Ever wondered how flame-retardant materials keep our gadgets safe? As a designer, it’s my job to dig deep into this.
Flame-retardant materials in injection molding effectively slow ignition and minimize flame spread, essential for consumer electronics safety. Their success hinges on the retardant type and application needs, ensuring fire safety compliance.
Navigating the world of flame-retardant materials can feel like choosing the perfect spice for a dish. You want just the right one to enhance the recipe without overpowering it. I remember the first time I had to select a flame-retardant for a new product line—it was both exciting and daunting. I had to consider not just safety and performance but also how it would impact the design process. Let’s explore these materials’ benefits, the hurdles they present, and what the future might hold for them in our designs.
Flame-retardant materials in injection molding always prevent fires.False
They reduce risk but do not completely prevent fires.
Flame-retardants are crucial for electronic component safety.True
They meet stringent fire safety standards, ensuring safety.
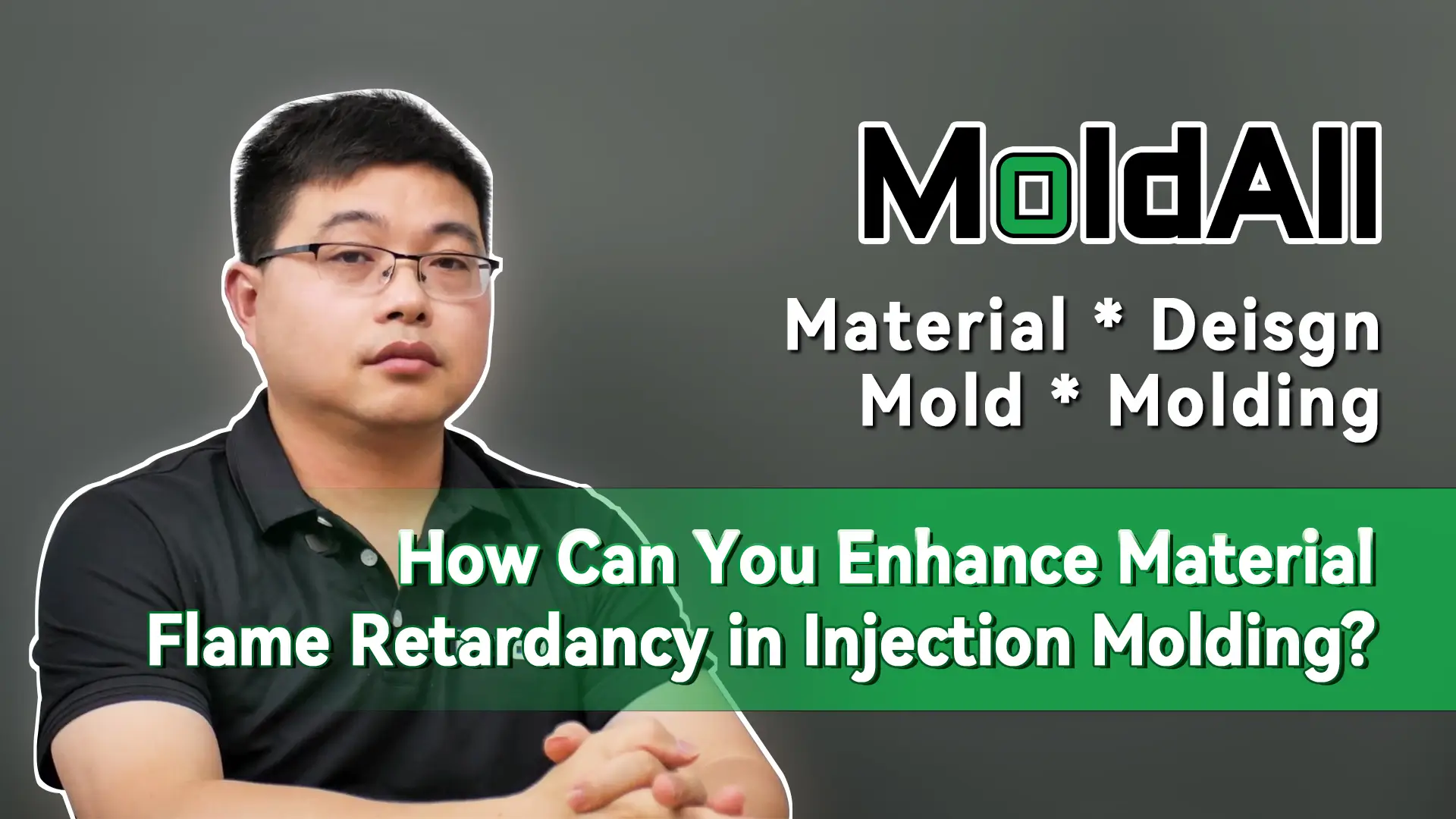
- 1. What Are the Common Types of Flame-Retardant Materials Used in Injection Molding?
