All Posts
blog & article
read our latest newsletter
Whether you’re curious about material selection, product design, mold design, mold making and injection molding, feel free to ask us anything. Our team is ready to provide the guidance and insights you need.
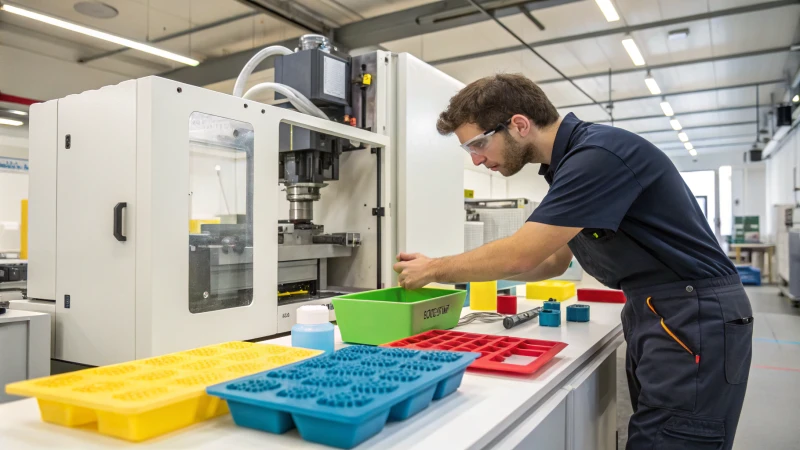
How Can You Minimize the Negative Impact of Injection Speed on the Tensile Strength of Plastic Products?
This article explores how to minimize the negative impact of injection speed on the tensile strength of plastic products. Key strategies include optimizing injection speed parameters, adjusting mold structure, and implementing effective material pretreatment and post-treatment processes. By fine-tuning injection ...
OPTIMIZATION

How Does Injection Speed Impact the Tensile Strength of Plastic Products?
This article explores how injection speed affects the tensile strength of plastic products. Moderate speeds (80-120mm/s for polyamide) improve material density and molecular chain orientation, enhancing strength. Conversely, excessive speeds create internal residual stress and surface defects, while low speeds ...
DEVELOPMENT
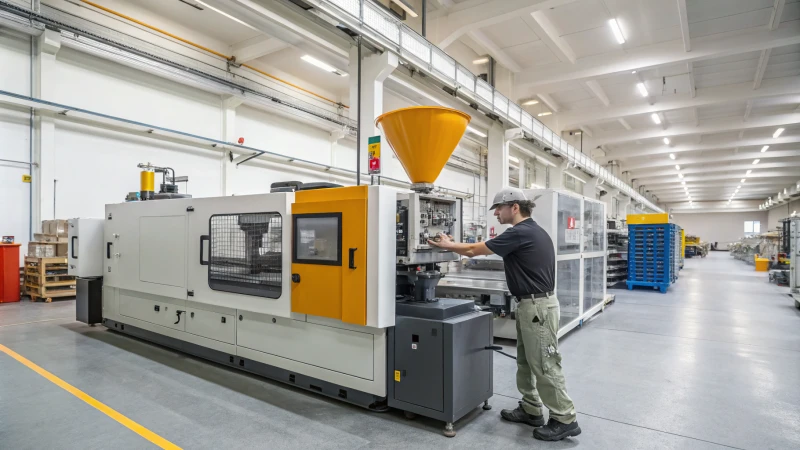
How Can You Adjust Injection Speed to Optimize Impact Strength?
This article explores how adjusting injection speed in the molding process can optimize impact strength. It emphasizes the importance of understanding material properties—differentiating between crystalline and non-crystalline plastics—and adapting speeds accordingly. For crystalline plastics like polypropylene, a controlled speed of ...
OPTIMIZATION
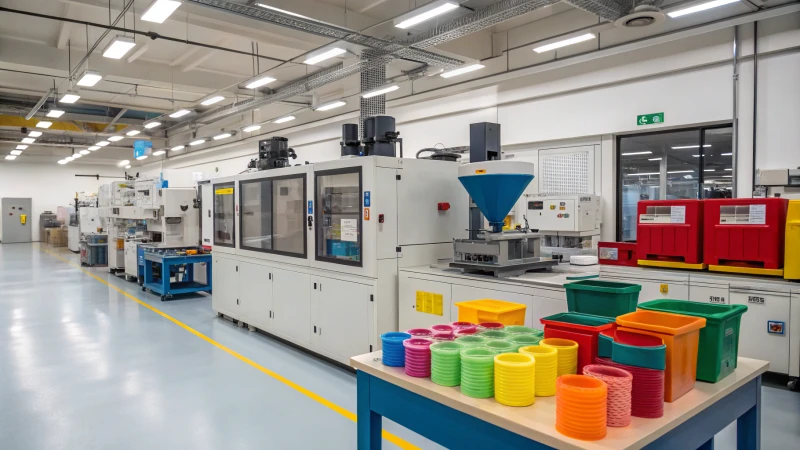
How Does Injection Speed Influence the Mechanical Properties of Plastic Products?
This article explores how injection speed affects the mechanical properties of plastic products, including tensile strength, impact resistance, and bending strength. It emphasizes the importance of maintaining optimal injection speeds for different materials to ensure even filling and proper crystallization. ...
