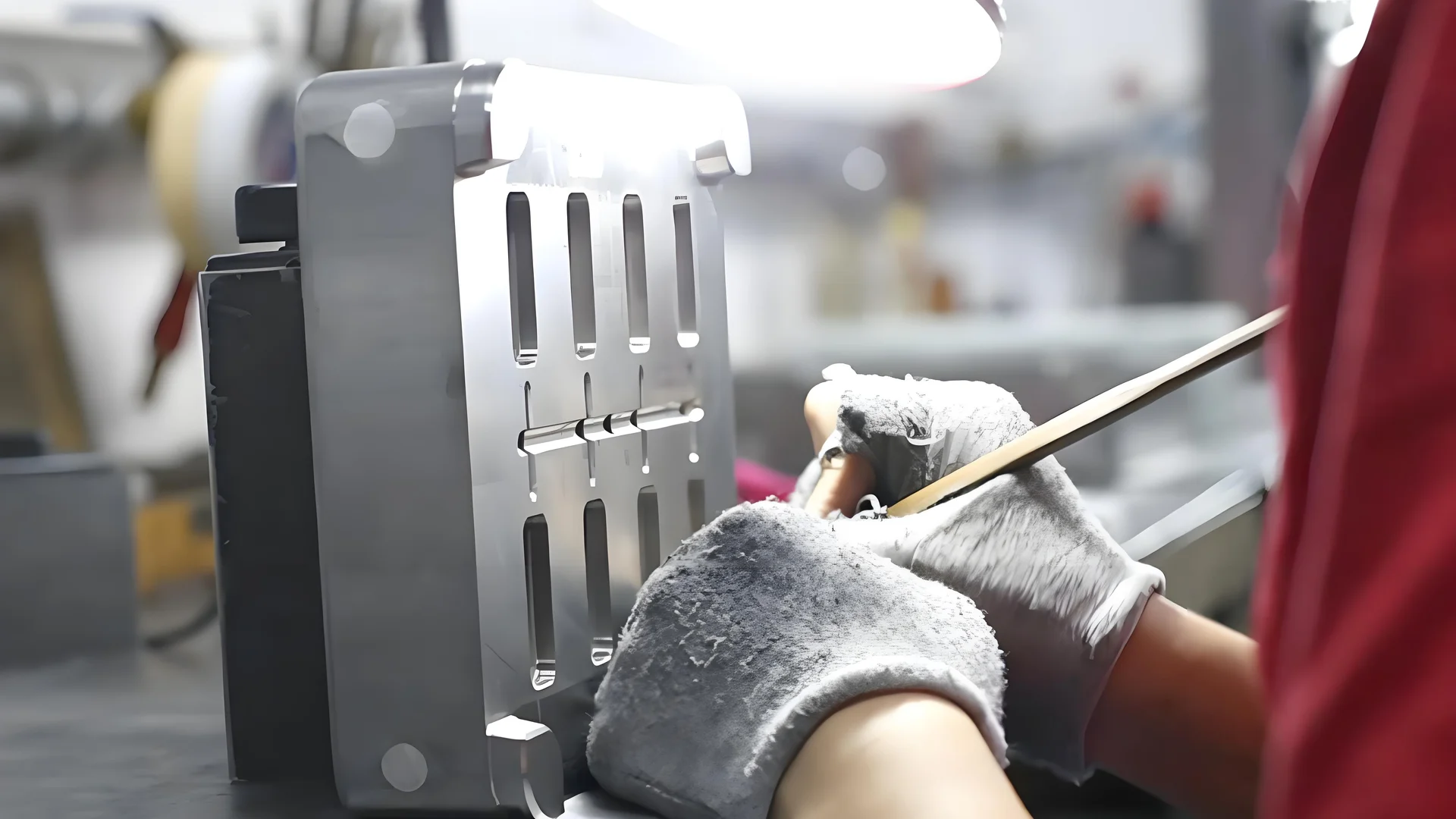
Comprendre les gaz d'échappement dans le moulage par injection
Imaginez que vous essayez de remplir un moule complexe avec du plastique fondu, mais que des bulles d'air gênantes continuent de bloquer le passage. Ces bulles piégées peuvent provoquer des tirs courts, où le plastique ne remplit pas complètement le moule, ou elles peuvent provoquer des marques de brûlure lorsque l'air prend feu sous la pression. Un système d’échappement intelligent est donc très important.