- 2. How do flame-retardant additives affect the mechanical properties of molded parts?
- 3. What are the key considerations when selecting flame-retardant materials for electronics?
- 4. How Do Flame-Retardants Impact the Environmental and Health Aspects of Manufacturing?
- 5. What Are the Challenges in Processing Flame-Retardant Materials in Injection Molding?
- 6. What Are the Future Trends in Flame-Retardant Technologies for Injection Molding?
- 7. Conclusion
What Are the Common Types of Flame-Retardant Materials Used in Injection Molding?
Flame-retardant materials have always been a mystery to me, especially in the fast-paced world of injection molding. Unraveling their secrets not only enhances safety but also ensures compliance with strict standards.
Common flame-retardant materials in injection molding include halogenated compounds, phosphorous-based additives, and nitrogen-based synergists, each offering unique benefits for various applications.
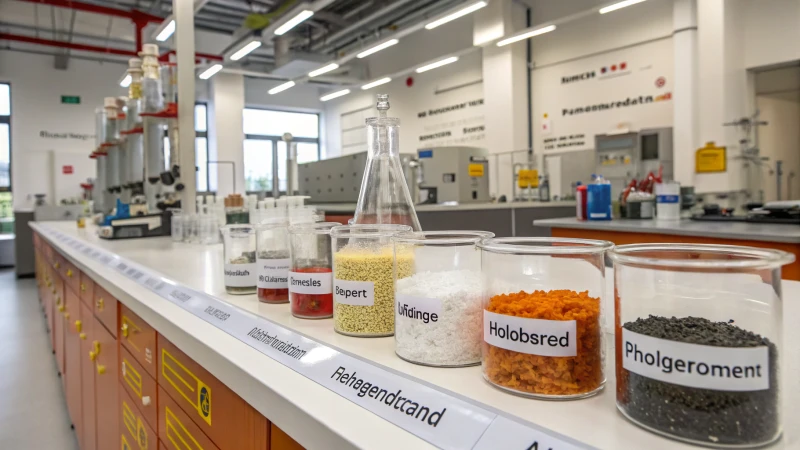
I remember the first time I encountered flame-retardant materials in my design work. It was a project that needed to meet both aesthetic and fire safety standards, and I was a bit overwhelmed by the options. But diving into the details of each type really opened my eyes to their distinct advantages and challenges.
Halogenated Compounds
Halogenated compounds were like my reliable old toolkit back then—trustworthy and effective. These compounds, including brominated or chlorinated flame retardants, are widely used due to their cost-effectiveness1 and efficiency. They work by releasing halogen radicals that interrupt combustion processes.
Advantages | Disadvantages |
---|---|
High efficiency | Environmental concerns |
Cost-effective | Health risks |
I often chose these for electronic housings, though environmental concerns have led me to rethink their usage in recent years.
Phosphorous-Based Additives
When I first learned about phosphorous-based additives, they seemed like the new kid on the block—exciting and promising a more eco-friendly2 alternative to halogens. These additives form a protective char layer on the material surface, acting as a barrier to flames.
Advantages | Disadvantages |
---|---|
Environmentally friendly | Higher cost |
Good thermal stability | Limited availability |
I found them particularly useful in automotive parts and electrical enclosures, where flame resistance is crucial without compromising structural integrity.
Nitrogen-Based Synergists
Nitrogen-based flame retardants were like the secret weapon in my arsenal. They often work in synergy with other compounds, reducing smoke production and enhancing the effectiveness of other retardants.
