Have you ever looked at a finished product and noticed unsightly marks that just ruin its appearance? I have, and trust me, it’s frustrating! But don’t worry—there are solutions to tackle those pesky gate marks in injection molding.
To solve gate mark problems in injection molding, consider adjusting process parameters such as increasing barrel temperature, injection pressure, and holding time. Optimizing mold design by selecting suitable gate types and improving cooling can also help.
But simply tweaking a few settings isn’t always enough. Join me as we dive deeper into comprehensive strategies to tackle gate marks, ensuring your manufacturing process yields high-quality results every time.
Increasing barrel temperature reduces gate marks.True
Higher temperatures improve plastic flow, reducing gate marks.
How Do Process Parameters Affect Gate Mark Formation?
Process parameters play a crucial role in the formation of gate marks during injection molding. Understanding and adjusting these parameters can significantly improve product quality.
Adjusting injection molding parameters such as barrel temperature, injection pressure, and holding time can reduce gate mark formation. These settings influence the flow and cooling of the plastic melt, directly impacting gate marks.
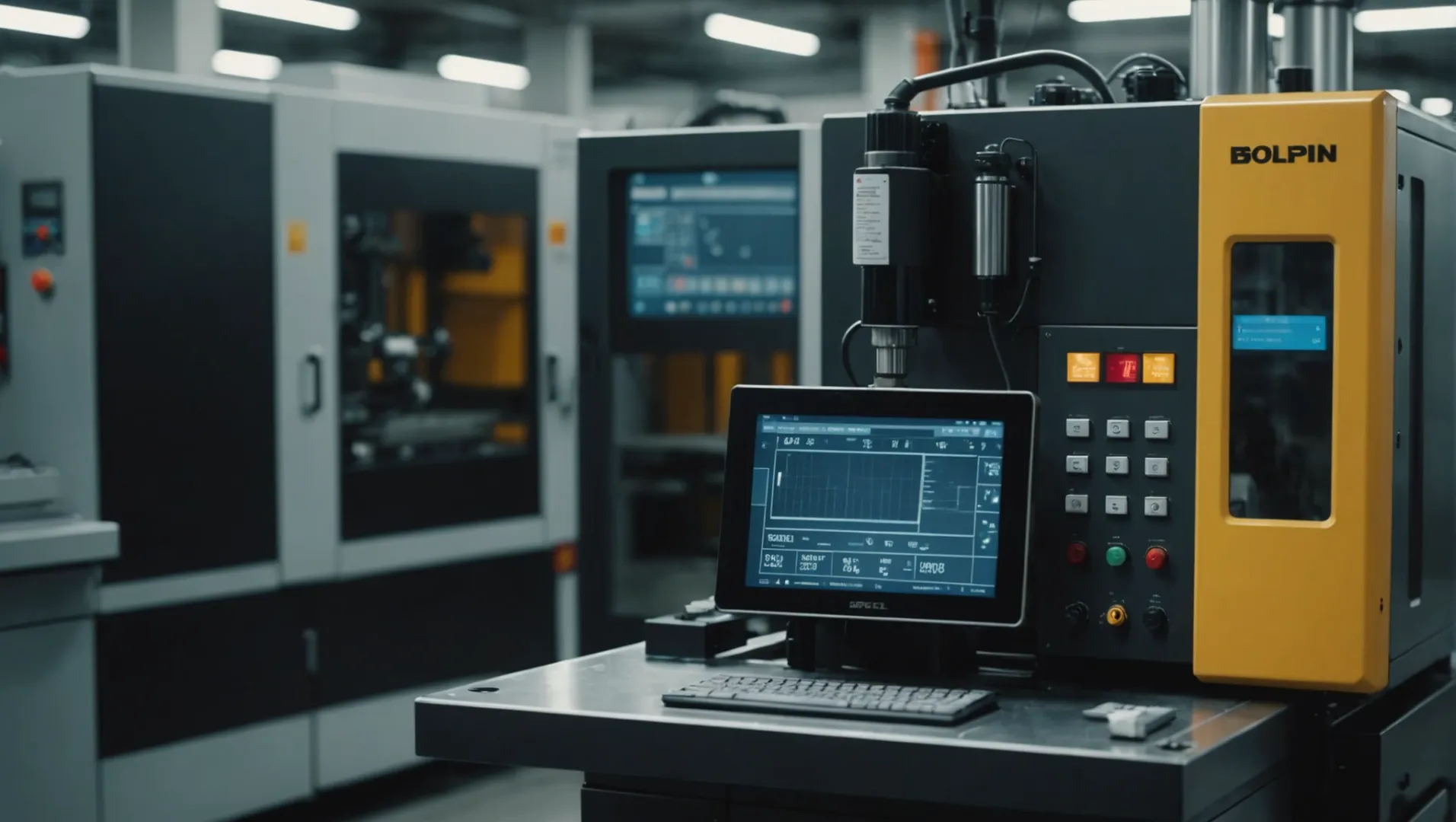
The Influence of Temperature on Gate Marks
Temperature settings, specifically barrel and nozzle temperatures, are critical in managing gate marks. By increasing these temperatures, the plastic melt becomes more fluid, allowing it to flow smoothly through the gate. This enhanced flow reduces the likelihood of gate marks, as the material can fill the mold cavity more evenly and with less resistance. However, it’s essential to maintain a balance; overly high temperatures may lead to degradation of the plastic material, negatively affecting the final product.
Injection Pressure and Speed
