I remember the first time I saw warping in an injection-molded part. It was eye-opening. Flaws like this affect the whole production. The impact spreads.
Warpage defects in injection molded parts greatly affect dimensional precision, mechanical properties and appearance quality. Such defects might cause problems when assembling and limit functionality. Internal stresses and environmental factors often cause these issues. Manufacturers need to address these problems for really good product performance. Very good performance is essential.
Warpage may appear easy to understand at first. However, its hidden effects on assembly, performance and looks are complex. These areas deserve more exploration. Examining them closely not only improves understanding but also reveals methods to tackle these problems. This approach leads to smoother production. Let’s dive deeper into this puzzle and find ways to change these problems into chances for improvement.
Warpage affects the dimensional accuracy of molded parts.True
Warpage causes parts to deviate from their intended dimensions.
Environmental factors do not cause warpage defects.False
Environmental factors like temperature and humidity can lead to warpage.
Why Do Injection Molded Parts Warp?
I remember the first moment I faced warped parts in my designs. What a headache! Reasons for this problem probably save both time and resources.
Warpage in injection molded parts happens mainly due to uneven cooling, material shrinkage and poor mold design. Fixing these problems directly improves size accuracy and strength. These parts might warp. Addressing the causes really helps.
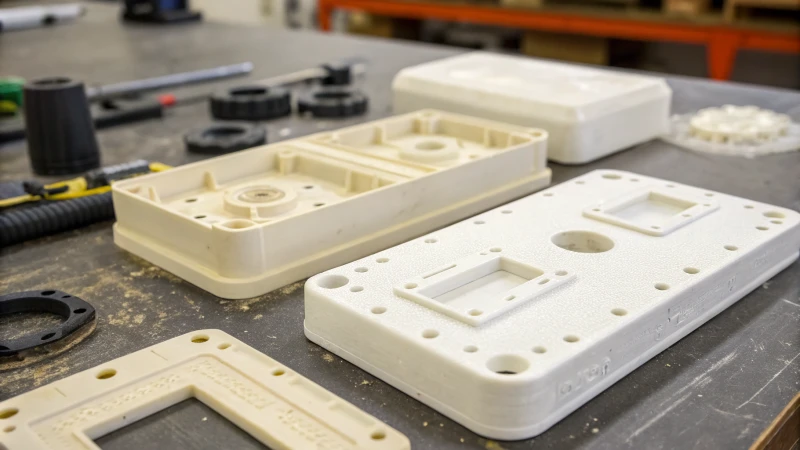
Uneven Cooling Rates
When I first saw warpage, it felt like a mystery to solve. One big reason is uneven cooling. Imagine baking a cake where the edges cook faster than the center. You’ll get an uneven cake. In injection molding, if parts cool unevenly, different sections shrink at different speeds, causing distortion.
Cooling Rate Comparison Table
Factor | Effect on Cooling |
---|---|
Mold Material | Thermal conductivity impacts cooling speed |
Part Thickness | Thicker areas cool slower |
Some years ago, I worked on a project with parts of different thicknesses. Thicker areas took a long time to cool, disrupting balance. This experience taught me to think about factors like mold material and part thickness because they really affect cooling speeds. Now, I always use computer tools1 to adjust cooling rates to make sure everything cools evenly.
Material Shrinkage
Picking the right material is like choosing the right ingredient for a recipe. It changes everything. For example, I once picked a strong crystalline material but found its high shrinkage caused a lot of warpage.
- Dimensional deviation: Shrinkage changes flatness and size. I’ve seen this with electronic housings where poor fits happened due to warping.
- Reduced strength: Areas with high shrinkage can become weak points, making parts less strong.
Now, I really think about shrinkage when designing parts that need accuracy and consider material behavior under stress2.
Incorrect Mold Design
I learned that mold design greatly affects the final product. Bad choices, like uneven wall thickness or poor gate placement, lead to uneven material flow and cooling.
Mold Design Checklist
- Uniform wall thickness
- Good gate placement for even material flow
- Good mold cooling channels for balanced temperature
Checking advanced mold design tips3 has helped me solve complex warpage problems in detailed parts.