- Applications: I’ve used them in textiles and automotive interiors because of their ability to reduce smoke and toxicity levels.
- Challenges: They sometimes require combination with other additives to achieve optimal results.
Choosing the right flame-retardant material often felt like piecing together a complex puzzle. It depended largely on application requirements, regulatory standards, and environmental considerations. For more insights on specific materials, you can check out this detailed guide3.
Halogenated compounds are eco-friendly.False
Halogenated compounds pose environmental concerns due to toxic emissions.
Phosphorous additives form a char layer.True
Phosphorous additives create a protective char layer, enhancing flame resistance.
How do flame-retardant additives affect the mechanical properties of molded parts?
Balancing fire safety with material performance is a challenge I face daily as a product designer.
Flame-retardant additives improve fire safety in molded parts but may reduce their strength and durability, necessitating careful evaluation to balance safety and performance in design.
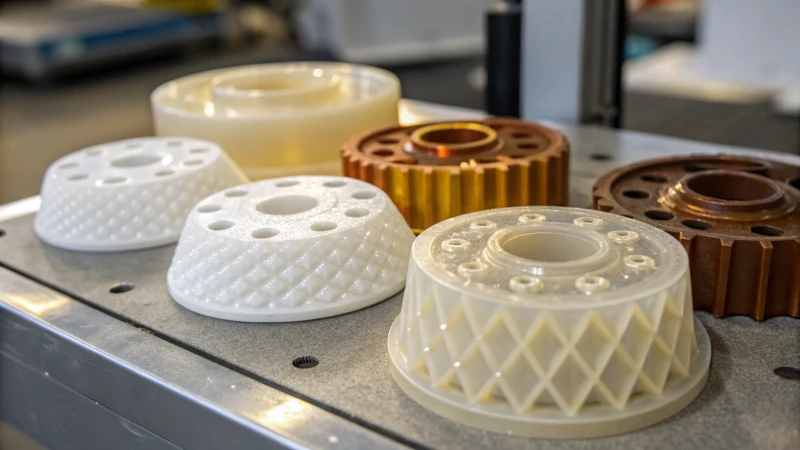
Impact on Mechanical Properties
Let me take you back to the day I realized the delicate dance between fire safety and mechanical integrity. We had a major project for a new consumer electronics component that demanded impeccable fire resistance without sacrificing its robustness. Here’s what I learned: flame-retardant additives, our go-to solution for fire safety, often tweak the material’s very essence. They can shave off some tensile strength and elasticity, leaving us with parts that might not hold up under stress as we’d like.
Property | Effect of Flame-Retardants |
---|---|
Tensile Strength | Often reduced |
Elastic Modulus | May decrease |
Impact Resistance | Can be compromised |
Understanding these shifts in material behavior is like piecing together a complex puzzle, but it’s crucial for making smart choices about what materials to use.
Types of Flame-Retardant Additives
Now, let’s talk additives. There’s quite a range to choose from, each with its quirks. Halogenated compounds4 are pretty effective but come with their own baggage—environmental concerns that can’t be ignored. On the flip side, non-halogenated alternatives present a greener option, albeit with varying levels of effectiveness.
Additive Type | Characteristics |
---|---|
Halogenated | High effectiveness, environmental issues |
Non-Halogenated | Safer profile, variable effectiveness |
Balancing Safety and Performance
For designers like me, it’s a constant juggle. Do we lean more towards safety and risk some performance, or vice versa? It’s never an easy call. I remember spending countless hours over coffee and CAD models, exploring every possible scenario with advanced modeling techniques like finite element analysis to predict how these additives would affect our designs under real-world conditions.
Case Studies and Examples
I’ve been inspired by studies showing that blending different flame-retardants can actually ease some of the mechanical trade-offs. One case that comes to mind involved intumescent additives combined with mineral fillers—a combo that preserved structural integrity while boosting fire retardance. That’s the kind of breakthrough that makes all the trial and error worthwhile.
Incorporating these lessons into our design practice is a blend of art and science, requiring us to understand both chemical interactions and physical realities. By staying on top of research and developments in the field, we can ensure our molded parts meet both safety and performance benchmarks effectively.
