Have you ever felt overwhelmed by the complexities of small batch injection molding? Trust me, you’re not alone. Let’s explore some common hurdles together and uncover practical solutions that could transform your production process.
Small batch injection molding faces challenges such as high costs due to mold expenses, unstable quality from process parameter fluctuations, and long production cycles. Solutions include rapid mold technology, optimizing processes, and improving supplier collaboration.
While these core solutions offer a glimpse into effective management of small batch injection molding, diving deeper into each aspect can unveil further insights. Continue reading to explore detailed strategies and expert advice tailored for small batch production.
Rapid mold technology reduces production costs.True
3D printing and silicone molds lower costs by reducing mold expenses.
How Can Rapid Mold Technology Lower Production Costs?
In the competitive arena of manufacturing, rapid mold technology emerges as a game-changer in reducing production costs, especially for small batch productions.
Rapid mold technology, such as 3D printing and silicone molds, significantly reduces production costs by lowering mold expenses and shortening production cycles. These innovative methods offer flexibility and efficiency, making them ideal for small batch manufacturing where cost control is paramount.
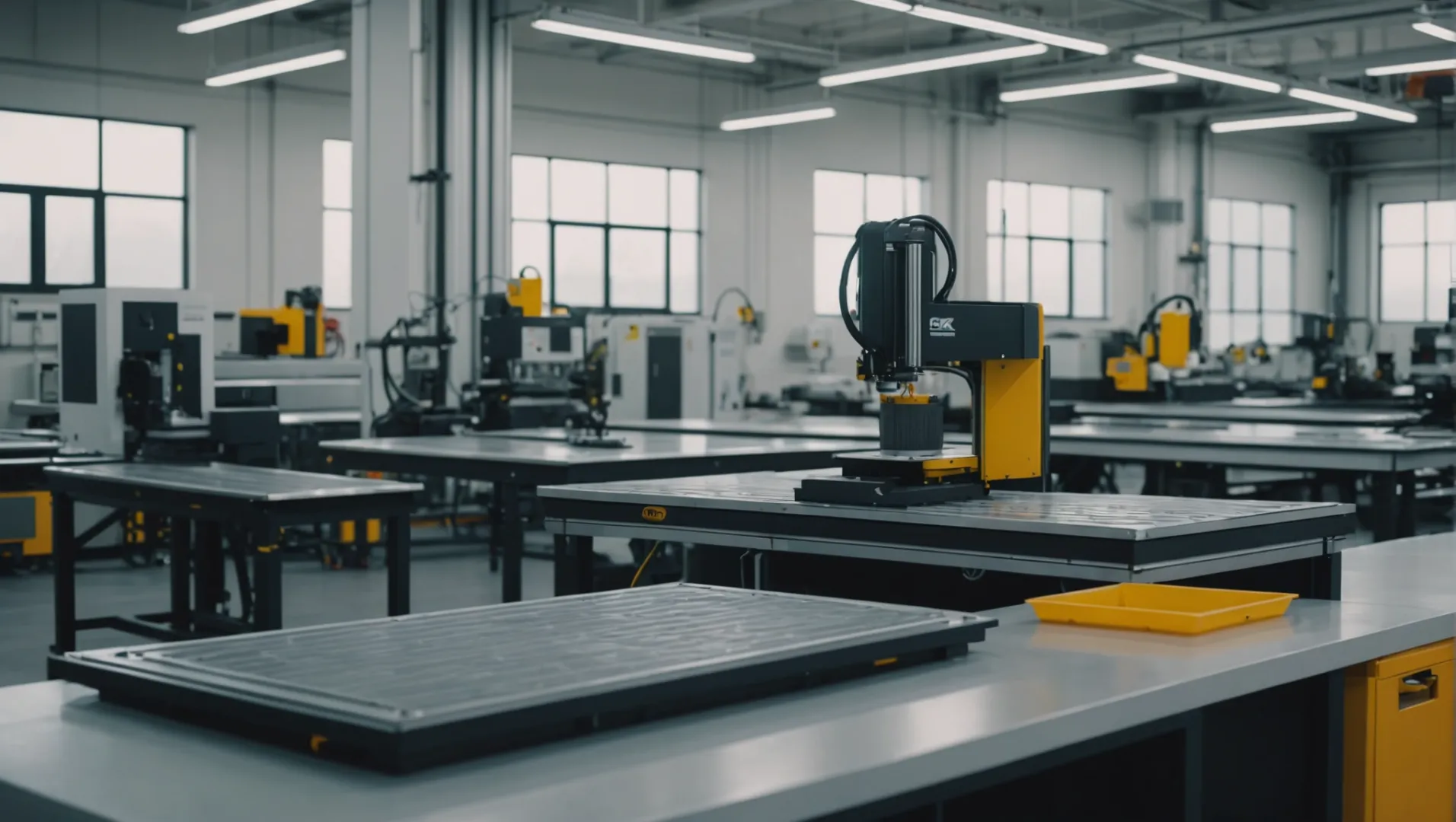
Understanding Rapid Mold Technology
Rapid mold technology encompasses a range of techniques designed to speed up the creation of molds while reducing costs. Two popular methods are 3D printing and silicone molding. Unlike traditional metal molds, these alternatives offer shorter production times and lower material costs, albeit with some trade-offs in durability.
-
3D Printing: This method allows for quick prototyping and mold creation. With advances in industrial 3D printing1, manufacturers can create intricate designs at a fraction of the cost of traditional methods. Although not as durable, 3D-printed molds are perfect for small batches where frequent changes might be required.
-
Silicone Molding: Silicone molds are cost-effective, especially for producing prototypes or small batches. They require less upfront investment compared to metal molds and offer a reasonable lifespan for low-volume production.
