All Posts
blog & article
read our latest newsletter
Whether you’re curious about material selection, product design, mold design, mold making and injection molding, feel free to ask us anything. Our team is ready to provide the guidance and insights you need.
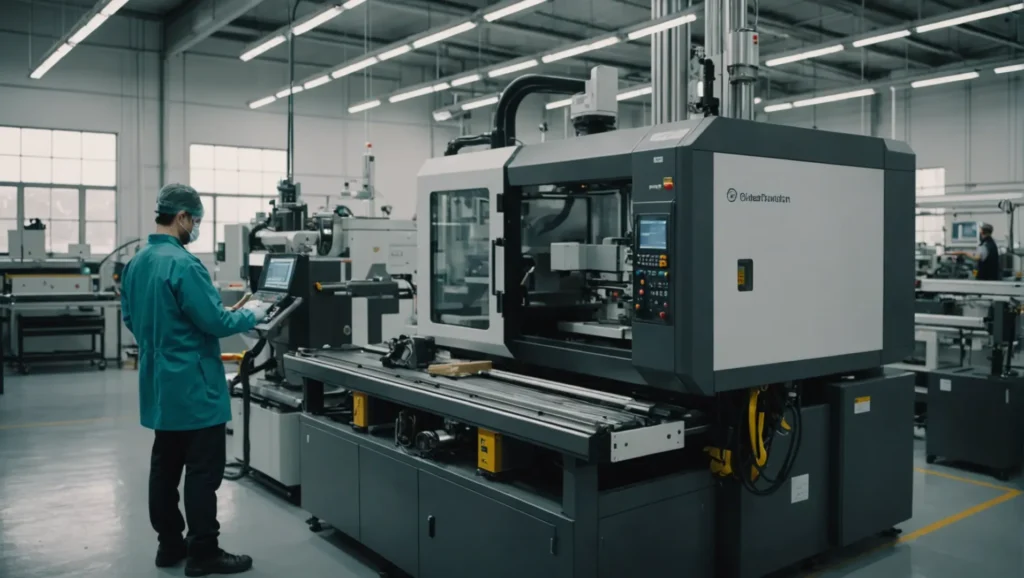
What Are the Common Problems and Solutions in Small Batch Injection Molding Production?
Navigating the intricate world of small batch injection molding can feel like walking a tightrope. From high costs to quality control issues, understanding the common challenges—and their solutions—is crucial for efficient production. Let’s dive into the most pressing issues and ...
OPTIMIZATION
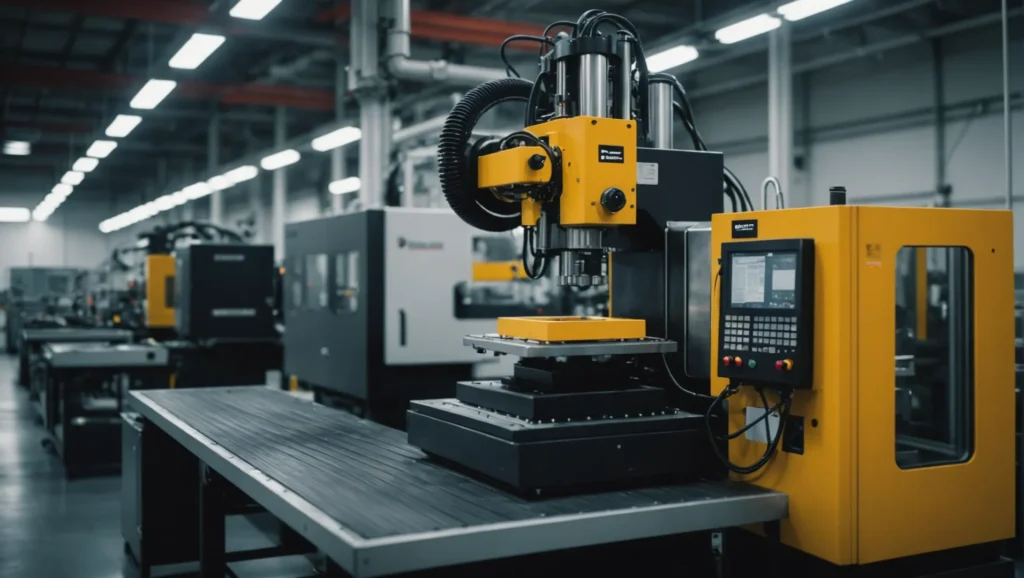
What Are the Solutions to Demolding Problems in Complex Structure Injection Molding?
Demolding challenges in injection molding of complex structures can significantly impact production efficiency and product quality. Understanding these challenges and implementing effective solutions is crucial for manufacturers. From optimizing mold design to improving surface quality, this article explores comprehensive strategies ...
DEVELOPMENT
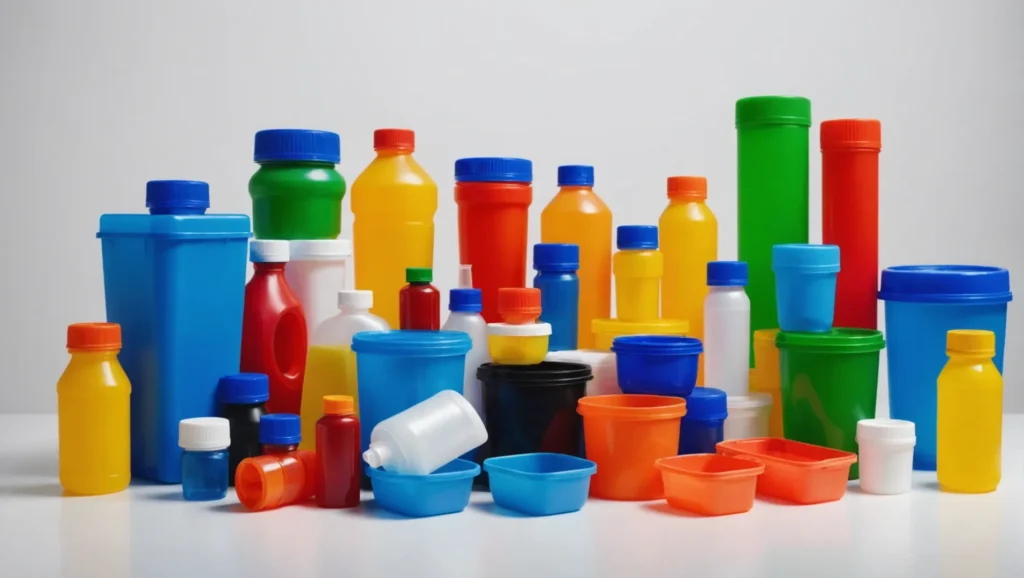
What Types of Injection Molded Plastic Are Recyclable?
Injection molding is a staple in plastic manufacturing, but its environmental footprint is significant. Understanding which types of injection molded plastics can be recycled is crucial for reducing waste and promoting sustainability. This article explores the recycling processes, benefits, and ...
Materials Recommendations
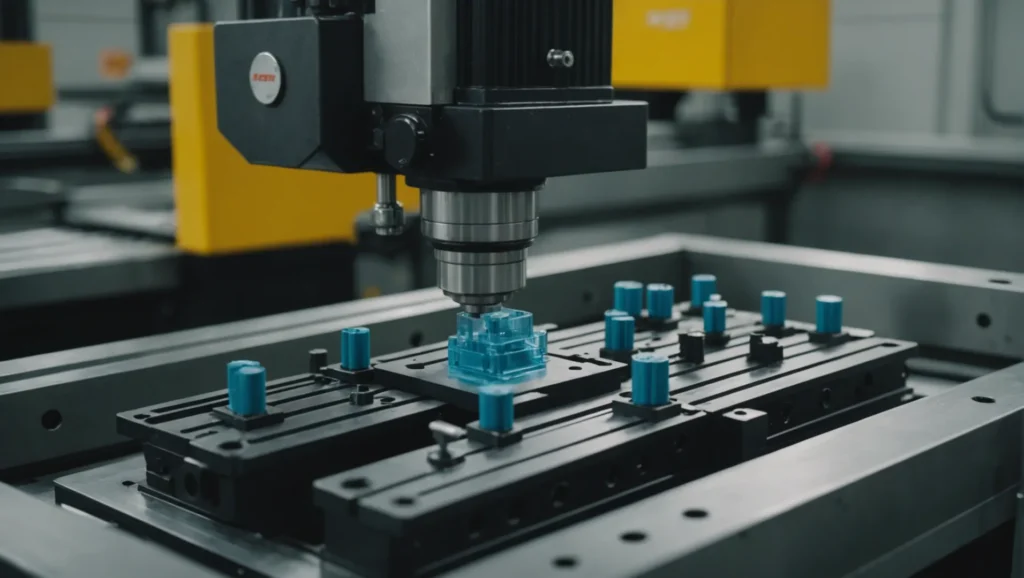
What Are Effective Ways to Reduce Stress Concentration in Injection Molding?