DEVELOPMENT
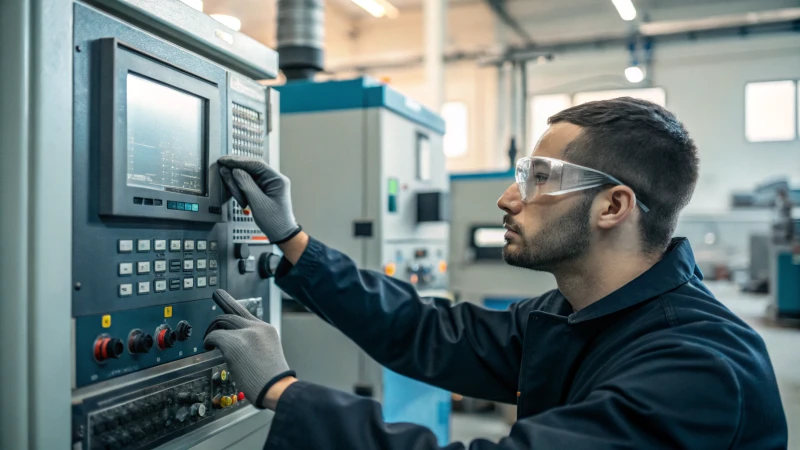
What is the Best Way to Determine the Most Suitable Injection Speed?
This article explores how to determine the most suitable injection speed in plastic molding. It emphasizes the importance of material properties such as viscosity, thermal conductivity, and density in setting initial speed ranges. The piece discusses trial molds and adjustments ...
DEVELOPMENT
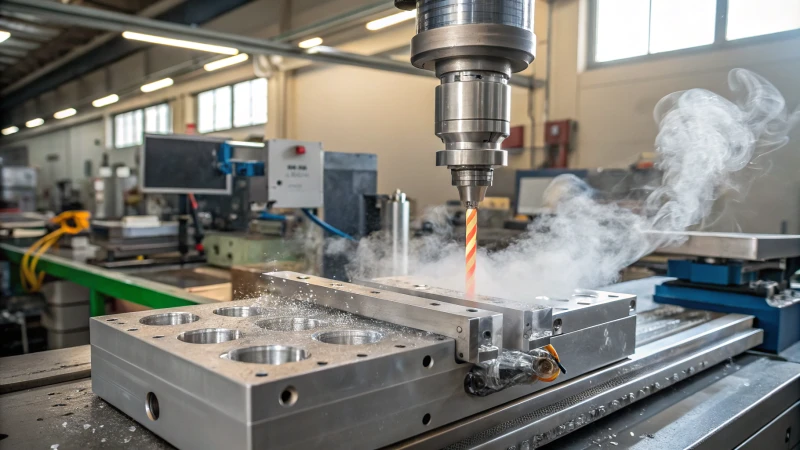
How Does Reducing Injection Mold Speed Enhance Product Quality?
Lowering the speed of injection molding significantly improves product quality. It reduces surface defects like flow marks and silver streaks while enhancing internal stability and density. Slower speeds allow for better replication of intricate textures and patterns, ensuring a smooth ...
MANUFACTURING
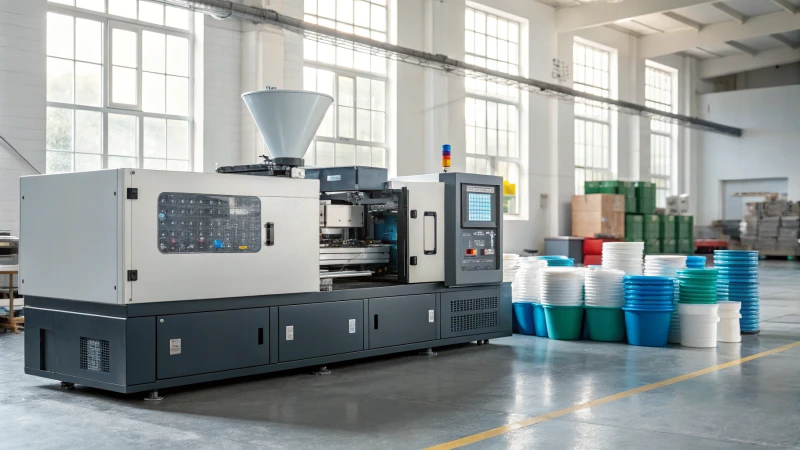
What Factors Determine the Best Injection Speed?
Choosing the right injection speed is crucial for optimizing plastic molding processes. Factors such as material characteristics (fluidity and heat sensitivity), mold design (gate size and runner system), and specific product requirements all influence the ideal injection speed. For instance, ...