Advantages Over Traditional Methods
-
Cost Reduction
- Material Savings: Both 3D printing and silicone molding use less expensive materials compared to metal molds.
- Reduced Labor Costs: These methods require less manual labor for mold creation, further cutting down expenses.
-
Time Efficiency
- Faster Production Cycles: Rapid mold technology drastically reduces the time from design to production, enabling quicker market entry.
- Quick Adjustments: In small batch manufacturing, the ability to quickly modify molds without significant delays is invaluable.
-
Flexibility in Design
- Rapid mold technology supports complex designs that may be cost-prohibitive with traditional molds. This flexibility allows manufacturers to innovate without escalating costs significantly.
Implementing Rapid Mold Technology
- Standardization: Standardizing the use of rapid mold technology across projects can streamline operations and ensure consistent quality.
- Collaboration with Suppliers: Establishing strong relationships with suppliers who specialize in rapid mold technologies can lead to better pricing and faster turnaround times.
- Investment in Technology: While initial investments might be necessary, the long-term savings on production costs make it worthwhile for companies focused on small batch manufacturing.
By leveraging rapid mold technology, manufacturers can maintain a competitive edge in small batch production, balancing quality with cost-effectiveness.
3D printing molds are more durable than metal molds.False
3D-printed molds are less durable but suitable for small batches.
Silicone molding requires higher upfront investment than metal molds.False
Silicone molds need less upfront investment, ideal for low-volume production.
What Role Does Supplier Collaboration Play in Quality Control?
Supplier collaboration can be a game-changer in enhancing quality control for small batch injection molding. By fostering a strong partnership, companies can streamline processes, ensure raw material consistency, and ultimately, improve product quality.
Supplier collaboration enhances quality control by ensuring consistent raw materials and timely deliveries, which helps maintain stable production parameters and reduces defects.
