Engineering plastics are revolutionizing the manufacturing landscape with their exceptional properties and adaptability. These high-performance thermoplastics1, such as polyamides (nylons) and polycarbonates, deliver superior strength, heat resistance, and durability, making them perfect for demanding applications. In this blog, we’ll dive into the world of engineering plastics and their critical role in injection molding2—a process that shapes these materials into precise, complex parts for industries like automotive, electronics, and medical devices.
Injection molding with engineering plastics3 produces high-performance components for automotive, electronics, and medical sectors, offering strength, precision, and cost-efficiency in large-scale production.
Understanding the characteristics of engineering plastics and the intricacies of the injection molding process is essential for manufacturers looking to optimize their production strategies. This guide will explore key concepts, practical applications, and technical insights to help you leverage this powerful combination effectively.
Engineering plastics are essential for high-performance applications.True
Their enhanced mechanical and thermal properties make them vital in industries where standard plastics fall short.
Injection molding is only suitable for basic plastic parts.False
Injection molding excels at creating intricate, high-tolerance parts, particularly with engineering plastics.
- 1. What Are Engineering Plastics?
- 2. How Are Engineering Plastics Used in Injection Molding?
- 3. What Is the Injection Molding Process for Engineering Plastics?
- 4. What Are the Design Considerations for Injection Molding with Engineering Plastics?
- 5. What Are the Related Technologies in Engineering Plastics and Injection Molding?
- 6. Conclusion
What Are Engineering Plastics?
Engineering plastics are a specialized group of thermoplastics renowned for their superior mechanical and thermal properties compared to commodity plastics like polyethylene and polypropylene. These materials are engineered for high-performance applications, often replacing metals in scenarios requiring strength, durability, and resistance to extreme conditions.
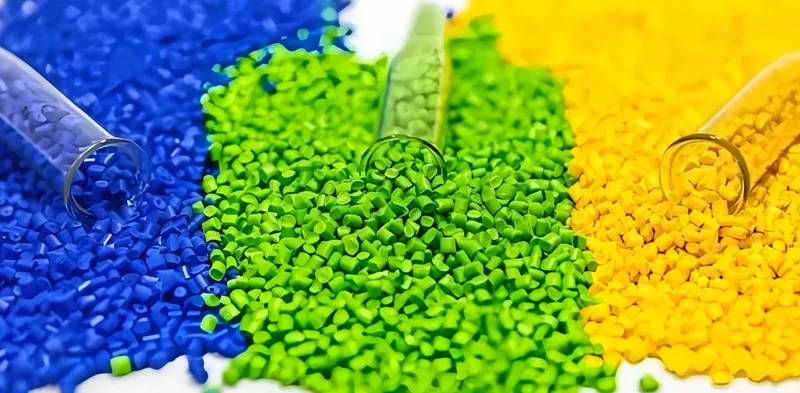
Definitions and Core Principles
-
Full Technical Names and Aliases: Key examples include polyamides (PA, commonly known as nylons), polycarbonates (PC), poly(methyl methacrylate) (PMMA, or acrylic glass), and acrylonitrile butadiene styrene (ABS).
-
Core Principles: These plastics boast high tensile strength, impact resistance, and thermal stability4, typically withstanding temperatures up to 150°C (300°F). They are prized for their versatility and ability to meet stringent technical demands.

Classification
-
By Material: Primarily thermoplastics, divided into semi-crystalline (e.g., nylon) and amorphous (e.g., polycarbonate) types.
-
By Process: Suitable for injection molding, extrusion, and blow molding, depending on their melt flow properties.
-
By Application: Widely used in automotive (e.g., engine components), electronics (e.g., connectors), and medical devices (e.g., housings).
Material | Key Properties | Common Applications |
---|---|---|
Polyamides (Nylon) | High strength, chemical resistance | Gears, automotive parts |
Polycarbonates (PC) | Transparency, impact resistance | Lenses, electronic enclosures |
PMMA (Acrylic) | Clarity, weatherability | Windows, medical devices |
ABS | Toughness, ease of processing | Consumer goods, dashboards |
Engineering plastics are only used in high-end industries.False
While prevalent in automotive and aerospace, they also appear in consumer goods and medical applications.
How Are Engineering Plastics Used in Injection Molding?
Injection molding is a manufacturing technique where molten plastic is injected into a mold, cooled, and ejected as a solid part. It’s ideal for producing complex, high-volume components with precision, making it a perfect match for engineering plastics.