External Factors
Even good designs and processes face outside issues. I stored parts in a humid place once and they warped later. So now, I store them in controlled spaces and use additives for better dimensional stability.
Preventative measures include:
- Storing parts in controlled environments
- Using additives to enhance dimensional stability4
Knowing these details helps me fix warpage better and improve product performance with smart design choices.
Uneven cooling causes injection molded parts to warp.True
Uneven cooling rates lead to differential shrinkage, causing warpage.
Crystalline materials have lower shrinkage than amorphous ones.False
Crystalline materials generally exhibit higher shrinkage than amorphous types.
How Does Warpage Affect Dimensional Accuracy?
Tried to put something together and found pieces oddly bent? Probably that annoying warping is the cause!
Warpage causes parts to bend and lose their proper shape and size. This bending disrupts the accurate alignment of pieces. Products struggle to fit together correctly. Performance suffers as a result. Assembly becomes a problem and functionality drops. It really compromises product quality.
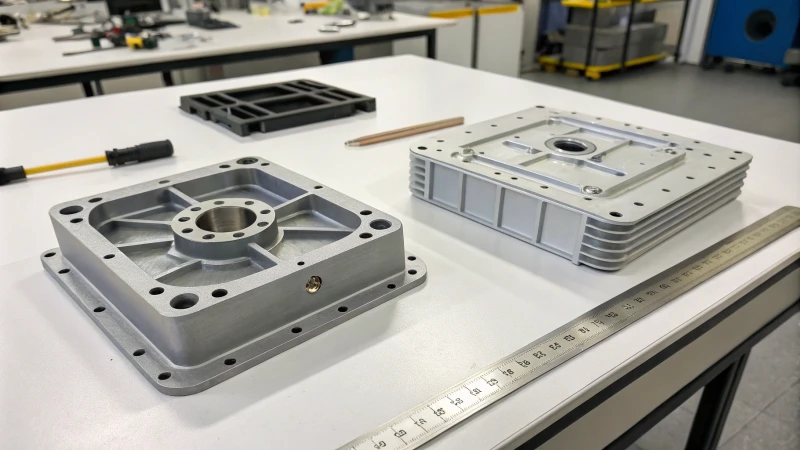
Warpage and Dimensional Changes
I recall my first project dealing with warps. It felt like forcing a square piece into a round opening – so frustrating and nearly impossible. When products bend or twist, their size and shape suffer. Think about creating a flat plastic plate, only to see its edges lift like leaves in the breeze. This is not just about looks; it messes up the whole assembly. Your carefully planned design now struggles to fit with other parts.
Aspect | Impact of Warpage |
---|---|
Flatness | Edges warp, altering surface planarity |
Linear Dimensions | Deviations from design specifications |
Less Dimensional Reliability
Warped pieces resemble an unstable friend – unpredictable. With time, changes in the environment and internal stress may change their size even more, lowering reliability. This is worrisome for pieces needing accuracy, like cases for sensitive instruments5.
Warpage and Mechanical Changes
Warping disrupts not only size – it affects strength too. A plastic bracket may look alright but crack under stress due to pressure spots. Warping alters the flexibility6 of the material, causing surprising deformations.
- Weaker Strength: Pressure spots raise breaking chances.
- Flexibility Changes: Deviates from expected bending behavior.
Decline in Visual Quality
Warping looks quite bad. A bent surface resembles a surface that’s been through hard times. I’ve watched lovely electronic cases lose appeal due to uneven surfaces and shifting colors.
- Surface Flatness: Bumpy surfaces hurt visual allure.
- Color and Shine: Warping messes with light reflection, disturbing coatings.
Assembly and Function Problems
Picture working on an assembly line. All smooth until – yep, a warped piece stops everything. Misfits raise scrap levels and costs. But that’s not all; product function suffers too. A bent container might leak or a lens holder may wreck device performance.
- Assembly Trouble: Increased automated process issues.
