Avez-vous déjà rencontré des problèmes avec vos projets de moulage par injection ? Explorons comment l'analyse des flux de moules peut tout transformer pour vous !
L'analyse du flux de moule optimise le moulage par injection en ajustant l'emplacement des portes, les systèmes de canaux, la pression d'injection et le temps de refroidissement, améliorant ainsi l'efficacité et la fluidité de la fabrication.
Je pense à mon parcours dans la conception de produits. Je me souviens des nombreuses heures que j'ai passées à résoudre les problèmes du processus de moulage par injection. J’ai découvert Mold Flow Analysis à cette époque. Cet outil est devenu une bouée de sauvetage pour moi. J'ai optimisé des paramètres tels que l'emplacement de la porte et la pression d'injection. J'ai commencé à remarquer des améliorations très impressionnantes. L'ajustement de l'emplacement de la porte m'a aidé à éviter les plans courts et les pièges à air dans les pièces complexes. Les pièces s'assemblent comme un puzzle !
L’analyse du flux de moule améliore l’efficacité du moulage par injection.Vrai
Cette affirmation est vraie car l’analyse des flux de moule permet d’optimiser les paramètres, conduisant à une meilleure efficacité de fabrication.
L'emplacement de la porte n'affecte pas la qualité du produit lors du moulage.FAUX
Cette affirmation est fausse car l’emplacement de la porte a un impact significatif sur le flux et la qualité du produit moulé.
- 1. Qu’est-ce que l’analyse des flux de moule et pourquoi est-elle importante ?
- 2. Quel est l'impact de l'emplacement de la porte sur le moulage par injection ?
- 3. Quel est l'impact des systèmes de guidage sur la qualité de remplissage dans le moulage par injection ?
- 4. Comment l’optimisation de la pression d’injection peut-elle réduire les défauts ?
- 5. Comment puis-je améliorer ma gestion du temps de refroidissement ?
- 6. Comment l’analyse des flux de moules peut-elle améliorer l’efficacité de la production ?
- 7. Conclusion
Qu’est-ce que l’analyse des flux de moule et pourquoi est-elle importante ?
Vous êtes-vous déjà demandé comment les fabricants vérifient que chaque pièce en plastique qu'ils créent est parfaite ? L’analyse des flux de moules détient la réponse. Cet outil optimise le processus de moulage par injection. C’est également un gage de qualité. L'efficacité s'améliore avec son utilisation. C’est vraiment important !
Mold Flow Analysis (MFA) utilise des simulations informatiques dans le moulage par injection pour optimiser le placement des portes, les systèmes de canaux et les méthodes de refroidissement, garantissant ainsi des produits de haute qualité et réduisant les défauts.
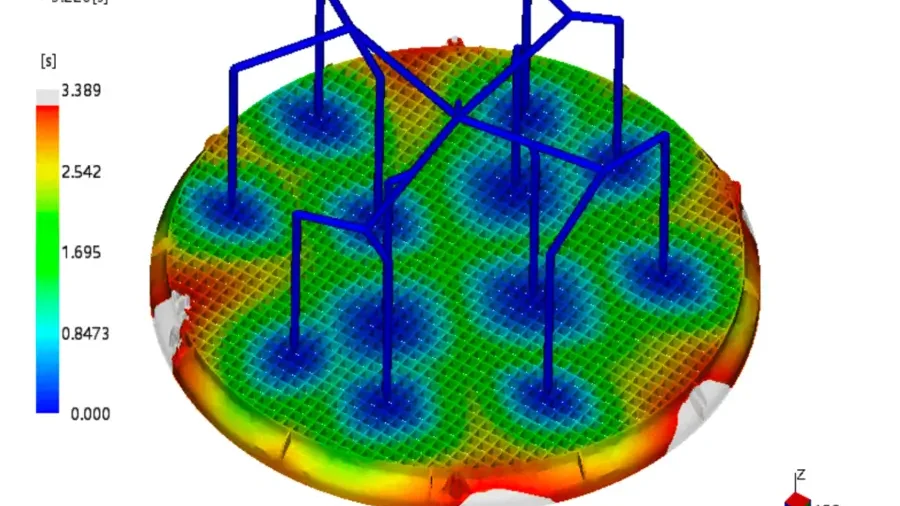
L'analyse de flux de moule (MFA) est une technologie de simulation qui joue un rôle central dans le processus de moulage par injection. Il permet aux concepteurs de prédire comment le plastique fondu s'écoule à travers un moule, garantissant ainsi un remplissage, un refroidissement et une solidification optimaux. Comprendre la MFA peut améliorer considérablement la qualité de la production tout en réduisant les coûts.
Importance de l’emplacement et du numéro de la porte
Un aspect essentiel de la MFA consiste à déterminer l' emplacement et le numéro de la porte . Un emplacement de porte optimisé garantit que la matière fondue remplit la cavité de manière uniforme, en particulier dans les formes géométriques complexes. Par exemple, lors de la production d'une pièce en plastique comportant à la fois des sections fines et épaisses, placer la porte à proximité de la zone à paroi mince permet d'obtenir un meilleur écoulement.
Dans un projet, j'ai placé le portail à proximité d'une fine section d'une pièce en plastique. Cela nous a donné un déroulement parfait et a vraiment amélioré le résultat.
En plus de l'emplacement, MFA peut également indiquer si plusieurs portes sont nécessaires. Par exemple, le tableau de bord d’une voiture peut nécessiter plusieurs portes pour assurer un remplissage uniforme dans toute sa grande cavité. Cette optimisation se traduit finalement par une réduction des défauts et une meilleure qualité du produit.
Paramètres du système de coureur
Le système de canaux joue un rôle important dans le flux de matière plastique. MFA aide à sélectionner la bonne forme et taille , ce qui affecte la résistance à l'écoulement. Un coureur rond a généralement une résistance inférieure à celle des coureurs trapézoïdaux ou en forme de U.
