All Posts
blog & article
read our latest newsletter
Whether you’re curious about material selection, product design, mold design, mold making and injection molding, feel free to ask us anything. Our team is ready to provide the guidance and insights you need.
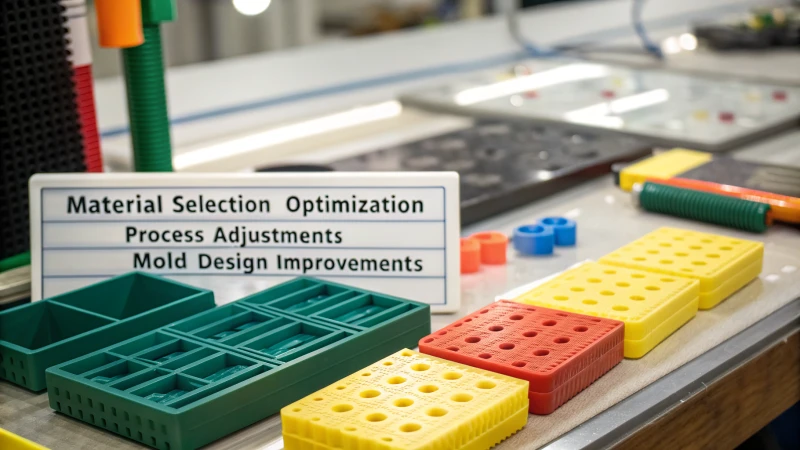
How Can You Effectively Handle Gate Marks from Point Gates?
Dealing with gate marks in injection molding can be challenging. This article explores various methods to effectively manage these imperfections, including manual and mechanical grinding techniques, chemical treatments like solvent wiping and polishing, advancements in hot runner technology, and strategic ...
OPTIMIZATION
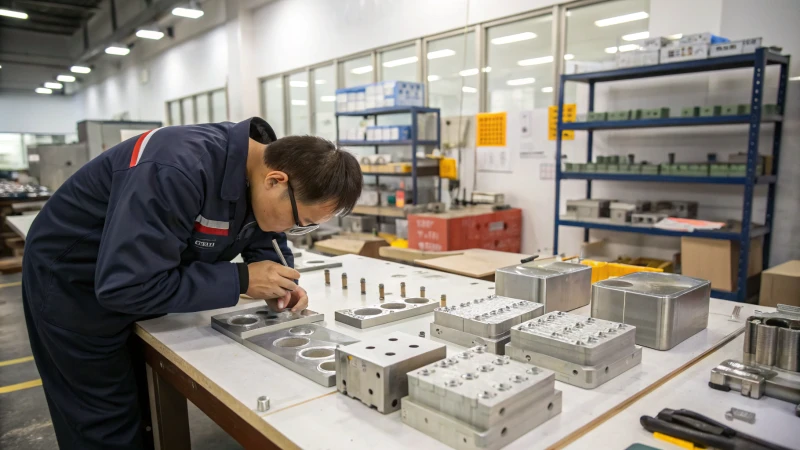
What Are the Most Common Defects in Mold Manufacturing?
This article explores common defects in mold manufacturing such as dimension deviations, surface quality issues, shape errors, and fitting problems. It discusses their causes—like equipment precision mistakes and poor assembly methods—and the significant impact these flaws have on product quality. ...
MANUFACTURING

What Impact Do Mold Design Issues Have on Injection Molding Process Parameters?
This article explores how mold design issues affect the injection molding process. It highlights the importance of gate size, runner system layout, and exhaust design in optimizing production efficiency and reducing defects. By understanding these elements, designers can enhance the ...
DESIGN
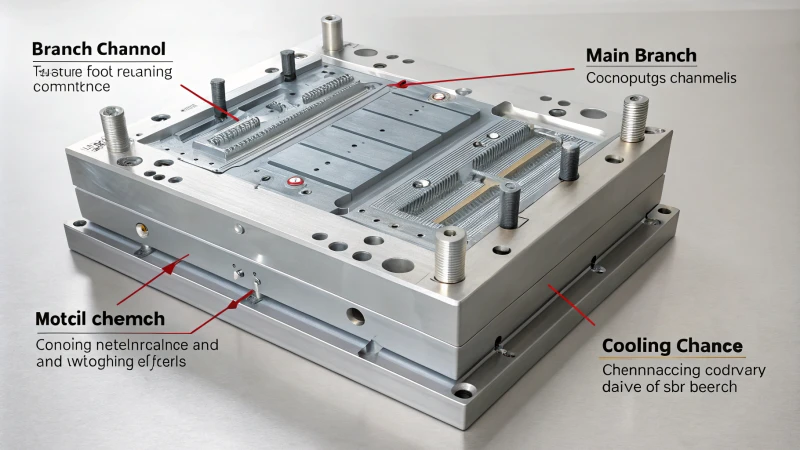
How Does the Design of Main and Branch Channels Affect Mold Service Life?
This article explores how the design of main and branch channels in injection molds affects their service life. Key factors such as channel size, surface smoothness, taper angles, and alignment with cooling systems are crucial for reducing wear and thermal ...
DESIGN
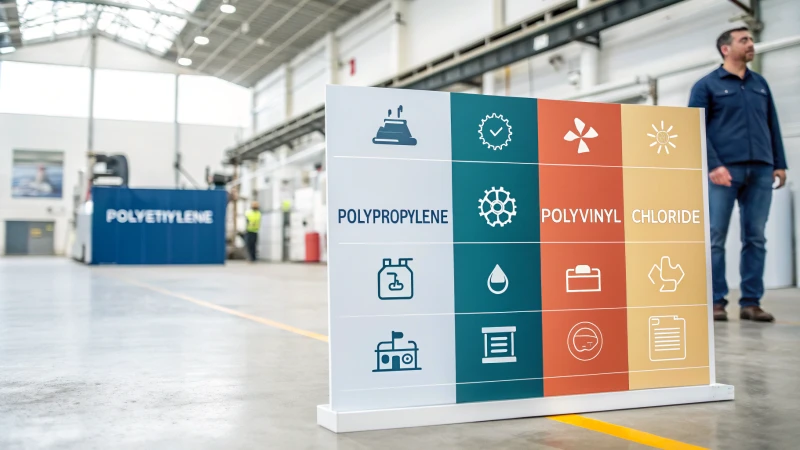
What Are the Optimal Processing Temperature Ranges for Various Plastic Materials?
