Curious about how injection molding becomes as smooth as silk? Everything depends on mastering injection speed and pressure.
To improve injection speed and pressure, first learn the material’s unique traits. Adjust settings based on your product’s plan. Conduct trial runs regularly. Start slowly, increase gradually and look for defects. Adjust when needed to reach perfect quality.
When I first started with injection molding, it was like solving a really tricky puzzle. I learned at each step that adjusting speed and pressure was more than just changing numbers; it was about knowing each material’s special story. At first, I set everything cautiously, like carefully stepping into cold water. But I found out that being patient and shifting things just right gave me much better results. Very interesting results.
Every product acts differently, needing its own settings. Thin-walled items needed a faster pace to avoid cooling too soon. On the other hand, thick-walled items needed slower handling to avoid problems like flash or bubbles. Balancing these elements felt like small wins on my road to becoming skilled.
Let’s explore these methods further and find the details that might really improve your injection molding skills.
Higher injection speed always improves product quality.False
Excessive speed can cause defects like warping or incomplete filling.
Systematic testing is crucial for optimizing injection settings.True
Testing helps identify optimal parameters, reducing defects and waste.
What are the Key Considerations for Injection Speed Adjustment?
Have you ever faced a molding machine, hands a little sweaty from excitement, realizing that changing the injection speed could either succeed or ruin your product?
Changing how fast you inject materials into a mold needs good knowledge of material traits, product shape and how machines work. This choice makes sure of good mold filling and high product quality. Problems like extra material or lines in the product reduce. Understanding these elements changes your molding results.

Understanding Material Characteristics
Fiddling with injection speed is like meeting a new friend – you need to know their quirks. For example, materials like polypropylene (PP) are quite friendly and tolerate faster speeds. But if you hurry with polycarbonate (PC), you get a mess. Always check the recommended settings1 from your supplier; they are very helpful.
Product Design Specifics
Product design affects speed choices a lot. Thin-walled designs need higher speeds to stop them from cooling too soon, like cooking a soufflé that needs just the right heat. On the other hand, thick-walled items need slower speeds, like a stew that cooks slowly to avoid problems.
Product Type | Recommended Speed |
---|---|
Thin-Walled | Higher |
Thick-Walled | Lower |
Operation Specifications
Before changing anything, I take a moment to prepare everything properly. Knowing the machine panel is important – it’s your main control area. Everything should be in perfect shape, from mold setup to machine condition. Using protective gear is a must; safety glasses and gloves are always my armor.
Start with slow and steady adjustments. I begin at a lower speed and slowly increase it, testing along the way. If I see weld marks, I raise the speed slightly. But if I notice flash, I lower the speed again.
Keeping a record of these settings is crucial. Every change is a step towards perfection and it helps avoid common mistakes by following the injection speed guidelines2.
Monitoring Injection Speed Impact
While adjusting, I watch how the plastic melts and flows. A smooth flow means I’m doing it right. If there’s any jetting or uneven flow, more fine-tuning is needed. Using sensor technology3 can really help, offering immediate feedback.
Understanding these details really matters. It’s about improving quality and efficiency in molding operations – something I’ve learned to value through every project.
Polypropylene requires slower injection speeds than polycarbonate.False
Polypropylene can handle faster speeds due to its high fluidity.
Thick-walled designs benefit from lower injection speeds.True
Lower speeds reduce issues like flash and bubbles in thick-walled designs.
How Does Material Type Influence Injection Pressure Settings?
Do you ever think about how the correct pressure changes everything in injection molding?
The material in injection molding really affects pressure settings. This happens because of differences in how materials flow and their thickness. Thick materials need high pressure. Thin ones need less. Correct settings help avoid flaws like flashes and shrink marks. Flashes and shrink marks are preventable.