Forme du coureur | Résistance à l'écoulement | Applications appropriées |
---|---|---|
Rond | Faible | Usage général |
Trapézoïdal | Moyen | Pièces complexes d'épaisseur variable |
en forme de U | Haut | Production en grand volume |
De plus, MFA garantit que les conceptions des canaux sont équilibrées dans les moules multi-empreintes, contribuant ainsi au remplissage simultané de chaque cavité. Je me souviens d'un projet impliquant des capsules de bouteilles en plastique où le maintien de l'uniformité était essentiel ; nous avions besoin de les remplir tous en même temps.
Optimisation de la pression et de la vitesse d'injection
MFA permet également d’optimiser la pression d’injection en analysant la résistance à l’écoulement dans la cavité du moule. Si la pression est trop élevée, des problèmes tels que des problèmes de flash et de démoulage peuvent survenir, tandis qu'une pression trop faible peut conduire à des tirs courts. L’optimisation de la pression d’injection est une autre leçon importante du MFA ; le réglage de la pression correcte était crucial pour les boîtiers électroniques à paroi mince.
De plus, le contrôle de la vitesse d’injection est essentiel pour obtenir des finitions de haute qualité sur les produits. Différentes vitesses affectent le front d’écoulement ; pour des pièces visuellement attrayantes comme celles des voitures, les simulations MFA m'ont conseillé sur les vitesses pour des surfaces parfaites et sans défauts.
Mettre de la pression et du temps
La phase de maintien après le remplissage est essentielle pour compenser le retrait dû au refroidissement. Après le remplissage du moule, cette étape compense le retrait lors du refroidissement ; J'ai utilisé les connaissances du MFA à de nombreuses reprises pour réduire les marques de retrait sur des pièces précises comme les engrenages en prédisant la pression de maintien .
Déterminer le temps de maintien est tout aussi essentiel ; en fonction de l'épaisseur des parois et des propriétés des matériaux, MFA calcule les temps optimaux garantissant l'intégrité sans allonger inutilement les cycles de production.
Temps de refroidissement et paramètres du système
Enfin, MFA optimise le temps de refroidissement en analysant la répartition de la température pendant les processus de refroidissement. Cette étape s'est avérée essentielle pour améliorer l'efficacité de la production tout en empêchant la déformation des pièces ; la réduction des temps de refroidissement a considérablement augmenté la production tout en maintenant la qualité au cours d'un projet de jouet.
MFA aide également à concevoir des systèmes de refroidissement en évaluant la disposition, le diamètre et le débit des tuyaux de refroidissement pour garantir un refroidissement uniforme des grandes pièces. Un système de refroidissement efficace évite la déformation, ce que j'ai appris lors de défis de projets précédents.
En intégrant l'analyse des flux de moules dans nos processus de conception et de production, nous augmentons la qualité des produits tout en réduisant les déchets et en améliorant l'efficacité globale.
L’analyse du flux de moule améliore l’efficacité du moulage par injection.Vrai
MFA optimise les processus en prédisant le flux de plastique, en améliorant l’efficacité et en réduisant les défauts de production.
Plusieurs portes ne sont pas nécessaires dans Mold Flow Analysis.FAUX
La MFA indique souvent la nécessité de plusieurs portes pour garantir un remplissage uniforme dans les grandes cavités, crucial pour la qualité.
Quel est l'impact de l'emplacement de la porte sur le moulage par injection ?
Avez-vous déjà réfléchi à la façon dont la position d'une porte dans le moulage par injection modifie le processus ? C'est vraiment intéressant ! Explorons l'impact de ce détail important sur nos tâches et la qualité de ce que nous produisons.
L'emplacement des portes dans le moulage par injection affecte l'écoulement de la matière fondue, l'efficacité du remplissage et les taux de défauts. Son optimisation améliore la qualité des pièces et minimise les problèmes de production.
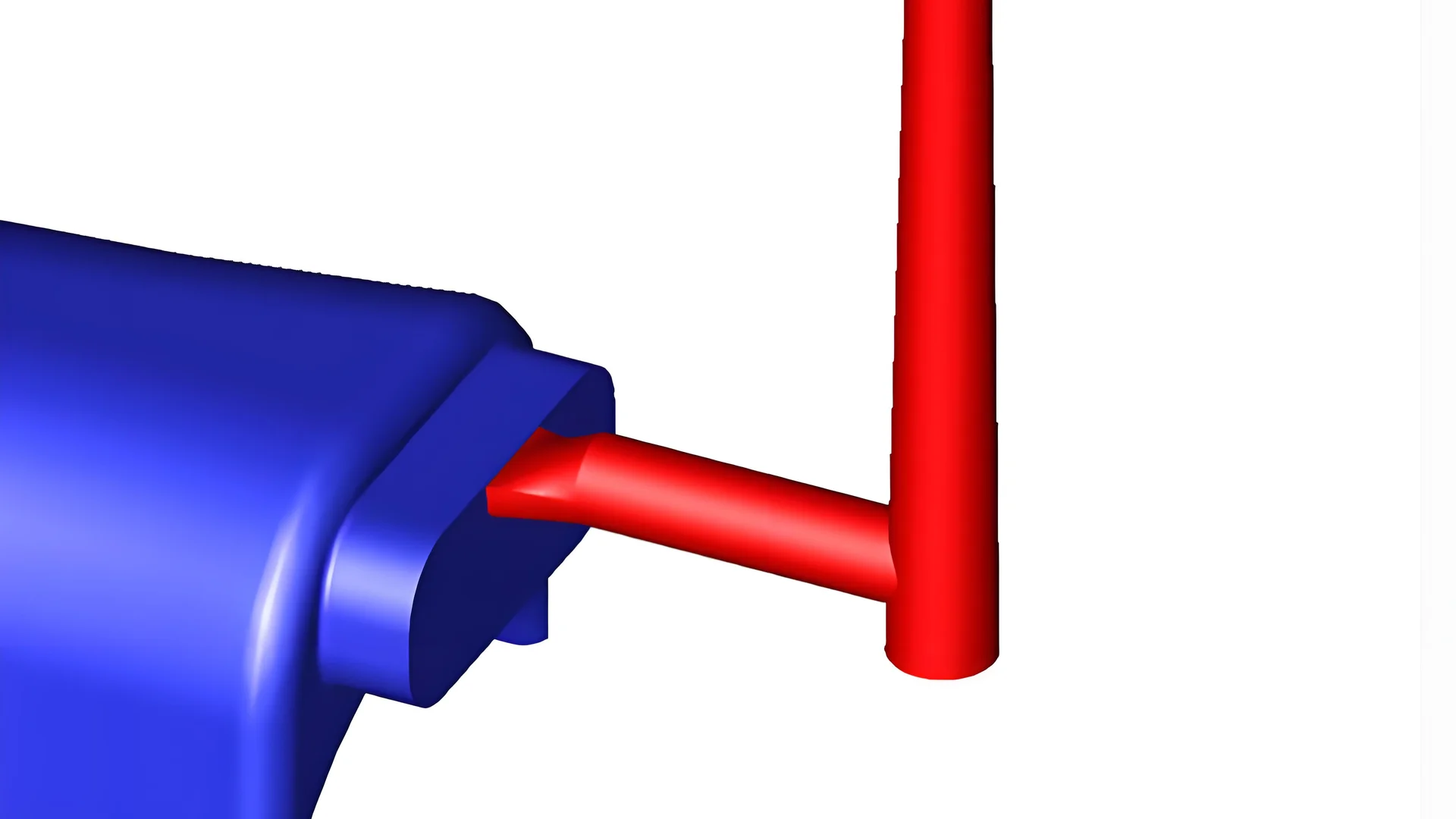
Comprendre l'emplacement des portes dans le moulage par injection
Le placement des portes dans le moulage par injection façonne nos pièces moulées. Je me souviens d'un projet où la position de la porte changeait complètement le produit final. La bonne porte affecte beaucoup l'écoulement de la matière fondue, l'efficacité du remplissage et les taux de défauts. Une bonne optimisation améliore la qualité des pièces et minimise les problèmes de production. C'est ce que veut tout designer.
