¿Alguna vez tuvo problemas con sus proyectos de moldeo por inyección? ¡Exploremos cómo el análisis de flujo de molde podría transformarlo todo para usted!
El análisis de flujo del molde optimiza el moldeo por inyección ajustando la ubicación de la compuerta, los sistemas de canales, la presión de inyección y el tiempo de enfriamiento, lo que mejora la eficiencia y la suavidad de la fabricación.
Pienso en mi viaje en el diseño de productos. Recuerdo las muchas horas que dediqué a solucionar problemas en el proceso de moldeo por inyección. Descubrí el análisis de flujo de moldes en ese momento. Esta herramienta se convirtió en un salvavidas para mí. Optimicé parámetros como ubicación de la compuerta y presión de inyección. Empecé a notar mejoras muy impresionantes. Ajustar la ubicación de la puerta me ayudó a evitar tomas cortas y trampas de aire en partes complejas. ¡Las piezas encajan como un rompecabezas!
El análisis del flujo del molde mejora la eficiencia del moldeo por inyección.Verdadero
Esta afirmación es cierta ya que el análisis de flujo del molde ayuda a optimizar los parámetros, lo que conduce a una mejor eficiencia de fabricación.
La ubicación de la puerta no afecta la calidad del producto en el moldeado.FALSO
Esta afirmación es falsa porque la ubicación de la compuerta afecta significativamente el flujo y la calidad del producto moldeado.
- 1. ¿Qué es el análisis de flujo del molde y por qué es importante?
- 2. ¿Cómo afecta la ubicación de la puerta al moldeo por inyección?
- 3. ¿Cómo afectan los sistemas de canales a la calidad del llenado en el moldeo por inyección?
- 4. ¿Cómo puede la optimización de la presión de inyección reducir los defectos?
- 5. ¿Cómo puedo mejorar la gestión del tiempo de enfriamiento?
- 6. ¿Cómo puede el análisis del flujo del molde mejorar la eficiencia de la producción?
- 7. Conclusión
¿Qué es el análisis de flujo del molde y por qué es importante?
¿Alguna vez te has preguntado cómo comprueban los fabricantes que cada pieza de plástico que crean sea perfecta? El análisis de flujo del molde tiene la respuesta. Esta herramienta optimiza el proceso de moldeo por inyección. También garantiza la calidad. La eficiencia mejora con su uso. ¡Esto realmente importa!
El análisis de flujo de molde (MFA) utiliza simulaciones por computadora en moldeo por inyección para optimizar la ubicación de la puerta, los sistemas de canales y los métodos de enfriamiento, garantizando productos de alta calidad y reduciendo defectos.
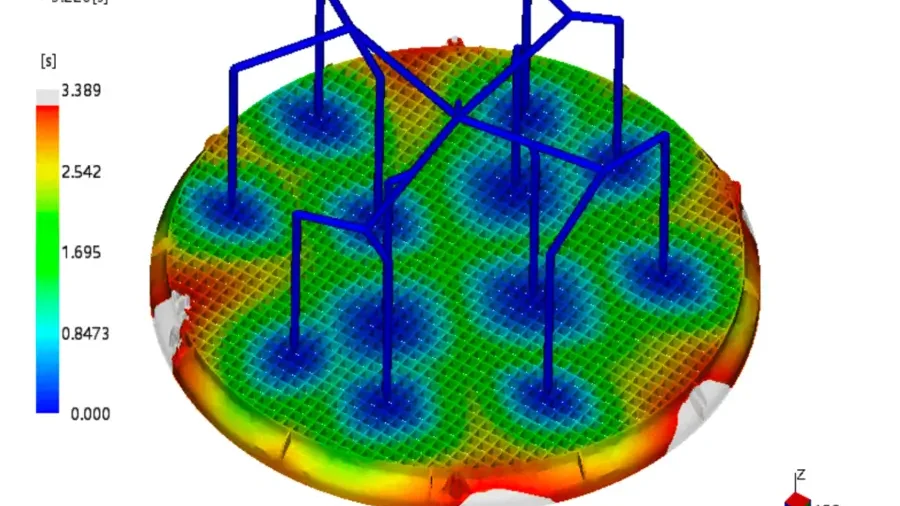
El análisis de flujo de molde (MFA) es una tecnología de simulación que desempeña un papel fundamental en el proceso de moldeo por inyección. Permite a los diseñadores predecir cómo fluye el plástico fundido a través de un molde, garantizando un llenado, enfriamiento y solidificación óptimos. Comprender MFA puede mejorar significativamente la calidad de la producción y al mismo tiempo reducir los costos.
Importancia de la ubicación y el número de la puerta
Un aspecto crítico de MFA es determinar la ubicación y el número de la puerta . Una ubicación optimizada de la puerta garantiza que la masa fundida llene la cavidad de manera uniforme, especialmente en formas geométricas complejas. Por ejemplo, al producir una pieza de plástico con secciones tanto delgadas como gruesas, colocar la compuerta cerca del área de paredes delgadas ayuda a lograr un mejor flujo.
En un proyecto, coloqué la puerta cerca de una sección delgada de una pieza de plástico. Esto nos dio un flujo perfecto y realmente mejoró el resultado.
Además de la ubicación, MFA también puede indicar si se necesitan varias puertas. Por ejemplo, el tablero de un automóvil puede requerir varias puertas para garantizar un llenado uniforme en toda su gran cavidad. Esta optimización, en última instancia, da como resultado una reducción de los defectos y una mejor calidad del producto.
Parámetros del sistema de corredores
El sistema de canales juega un papel importante en el flujo de material plástico. MFA ayuda a seleccionar la forma y el tamaño , lo que afecta la resistencia al flujo. Una guía redonda suele tener una resistencia menor en comparación con las guías trapezoidales o en forma de U.