Méthodes de conception des gaz d'échappement
Rainures et trous d'échappement
Les rainures ou les trous d'échappement changent vraiment la donne lorsqu'ils sont placés aux bons endroits. Par exemple, dans un projet comportant des cavités de moule profondes, l'ajout de rainures d'échappement de seulement 0,03 mm de large et 0,2 mm de profondeur a permis à l'air de s'échapper facilement. Autour des broches d'éjection, des trous d'échappement ont permis à toutes les pièces de fonctionner sans problème et de réduire considérablement les défauts.
Matériaux respirants
Que se passe-t-il si les rainures et les trous ne fonctionnent pas ? L’utilisation de matériaux respirants, tels que l’acier respirant, pourrait très bien sauver la situation. Cet acier laisse l'air circuler à travers ses minuscules pores, offrant une solution intelligente lorsque les techniques habituelles échouent.
Optimisation des systèmes de ventilation : un tableau comparatif
Méthode | Exemple d'application | Avantages |
---|---|---|
Rainures d'échappement | Cavités profondes dans les moules | Empêche la compression de l'air et la contre-pression |
Trous d'échappement | Autour des éjecteurs | Assure un fonctionnement fluide et réduit les défauts |
Matériaux respirants | Structures internes complexes | Résout le sous-remplissage lorsque l’air ne peut pas s’échapper |
Impacts sur les performances du moulage par injection
Une conception correcte des gaz d'échappement améliore non seulement les performances du moule 6 , mais améliore également la qualité du produit tout en réduisant les déchets et les coûts de production. Avec moins de défauts à gérer, le temps de cycle devient plus rapide. Ça accélère vraiment !
Considérations connexes dans la conception de moules
Le réglage précis de la conception des gaz d'échappement nécessite de réfléchir à d'autres éléments tels que l'emplacement des portes et les systèmes de glissières. Changer la taille de la porte 7 peut également aider à répartir le matériau uniformément, évitant ainsi d'éventuels défauts.
L'intégration de la conception des gaz d'échappement dans ces considérations plus larges permet aux fabricants d'atteindre un niveau élevé de réussite en matière de moulage.
L'ajustement de l'emplacement de la porte réduit le risque de sous-remplissage.Vrai
Le positionnement des portes à proximité des zones à parois minces garantit un écoulement uniforme de la matière fondue.
L'augmentation du diamètre du canal diminue la résistance à l'écoulement de la matière fondue.Vrai
Des diamètres plus grands permettent à une plus grande quantité de matière fondue de passer en douceur, améliorant ainsi le remplissage.
Quels matériaux améliorent la ventilation des moisissures ?
L’exploration des matériaux de ventilation des moisissures contribue à créer un air plus frais et plus sain. Les bonnes décisions protègent votre espace de la moisissure.
L'acier respirant et les plastiques poreux brillent dans la ventilation des moules. Ces matériaux aident l’air à circuler dans l’espace. La réduction de l'humidité s'effectue efficacement. Les risques de croissance de moisissures diminuent probablement considérablement. Les risques de moisissure restent très faibles. C'est important. Les risques de moisissure restent très faibles.

Acier respirant
L'acier respirant est un matériau innovant utilisé dans la fabrication de moules pour améliorer la ventilation. Sa nature poreuse permet à l'air de s'échapper à travers l'acier lui-même, ce qui est particulièrement utile dans les structures complexes 8 où les solutions d'échappement traditionnelles ne sont pas réalisables.
Je me souviens d'une époque où je travaillais sur un projet avec des jouets en plastique détaillés pour les enfants. Les jouets devaient être parfaits en termes d’apparence et de sécurité. L’acier respirant est devenu un sauveur surprenant. Ses minuscules trous permettent à l’air de s’échapper, en particulier dans les zones délicates où les méthodes habituelles échouent souvent. Une fois, cela a résolu un problème d’air dur dans le petit nez d’un jouet. Cela a sauvé le projet et ma santé mentale. Ce fut un vrai soulagement.
Par exemple, lors du moulage de produits en plastique complexes, l’acier respirant peut être placé stratégiquement dans les zones sujettes à la rétention d’air, permettant ainsi une circulation d’air fluide.