For more insights, I often dive into studies on blended additive impacts5 and explore advanced modeling techniques for flame-retardant materials. Each new piece of knowledge helps me craft better solutions in this ever-evolving landscape.
Flame-retardants reduce tensile strength in molded parts.True
Flame-retardant additives often decrease the tensile strength of materials.
Non-halogenated additives are environmentally harmful.False
Non-halogenated additives are considered safer for the environment.
What are the key considerations when selecting flame-retardant materials for electronics?
Choosing the right flame-retardant materials for electronics isn’t just a technical decision—it’s a personal commitment to safety and innovation.
When selecting flame-retardant materials for electronics, prioritize compliance with safety standards, assess thermal stability and electrical properties, consider environmental impact, and ensure cost-effectiveness to balance safety and performance.
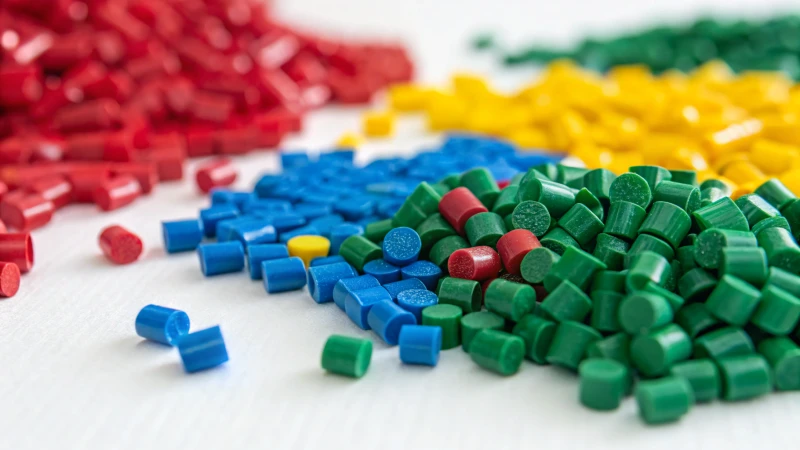
Understanding Regulatory Compliance
I remember the first time I had to navigate the maze of industry safety standards6 like UL 94. It felt like learning a new language! But mastering these standards is crucial. They ensure that our designs not only get the green light for market entry but also keep users safe.
Evaluating Thermal Stability
Back in my early days, I designed a component that failed under heat stress. It was a hard lesson in understanding thermal stability. Now, I make sure every material can withstand high temperatures, ensuring durability and reliability even in warm environments.
Balancing Electrical Properties
One time, a colleague’s project encountered unexpected electrical failures. That experience taught me the importance of balancing electrical properties with fire safety. I now look for materials with excellent dielectric strength and low conductivity to prevent such mishaps.
Considering Environmental Impact
With growing awareness about sustainability, choosing eco-friendly flame retardants7 is more important than ever. I strive to select materials that minimize harmful emissions and align with sustainable practices, ensuring my designs leave a smaller ecological footprint.
Factor | Importance |
---|---|
Compliance | Ensures safety and adherence to legal requirements. |
Thermal Stability | Maintains performance under high temperatures. |
Electrical Properties | Prevents electrical malfunctions or hazards. |
Environmental Impact | Supports sustainability and reduces ecological footprint. |
Cost-Effectiveness | Balances budget constraints with quality and performance needs. |
Analyzing Cost-Effectiveness
Balancing quality with budget constraints is always tricky. I’ve learned that sometimes, investing in higher-quality materials upfront can save costs in the long run by reducing failures and increasing product longevity. It’s about weighing immediate expenses against long-term benefits.
Choosing the right material is a delicate dance between safety, performance, and environmental responsibility, ensuring that the final product meets both regulatory demands and consumer expectations.
UL 94 classifies the flammability of plastic materials.True
UL 94 is a standard for safety testing of plastic materials' flammability.
Eco-friendly flame retardants increase harmful emissions.False
Eco-friendly flame retardants are designed to reduce harmful emissions.
How Do Flame-Retardants Impact the Environmental and Health Aspects of Manufacturing?
I remember the first time I learned about flame-retardants in manufacturing. It felt like unlocking a new level of responsibility—not just for safety, but for our environment and health.