MANUFACTURING
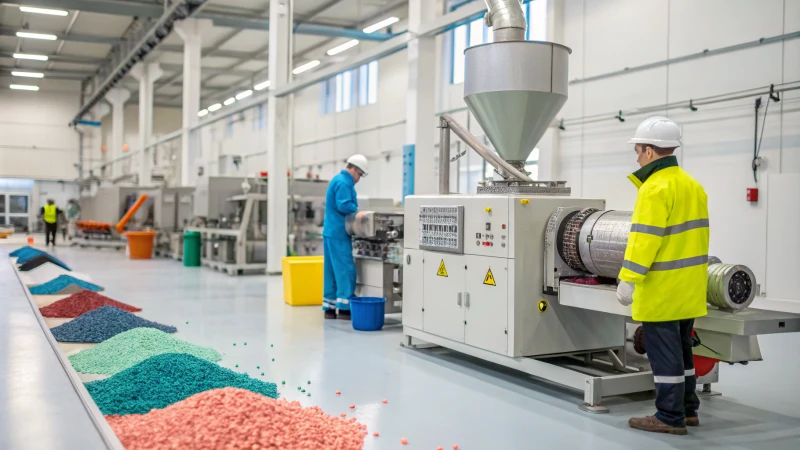
How Does Injection Pressure Impact the Quality of Injection Molds?
This article explores the critical role of injection pressure in molding processes, highlighting its impact on product quality, internal structure, and mold longevity. Properly adjusted pressure ensures complete filling of molds, enhances material properties, and extends the service life of ...
Quality Inspection
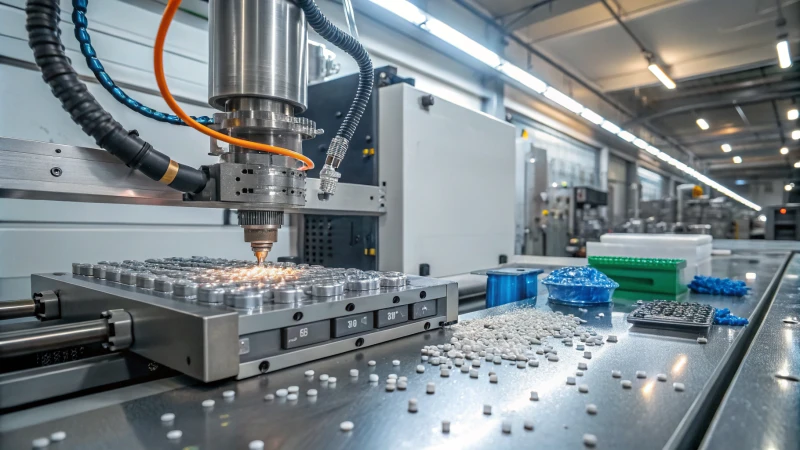
How is Injection Mold Injection Pressure Determined?
This article explores how injection mold pressure is determined by various factors including material characteristics, mold structure, and product requirements. Key aspects such as fluidity of plastics like polyethylene (PE) and polycarbonate (PC), gate size, runner system design, and the ...
MANUFACTURING
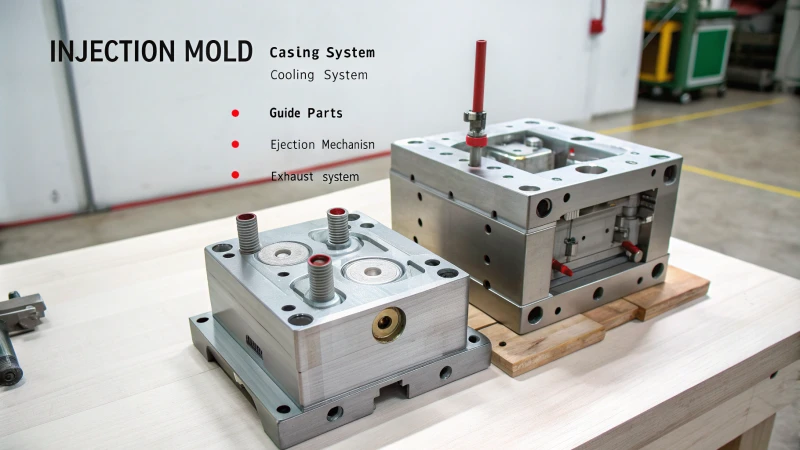
What Are the Functions of Each Part of an Injection Mold?
Injection molds consist of various critical components that work together to produce high-quality plastic parts. This article delves into the functions of each part: the casting system guides melted plastic; molded parts shape products; guide parts ensure precise alignment; ejection ...
DESIGN
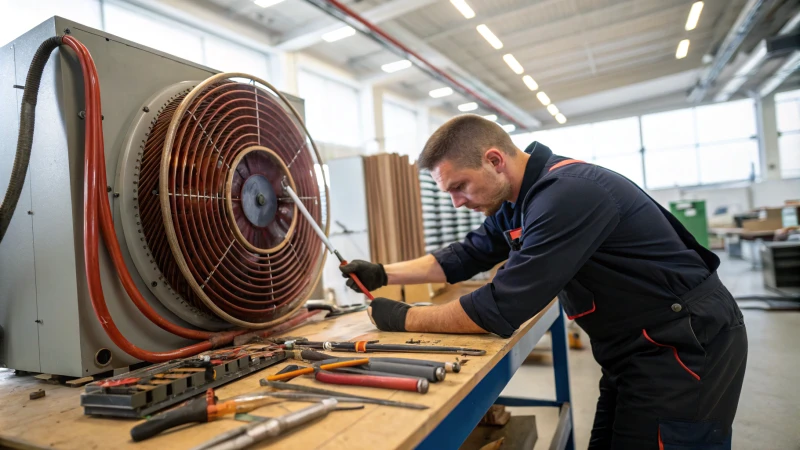
What Key Details Should You Consider When Installing a Heating Ring?