Plastiques poreux
Les plastiques poreux constituent un autre excellent choix pour améliorer la ventilation. Ces matériaux sont conçus avec des micro-trous qui permettent le passage de l'air tout en préservant l'intégrité structurelle.
Les plastiques poreux se sont avérés utiles lors de la rénovation de ma cuisine. Ces matériaux conviennent très bien aux moulures comportant des espaces profonds. Ils comportent de minuscules trous permettant à l’air de passer tout en restant solides. C'était énorme pour empêcher les bulles d'air de ruiner mes nouvelles armoires.
Une application courante concerne la fabrication de produits comportant des cavités profondes, où ces plastiques aident à empêcher la formation de poches d’air pendant le processus de moulage.
Matériel | Avantages |
---|---|
Acier respirant | Permet à l'air de s'échapper dans les structures de moules complexes |
Plastiques poreux | Empêche les poches d'air et maintient la forme du produit |
Caoutchouc de silicone
Le caoutchouc de silicone est réputé pour sa flexibilité et sa résistance à l'humidité. Il peut être utilisé dans les moules pour créer des joints qui empêchent la pénétration indésirable d’air et d’humidité, contrôlant ainsi efficacement les niveaux d’humidité.
Le caoutchouc de silicone était essentiel lorsque j'avais besoin de flexibilité et de résistance à l'humidité. Il agissait comme une aide invisible, équilibrant entre empêcher l’humidité d’entrer et laisser entrer l’air. Idéal pour les moules nécessitant des changements fréquents, le caoutchouc de silicone offrait la flexibilité qui garantissait le bon déroulement du processus.
De plus, les qualités inhérentes du caoutchouc de silicone le rendent idéal pour les moules nécessitant des ajustements ou des modifications fréquents.
Incorporation de matériaux avancés
L'exploration de matériaux avancés 9 comme les résines composites ou les métaux traités peut également contribuer à améliorer la ventilation. Les résines composites sont légères mais robustes, offrant un excellent équilibre entre résistance et perméabilité.
Essayer des matériaux avancés, c’était comme découvrir de nouvelles opportunités. Les résines composites et les métaux traités sont devenus pour moi des outils indispensables :
- Résines composites : Légères mais résistantes, offrant le mélange parfait pour les conceptions complexes.
- Métaux traités : Réduisez la friction en améliorant la circulation de l'air grâce à une friction de surface réduite ; parfait pour les conceptions de moules détaillées.
En sélectionnant soigneusement ces matériaux, j'ai non seulement amélioré mes conceptions, mais j'ai également renforcé ma confiance dans la conception de projets plus efficaces tout en réduisant les défauts dus à un mauvais mouvement de l'air.
La taille de la porte devrait augmenter pour les produits plus gros.Vrai
Les produits plus gros nécessitent une taille de porte plus grande pour améliorer l'écoulement de la matière fondue.
Les surfaces rugueuses des canaux améliorent l'écoulement de la matière fondue.FAUX
Les canaux lisses réduisent la friction, améliorant ainsi l'efficacité de l'écoulement de la matière fondue.
Comment la qualité de la surface du moule affecte-t-elle le résultat du produit ?
Vous êtes-vous déjà demandé comment les moindres détails déterminent le succès ou l'échec d'un produit ?
La qualité de la surface d'un moule affecte grandement l'apparence, la sensation et le fonctionnement du produit final. Un moule lisse aide le matériau à s'écouler uniformément. Cela réduit les défauts. Cela améliore également l’apparence et la résistance. C’est crucial. Ceci est très important pour créer des articles de haute qualité.
