¿Alguna vez has mirado un producto y te has preguntado cómo algo tan aparentemente simple puede ser tan complejo? ¡Sumergámonos en el fascinante mundo del moldeo por inyección!
El espesor desigual de la pared en productos moldeados por inyección a menudo es causado por factores como un diseño de molde irrazonable, una fabricación de molde inexacta, una presión de inyección inestable y una selección inadecuada de material. Para optimizar esto, los fabricantes deben perfeccionar el diseño del molde, estabilizar los parámetros del proceso y seleccionar materiales adecuados.
Si bien esta descripción general proporciona una instantánea de las causas y soluciones del espesor de pared desigual, una comprensión más profunda es esencial para solucionar problemas y optimizar sus procesos de fabricación de manera efectiva. Continúe leyendo para explorar estrategias detalladas para mejorar los resultados de su moldeo por inyección.
El diseño del molde afecta la uniformidad del espesor de la pared.Verdadero
El diseño del molde afecta el espesor de la pared a través del diseño de la cavidad y el posicionamiento de la compuerta.
- 1. ¿Cómo afecta el diseño del molde al espesor de la pared?
- 2. ¿Qué papel juega la presión de inyección en la uniformidad de la pared?
- 3. ¿Por qué es crucial la selección de materiales para lograr un espesor de pared constante?
- 4. ¿Cómo pueden los ajustes del proceso mejorar la consistencia del espesor de la pared?
- 5. Conclusión
¿Cómo afecta el diseño del molde al espesor de la pared?
El diseño de moldes es fundamental para determinar la uniformidad del espesor de pared en productos moldeados por inyección. Requiere precisión y optimización.
El diseño del molde afecta el espesor de la pared a través de factores como el diseño de la cavidad, la posición de la puerta y la precisión de fabricación. Los moldes no optimizados pueden provocar variaciones de espesor, afectando la calidad del producto.
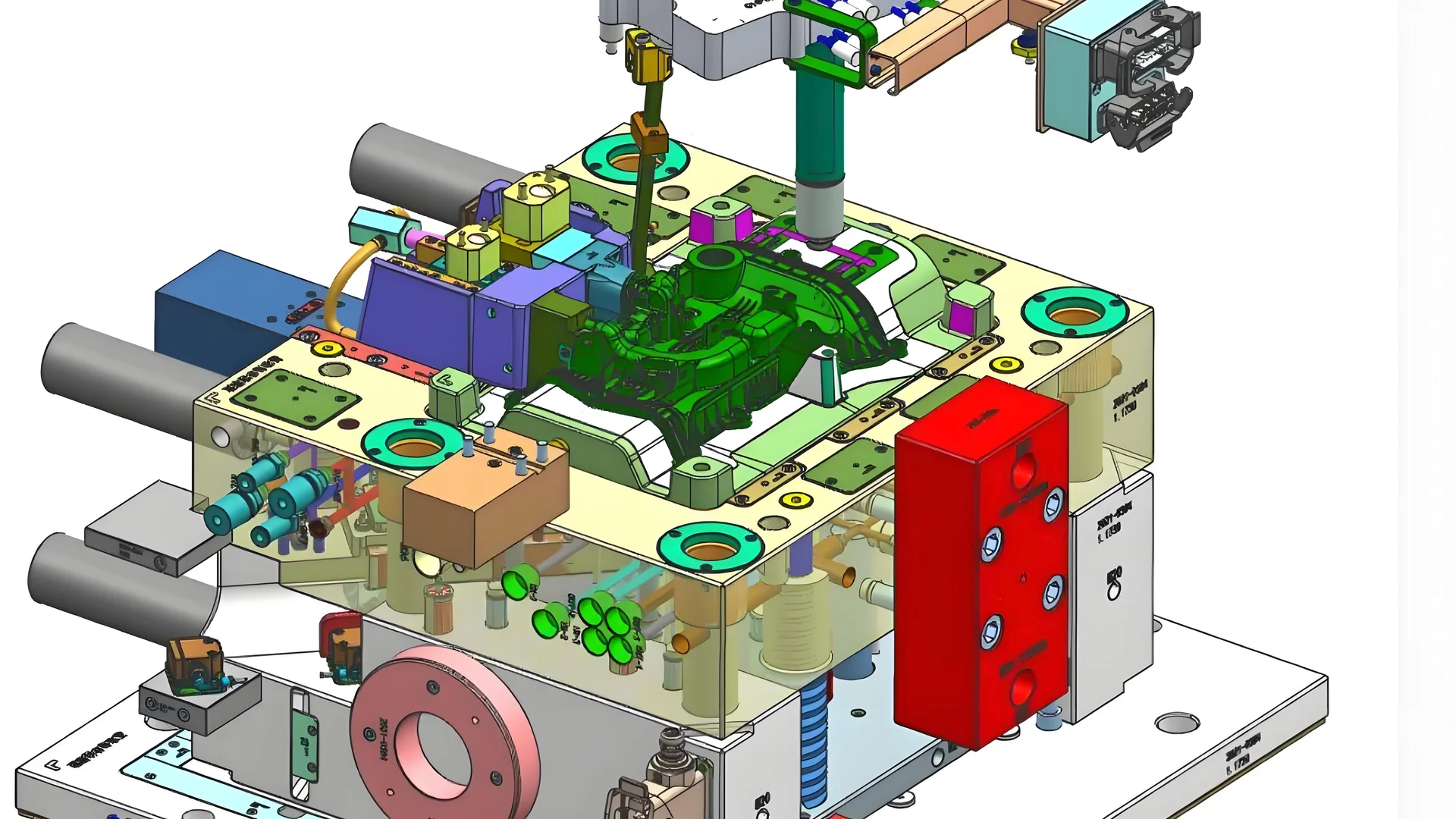
La influencia del diseño de la cavidad