Installing a heating ring on machinery demands precision and attention to detail. Key steps include inspecting the heating coil and barrel for damage, ensuring specifications match, achieving a snug fit for optimal heat transfer, securing electrical connections properly, and conducting ...
OPTIMIZATION
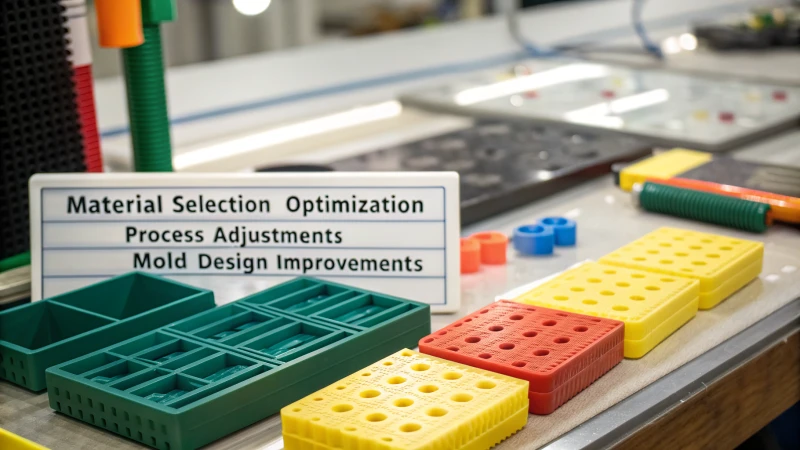
How Can Product Design Optimization Solve Warpage Defects in Injection Molded Parts?
This article explores how product design optimization can address warpage defects in injection molded parts. Key strategies include maintaining uniform wall thickness to ensure even cooling, strategically designing ribs to enhance strength without increasing thickness, and simplifying complex shapes to ...
OPTIMIZATION
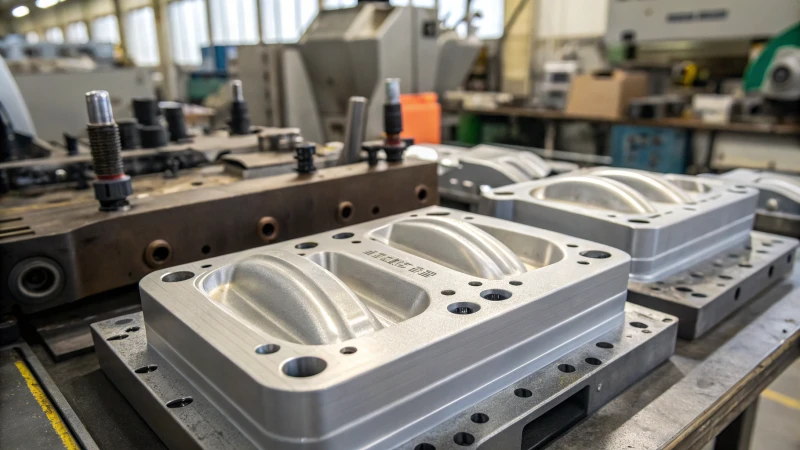
How Do Warpage Defects Affect the Performance of Injection Molded Parts?
Warpage defects significantly impact the performance of injection molded parts by altering their dimensional accuracy, mechanical properties, and appearance. These issues arise from uneven cooling, material shrinkage, and poor mold design. Warped components can lead to assembly challenges and functional ...
OPTIMIZATION
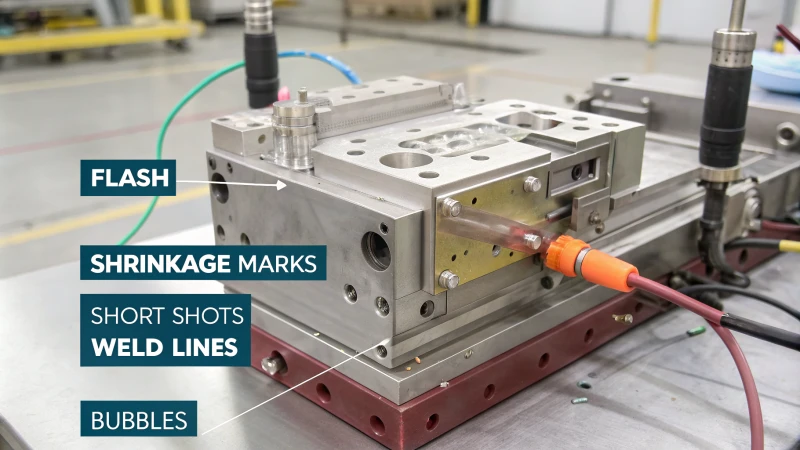
What Are the Most Common Defects in Injection Molding?
Injection molding can lead to various defects that affect product quality and efficiency. Common issues include flash caused by excessive pressure, shrinkage marks from uneven cooling, weld marks from flow convergence, bubbles due to moisture or poor venting, and short ...