Injection pressure and speed are pivotal in controlling the formation of gate marks. Higher injection pressure ensures that the plastic melt fills the mold cavity quickly and uniformly, minimizing the formation of defects like gate marks. Similarly, adjusting the injection speed helps in achieving a smooth finish by preventing premature solidification at the gate.
The Role of Holding Time
Extending the holding time allows for additional compaction of the plastic melt at the gate. This phase is crucial because it compensates for any material shrinkage that occurs as the melt cools and solidifies. Ensuring adequate holding time is key to reducing voids and ensuring a robust, mark-free surface finish.
Adjustments in Injection Cycle
Altering the injection cycle can also impact gate mark formation. By extending the cycle, manufacturers give the plastic melt ample time to cool and solidify, which aids in reducing gate marks. Each adjustment should be made carefully to prevent adverse effects on other aspects of the product quality.
Optimization of Injection Molding Process1
Each adjustment in process parameters requires careful monitoring to ensure they do not adversely affect other properties of the molded parts. Experimenting with these settings under controlled conditions can help identify the most effective combination for specific materials and molds.
Higher barrel temperatures reduce gate marks.True
Increased temperatures improve plastic flow, reducing gate marks.
Shorter holding times lead to fewer gate marks.False
Short holding times may cause shrinkage, increasing gate marks.
What Role Does Mold Design Play in Preventing Gate Marks?
Gate marks are a common challenge in injection molding, impacting both aesthetics and functionality. Fortunately, mold design holds the key to minimizing these defects.
Optimizing mold design plays a crucial role in preventing gate marks by selecting appropriate gate locations, adjusting runner sizes, and ensuring efficient cooling. These strategies enhance the flow and solidification of plastic melt, reducing visible marks.