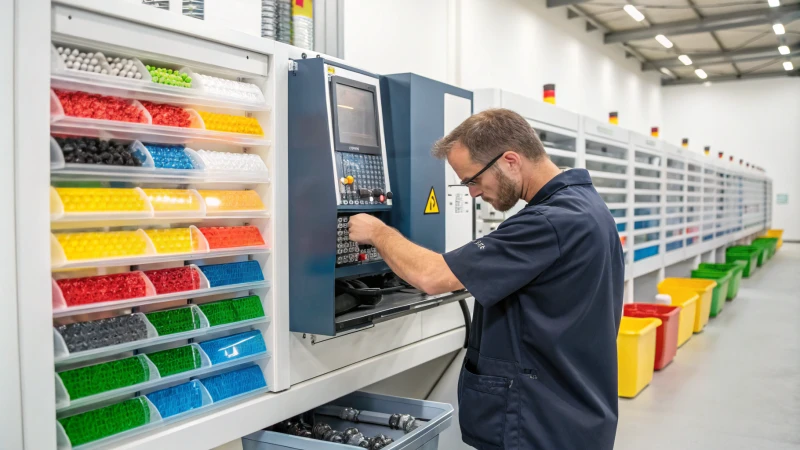
Understanding Material Characteristics
In the beginning, working with injection molding was hard because each material acts differently under pressure. Think about pushing honey and water through a small tube. Honey is thick, so it needs much force. The same happens with materials like glass-fiber reinforced plastics; they are thick and need high pressure. But materials like polypropylene (PP)4 flow easily and need less pressure.
Shrinkage was a problem, too. Some materials shrink a lot when they cool down. These need higher pressure to keep their shape. Grasping these details really improves product quality. Yes, really.
Material Type | Viscosity Level | Recommended Pressure |
---|---|---|
Glass-fiber Reinforced | High | Higher |
Polypropylene (PP) | Low | Lower |
Injection Pressure Adjustment
Over time, I realized adjusting injection pressure is like solving a mystery. You must study material traits and adapt them. Large or complex shapes need higher pressure to fill the mold right. Too much pressure causes defects like flash. Fixing flash is not fun.
Knowing the operation panel5 of the injection molding machine is important. It’s the place where everything happens. Adjustments are usually done through a control system that uses feedback from pressure sensors.
Practical Steps for Adjusting Injection Pressure
- Start Low: Begin with lower pressure. It’s safer and allows a gradual increase while checking how well the mold fills.
- Monitor Defects: Watch for flash or shrink marks. Adjust until you find the correct setting.
- Document Results: Write down what works and what doesn’t for future use.
Following these steps improves efficiency and product quality. Finding the right balance between material traits and injection pressure lessens defects and achieves success in the manufacturing process6. Maybe, just maybe, this is the way.
Glass-fiber reinforced plastics need higher injection pressures.True
Due to high viscosity, these materials require more pressure for proper flow.
Polypropylene requires higher pressure than glass-fiber plastics.False
Polypropylene has low viscosity, thus needing lower injection pressure.
Why is Systematic Testing Crucial in Injection Molding Optimization?
Have you ever questioned how organized testing changes the injection molding industry? I want to share my experience on why it truly matters.
Systematic testing in injection molding plays a key role in making production better. It keeps things consistent and identifies flaws quickly. Also, it adjusts settings such as injection speed and pressure to improve the quality and efficiency of products.
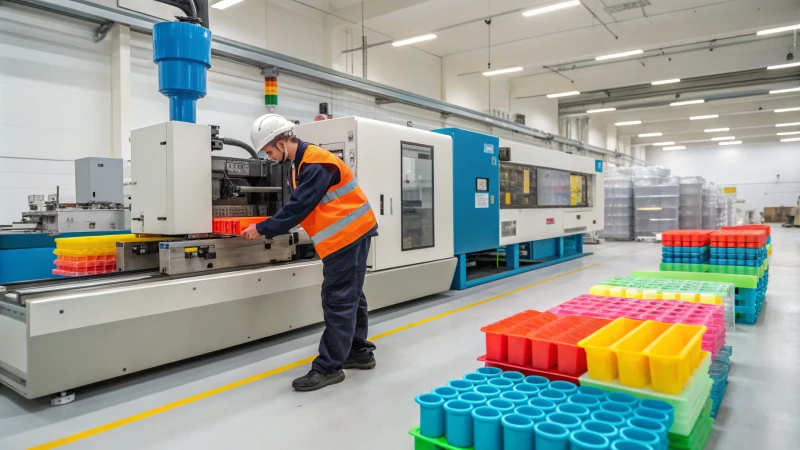
The Role of Systematic Testing
Systematic testing is like the heart of perfecting injection molding, ensuring consistent quality and efficiency in production. It isn’t just about producing items; it’s about crafting them properly, every single time. Testing helps identify variations in the molding process, allowing for adjustments that prevent defects such as flash or bubbles.