El diseño de la cavidad es fundamental para el diseño del molde e influye directamente en el espesor de la pared del producto final. Si la cavidad está diseñada con un espesor de pared desigual, puede provocar que partes del producto sean demasiado gruesas o demasiado delgadas. Esto sucede a menudo en productos de formas complejas donde ciertas áreas se diseñan sin querer con más material del necesario.
Para solucionar esto, los ingenieros deben utilizar software de simulación de flujo para optimizar el diseño del molde 1 antes de la fabricación. Esto garantiza que el espesor de la pared se distribuya uniformemente por todo el producto, lo que reduce la probabilidad de defectos.
Importancia del posicionamiento de la puerta
La posición de la puerta, a través de la cual el plástico fundido ingresa a la cavidad del molde, es otro aspecto crítico. La colocación inadecuada de la puerta puede provocar una distribución desigual del material. Por ejemplo, si la puerta se coloca demasiado cerca de una sección específica, esa área puede volverse más gruesa a medida que se llena primero.
El uso de múltiples puertas o puertas latentes puede ayudar a lograr una distribución más uniforme al equilibrar el flujo de plástico a través de la cavidad. Este enfoque minimiza las áreas de exceso o insuficiencia de material.
La precisión de la fabricación es importante
La fabricación precisa es esencial para mantener un espesor de pared constante. Durante el proceso de creación del molde, cualquier error, ya sea por desgaste de la herramienta o imprecisiones en el ensamblaje, puede provocar desviaciones en las dimensiones de la cavidad. Estos pequeños errores pueden acumularse, dando como resultado un espesor de pared desigual en el producto final.
El empleo de máquinas CNC de alta precisión y la verificación periódica de la integridad de las herramientas pueden mitigar estos problemas. Además, garantizar tolerancias estrictas durante el montaje del molde también contribuirá a una calidad constante del producto.