Injection molding is a critical manufacturing process that often faces challenges with stress concentration, leading to defects like cracking and deformation. Understanding how to effectively manage this issue through material selection, mold design, and process parameters is essential. This article ...
OPTIMIZATION
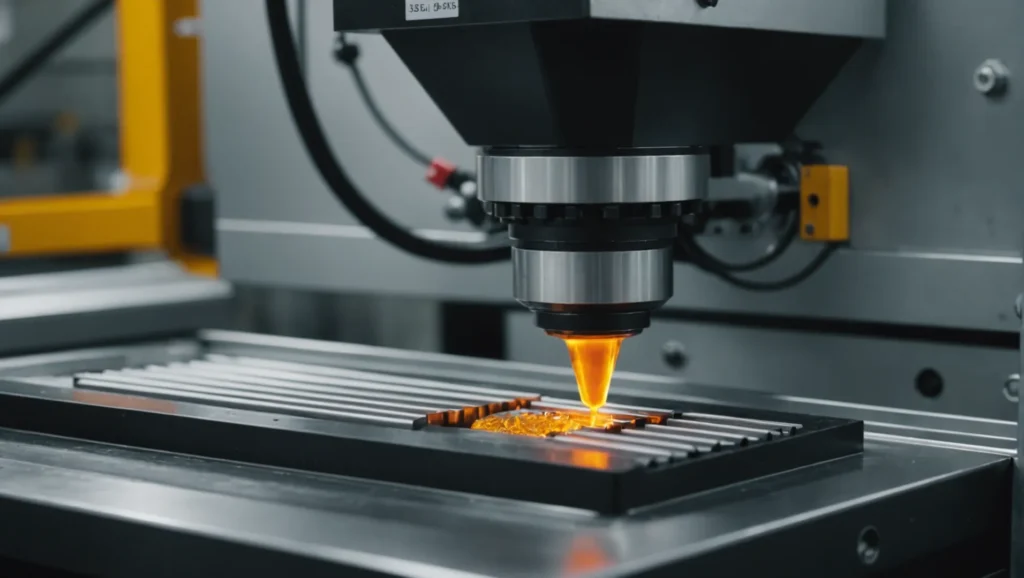
How Does Plastic Fluidity Affect Injection Molding and How Can It Be Controlled?
Understanding plastic fluidity is essential for optimizing injection molding processes. It directly influences filling performance, product quality, and production efficiency. This guide explores how to control fluidity through material selection, process parameters, and mold design for improved manufacturing outcomes.
DEVELOPMENT
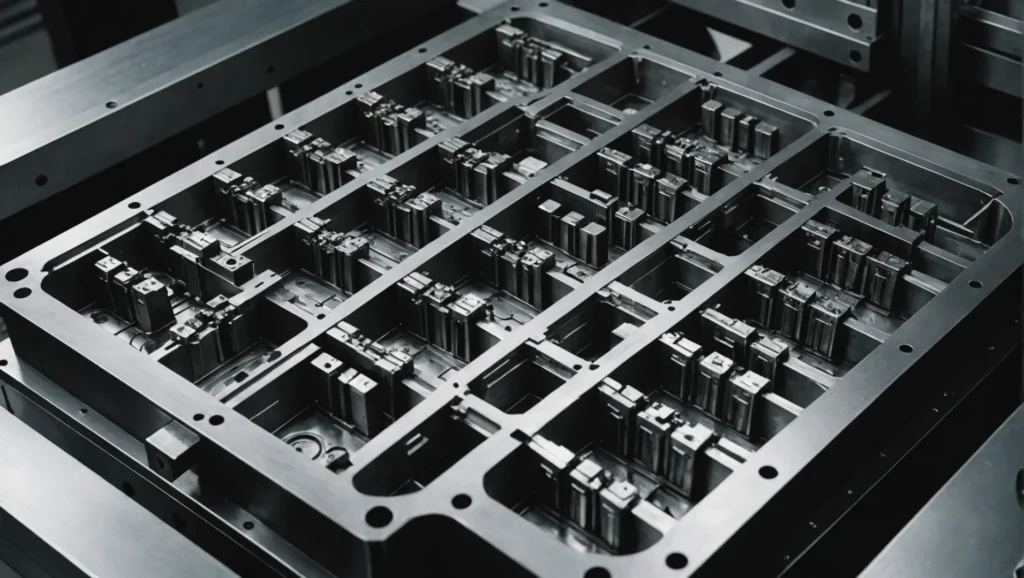
What Are the Best Strategies to Optimize Filling Balance in Multi-Cavity Molds?
Achieving optimal filling balance in multi-cavity molds is essential for high-quality injection molding processes. By focusing on runner and gate design, process parameter adjustments, and rigorous equipment maintenance, manufacturers can significantly improve both product quality and operational efficiency.
DEVELOPMENT
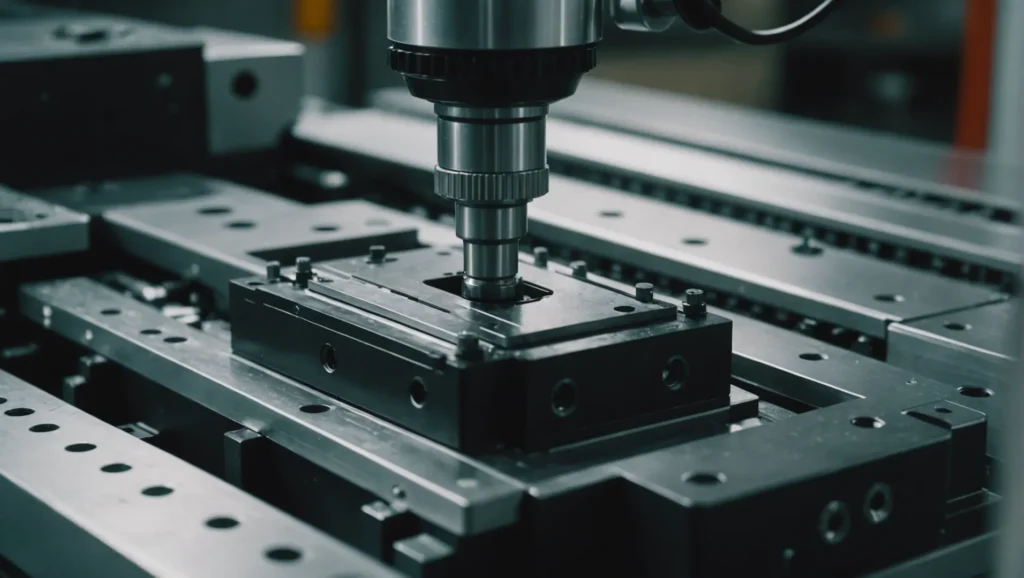
What Are the Causes and Preventive Measures for Mold Sticking in Injection Molded Products?
Mold sticking in injection molded products poses a significant challenge for manufacturers, impacting efficiency and product quality. Understanding the underlying causes—such as mold design flaws, improper process parameters, and unsuitable material choices—is crucial. This article explores effective preventive measures to ...