Forma del corredor | Resistencia al flujo | Aplicaciones adecuadas |
---|---|---|
Redondo | Bajo | Propósito general |
trapezoidal | Medio | Piezas complejas con espesor variable |
en forma de U | Alto | Producción de alto volumen |
Además, MFA garantiza que los diseños de canales estén equilibrados en moldes de múltiples cavidades, lo que ayuda a lograr el llenado simultáneo de cada cavidad. Recuerdo un proyecto con tapas de botellas de plástico en el que mantener la uniformidad era esencial; necesitábamos que se llenaran todos a la vez.
Optimización de la presión y la velocidad de inyección
MFA también permite optimizar la presión de inyección analizando la resistencia al flujo dentro de la cavidad del molde. Si la presión es demasiado alta, pueden surgir problemas como flash y problemas de desmoldeo, mientras que una presión demasiado baja puede provocar disparos cortos. La optimización de la presión de inyección es otra lección importante de MFA; establecer la presión correcta era crucial para las cajas electrónicas de paredes delgadas.
Además, controlar la velocidad de inyección es vital para lograr acabados de alta calidad en los productos. Diferentes velocidades afectan el frente de flujo; Para piezas visualmente atractivas como las de los automóviles, las simulaciones de MFA me aconsejaron sobre velocidades para superficies perfectas y sin defectos.
Poner presión y tiempo
La etapa de mantenimiento después del llenado es crítica para compensar la contracción por enfriamiento. Después del llenado del molde, esta etapa compensa la contracción durante el enfriamiento; He utilizado los conocimientos de MFA en numerosas ocasiones para reducir las marcas de contracción en piezas precisas, como engranajes, prediciendo la presión de retención .
determinar el tiempo de espera ; Según el espesor de la pared y las propiedades del material, MFA calcula los tiempos óptimos para garantizar la integridad sin alargar innecesariamente los ciclos de producción.
Tiempo de enfriamiento y parámetros del sistema
Por último, MFA optimiza el tiempo de enfriamiento analizando la distribución de temperatura durante los procesos de enfriamiento. Este paso ha sido fundamental para mejorar la eficiencia de la producción y al mismo tiempo prevenir la deformación de las piezas; La reducción de los tiempos de enfriamiento aumentó considerablemente la producción y al mismo tiempo mantuvo la calidad durante un proyecto de juguete.
MFA también ayuda en el diseño de sistemas de enfriamiento al evaluar el diseño, el diámetro y el caudal de las tuberías de enfriamiento para garantizar un enfriamiento uniforme en piezas grandes; un sistema de enfriamiento efectivo evita la deformación, lo cual aprendí en desafíos de proyectos anteriores.
Al integrar el análisis de flujo de moldes en nuestros procesos de diseño y producción, aumenta la calidad del producto al tiempo que se reducen los residuos y se aumenta la eficiencia general.
El análisis del flujo del molde mejora la eficiencia del moldeo por inyección.Verdadero
MFA optimiza los procesos prediciendo el flujo de plástico, mejorando la eficiencia y reduciendo los defectos en la producción.
No son necesarias varias puertas en el análisis de flujo del molde.FALSO
MFA a menudo indica la necesidad de múltiples puertas para garantizar un llenado uniforme en cavidades grandes, crucial para la calidad.
¿Cómo afecta la ubicación de la puerta al moldeo por inyección?
¿Alguna vez pensó en cómo la posición de una compuerta en el moldeo por inyección cambia el proceso? ¡Es realmente interesante! Exploremos cómo este importante detalle impacta nuestras tareas y la calidad de lo que producimos.
La ubicación de la puerta en el moldeo por inyección afecta el flujo de fusión, la eficiencia del llenado y las tasas de defectos. Optimizarlo mejora la calidad de las piezas y minimiza los problemas de producción.
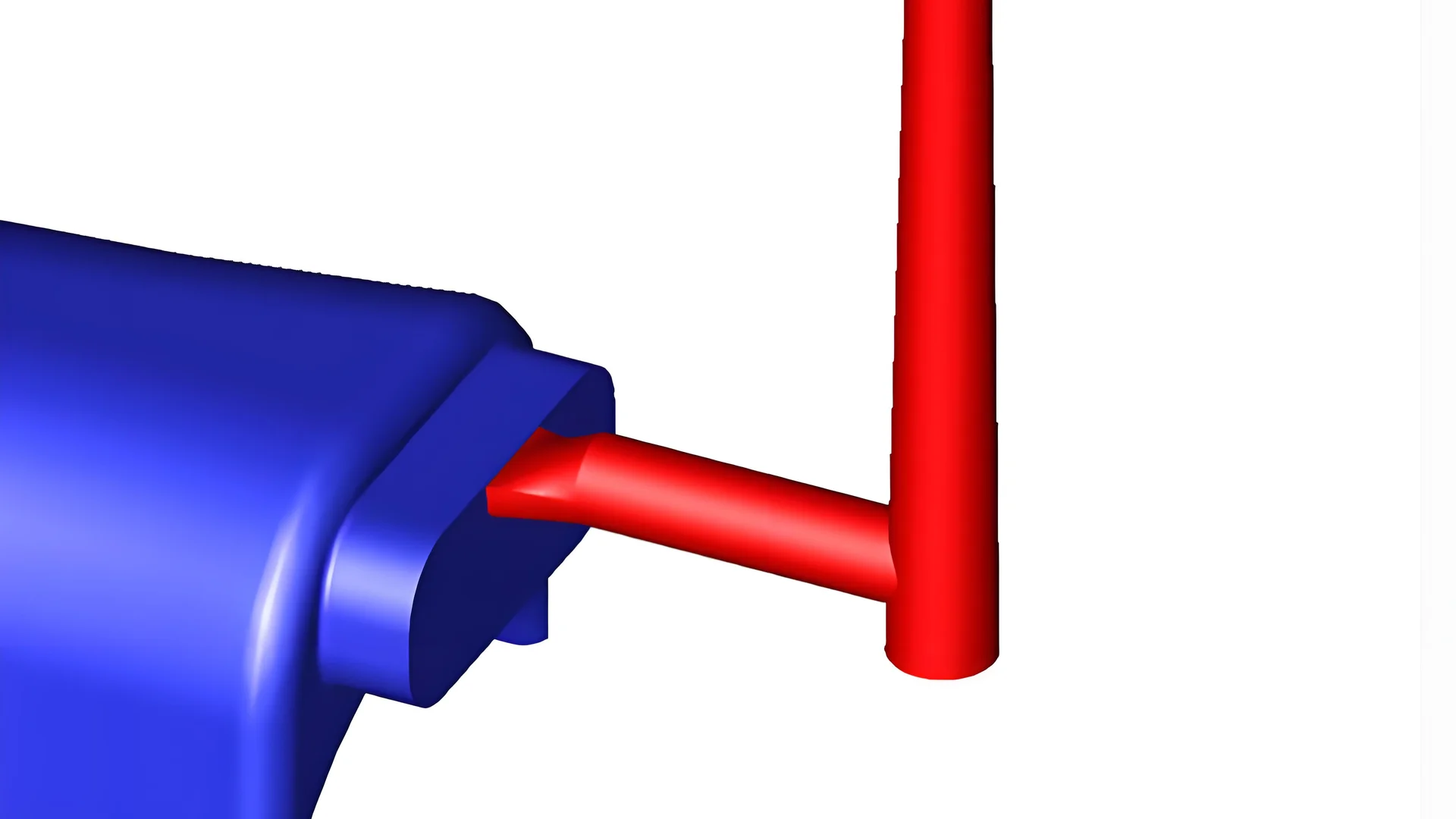
Comprender la ubicación de la puerta en el moldeo por inyección
La colocación de la puerta en moldeo por inyección da forma a nuestras piezas moldeadas. Recuerdo un proyecto en el que la posición de la puerta cambió por completo el producto final. La compuerta correcta afecta en gran medida el flujo de fusión, la eficiencia de llenado y las tasas de defectos. Una buena optimización mejora la calidad de las piezas y minimiza los problemas de producción. Esto es lo que todo diseñador quiere.
