In the beginning of my journey into plastic manufacturing, I quickly saw that injection speed goes beyond a machine setting. It’s a fine dance. This dance influences the strength of plastic. Yes, it’s very important.
Injection speed affects the strength of plastic products. It changes material density, molecular orientation and leftover stress. Moderate speed increases density and orientation. This increases strength. Very fast or slow speeds probably create defects and weaken the product. Defects weaken the product.
Thinking about my early days in the mold industry, a project comes to mind where getting the injection speed just right felt like solving a tricky puzzle. Finding this balance is very important to having high-quality products.
Moderate injection speeds let the plastic melt fill molds evenly, similar to getting pancake batter smooth without lumps. This results in a tighter internal structure. It is crucial because it helps handle stress and may increase tensile strength. However, if the speed is too high, it feels like driving too fast on a rough road. Problems such as residual stress, microcracks and damaged molecular chains could appear. Conversely, if the speed is too low, it’s like running out of steam before reaching your destination. Gaps and not enough filling can really hurt strength.
Anyone like me, spending long hours adjusting these settings, knows how important these details are. They help optimize production and make sure every product withstands time. It must endure.
Moderate injection speeds enhance tensile strength.True
Moderate speeds improve material density and molecular orientation.
High injection speeds reduce residual stress in plastics.False
High speeds increase residual stress, weakening the product.
What Happens When Injection Speed is Too High?
Have you ever felt the excitement of testing boundaries, only to discover you’ve overstepped? That is exactly what occurs when injection speed in molding shoots up too high.
High injection speed leads to internal stress. This speed harms the molecular chain structure. It also causes surface defects. These issues lower the quality of plastic products and reduce their tensile strength. Quality suffers. Tensile strength drops.
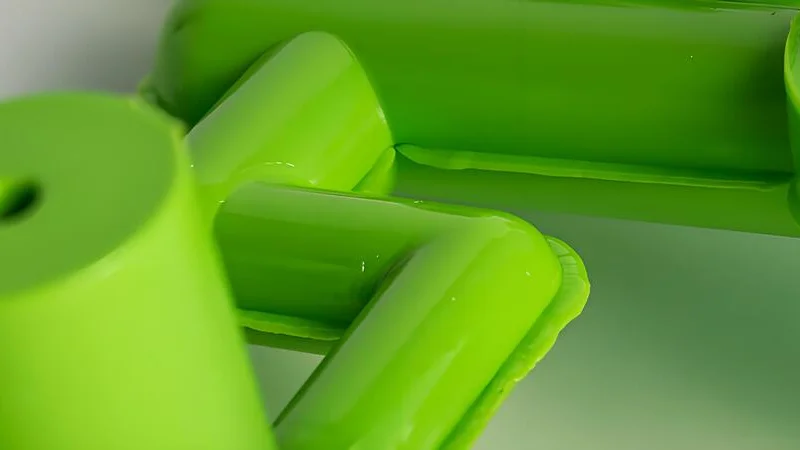
Internal Residual Stress Formation
Rushing to bake a cake often causes cracks. Fast movements in plastic molding do the same. Plastic pushes through a mold very quickly, leading to stress inside. Stress builds up at high speeds like 200mm/s. Pressure acts like a cooker ready to explode. This results in tiny cracks within. Weakened products resemble my broken cake. Simply put, cracks form, weakening items.
When injection speed surpasses optimal levels, the plastic melt experiences significant shear forces within the mold cavity. For instance, speeds over 200mm/s can convert these forces into internal residual stress. This stress concentration1 is detrimental as it fosters microcracks that weaken the product under tensile force.
Molecular Chain Structure Damage
Bubble gum stretches until it breaks. Similar damage occurs in plastic at high speeds. Speeds over 250mm/s ruin molecular chains. Chains get pulled or snap, losing their strength. Keeping speed controlled maintains these chains, just like not stretching gum too far.
Fast injection speeds, particularly those exceeding 250mm/s, can overstretch or even break long-chain molecular structures like those in thermoplastic elastomers. This disruption prevents molecular chains from effectively transmitting external forces, diminishing tensile strength. Proper injection speed2 settings ensure these structures remain intact.