This article explores the optimal processing temperature ranges for different plastic materials including polyethylene (LDPE and HDPE), polypropylene (PP), polystyrene (PS), polyvinyl chloride (PVC), polycarbonate (PC), nylon, and ABS. It emphasizes the importance of precise temperature control in achieving high-quality ...
OPTIMIZATION
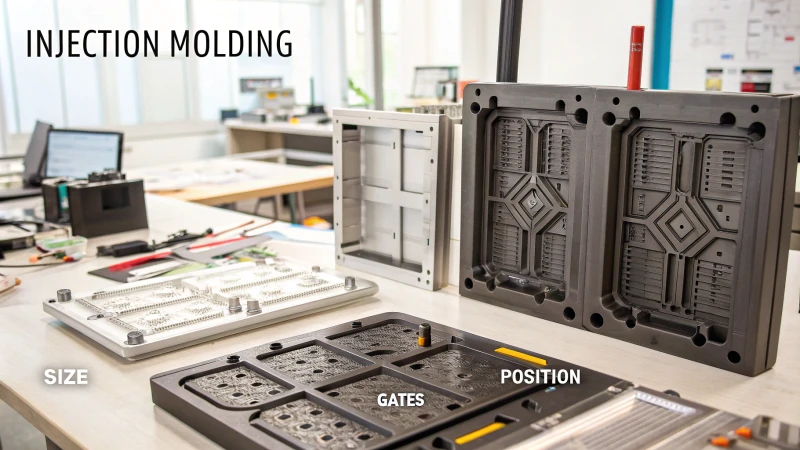
How Does Gate Design Impact Injection Molding Process Parameters?
This article explores how gate design impacts the injection molding process by influencing key parameters such as pressure, speed, and time. It discusses the importance of gate size, position, and quantity in optimizing material flow and minimizing defects like weld ...
DESIGN
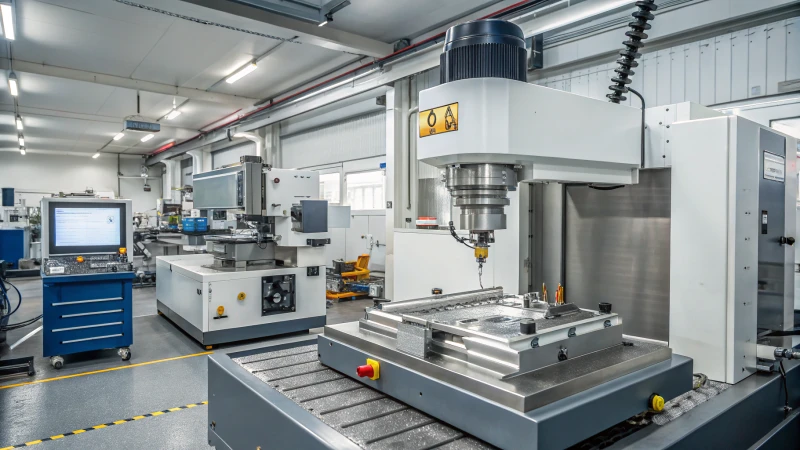
What Are the Best Ways to Reduce Dimensional Deviation in Mold Manufacturing?
Reducing dimensional deviation in mold manufacturing is crucial for achieving high precision and quality. Key strategies include regular maintenance of equipment like CNC machines, careful selection and monitoring of tools, optimizing processing parameters, and thoughtful mold design. Implementing rigorous quality ...
OPTIMIZATION
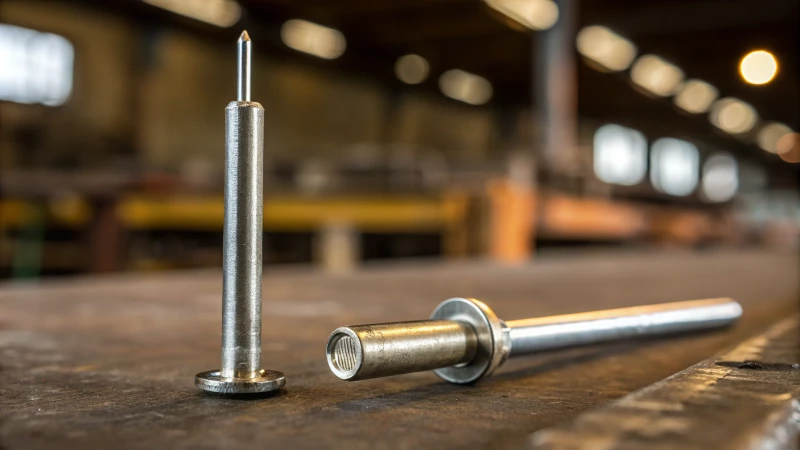
What Distinguishes an Ejector Pin from a Sleeve Pin?
This article explores the differences between ejector pins and sleeve pins in mold design. Ejector pins are straightforward cylindrical rods ideal for simple structures like bottle caps, leaving minimal marks. In contrast, sleeve pins consist of a hollow sleeve and ...
