Haben Sie schon einmal ein Labyrinth von Formen starrten und sich gefragt, wo Sie anfangen sollen? Ich war dort und weiß, wie wichtig das Design von Multi-Cavity-Schimmelpilzdesign ist.
Die wichtigsten Faktoren bei der Gestaltung von Multi-Cavity-Formen sind Materialauswahl, Hohlraumbalance, Kühlsystemdesign und effiziente Ejektionsmethoden, die für eine hohe Produktionseffizienz und eine konsistente Qualität von wesentlicher Bedeutung sind.
Ich erinnere mich an mein erstes Projekt, als ich vor dieser gewaltigen Auswahl an Formen stand und mich überwältigt fühlte, aber dennoch lernbegierig war. Während das Verständnis der Grundlagen mir Selbstvertrauen gab, offenbarte ein tieferes Eintauchen in die einzelnen Elemente Nuancen, an die ich nicht gedacht hatte. Lassen Sie uns diese Faktoren gemeinsam aufschlüsseln und das Potenzial für eine verbesserte Effizienz und Qualität beim Formenbau erschließen.
Die Materialauswahl ist bei der Formenkonstruktion nicht wichtig.FALSCH
Die Materialauswahl ist entscheidend für die Gewährleistung von Haltbarkeit und Funktionalität.
Effiziente Auswurfmethoden steigern die Produktionseffizienz.WAHR
Ein effizienter Auswurf verkürzt die Zykluszeit und steigert die Gesamtproduktionsrate.
- 1. Wie wirkt sich die Materialauswahl auf das Formendesign aus?
- 2. Warum ist das Hohlraumgleichgewicht bei Formen mit mehreren Kavitäten wichtig?
- 3. Warum ist das Design des Kühlsystems für die Effizienz der Form von entscheidender Bedeutung?
- 4. Wie kann ich Auswurfmethoden für die Massenproduktion optimieren?
- 5. Vor welchen Herausforderungen stehen Konstrukteure beim Design von Formen mit mehreren Kavitäten?
- 6. Wie können fortschrittliche CAD-Tools die Präzision der Formenkonstruktion verbessern?
- 7. Abschluss
Wie wirkt sich die Materialauswahl auf das Formendesign aus?
Jeder Formenbauer kennt die Schwierigkeit, die Materialauswahl mit den Designanforderungen in Einklang zu bringen. Es geht nicht nur darum, etwas auszuwählen, das gut aussieht – es geht darum, eine Form herzustellen, die den Test der Zeit besteht und effizient funktioniert.
Die Materialauswahl wirkt sich auf das Formendesign aus, indem sie Haltbarkeit, Kosten und thermische Effizienz beeinflusst und so robuste Formen, eine kostengünstige Produktion und qualitativ hochwertige Produkte gewährleistet.
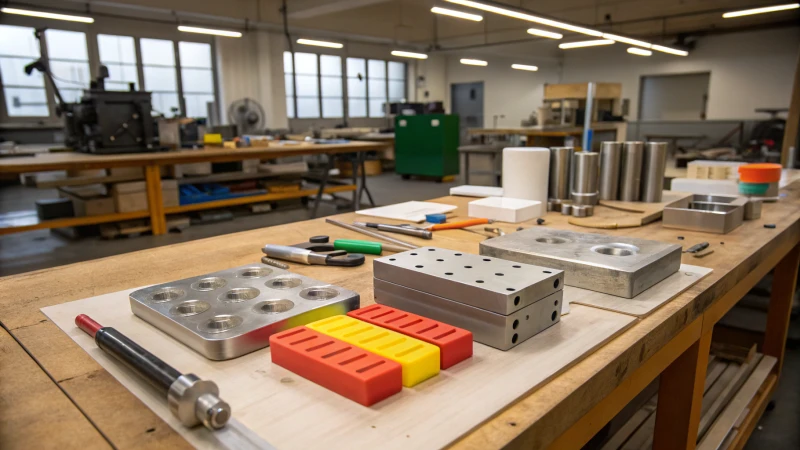
Haltbarkeit und Langlebigkeit
Die Materialauswahl kann die Haltbarkeit und Langlebigkeit eines Projekts erheblich beeinflussen. Ich erinnere mich an das erste Mal, als ich mich für ein Projekt zwischen Edelstahl und Aluminium entscheiden musste. Es war ein bisschen so, als würde man entscheiden, ob man in ein Luxusauto investiert oder sich für etwas Sparsameres, aber weniger Langlebiges entscheidet. Edelstahl schien aufgrund seiner Widerstandsfähigkeit gegen Verschleiß und Korrosion 1 die sichere Wahl für den Langzeitgebrauch zu sein. Allerdings ließen mich die hohen Kosten zögern. Aluminium schien verlockend für schnelle Prototypen zu sein, bei denen das Budget knapp war und die Langlebigkeit keine entscheidende Rolle spielte.
- Edelstahl : Ein Champion in Sachen Korrosionsbeständigkeit, perfekt für Projekte, bei denen Haltbarkeit eine nicht verhandelbare Rolle spielt.
- Aluminium : Meine erste Wahl für Versuchsläufe, wenn wir den Produktionsprozess noch ausprobieren.