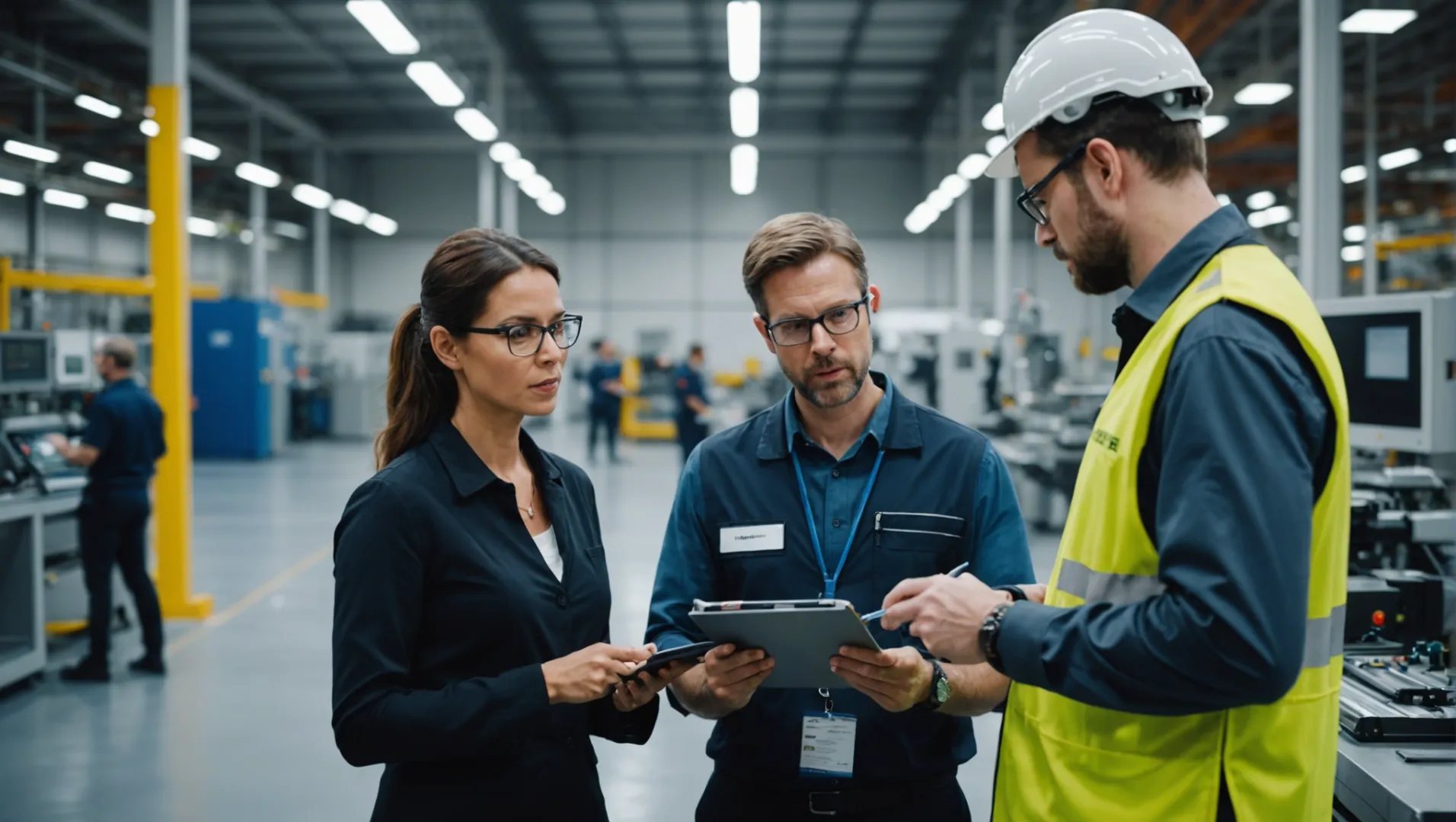
Enhancing Raw Material Consistency
One of the primary benefits of supplier collaboration is the ability to ensure consistent raw material quality. By establishing robust relationships with suppliers, manufacturers can work closely to select the right materials that meet specific quality standards. This collaboration involves regular communication and feedback loops to keep suppliers informed about any changes in requirements or specifications.
For instance, if a supplier understands the criticality of maintaining material properties across batches, they can implement stricter quality checks before dispatching materials. This reduces the likelihood of discrepancies in material quality, which is crucial in small batch production where even minor variations can lead to significant defects.