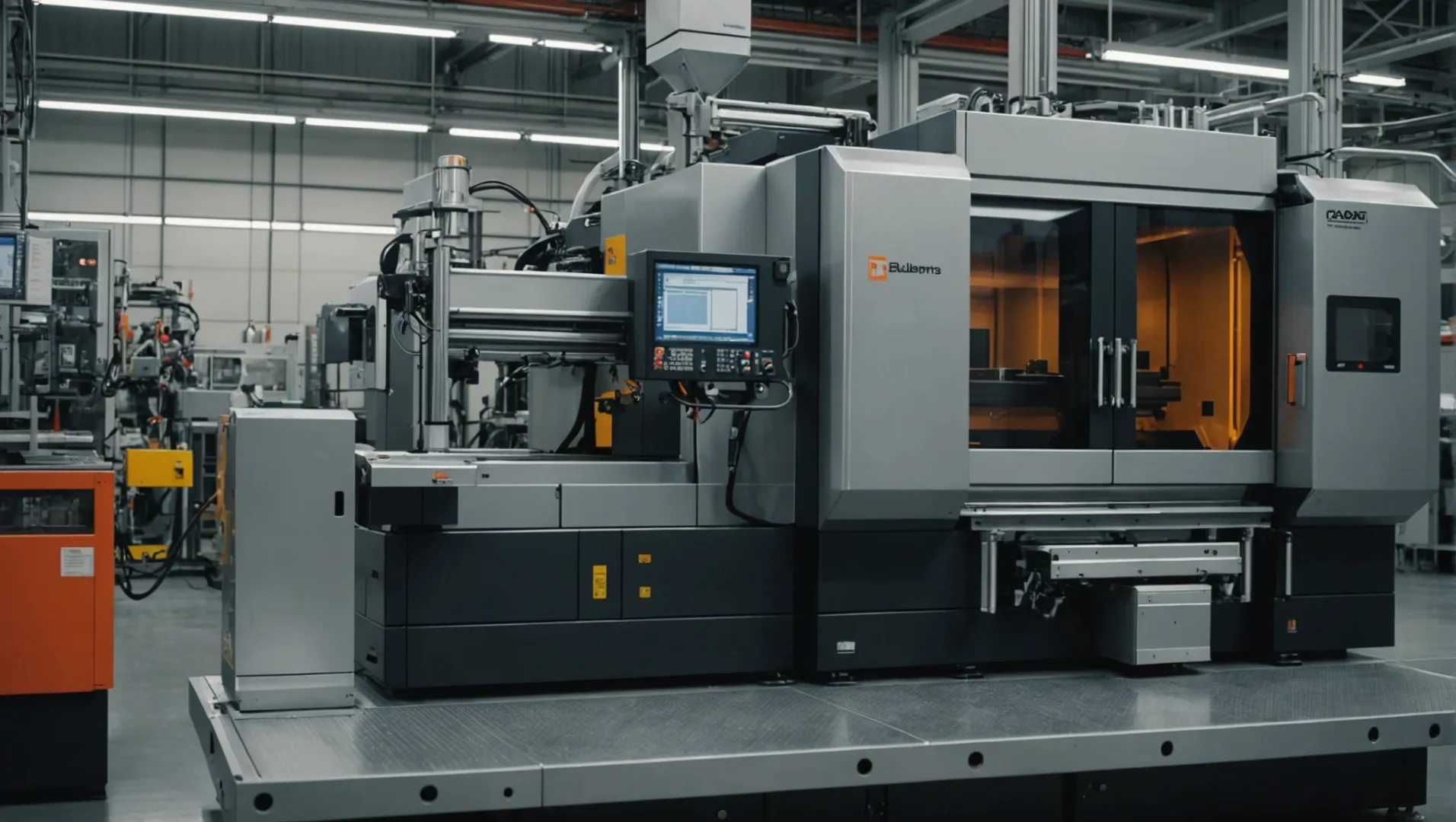
Understanding Gate Marks and Their Impact
Gate marks are imperfections that occur at the point where the molten plastic enters the mold cavity. These marks can compromise the final product’s surface quality and structural integrity. A well-thought-out mold design2 can significantly mitigate these issues by addressing various factors influencing gate mark formation.
Strategic Gate Location and Type Selection
Choosing the right location and type of gate is pivotal. Placing gates in areas that minimize stress concentration and pressure buildup helps reduce heat accumulation. For instance, edge gates are often used to direct flow along the edge of a part, minimizing marks on visible surfaces.