Kosteneffizienz
Budgetbeschränkungen sind ein ständiger Begleiter bei der Designarbeit. Ich habe gelernt, dass es sich manchmal lohnt, in Materialien zu investieren, die Langlebigkeit versprechen, insbesondere wenn das Endziel die Massenproduktion ist. Aber es gibt Momente, in denen die Entscheidung für eine günstigere Option wie Aluminium eine kluge Entscheidung ist, insbesondere bei kurzfristigen Projekten.
Material | Kosten | Haltbarkeit |
---|---|---|
Edelstahl | Hoch | Hoch |
Aluminium | Mäßig | Niedrig |
Wärmeleitfähigkeit
Ich erinnere mich an ein Projekt, bei dem die Abkühlzeit unseren Produktionsplan verschlang. Da entdeckte ich die Magie von Beryllium-Kupfer. Seine Wärmeleitfähigkeit war ein entscheidender Faktor, der die Zykluszeiten verkürzte und die Effizienz steigerte – ein echter Lebensretter, wenn die Fristen drohen.
- Beryllium-Kupfer : Ein unbesungener Held im Wärmemanagement, der unsere hektischen Zeitpläne in überschaubare Zeitpläne verwandelt.
Ästhetische und funktionale Anforderungen
Bei meiner Arbeit im Bereich Unterhaltungselektronik 2 ist die ästhetische Verarbeitung ebenso entscheidend wie die Funktionalität. Ich musste Materialien, die ein elegantes Finish bieten, mit solchen kombinieren, die strukturelle Integrität bieten. Es ist, als würde man versuchen, das perfekte Paar Schuhe zu finden – stilvoll und dennoch robust.
Anwendungen aus der Praxis
Wenn ich an ein Automobilprojekt zurückdenke, steht viel auf dem Spiel. Wir brauchten Materialien, die sowohl Belastungen als auch extremen Temperaturen standhalten. Bei der Auswahl geht es hier nicht nur um technische Spezifikationen; Es geht ihnen um die Gewissheit, dass das Endprodukt unter Druck nicht versagt.
Designer wie ich müssen mit diesen Faktoren umgehen und Materialeigenschaften unter einen Hut bringen, um sicherzustellen, dass jede Designentscheidung mit der ultimativen Vision von Qualität und Leistung übereinstimmt. Das Verständnis dieser Nuancen hilft dabei, Produkte herzustellen, die nicht nur auf Langlebigkeit ausgelegt sind, sondern auch die Erwartungen in jeder Hinsicht übertreffen.
Edelstahl ist das kostengünstigste Formmaterial.FALSCH
Edelstahl ist langlebig, aber aufgrund der hohen Kosten nicht wirtschaftlich.
Beryllium-Kupfer verbessert die Kühleffizienz in Formen.WAHR
Die hervorragende Wärmeleitfähigkeit von Berylliumkupfer erhöht die Abkühlgeschwindigkeit.
Warum ist das Hohlraumgleichgewicht bei Formen mit mehreren Kavitäten wichtig?
Haben Sie sich jemals gefragt, warum manche Formteile einfach perfekt sind, während andere ein Albtraum sind? Das Geheimnis liegt oft in der Ausgewogenheit der Kavitäten, insbesondere bei Formen mit mehreren Kavitäten.
Die Kavitätsbalance in Mehrkavitätenwerkzeugen sorgt für eine gleichmäßige Füllung, die für gleichbleibende Qualität und Abmessungen entscheidend ist, Fehler reduziert, Zykluszeiten verkürzt und die Produktionseffizienz steigert.
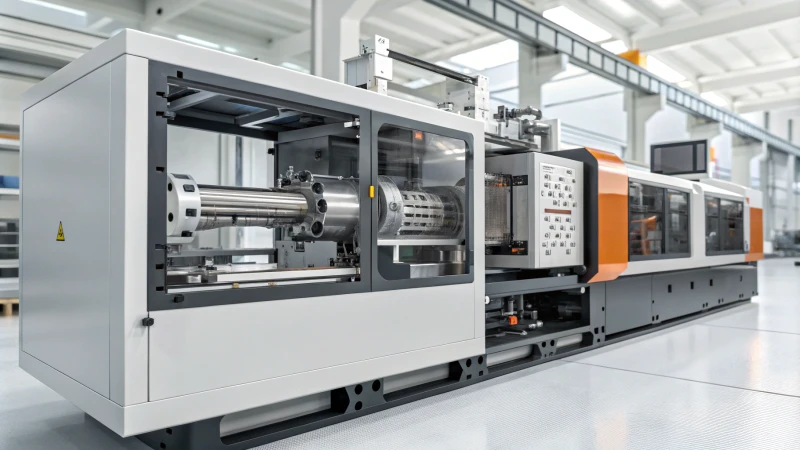
Hohlraumgleichgewicht verstehen
Unter Hohlraumgleichgewicht versteht man die gleichmäßige Verteilung des Materialflusses innerhalb der Form während des Einspritzvorgangs. Bei Formen mit mehreren Kavitäten ist das Erreichen der Kavitätsbalance 3 von entscheidender Bedeutung, um sicherzustellen, dass jede Kavität mit der gleichen Geschwindigkeit gefüllt wird. Diese Gleichmäßigkeit verhindert Probleme wie Verzug oder ungleichmäßige Abkühlung, die die Teilequalität beeinträchtigen können.