DESIGN
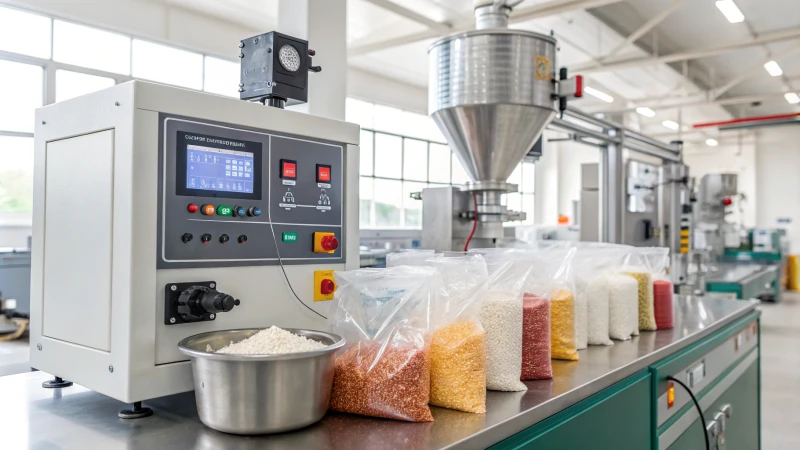
How Do Various Factors Influence the Processing Temperature of Materials?
The processing temperature of materials significantly affects their behavior during manufacturing. Factors such as crystallinity determine melting points; non-crystalline plastics soften over a range. Molecular structure influences flow characteristics, with shorter chains requiring lower temperatures. Additives like plasticizers can reduce ...
MANUFACTURING
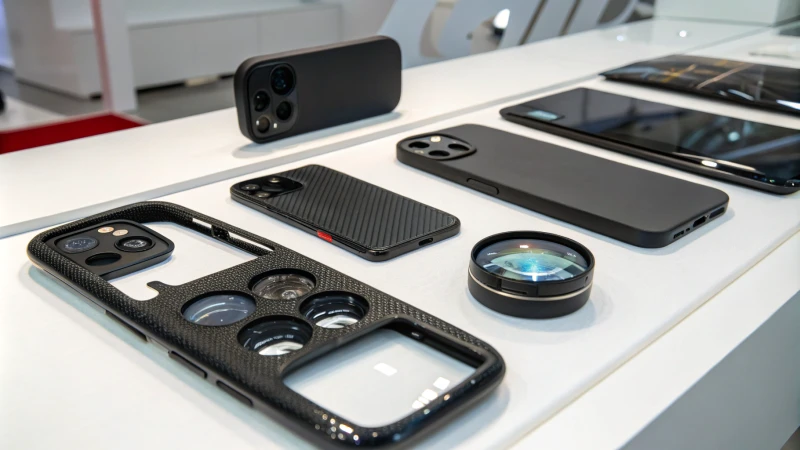
What Injection Molding Products Require High Surface Flatness?
This article explores the critical importance of high surface flatness in injection molding products such as optical lenses, smartphone cases, car dashboards, and household items. It discusses how precise flat surfaces enhance clarity in optical devices, improve aesthetics and functionality ...
Quality Inspection
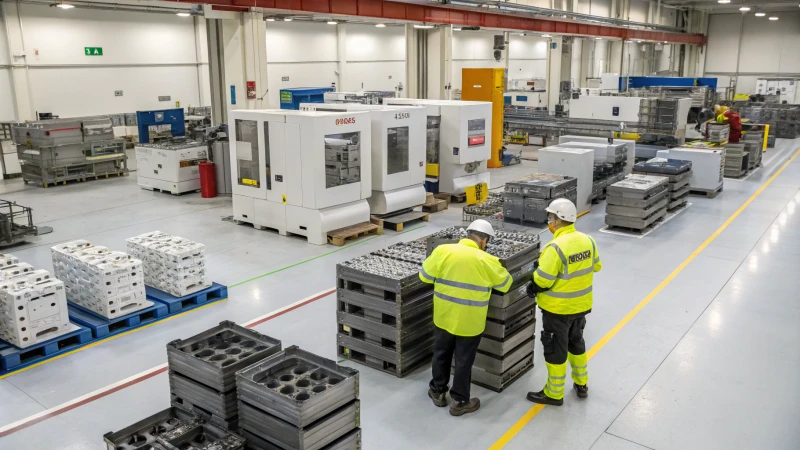
What Are the Key Steps to Examine the Production Management Process of a Mold Manufacturer?
Understanding the production management process is crucial for mold manufacturers to ensure quality and efficiency. This article details key areas to examine during evaluations: raw material management, production planning, machining processes, assembly operations, and quality inspections. Each step is vital ...
Quality Inspection
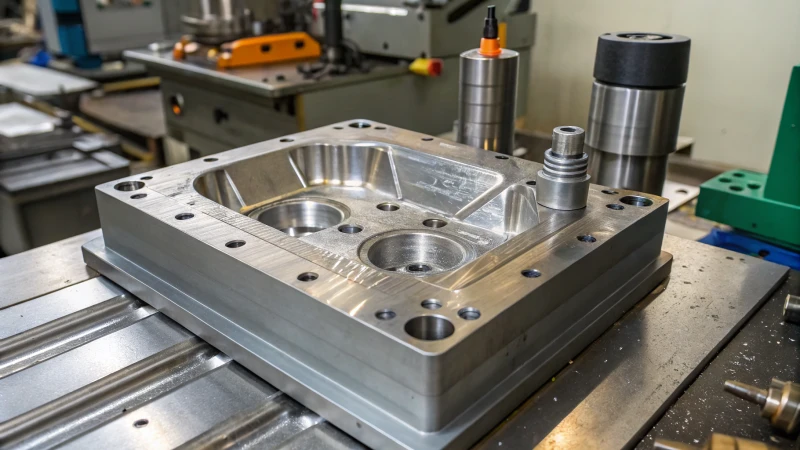
What Causes Short Shot Defects in Plastic Products?
Short shot defects occur when the plastic melt fails to fill the mold completely during injection molding. This issue can stem from various factors including low injection pressure, slow filling speeds, material characteristics such as viscosity and contamination, as well ...