L'optimisation de l' emplacement de la porte garantit un débit uniforme et évite les défauts tels que les tirs courts ou les pièges à air. Une fois, j'ai travaillé sur une pièce complexe avec des sections épaisses et fines. Placer la porte près de la zone la plus fine a permis un remplissage rapide, évitant ainsi les poches d'air emprisonnées gênantes.
Importance de l’ajustement du numéro de porte
Parfois, une seule porte ne suffit pas, notamment pour les formes grandes ou complexes. L'analyse du flux de moule joue un rôle essentiel pour décider si plusieurs portes sont nécessaires.
Prenons l'exemple d'un tableau de bord de voiture où il est crucial d'obtenir un remplissage uniforme de la matière fondue. Cela nécessite souvent un nombre accru de portes pour garantir une qualité constante dans tout le moule. Le tableau suivant illustre ce concept :
Type de pièce | Portes recommandées | Raison des portes multiples |
---|---|---|
Tableau de bord de voiture | 2-4 | Assure un remplissage uniforme de la matière fondue |
Bouchons de bouteilles en plastique | 1-2 | La forme simplifiée permet une porte unique |
Paramètres du système de coureur
La conception du système de canaux est très importante car elle détermine l'efficacité avec laquelle la matière fondue se déplace de la porte à la cavité. La forme et la taille des canaux ont un impact sur la résistance à l’écoulement et la perte de pression. Généralement, les canaux ronds sont préférés en raison de leur plus faible résistance à l’écoulement.
L'analyse du flux de moule aide à sélectionner les paramètres optimaux des canaux pour des transitions en douceur sans perte de pression. Ceci est important, en particulier dans les moules multi-empreintes où des taux de remplissage égaux sont essentiels.
Contrôle de la pression et de la vitesse d'injection
L'emplacement de la porte influence également la pression d'injection et la vitesse utilisées pendant le processus de moulage. L'analyse de la résistance à l'écoulement en différents points m'a permis d'optimiser les pressions pour éviter des défauts comme des éclairs ou des difficultés de démoulage.
Le réglage de la vitesse d’injection est également crucial ; lors de la création de pièces de haute qualité, comme les intérieurs de voitures, le contrôle de la vitesse d’injection évite les traces d’écoulement disgracieuses.
Paramètres de pression et de temps de maintien
Après le remplissage, une pression de maintien correcte est cruciale. J'ai travaillé avec des engrenages de haute précision où la prévision des pressions de maintien a permis de minimiser les marques de retrait et les problèmes dimensionnels.
Fixer des temps d’attente appropriés est un exercice d’équilibre ; trop court provoque des marques de rétrécissement visibles tandis que trop long allonge inutilement les temps de cycle. Le tableau suivant présente les temps de maintien optimaux en fonction de l'épaisseur de la paroi :
Épaisseur de paroi (mm) | Temps de maintien recommandé (secondes) |
---|---|
< 1 | 5-7 |
1-3 | 8-10 |
> 3 | 12-15 |
Optimisation du temps de refroidissement
Enfin, le temps de refroidissement et les paramètres du système sont très importants. Saviez-vous que l’emplacement de la porte affecte l’efficacité du refroidissement ? J'ai conçu des configurations de tuyaux de refroidissement pour un refroidissement uniforme afin d'améliorer l'efficacité sans perte de qualité ?
L'optimisation des temps de refroidissement grâce à l'analyse du flux de moule peut améliorer considérablement l'efficacité de la production sans compromettre l'intégrité des pièces.
Par exemple, les petits jouets en plastique peuvent bénéficier de temps de refroidissement réduits tout en garantissant une qualité adéquate.
En conclusion, il est essentiel de connaître l'impact de l'emplacement des portes sur de nombreux facteurs pour optimiser la qualité des pièces et l'efficacité de la production. Pour en savoir plus sur les stratégies efficaces de placement de portes, explorez ce guide détaillé 1 .
L'emplacement de la porte affecte les modèles d'écoulement de la matière fondue dans le moulage par injection.Vrai
L'emplacement des portes influence directement la façon dont le matériau en fusion remplit le moule, ce qui a un impact sur la qualité et l'efficacité globales des pièces.