Conclusión
En resumen, el diseño del molde afecta de manera intrincada el espesor de la pared a través de varios factores, como el diseño de la cavidad, la posición de la puerta y la precisión de fabricación. Cada componente debe diseñarse y ejecutarse meticulosamente para lograr un producto de alta calidad. Al centrarse en estas áreas, los fabricantes pueden mejorar significativamente los resultados de su moldeo por inyección.
El diseño de la cavidad afecta la uniformidad del espesor de la pared.Verdadero
El diseño de la cavidad influye directamente en el espesor de la pared al determinar el flujo de material.
La posición de la puerta no tiene impacto en el espesor de la pared.FALSO
La colocación inadecuada de la puerta puede provocar una distribución desigual del material.
¿Qué papel juega la presión de inyección en la uniformidad de la pared?
La presión de inyección es un factor fundamental para determinar la uniformidad del espesor de pared en productos moldeados.
La presión de inyección afecta la uniformidad de la pared al influir en el flujo plástico en la cavidad del molde. La alta presión puede causar un llenado excesivo y paredes gruesas, mientras que la baja presión corre el riesgo de un llenado insuficiente y paredes delgadas. La presión constante garantiza una distribución uniforme del material.
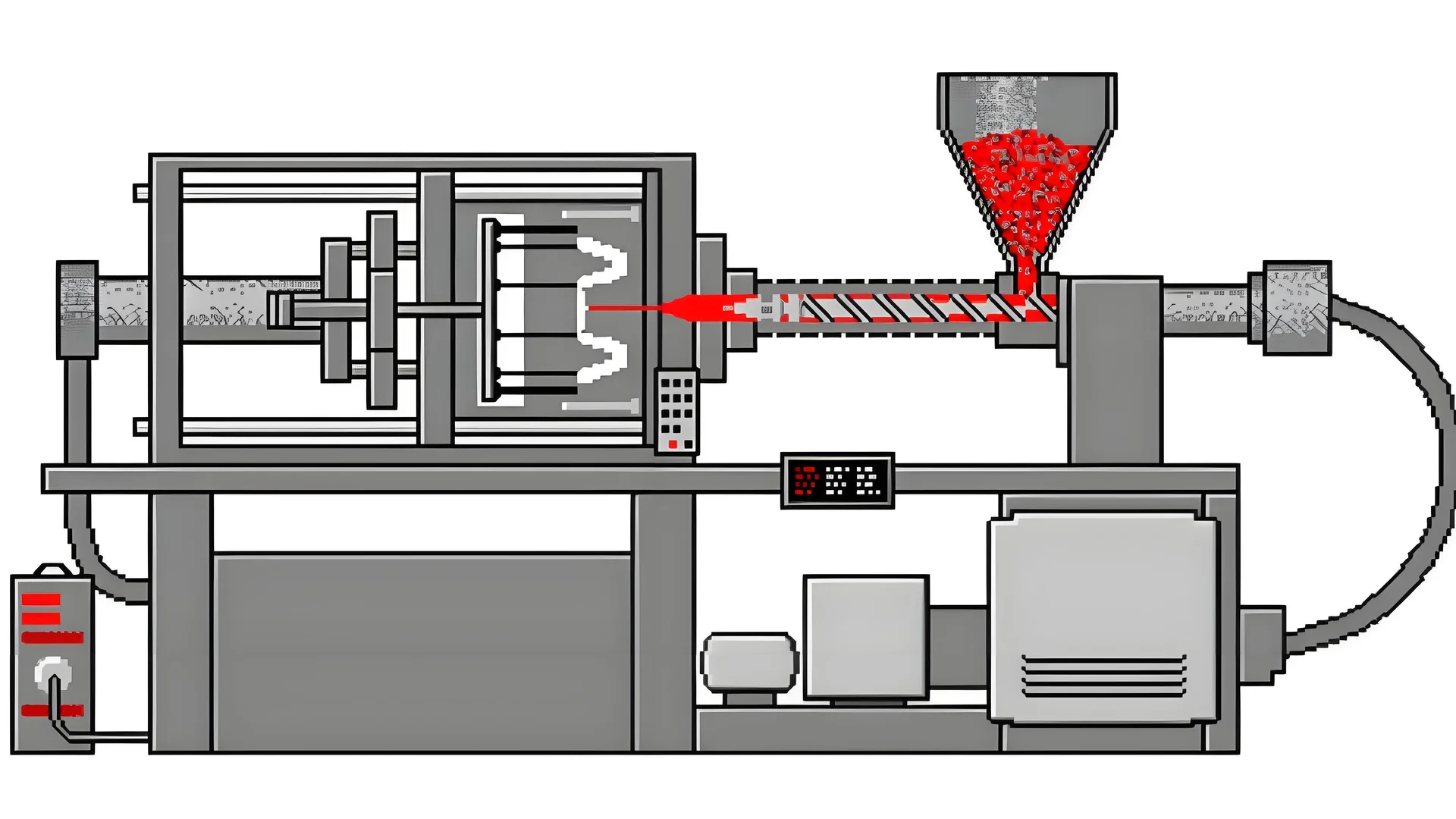
Comprender la presión de inyección
La presión de inyección es la fuerza ejercida por la máquina de moldeo por inyección para empujar el plástico fundido hacia la cavidad del molde. La consistencia de esta presión es vital para lograr un espesor de pared uniforme.
Cómo afecta la presión al espesor de la pared
-
Alta presión de inyección: cuando la presión es excesivamente alta, el plástico fluye demasiado rápido, lo que puede provocar un llenado excesivo. Esto puede aumentar el espesor de la pared en áreas cercanas a la puerta por donde ingresa el material. Con el tiempo, esto puede causar defectos como deformaciones o marcas de tensión.
-
Baja presión de inyección: por el contrario, una presión insuficiente podría no llenar completamente la cavidad, lo que provocaría paredes más delgadas e incluso piezas incompletas. Esto puede comprometer la integridad estructural del producto final.