Surface Defects
Rushed painting creates streaks; quick plastic injection does likewise. Over 300mm/s causes marks on surfaces where weak spots appear, leading to cracks.
Rapid injection speeds often lead to unstable flow states, resulting in surface defects such as flow marks or silver streaks. At speeds beyond 300mm/s, these imperfections are prominent and act as stress concentration areas.
Speed (mm/s) | Potential Issue |
---|---|
>200 | Internal residual stress |
>250 | Molecular chain damage |
>300 | Surface defects (e.g., flow marks) |
Importance of Moderate Injection Speed
Moderate speeds resemble perfect cake baking – balanced heat and time; within 80-120mm/s polyamide molds well.
Material smoothly fits the mold forming a dense core where stress travels efficiently inside—watching this is fascinating! Chains align strengthening the material perfectly aligned like layered croissants adding strength.
Moderate speeds enhance material density by allowing even mold cavity filling—for example polyamide injected at 80-120mm/s achieves a denser structure that effectively transmits stress Additionally molecular orientation3 benefits from regulated speeds improving tensile strength by aligning molecular chains along the flow direction.
Balancing speed and quality is important in molding tailoring process ensures better results think of it as customizing recipe for good baking reducing defects improving product performance balancing ensures success.
Injection speed over 200mm/s causes residual stress.True
Speeds above 200mm/s lead to significant shear forces causing stress.
Moderate speeds reduce surface defects in molded plastics.True
Controlled speeds ensure even mold filling, minimizing defects.
How does low injection speed affect product quality?
I remember when problems with injection speeds appeared in molding. Product quality changed a lot. This really opened my eyes. Injection speeds influence many things, like the way materials move and how strong the finished item is. They truly have a big effect.
Slow injection speed during molding often causes gaps because the material does not fill properly. These gaps transform into points where stress gathers. This weakens the material’s tensile strength. Defects occur, like uneven alignment of molecules. This is a common issue.
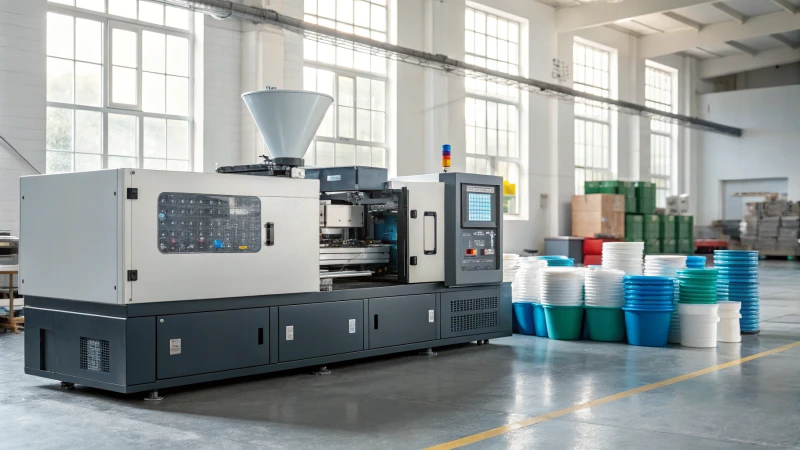
Insufficient Filling: The Domino Effect
Slow injection speeds create big issues, especially with thick-walled items. Picture trying to fill a mold with slow, sticky plastic. It doesn’t fit into all the small spaces. If speed falls under 40mm/s, the filling may be incomplete. These gaps not only look bad; they also become stress points. They weaken the product’s tensile strength4 and really increase the risk of damage.
Injection Speed | Outcome |
---|---|
< 40mm/s | Insufficient filling |
Molecular Chain Orientation and Crystallization
It’s interesting how a small thing like injection speed impacts molecular orientation. Low speeds below 60mm/s can disrupt crystallinity in crystalline plastics like polyoxymethylene. This leads to uneven crystals. Non-crystalline plastics show irregular molecular chains at these speeds, lowering tensile strength5. The structure struggles to resist outside forces. It really struggles.
