Crafting Precision, Shaping Innovation
Master Injection Mold & Injection Molding with MoldAll – Your Hub for Learning
At MoldAll, we share expert knowledge to drive innovation in material selection, product design, mold design, mold making and injection molding. Whether you’re a student, designer, or operator, our tutorials and resources provide practical insights to help you excel.
Quck Contact
For inquiries or collaboration, feel free to reach us at here.
Video Tutorial
YouTube tutorials on all injection mold basics, from scratch.
Your Trusted Source for injection Mold and Injection Molding Knowledge
We empower learners and professionals with expert content, ensuring you stay updated and refine your skills in material selection, product design, mold design, mold making and injection molding.
About Us
Empowering Innovation in Mold Design and Manufacturing
Moldall is a sub-brand of ZetarMold. All knowledge is based on the ZetarMold team’s more than twenty years of work experience. MoldAll empowers learners and professionals by turning concepts into reality. From material properties to solving production challenges, our tutorials, case studies, and expert articles help students, designers, and operators refine their skills and stay current with industry trends.
Our resources cater to students, designers, and operators, equipping them with practical knowledge that bridges the gap between theory and real-world application. We believe that sharing expertise accelerates innovation, helping individuals and industries thrive. Join our growing community of learners and professionals who are shaping the future of manufacturing.
10+ Years of
Experience
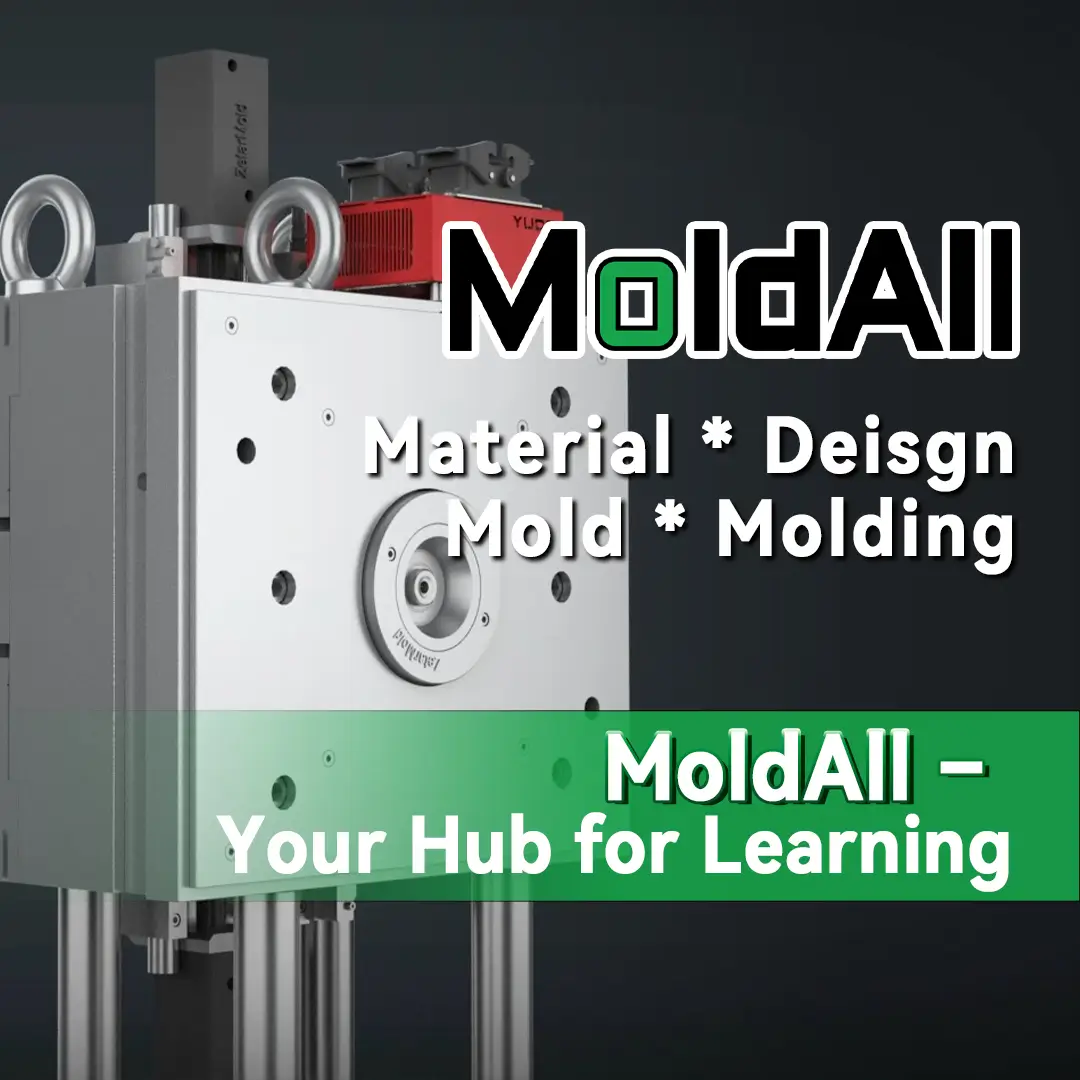
Services
Comprehensive Resources for Your Growth
Materials
Material Recommendations
Explore our expert recommendations for mold steel and plastic materials. From durability to shrinkage control, our curated selections ensure long-lasting and high-performance mold designs.