Quality Inspection
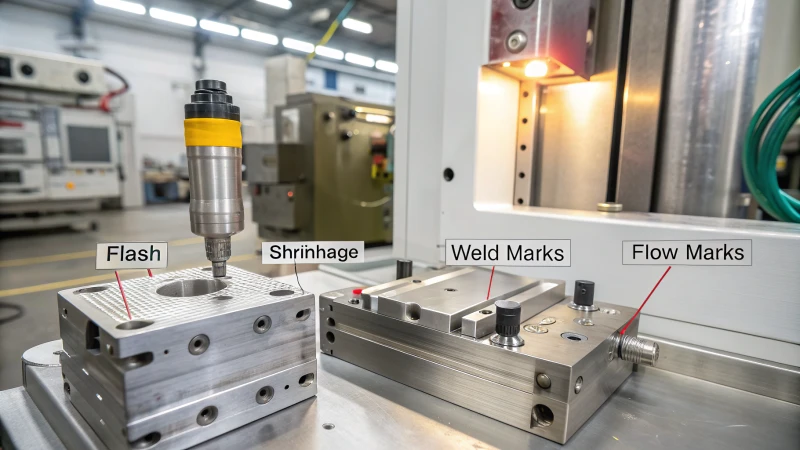
What Are the Most Common Defects in Injection Molded Products?
Injection molded products often suffer from various defects such as flash, shrinkage, weld marks, flow marks, and silver streaks. These flaws arise from issues like excessive pressure, uneven cooling, and moisture in materials. Flash occurs when excess plastic spills over ...
Quality Inspection
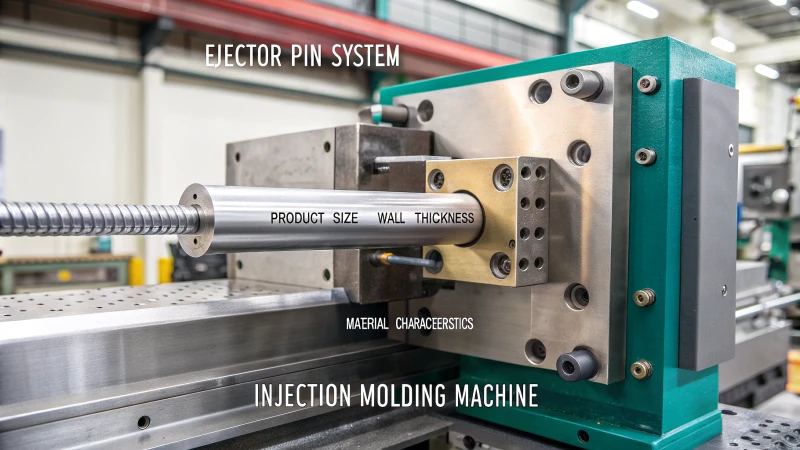
What Factors Influence the Ejection Force of an Ejector Pin?
Understanding the factors influencing ejection force in injection molding is crucial for effective mold design. Key elements include product size and shape, wall thickness, material characteristics, and the design of the ejector mechanism. Larger products typically require greater ejection forces ...
DESIGN
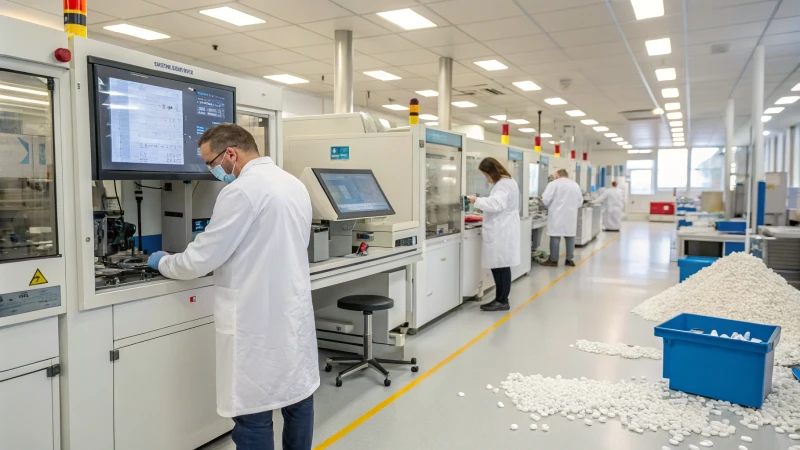
How Do You Determine the Optimal Processing Temperature for Plastic Materials?
This article explores how to determine the optimal processing temperature for plastic materials by examining key factors such as melting points, thermal stability, viscosity, hygroscopicity, and the effects of additives. Understanding these characteristics is crucial for achieving efficient production and ...
OPTIMIZATION
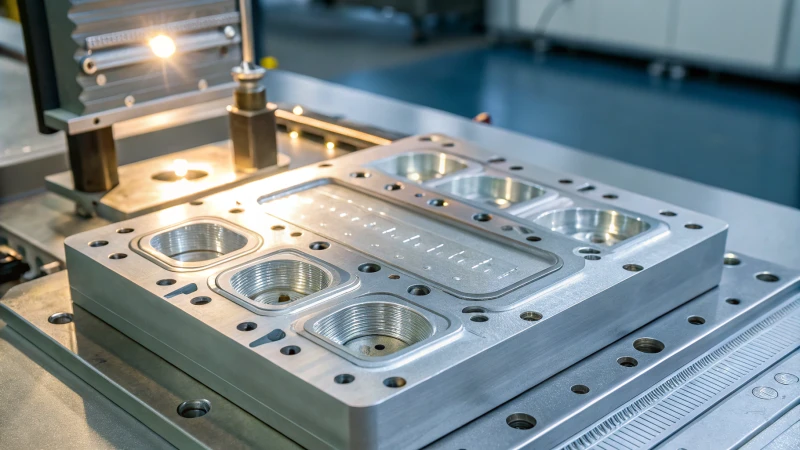
How Does Dimensional Deviation Affect Mold Quality in Manufacturing?
This article explores how dimensional deviation affects mold quality in manufacturing. It highlights the importance of precision in mold design and production, detailing the consequences of inaccuracies on mold performance, assembly difficulties, wear and tear, and overall product quality. Factors ...