Lassen Sie mich Sie auf die Zeit zurückführen, als ich zum ersten Mal die Kraft des Hohlraumgleichgewichts erkannte. Ich war noch mit dem Formenbau beschäftigt, als mir ein älterer Kollege die Grundlagen zeigte. Es war, als würde man einem Meisterkoch zusehen, wie er die Aromen eines komplexen Gerichts ausbalanciert.
Bedeutung im Spritzguss
Die Rolle des Hohlraumgleichgewichts beim Spritzgießen 4 . Es hat direkten Einfluss auf die Qualität und Konsistenz der Formteile. Wenn Kavitäten nicht ausgeglichen sind, füllen sich einige möglicherweise schneller als andere, was zu Abweichungen bei den Teileabmessungen und der Oberflächenbeschaffenheit führt. Diese Inkonsistenzen können zu erhöhten Ausschussraten und einer beeinträchtigten Produktleistung führen.
Ich erinnere mich an das erste Projekt, bei dem ich mich wirklich mit diesem Konzept auseinandersetzen musste. Wir hatten eine Menge Handyhüllen, die immer wieder anders ausfielen, obwohl sie eigentlich identisch sein sollten. Es stellte sich heraus, dass das Problem bei unausgeglichenen Hohlräumen lag.
Vorteile des Erreichens eines Hohlraumgleichgewichts
- Verbesserte Teilequalität : Ausgewogene Hohlräume führen zu einheitlichen Teileabmessungen und verbessern die Gesamtqualität.
- Reduzierte Zykluszeiten : Die richtige Ausgewogenheit der Kavität ermöglicht ein gleichzeitiges Füllen und verkürzt die Zykluszeiten.
- Minimierte Fehler : Durch eine ausgewogene Füllung werden Fehler wie kurze Aufnahmen oder Blitzlichter minimiert.
Vorteile | Einzelheiten |
---|---|
Konsistenz | Einheitliche Teileabmessungen |
Effizienz | Reduzierte Zykluszeiten |
Qualität | Minimierte Mängel wie Verzug und Grat |
Techniken zur Erzielung eines Hohlraumgleichgewichts
Ich habe mehrere Techniken gefunden, die nützlich sind, um dieses schwer fassbare Gleichgewicht zu erreichen:
- Optimierung des Anschnittdesigns : Durch Anpassen der Anschnittgrößen oder -positionen können Sie steuern, wie Material in jede Kavität fließt.
- Strömungssimulationssoftware : Der Einsatz von Strömungssimulationstools 5 kann dabei helfen, Strömungsungleichgewichte vor der eigentlichen Produktion vorherzusagen und auszugleichen.
- Anpassungen des Angusssystems : Eine Änderung des Angusssystems kann dazu beitragen, eine gleichmäßige Materialverteilung zu erreichen.
Herausforderungen bei der Aufrechterhaltung des Hohlraumgleichgewichts
Aber seien wir ehrlich: Es ist leichter gesagt als getan, die Dinge im Gleichgewicht zu halten. Trotz ihrer Bedeutung kann die Aufrechterhaltung des Hohlraumgleichgewichts eine Herausforderung darstellen, da Schwankungen in der Materialviskosität oder Änderungen in der Formtemperatur das Gleichgewicht stören. Für eine optimale Leistung ist es wichtig, diese Variablen kontinuierlich zu überwachen und bei Bedarf anzupassen.
Die Untersuchung dieser Aspekte aus mehreren Perspektiven hilft Formenbauern 6, ihre Prozesse für bessere Ergebnisse zu optimieren.
Die Kavitätsbalance verkürzt die Zykluszeiten beim Spritzgießen.WAHR
Ausgewogene Hohlräume füllen sich gleichzeitig, was die Gesamtzykluszeit verkürzt.
Eine ungleichmäßige Hohlraumfüllung führt zu einheitlichen Teileabmessungen.FALSCH
Eine ungleichmäßige Füllung führt zu Abweichungen bei den Teileabmessungen und nicht bei der Konsistenz.
Warum ist das Design des Kühlsystems für die Effizienz der Form von entscheidender Bedeutung?
Ich erinnere mich an meine ersten Tage im Formenbau; Ich habe schnell gelernt, wie wichtig ein Kühlsystem ist. Es war wie der Herzschlag des gesamten Prozesses und beeinflusste alles von der Geschwindigkeit bis zur Qualität. Lassen Sie uns untersuchen, warum Kühlsysteme so wichtig sind.
Das Design des Kühlsystems ist für die Effizienz der Form von entscheidender Bedeutung, da es Zykluszeiten, Produktqualität und Kosten beeinflusst, Fehler reduziert, die Energieeffizienz verbessert und die Produktivität steigert.