Quality Inspection
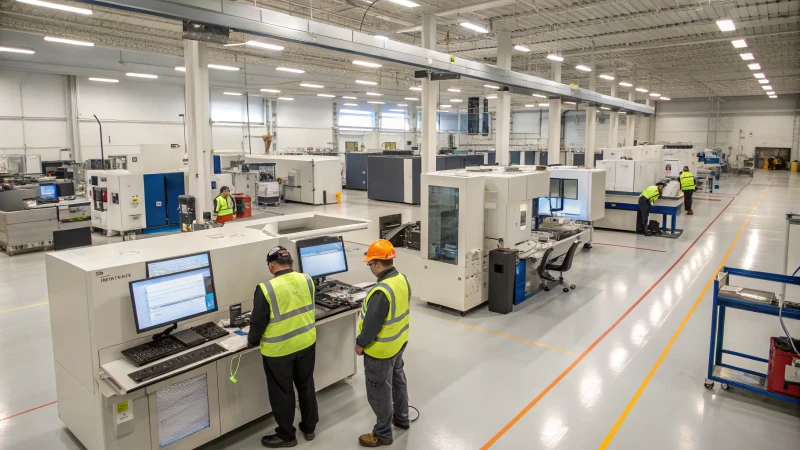
How Can You Integrate Mold Design Standardization with Personalized Design?
This article explores how to effectively integrate mold design standardization with personalized elements. It emphasizes the importance of understanding product demand, developing a strategic design plan, and utilizing parametric design software to achieve a balance between creativity and efficiency. By ...
DESIGN
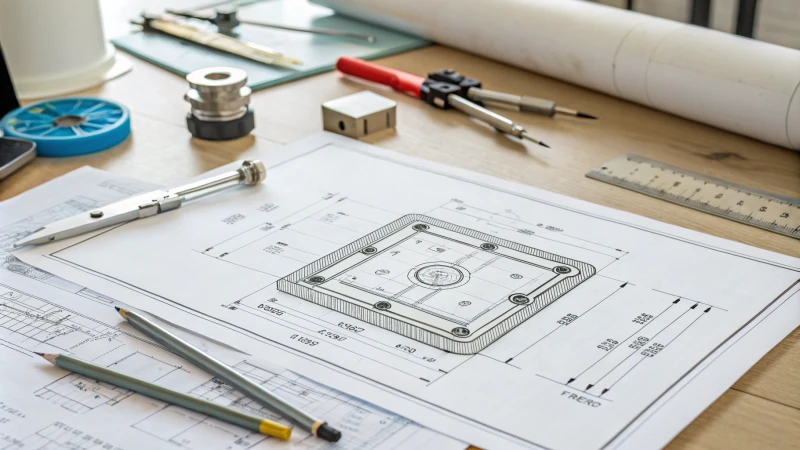
How Can You Effectively Minimize Shortcomings in Mold Design Standardization?
The article explores how to effectively minimize shortcomings in mold design standardization by encouraging innovation through incentive mechanisms, applying flexible standards, optimizing initial investment strategies, and enhancing adaptability to updates. It emphasizes the importance of collaboration among industry players to ...
DESIGN
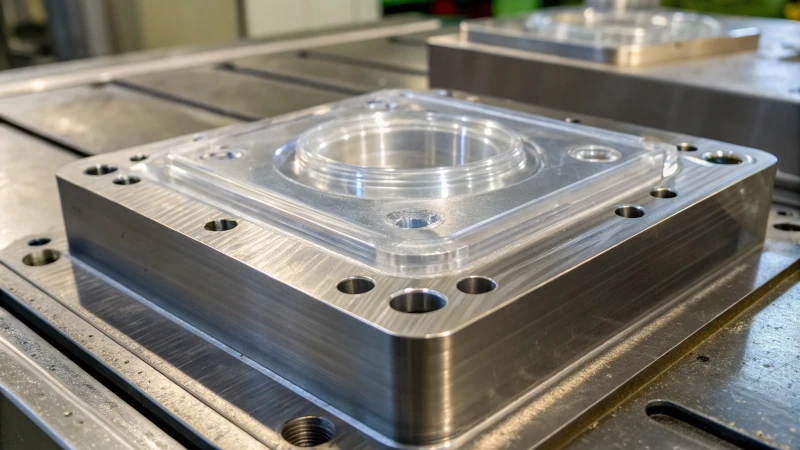
How Does the Parting Line Affect the Precision of Injection Molded Products?
This article explores the critical role of parting lines in injection molding, emphasizing their influence on dimensional accuracy, shape integrity, and assembly position. Poorly managed parting lines can lead to issues such as flash formation, uneven surfaces, and misalignment in ...
MANUFACTURING
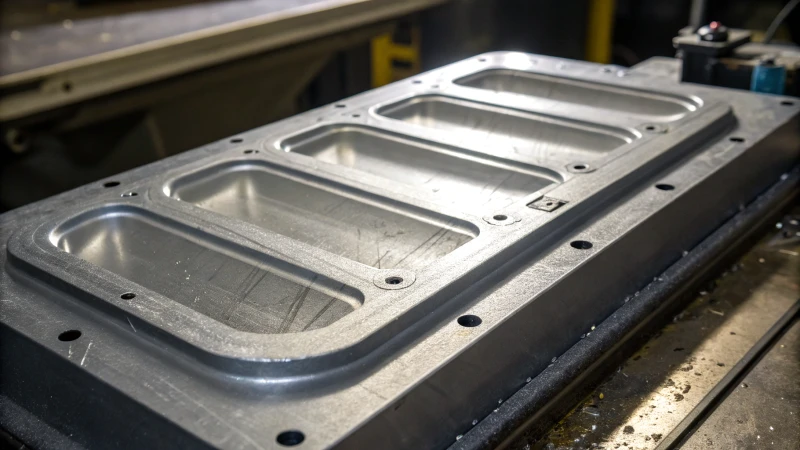
What Does the ‘Parting Line’ Mean in Injection Molding?