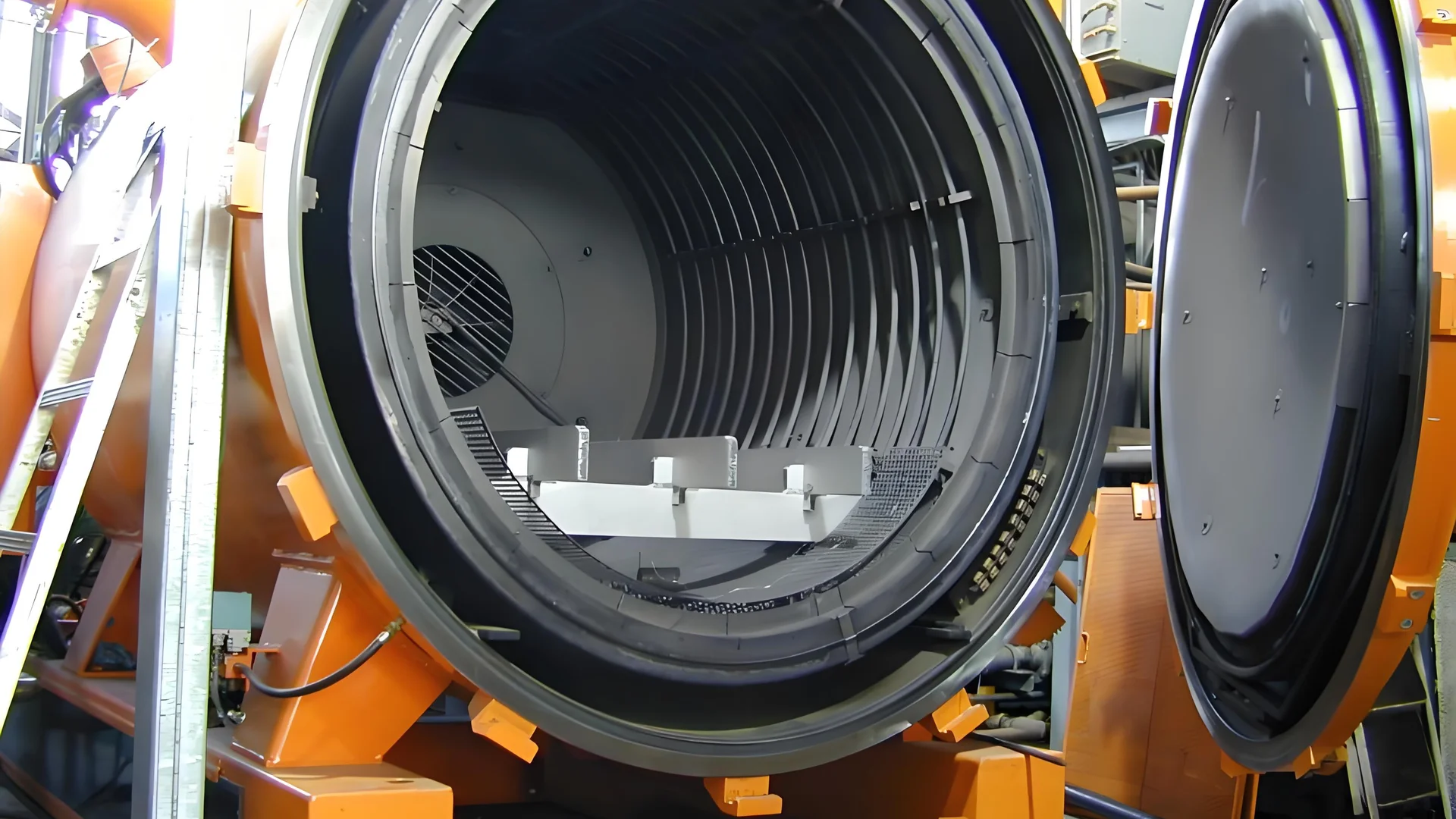
Le rôle de la finition de surface dans l'esthétique et la fonctionnalité
La première fois que j'ai remarqué l'impact d'un moule poli a été inoubliable. C'était comme par magie de voir le matériau en fusion glisser dans chaque coin sans aucun problème. Avec moins de friction, une surface lisse permet à la matière fondue de se déplacer facilement 10 , donnant une finition si uniforme que les défauts disparaissent presque. Regardez par exemple les boîtiers électroniques. Une finition brillante est non seulement élégante, mais agit également comme un bouclier, gardant la saleté à l'écart et son éclat intact pendant longtemps.
Qualité de surface et intégrité structurelle
Rien n’est plus frustrant que de voir un design gâché par des irrégularités ou des points faibles. J'ai découvert, au fil des défis, que ces problèmes provenaient souvent de surfaces de moules rugueuses. En améliorant soigneusement la douceur grâce au polissage, nous maintenons un refroidissement équilibré et protégeons la forme et la résistance du produit. C'est comme placer une armure sur votre produit.