La optimización de la ubicación de la compuerta garantiza un flujo uniforme y evita defectos como disparos cortos o trampas de aire. Una vez trabajé en una pieza compleja con secciones gruesas y delgadas. Colocar la puerta cerca del área más delgada ayudó a un llenado rápido, evitando molestas bolsas de aire atrapadas.
Importancia del ajuste del número de puerta
A veces, una puerta no es suficiente, especialmente para formas grandes o complejas. El análisis del flujo del molde juega un papel vital a la hora de decidir si son necesarias varias puertas.
Considere el tablero de un automóvil donde lograr un llenado uniforme del material fundido es crucial. Esto a menudo requiere un mayor número de puertas para garantizar una calidad constante en todo el molde. La siguiente tabla ilustra este concepto:
Tipo de pieza | Puertas recomendadas | Razón de múltiples puertas |
---|---|---|
Tablero de instrumentos del coche | 2-4 | Garantiza un llenado uniforme del material fundido |
Tapas de botellas de plástico | 1-2 | La forma simplificada permite una sola puerta |
Parámetros del sistema de corredores
El diseño del sistema de canales es muy importante, ya que determina la eficacia con la que la masa fundida viaja desde la puerta hasta la cavidad. La forma y el tamaño de los corredores afectan la resistencia al flujo y la pérdida de presión. Generalmente, se prefieren los canales redondos por su menor resistencia al flujo.
El análisis del flujo del molde ayuda a seleccionar los parámetros óptimos del canal para transiciones suaves sin pérdida de presión. Esto es importante, especialmente en moldes de múltiples cavidades donde las tasas de llenado iguales son clave.
Control de presión y velocidad de inyección
La ubicación de la compuerta también influye en la presión de inyección y la velocidad utilizada durante el proceso de moldeo. Analizar la resistencia al flujo en diferentes puntos me permitió optimizar las presiones para evitar defectos como rebabas o dificultades de desmolde.
Ajustar la velocidad de inyección también es crucial; Al crear piezas de alta calidad, como interiores de automóviles, controlar la velocidad de inyección evita marcas de flujo antiestéticas.
Mantenga la configuración de presión y tiempo
Después del llenado, es fundamental mantener una presión de mantenimiento correcta. Trabajé con engranajes de alta precisión donde predecir las presiones de retención ayudó a minimizar las marcas de contracción y los problemas dimensionales.
Establecer tiempos de espera adecuados es un acto de equilibrio; demasiado corto provoca marcas de contracción visibles, mientras que demasiado largo alarga innecesariamente los tiempos de ciclo. La siguiente tabla describe los tiempos de retención óptimos según el espesor de la pared:
Espesor de pared (mm) | Tiempo de espera recomendado (segundos) |
---|---|
< 1 | 5-7 |
1-3 | 8-10 |
> 3 | 12-15 |
Optimización del tiempo de enfriamiento
Por último, el tiempo de enfriamiento y los parámetros del sistema son muy importantes. ¿Sabía que la ubicación de la puerta afecta la eficiencia del enfriamiento? ¿Diseñé diseños de tuberías de refrigeración para una refrigeración uniforme y mejorar la eficiencia sin perder calidad?
La optimización de los tiempos de enfriamiento mediante el análisis del flujo del molde puede mejorar significativamente la eficiencia de la producción sin comprometer la integridad de la pieza.
Por ejemplo, los juguetes de plástico pequeños pueden beneficiarse de tiempos de enfriamiento reducidos y al mismo tiempo garantizar una calidad adecuada.
En conclusión, saber cómo la ubicación de la puerta afecta muchos factores es esencial para optimizar la calidad de las piezas y la eficiencia de la producción. Para obtener más información sobre estrategias efectivas de colocación de puertas, explore esta guía detallada 1 .
La ubicación de la puerta afecta los patrones de flujo de fusión en el moldeo por inyección.Verdadero
La ubicación de las compuertas influye directamente en cómo el material fundido llena el molde, lo que afecta la calidad y eficiencia general de la pieza.