Streamlining Communication for Efficiency
Effective supplier collaboration also involves transparent and open communication channels. This helps in minimizing misunderstandings and ensuring that any potential issues are addressed promptly. Regular meetings or updates between the supplier and manufacturer allow both parties to stay aligned on production goals and timelines.
Incorporating technology like Supplier Relationship Management (SRM) systems can further enhance this communication. These platforms enable real-time data sharing and tracking of materials, ensuring that both parties are updated about any changes or delays instantly.
Reducing Production Delays
Collaboration with suppliers ensures that raw materials are available when needed, reducing potential production delays. A well-coordinated supply chain means that manufacturers can rely on their suppliers for timely deliveries, which is essential to maintain the production schedule.
To foster this reliability, manufacturers might consider strategies such as joint inventory management. By sharing inventory levels with suppliers, both parties can plan and manage stock levels more effectively, ensuring materials are available just in time for production needs.
Building Long-Term Relationships for Quality Assurance
Long-term partnerships with suppliers lead to better understanding and mutual trust, which is pivotal for quality assurance. Such relationships often result in suppliers prioritizing the needs of their loyal customers, offering customized solutions, or providing priority service during high-demand periods.
Through consistent engagement and collaboration, manufacturers can work with suppliers to continuously improve material quality and adapt quickly to any necessary changes in production processes or material specifications.
Conclusion: Maximizing Quality through Collaboration
By fostering strong supplier relationships, manufacturers can tackle some of the primary challenges in small batch injection molding—namely, maintaining consistent quality and minimizing delays. This collaborative approach not only enhances quality control but also contributes significantly to reducing costs and improving overall efficiency in production.
For further insights on enhancing supplier relationships, you may want to explore topics such as effective communication strategies2 in supply chains and utilizing technology3 for better supplier management.
Supplier collaboration reduces production delays.True
Collaboration ensures timely material delivery, minimizing delays.
Supplier collaboration has no impact on raw material consistency.False
Collaboration ensures consistent material quality, reducing defects.
How to Optimize Process Parameters for Consistent Quality?
Achieving consistent quality in small batch injection molding hinges on optimizing process parameters effectively. A delicate balance between precision and adaptability can lead to superior product quality and minimized waste.
To optimize process parameters for consistent quality in small batch injection molding, establish a process database, standardize parameter settings, and integrate real-time monitoring systems. These steps help maintain stability across batches and reduce variability.

Understanding the Role of Process Parameters
In small batch injection molding, process parameters such as temperature, pressure, and cooling time are crucial to product quality. Inconsistent settings can lead to defects like warping or incomplete fills. Establishing a reliable system for tracking these variables4 is key to maintaining product consistency.
Establishing a Process Database
Creating a database that records every parameter setting used during production is an invaluable tool. This database allows manufacturers to analyze past productions to identify successful configurations and avoid previously problematic ones. It should include:
- Material Type: As different materials react uniquely under similar conditions, tracking material specifics helps in predicting behavior.
- Machine Settings: Documenting exact machine settings ensures repeatability.
- Environmental Conditions: Ambient temperature and humidity can influence the molding process.
Data Point | Importance |
---|---|
Material Type | Predicts material behavior |
Machine Settings | Ensures repeatability |
Environmental Data | Accounts for external influences |
Standardizing Parameter Settings
Once optimal parameters are identified, standardization is essential. This involves training staff on these settings and regularly calibrating equipment to maintain consistency. Standardization not only reduces variability but also streamlines the production process by minimizing the need for constant adjustments.
Real-Time Monitoring and Adjustments
Integrating real-time monitoring systems can significantly enhance quality control. These systems track key metrics and alert operators to deviations from set parameters. Implementing advanced monitoring technologies5 allows for:
- Immediate corrective actions.
- Reduced waste due to less trial-and-error.
- Enhanced understanding of parameter impacts.
Real-time data also contributes to a more responsive production environment where issues can be addressed before they impact the entire batch.