DEVELOPMENT
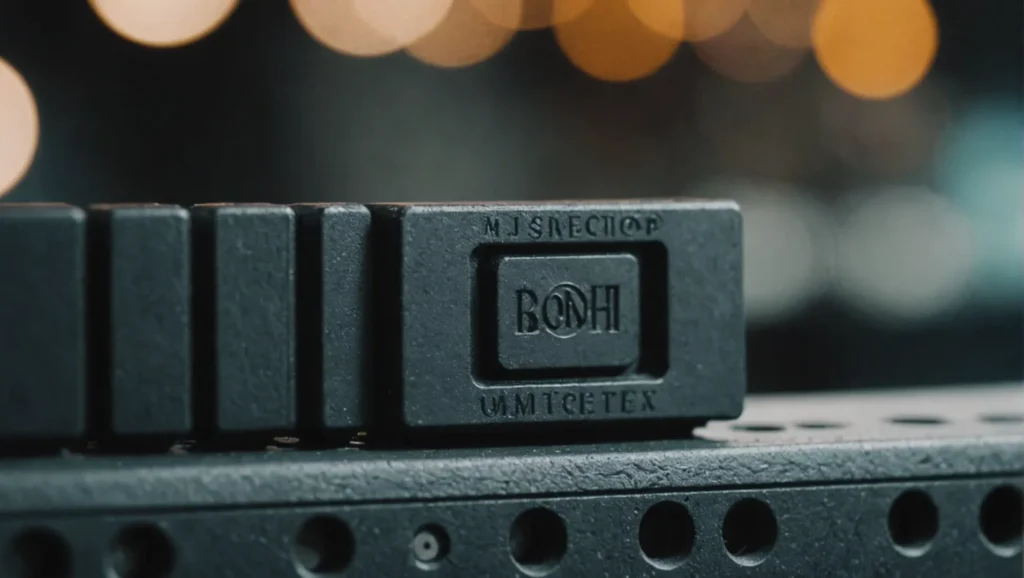
What Are the Best Solutions for Gate Mark Problems in Injection Molding?
Facing gate mark issues in injection molding? You're not alone. These marks can mar the appearance and functionality of finished products, but solutions are available. Explore how to effectively tackle these problems with adjustments in process parameters, mold design, and ...
OPTIMIZATION
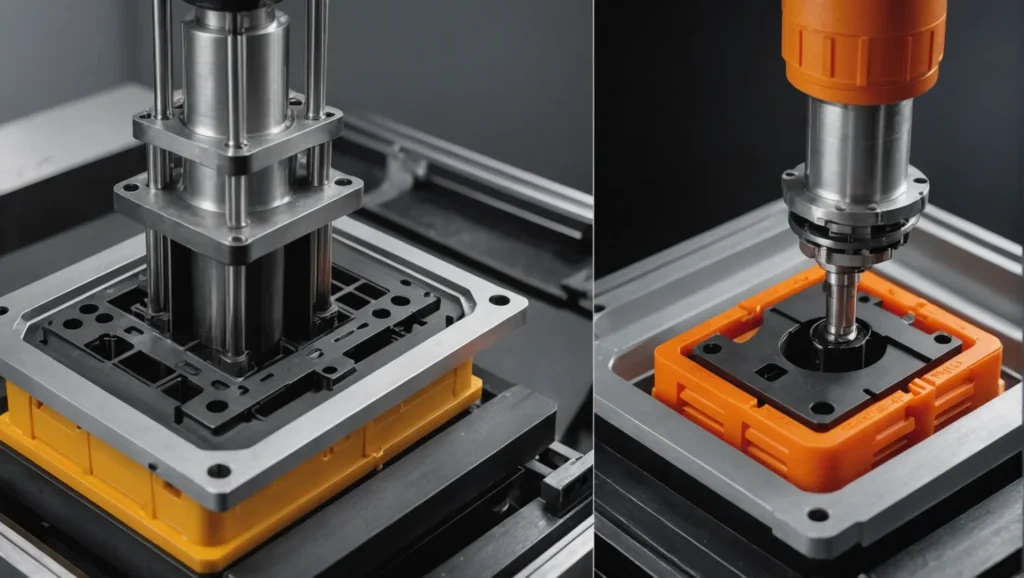
What Are the Key Differences Between Hot Runners and Cold Runners in Injection Molding?
Navigating the complexities of injection molding requires a careful choice between hot and cold runner systems. Each offers distinct advantages and challenges that can significantly impact production efficiency and costs. Understanding these differences is crucial for optimizing manufacturing processes and ...
MANUFACTURING
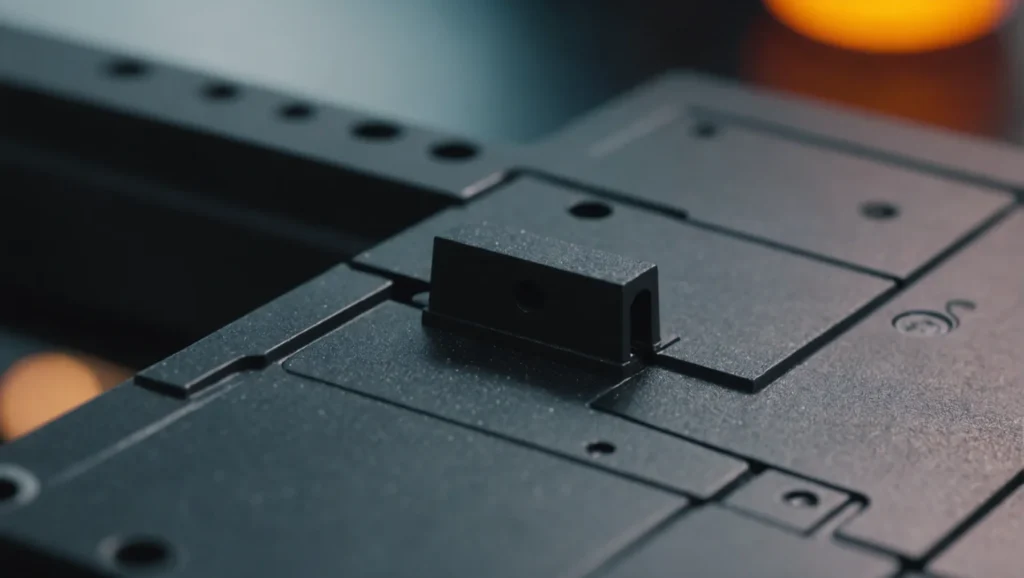
What Are the Best Ways to Prevent Jet Marks on Injection Molded Parts?
Jet marks are a frustrating defect in injection molded parts that can compromise their appearance and overall quality. Fortunately, there are several effective strategies to mitigate this issue. By focusing on mold design, material selection, and adjusting process conditions, manufacturers ...
OPTIMIZATION
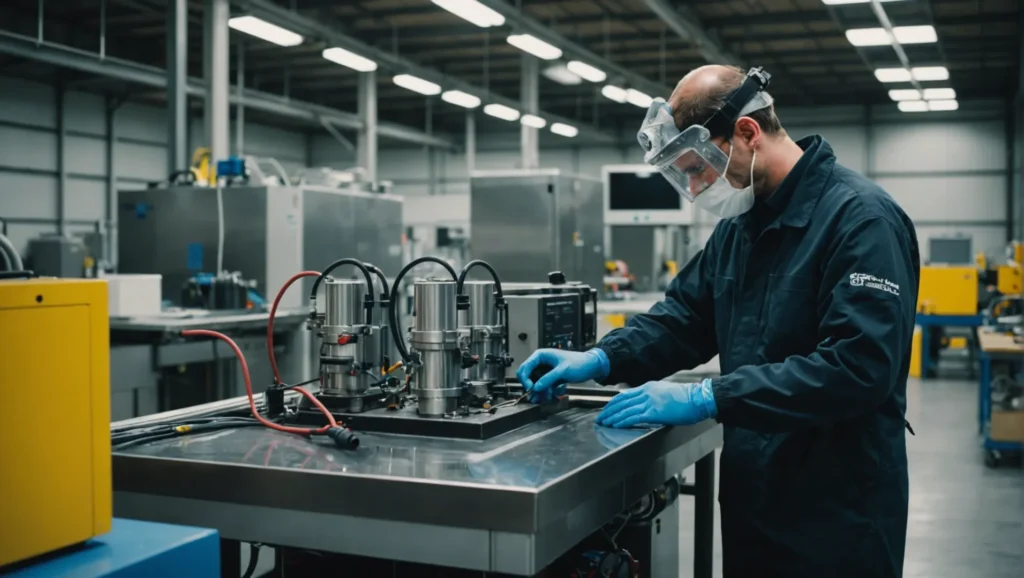
How Can You Effectively Clean Blockages in Injection Mold Cooling Pipes?