No son necesarias varias puertas para diseños de moldes complejos.FALSO
En geometrías complejas, pueden ser esenciales múltiples puertas para garantizar un llenado uniforme y minimizar los defectos durante el proceso de inyección.
¿Cómo afectan los sistemas de canales a la calidad del llenado en el moldeo por inyección?
¿Alguna vez ha pensado en cómo una pequeña pieza podría realmente cambiar la calidad de sus piezas moldeadas? Analicemos los sistemas de canales y veamos qué importancia tienen en el moldeo por inyección. Estos sistemas ayudan a llenar los moldes correctamente.
Los sistemas de canales en el moldeo por inyección influyen en el flujo de material, la distribución de presión y el enfriamiento. La ubicación adecuada de la compuerta, las formas de los canales y los ajustes de inyección son esenciales para obtener piezas de alta calidad con menos defectos.
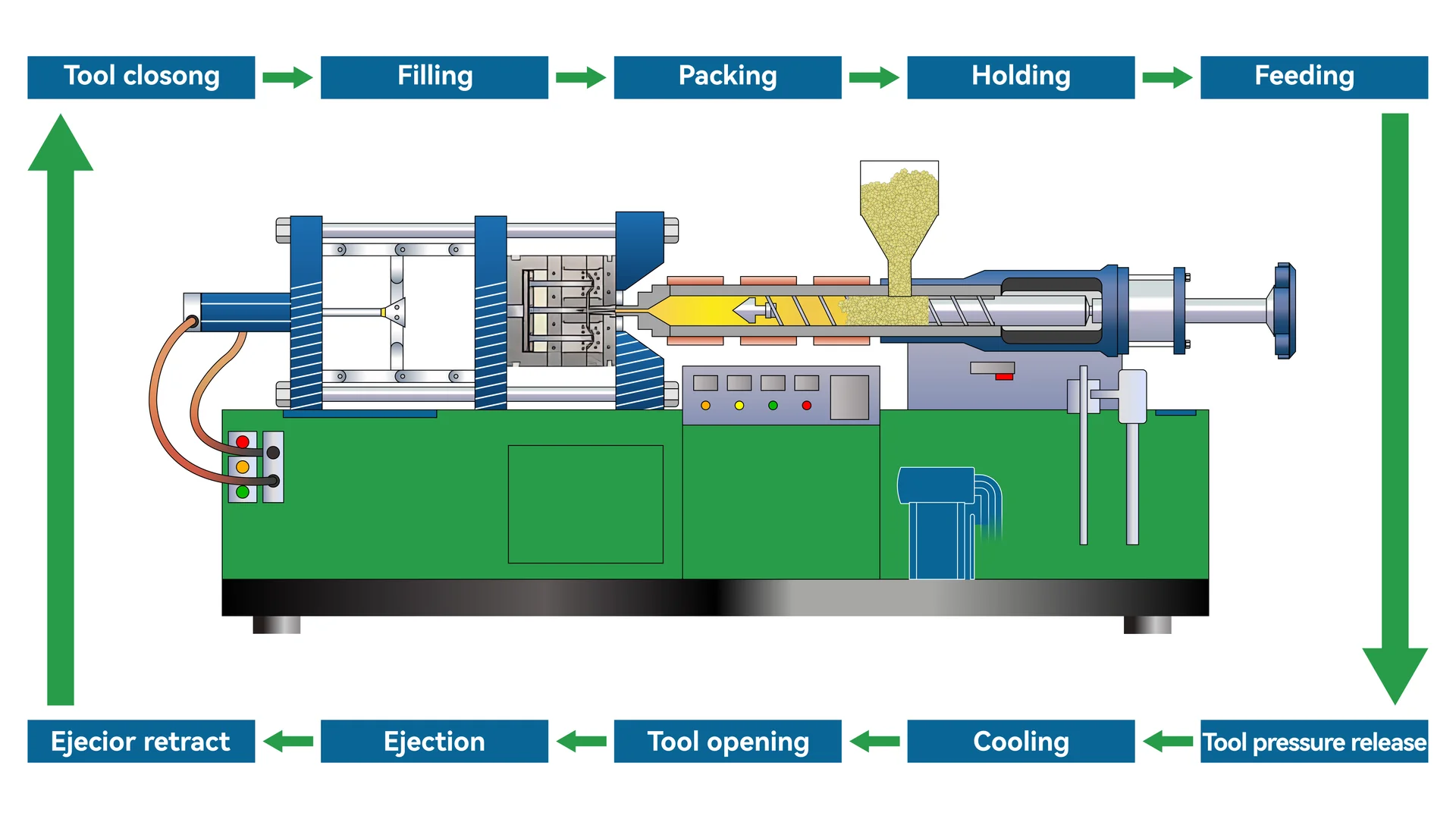
Comprender los sistemas de corredores
Los sistemas de canales son componentes críticos en el proceso de moldeo por inyección que desempeñan un papel importante para garantizar que la masa fundida llene las cavidades del molde de manera eficiente y efectiva. El diseño del sistema de canales puede influir en la calidad general del llenado de los componentes de plástico.
1. Ubicación y número de compuertas
Optimizar la ubicación de las compuertas es esencial para una distribución uniforme del material fundido. Para geometrías complejas, el análisis del flujo del molde puede determinar los mejores puntos de entrada para la masa fundida.
- Ejemplo : en una sección de una pieza de paredes delgadas, colocar la compuerta cerca de esta área garantiza un llenado rápido, lo que reduce las posibilidades de defectos como disparos cortos o trampas de aire.
- Número de compuerta : Puede ser necesario aumentar el número de compuertas para que piezas grandes logren un llenado uniforme.
2. Parámetros del sistema de canales
La forma y el tamaño de los canales afectan la resistencia al flujo. Los corredores se pueden diseñar en varias formas:
Forma del corredor | Resistencia al flujo | Eficiencia |
---|---|---|
Redondo | Bajo | Alto |
trapezoidal | Moderado | Moderado |
en forma de U | Alto | Bajo |
Elegir el tamaño correcto es igualmente importante. Un canal demasiado estrecho puede provocar una pérdida de presión, mientras que uno demasiado ancho puede desperdiciar material.