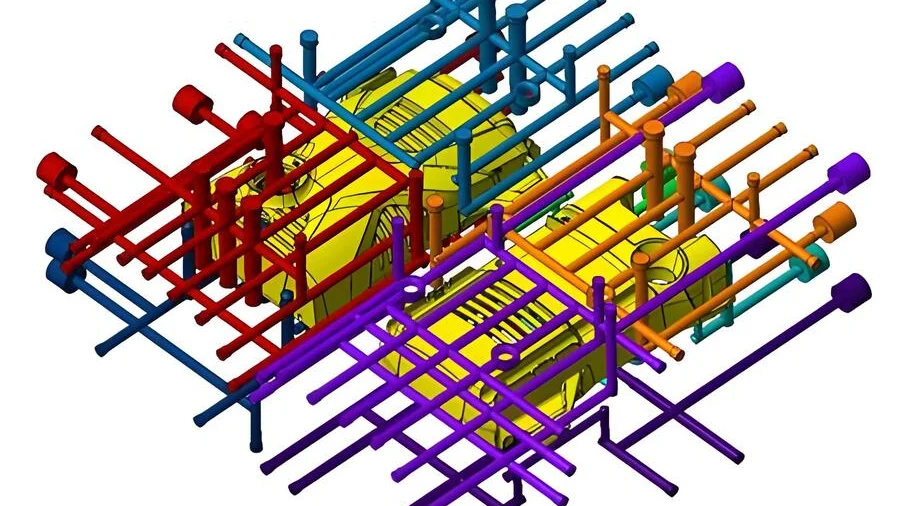
Die Rolle der Kühlung für die Effizienz von Formen
, wie wichtig ein effektives Kühlsystem im Spritzgussprozess . Es steuert die Abkühlgeschwindigkeit der Form, was sich wiederum auf die Zykluszeit und die Produktionseffizienz auswirkt. Wenn die Kühlung nicht ausreichend ist, kann es zu Problemen wie Verformungen, Einfallstellen oder nicht vollständig geformten Teilen kommen. Es ist, als würde man einen Kuchen backen und zu spät merken, dass man vergessen hat, den Ofen vorzuheizen – frustrierend und verschwenderisch.
Wichtige Überlegungen beim Kühldesign
-
Gleichmäßige Kühlung : Meiner Erfahrung nach ist es entscheidend, eine gleichmäßige Kühlung über die gesamte Form zu erreichen. Es gewährleistet die Teileintegrität und vermeidet Probleme wie unterschiedliche Schrumpfung, die zu Verformungen führen kann. Ich hatte einmal ein Projekt, bei dem uns eine ungleichmäßige Kühlung fast aus der Bahn geworfen hätte. Es war ein lehrreicher Moment, den ich nicht vergessen werde.
-
Materialkompatibilität : Verschiedene Materialien haben ihre eigenen thermischen Eigenheiten. Wenn Sie diese verstehen, können Sie ein Kühlsystem entwickeln, das die Wärmeübertragung maximiert. Es erinnert mich an die Kombination eines guten Weins mit dem richtigen Käse – wenn man es falsch macht, geht das Erlebnis ins Leere.
-
Durchflussrate und Druck : Die sorgfältige Kalibrierung der Durchflussrate und des Drucks Ihres Kühlmediums ist der Schlüssel für eine effiziente Wärmeabfuhr.
Parameter | Auswirkungen auf die Effizienz |
---|---|
Durchflussrate | Beeinflusst die Geschwindigkeit der Wärmeabfuhr |
Druck | Beeinflusst die Gleichmäßigkeit der Kühlung |
Wärmeleitfähigkeit | Bestimmt die Kühlwirksamkeit |
Gemeinsame Herausforderungen und Lösungen
-
Hot Spots : Manchmal kühlen bestimmte Bereiche langsamer ab, was zu Defekten führt. Ich habe festgestellt, dass konforme Kühlkanäle fantastisch sind, um gezielte Kühlung dort bereitzustellen, wo sie am meisten benötigt wird, und so diese störenden Hotspots zu reduzieren.
-
Reduzierung der Zykluszeit : Durch die Optimierung des Kühlsystemdesigns 8 habe ich aus erster Hand gesehen, wie Hersteller die Zykluszeiten verkürzen und so den Produktionsdurchsatz erheblich steigern können.
Fortschrittliche Kühltechniken
Durch den Einsatz fortschrittlicher Techniken wie Leitbleche oder Blasen kann die Wärmeabfuhr in komplexen Formen erheblich verbessert werden. Und Technologien wie die konforme Kühlung 9 mittels 3D-Druck ermöglichen maßgeschneiderte Kühllösungen, die perfekt zu komplizierten Geometrien passen.
Das Verständnis dieser Elemente des Kühldesigns kann zu einer verbesserten Formeffizienz 10 , einer höheren Produktqualität und geringeren Produktionskosten führen. Vertrauen Sie mir, sobald Sie diesen Aspekt beherrschen, werden Sie sich fragen, wie Sie jemals ohne ihn ausgekommen sind.
Durch die gleichmäßige Kühlung wird ein Verziehen der Formteile verhindert.WAHR
Eine gleichmäßige Kühlung gewährleistet eine gleichmäßige Schrumpfung und verhindert ein Verziehen.
Eine hohe Durchflussrate verringert die Kühlwirkung.FALSCH
Eine hohe Durchflussrate verbessert die Wärmeabfuhr und verbessert die Kühleffizienz.
Wie kann ich Auswurfmethoden für die Massenproduktion optimieren?
Erinnern Sie sich an die Zeit, als eine kleine Optimierung in der Produktion den Tag rettete? Bei der Optimierung von Auswurfmethoden handelt es sich um eine einfache Änderung, die zu großen Effizienzgewinnen führt.