- Performance: Hurts key application effectiveness.
Knowing these effects helps creators like me foresee hurdles and develop ways to keep size accuracy and product excellence intact.
Warpage affects the flatness of a product.True
Warpage causes edges to warp, altering surface planarity and affecting flatness.
Warped parts maintain long-term dimensional stability.False
Warped parts face reduced stability due to internal stress and environmental factors.
How do warpage defects affect mechanical properties?
A tiny flaw disrupts the whole design process. This little issue impacts everything. Even small problems cause big issues.
Warpage defects in materials cause serious problems by changing their shape, weakening their structure and affecting their elasticity. This often results in difficult assembly and performance issues, especially in parts that need precision. Such defects can really be troublesome. They mess up the design.
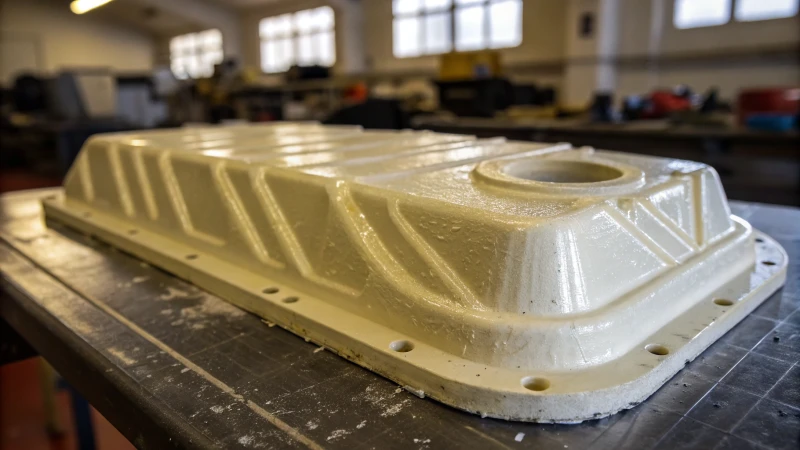
Dimensional Accuracy and Stability
Here’s a small story. Imagine designing a smooth plastic case for an electronic device. Everything seemed perfect on the computer screen. But when the actual model came, the corners looked a bit bent, similar to a pizza slice that had lost its shape. Even a small bend affected the sizes, making it hard to join with other parts. These size changes are very problematic when parts need to fit perfectly together. Even a tiny bend stops the proper assembly and affects the perfect snap-fit, which is very frustrating.
Warpage in materials often leads to dimensional deviation, where the actual size of a product deviates from its intended design. For instance, a warped plastic plate might show altered edges, impacting dimensional accuracy7. Such deviations can prevent proper assembly or fitting with other components.
Impact | Description |
---|---|
Dimensional Deviation | Changes in flatness and linear dimensions |
Reduced Stability | Size variations due to stress and environment |
Mechanical Properties: Strength and Elastic Modulus
Strength is something I really think about seriously. Bent parts have stress unevenly spread, which can lead to sudden breaks. Picture a plastic bracket folding with little pressure because of warping that weakens it.
Warped components often exhibit reduced strength due to uneven stress distribution, leading to stress concentration areas. These spots are prone to failure when subjected to load, compromising the strength8 of the material.
- Reduced Strength: Warped parts have uneven stress distribution, making them susceptible to damage.
- Elastic Modulus Change: Warping affects material’s deformation behavior under force.
Warping alters elastic strength and this makes pressure reactions very hard to predict. This is really troubling for designs in high-stress places.
Appearance Quality: Surface Flatness and Color
Look is not only about looks; it matters a lot for many items. Bent surfaces may appear unattractive and ruin color and shine, especially with surface treatments.
The appearance of warped parts can suffer, with surface flatness being significantly compromised. In industries demanding high aesthetic standards like electronics or automotive, this can be a major drawback. Uneven surfaces lead to poor visual appeal,
and warpage may result in uneven color and gloss9, affecting treatments like painting or electroplating.
I experienced this once with a car part where the bend ruined the paint job’s consistency—the finish was really unsightly and noticeable.