3. Presión y velocidad de inyección
Utilizando el análisis del flujo del molde, los diseñadores pueden optimizar la presión de inyección para evitar problemas como rebabas o dificultades de desmolde.
- Control de velocidad de inyección : la velocidad correcta es crucial para mantener la calidad de la superficie, especialmente para piezas estéticas como los interiores de automóviles. El análisis de los frentes de flujo a varias velocidades ayuda a determinar la velocidad óptima para evitar defectos como marcas de flujo.
4. Presión de mantenimiento y tiempo
Una vez llena la cavidad, la presión de mantenimiento compensa la contracción por enfriamiento. He aquí cómo:
- Determinación de la presión de retención : utilizando el análisis de flujo del molde, los diseñadores pueden predecir las presiones de retención necesarias para minimizar las marcas de contracción.
- Configuración del tiempo de retención : El cálculo del tiempo de retención óptimo garantiza una compensación efectiva de la presión durante el enfriamiento, equilibrando la eficiencia y el costo.
5. Tiempo de enfriamiento y parámetros del sistema de enfriamiento
El tiempo de enfriamiento impacta directamente la eficiencia de la producción:
- Optimización del tiempo de enfriamiento : acortar el tiempo de enfriamiento mediante un análisis preciso de la distribución de la temperatura puede mejorar la productividad sin sacrificar la calidad.
- Ajuste de los parámetros del sistema de enfriamiento : El diseño y el caudal de las tuberías de enfriamiento deben diseñarse cuidadosamente para un enfriamiento uniforme y evitar deformaciones.
En resumen, los sistemas de canales desempeñan un papel fundamental a la hora de determinar la calidad de los moldes llenos al influir en varios factores, como el flujo de fusión, la distribución de la presión y la eficiencia de enfriamiento. Al optimizar estos elementos mediante un análisis cuidadoso, los diseñadores pueden mejorar significativamente la calidad del producto y minimizar los defectos.
Los sistemas de canales afectan directamente el flujo de fusión en el moldeo por inyección.Verdadero
El diseño de los sistemas de canales es fundamental para garantizar un flujo de fusión eficiente, lo que afecta la calidad del llenado de las piezas moldeadas.
Aumentar el número de puertas siempre mejora la calidad del llenado.FALSO
Si bien más compuertas pueden ayudar, es posible que no siempre mejoren la calidad del llenado y pueden generar ineficiencias si no se optimizan correctamente.
¿Cómo puede la optimización de la presión de inyección reducir los defectos?
¿Se ha sentido molesto porque los defectos estropearon su producto perfectamente diseñado? Yo también lo he sentido. Reducir los defectos realmente importa. La optimización de la presión de inyección mejora enormemente la calidad del producto. Este cambio probablemente ayude a minimizar defectos molestos.
La optimización de la presión de inyección en el moldeo garantiza un flujo de fusión constante y una presión controlada, lo que reduce defectos como disparos cortos e imperfecciones de la superficie, mejorando así la calidad del producto. Ajustar los tiempos de enfriamiento es crucial para estas mejoras.
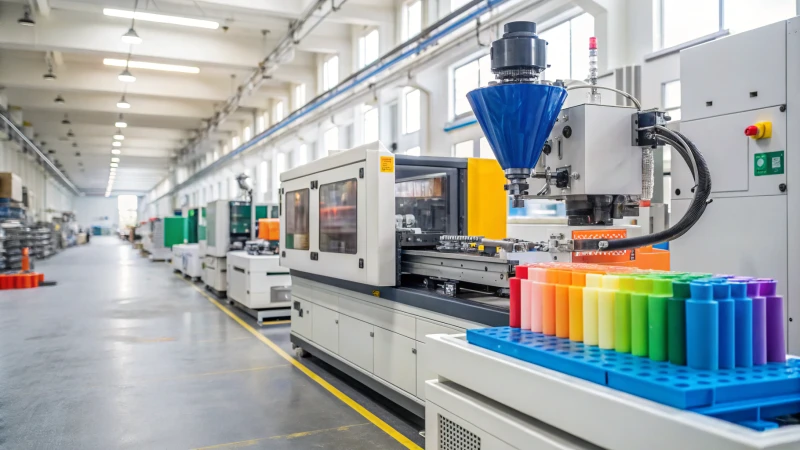
Comprender la optimización de la presión de inyección
Optimizar la presión de inyección es muy importante para reducir los defectos en el proceso de moldeo por inyección. Al analizar y ajustar cuidadosamente la presión a la que se inyecta el plástico fundido en el molde, los fabricantes pueden lograr mejores patrones de llenado y reducir defectos comunes como disparos cortos, huecos y deformaciones.
Por ejemplo, aplicar la presión de inyección adecuada garantiza que la masa fundida llene la cavidad del molde de manera uniforme, especialmente en geometrías complejas. En los casos en que las piezas tienen paredes delgadas y gruesas, aprendí a colocar la compuerta cerca de áreas delgadas para permitir un llenado eficiente. Las herramientas de análisis del flujo de moho se convirtieron en mi arma secreta para identificar estas ubicaciones óptimas.
Factores clave que afectan las tasas de defectos
- Presión de inyección
Encontrar la presión adecuada es crucial. Demasiada presión provoca rebabas y problemas durante la extracción. Muy poca presión da como resultado tiros cortos y vacíos.
Nivel de presión | Posibles defectos |
---|---|
demasiado alto | Flash, dificultades de desmoldeo |
Demasiado bajo | Planos cortos, vacíos |
-
Control de velocidad de inyección
La velocidad de inyección es muy crítica. La velocidad incorrecta provocó marcas de flujo al trabajar en piezas interiores del automóvil. Los ajustes basados en el análisis del flujo del molde mejoraron esto al crear acabados suaves que satisficieron a nuestros clientes. -
Presión de mantenimiento y tiempo
Después del llenado, la presión de mantenimiento correcta es esencial para controlar la contracción a medida que se enfría. Muy poca presión produce marcas de contracción, mientras que demasiada aumenta los tiempos de ciclo y los costos.- Presión de mantenimiento óptima : Mantiene la presión adecuada para evitar defectos durante el enfriamiento.