Flame-retardants pose environmental and health risks by accumulating in ecosystems and affecting humans via inhalation and skin contact, necessitating regulatory measures to mitigate these impacts.
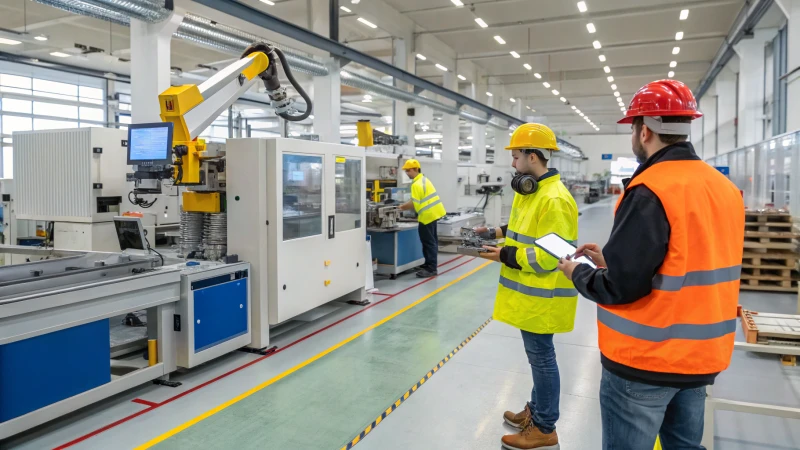
Understanding Flame-Retardants
When I first got into product design, the role of flame-retardants in ensuring safety fascinated me. They’re these unsung heroes used to prevent or slow the spread of fire in everyday products—from the plastics in our gadgets to the textiles in our homes. Their importance can’t be overstated, but neither can their risks.
Type | Common Use | Chemical Components |
---|---|---|
Brominated | Electronics | Bromine-based compounds |
Phosphorous | Textiles | Phosphate esters |
Chlorinated | Plastics | Chlorine-based agents |
The tricky part is that these chemicals can leach into our environment, contaminating soil and water. I remember hearing about how flame-retardants could travel through air and water, making them more widespread than I initially thought.
Environmental Impact
I once visited a manufacturing plant and saw firsthand how industrial waste could affect nearby rivers. It’s alarming to think that flame-retardants could accumulate in such environments, posing significant threats to wildlife. Imagine the impact on fish, where bioaccumulation8 disrupts reproductive systems—a stark reminder that our actions have ripple effects.
- Water Pollution: These chemicals can enter water systems through industrial discharge or improper disposal.
- Soil Contamination: Flame-retardants can bind to soil particles, leading to long-term land pollution.
Health Concerns
At a recent industry conference, I heard stories about workers developing respiratory issues from inhaling flame-retardant dust. It’s not just about those in the plants—these substances can linger in homes and offices too. They’ve been linked to endocrine disruption, mimicking natural hormones and potentially causing imbalances.
- Respiratory Issues: A real concern for workers and nearby communities.
- Endocrine Disruption: Some flame-retardants mimic natural hormones, leading to potential imbalances.
Mitigating the Impact
During my time in product design, I’ve seen how crucial it is for regulatory agencies to step up. Many are now pushing for safer alternatives and stricter guidelines. It’s about finding that balance between safety and sustainability—like using green chemistry9 to create flame-resistant materials without the toxic fallout.
Regulatory Frameworks
Navigating regulations is part of my job. I’ve seen how the EU’s REACH regulations demand transparency about chemical usage, while the US EPA promotes safer alternatives. Staying informed about these frameworks is essential for compliance and reducing negative impacts.
- EU REACH Regulations: Focus on registration and restriction of harmful chemicals.
- US EPA Initiatives: Encourage safer alternatives and strict monitoring.
These insights remind me of the ongoing challenges we face with flame-retardants. It’s a call to action for us in the industry to innovate responsibly. By embracing eco-friendly practices, we can protect both human health and our planet without sacrificing safety standards.
Flame-retardants can disrupt fish reproductive systems.True
Flame-retardants bioaccumulate in fish, affecting reproduction.
All flame-retardants are biodegradable and eco-friendly.False
Many flame-retardants are persistent, not biodegradable.