Keeping injection mold cooling pipes clear of blockages is essential for maintaining production efficiency and product quality. Understanding the causes of these blockages and how to effectively clean them can save time and resources. This guide explores common blockage causes, ...
MANUFACTURING
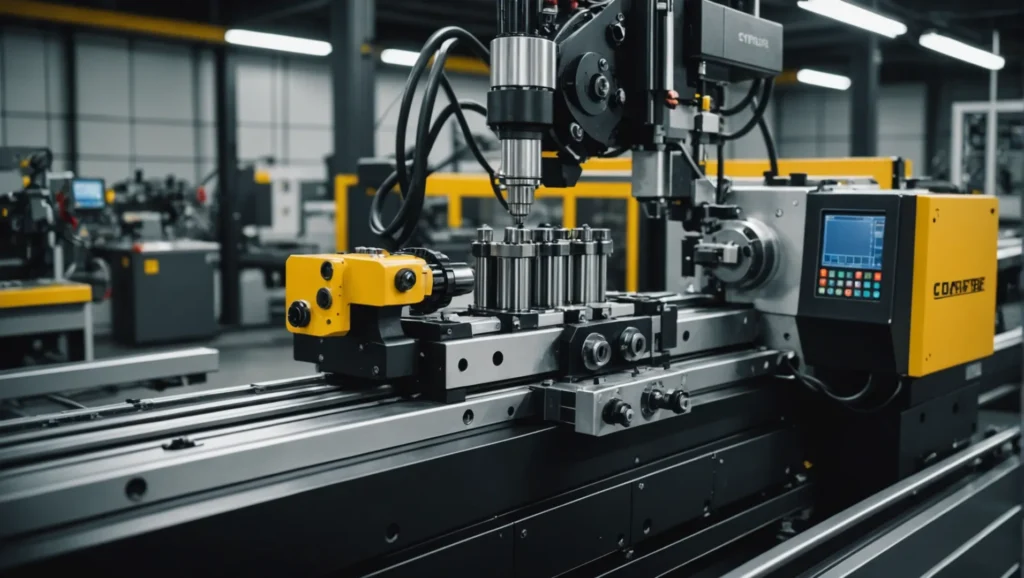
What Are the Different Clamping Methods in Injection Molding and Their Ideal Applications?
Injection molding is a crucial manufacturing process that significantly influences production efficiency and product quality. Understanding the various clamping methods—hydraulic, hydraulic-mechanical, mechanical, direct pressure, and center clamping—can help manufacturers choose the best approach for their specific needs. This article explores ...
MANUFACTURING
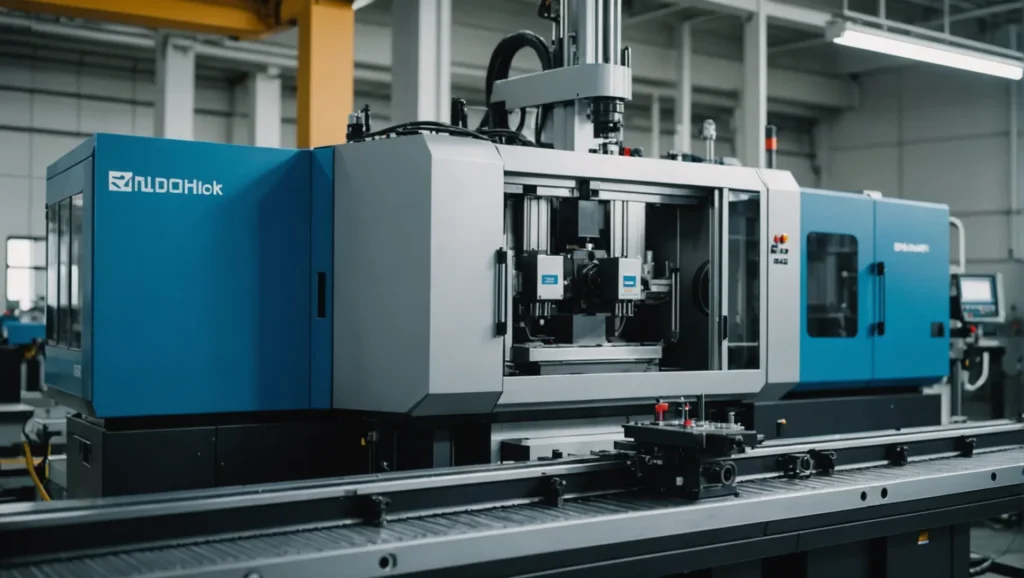
How Can You Prevent Product Edge Fracture in Injection Molding?
Injection molding is a cornerstone of modern manufacturing, but edge fractures can lead to significant quality concerns. This article explores practical strategies to prevent these issues, including adjusting injection parameters, optimizing mold design, selecting the right materials, and maintaining equipment ...
OPTIMIZATION
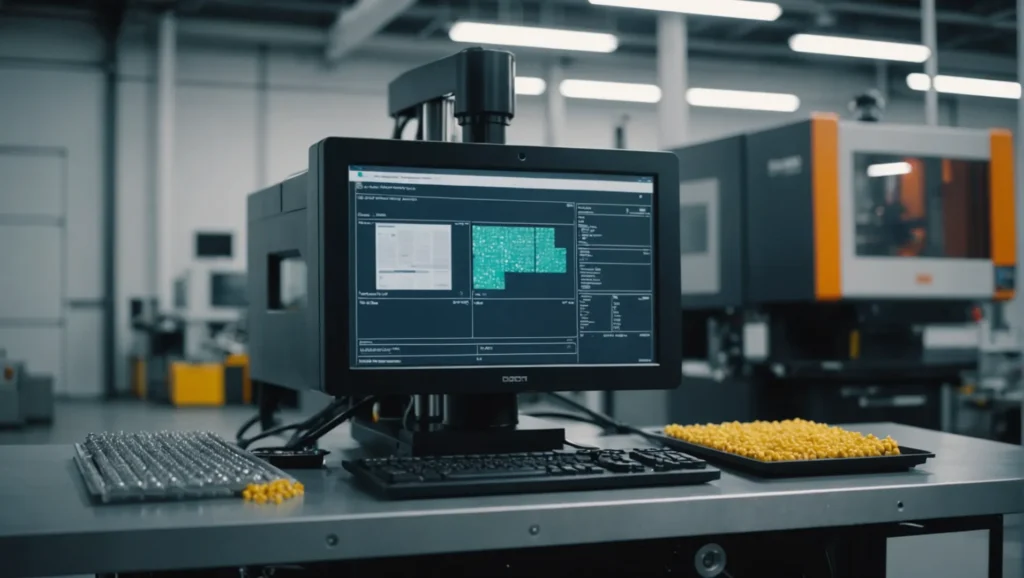
How Can You Predict and Control Shrinkage in Injection Molding Production?
Injection molding is a crucial manufacturing method, but shrinkage can create significant challenges. This guide explores how understanding material properties, mold design, and process parameters can help predict and control shrinkage effectively, ensuring high-quality production.
OPTIMIZATION
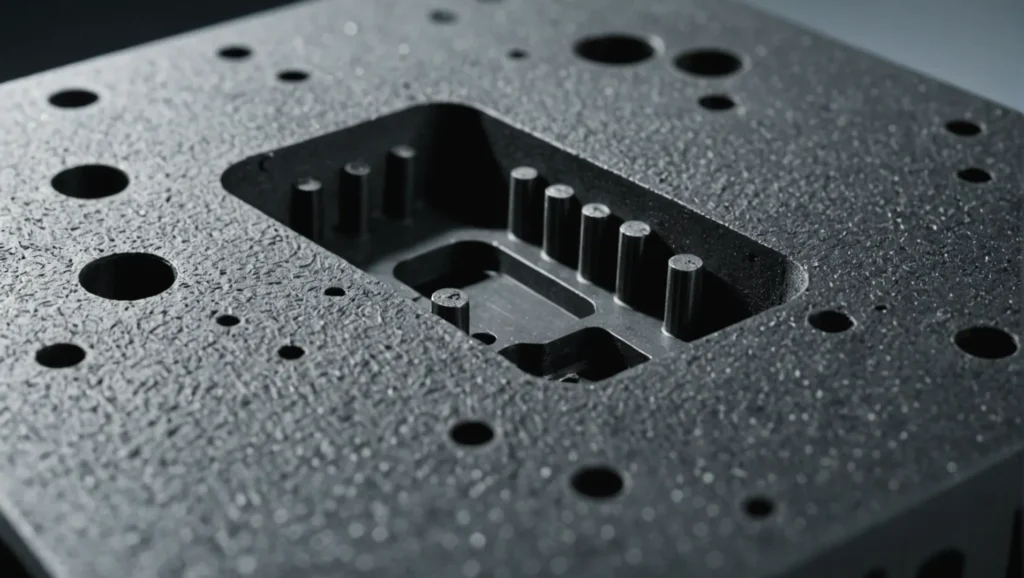
How Can You Identify Shrinkage Defects in Injection Molded Parts and Improve Them?