- Tiempo de retención calculado : permite suficiente tiempo de enfriamiento sin retrasar la producción innecesariamente.
-
Optimización del tiempo de enfriamiento
El enfriamiento solidifica todo; ¡debe ser correcto! ¡Una vez me apresuré a dar este paso y vi que las piezas se deformaban! El análisis del flujo del molde me indicó los tiempos de enfriamiento perfectos que mantuvieron las piezas precisas y mejoraron la eficiencia.- Tiempo de enfriamiento reducido : aumenta la velocidad de producción.
- Distribución uniforme de la temperatura : reduce el riesgo de deformación.
Aplicaciones prácticas de técnicas de optimización
La aplicación de estas técnicas mejoró significativamente la calidad del producto. Por ejemplo, al diseñar tableros de instrumentos de automóviles, las compuertas múltiples eran cruciales para lograr un llenado uniforme y evitar defectos debidos a una distribución desigual de la presión.
En resumen, centrarme en la optimización de la presión de inyección cambió mi visión sobre el moldeo por inyección. Es sorprendente cómo estas estrategias reducen las tasas de defectos y al mismo tiempo mejoran significativamente la calidad del producto. Para obtener más información sobre cómo implementar estas estrategias de manera efectiva, consulte las técnicas de moldeo por inyección .
Al verificar constantemente cada parámetro relacionado con la presión de inyección, la velocidad y el enfriamiento, he optimizado nuestros procesos, lo que nos permite entregar piezas de plástico de alta calidad de manera muy eficiente.
La optimización de la presión de inyección minimiza los disparos cortos en el moldeo.Verdadero
El ajuste adecuado de la presión de inyección garantiza un flujo uniforme del material fundido, lo que reduce significativamente la aparición de disparos cortos durante el proceso de moldeo por inyección.
La alta velocidad de inyección siempre mejora la calidad de la superficie.FALSO
Las altas velocidades de inyección pueden provocar turbulencias, lo que provoca imperfecciones en la superficie en lugar de mejorar la calidad, lo que hace que esta afirmación sea falsa.
¿Cómo puedo mejorar la gestión del tiempo de enfriamiento?
Gestionar el tiempo de enfriamiento es muy importante en la fabricación. Esto es especialmente cierto para el moldeo por inyección. Quiero compartir algunas de las mejores prácticas. Estos no solo mejoran la rapidez con la que se produce la producción, sino que también mejoran la calidad de los productos. ¡Exploremos estas ideas juntos!
Optimice el tiempo de enfriamiento en la fabricación mejorando las ubicaciones de las compuertas, ajustando la configuración de los canales, controlando los parámetros de inyección, configurando con precisión la presión y el tiempo de mantenimiento y refinando los sistemas de enfriamiento.
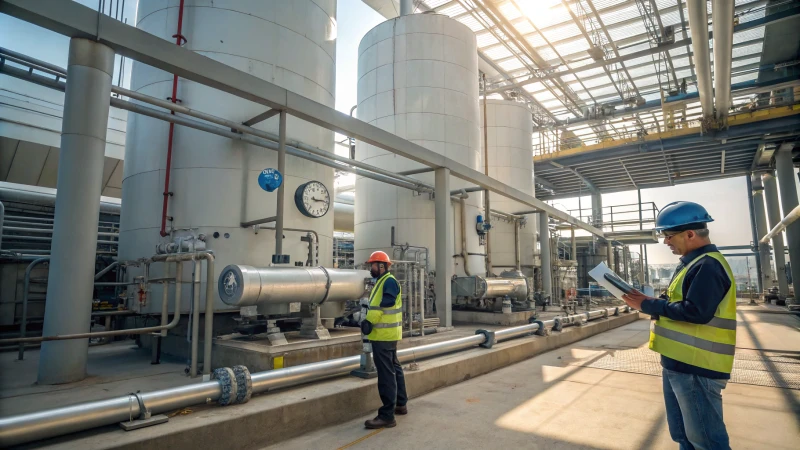
Comprender la gestión del tiempo de enfriamiento
La gestión del tiempo de enfriamiento no es sólo una necesidad técnica. Es una parte clave de la creación de productos de primera calidad que he aprendido a valorar como diseñador. Lo ignoré una vez y luego vi cuánto impactó mi trabajo. Una buena refrigeración aumenta la eficiencia y la calidad del producto. Fabricantes como nosotros consiguen reducir los tiempos de producción y ahorrar dinero sin perder calidad.
Para mejorar la gestión del tiempo de enfriamiento, algunas prácticas recomendadas realmente ayudan:
1. Optimice la ubicación y el número de puertas
La colocación de las puertas y el recuento en el molde son cruciales para un enfriamiento adecuado.
-
Optimización de la ubicación de la puerta : el análisis del flujo del molde me mostró los mejores lugares de la puerta. Aseguró un llenado uniforme de la cavidad del molde. Para formas complejas, colocar las compuertas cerca de secciones más delgadas permitió un fácil llenado y menos defectos.
-
Ajuste del número de puerta : A veces, las piezas grandes necesitan más de una puerta. Mientras trabajábamos en el tablero de un automóvil, utilizamos varias puertas para garantizar un llenado uniforme. Este enfoque redujo significativamente las variaciones de enfriamiento, manteniendo nuestros productos consistentes.
2. Ajustar los parámetros del sistema de canal
Los corredores guían el plástico derretido hacia los moldes. Su diseño afecta en gran medida el tiempo de enfriamiento.