What Are the Challenges in Processing Flame-Retardant Materials in Injection Molding?
Ever wonder what makes flame-retardant materials a tough nut to crack in injection molding? Trust me, it’s a fascinating challenge!
Processing flame-retardant materials in injection molding involves challenges like moisture sensitivity, thermal degradation, and polymer compatibility, requiring careful material selection and process optimization.
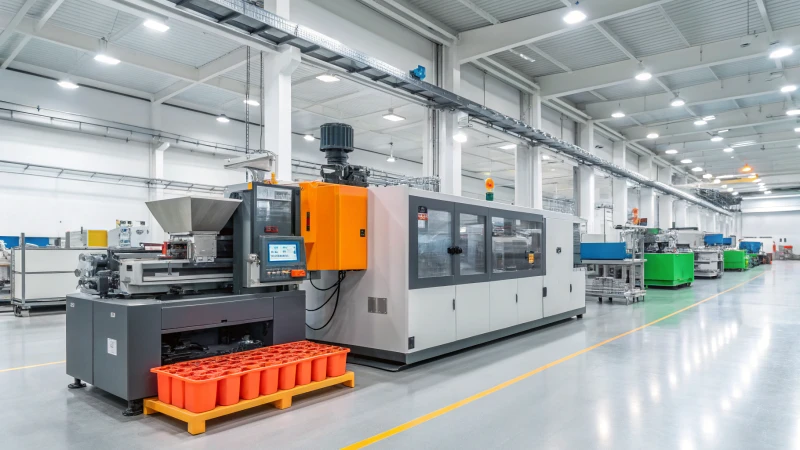
Moisture Sensitivity
I remember the first time I encountered moisture issues in flame-retardant plastics. It was a real eye-opener! These additives are like sponges, soaking up moisture and causing all sorts of havoc, from hydrolysis to weakened mechanical properties. That’s why pre-drying materials and keeping a tight lid on the molding environment is crucial. It’s like prepping for a big cooking show—everything needs to be just right.
Problem | Solution |
---|---|
Hydrolysis | Pre-dry materials |
Reduced properties | Optimize processing temps |
Thermal Stability
The thrill of maintaining thermal stability is akin to a high-wire act. Flame-retardants can throw the thermal balance off, shrinking the processing window. I’ve learned that precise control over temperature profiles10 is not just a recommendation—it’s essential to prevent degradation. Imagine trying to bake a soufflé without a timer; precision matters!
Compatibility with Polymers
Compatibility testing reminds me of matchmaking, finding the perfect partner between flame-retardants and base polymers. Get it wrong, and you end up with compromised performance characteristics. But nail it, and you’ve got a match made in manufacturing heaven. Testing for compatibility11 is like my ritual—never skipped.
Dispersion Issues
Ever tried mixing oil with water? That’s what inadequate dispersion feels like when flame-retardants don’t spread uniformly within the polymer matrix. Weak spots emerge, much like a poorly mixed cake batter. Techniques like twin-screw extrusion come to the rescue here, ensuring that every piece of the puzzle fits perfectly for uniform dispersion12.
Mechanical Property Alteration
Balancing flame retardancy with mechanical performance feels like walking a tightrope. Adding flame-retardants can weaken aspects like tensile strength and impact resistance. It’s a puzzle that requires constant tinkering, testing, and tweaking. The iterative testing and material adjustments13 involved remind me of adjusting a recipe until it’s just right.
Understanding these challenges and adopting strategies to counteract them can lead to successful processing of flame-retardant materials in injection molding. By employing best practices, manufacturers not only enhance product quality but also ensure they meet those ever-important safety standards.
Flame-retardants increase moisture sensitivity in plastics.True
Flame-retardants often lead to hydrolysis and reduced mechanical properties.
Uniform dispersion of flame-retardants is not crucial.False
Inadequate dispersion leads to weak spots and inconsistent properties.
What Are the Future Trends in Flame-Retardant Technologies for Injection Molding?
The world of injection molding is always evolving, and as a designer, keeping up with flame-retardant technology trends is crucial for both safety and innovation.