Balancing Injection Speed
Finding the right injection speed is like tuning an instrument; everything aligns beautifully when done right. Moderate speeds, around 80-120mm/s for polyamide, improve density and optimize molecular chain orientation. This balance boosts durability and really enhances quality.
For those aiming for perfection in molded products, adapting this knowledge helps reduce defects. Dive into expert insights6 for a comprehensive guide.
Low injection speed causes incomplete mold filling.True
Speeds below 40mm/s can lead to insufficient filling, creating gaps.
High injection speeds reduce crystallinity in plastics.False
Low speeds, not high, affect crystallinity by causing uneven crystal morphology.
Why is Moderate Injection Speed Optimal for Strength?
Do you ever ask yourself why injection molding speed is important? It’s not only about how fast it is. It finds the perfect balance for strength and longevity.
A moderate injection speed is vital for strengthening plastic items. It optimizes material density and arranges molecular chains. This reduces defects caused by extreme speeds. The balance also lowers leftover stress. Durable and reliable molded products result from this. Reliable products are the outcome.
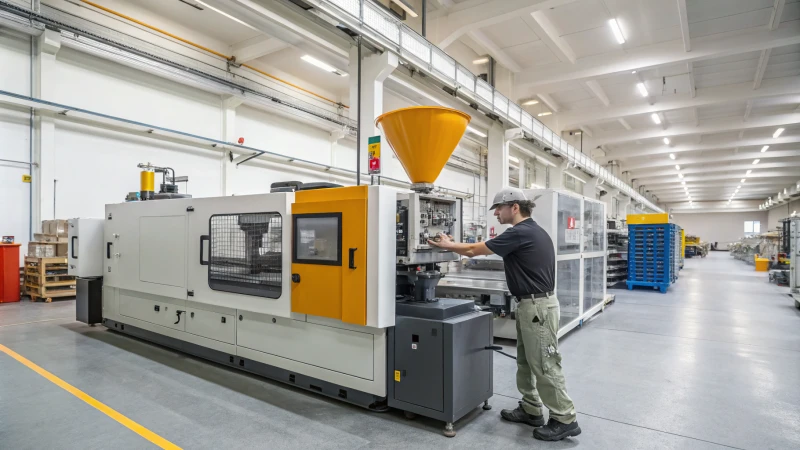
Benefits of Moderate Injection Speed
People know that in injection molding, moderation truly matters. The correct speed improves the material density of plastic pieces. Think of a smooth river of molten plastic filling the mold, like pouring a perfect glass of wine. For engineering plastics like polyamide, speeds of 80-120mm/s work well. The plastic then has time to settle and compact, creating a stronger structure. This density is important as it helps manage stress and increases tensile strength.
Moderate speeds also give molecular chains a good orientation. Think of this as aligning rowers on a team, ready to face pressure together. Polystyrene requires a speed of 70-100mm/s for aligned chains. This alignment strengthens the material.
Pitfalls of Excessive Injection Speeds
Raising the speed to finish quickly might be harmful. Speeds above 200mm/s can convert internal shear forces into leftover stress after cooling. This stress causes microcracks, which weaken the structure.
Fast speeds also damage molecular structures. Thermoplastic elastomers with long chains can break if speeds exceed 250mm/s, leading to surface problems like flow marks and streaks appearing.
Risks of Slow Injection Speeds
Going too slow is not good either. Filling the mold slowly, below 40mm/s, might result in weak spots. With crystalline plastics, slow speeds affect crystallization and molecular orientation; for example, polyoxymethylene molded under 60mm/s becomes uneven.
Understanding these effects helps achieve plastic products that look and function well without losing their main strength. Balance is very vital for optimal manufacturing success.
Comparison Table: Injection Speed Impacts
Injection Speed Range | Effects on Material | Strength Implications |
---|---|---|
80-120mm/s | Dense structure | Enhanced tensile strength |
>200mm/s | Residual stress | Microcrack formation |
<40mm/s | Insufficient filling | Weak points under stress |
Understanding these dynamics aids in achieving optimal manufacturing efficiency7, ensuring that plastic products meet both aesthetic and functional requirements without compromising their structural integrity.
Moderate speed optimizes molecular orientation in plastics.True
Moderate speeds align molecular chains, improving tensile strength.