Key Testing Areas
-
Injection Speed: Adjusting speed was a real light bulb moment for me. Think about driving; you adjust your speed depending on the road. Similar in injection molding, starting slowly and speeding up gradually let me see how plastic flowed in the mold. Thin-walled items reminded me of fragile pastry layers – fast speed stopped them from cooling too quickly.
- Operators need to be familiar with the operation panel and wear personal protective equipment.
- Start at a lower speed and gradually increase it, observing the flow of plastic melt in the mold.
- Adjustments must consider the size and shape of the product, with thin-walled items needing higher speeds.
-
Injection Pressure: Setting pressure is like tuning a guitar. Too tight could snap a string – or make flash. I started low and increased slowly, finding a balance between the machine and material.
- Ensure key components like the hydraulic system are functioning correctly.
- Begin with lower pressure settings, increasing gradually while monitoring product quality.
Parameter | Thin-Walled Products | Thick-Walled Products |
---|---|---|
Speed | Higher | Lower |
Pressure | Moderate | Higher |
Benefits of Systematic Testing
Systematic testing became my reliable helper, truly improving our processes:
- Early Defect Identification: It’s like spotting a typo before printing a thousand pages. By continuously monitoring parameters, defects can be detected early, reducing waste and rework.
- Parameter Refinement: Like a chef perfects a dish, systematic testing helps refine parameters like injection speed adjustment7 and pressure settings, ensuring optimal performance.
- Safety Enhancements: Absolutely crucial. Systematic approaches ensure operations remain within safe limits, protecting both personnel and machinery.
Practical Examples
We once had to create a complex electronic casing. It reminded me of building LEGO structures with my kids – precision was very important. Systematic testing let us tweak speed to prevent early cooling and pressure was adjusted to form every detail correctly:
- Determine ideal injection speed to avoid cooling too quickly, preventing incomplete fills.
- Correct pressure settings would prevent flash while ensuring that intricate features are well-formed.
Adopting systematic testing allowed me to maintain high quality while saving resources and minimizing downtime—like leading an orchestra where each note must be just right.
In summary, while the optimization of injection molding8 benefits significantly from systematic testing, it requires skilled operators who understand the nuances of machinery and materials involved. Engaging with resources like injection pressure adjustment9 guides can further enhance outcomes in manufacturing settings.
Systematic testing reduces defects in injection molding.True
Testing identifies variations, allowing adjustments to prevent defects.
Higher injection speed is best for thick-walled products.False
Thick-walled products require lower speeds for proper filling.
How Can You Stay Safe While Tweaking Injection Molding Machines?
Do you ever get nervous while adjusting an injection molding machine? This experience taught me that safety is never something to ignore. Safety is crucial.
To stay safe during injection molding adjustments, understand the machine’s control panel. Wear gear like safety glasses and gloves. Adjust speeds and pressures slowly. Always watch the outcomes. Very important꞉ Always note any changes.