Consider a scenario where an injection-molded component experiences excessive marks due to a central gate location. Shifting the gate to an edge or using a fan gate could distribute flow more evenly, reducing pressure and heat at the entry point.
Optimizing Runner and Gate Size
The size of runners and gates directly affects the flow of plastic melt. Larger runners can lower resistance, enhancing fluidity while reducing potential for gate marks. For example, if a product exhibits uneven flow due to small gates, increasing their size can facilitate smoother flow.
Design Aspect | Impact on Gate Marks |
---|---|
Gate Location | Reduces stress/pressure |
Runner Size | Improves fluidity |
Cooling Efficiency | Speeds solidification |
Enhancing Mold Cooling and Exhaust Systems
Efficient cooling systems are integral to preventing gate marks. Rapid cooling helps solidify the plastic melt before it can form noticeable marks. Additionally, improving mold exhaust prevents air pockets that can lead to blemishes.
For instance, using conformal cooling channels that follow the contour of the mold can ensure even cooling across complex geometries, further reducing gate mark occurrence.
The Balance of Multiple Gates
For large or intricate parts, incorporating multiple gates can aid in uniform filling, reducing pressure at any single point and minimizing marks. This technique involves balancing flow from different gates to ensure even distribution across the mold.
By understanding and implementing these strategies in mold design, manufacturers can significantly reduce gate marks, enhancing both the visual and functional quality of injection-molded parts.
Gate location affects stress concentration.True
Strategic gate placement minimizes stress and pressure buildup.
Smaller gates improve plastic flow.False
Larger gates reduce resistance, enhancing fluidity of plastic melt.
Which Plastic Materials Are Best for Reducing Gate Marks?
Gate marks in injection molding are a common challenge. Choosing the right plastic materials can significantly mitigate these imperfections.
To reduce gate marks in injection molding, opt for plastic materials with high fluidity and low shrinkage. Such materials allow smoother flow through gates, reducing marks.
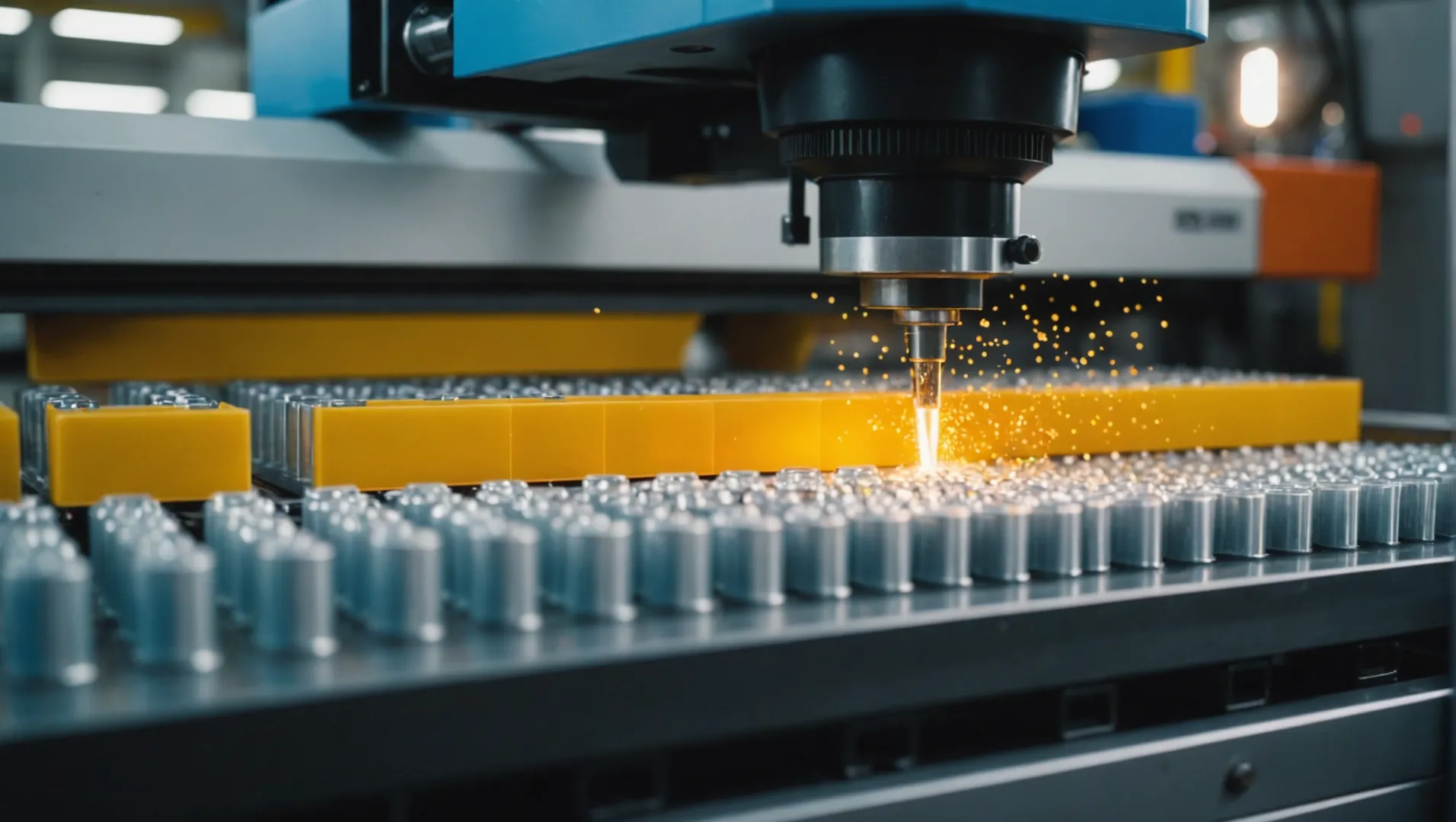