Estabilización de la presión de inyección
-
Sistemas de monitoreo: la incorporación de sistemas de monitoreo en tiempo real, como sensores de presión, ayuda a mantener una presión constante durante todo el proceso de inyección. Estos sistemas pueden detectar fluctuaciones y permitir ajustes inmediatos.
-
Mantenimiento del sistema hidráulico: El mantenimiento regular del sistema hidráulico de la máquina garantiza su funcionamiento correcto, minimizando el riesgo de caídas o picos de presión.
Ejemplo práctico: calibración de la presión de inyección
Considere un escenario en el que está produciendo una carcasa de plástico con un espesor de pared objetivo de 2 mm:
Paso | Acción | Resultado esperado |
---|---|---|
1 | Establezca la presión inicial según las especificaciones del material. | Llenado inicial de la cavidad. |
2 | Monitoree usando sensores para una presión constante. | Detectar y ajustar las fluctuaciones. |
3 | Ajuste la presión de forma incremental según las mediciones del espesor de la pared. | Lograr uniformidad objetivo en toda la pieza. |
Exploración adicional de la presión de inyección2
Profundizar en cómo interactúa la presión de inyección con otras variables, como la temperatura y el diseño del molde, puede proporcionar información adicional para ajustar el proceso de moldeo por inyección.
Al comprender y controlar la presión de inyección, los fabricantes pueden mejorar significativamente la calidad del producto, garantizando que cada producto cumpla con las especificaciones exactas y funcione de manera confiable.
La alta presión de inyección provoca un llenado excesivo.Verdadero
Una presión excesiva empuja el plástico demasiado rápido, lo que provoca un llenado excesivo.
La baja presión de inyección garantiza paredes gruesas.FALSO
Una presión insuficiente provoca un llenado insuficiente, lo que provoca paredes más delgadas.
¿Por qué es crucial la selección de materiales para lograr un espesor de pared constante?
Elegir el material adecuado es fundamental para lograr un espesor de pared constante en el moldeo por inyección, lo que afecta directamente la confiabilidad y el rendimiento del producto.