Shrinking defects can significantly impact the quality of injection molded parts. By understanding the causes of these issues and implementing effective solutions, manufacturers can enhance the performance and aesthetics of their products. Explore comprehensive strategies to combat shrinkage defects and ...
OPTIMIZATION
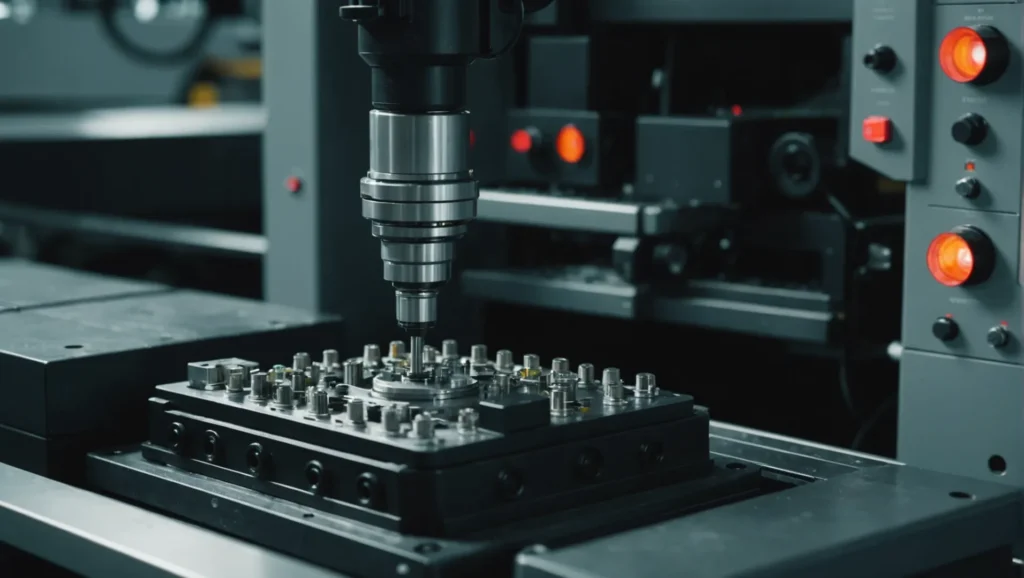
What Are the Key Control Points in Injection Molding of Small Parts?
Injection molding is a multifaceted process with many variables, particularly when it comes to small parts. Understanding the key control points—material selection, mold design, parameter control, and quality inspection—can make all the difference in ensuring a successful outcome. Join me ...
MANUFACTURING
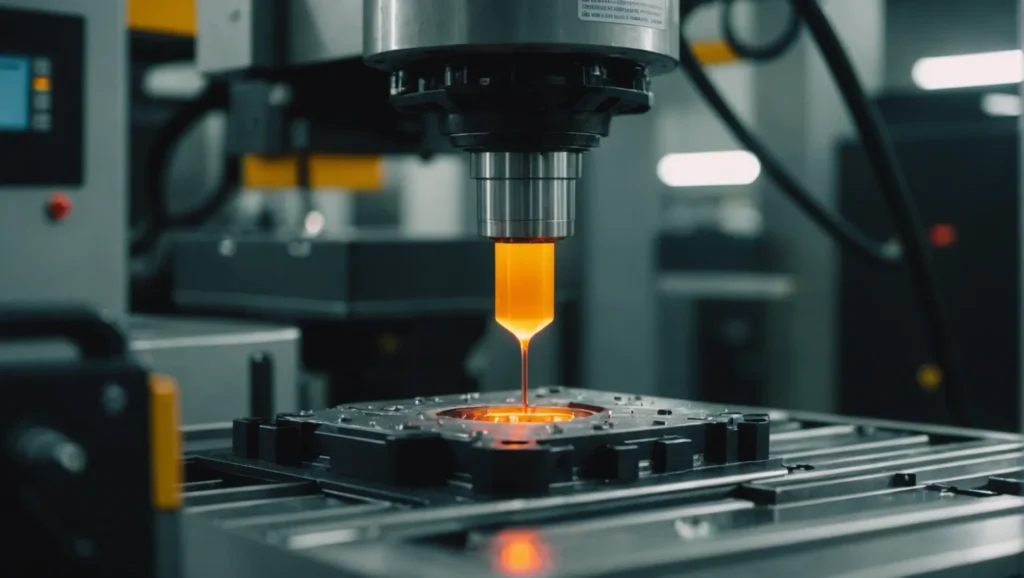
How Does Shear Heat Affect Products in Injection Molding?
In the intricate world of injection molding, shear heat is a critical factor influencing product outcomes. Understanding its impact is essential for optimizing manufacturing practices. This article explores the positive and negative effects of shear heat on product quality, material ...
MANUFACTURING
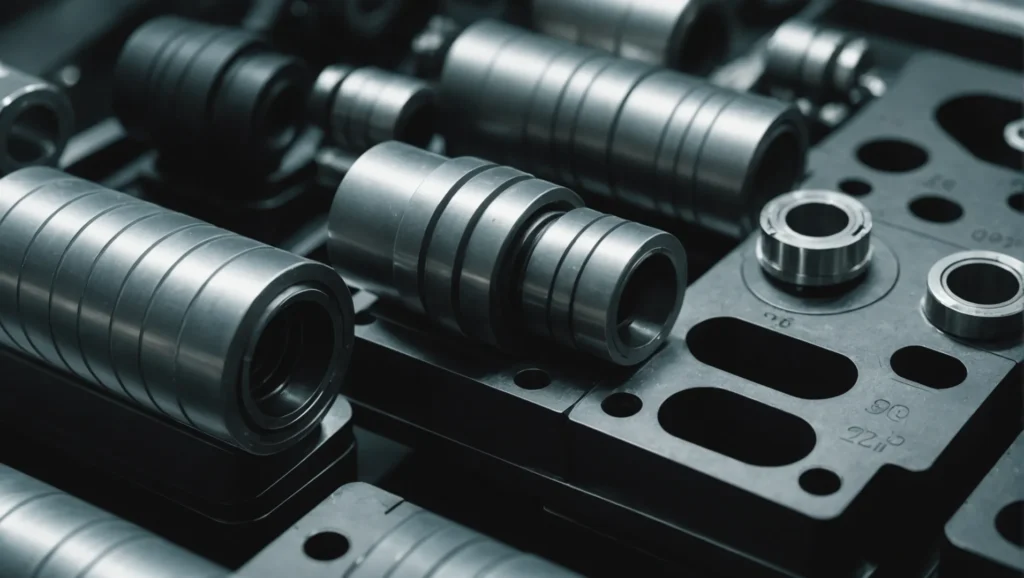
How Can You Enhance the Flexibility of Injection Molded Parts?
Injection molded parts are a staple in various industries, yet achieving optimal flexibility can be challenging. Understanding how to enhance this property is essential for creating versatile and resilient components. By selecting the right materials, adjusting process parameters, and employing ...