Améliorations dans la conception des portes et des coureurs
Optimisation de la conception des portes :
- Ajustement de l'emplacement du portail : j'ai dû déplacer le portail une fois par les poignées des conteneurs en plastique et wow, quel changement ! Ce petit changement apporte un remplissage uniforme, en particulier dans les zones difficiles à parois minces.
- Ajustements de taille et de nombre : Pour les moules plus grands, augmenter la taille de la porte est très utile. L’ajout de portes supplémentaires dans des pièces complexes peut également faire une énorme différence.
Type de produit | Ajustement du portail |
---|---|
Conteneurs à parois minces | Près des zones minces |
Grands plateaux | Diamètre de porte plus grand |
Des boîtes à outils complexes | Portails auxiliaires supplémentaires |
Améliorations du système de coureurs
Ajustement de la longueur et du diamètre des glissières :
J'ai essayé de raccourcir les glissières pour réduire les pertes de chaleur. Dans les articles plus gros, l’augmentation du diamètre du canal permet à la matière fondue de s’écouler plus facilement.
- Qualité de surface : des patins polis ? Absolument! Ils réduisent considérablement la friction, ce qui signifie moins de problèmes de remplissages incomplets – une véritable bouée de sauvetage en production.
Amélioration de la conception des gaz d'échappement
Mise en œuvre des fentes d'échappement :
les cavités profondes bénéficient des fentes d'échappement, arrêtant l'air emprisonné gênant qui conduit à l'accumulation de pression. Des trous d’échappement bien placés sont très importants pour une évacuation claire de l’air.
Caractéristique du moule | Conception d'échappement |
---|---|
Cavités profondes | Fentes d'échappement |
Surfaces de séparation | Trous d'échappement réguliers |
Se concentrer sur la qualité de la surface du moule, c'est comme perfectionner un art : cela améliore considérablement les résultats des produits. Cette concentration donne non seulement une meilleure apparence aux produits, mais garantit également qu'ils restent fermes et fonctionnent bien. Ceux qui souhaitent en savoir plus devraient explorer d’autres ressources sur l’amélioration des moules 11 pour obtenir des informations précieuses sur l’amélioration des stratégies de production.
L'emplacement de la porte affecte l'efficacité du remplissage du moule.Vrai
Le positionnement des portes à proximité des zones à parois minces garantit un écoulement uniforme de la matière fondue.
La qualité de la surface des coureurs n’a pas d’impact sur le remplissage du moule.FAUX
Des canaux plus lisses réduisent la friction, améliorant ainsi l'efficacité de l'écoulement de la matière fondue.
Conclusion
Cet article explore des solutions efficaces de conception de moules pour résoudre les problèmes de sous-remplissage, en se concentrant sur l'optimisation des portes, l'amélioration du système d'alimentation et la conception des gaz d'échappement pour améliorer l'efficacité et la qualité du produit.
-
Découvrez comment différents placements de portes affectent le remplissage des moules dans des formes complexes, améliorant ainsi vos conceptions. ↩
-
Découvrez pourquoi plusieurs portes peuvent optimiser le remplissage de moules pour des produits complexes. ↩
-
Comprenez comment la conception de l'échappement améliore le remplissage du moule en permettant à l'air emprisonné de s'échapper. ↩
-
Explorez des stratégies de placement et de dimensionnement des portes qui améliorent l'efficacité du remplissage dans des moules complexes. ↩
-
Découvrez des méthodes pour améliorer l'évacuation de l'air des moules, réduisant ainsi les défauts comme le sous-remplissage. ↩
-
Découvrez les avantages d’un système d’échappement bien conçu pour améliorer l’efficacité du moule et la qualité des produits. ↩
-
Comprenez comment l'ajustement de la taille des portes peut améliorer la distribution des matériaux et compléter les stratégies de gaz d'échappement. ↩
-
Ce lien explique comment les propriétés uniques de l'acier respirant améliorent la circulation de l'air et empêchent la rétention d'air. ↩
-
Découvrez comment des matériaux avancés tels que les résines composites optimisent la conception des moules en améliorant la circulation de l'air et la résistance. ↩
-
Découvrez comment des surfaces plus lisses facilitent un écoulement efficace de la matière fondue, réduisant ainsi les défauts. ↩
-
Découvrez des méthodes pour améliorer la qualité des moules, garantissant ainsi des performances produit supérieures. ↩