La selección del material es crucial para lograr un espesor de pared consistente porque diferentes materiales exhiben diferentes tasas de fluidez y contracción durante el proceso de moldeo por inyección. La selección de un material con propiedades adecuadas garantiza un flujo y enfriamiento uniformes, minimizando las variaciones de espesor.
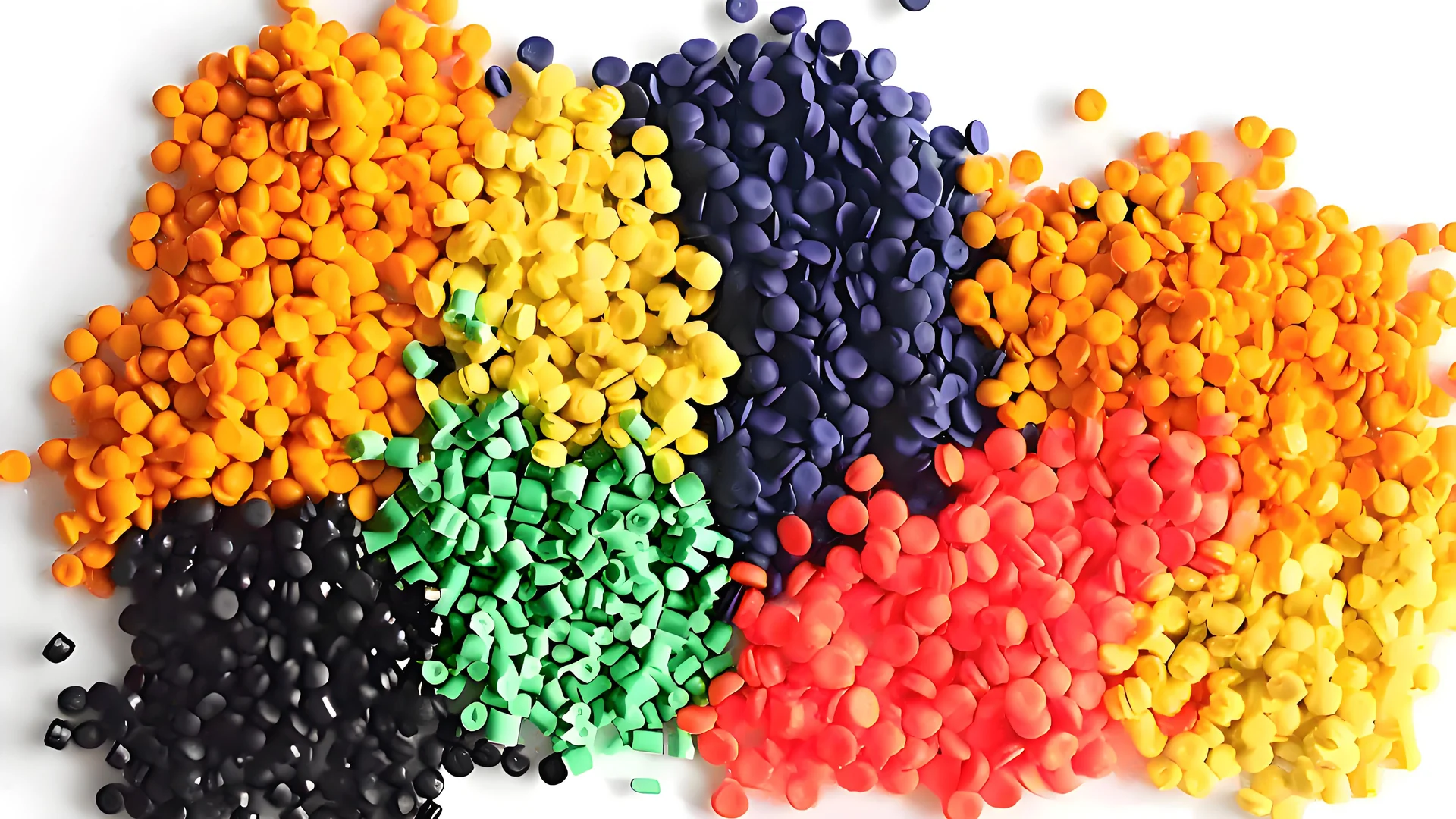
Comprender la fluidez del material
La fluidez de un material determina la facilidad con la que puede llenar la cavidad de un molde. Los materiales con mayor fluidez garantizan una distribución uniforme en geometrías complejas, lo que reduce el riesgo de espesores de pared desiguales 3 . Por el contrario, los materiales con baja fluidez pueden tener dificultades para llegar a todas las áreas del molde, lo que genera un espesor inconsistente.