read moreDESIGN
Material Designing System
Gain valuable insights from industry professionals to perfect your injection mold and product designs. Learn techniques for optimizing functionality, manufacturability, and innovative solutions to common challenges.
read moreMANUFACTURING
Mold & Product Manufacturing
Master the art of injection mold and product manufacturing with expert advice. From material selection to quality control, our shared experiences ensure superior results and reduced production errors.
read moreOPTIMIZATION
Troubleshooting Injection Molding
Overcome production challenges with proven solutions to common problems. From defect prevention to troubleshooting dimensional inaccuracies, our expert insights ensure smooth operations.
read moreDEVELOPMENT
Production Efficiency Optimization
Enhance your production process with tips for optimizing efficiency and reducing cycle times. Discover best practices for streamlining workflows and improving overall productivity.
read moreQuality Inspection
Quality Inspection Tips
Learn from industry experts with practical tips for effective quality inspections. From troubleshooting defects to ensuring dimensional accuracy, our shared experiences help you achieve top-notch results.
read morefrequently asked questions
Frequently Asked Questions: Material Selection, Mold Design, Mold Making & Injection Molding
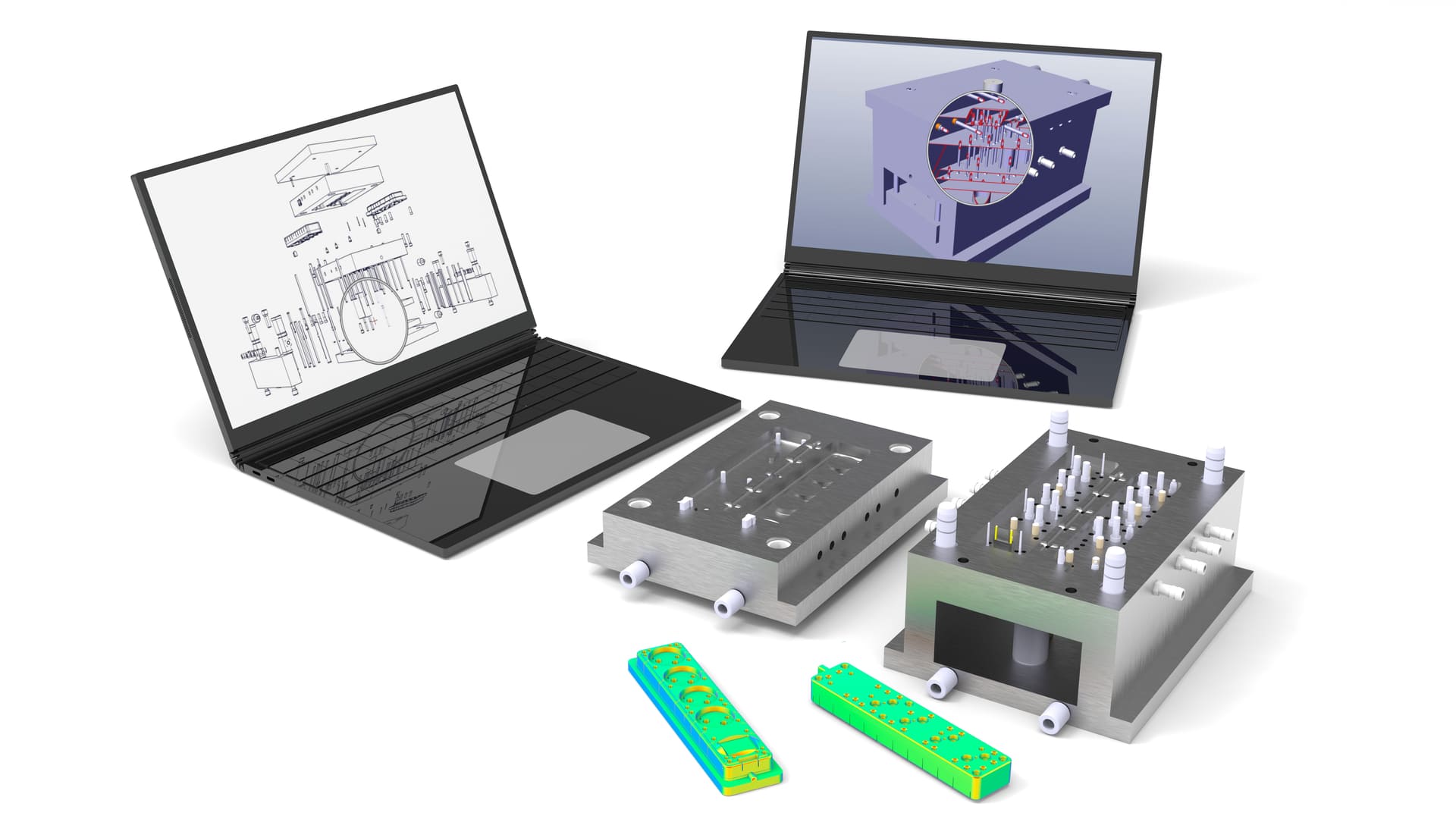