MANUFACTURING
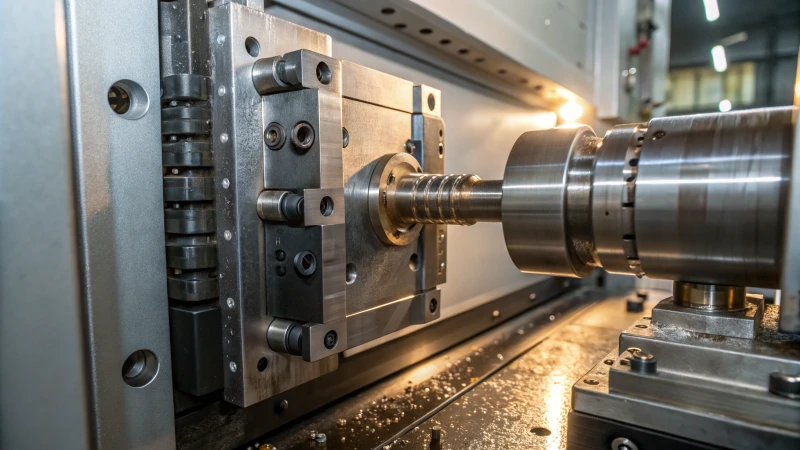
What Are the Key Characteristics and Benefits of a Film Gate?
Film gates, also known as thin-sheet or burr gates, play a crucial role in injection molding by providing excellent flow characteristics. They ensure even melt distribution, which is essential for producing large flat or thin-walled plastic parts without defects. The ...
DESIGN
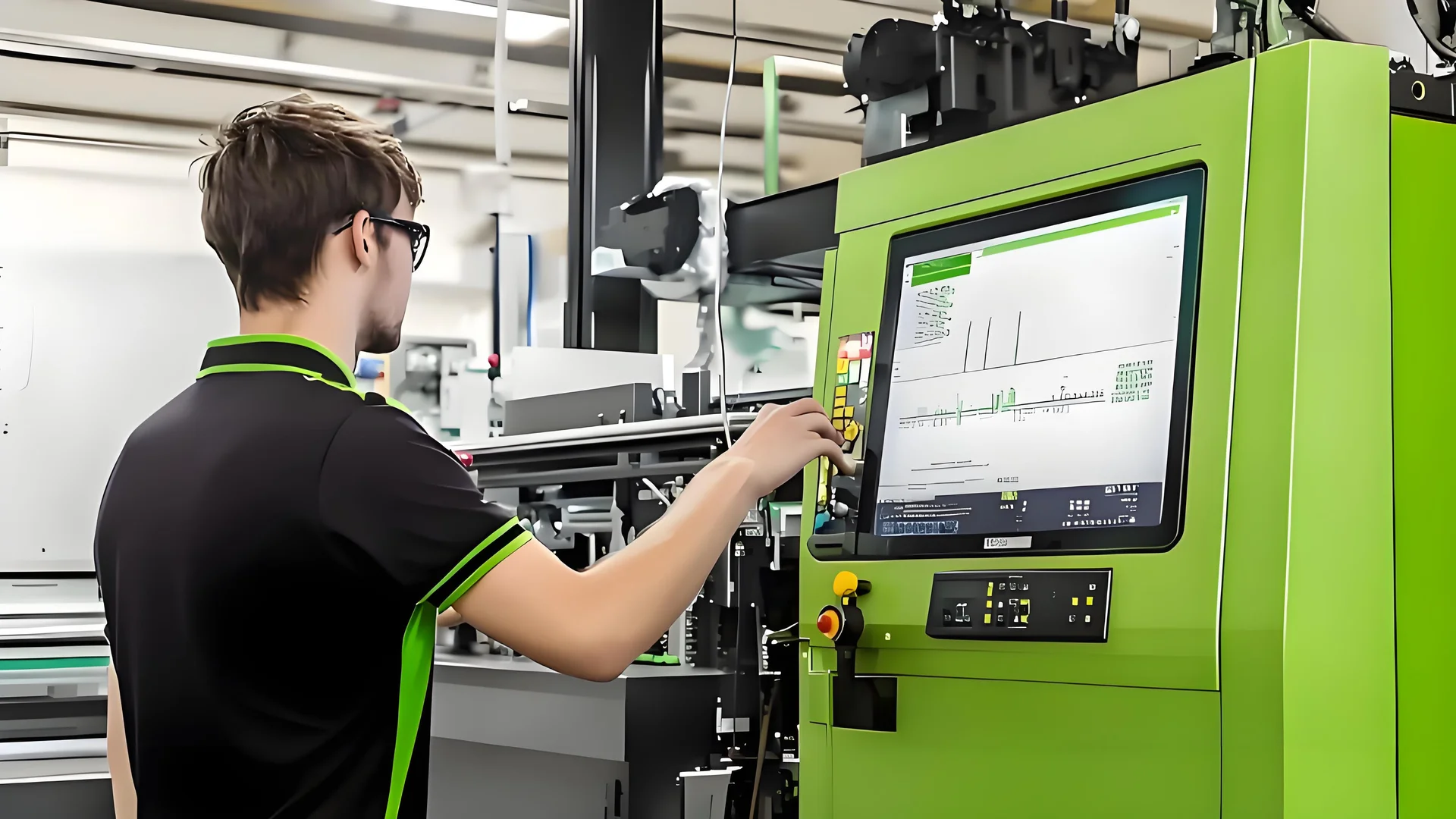
How Do You Optimize Injection Speed and Pressure for Better Performance?
Optimizing injection speed and pressure in molding is essential for achieving high-quality products. Understanding material traits and product designs allows for precise adjustments. Systematic testing helps identify flaws early, ensuring consistent results. Operators should familiarize themselves with machine controls and ...