Por ejemplo, los plásticos amorfos como el ABS (acrilonitrilo butadieno estireno) suelen poseer una mayor fluidez en comparación con los plásticos semicristalinos como el PP (polipropileno). La elección de un plástico con una fluidez óptima para el diseño del producto garantiza un flujo más suave y una distribución uniforme en las paredes.
El papel de la contracción del material
Diferentes materiales se encogen a diferentes velocidades a medida que se enfrían. Esta característica puede influir significativamente en el espesor de la pared si no se tiene en cuenta en el diseño del molde y la elección del material. La selección de materiales con una contracción mínima puede prevenir deformidades posteriores al moldeado, asegurando un espesor constante en todo el producto.
Por ejemplo, materiales como el nailon tienen tasas de contracción más altas que el poliestireno. Por lo tanto, comprender las propiedades de contracción de los materiales potenciales es esencial para mantener un espesor de pared uniforme.
Contenido de humedad y su impacto
La humedad dentro de los materiales plásticos puede vaporizarse durante el moldeo, provocando defectos como burbujas o huecos que comprometen la consistencia del espesor de la pared. El secado adecuado de materiales como policarbonato y nailon es crucial antes del moldeo por inyección para mantener la integridad y uniformidad del producto terminado.
Aprovechando los plásticos modificados
El uso de plásticos modificados puede resultar beneficioso cuando los plásticos estándar no cumplen con los requisitos específicos de consistencia del espesor de la pared. Los plásticos reforzados o retardantes de llama pueden ofrecer un rendimiento y una estabilidad mejorados. Para productos que requieren atributos especiales, estas modificaciones pueden proporcionar las propiedades necesarias sin sacrificar la uniformidad del espesor de la pared.
Seleccionar el material adecuado implica considerar factores como la fluidez, la contracción, la sensibilidad a la humedad y cualquier requisito de rendimiento específico. Un análisis exhaustivo de estas propiedades, posiblemente consultando con proveedores o mediante pruebas de materiales, es esencial para lograr un espesor de pared constante en los procesos de moldeo por inyección.
Los plásticos amorfos tienen mayor fluidez que los plásticos semicristalinos.Verdadero
Los plásticos amorfos como el ABS fluyen mejor en los moldes que el PP.
La contracción del material no afecta la consistencia del espesor de la pared.FALSO
Diferentes tasas de contracción pueden provocar un espesor de pared desigual después del moldeado.
¿Cómo pueden los ajustes del proceso mejorar la consistencia del espesor de la pared?
Lograr un espesor de pared constante en el moldeo por inyección es clave para mantener la calidad y confiabilidad del producto.
Los ajustes del proceso, como la estabilización de la presión de inyección, la optimización de la velocidad de inyección y el ajuste del tiempo y la presión de retención, son cruciales para mejorar la consistencia del espesor de la pared en los productos moldeados por inyección. Estos ajustes ayudan a controlar el flujo y el enfriamiento de los materiales, asegurando la uniformidad en todo el producto.