Our FAQ section addresses the most common questions from students, designers, and operators. Get clear, straightforward answers to help you in your journey to mastering mold design and injection molding.
CONTACT USHow do I choose the right material for injection molding?
Selecting the right material depends on factors like strength, flexibility, and thermal properties. Our guides walk you through the process of evaluating different plastics to meet your project’s requirements.
How can I reduce defects in my injection molding process?
Common defects such as warping and sink marks can be minimized through proper mold design and machine settings. We provide actionable tips to help you fine-tune your process for better results.
What’s the best way to balance cost and quality in mold design?
Achieving the right balance requires efficient design practices and smart material choices. MoldAll’s resources on Design for Manufacturing (DFM) help you make cost-effective decisions while ensuring quality.
blog & article
read our latest Knowlege Share
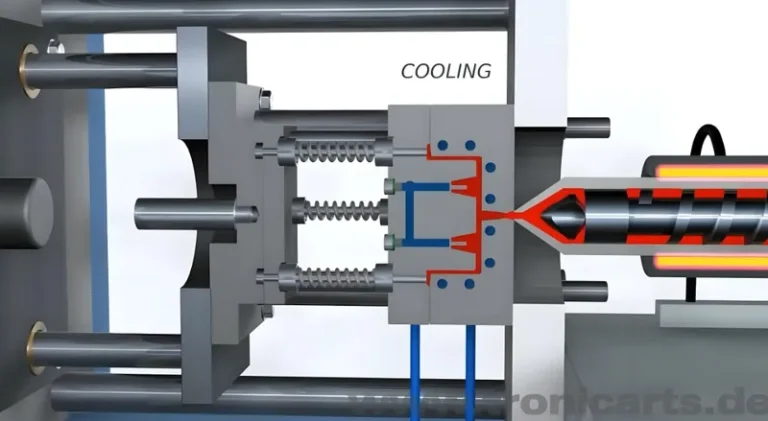
How Does the Ejector System Work in Injection Molding?
The ejector system in injection molding is a crucial mechanism that ensures the efficient removal of molded parts from the ...
Injection moulding
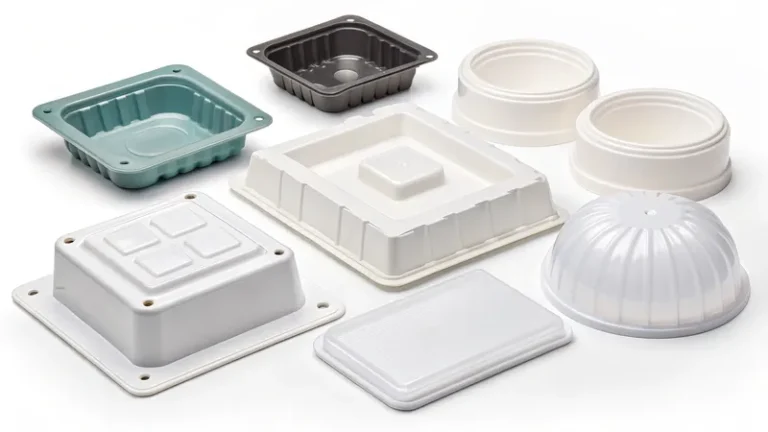
How Does Insert Molding Enhance Injection Processes?