Plusieurs portes ne sont pas nécessaires pour les conceptions de moules complexes.FAUX
Dans les géométries complexes, plusieurs portes peuvent être essentielles pour garantir un remplissage uniforme et minimiser les défauts pendant le processus d'injection.
Quel est l'impact des systèmes de guidage sur la qualité de remplissage dans le moulage par injection ?
Avez-vous déjà pensé à la façon dont une petite pièce pourrait réellement changer la qualité de vos pièces moulées ? Examinons les systèmes de canaux et voyons à quel point ils sont importants dans le moulage par injection. Ces systèmes permettent de remplir correctement les moules.
Les systèmes de canaux dans le moulage par injection influencent le flux de matière, la répartition de la pression et le refroidissement. Un placement correct des portes, des formes de canaux et des paramètres d'injection appropriés sont essentiels pour obtenir des pièces de haute qualité présentant moins de défauts.
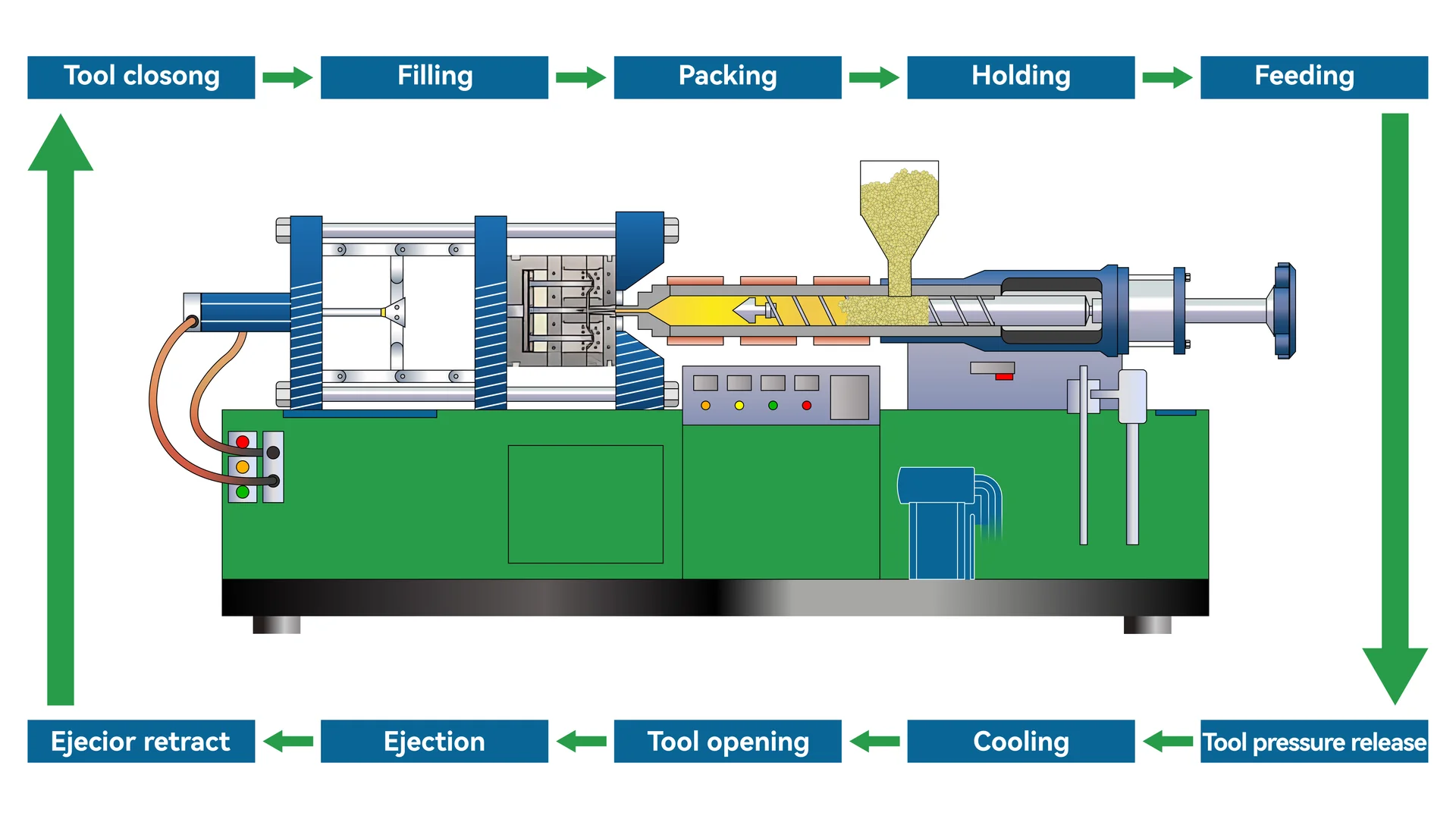
Comprendre les systèmes de coureurs
Les systèmes de canaux sont des composants essentiels du processus de moulage par injection qui jouent un rôle important en garantissant que la matière fondue remplit les cavités du moule de manière efficace et efficiente. La conception du système de guidage peut influencer la qualité globale de remplissage des composants en plastique.
1. Emplacement et nombre des portes
L'optimisation de l'emplacement des portes est essentielle pour une distribution uniforme de la matière fondue. Pour les géométries complexes, l’analyse du flux de moule peut déterminer les meilleurs points d’entrée pour la matière fondue.
- Exemple : Dans une section à paroi mince d'une pièce, placer la porte à proximité de cette zone garantit un remplissage rapide, réduisant ainsi les risques de défauts tels que des tirs courts ou des pièges à air.
- Numéro de porte : Augmenter le nombre de portes peut être nécessaire pour les grandes pièces afin d'obtenir un remplissage uniforme.
2. Paramètres du système de canaux
La forme et la taille des canaux affectent la résistance à l'écoulement. Les coureurs peuvent être conçus sous différentes formes :
Forme du coureur | Résistance à l'écoulement | Efficacité |
---|---|---|
Rond | Faible | Haut |
Trapézoïdal | Modéré | Modéré |
en forme de U | Haut | Faible |
Choisir la bonne taille est tout aussi important. Un canal trop étroit peut entraîner une perte de pression, tandis qu'un canal trop large peut entraîner un gaspillage de matériau.