Assembly and Functional Performance Challenges
Warpage complicates assembly lines seriously. Bent sizes cause misalignments, turning smooth assembly into solving a mismatched puzzle.
Products with warpage defects often face assembly challenges as dimensional deviations hinder proper alignment on automated lines,
increasing scrap rates.
Additionally, specific functional parts might have limited use if their intended performance is compromised.
- Assembly Difficulties: Warped products struggle with precise embedding during assembly.
- Functional Limitations: Warpage affects the utility of specialized components.
A colleague told me about an incident involving a bent optical holder harming lens performance in an important project—this shows how bad defects can really be.
Warpage reduces the strength of materials.True
Warped components exhibit uneven stress distribution, reducing material strength.
Warpage defects improve surface flatness.False
Warpage compromises surface flatness, leading to poor visual appeal.
How does warpage mess with your product’s appearance?
Have you ever seen a product and spotted those unexpected twists and turns? Those are due to warpage, quietly ruining the appearance and texture of things you like.
Warpage ruins your sleek design, turning it into a bumpy mess. It changes surface smoothness. Color looks different. Parts might not fit well together.
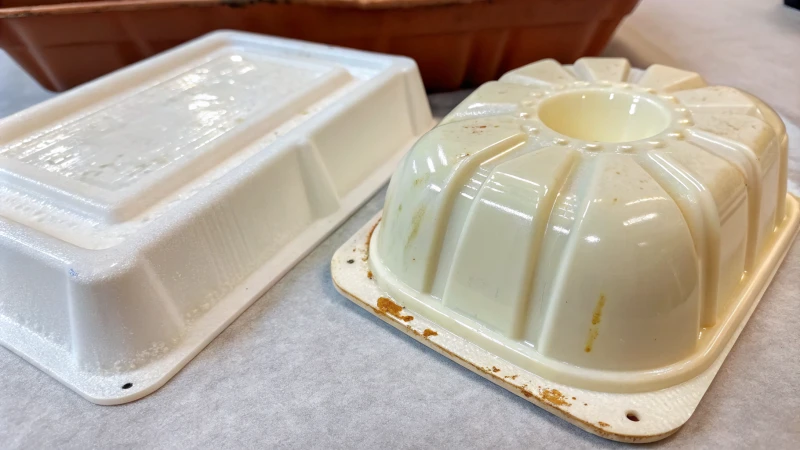
Dimensional Accuracy and Appearance
One of the primary ways warpage impacts the appearance quality of products is through dimensional deviation. Sometimes, when pieces don’t fit together, it’s because of warpage ruining the exact fit. I once designed a smooth plastic cover, but warpage caused the edges to bend like a burnt pizza crust. This bending not only spoiled the look but also messed up the fitting.
Impact | Description |
---|---|
Flatness Change | The warped surface reduces aesthetic appeal |
Assembly Issues | Misalignment may lead to visible gaps |
Reduced dimensional stability further complicates this issue, as internal stress and environmental factors can cause additional changes over time, especially in precise tasks.
Mechanical Properties and Visual Quality
Warpage affects more than just looks; it alters the strength of materials too. Imagine creating a strong plastic bracket, but warping caused uneven pressure. Under stress, it folded like a wet cardboard box. This unpredictable behavior results from changes in material stress and elastic modulus10.
Surface and Color Variations
The most evident impact of warpage on appearance quality is the deterioration of surface flatness. Even after applying a shiny coat, the small waves and dents from warping are hard to cover. It’s like trying to flatten a crumpled paper – it doesn’t work well. These defects are annoying, especially for high-quality items like tech cases or car interiors.
Furthermore, don’t overlook uneven color and gloss changes. Warped spots reflect light oddly, creating ugly shadows and spots that look cheap. Even the best paint can’t hide these problems completely.
Assembly Challenges and Functional Implications
Warped products cause trouble during assembly. Imagine trying to fit a twisted puzzle; it’s a sure way to waste materials and increase production costs.