In injection molding, the parting line is where mold sections meet, significantly impacting both the aesthetic and structural qualities of the final product. Proper placement of this line is essential to avoid visible marks and stress points that can weaken ...
DESIGN
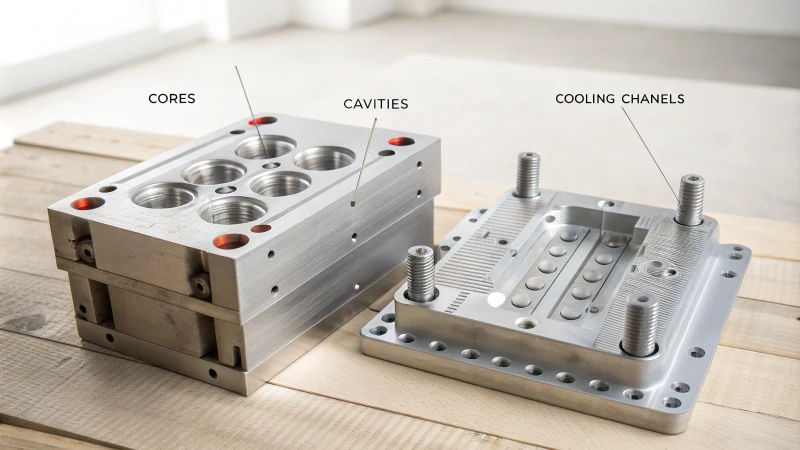
How Does Standardization Impact Injection Mold Design?
This article explores how standardization impacts injection mold design by establishing common rules for dimensions, specifications, and materials. It highlights the benefits of consistency in mold components such as templates, gates, runners, demolding mechanisms, and cooling systems. By following standardized ...
DESIGN
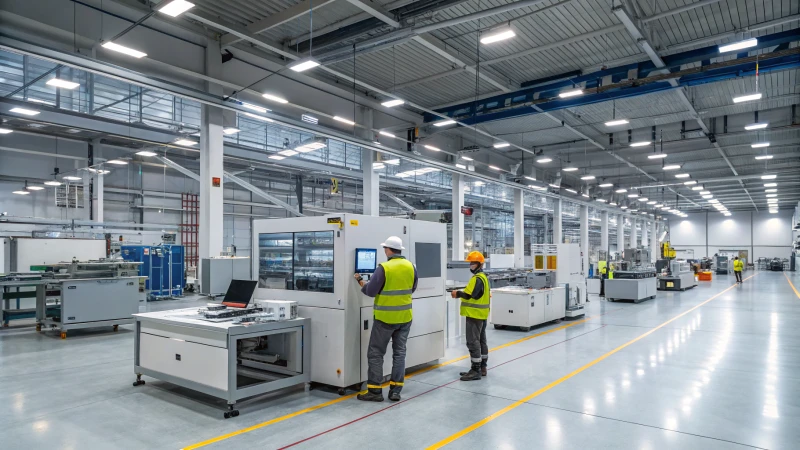
What Are the Key Advantages of Mold Design Standardization?
Mold design standardization streamlines the manufacturing process by using consistent parts and methods. This approach drastically shortens design cycles from weeks to days, boosts productivity, lowers production costs through bulk purchasing, and enhances product quality with reliable components. Standardized designs ...
DESIGN
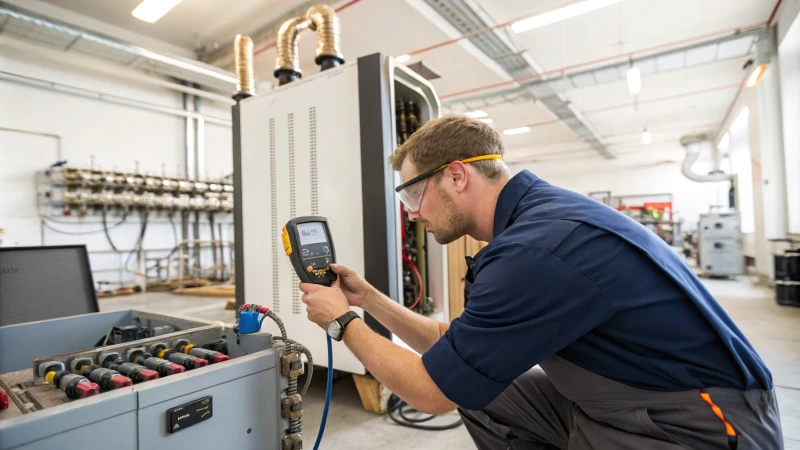
How Do You Accurately Measure a Machine’s Heating Capacity?