OPTIMIZATION
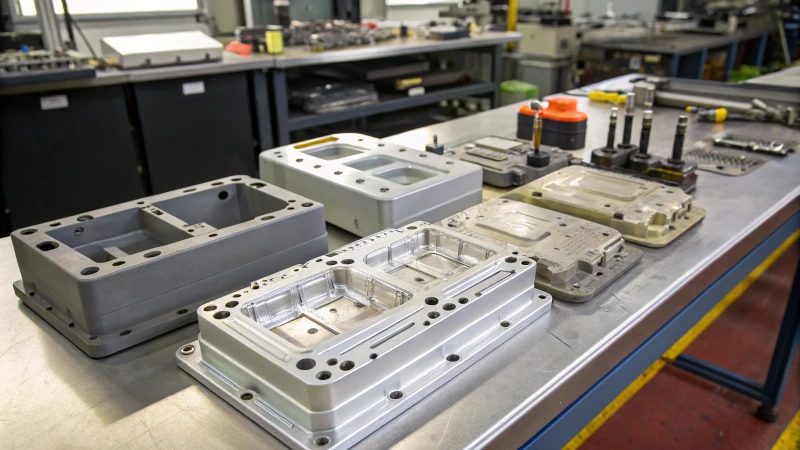
What Are Effective Ways to Reduce Appearance Defects in Injection Molded Products?
Injection molding can lead to various defects like flash, shrinkage, weld marks, flow marks, and silver streaks. This article outlines effective methods for reducing these appearance defects through optimized mold design, careful material selection, and precise adjustments in the injection ...
OPTIMIZATION
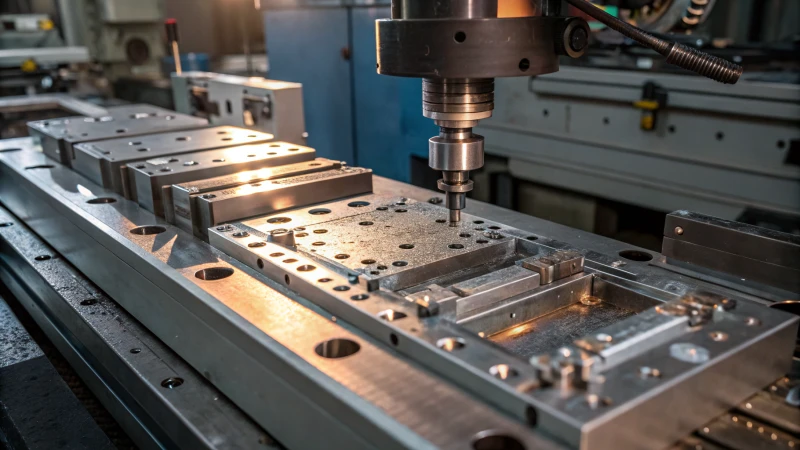
How Can You Increase Ejection Force by Enhancing Mold Structure?
This article explores effective strategies for increasing ejection force in injection molding. Key methods include optimizing the mold design, enhancing ejector mechanisms, strengthening guiding structures, and adjusting demolding angles. By implementing these techniques, manufacturers can achieve smoother product releases, minimize ...
OPTIMIZATION
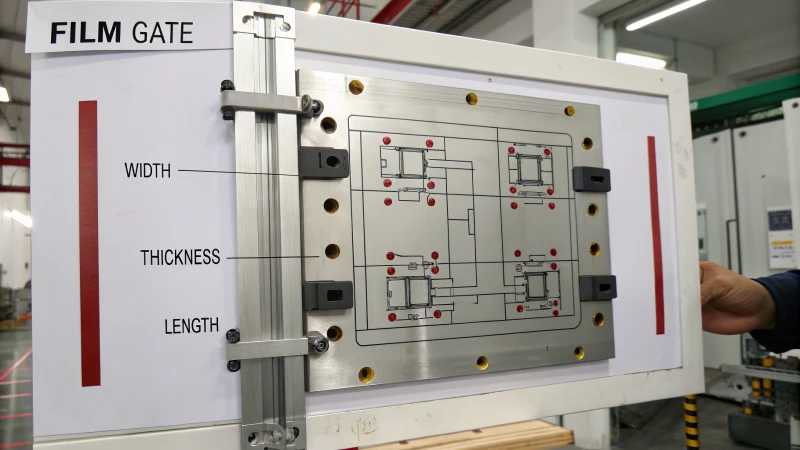
How Can You Determine the Specific Size of a Film Gate?
Determining the correct size of a film gate is crucial in mold design. This article outlines key factors such as product width, wall thickness, material behavior, and gate length. Gate width typically ranges from 25% to 100% of the product ...
DESIGN
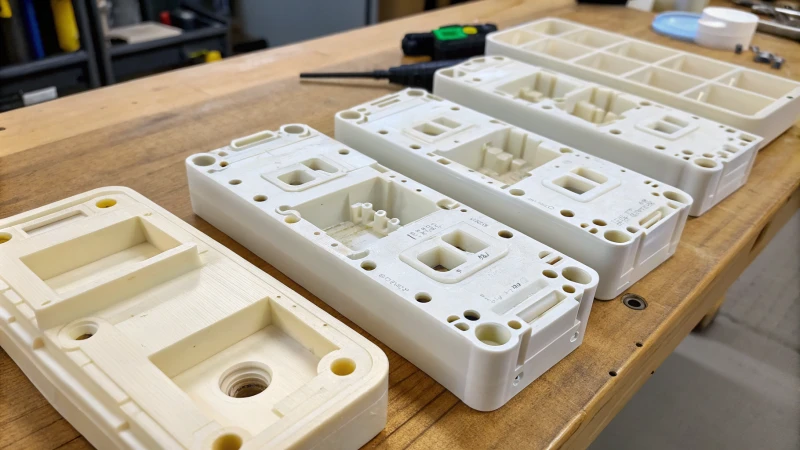
What Are the Common Appearance Defects in Injection Molded Products?
Injection molding can lead to various appearance defects that affect both aesthetics and functionality. Common issues include flash (overflow), shrinkage (dent), weld marks, flow marks, silver streaks, poor gloss, and bubbles. Each defect arises from specific causes such as high ...