Leveraging Data Analytics
Data analytics tools can provide deeper insights into the relationship between process parameters and product quality. By analyzing historical data, manufacturers can develop predictive models that forecast outcomes based on specific settings. This proactive approach supports continuous improvement efforts and fosters innovation in process optimization.
Standardizing settings reduces production variability.True
Standardization ensures consistent application of optimal parameters, minimizing variability.
Real-time monitoring increases waste in production.False
Real-time monitoring reduces waste by enabling immediate corrective actions.
What Are the Benefits of Concurrent Engineering in Injection Molding?
Concurrent engineering transforms the injection molding process by integrating design, manufacturing, and quality assurance, leading to more efficient production cycles and superior product quality.
Concurrent engineering enhances injection molding by reducing time-to-market, improving product quality, and cutting costs through integrated design and production processes.
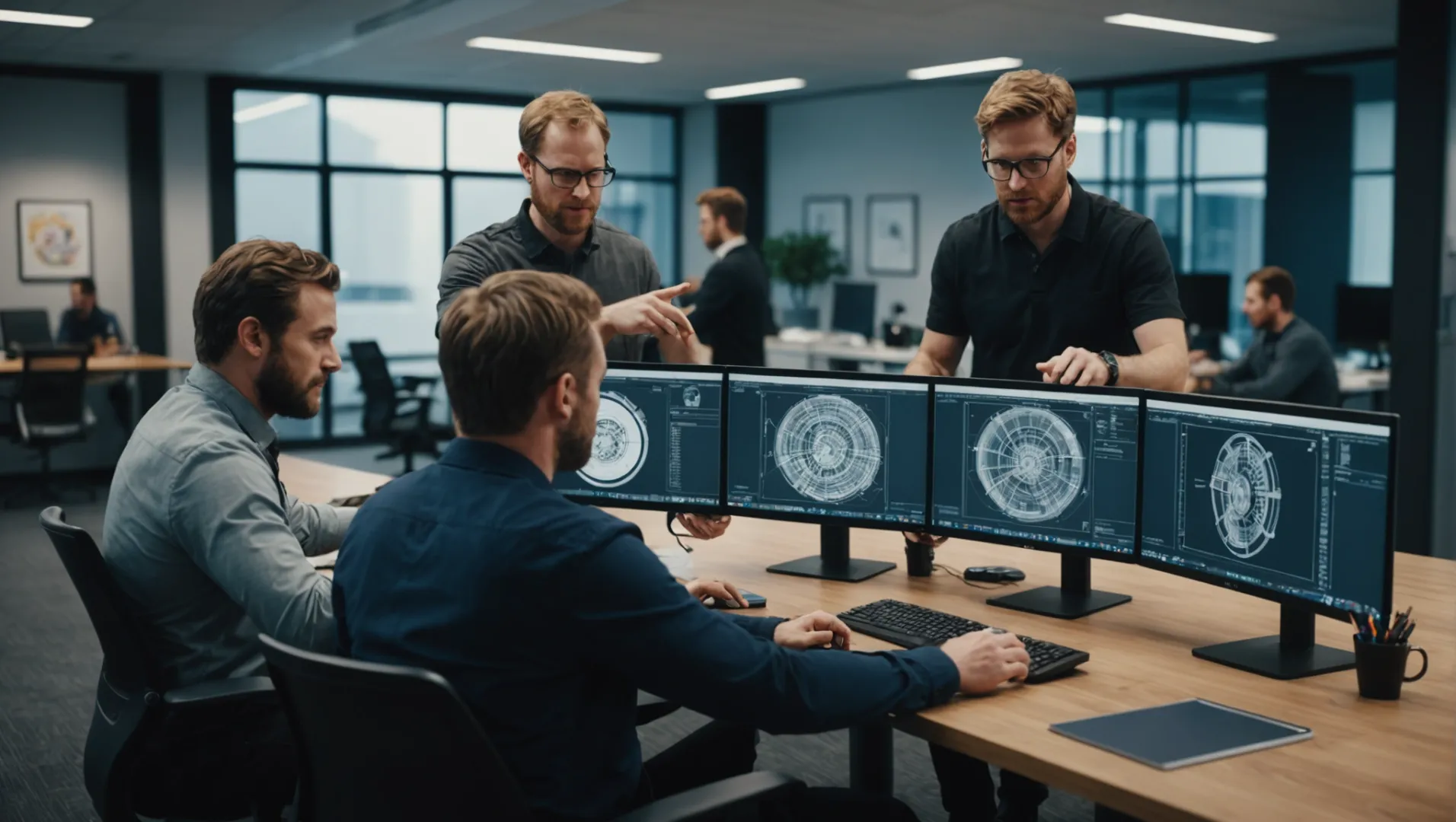
Integrated Design and Production
Concurrent engineering enables simultaneous collaboration6 among designers, engineers, and manufacturers. This integration fosters a seamless flow of information, reducing the risk of miscommunication and errors. For example, when mold design occurs alongside product design, potential manufacturing issues can be identified and resolved early, minimizing costly redesigns.