3. Pression et vitesse d'injection
Grâce à l'analyse du flux de moule, les concepteurs peuvent optimiser la pression d'injection pour éviter des problèmes tels que des éclairs ou des difficultés de démoulage.
- Contrôle de la vitesse d'injection : La bonne vitesse est cruciale pour maintenir la qualité de la surface, en particulier pour les pièces esthétiques comme les intérieurs d'automobile. L'analyse des fronts d'écoulement à différentes vitesses aide à déterminer la vitesse optimale pour éviter les défauts tels que les marques d'écoulement.
4. Pression de maintien et durée
Une fois la cavité remplie, la pression de maintien compense le retrait de refroidissement. Voici comment procéder :
- Détermination de la pression de maintien : grâce à l'analyse du flux de moule, les concepteurs peuvent prédire les pressions de maintien nécessaires pour minimiser les marques de retrait.
- Réglage du temps de maintien : Le calcul du temps de maintien optimal garantit une compensation efficace de la pression pendant le refroidissement, équilibrant ainsi l'efficacité et le coût.
5. Temps de refroidissement et paramètres du système de refroidissement
Le temps de refroidissement a un impact direct sur l'efficacité de la production :
- Optimisation du temps de refroidissement : raccourcir le temps de refroidissement grâce à une analyse précise de la répartition de la température peut améliorer la productivité sans sacrifier la qualité.
- Réglage des paramètres du système de refroidissement : La disposition et le débit des tuyaux de refroidissement doivent être soigneusement conçus pour un refroidissement uniforme afin d'éviter toute déformation.
En résumé, les systèmes de canaux jouent un rôle central dans la détermination de la qualité des moules remplis en influençant divers facteurs tels que l'écoulement de la matière fondue, la répartition de la pression et l'efficacité du refroidissement. En optimisant ces éléments grâce à une analyse minutieuse, les concepteurs peuvent améliorer considérablement la qualité du produit tout en minimisant les défauts.
Les systèmes de canaux affectent directement l’écoulement de la matière fondue dans le moulage par injection.Vrai
La conception des systèmes de canaux est essentielle pour garantir un écoulement efficace de la matière fondue, ce qui a un impact sur la qualité de remplissage des pièces moulées.
L'augmentation du nombre de portes améliore toujours la qualité du remplissage.FAUX
Même si un plus grand nombre de portes peut aider, elles n’améliorent pas toujours la qualité du remplissage et peuvent conduire à des inefficacités si elles ne sont pas correctement optimisées.
Comment l’optimisation de la pression d’injection peut-elle réduire les défauts ?
Vous êtes-vous senti contrarié parce que des défauts ont gâché votre produit parfaitement conçu ? J'ai ressenti cela aussi. La réduction des défauts est vraiment importante. L’optimisation de la pression d’injection améliore considérablement la qualité du produit. Ce changement contribue probablement à minimiser les défauts gênants.
L'optimisation de la pression d'injection dans le moulage garantit un écoulement de matière fondu constant et une pression contrôlée, réduisant ainsi les défauts tels que les tirs courts et les imperfections de surface, améliorant ainsi la qualité du produit. L’ajustement des temps de refroidissement est crucial pour ces améliorations.
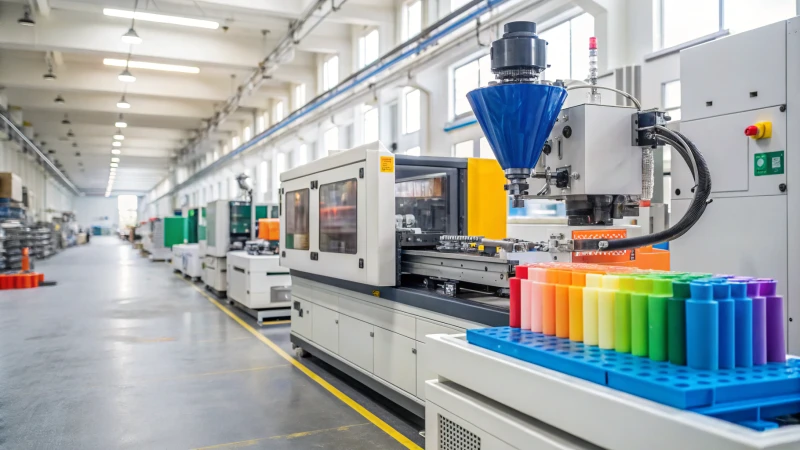
Comprendre l'optimisation de la pression d'injection
L'optimisation de la pression d'injection est très importante pour réduire les défauts dans le processus de moulage par injection. En analysant et en ajustant soigneusement la pression à laquelle le plastique fondu est injecté dans le moule, les fabricants peuvent obtenir de meilleurs modèles de remplissage et réduire les défauts courants tels que les tirs courts, les vides et les déformations.
Par exemple, l’application de la bonne pression d’injection garantit que la matière fondue remplit uniformément la cavité du moule, en particulier dans les géométries complexes. Dans les cas où les pièces ont des parois à la fois fines et épaisses, j'ai appris à placer la porte à proximité de zones minces pour permettre un remplissage efficace. Les outils d’analyse des flux de moules sont devenus mon arme secrète pour identifier ces emplacements optimaux.
Facteurs clés ayant un impact sur les taux de défauts
- Pression d'injection
Trouver la bonne pression est crucial. Une pression trop élevée provoque des éclairs et des problèmes lors du retrait. Trop peu de pression entraîne des tirs courts et des vides.