Future flame-retardant trends in injection molding focus on non-halogenated materials, nano-additives, and sustainable solutions, enhancing safety, regulatory compliance, and environmental impact reduction.

Non-Halogenated Materials
When I first heard about the shift to non-halogenated flame retardants, I was intrigued. The push away from halogenated compounds isn’t just about compliance; it’s about creating a safer, greener future. One of my colleagues, who’s as passionate about eco-friendly solutions as I am, swears by phosphorus-based materials. They offer an impressive balance of reduced environmental impact14 and excellent flame-retardant qualities. It’s exciting to see how these innovations are redefining our approach to safety in design.
Nano-Based Additives
Nanotechnology has always felt like science fiction to me, but it’s becoming a reality in our field. The idea that nano-sized particles like clay or graphene could significantly enhance fire resistance while preserving mechanical properties is nothing short of revolutionary. I remember a project where we experimented with these additives. Watching them form a protective char layer that insulated the material was like seeing magic in action. For more on this, explore how nanotechnology is revolutionizing15 the field.
Sustainability and Recyclability
Sustainability is a buzzword that’s become central to our design discussions. I recall when we first started exploring bio-based materials; it was a challenge but also deeply rewarding. Polylactic acid (PLA) composites, for example, have shown potential as effective and biodegradable flame-retardants. It’s heartening to think that our work could align with global eco-friendly initiatives and promote recycling in manufacturing processes.
Trend | Key Feature | Benefit |
---|---|---|
Non-Halogenated Materials | Phosphorus-based, reduced toxicity | Environmental safety |
Nano-Based Additives | Clay/graphene particles, enhanced fire resistance | Improved material properties |
Sustainability | Bio-based, biodegradable options | Aligns with eco-friendly initiatives |
Regulatory and Market Influences
Navigating regulations has always felt like threading a needle. Standards like UL 94 and RoHS are the benchmarks we aim to meet. Staying updated on regulatory changes16 is not just about compliance; it’s about gaining a competitive edge. It’s essential for us to ensure that our products aren’t just meeting current standards but are also ready for what’s coming next.
Conclusion
This journey through flame-retardant technologies is ongoing and exhilarating. As we balance performance with safety and environmental responsibility, it’s clear that staying ahead of these trends is key for designers like myself. It’s not just about keeping up; it’s about leading the way in innovation.
Phosphorus-based materials are non-halogenated.True
Phosphorus-based flame retardants are non-halogenated, reducing toxicity.
Nanotechnology reduces mechanical properties in flame retardants.False
Nano-based additives maintain mechanical properties while enhancing fire resistance.
Conclusion
Flame-retardant materials in injection molding enhance safety but pose challenges like moisture sensitivity and mechanical property alterations. Innovations focus on non-halogenated, nano-based, and sustainable options for improved performance.
-
Understand why halogenated compounds remain popular despite environmental concerns. ↩
-
Explore how these additives provide environmental benefits over traditional options. ↩
-
Gain comprehensive knowledge on selecting the right material for your needs. ↩
-
Explore the environmental impact and effectiveness of halogenated flame retardants compared to other types. ↩
-
Read studies on how blended additives can balance mechanical integrity with enhanced fire resistance. ↩
-
Understanding UL 94 standards helps ensure material compliance with fire safety regulations. ↩
-
Exploring eco-friendly options helps you align material choices with sustainability goals. ↩
-
Exploring this link provides insight into how flame-retardants accumulate in marine life, affecting their reproductive systems. ↩
-
Discovering green chemistry solutions offers promising alternatives to toxic flame-retardants, advancing safer manufacturing practices. ↩
-
Explore techniques for maintaining optimal temperature profiles to avoid thermal degradation. ↩
-
Learn how to test and ensure compatibility between flame-retardant additives and base polymers. ↩
-
Find out how to achieve better dispersion of additives within polymer matrices. ↩
-
Understand how to balance flame retardancy with mechanical performance through material adjustments. ↩
-
Discover why phosphorus-based materials are gaining popularity as environmentally friendly flame retardants. ↩
-
Learn how nanotechnology enhances fire resistance in materials without compromising their mechanical properties. ↩
-
Stay updated with regulatory shifts that influence flame retardant technologies and ensure compliance. ↩