Measuring a machine's heating capacity involves careful preparation and execution. Key steps include selecting appropriate tools like calorimeters and infrared thermometers, ensuring a safe environment, making precise connections, and documenting results meticulously. Proper calibration of instruments and attention to environmental ...
Quality Inspection

What Are the Key Steps to Becoming a Successful Mold Designer?
Becoming a successful mold designer requires a blend of theoretical knowledge, practical experience, and strong communication skills. Start by mastering the basics of mold design, including understanding different types of molds such as injection and stamping. Gain hands-on experience through ...
DEVELOPMENT
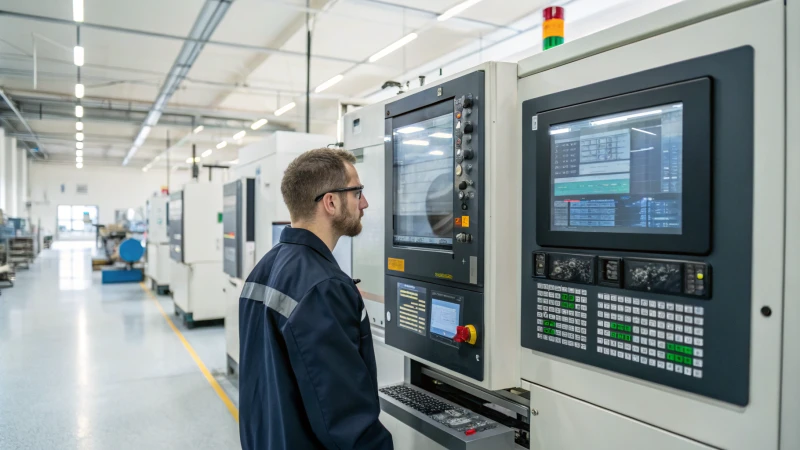
What Is the Service Life of an Injection Molding Machine’s Heating Coil?
The lifespan of heating coils in injection molding machines ranges from 5 to 10 years, depending on factors such as environmental conditions, operating temperatures, material quality, and maintenance routines. Ceramic coils generally outlast stainless steel ones. High humidity and corrosive ...
MANUFACTURING

How Do Injection Molding Machines Achieve Temperature Control in Their Heating Systems?
Temperature control is crucial in injection molding, acting as the heartbeat of quality production. This process relies on a combination of temperature sensors, controllers, and PID algorithms to maintain steady and precise heat levels. Sensors monitor real-time temperatures in various ...
MANUFACTURING
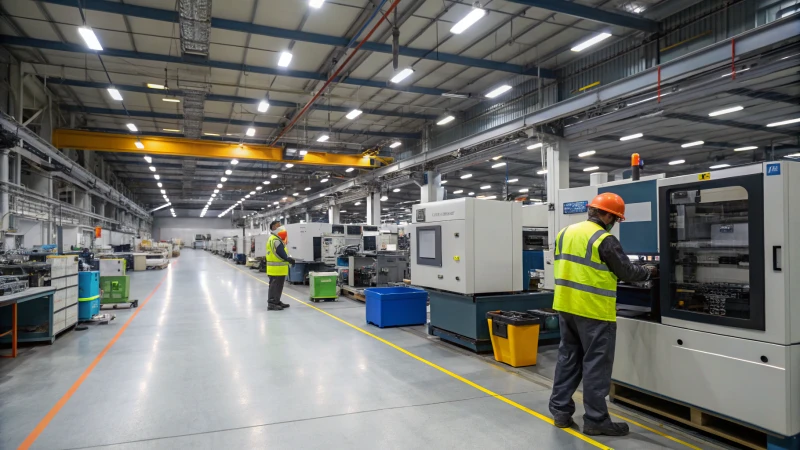
How Does Injection Molding Melt Raw Materials?
This article explores the intricate process of injection molding, focusing on how heating systems and shear heat work together to melt raw materials like plastics. The heating rings in the machine's barrel provide controlled temperatures that soften thermoplastics, while the ...
MANUFACTURING
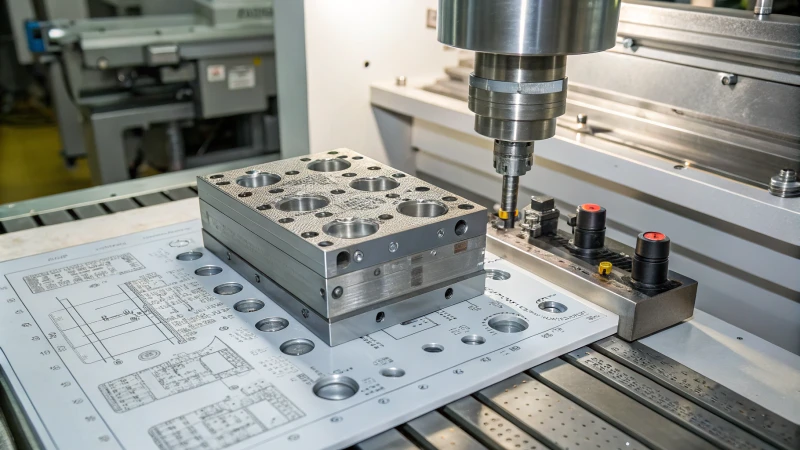
What Are the Best Methods to Determine Gate Location and Size?