Niveau de pression | Défauts possibles |
---|---|
Trop haut | Flash, difficultés de démoulage |
Trop bas | Plans courts, vides |
-
Contrôle de la vitesse d'injection
La vitesse d'injection est très critique. Une vitesse incorrecte provoquait des traces d'écoulement lors des travaux sur les pièces intérieures de la voiture. Les ajustements basés sur l'analyse du flux de moule ont amélioré ce résultat en créant des finitions lisses qui ont satisfait nos clients. -
Pression et durée de maintien
Après le remplissage, une pression de maintien correcte est essentielle pour contrôler le retrait lors du refroidissement. Une pression trop faible entraîne des marques de rétrécissement, tandis qu'une pression trop faible augmente les temps de cycle et les coûts.- Pression de maintien optimale : maintient la bonne pression pour éviter les défauts pendant le refroidissement.
- Temps de maintien calculé : permet un temps de refroidissement suffisant sans retarder inutilement la production.
-
Optimisation du temps de refroidissement
Le refroidissement solidifie le tout ; ça doit être vrai ! Une fois, j'ai précipité cette étape et j'ai vu des pièces se déformer ! L’analyse du flux de moule m’a indiqué les temps de refroidissement parfaits qui ont permis de conserver la précision des pièces et d’améliorer l’efficacité.- Temps de refroidissement raccourci : augmente la vitesse de production.
- Répartition uniforme de la température : réduit le risque de déformation.
Applications pratiques des techniques d'optimisation
L'application de ces techniques a considérablement amélioré la qualité du produit. Par exemple, lors de la conception des tableaux de bord des voitures, plusieurs portes étaient cruciales pour obtenir un remplissage uniforme et éviter les défauts dus à une répartition inégale de la pression.
En résumé, me concentrer sur l’optimisation de la pression d’injection a changé ma vision du moulage par injection. Il est étonnant de constater à quel point ces stratégies réduisent les taux de défauts tout en améliorant considérablement la qualité des produits. Pour plus d'informations sur la manière de mettre en œuvre efficacement ces stratégies, consultez les techniques de moulage par injection .
En vérifiant constamment chaque paramètre lié à la pression d'injection, à la vitesse et au refroidissement, j'ai rationalisé nos processus nous permettant de livrer des pièces en plastique de haute qualité de manière très efficace.
L'optimisation de la pression d'injection minimise les tirs courts lors du moulage.Vrai
Un réglage correct de la pression d'injection garantit un écoulement uniforme de la matière fondue, réduisant considérablement l'apparition de tirs courts pendant le processus de moulage par injection.
Une vitesse d'injection élevée améliore toujours la qualité de la surface.FAUX
Des vitesses d'injection élevées peuvent provoquer des turbulences, entraînant des imperfections de surface plutôt que d'améliorer la qualité, ce qui rend cette affirmation fausse.
Comment puis-je améliorer ma gestion du temps de refroidissement ?
La gestion du temps de refroidissement est très importante dans le secteur manufacturier. Cela est particulièrement vrai pour le moulage par injection. Je souhaite partager quelques bonnes pratiques. Ceux-ci améliorent non seulement la rapidité de la production, mais améliorent également la qualité des produits. Explorons ces idées ensemble !
Optimisez le temps de refroidissement dans la fabrication en améliorant l'emplacement des portes, en ajustant les paramètres des canaux, en contrôlant les paramètres d'injection, en réglant avec précision la pression et le temps de maintien et en affinant les systèmes de refroidissement.
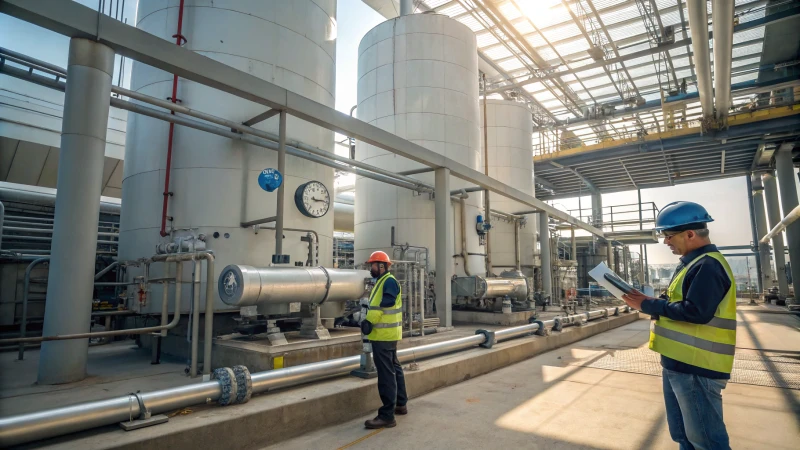
Comprendre la gestion du temps de refroidissement
La gestion du temps de refroidissement n’est pas seulement une nécessité technique. C'est un élément clé de la création de produits haut de gamme que j'ai appris à valoriser en tant que designer. Je l'ai ignoré une fois et j'ai vu plus tard à quel point cela avait un impact sur mon travail. Un bon refroidissement augmente l’efficacité et la qualité du produit. Les fabricants comme nous parviennent à réduire les délais de production et à économiser de l’argent sans perdre en qualité.
Pour maîtriser la gestion du temps de refroidissement, quelques bonnes pratiques sont vraiment utiles :
1. Optimiser l'emplacement et le nombre de portes
Le placement des portes et le comptage dans le moule sont cruciaux pour un refroidissement correct.
-
Optimisation de l'emplacement des portes : L'analyse du flux de moule m'a montré les meilleurs points de porte. Cela garantissait un remplissage uniforme de la cavité du moule. Pour les formes complexes, placer les portes à proximité de sections plus fines a permis un remplissage facile et moins de défauts.
-
Ajustement du numéro de porte : Parfois, les grandes pièces nécessitent plus d'une porte. En travaillant sur un tableau de bord de voiture, nous avons utilisé plusieurs portes pour assurer un remplissage uniforme. Cette approche réduit considérablement les variations de refroidissement, garantissant ainsi la cohérence de nos produits.
2. Ajuster les paramètres du système de coureur
Les glissières guident le plastique fondu dans les moules. Leur conception affecte grandement le temps de refroidissement.