Optimieren Sie das Auswerfen von Großserien durch die Auswahl geeigneter Systeme, die Aufrechterhaltung der Formbedingungen und den Einsatz fortschrittlicher Technologien. Diese Schritte verbessern die Effizienz, verkürzen die Zykluszeiten und verbessern die Qualität.
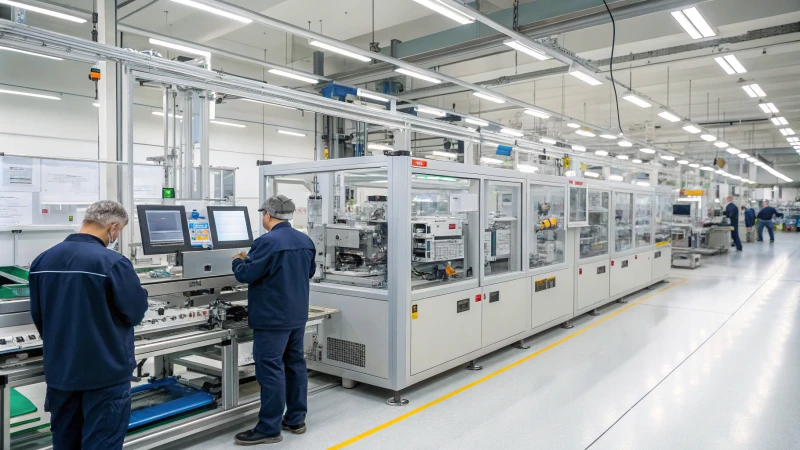
Auswahl des richtigen Auswurfsystems
Als ich anfing, mit der Großserienproduktion zu arbeiten, fühlte sich die Auswahl des richtigen Auswurfsystems wie die Navigation durch ein Labyrinth an. Ich habe schnell gelernt, dass man Materialtyp, Teilekomplexität und Produktionsvolumen berücksichtigen muss. Bei komplizierten Konstruktionen habe ich mich für hydraulische Auswerfer entschieden – sie bieten die nötige Präzision. Ich habe einmal einen umfassenden Leitfaden 11 , der mir wirklich dabei geholfen hat, verschiedene Systeme zu bewerten und das beste System für meine Projekte auszuwählen.
Aufrechterhaltung optimaler Formbedingungen
Lassen Sie mich Ihnen sagen: Die Wartung von Formen ist wie die Pflege eines Oldtimers. Sie müssen bei regelmäßigen Inspektionen sorgfältig vorgehen. Früher habe ich das vernachlässigt, weil ich dachte, es sei geringfügig, bis der Verschleiß der Auswerferstifte zu einem kostspieligen Produktionsstopp führte. Die Implementierung eines vorbeugenden Wartungsplans 12 war ein entscheidender Schritt zur Verlängerung der Werkzeuglebensdauer und zur Steigerung der Leistung.
Nutzung fortschrittlicher Technologien
Fortschrittliche Technologien sind wie das Sahnehäubchen eines gut geölten Produktionsprozesses. Servogetriebene Ejektoren beispielsweise sorgen nicht nur für Energieeffizienz, sondern auch für eine beispiellose Kontrolle. Darüber hinaus war die Integration von Sensoren 13 zur Echtzeitüberwachung für mich von unschätzbarem Wert, um Auswurfprobleme vorherzusehen und zu beheben, bevor sie eskalieren.
Technologie | Vorteile |
---|---|
Servogetrieben | Energieeffiziente und präzise Steuerung |
Sensoren | Echtzeitüberwachung für proaktive Wartung |
Anpassen von Auswerferdesigns
Das Anpassen von Ejektordesigns kann sich wie das Maßschneidern eines Anzugs anfühlen – alles muss genau passen. Ich habe einmal an einem Projekt mit komplexen Formen gearbeitet, und die Verwendung von Multi-Pin-Systemen war entscheidend für eine gleichmäßige Teileentnahme ohne Verzögerung der Zykluszeit. Vielleicht möchten Sie benutzerdefinierte Designtechniken 14 , um die Effizienz Ihrer eigenen Setups zu verbessern.
Analyse der Zykluszeitverkürzung
Die Reduzierung der Zykluszeit ist oft der unbesungene Held der Produktionseffizienz. Ich habe festgestellt, dass eine genaue Untersuchung der Auswurfgeschwindigkeit und des Timings den entscheidenden Unterschied macht. Mit Tools zur Zykluszeitanalyse 15 konnte ich Engpässe identifizieren und Abläufe weiter rationalisieren – jede eingesparte Sekunde fühlte sich wie ein kleiner Sieg an.
Hydraulische Auswerfer bieten eine präzise Steuerung für komplizierte Designs.WAHR
Hydraulische Auswerfer sorgen für Präzision, was bei komplexen Teilen von Vorteil ist.
Regelmäßige Forminspektionen sind für die Auswurfeffizienz nicht erforderlich.FALSCH
Regelmäßige Inspektionen beugen Verschleiß vor und sorgen für einen effizienten Auswurf.
Vor welchen Herausforderungen stehen Konstrukteure beim Design von Formen mit mehreren Kavitäten?
Haben Sie schon einmal versucht, das Design von Formen mit mehreren Kavitäten in Angriff zu nehmen? Es ist wie Jonglieren – eine falsche Bewegung und alles kann auseinanderfallen. Aber die Bewältigung dieser Herausforderungen ist es, was unsere Designs zum Leuchten bringt.