For important parts like airtight containers or accurate lens holders requiring precise alignment, warping can really reduce their usefulness significantly.
Recognizing these impacts provides valuable insights for designers like Jacky11, enabling them to anticipate potential issues early and develop more effective solutions smartly during the design phase.
Warpage causes uneven surface appearance.True
Warped surfaces lose flatness, reducing aesthetic appeal significantly.
Warpage improves assembly precision of products.False
Misalignment due to warpage leads to visible gaps and assembly issues.
How Can You Prevent Warpage in Injection Molding?
Imagine the annoyance when a well-crafted product appears bent and lopsided. The issue happens often in injection molding. Various methods exist to address this problem directly.
Stopping warping during injection molding uses good mold design, controls how fast the parts cool and picks the best materials. These steps improve shape stability and strength, reducing mistakes and increasing product quality.
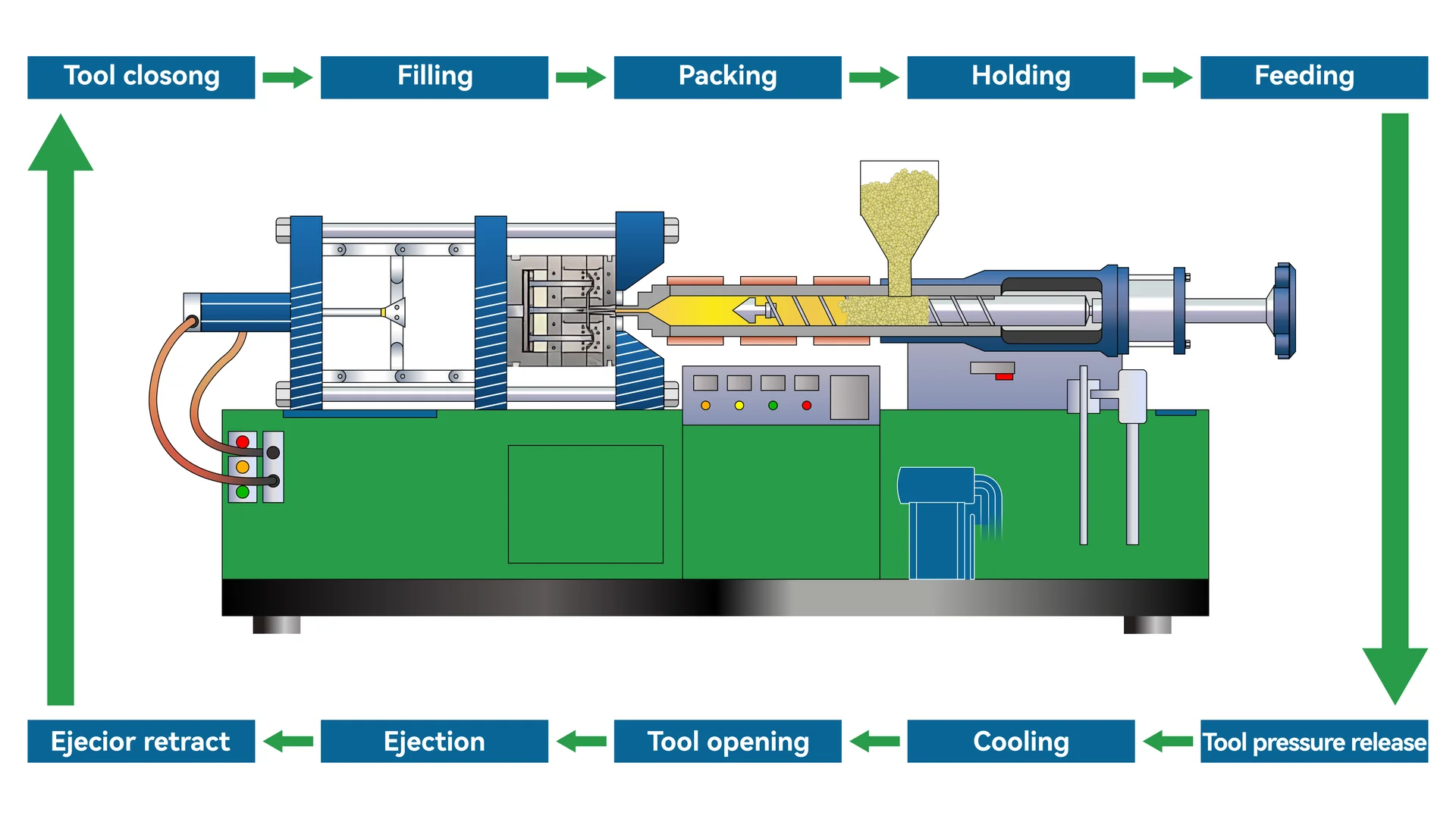
Making Mold Design Better
When I started with molds, I found out fast that a good design stops warping. Picture a mold with the same wall thickness everywhere. It’s like giving your part a fair share of food, keeping it steady and stopping stress. I once added ribs and bosses12 to a project. That changed everything by adding strength while keeping it light.