Insert molding is a specialized injection molding technique1 that integrates pre-formed inserts—typically metal components2—into plastic parts during the molding process. ...
Injection moulding
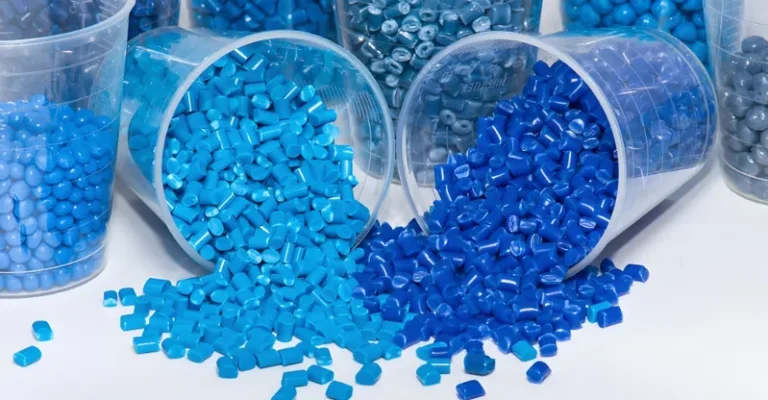
Choosing the Right Plastic B Side Features: A Comprehensive Guide
When designing plastic parts for injection molding, one of the critical aspects to consider is the selection of B side ...
Injection molding raw materials
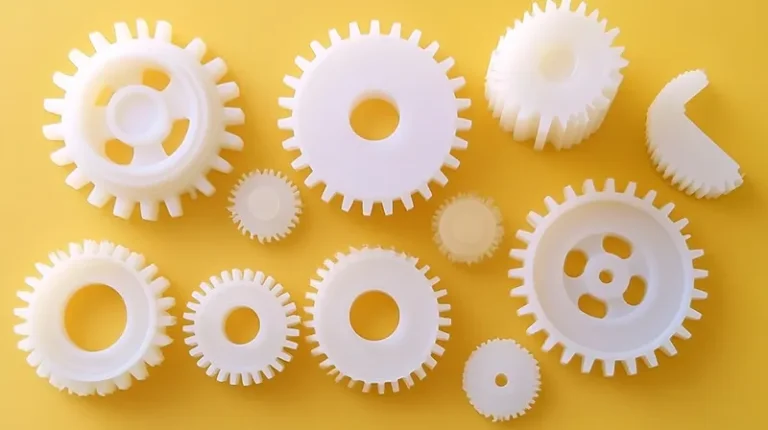
How Biopolymers Enhance the Sustainability of Injection Molding
Biopolymers are transforming the injection molding1 industry by offering a sustainable alternative to traditional petroleum-based plastics. Derived from renewable resources ...
Injection Molded Products

What Are the Essential Tools for Injection Mold Making?
Injection mold making1 is a critical process in manufacturing, enabling the production of precise plastic parts for industries like automotive, ...
Injection mold
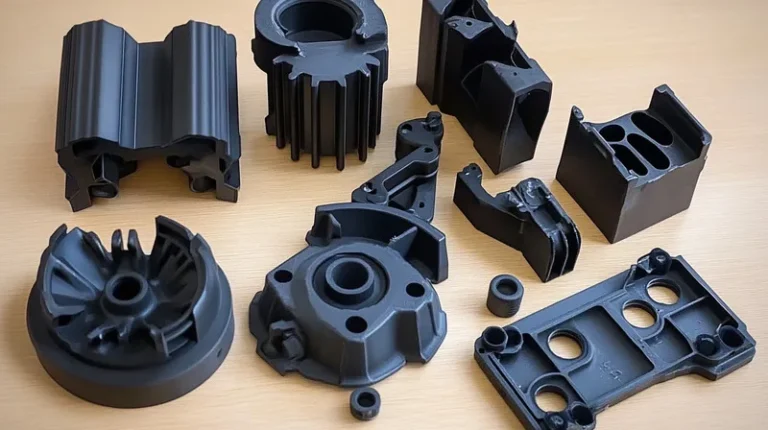
What Are the Best Practices for Managing Post-Processing in Injection Molding?
Injection molding is a cornerstone of modern manufacturing, producing plastic parts for industries ranging from automotive to medical devices. However, ...
Injection moulding