Excessive injection speeds reduce tensile strength of plastics.True
High speeds cause residual stress and microcracks, weakening structure.
How to Determine the Right Injection Speed for Your Material?
Did you ever think about how fast injection molding changes the quality of the finished product?
I always think about the material type, mold design and desired product properties to find the right injection speed. Moderate speeds often help in achieving good material thickness and aligning molecules well. Very fast or slow speeds might probably lead to defects or stress problems.
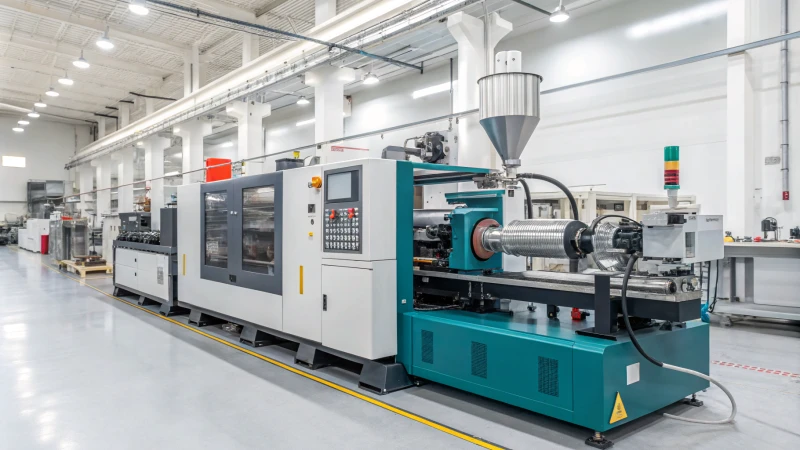
Material Basics
I think back to my early mold design days, holding polyamide and a chart, trying to find the right speed for injecting. Each kind of plastic felt unique – like polyamide. It works best when injected at 80-120mm/s. This material flows smoothly into every mold corner, creating dense and strong products.
Effects of Medium Injection Speed
The real wonder happens with medium speed. I’ve watched molecules in polystyrene organize themselves perfectly. Aiming for 70-100mm/s seems just right. At this speed, the chains line up neatly, like soldiers prepared for any pulling force. This alignment strengthens the material.
Material | Optimal Speed (mm/s) |
---|---|
Polyamide | 80-120 |
Polystyrene | 70-100 |
Dangers of High Injection Speeds
But increasing speed too much brings problems! Once, I used a high speed on thermoplastic elastomer. It was meant to be simple but ended with surface flaws showing stress spots. Speeds over 200mm/s invite stress, causing unwanted cracks. High speeds create trouble.
Problems with Low Injection Speeds
Going too slow poses difficulties too. I worked on a thick piece where speed fell under 40mm/s. We faced filling issues and weak areas. Slow speeds mess with crystalline plastics; this affects the structure.
Practical Thoughts
Finding the right speed is tricky, balancing mold design and product needs. Over time, I learned to rely on test data or ask industry experts8 for help. Every mold can be different; sometimes unique shapes need changes, especially for special looks.
Polyamide requires injection speeds of 80-120mm/s.True
Polyamide benefits from these speeds for optimal flow and product density.
Injection speeds over 200mm/s improve tensile strength.False
High speeds generate stress, risking microcracks and reducing tensile strength.
Conclusion
Injection speed significantly influences the tensile strength of plastic products, with moderate speeds enhancing material density and molecular orientation while extremes lead to defects and reduced strength.
-
Understanding residual stress helps in mitigating microcrack formation and improving product durability. ↩
-
Knowing optimal speeds ensures molecular structures remain intact for better product performance. ↩
-
Explores how proper orientation enhances tensile strength and material performance. ↩
-
Discover how variations in injection speed influence tensile strength, crucial for maintaining product durability. ↩
-
Learn about molecular orientation’s impact on tensile strength, essential for enhancing product performance. ↩
-
Explore guidelines for choosing the right injection speed to enhance material performance and product quality. ↩
-
Learn strategies to enhance manufacturing efficiency while maintaining product quality. ↩
-
Find expert advice on setting appropriate injection speeds based on material and design. ↩