Getting the gate position correct is really important too. It helps fill the mold evenly and cuts down on stresses. I rely on simulation tools to foresee possible warping before the mold gets produced. It acts like a magical glimpse into the future of molding!
Controlling Cooling Rates
Cooling is very important. Uneven cooling is like leaving half an ice cube tray out of the fridge, leading to bad results. By placing cooling channels in the right spots, consistent temperature spreads, preventing warping.
A cooling rate control table can be useful:
Parameter | Description |
---|---|
Cooling Time | Adjust according to material used |
Coolant Type | Water or oil |
Channel Design | Conformal or standard |
Temperature | Maintain consistent throughout mold |
This approach has saved me from big problems and kept projects stable.
Choosing the Right Materials
Picking the right material is crucial. I go for materials with low shrink rates and high stability. PEEK or polycarbonate stand out with good qualities.
For an enhanced material selection guide, consider these factors:
- Shrinkage Rate: Less shrinkage means less warping.
- Elastic Modulus: High modulus fights deformation.
- Thermal Expansion: Low rates keep the shape steady.
Checking material information13 helps me find the best fit.
Making Process Changes
Sometimes, little changes really help. Tweaking injection pressure or hold time changes stability a lot. Machine alignment is also vital – regular checks stop issues during production.
Utilizing a process parameter checklist:
- Injection Pressure: Balance it to dodge over-filling.
- Holding Time: Assure full filling and hardening.
- Machine Alignment: Check and repair regularly.
Adjusting these makes great and very reliable parts.
Uniform wall thickness reduces warpage.True
Uniform wall thickness helps distribute stress evenly, reducing warpage.
Higher thermal expansion materials resist warping.False
Materials with lower thermal expansion coefficients better maintain shape, reducing warping.
Conclusion
Warpage defects in injection molded parts compromise dimensional accuracy, mechanical strength, and visual quality, leading to assembly difficulties and reduced functionality, ultimately affecting product performance.
-
Discover techniques for simulating cooling rates, helping you predict and prevent warpage in your designs. ↩
-
Gain deeper understanding of how materials react under stress conditions, crucial for reducing warpage. ↩
-
Explore innovative mold design strategies that address common warpage challenges. ↩
-
Learn about additives and methods that improve the stability of plastic components. ↩
-
This link explains how maintaining dimensional accuracy is crucial in manufacturing processes. ↩
-
Explore how stress variations influence the elastic properties of materials. ↩
-
Explore how warpage leads to changes in product dimensions and impacts assembly. ↩
-
Learn about stress distribution changes in materials caused by warpage. ↩
-
Understand how surface deformations affect appearance quality. ↩
-
Explores how warpage changes material properties like elastic modulus, impacting product performance. ↩
-
Guides designers like Jacky in preventing warpage during the design phase, ensuring better quality. ↩
-
Understanding how ribs and bosses support mold design can improve structural integrity and reduce warpage. ↩
-
Material datasheets offer detailed insights into material properties, aiding in selecting the right material for reducing warpage. ↩