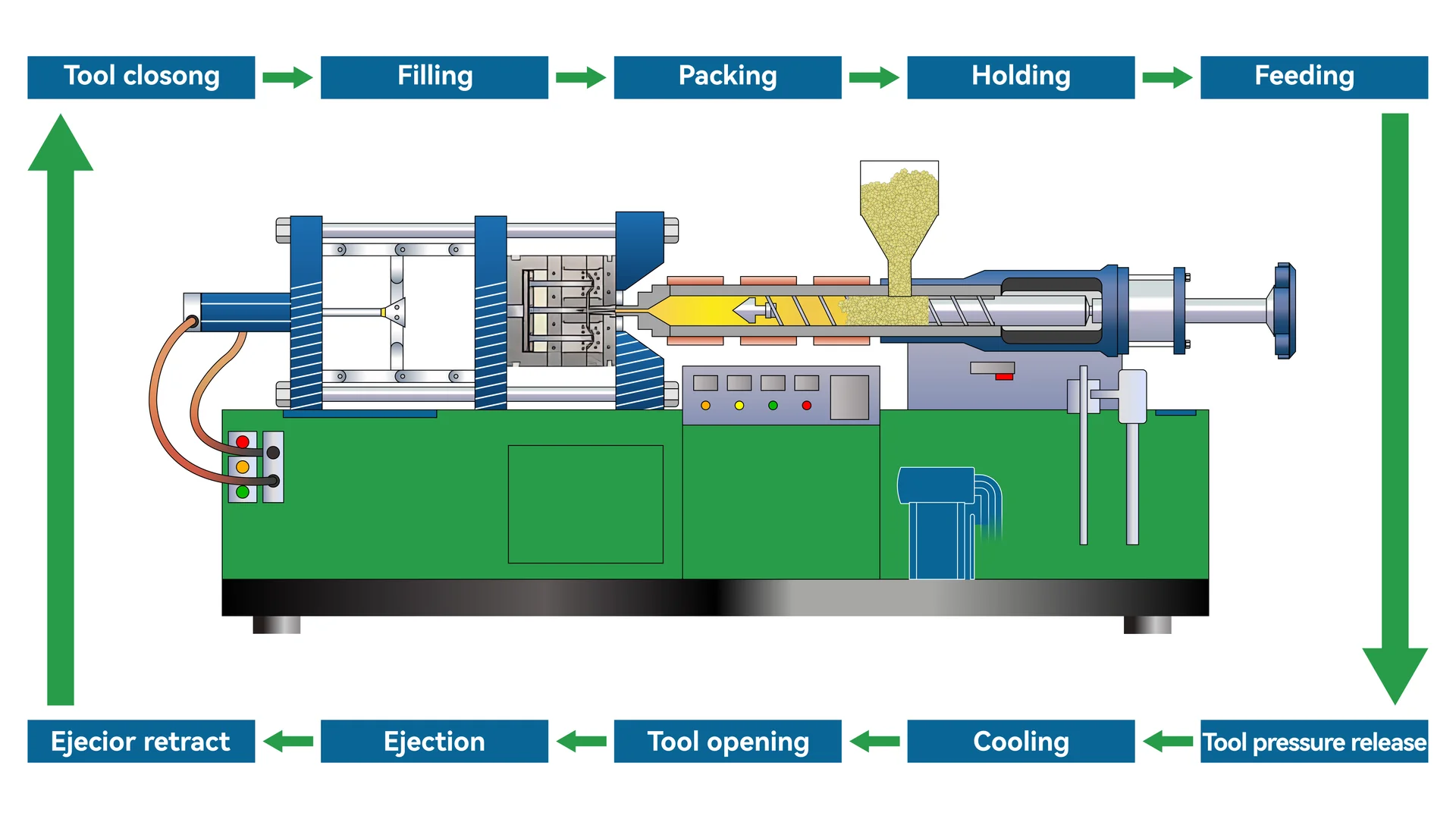
El impacto de la presión de inyección
Estabilizar la presión de inyección es fundamental para lograr un espesor de pared uniforme. Las fluctuaciones de presión pueden provocar un flujo de material desigual, provocando variaciones en el espesor de la pared. Las comprobaciones periódicas del sistema hidráulico pueden garantizar la estabilidad. El empleo de sensores de presión ayuda en el monitoreo en tiempo real, lo que permite realizar ajustes oportunos para mantener un llenado constante en todo el molde.