Reduced Time-to-Market
By employing concurrent engineering, companies can significantly shorten their product development cycle. This approach allows for multiple project phases to occur in parallel rather than sequentially. Consequently, tasks like mold creation and production setup are initiated before the final design approval, expediting the entire process.
Enhanced Product Quality
When quality assurance teams are involved from the beginning, they can influence design decisions that directly impact product quality. Concurrent engineering encourages constant feedback loops, ensuring any design flaws are addressed swiftly. This proactive stance leads to fewer defects and enhances the overall reliability of the final product.
Cost Efficiency
By detecting potential issues earlier in the design phase, concurrent engineering helps in reducing the need for extensive modifications later. This not only saves on material and labor costs but also prevents production delays. Additionally, by aligning different departments’ objectives early on, wasteful practices are minimized, leading to cost-effective manufacturing.
Improved Communication
A vital advantage of concurrent engineering is the improved communication channels7 it establishes among different teams. Regular meetings and collaborative platforms enable stakeholders to remain aligned with project goals, ensuring everyone is updated on progress and potential roadblocks.
Case Study: A Practical Example
Consider a company producing custom automotive parts through injection molding. By implementing concurrent engineering, they were able to reduce their development cycle by 20%, cut production costs by 15%, and increase product launch success rates by focusing on cross-departmental collaboration from day one. This example underscores the tangible benefits of adopting a concurrent engineering approach in injection molding.
Concurrent engineering reduces injection molding time-to-market.True
Concurrent engineering allows parallel processing, speeding up development.
Concurrent engineering increases injection molding production costs.False
It reduces costs by minimizing redesigns and improving efficiency.
Conclusion
In summary, addressing the challenges of small batch injection molding requires strategic planning and innovative solutions. By focusing on cost reduction, quality stability, and efficient production cycles, manufacturers can enhance their operations and remain competitive in the market.
-
Discover how industrial 3D printing creates cost-effective molds quickly.: For industrial manufacturers, 3D printing offers new ways to improve manufacturing processes, develop new business models and drive innovation. ↩
-
Explore methods to improve supplier-manufacturer communication efficiency.: 1. Set Clear Expectations from the Beginning When Communicating with Suppliers · 2. Identify Supply Chain Planning Stakeholders · 3. Prioritize … ↩
-
Discover how technology aids in managing supplier relationships effectively.: Understand what supplier management is, how to execute it, learn the best practices, and discover how technology can contribute. ↩
-
Explore how tracking parameters enhances consistency across production.: Here are the 8 key parameters in injection molding that you need to align in order to produce consistent, high quality plastic parts. ↩
-
Discover benefits of advanced monitoring for quality assurance.: SmartMOLD is a cloud-based software platform dedicated to the plastics industry providing real-time data to drive injection molding innovation. ↩
-
Explores how concurrent engineering integrates design with production efficiently.: Concurrent engineering provides benefits such as multidisciplinary collaboration, improved productivity, and a faster design process. ↩
-
Highlights how improved communication channels enhance collaboration.: Benefits of concurrent engineering · Innovative solutions · Early modifications · Minimized risk of loss · Reduced time to market. ↩