Quality Inspection
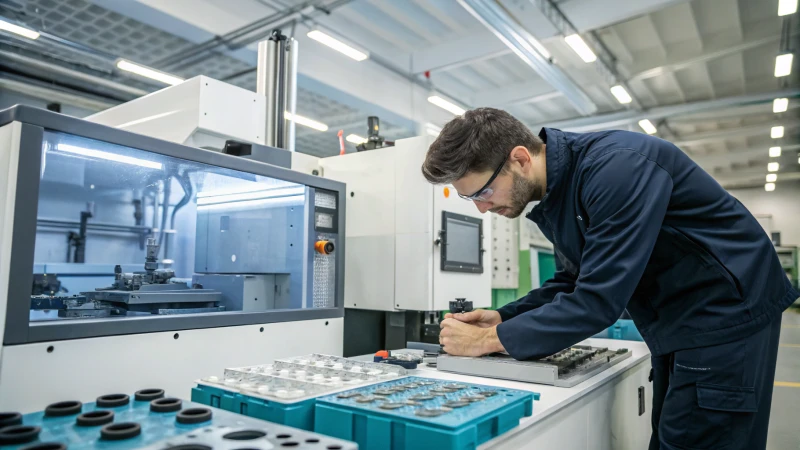
How Can You Adjust Injection Pressure According to Operating Specifications?
This article explores the critical process of adjusting injection pressure in molding operations. It emphasizes the importance of proper training for technicians, thorough equipment inspections, and a deep understanding of material properties. Key steps include starting with lower initial pressure ...
MANUFACTURING
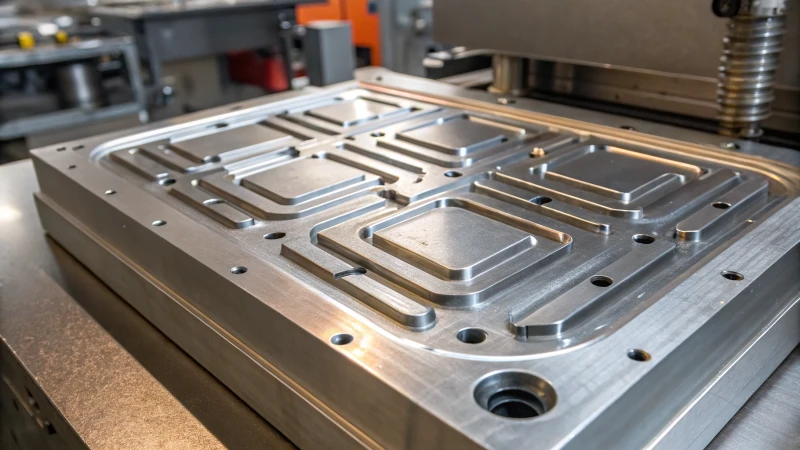
How Does the Design of Main and Branch Channels Influence Mold Production Costs?
This article explores how the design of main and branch channels in mold production affects costs. Key factors include material consumption, processing complexity, and maintenance requirements. Effective channel design can lead to significant savings while maintaining high quality. By understanding ...
DESIGN
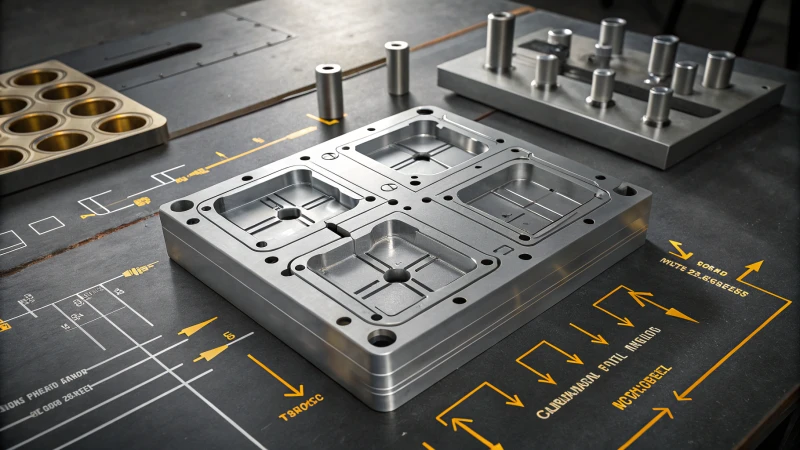
What Are the Design Standards for Main and Branch Channels in Mold Design?
In mold design, adhering to specific standards for main and branch channels is crucial for achieving smooth plastic flow. This article delves into the importance of channel shape, size, layout, and material choice. The main runner typically features a conical ...
DESIGN
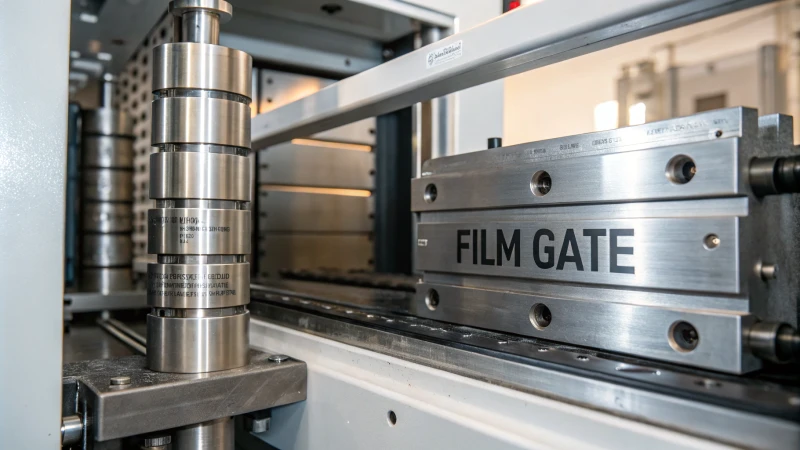
What is the Typical Gate Length of a Film Gate?
Understanding the typical gate length of a film gate is crucial in injection molding. Ranging from 0.5 to 2mm, this length minimizes pressure and heat loss during the process. Smaller products with thin walls require shorter gates (0.5-1mm) for efficient ...