- Para secciones de paredes delgadas, una reducción moderada de la presión puede evitar el sobrellenado.
- En áreas más gruesas, puede ser necesario aumentar la presión para asegurar un llenado adecuado.
Optimización de la velocidad de inyección
La velocidad a la que se inyecta el material en el molde influye significativamente en su distribución y enfriamiento. Una velocidad optimizada garantiza que el plástico fluya de manera uniforme, minimizando los riesgos de defectos como salpicaduras o huecos.
- Las velocidades rápidas mejoran la fluidez de los productos de paredes delgadas, mientras que las velocidades más lentas son preferibles para las secciones más gruesas para evitar problemas como la pulverización.
- La implementación de un control de velocidad de múltiples etapas permite una dinámica de flujo personalizada en diferentes etapas del proceso de moldeo.
Ajustes de presión y tiempo de retención
Los ajustes de tiempo de retención y presión son cruciales en la fase de enfriamiento del moldeo. Los ajustes adecuados pueden prevenir defectos causados por contracción o llenado excesivo.
- Realice experimentos para determinar los tiempos de retención óptimos según las dimensiones del producto y las tasas de contracción del material.
- La reducción gradual de la presión de retención durante el enfriamiento ayuda a evitar el sobrellenado, lo que garantiza un espesor de pared preciso.
Beneficios de la selección y el procesamiento de materiales
Si bien se centra principalmente en los ajustes del proceso, la elección de los materiales desempeña un papel de apoyo para lograr la uniformidad. Es esencial seleccionar materiales con excelentes características de flujo y garantizar que se sequen adecuadamente antes del moldeo.
- Consulte las hojas de datos técnicos 4 de los proveedores de materiales para elegir la que mejor se ajuste a los requisitos de su producto.
- Utilice secadoras u hornos para eliminar la humedad de materiales higroscópicos como el nailon, ya que la humedad puede provocar irregularidades en el espesor de las paredes.
La presión de inyección estabilizadora garantiza un espesor de pared uniforme.Verdadero
La presión constante evita el flujo desigual, logrando un espesor uniforme.
Las velocidades de inyección más rápidas son ideales para secciones más gruesas.FALSO
Las velocidades más lentas son mejores para secciones más gruesas para evitar defectos.
Conclusión
En resumen, el diseño del molde afecta de manera intrincada el espesor de la pared a través de varios factores, como el diseño de la cavidad, la posición de la puerta y la precisión de fabricación. Al centrarse en estas áreas, los fabricantes pueden mejorar significativamente los resultados de su moldeo por inyección.
-
Descubra herramientas y técnicas para lograr un espesor de pared uniforme: Es mejor modificar la geometría de una pieza para eliminar secciones gruesas en lugar de diseñar un enfriamiento especial para las secciones gruesas para evitar... ↩
-
Comprenda cómo interactúa la presión con el flujo de material para un mejor diseño del molde. En tercer lugar, la alta presión de inyección puede forzar la apertura del molde en la línea de separación. Esto crea destellos en la pieza, pero lo más importante es que puede... ↩
-
Descubra cómo la fluidez del material afecta la consistencia del producto en el moldeo por inyección: La fluidez del material de moldeo de plástico se refiere a la capacidad de los materiales plásticos para fluir dentro del molde de inyección en la fabricación de productos plásticos. ↩
-
Acceda a especificaciones detalladas para seleccionar materiales que se adapten a las necesidades de su producto: La hoja de datos del material estándar consta casi en su totalidad de características de rendimiento medidas a temperatura ambiente. Además, la actuación… ↩