Forma del corredor | Resistencia al flujo | Aplicaciones recomendadas |
---|---|---|
Redondo | Bajo | La mayoría de las aplicaciones |
trapezoidal | Medio | Formas complejas |
en forma de U | Alto | Piezas grandes |
- Diseño equilibrado : en moldes de múltiples cavidades, un sistema de canales equilibrado es crucial para llenar todas las cavidades a la vez. El análisis del flujo del molde ayudó a ajustar los diseños de los canales, lo cual fue vital para fabricar tapas de botellas uniformes.
3. Optimice la presión y la velocidad de inyección
La presión y la velocidad de inyección afectan no solo a las velocidades de llenado sino también a las de enfriamiento.
-
Optimización de la presión de inyección : en un proyecto, la evaluación de la resistencia al flujo ayudó a establecer presiones de inyección óptimas. La alta presión provocó defectos como destellos; la baja presión provocó llenados incompletos. Para las piezas electrónicas de paredes delgadas, los ajustes precisos eran importantes.
-
Control de velocidad de inyección : Controlar la velocidad de inyección es clave para obtener una excelente calidad de superficie. Es crucial ajustar esta velocidad para evitar fallas mientras se mantiene la función.
4. Determinar la presión y el tiempo de mantenimiento
Después de llenar la cavidad, mantener la presión se vuelve crucial para evitar la contracción.
-
Determinación de la presión de mantenimiento : el análisis del flujo del molde predice las presiones de mantenimiento necesarias. Esto es vital para reducir las marcas de contracción en piezas de precisión como engranajes; La presión correcta es clave para mantener las dimensiones precisas.
-
Configuración del tiempo de espera : es importante encontrar el tiempo de espera perfecto; demasiado corto causa defectos mientras que demasiado largo aumenta los tiempos de ciclo. A menudo reviso el espesor de la pared y las propiedades del material para realizar ajustes precisos.
5. Optimización del tiempo de enfriamiento y de los parámetros del sistema
La optimización de los tiempos de enfriamiento eleva enormemente la productividad.
-
Optimización del tiempo de enfriamiento : el análisis detallado ayudó a calcular los tiempos de enfriamiento más cortos manteniendo la calidad alta; Al moldear juguetes pequeños, los ciclos más cortos aumentaron la eficiencia sin perder integridad.
-
Ajuste los parámetros del sistema de enfriamiento : cambiar el diseño, el diámetro y el caudal de los canales de enfriamiento ayuda a una distribución uniforme de la temperatura; Vi cómo un diseño inteligente evita la deformación durante el enfriamiento.
Para obtener más información sobre cómo perfeccionar sus procesos, consulte las técnicas de enfriamiento avanzadas o las mejores prácticas en el diseño de moldes 2 . Me encanta compartir mis experiencias: ¡juntos mejoremos nuestro oficio!
La optimización de la ubicación de la puerta mejora la eficiencia de enfriamiento en el moldeado.Verdadero
La ubicación estratégica de la puerta garantiza una distribución uniforme de la masa fundida, lo que reduce los defectos y mejora la eficiencia de enfriamiento durante el proceso de moldeo por inyección.
No son necesarias varias puertas para piezas moldeadas pequeñas.FALSO
Para componentes más grandes, el uso de múltiples puertas es esencial para lograr un llenado uniforme y un enfriamiento constante, evitando problemas de calidad.
¿Cómo puede el análisis del flujo del molde mejorar la eficiencia de la producción?
¿Alguna vez has pensado en cómo las fábricas ajustan sus métodos de moldeo por inyección para que sean perfectos? El análisis de flujo de molde (MFA) es realmente fascinante. Cambia la industria. Esta herramienta permite a las fábricas mejorar la eficiencia de la producción mejor que nunca. ¡Exploremos juntos esta increíble herramienta!
El análisis de flujo de moldes mejora la eficiencia de la producción al optimizar las ubicaciones de las compuertas, los sistemas de canales, las presiones de inyección y los tiempos de enfriamiento, reducir los defectos, mejorar los tiempos de los ciclos y garantizar resultados de alta calidad en la fabricación.
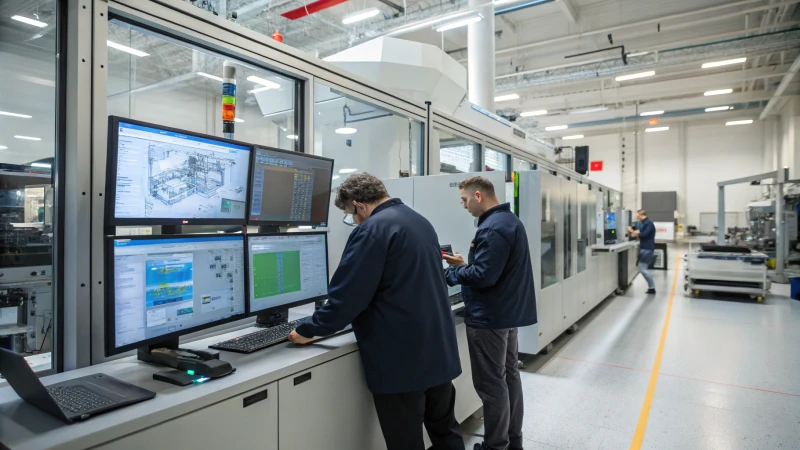
Comprender el análisis del flujo del molde
El análisis de flujo de molde (MFA) es una poderosa herramienta que permite a los fabricantes simular el proceso de moldeo por inyección antes de que comience la producción real. Esta técnica ayuda a identificar defectos potenciales y optimizar los parámetros de diseño para mejorar la eficiencia de la producción.
Al utilizar MFA , los diseñadores pueden analizar varios factores, como el flujo de fusión, los tiempos de enfriamiento y la distribución de presión dentro del molde. Esta capacidad predictiva conduce a una toma de decisiones más informada en el proceso de diseño.
Optimización de la ubicación de la puerta
La ubicación y el número de la puerta juegan un papel fundamental en el proceso de moldeo por inyección.