This article explores the best methods for determining gate location and size in injection molding. Proper gate placement is essential for achieving optimal melt flow balance, which directly impacts product quality by preventing defects such as air pockets and uneven ...
OPTIMIZATION

What Is the Best Gate Type for Optimizing Plastic Melt Fluidity?
Selecting the appropriate gate type in injection molding significantly influences the flow of molten plastic, impacting product quality and manufacturing efficiency. High viscosity plastics benefit from pin gates that increase shear heat, while low viscosity materials like polyethylene are better ...
OPTIMIZATION
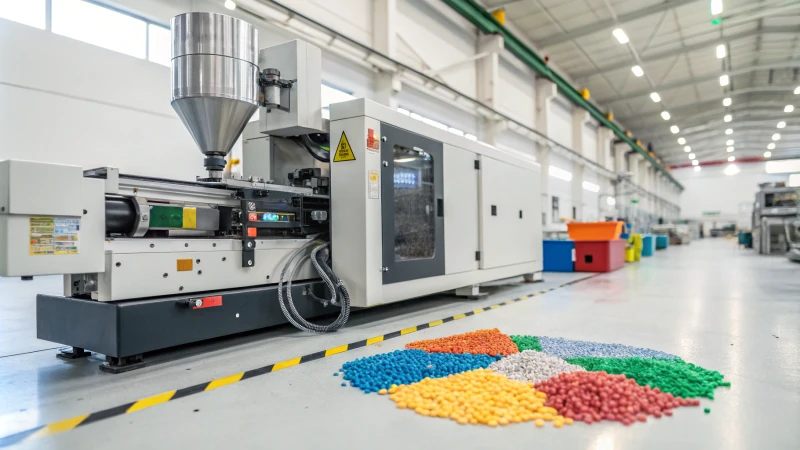
What Are the Best Methods to Improve Plastic Melt Fluidity at the Gate?
This article explores effective methods to improve plastic melt fluidity during injection molding. Key strategies include optimizing gate design, controlling molding parameters such as temperature and pressure, selecting suitable high-fluidity materials like polyethylene and polypropylene, and incorporating additives such as ...
OPTIMIZATION
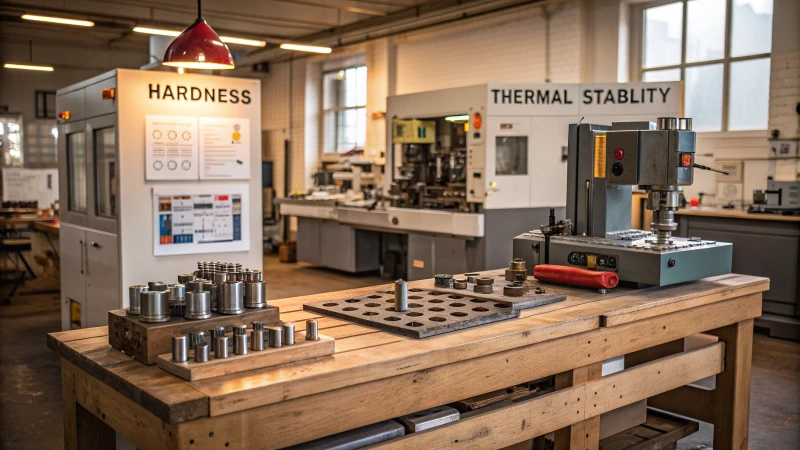
How Can You Choose the Right Processing Technology for Different Mold Material Characteristics?
Selecting appropriate processing technology for various mold materials is crucial for achieving optimal results. Factors such as material hardness, toughness, ductility, and thermal stability significantly influence tool selection and processing methods. High-hardness materials like H13 require carbide tools for effective ...
OPTIMIZATION
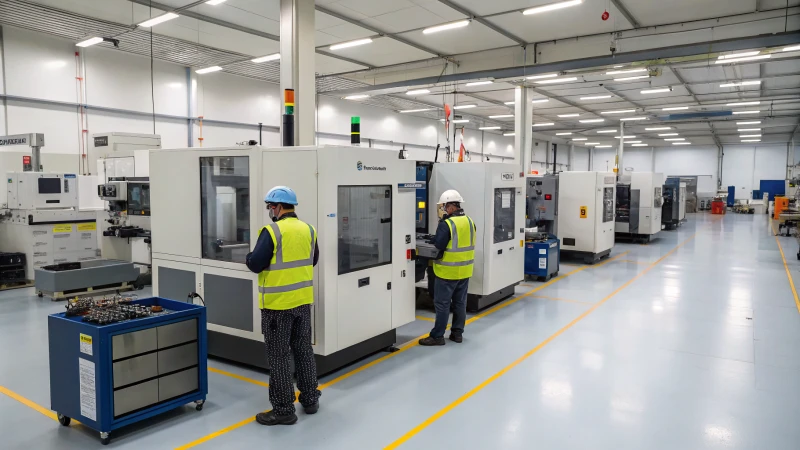
What Are the Key Factors Influencing Mold Processing Technology Choices?
Choosing the right mold processing technology is essential for manufacturing success. Factors such as design complexity, material characteristics, production requirements, available equipment, technician expertise, and budget constraints play a critical role in decision-making. Understanding how these elements interact helps manufacturers ...
MANUFACTURING