Understanding Plastic Material Properties
When aiming to reduce gate marks, the choice of plastic material plays a crucial role. The properties of these materials directly influence how well they fill the mold and how much they shrink upon cooling.
-
Fluidity: Materials with high fluidity, such as certain grades of polypropylene and polyethylene, flow more easily into the mold cavities. This ease of flow helps prevent the excessive buildup of material at the gate, which can lead to marks. Learn more about fluidity3.
-
Shrinkage: Low shrinkage materials like polycarbonate tend to hold their shape better as they cool, minimizing distortions at the gate. Discover low shrinkage materials4.
Comparing Different Plastics
Let’s consider a comparison of common plastics used in injection molding and their suitability for reducing gate marks:
Material | Fluidity | Shrinkage | Suitability for Reducing Gate Marks |
---|---|---|---|
Polypropylene | High | Moderate | High |
Polyethylene | High | Moderate | High |
Polycarbonate | Moderate | Low | Moderate |
ABS (Acrylonitrile Butadiene Styrene) | Moderate | Moderate | Moderate |
Tailoring Material Selection to Product Needs
The choice of material should align with the product’s requirements beyond just reducing gate marks. For instance, if the product requires high impact resistance, polycarbonate might be more suitable despite its moderate fluidity. Explore impact resistance5.
Moreover, it is critical to consider the temperature sensitivity6 of these materials, as some may require higher processing temperatures that could affect their flow characteristics.
Balancing Material and Process Adjustments
While selecting appropriate materials is vital, it’s essential to combine this with process parameter adjustments such as optimizing the injection speed and temperature settings to enhance overall results. This combination can lead to significant improvements in reducing gate marks without compromising the structural integrity or aesthetic quality of the molded parts.
Polypropylene has high fluidity for injection molding.True
Polypropylene flows easily into mold cavities, reducing gate marks.
Polycarbonate has high shrinkage in injection molding.False
Polycarbonate exhibits low shrinkage, minimizing distortions at gates.