- Ubicación de la compuerta : la optimización de la ubicación de la compuerta garantiza que la masa fundida llene la cavidad de manera uniforme, evitando problemas como disparos cortos o aire atrapado. Por ejemplo, colocar la compuerta cerca de secciones de paredes delgadas mejora la eficiencia del llenado. Trabajé en un proyecto en el que colocar la compuerta era vital para lograr un llenado uniforme del material fundido. Colocar la puerta cerca de partes delgadas de nuestro objeto detuvo los disparos cortos y el aire atrapado. ¡Aprendí esta lección de la manera más difícil!
- Número de puerta : en casos de piezas grandes o complejas, puede ser necesario utilizar varias puertas. Por ejemplo, una vez, al diseñar el tablero de un automóvil, me mostró que una puerta era insuficiente. MFA me ayudó a ver que se necesitaban varias puertas para lograr una distribución uniforme del material fundido, lo que mejoró enormemente el resultado.
Parámetros del sistema de corredores
El sistema de canales es esencial para controlar cómo fluye la masa fundida hacia las cavidades del molde.
Parámetro | Descripción | Impacto en la producción |
---|---|---|
Forma del corredor | Diferentes formas (redondas, en forma de U) afectan la resistencia al flujo. | Los corredores redondos suelen tener menor resistencia, lo que ayuda a un flujo más suave. |
Tamaño del corredor | El diámetro afecta la caída de presión; demasiado estrecho provoca una pérdida excesiva de presión. | El tamaño adecuado es crucial para mantener la eficiencia en los caudales. |
Un diseño de canal equilibrado garantiza que todas las cavidades se llenen simultáneamente, lo cual es vital en moldes de múltiples cavidades. Recuerdo claramente cambiar la configuración del canal en un molde de tapas de botellas con múltiples cavidades; ¡Cada cavidad llenada al mismo tiempo era como dirigir una sinfonía perfecta!
Control de presión y velocidad de inyección
Otra área clave donde el análisis del flujo del molde mejora la eficiencia de la producción es mediante la optimización de la presión y la velocidad de inyección.
- Presión de inyección : el análisis de la resistencia del flujo ayuda a determinar la presión de inyección óptima, equilibrando el riesgo de defectos como rebabas y garantizando un llenado completo. Al examinar la resistencia al flujo, descubrí las mejores presiones de inyección para diferentes proyectos; demasiado causó defectos mientras que muy poco resultó en tomas cortas.
- Velocidad de inyección : El avance del frente de flujo se puede simular a varias velocidades para garantizar un acabado superficial de alta calidad, lo que es especialmente importante en piezas con estrictos requisitos estéticos, como los interiores de automóviles. Un proyecto de interior de automóvil necesitaba una velocidad específica para evitar defectos en la superficie; MFA me permitió probar diferentes velocidades y lograr un acabado perfecto.
Ajustes de presión y tiempo de mantenimiento
Determinar la presión de retención adecuada y el tiempo después del llenado es crucial para mantener la precisión dimensional y reducir los defectos.
- Presión de mantenimiento : una presión de mantenimiento adecuada compensa la contracción durante el enfriamiento, algo crucial para componentes de alta precisión como los engranajes. Cuando trabajaba con piezas de alta precisión, como engranajes, utilicé MFA para encontrar la presión de sujeción adecuada para evitar la contracción; verlo encajar perfectamente fue muy gratificante.
- Tiempo de retención : El tiempo de retención calculado garantiza que las piezas se enfríen uniformemente sin que aparezcan marcas de deformación o contracción. Encontrar el tiempo de espera ideal es complicado; si aparecen defectos demasiado cortos, mientras que si son demasiado largos aumentan los costes. Con MFA, calculé diseños para alcanzar los mejores resultados.
Tiempo de enfriamiento y parámetros del sistema
El análisis del flujo del molde también contribuye significativamente a optimizar los tiempos y sistemas de enfriamiento.
- Optimización del tiempo de enfriamiento : MFA predice la distribución de temperatura y permite a los diseñadores calcular el tiempo de enfriamiento más corto necesario, mejorando así los tiempos de ciclo. La optimización de los tiempos de enfriamiento transformó una vez mi ciclo para pequeños juguetes de plástico; calcular el tiempo de enfriamiento más corto realmente aumentó la eficiencia y al mismo tiempo mantuvo intacta la calidad de las piezas.
- Diseño del sistema de enfriamiento : el diseño y el tamaño de los canales de enfriamiento se pueden ajustar para garantizar un enfriamiento uniforme y evitar deformaciones. Ajustar la disposición de los canales de refrigeración se volvió natural con MFA; incluso el enfriamiento puede detener la deformación, especialmente en piezas más grandes.
En conclusión, emplear el análisis del flujo del molde en los procesos de producción no sólo identifica problemas potenciales sino que también allana el camino para mejoras que conduzcan a una mayor eficiencia y una reducción de costos. Para obtener más información sobre las mejores prácticas en el diseño de moldes, consulte técnicas avanzadas 3 .
El análisis del flujo del molde ayuda a prevenir defectos en el moldeo por inyección.Verdadero
Al simular el proceso de inyección, el análisis del flujo del molde identifica defectos potenciales, mejorando la calidad general de las piezas producidas.
La optimización de la ubicación de las puertas aumenta los tiempos del ciclo de producción.FALSO
La posición correcta de la compuerta mejora el flujo de fusión y reduce los tiempos de ciclo, lo que lleva a procesos de producción más eficientes.
Conclusión
El análisis de flujo de molde mejora el moldeo por inyección al optimizar las ubicaciones de las compuertas, los sistemas de canales, las presiones de inyección y los tiempos de enfriamiento para mejorar la eficiencia y la calidad del producto.
-
Este enlace proporciona un análisis en profundidad sobre la optimización de las ubicaciones de las puertas para obtener mejores resultados en el diseño de moldes. ↩
-
Descubra ideas y estrategias de expertos sobre prácticas efectivas de gestión del tiempo de enfriamiento para mejorar la eficiencia de su producción. ↩
-
Descubra cómo MFA puede mejorar significativamente sus procesos de fabricación y reducir costos de manera efectiva. ↩