OPTIMIZATION
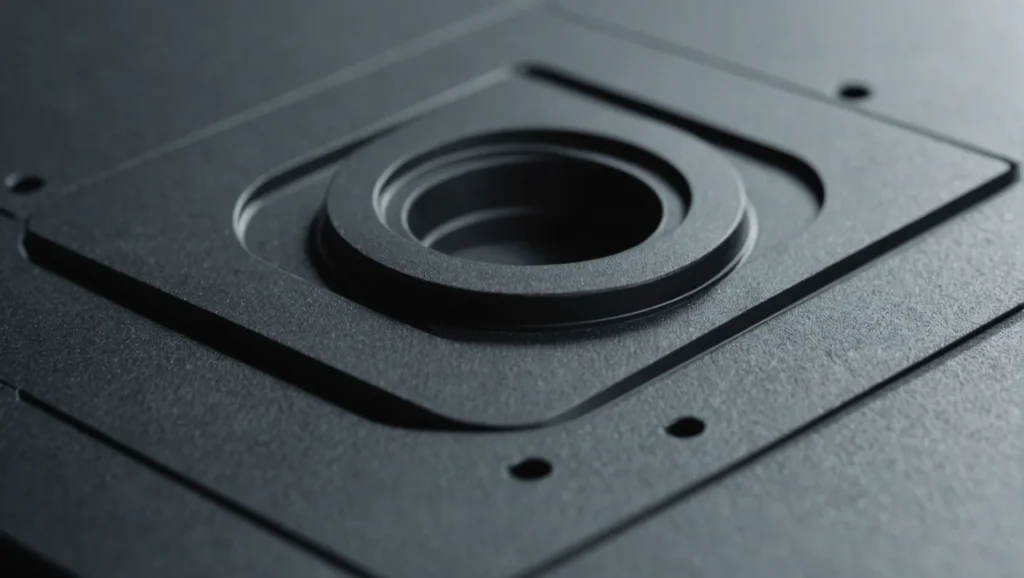
How Can You Achieve Smooth Surfaces in Injection Molding?
Achieving smooth surfaces in injection molding is essential for creating high-quality plastic parts. From material selection to post-processing techniques, every step in the process impacts the final product's aesthetic and functional qualities. Discover how to refine your techniques for superior ...
MANUFACTURING
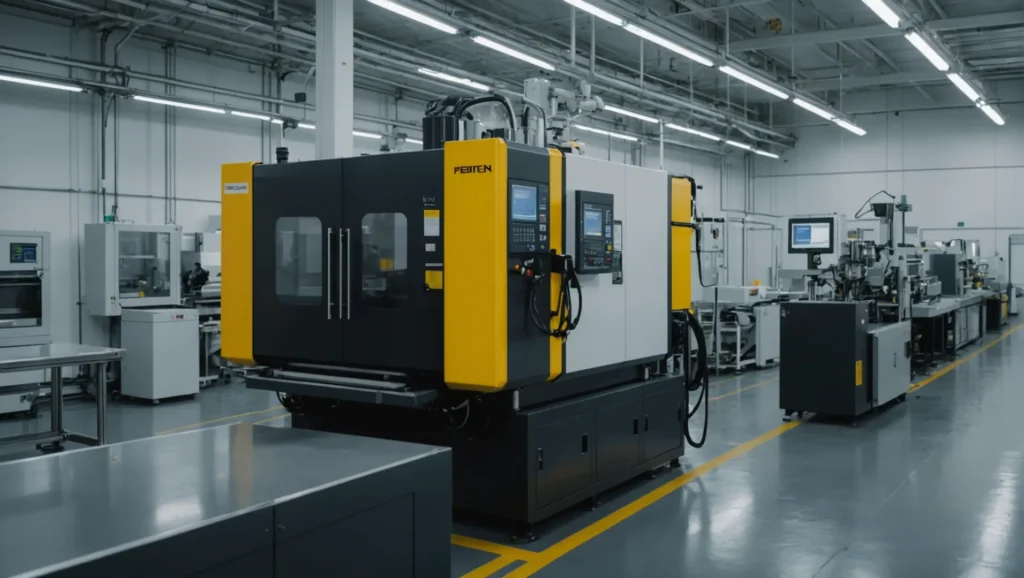
How Can You Prevent Raw Material Decomposition in Injection Molding?
Preventing raw material decomposition is essential for high-quality injection molded products. This guide outlines effective strategies, including raw material selection, process optimization, and maintenance practices, to enhance product integrity and reduce defects.
OPTIMIZATION
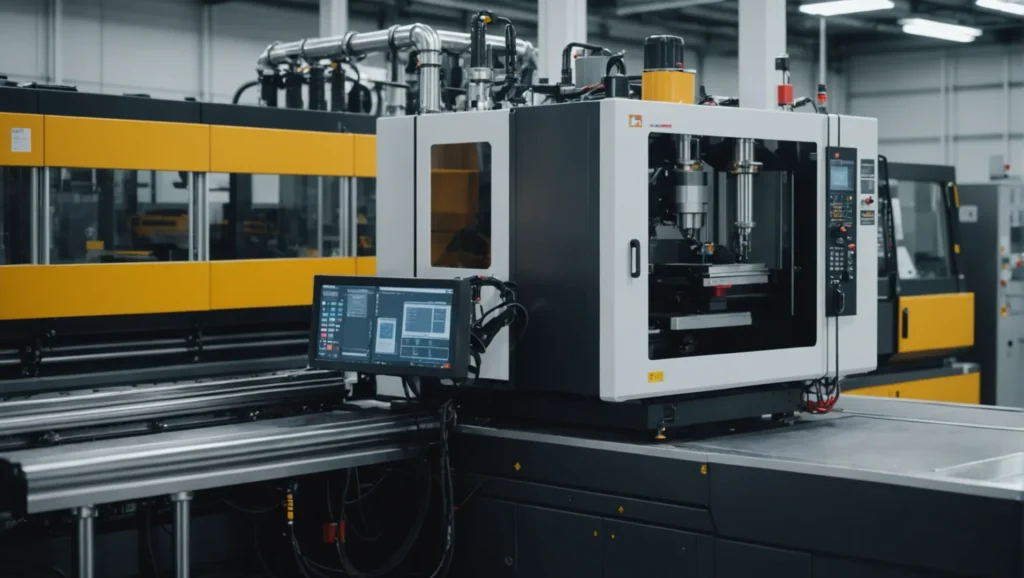
What Are the Best Ways to Optimize Cooling Rate in Injection Molding?
Optimizing the cooling rate in injection molding is crucial for improving product quality and efficiency. By focusing on the design of cooling systems, selecting the right mediums, and adjusting process parameters, manufacturers can achieve significant improvements in their production processes. ...
MANUFACTURING
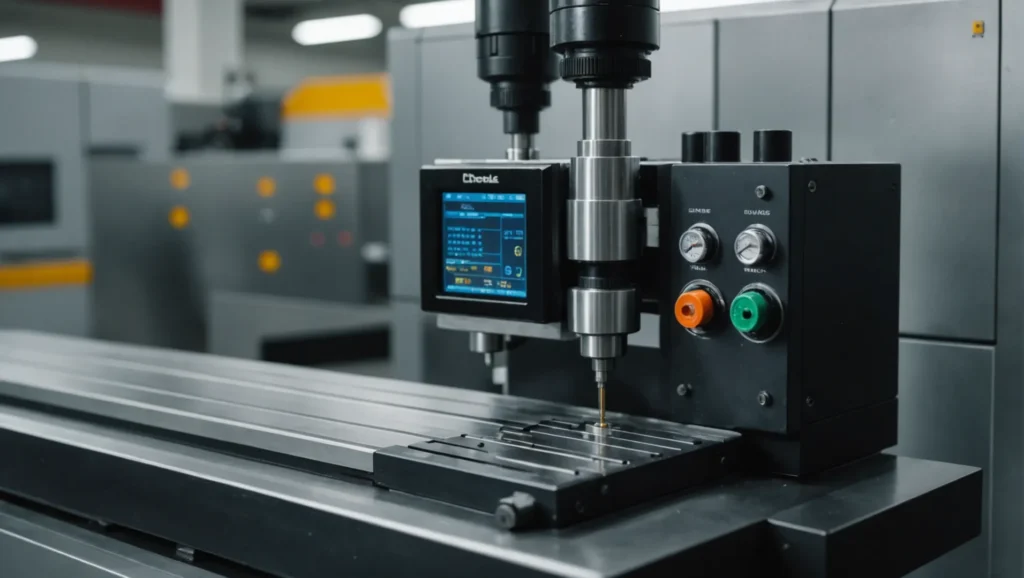
How Can You Effectively Control Pressure Loss in Injection Molding?