How Can Regular Maintenance Reduce Gate Mark Issues?
Gate marks can compromise the quality of injection molded products, but regular maintenance can significantly mitigate these issues.
Regular maintenance of molds and equipment is crucial in minimizing gate mark issues by preventing impurities and ensuring optimal functioning.
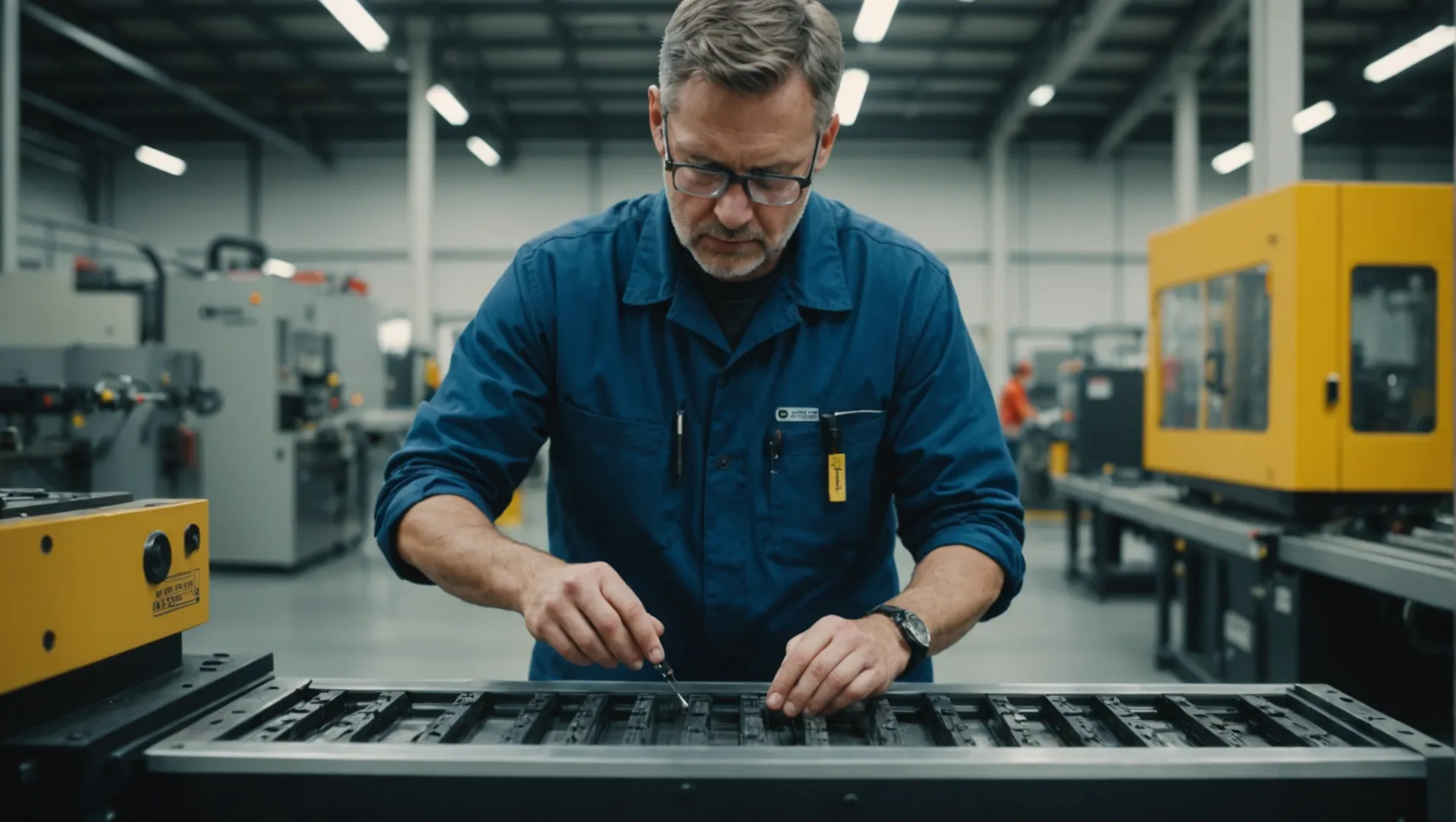
Understanding Gate Marks
Gate marks are blemishes or imperfections that occur at the point where molten plastic enters the mold. They are often caused by irregularities in the injection molding process or flaws in mold design. Regular maintenance can address these problems by ensuring smooth operations and consistent quality.