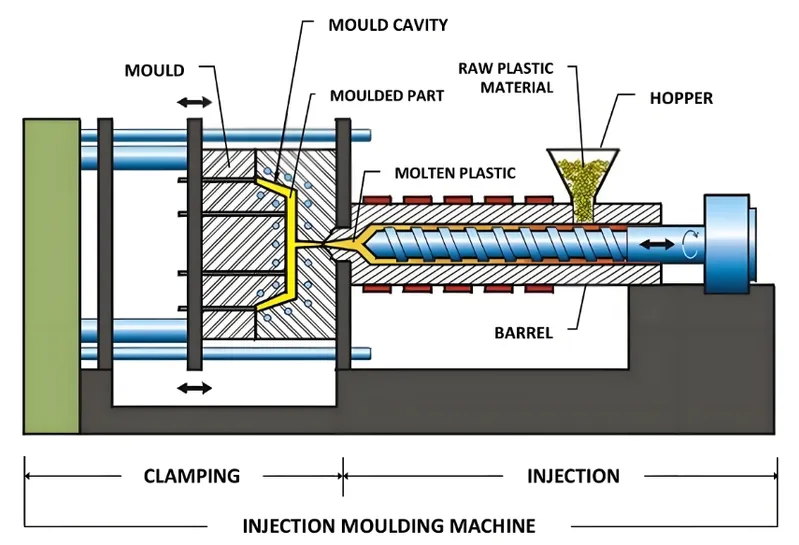
Typical Application Scenarios
-
Automotive: Engine covers, bumpers, and fuel tanks leverage polyamide’s strength and heat resistance.
-
Electronics: Connectors and enclosures use polycarbonate5 for its insulation and durability.
-
Medical Devices: Housings and precision parts benefit from ABS’s impact resistance and PMMA’s transparency.
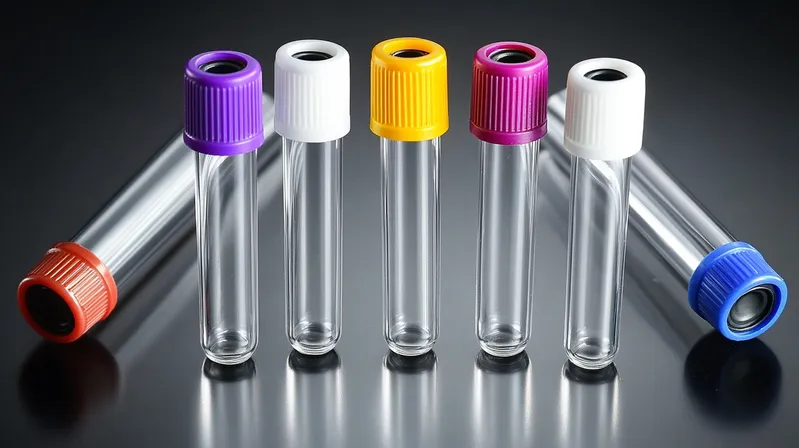
Pros and Cons Comparison
When compared to alternatives like 3D printing or CNC machining, injection molding with engineering plastics offers:
-
Pros: High-volume production, low per-unit costs, design flexibility, and extensive material options.
-
Cons: High initial mold costs, longer lead times, and limited suitability for prototyping.
Injection molding with engineering plastics is the best choice for all manufacturing needs.False
It excels in high-volume production but may not suit small runs or rapid prototyping.
What Is the Injection Molding Process for Engineering Plastics?
The injection molding process is a multi-step operation requiring precise control to ensure quality outcomes with engineering plastics.
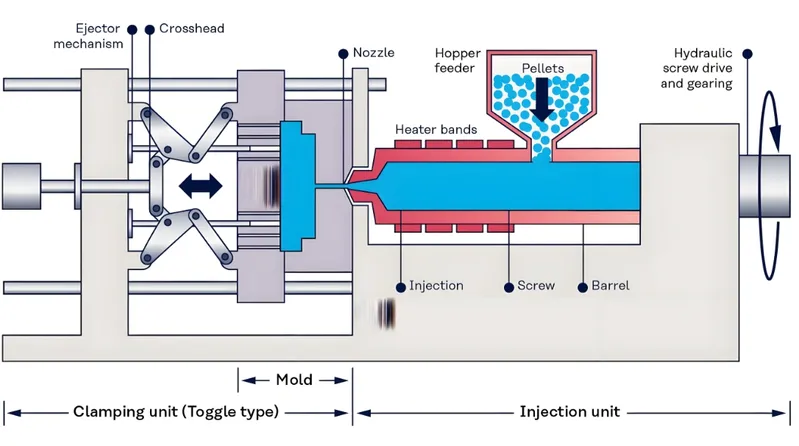
Process Workflow Breakdown
-
Tooling Fabrication: Design and machine a mold, typically from steel or aluminum.