DESIGN
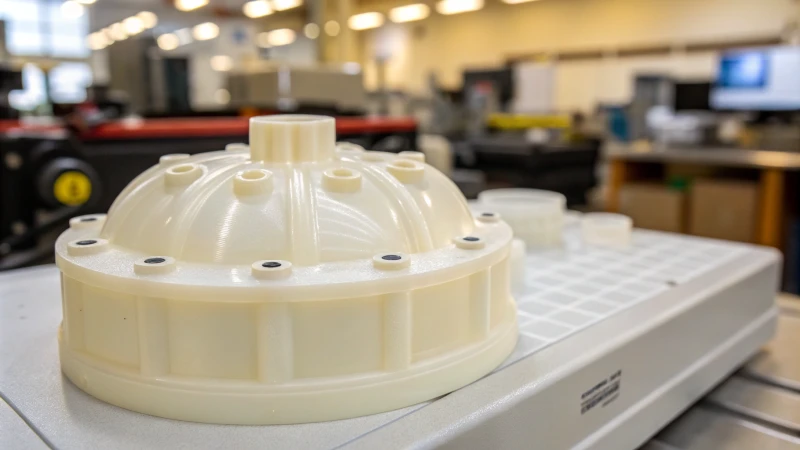
How Can Mold Design Optimization Reduce Flow Mark Defects in Injection Molded Products?
This article explores how optimizing mold design can effectively reduce flow mark defects in injection molded products. Key strategies include refining runner system shapes and sizes to minimize resistance, selecting appropriate gate types for even melt distribution, and implementing effective ...
DESIGN
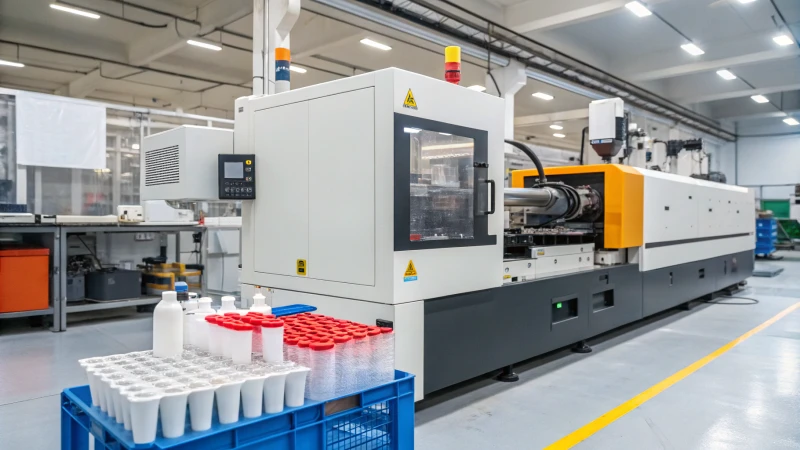
How Does Ejection Force Impact Molds and Plastic Products?
Ejection force plays a critical role in injection molding, affecting both the quality of plastic products and the longevity of molds. Excessive ejection force can lead to surface damage, dimensional inaccuracies, and internal structure failures in molded products, while insufficient ...
OPTIMIZATION
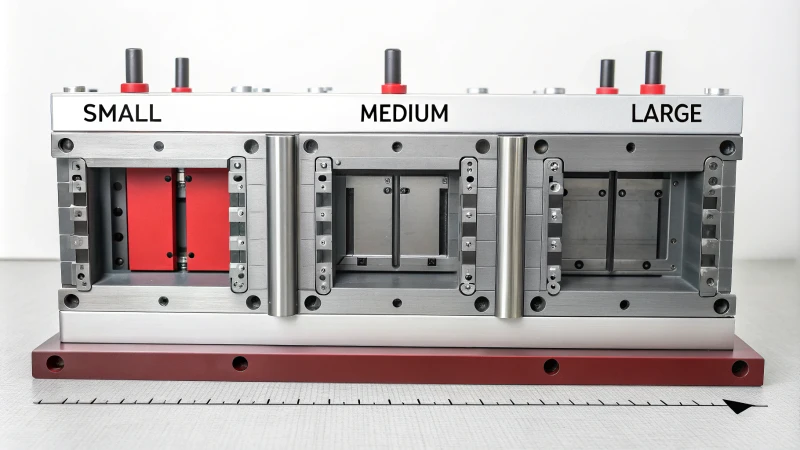
What Is the Best Method to Determine Film Gate Width for Specific Product Size and Wall Thickness?
In injection molding, selecting the correct film gate width significantly impacts product quality and efficiency. This article outlines guidelines based on product size—small (50%-100% of width), medium (30%-70%), and large (20%-50%)—and wall thickness considerations. For thin-wall products, wider gates (40%-80%) ...
OPTIMIZATION
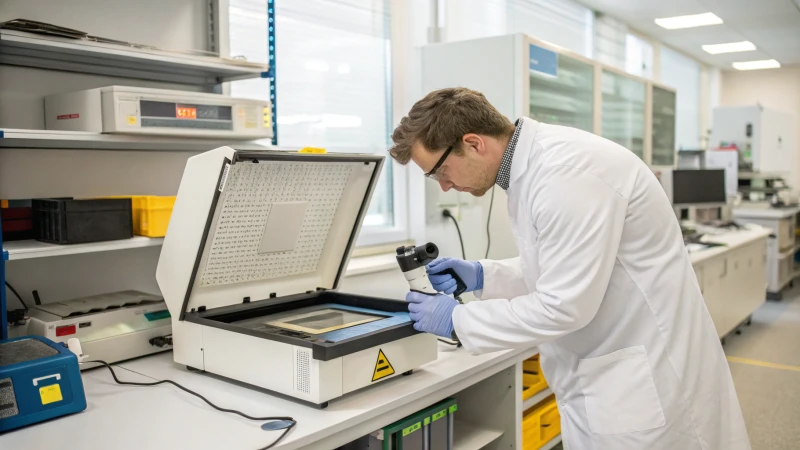
How Do You Choose the Right Processing Temperature for Your Material’s Properties and Application Needs?
Selecting the appropriate processing temperature is essential for achieving desired material properties and product quality. This article explores how factors like crystallinity, thermal stability, flowability, and application requirements influence temperature settings. Crystalline materials require temperatures above their melting points for ...
OPTIMIZATION