The Role of Equipment Maintenance
Maintaining injection molding machines is paramount in reducing gate marks. Regular cleaning and inspection7 of molds prevent the accumulation of dirt and impurities that can obstruct plastic flow, causing inconsistencies. Ensuring that all parts of the machine are in good working order minimizes disruptions in the injection cycle, which can lead to uneven cooling and gate mark formation.
Key Maintenance Practices:
- Routine Cleaning: Remove any build-up from molds and equipment to maintain smooth plastic flow.
- Lubrication: Regularly lubricate moving parts to prevent wear and ensure smooth operation.
- Calibration: Frequently calibrate machines to ensure they operate within specified parameters.
Mold Surface Maintenance
The condition of mold surfaces is critical in managing gate marks. Imperfections on mold surfaces can lead to air entrapment and inconsistent cooling, resulting in visible marks.
Steps for Mold Surface Care:
- Inspect for Damage: Regularly check for scratches or other damage that may affect the final product.
- Polish Surfaces: Ensure surfaces are polished to a fine finish to minimize friction and enhance plastic flow.
- Coating Applications: Apply anti-corrosion coatings to extend the mold’s lifespan and maintain quality.
Monitoring System Performance
Advanced monitoring systems can detect minor deviations in process parameters early on, allowing for prompt adjustments. This proactive approach helps in maintaining optimal conditions for molding, thus reducing gate mark occurrences.
Implementing these maintenance strategies not only reduces gate mark issues but also enhances overall production efficiency and product quality. Regular upkeep is a cost-effective approach to managing and preventing defects, ultimately leading to better end products.
Regular maintenance reduces gate mark issues in molds.True
Maintenance prevents impurities and ensures equipment functions optimally.
Ignoring mold maintenance leads to fewer gate marks.False
Neglecting maintenance increases impurities, causing more gate marks.
Conclusion
By combining parameter adjustments and mold optimizations, you can significantly reduce gate marks and enhance the quality of your products.
-
Explore strategies for optimizing injection molding settings to improve product quality.: The 8 Key Parameters in Injection Molding Process Optimization to Avoid Defects · 1. Temperature Control: · 2. Injection Speed: · 3. Cooling … ↩
-
Discover how strategic mold design minimizes defects like gate marks.: Mike Baranoski, a Design Engineer at Rodon, discusses how his role and having a solid design are critical to the plastic injection molding process. ↩
-
Fluidity impacts mold filling efficiency, reducing gate marks.: ①Plastic temperature during injection molding: high material temperature increases fluidity, but different plastics have their own differences. ↩
-
Low shrinkage reduces distortions, minimizing gate marks.: The shrinkage of molded plastic parts can be as much as 20% by volume when measured at the processing and ambient temperature. ↩
-
High impact resistance is crucial for durable products.: Acrylonitrile butadiene styrene (ABS) is a popular choice among manufacturers, as it boasts high impact resistance at a mid-range cost. ↩
-
Temperature sensitivity affects plastic flow and quality.: Mold temperature refers to the surface temperature of the mold cavity and core. It is one of the most basic control parameters in the injection molding process. ↩
-
Discover how cleaning equipment enhances plastic flow and reduces defects.: An injection mold’s condition influences the quality of the plastic components and performing maintenance increases tool longevity and part quality. Injection … ↩