Are you struggling with pressure loss in your injection molding process? Fear not! By understanding and mitigating this issue, you can significantly enhance your production efficiency. This article explores the vital aspects of equipment, mold design, process adjustments, and operator ...
MANUFACTURING
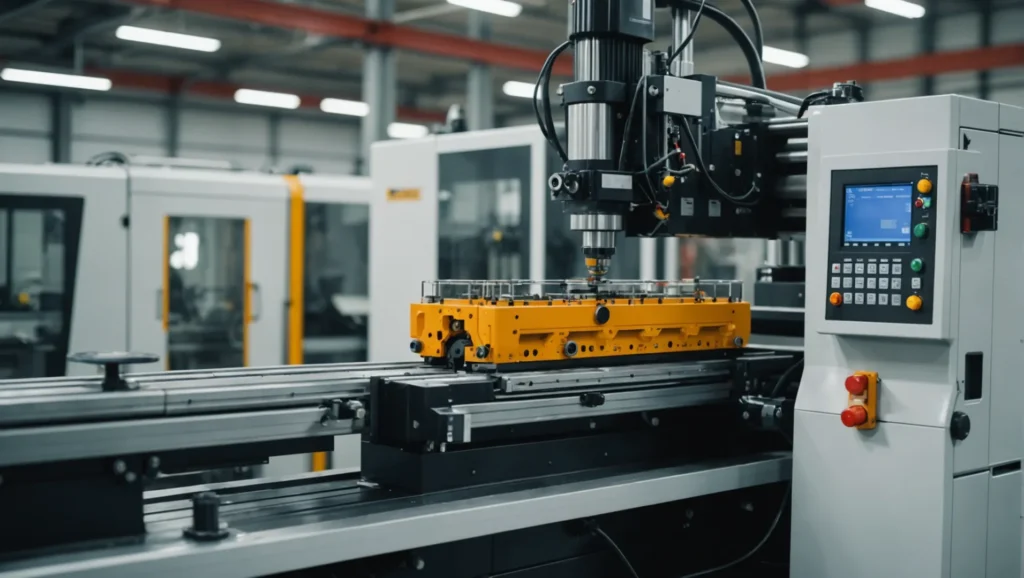
How Can You Effectively Reduce Uneven Filling in Injection Molding?
Achieving uniform filling in injection molding is crucial for ensuring high-quality finished products. Uneven filling can lead to significant defects that compromise product integrity. This article explores effective strategies including material selection, mold design, process adjustments, and maintenance practices that ...
OPTIMIZATION

How Can You Effectively Reduce Product Differences in Dual-Cavity Molds?
In the competitive world of manufacturing, consistency is key. When using dual-cavity molds, ensuring uniformity between products is essential for quality and efficiency. By focusing on strategies like precise mold design and stringent process controls, manufacturers can significantly enhance product ...
DEVELOPMENT
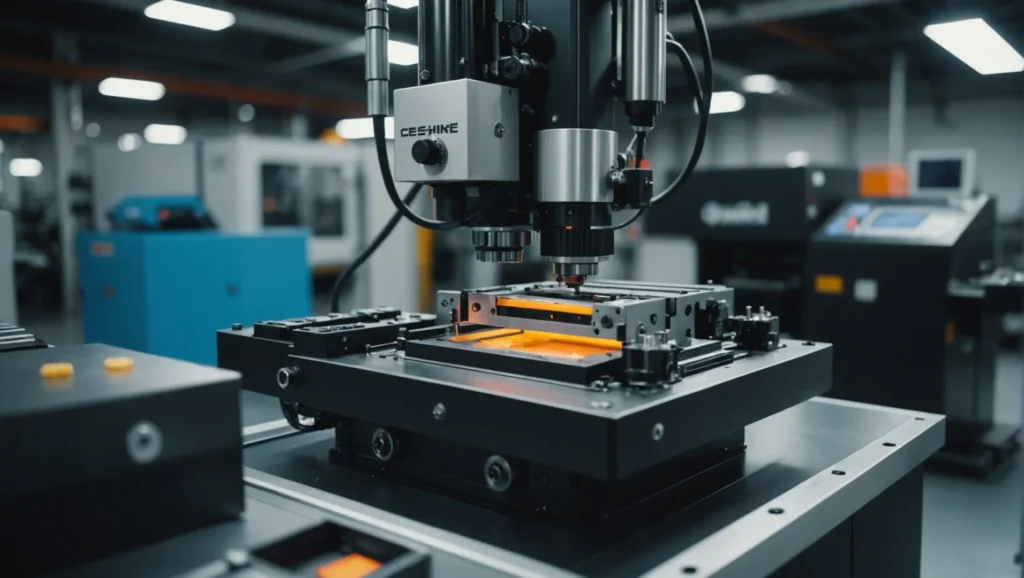
How is Micro Injection Molding Technology Revolutionizing Electronic Components?
In an ever-evolving electronic landscape, micro injection molding technology stands out as a beacon of innovation. This transformative approach enables the creation of incredibly precise, miniaturized components that not only meet current demands but also pave the way for future ...
MANUFACTURING
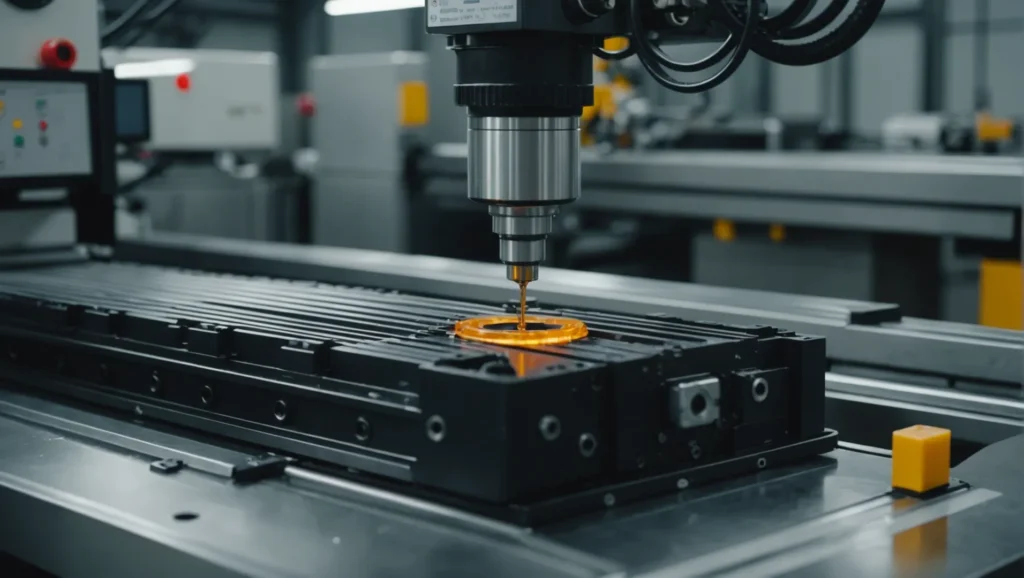
How Can You Maintain Material Fluidity in Injection Molding Production?
Injection molding is a complex process that demands precision and control, especially when it comes to maintaining material fluidity. By selecting the right materials, controlling temperature and pressure, and optimizing mold design, manufacturers can significantly enhance their production efficiency and ...