Konstrukteure im Formenbau mit mehreren Kavitäten stehen vor Herausforderungen wie dem Ausgleich des Hohlraumdrucks, der Sicherstellung der Teilekonsistenz und der Bewältigung thermischer Schwankungen. Diese werden durch die Optimierung von Angusssystemen und Kühlkanälen angegangen.
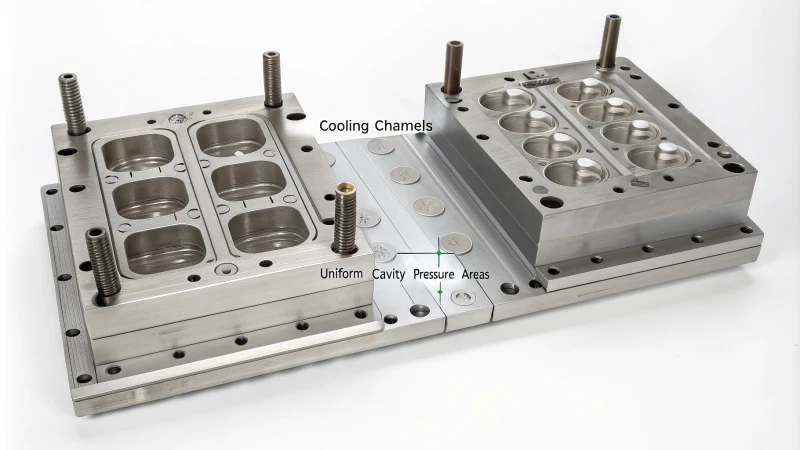
Den gleichmäßigen Hohlraumdruck verstehen
Ich erinnere mich an mein erstes großes Projekt mit Formen mit mehreren Kavitäten. Es fühlte sich an wie eine Gratwanderung. Die Aufrechterhaltung eines gleichmäßigen Hohlraumdrucks war ein ständiger Kampf. Eines Tages starrte ich auf den Bildschirm und fragte mich, warum einige Teile nur leicht abweichend waren. Da wurde es mir klar: Die Läufersysteme 16 waren nicht ausbalanciert. Jeder Hohlraum war einer unterschiedlichen Druckdosis ausgesetzt, was zu Dimensionsproblemen führte. Der Schlüssel lag in der Optimierung der Angusssysteme, um die Schmelze gleichmäßig zu verteilen – etwas, das oft sorgfältige Berechnungen und ein wenig Versuch und Irrtum erfordert.
Sicherstellung einer gleichbleibenden Teilequalität
Konsistenz über Hohlräume hinweg ist nicht nur ein Schlagwort; es ist eine Lebensader. Ich erinnere mich, dass ich stundenlang mit CAD-Tools gearbeitet habe und versucht habe, etwaige Qualitätsmängel bei den Teilen vorherzusehen. Einmal brachte eine leichte Variation der Torgröße alles aus dem Gleichgewicht. Die Lösung? Regelmäßige Wartung und Präzisionsbearbeitung wurden zu meinen neuen besten Freunden. Und vergessen wir nicht die fortschrittlichen CAD-Simulationen 17 , die dabei halfen, potenzielle Probleme vorherzusagen, bevor sie zu kostspieligen Rückschlägen führten.
Bewältigung thermischer Schwankungen
Wärmemanagement kann wie die Zähmung eines wilden Pferdes sein. Ich hatte einmal Probleme mit der Verformung, weil die Abkühlraten nicht in allen Hohlräumen gleich waren. Dadurch habe ich gelernt, wie wichtig es ist, effektive Kühlkanäle 18 . Software für die thermische Analyse wurde unverzichtbar und half mir, potenzielle Hotspots zu erkennen, bevor sie zu Problemen wurden.
Durchflussraten ausgleichen
Der Durchflussausgleich ist vergleichbar mit dem Dirigieren eines Orchesters – alles muss perfekt getimt sein. Ich habe das auf die harte Tour gelernt, als ich mit Mängeln wie kurzen Aufnahmen und Blitzlicht zu kämpfen hatte. Das Angusssystem erforderte eine sorgfältige Konstruktion, damit jeder Hohlraum gleichzeitig gefüllt wurde. Die Verwendung der Formflussanalyse 19 lieferte Erkenntnisse, die für die Anpassung der Durchflussraten zur Gewährleistung einer gleichmäßigen Materialverteilung von unschätzbarem Wert waren.
Herausforderung | Lösungsstrategie |
---|---|
Gleichmäßiger Hohlraumdruck | Läufersysteme optimieren |
Gleichbleibende Teilequalität | Präzise Bearbeitung und Wartung |
Thermische Variationen | Effektive Kühlkanäle |
Durchflussmengenausgleich | Formflussanalyse |
Diese Erfahrungen haben mich gelehrt, dass die Gestaltung von Formen mit mehreren Kavitäten zwar entmutigend sein kann, jede Herausforderung jedoch eine Gelegenheit ist, unser Handwerk zu verfeinern und tadellose Ergebnisse zu erzielen.