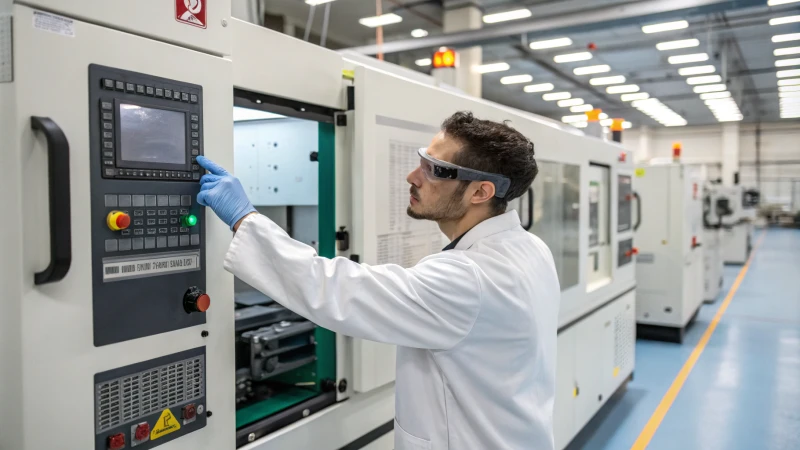
Understanding the Equipment and Preparing for Adjustments
Learn about your injection molding machine before changing settings. I spent many hours understanding the operation panel10 until I knew it very well. Knowing each part helps precision.
Personal Protective Equipment (PPE):
- Safety glasses
- Gloves
These protect me in the workshop from surprises.
Injection Speed Adjustment
Preparation:
- Check the machine conditions.
- Confirm the mold’s correct setup and testing.
- Understand your material – its flow and thickness.
Parameter Setting Principles:
Thin-walled items benefit from faster speeds to avoid cooling too soon. Mastering this was hard, but success felt great. Here’s a brief guide:
Product Type | Recommended Speed |
---|---|
Thin-walled | Higher |
Thick-walled | Lower |
Steps:
- Find speed settings on the panel.
- Start slow, then go faster.
- Watch mold filling to prevent flaws like flash or weld lines.
- Write down settings after changes.
Injection Pressure Adjustment
Preparation:
Inspect parts like the hydraulic system11. Also, check the mold’s cooling system as it affects pressure flow.
Parameter Setting Basis:
The pressure depends on size and shape – larger or complex designs might need more. I struggled at first, but notes helped me learn quickly.
Steps:
- Find pressure settings on the panel.
- Begin low, then raise pressure to fill easily.
- Adjust if flaws arise.
- Record changes to find best settings.
Monitoring and Documenting Adjustments
Detailed notes are important. Each change helps improve over time, keeping quality high and processes safe. Learn more12 about clear documentation in manufacturing.
\Following these rules not only keeps machinery safe but also really improves plastic product quality through injection molding. Trust me, success is gratifying.
PPE is optional during injection molding adjustments.False
PPE, like safety glasses and gloves, is essential for protection.
Higher speeds are needed for thin-walled products.True
Thin-walled products require higher speeds to prevent premature cooling.
Conclusion
Mastering injection speed and pressure is crucial for optimizing injection molding performance, ensuring quality products by understanding material characteristics, product design, and systematic testing.
-
Discover specific guidelines for various materials to optimize injection speed settings. ↩
-
Learn best practices and avoid common mistakes when setting injection speed. ↩
-
Explore how sensor technology aids in real-time monitoring and adjusting of parameters. ↩
-
Understanding viscosity differences aids in selecting the right injection pressure, enhancing product quality. ↩
-
Familiarizing with the operation panel features helps operators make precise adjustments for optimal molding. ↩
-
Learning about manufacturing efficiency improves production quality and operational cost-effectiveness. ↩
-
Explore guidelines for adjusting injection speed to optimize product quality. ↩
-
Learn how systematic testing enhances consistency and reduces defects in injection molding processes. ↩
-
Discover effective techniques for setting injection pressure in molding. ↩
-
This link will offer in-depth insights into using injection molding machine operation panels effectively, crucial for safety. ↩
-
Understanding the hydraulic system’s role ensures smooth operation and helps prevent accidents during adjustments. ↩
-
This link provides best practices for documenting manufacturing processes, enhancing quality and safety. ↩