Forme du coureur | Résistance à l'écoulement | Applications recommandées |
---|---|---|
Rond | Faible | La plupart des applications |
Trapézoïdal | Moyen | Formes complexes |
en forme de U | Haut | Grandes pièces |
- Conception équilibrée : dans les moules multi-empreintes, un système de canaux équilibrés est crucial pour remplir toutes les cavités en même temps. L'analyse du flux de moule a permis d'ajuster la conception des canaux, ce qui était essentiel pour fabriquer des capsules de bouteilles uniformes.
3. Optimiser la pression et la vitesse d'injection
La pression et la vitesse d’injection ont un impact non seulement sur les taux de remplissage mais également sur les taux de refroidissement.
-
Optimisation de la pression d'injection : dans un projet, l'évaluation de la résistance à l'écoulement a permis de définir des pressions d'injection optimales. La haute pression a provoqué des défauts comme le flash ; la basse pression a conduit à des remplissages incomplets. Pour les pièces électroniques à paroi mince, des ajustements précis étaient importants.
-
Contrôle de la vitesse d'injection : Le contrôle de la vitesse d'injection est la clé d'une excellente qualité de surface. Il est crucial d'ajuster cette vitesse pour éviter les défauts tout en conservant la fonction.
4. Déterminer la pression et le temps de maintien
Après avoir rempli la cavité, maintenir la pression devient crucial pour éviter le retrait.
-
Détermination de la pression de maintien : l'analyse du flux de moule prédit les pressions de maintien nécessaires. Ceci est essentiel pour réduire les marques de retrait sur les pièces de précision comme les engrenages ; une pression correcte est essentielle pour maintenir les dimensions exactes.
-
Réglage du temps de maintien : Il est important de trouver le temps de maintien idéal ; trop court provoque des défauts tandis que trop long augmente les temps de cycle. Je vérifie souvent l’épaisseur des parois et les propriétés des matériaux pour des ajustements précis.
5. Optimisation du temps de refroidissement et des paramètres du système
L’optimisation des temps de refroidissement augmente considérablement la productivité.
-
Optimisation du temps de refroidissement : une analyse détaillée a permis de calculer les temps de refroidissement les plus courts tout en maintenant une qualité élevée ; lors du moulage de petits jouets, des cycles plus courts ont amélioré l'efficacité sans perdre en intégrité.
-
Ajustez les paramètres du système de refroidissement : la modification de la disposition, du diamètre et du débit des canaux de refroidissement contribue à une répartition uniforme de la température ; J'ai vu comment une conception intelligente empêche la déformation pendant le refroidissement.
Pour plus d'informations sur l'amélioration de vos processus, consultez les techniques de refroidissement avancées ou les meilleures pratiques en matière de conception de moules 2 . J'aime partager mes expériences – ensemble, améliorons notre métier !
L'optimisation de l'emplacement des portes améliore l'efficacité du refroidissement lors du moulage.Vrai
Le placement stratégique des portes garantit une répartition uniforme de la matière fondue, réduisant ainsi les défauts et améliorant l'efficacité du refroidissement pendant le processus de moulage par injection.
Plusieurs portes sont inutiles pour les petites pièces moulées.FAUX
Pour les composants plus gros, l’utilisation de plusieurs portes est essentielle pour obtenir un remplissage et un refroidissement uniformes, évitant ainsi les problèmes de qualité.
Comment l’analyse des flux de moules peut-elle améliorer l’efficacité de la production ?
Avez-vous déjà réfléchi à la façon dont les usines ajustent leurs méthodes de moulage par injection pour être parfaites ? L’analyse des flux de moules (MFA) est vraiment fascinante. Cela change l’industrie. Cet outil permet aux usines d’améliorer plus que jamais l’efficacité de leur production. Explorons ensemble cet outil étonnant !
L'analyse des flux de moule améliore l'efficacité de la production en optimisant les emplacements des portes, les systèmes de canaux, les pressions d'injection et les temps de refroidissement, en réduisant les défauts, en améliorant les temps de cycle et en garantissant des résultats de fabrication de haute qualité.
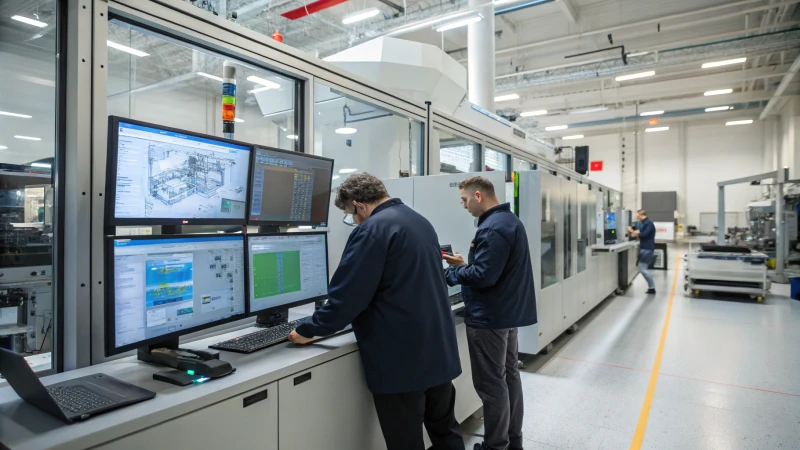
Comprendre l'analyse des flux de moule
L'analyse du flux de moule (MFA) est un outil puissant qui permet aux fabricants de simuler le processus de moulage par injection avant le début de la production réelle. Cette technique permet d'identifier les défauts potentiels et d'optimiser les paramètres de conception pour améliorer l'efficacité de la production.
En utilisant la MFA , les concepteurs peuvent analyser divers facteurs tels que l'écoulement de la matière fondue, les temps de refroidissement et la répartition de la pression dans le moule. Cette capacité prédictive conduit à une prise de décision plus éclairée dans le processus de conception.
Optimisation de l'emplacement des portes
L'emplacement et le nombre des portes jouent un rôle essentiel dans le processus de moulage par injection.