Ein ungleichmäßiger Hohlraumdruck wirkt sich auf die Teileabmessungen aus.WAHR
Druckschwankungen können zu inkonsistenten Abmessungen führen und die Qualität beeinträchtigen.
Bei der Formenkonstruktion ist ein Wärmemanagement nicht erforderlich.FALSCH
Ein effektives Wärmemanagement verhindert Defekte wie Verzug und unvollständige Füllung.
Wie können fortschrittliche CAD-Tools die Präzision der Formenkonstruktion verbessern?
Haben Sie sich jemals gefragt, wie die eleganten Designs, auf die wir uns jeden Tag verlassen, zum Leben erwachen? Als Formenbauer habe ich herausgefunden, dass Präzision das A und O ist und dass ich dafür auf fortschrittliche CAD-Tools zurückgreifen muss.
Fortschrittliche CAD-Tools verbessern die Präzision des Formenentwurfs durch genaue Simulationen, ermöglichen komplexe Geometrien, präzise Toleranzen, Zusammenarbeit in Echtzeit und automatisierte Fehlererkennung und rationalisieren so den Designprozess insgesamt.
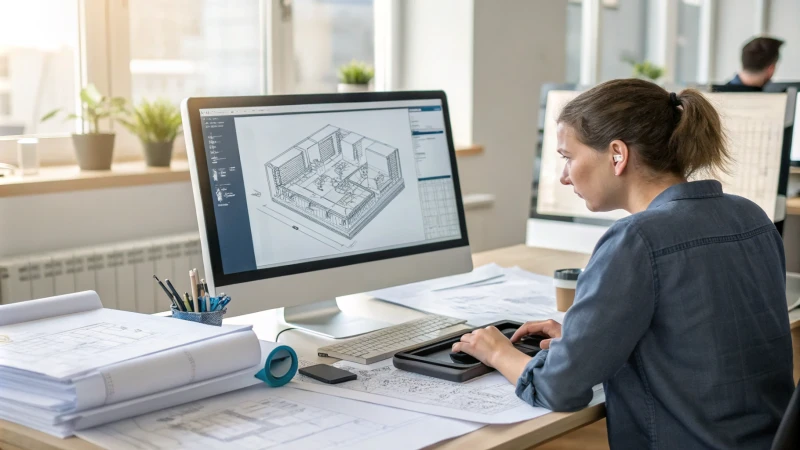
Die Rolle der Simulation bei der Verbesserung der Präzision
Ich erinnere mich an das erste Mal, als ich mir eine Simulation eines Formenentwurfs 20 . Es war, als würde man in eine Kristallkugel blicken – man würde vorhersagen, wie Materialien fließen würden und wo es zu möglichen Störungen kommen könnte. Diese Simulationen haben mir unzählige Stunden erspart und mir ermöglicht, Designs zu optimieren und zu perfektionieren, bevor der erste Prototyp überhaupt geformt wurde. Das Schöne an diesen Tools liegt in ihrer Fähigkeit, Probleme frühzeitig zu erkennen und so sowohl Zeit als auch Materialverschwendung zu sparen.
Vorteile der Simulation | Beschreibung |
---|---|
Frühzeitige Fehlererkennung | Identifizieren Sie Designfehler vor der physischen Prototypenerstellung |
Kosteneffizienz | Reduzieren Sie die mit Nacharbeit und Materialverschwendung verbundenen Kosten |
Zeitersparnis | Beschleunigen Sie die Zeitspanne vom Design bis zur Produktion |
Komplexe Geometrien ermöglichen
Es gab dieses eine Projekt, an dem ich gearbeitet habe, das einige wirklich komplizierte interne Strukturen erforderte. Die Verwendung fortschrittlicher CAD-Tools fühlte sich an, als hätte man einen Zauberstab. Mit diesen Tools konnte ich Entwürfe in 3D visualisieren, sie im Handumdrehen anpassen und sicherstellen, dass jedes kleine Detail genau stimmte. Die Algorithmen bewältigten komplexe Geometrien problemlos, sodass ich mich auf meine Kreativität konzentrieren konnte, ohne mir Gedanken über technische Einschränkungen machen zu müssen.
- Visualisieren und passen Sie Designs in 3D an
- Setzen Sie präzise Maße und Abmessungen um
- Stellen Sie die Konsistenz aller Komponenten sicher
Funktionen für die Zusammenarbeit in Echtzeit
Das Arbeiten über Zeitzonen und Grenzen hinweg gehört jetzt zum Job, und fortschrittliche CAD-Tools machen es nahtlos. Ich kann nicht zählen, wie oft die Zusammenarbeit in Echtzeit den Tag gerettet hat. Stellen Sie sich vor, Sie könnten Designaktualisierungen 21 sofort mit Kollegen auf der ganzen Welt teilen und direkt vor Ort gemeinsam Optimierungen vornehmen. Es reduziert Missverständnisse und stellt sicher, dass wir alle auf dem gleichen Stand sind.
Automatisierte Fehlererkennung und -korrektur
Die automatische Fehlererkennung fühlt sich an, als würde mir ein zusätzliches Paar Augen über die Schulter schauen. Fortschrittliche CAD-Systeme erkennen potenzielle Probleme, die selbst erfahrene Designer wie ich möglicherweise übersehen. Es ist, als hätte man ein Sicherheitsnetz, das kleine Unstimmigkeiten auffängt, bevor sie sich zu größeren Produktionsproblemen ausweiten.