-
Material Preparation: Feed engineering plastic pellets into the injection molding machine.
-
Melting: Heat the pellets to a molten state, with temperatures ranging from 300-800°F (149-426°C) based on the material.
-
Injection: Inject the molten plastic into the mold under high pressure.
-
Cooling: Allow the plastic to solidify within the mold.
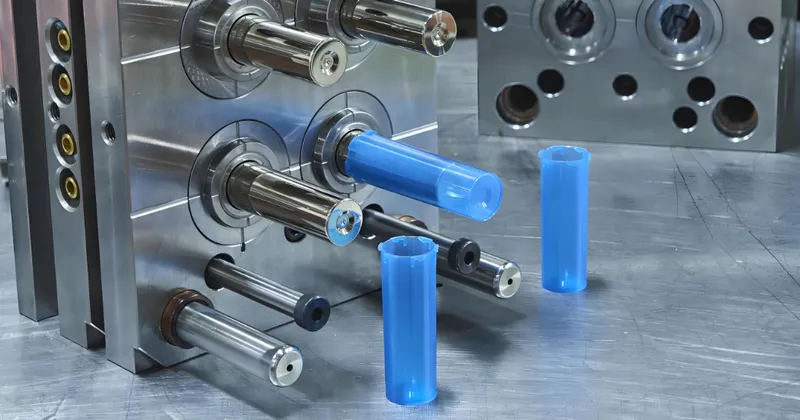
- Ejection: Open the mold and remove the finished part.
Key Parameters
-
Melt Temperature: Varies by plastic (e.g., higher for nylon, lower for ABS).
-
Mold Temperature: Influences shrinkage and crystallinity.
-
Injection Pressure: Ensures complete mold filling, critical for viscous materials like polycarbonate.
-
Cooling Time: Balances cycle time and prevents defects like warping.
Material Compatibility
Each engineering plastic affects the process differently:

-
Nylon (PA): Susceptible to shrinkage; requires precise cooling.
-
Polycarbonate (PC): High viscosity demands careful temperature management.
-
ABS: Easier to process, with good flow and toughness.
-
PMMA (Acrylic): Brittle; needs gentle handling to avoid cracking.
Material selection significantly impacts the injection molding process.True
The unique properties of each plastic influence flow, shrinkage, and final part quality.
What Are the Design Considerations for Injection Molding with Engineering Plastics?
Effective design for injection molding with engineering plastics hinges on understanding process limitations and material-specific guidelines.
Design Checklist
Category | Details |
---|---|
Wall Thickness6 | Varies by material (e.g., ABS: 0.045-0.140 in., Nylon: 0.030-0.115 in.) |
Draft Angles7 | 0.5° to 2° for vertical faces; higher for textured surfaces |
Undercuts | Limited by mold design; may require side cores |
Radii | Add radii to corners to reduce stress concentrations |
Process Selection Decision-Making
Use this simple decision tree:
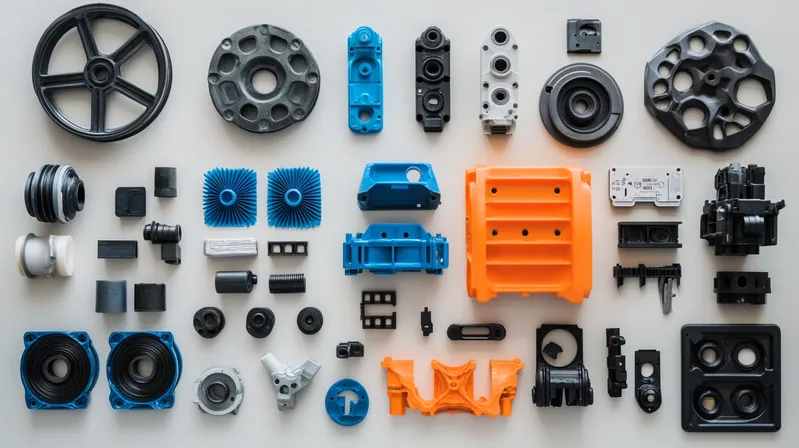
-
Production Volume: Over 1,000 units? Injection molding is a strong candidate.
-
Part Complexity: Need intricate geometries? Injection molding excels.