- Emplacement de la porte : l'optimisation de l'emplacement de la porte garantit que la matière fondue remplit la cavité de manière uniforme, évitant ainsi des problèmes tels que des tirs courts ou de l'air emprisonné. Par exemple, placer la porte à proximité de sections à parois minces améliore l’efficacité du remplissage. J'ai travaillé sur un projet où le placement de la porte était vital pour un remplissage uniforme de la matière fondue. Placer la porte à proximité de parties minces de notre objet a arrêté les tirs courts et l'air emprisonné. J'ai appris cette leçon à mes dépens !
- Numéro de porte : Dans le cas de pièces volumineuses ou complexes, il peut être nécessaire d'utiliser plusieurs portes. Par exemple, la conception d’un tableau de bord de voiture m’a montré un jour qu’une seule porte ne suffisait pas. MFA m'a aidé à comprendre que plusieurs portes étaient nécessaires pour une propagation uniforme de la matière fondue, améliorant ainsi considérablement le résultat.
Paramètres du système de coureur
Le système de canaux est essentiel pour contrôler la manière dont la matière fondue s'écoule dans les cavités du moule.
Paramètre | Description | Impact sur la production |
---|---|---|
Forme du coureur | Différentes formes (rondes, en forme de U) affectent la résistance à l'écoulement. | Les coureurs ronds ont généralement une résistance plus faible, ce qui facilite un écoulement plus fluide. |
Taille du coureur | Le diamètre a un impact sur la chute de pression ; trop étroit entraîne une perte de pression excessive. | Un dimensionnement approprié est crucial pour maintenir l’efficacité des débits. |
Une conception équilibrée des canaux garantit que toutes les cavités se remplissent simultanément, ce qui est vital dans les moules multi-empreintes. Je me souviens clairement d'avoir modifié les paramètres des canaux dans un moule pour capsules de bouteilles à plusieurs cavités ; chaque cavité se remplissant en même temps, c'était comme diriger une symphonie parfaite !
Contrôle de la pression et de la vitesse d'injection
Un autre domaine clé dans lequel l’analyse du flux de moule améliore l’efficacité de la production est l’optimisation de la pression et de la vitesse d’injection.
- Pression d'injection : l'analyse de la résistance à l'écoulement permet de déterminer la pression d'injection optimale, en équilibrant le risque de défauts comme le flash et la garantie d'un remplissage complet. En examinant la résistance à l'écoulement, j'ai découvert les meilleures pressions d'injection pour différents projets ; trop de choses provoquaient des défauts tandis que trop peu entraînaient des plans courts.
- Vitesse d'injection : L'avancement du front d'écoulement peut être simulé à différentes vitesses pour garantir une finition de surface de haute qualité, particulièrement importante dans les pièces ayant des exigences esthétiques strictes comme les intérieurs d'automobile. Un projet d'intérieur automobile nécessitait une vitesse spécifique pour éviter les défauts de surface ; MFA m'a permis de tester différentes vitesses et d'obtenir une finition parfaite.
Paramètres de pression et de temps de maintien
La détermination de la pression de maintien et du temps appropriés après le remplissage est cruciale pour maintenir la précision dimensionnelle et réduire les défauts.
- Pression de maintien : Une pression de maintien adéquate compense le retrait pendant le refroidissement, crucial pour les composants de haute précision comme les engrenages. Lorsque je travaillais avec des pièces de haute précision comme des engrenages, j'utilisais la MFA pour trouver la bonne pression de maintien afin d'éviter le retrait ; le voir s'adapter parfaitement était très gratifiant.
- Temps de maintien : Le temps de maintien calculé garantit que les pièces refroidissent uniformément sans apparition de déformations ou de marques de retrait. Trouver le temps de maintien idéal est délicat ; si des défauts trop courts apparaissent, si trop longs les coûts augmentent. Avec MFA, j'ai calculé des conceptions pour obtenir les meilleurs résultats.
Temps de refroidissement et paramètres du système
L'analyse du flux de moule contribue également de manière significative à l'optimisation des temps et des systèmes de refroidissement.
- Optimisation du temps de refroidissement : MFA prédit la répartition de la température et permet aux concepteurs de calculer le temps de refroidissement nécessaire le plus court, améliorant ainsi les temps de cycle. L'optimisation des temps de refroidissement a transformé mon cycle pour les petits jouets en plastique ; le calcul du temps de refroidissement le plus court a réellement augmenté l'efficacité tout en préservant la qualité des pièces intacte.
- Disposition du système de refroidissement : La disposition et la taille des canaux de refroidissement peuvent être ajustées pour garantir un refroidissement uniforme et éviter toute déformation. L'ajustement de la disposition des canaux de refroidissement est devenu naturel avec MFA ; même le refroidissement peut arrêter la déformation, en particulier dans les gros morceaux.
En conclusion, l'utilisation de l'analyse des flux de moule dans les processus de production permet non seulement d'identifier les problèmes potentiels, mais ouvre également la voie à des améliorations conduisant à une efficacité accrue et à une réduction des coûts. Pour plus d'informations sur les meilleures pratiques en matière de conception de moules, consultez les techniques avancées 3 .
L'analyse du flux de moule aide à prévenir les défauts lors du moulage par injection.Vrai
En simulant le processus d'injection, l'analyse du flux de moule identifie les défauts potentiels, améliorant ainsi la qualité globale des pièces produites.
L’optimisation des emplacements des portes augmente les temps de cycle de production.FAUX
Un positionnement correct des portes améliore l'écoulement de la matière fondue et réduit les temps de cycle, conduisant à des processus de production plus efficaces.
Conclusion
L'analyse des flux de moule améliore le moulage par injection en optimisant les emplacements des portes, les systèmes de canaux, les pressions d'injection et les temps de refroidissement pour améliorer l'efficacité et la qualité des produits.
-
Ce lien fournit une analyse approfondie sur l'optimisation des emplacements des portes pour de meilleurs résultats de conception de moules. ↩
-
Découvrez des informations et des stratégies d'experts sur les pratiques efficaces de gestion du temps de refroidissement pour améliorer l'efficacité de votre production. ↩
-
Découvrez comment MFA peut améliorer considérablement vos processus de fabrication et réduire efficacement les coûts. ↩