Durch die Integration dieser Funktionen in meinen Arbeitsablauf habe ich aus erster Hand gesehen, wie sie zu qualitativ hochwertigen Produkten und einer höheren Fertigungseffizienz führen. Diese Werkzeuge sind für mein Streben nach Präzision und Exzellenz im Formenbau unverzichtbar geworden.
Fortschrittliche CAD-Tools können das Verhalten von Formen unter Belastung vorhersagen.WAHR
CAD-Simulationen testen Szenarien, um das Verhalten der Form vorherzusagen und so die Designpräzision sicherzustellen.
Die Zusammenarbeit in CAD-Tools in Echtzeit verringert die Designgenauigkeit.FALSCH
Die Zusammenarbeit minimiert Missverständnisse und erhöht die Präzision, indem sie sofortige Aktualisierungen ermöglicht.
Abschluss
Die Beherrschung des Formenbaus mit mehreren Kavitäten erfordert Schlüsselfaktoren wie Materialauswahl, Kavitätenbalance, Kühlsysteme und Auswurfmethoden, um die Produktionseffizienz und Produktqualität zu verbessern.
-
Erkundet, warum Edelstahl wegen seiner Haltbarkeit und Widerstandsfähigkeit gegen Verschleiß und Korrosion bevorzugt wird. ↩
-
Erfahren Sie, welche Materialien für glatte Oberflächen sorgen, die ideal für die Elektronik sind. ↩
-
Entdecken Sie die Grundlagen der Hohlraumbalance und warum sie für die Sicherstellung einer gleichbleibenden Teilequalität von entscheidender Bedeutung ist. ↩
-
Erfahren Sie mehr über die Bedeutung des Hohlraumgleichgewichts für die Verbesserung der Produktkonsistenz und die Reduzierung von Fehlern. ↩
-
Entdecken Sie, wie Strömungssimulationstools dabei helfen, Strömungsungleichgewichte vor der Produktion vorherzusagen und zu korrigieren. ↩
-
Erhalten Sie von erfahrenen Designern Einblicke in Strategien zur effektiven Aufrechterhaltung des Hohlraumgleichgewichts. ↩
-
Entdecken Sie die grundlegenden Aspekte von Spritzguss-Kühlsystemen und deren Auswirkungen auf Herstellungsprozesse. ↩
-
Erfahren Sie mehr über verschiedene Strategien zur Optimierung von Kühlsystemen für eine höhere Effizienz beim Spritzgießen. ↩
-
Entdecken Sie, wie konforme Kühlung die Wärmeabfuhr verbessert und die Zykluszeit in komplexen Formen verkürzt. ↩
-
Verstehen Sie den direkten Zusammenhang zwischen Kühldesign und Verbesserungen der Werkzeugeffizienz. ↩
-
Erfahren Sie mehr über verschiedene Auswurfsysteme, ihre Vorteile und besten Einsatzmöglichkeiten. Dieses Wissen hilft Ihnen bei der Auswahl des richtigen Systems für Ihre Produktionsanforderungen. ↩
-
Verstehen Sie, wie ein vorbeugender Wartungsplan den optimalen Zustand der Formen aufrechterhalten, ihre Lebensdauer verlängern und die Leistung verbessern kann. ↩
-
Entdecken Sie, wie Sensoren eine Echtzeitüberwachung ermöglichen, die zur Aufrechterhaltung der Effizienz und zur Vermeidung potenzieller Auswurfprobleme beiträgt. ↩
-
Finden Sie Techniken zur kundenspezifischen Anpassung von Ejektordesigns, um die Effizienz zu steigern und eine bessere Leistung zu gewährleisten, die auf spezifische Produktionsanforderungen zugeschnitten ist. ↩
-
Erhalten Sie Einblicke in Tools, die dabei helfen, Zykluszeitverkürzungen zu analysieren, Engpässe zu identifizieren und Möglichkeiten zur Rationalisierung von Abläufen zu erkennen. ↩
-
Entdecken Sie Strategien zur Optimierung von Angusssystemen, die für die Sicherstellung einer gleichmäßigen Schmelzeverteilung und die Vermeidung von Druckabfallproblemen in Formen mit mehreren Kavitäten von entscheidender Bedeutung sind. ↩
-
Entdecken Sie die Vorteile der Verwendung fortschrittlicher CAD-Tools zur Simulation und Vorhersage potenzieller Probleme bei der Formenkonstruktion, bevor sie auftreten. ↩
-
Erfahren Sie, wie ein effektives Kühlkanaldesign eine gleichmäßige Temperaturverteilung gewährleistet, die für die Bewältigung thermischer Schwankungen in Formen von entscheidender Bedeutung ist. ↩
-
Verstehen Sie die Bedeutung der Formflussanalyse für die Vorhersage und Anpassung der Flussraten für eine optimale Materialverteilung. ↩
-
Entdecken Sie, wie CAD-Simulationen dabei helfen, Probleme bei der Formenkonstruktion frühzeitig vorherzusagen und so Zeit und Ressourcen zu sparen. ↩
-
Entdecken Sie, wie die Zusammenarbeit in CAD-Software in Echtzeit die Teamarbeit und die Designpräzision verbessert. ↩