-
Material Needs: Require high strength or heat resistance? Engineering plastics fit.
-
Cost Feasibility: Can you justify the mold cost? If yes, proceed.
Injection molding is always the most cost-effective manufacturing method.False
For low-volume runs, alternatives like 3D printing may be more economical.
The ecosystem surrounding engineering plastics and injection molding includes upstream and downstream processes that enhance its capabilities.
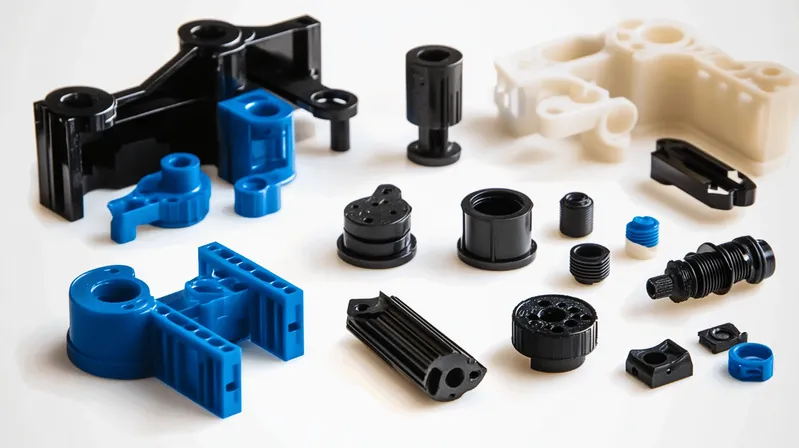
Upstream Technologies
-
Polymer Synthesis: Producing base polymers via petrochemical processes.
-
Material Compounding: Adding fillers or additives to tailor properties.
Downstream Technologies
- Assembly: Integrating molded parts using robotics or manual methods.
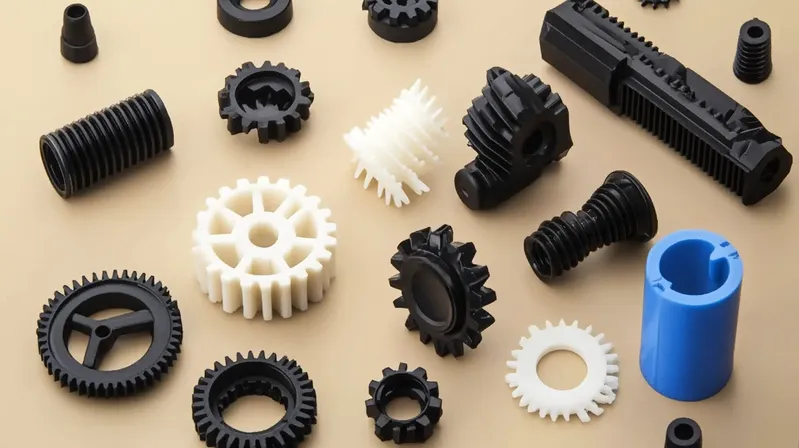
-
Finishing Operations: Applying coatings, painting, or plating.
-
Recycling: Reprocessing engineering plastics for sustainability.
Emerging trends include bio-based engineering plastics8 and Industry 4.0 innovations like IoT and AI, which optimize production efficiency.
Recycling engineering plastics is a growing trend in the industry.True
Sustainability initiatives are advancing recycling techniques for these materials.
Conclusion
Engineering plastics paired with injection molding offer a robust solution for crafting high-performance parts across diverse industries. By grasping the properties of these materials, mastering the molding process, and exploring the broader technological landscape, manufacturers can unlock significant advantages. Whether you’re producing automotive components, electronic housings, or medical devices, this combination can elevate your products to new levels of quality and efficiency.
-
Discover the applications of high-performance thermoplastics to see their role in various industries and innovations. ↩
-
Learn about the injection molding process to see how it shapes engineering plastics into high-performance components. ↩
-
Explore the advantages of engineering plastics to understand their impact on modern manufacturing processes. ↩
-
Discover the importance of thermal stability in engineering plastics and its impact on performance in extreme conditions. ↩
-
Discover the unique properties of polycarbonate and its applications in electronics and medical devices. ↩
-
Learn about the critical role of wall thickness in injection molding to optimize your designs and material usage. ↩
-
Discover the importance of draft angles in injection molding to ensure easy part removal and improve production efficiency. ↩
-
Discover the benefits of bio-based engineering plastics for sustainable manufacturing and their impact on the environment. ↩