DEVELOPMENT
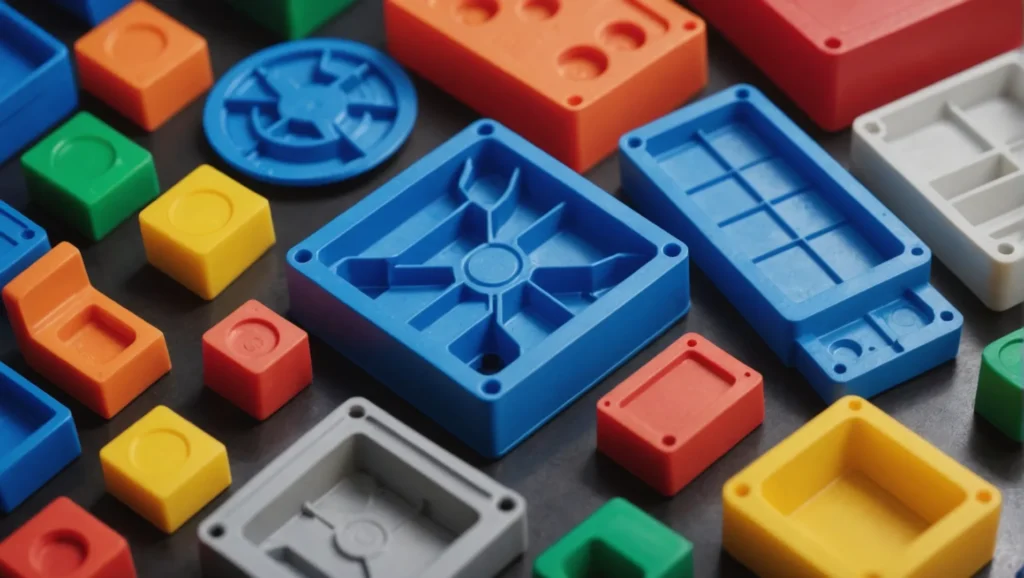
What Are the Common Defects and Solutions in Multi-Color Injection Molding of Thermoplastic Plastics?
Multi-color injection molding offers exciting possibilities in product design, but it also comes with its set of challenges. Understanding common defects like poor color mixing and stratification is key to enhancing production quality. This article explores effective solutions that can ...
OPTIMIZATION
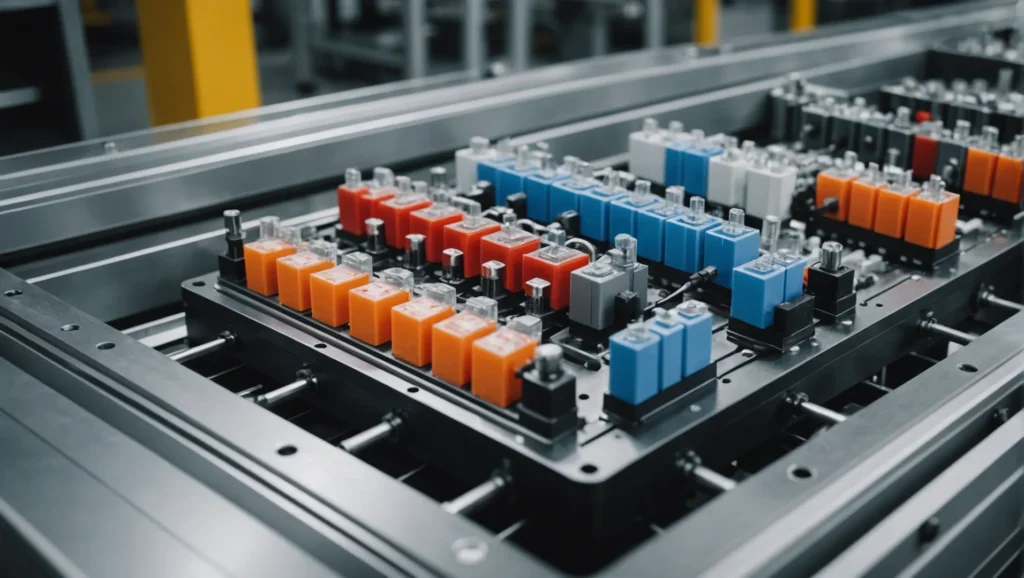
How Can Runner Design Boost Injection Molding Efficiency?
Injection molding is fundamental to modern manufacturing, yet achieving optimal efficiency remains a challenge. By focusing on runner design, manufacturers can significantly enhance their processes. From understanding hot and cold runner systems to optimizing sizes and layouts, this article explores ...
DEVELOPMENT
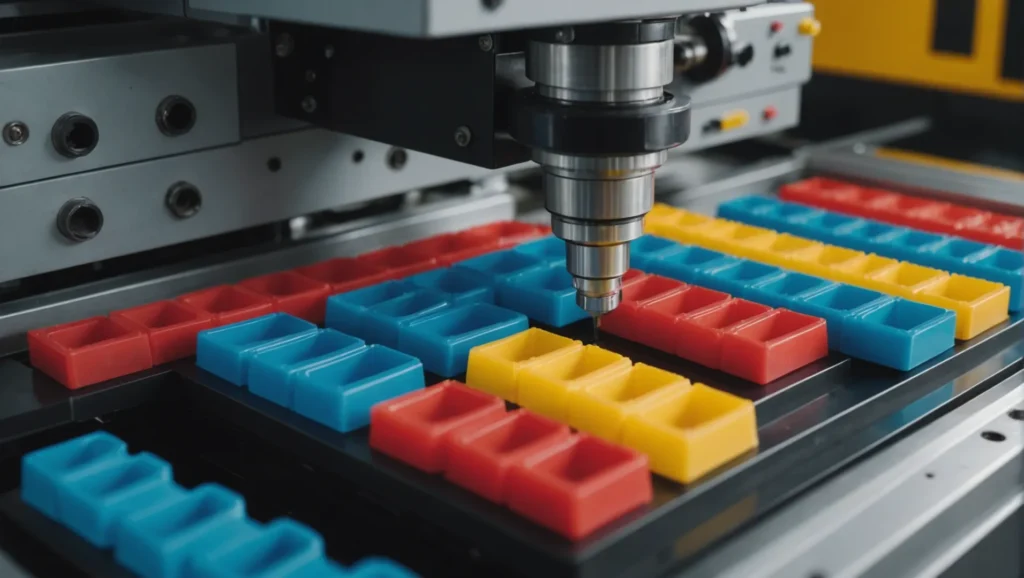
How Can You Prevent Color Mixing in Multi-Color Injection Molding?
Preventing color mixing in multi-color injection molding is essential for maintaining product quality and aesthetic appeal. This article explores effective strategies such as mold design, process control, material selection, and equipment maintenance to help you achieve flawless results.
OPTIMIZATION
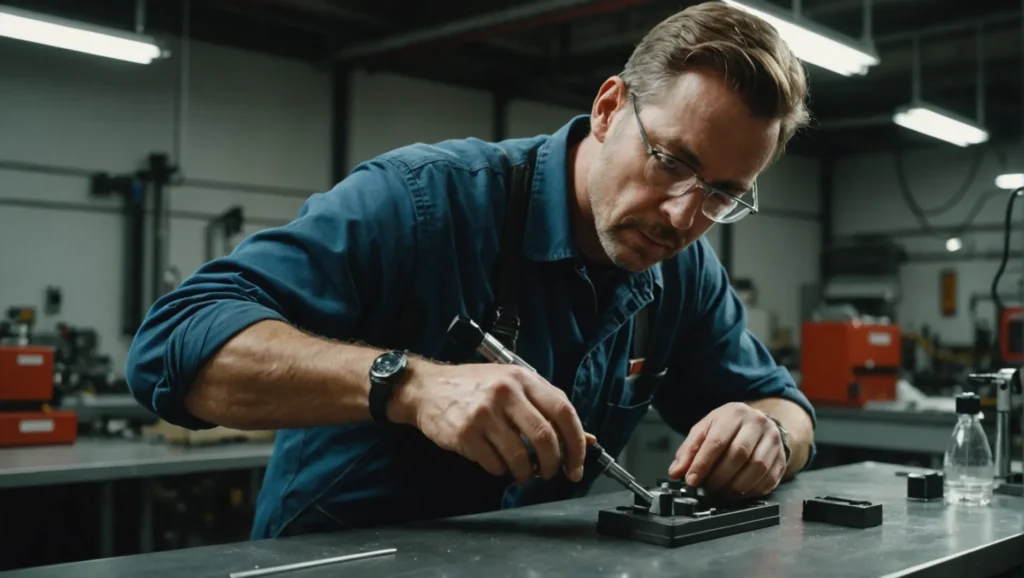
How is the Polishing Process Applied to Injection Molded Products?
Injection molding is a popular manufacturing process, but achieving a high-quality finish requires effective polishing. This article explores various polishing techniques—mechanical, chemical, electrolytic, and ultrasonic—that can enhance the surface quality of injection molded products. Each method has its unique advantages ...
MANUFACTURING