All Posts
blog & article
read our latest newsletter
Whether you’re curious about material selection, product design, mold design, mold making and injection molding, feel free to ask us anything. Our team is ready to provide the guidance and insights you need.
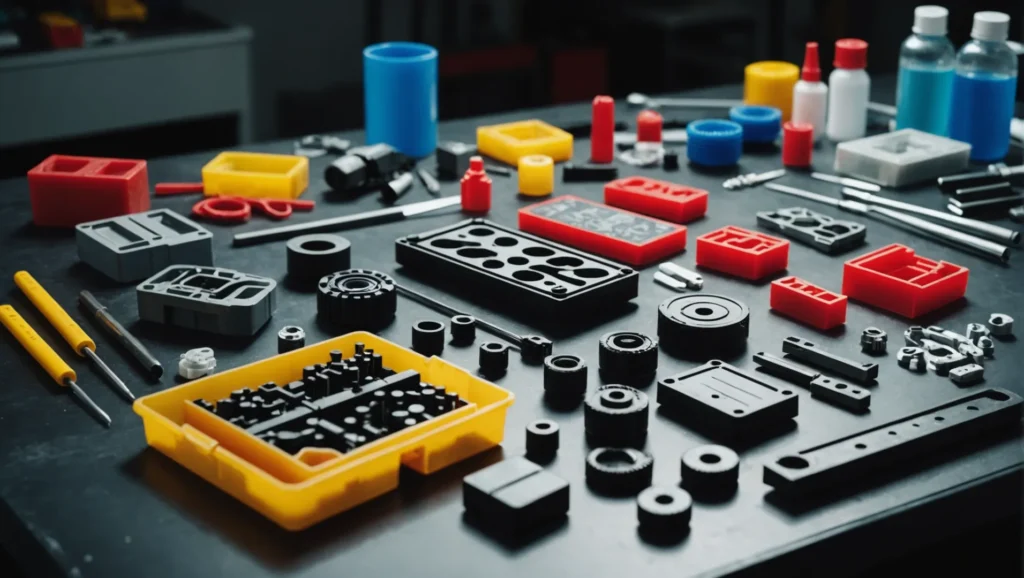
How Can You Enhance the Mechanical Properties of Injection Molded Parts?
In the world of manufacturing, the quality of injection molded parts can make or break a product's success. By focusing on raw material selection, process optimization, mold design, and post-processing techniques, manufacturers can significantly enhance the mechanical properties of their ...
OPTIMIZATION
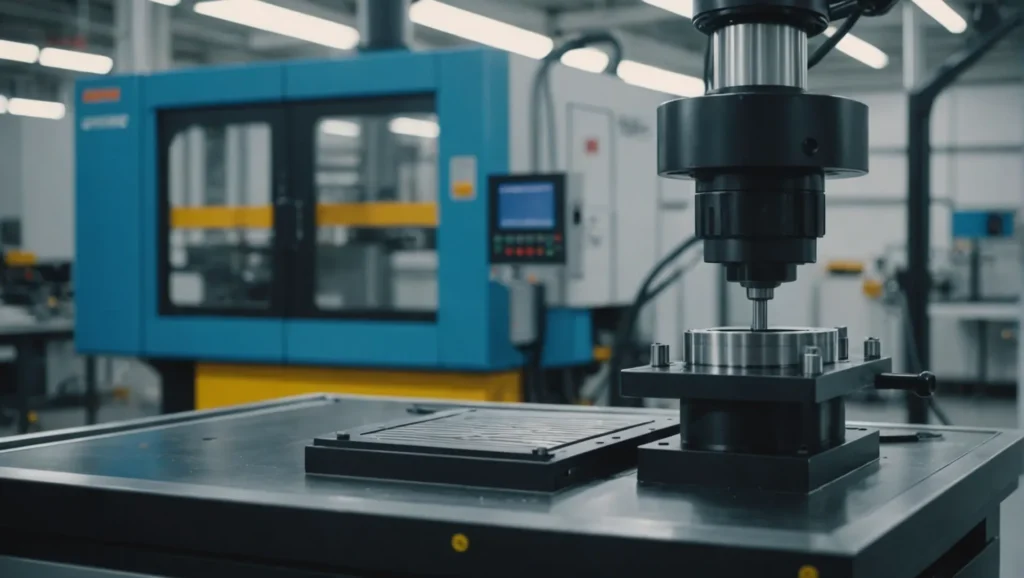
How Can You Effectively Reduce Warping in Injection Molding?
Warping is a common challenge in injection molding that can compromise the integrity of manufactured parts. Understanding how to reduce it is essential for maintaining quality standards. In this article, I share my insights on optimizing mold design, selecting the ...
OPTIMIZATION
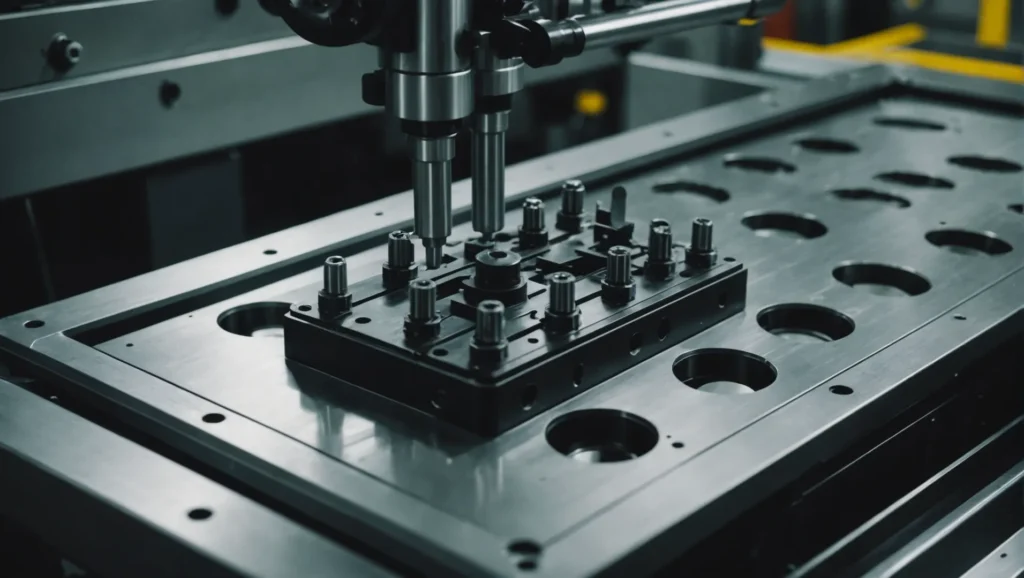
How Can You Prevent Overheating in the Gate Area of Injection Molding?
Overheating in the gate area of injection molding is a common challenge that can lead to quality issues and inefficiencies in production. To combat this, understanding the intricacies of mold design, process parameters, material selection, and maintenance practices is essential. ...
OPTIMIZATION
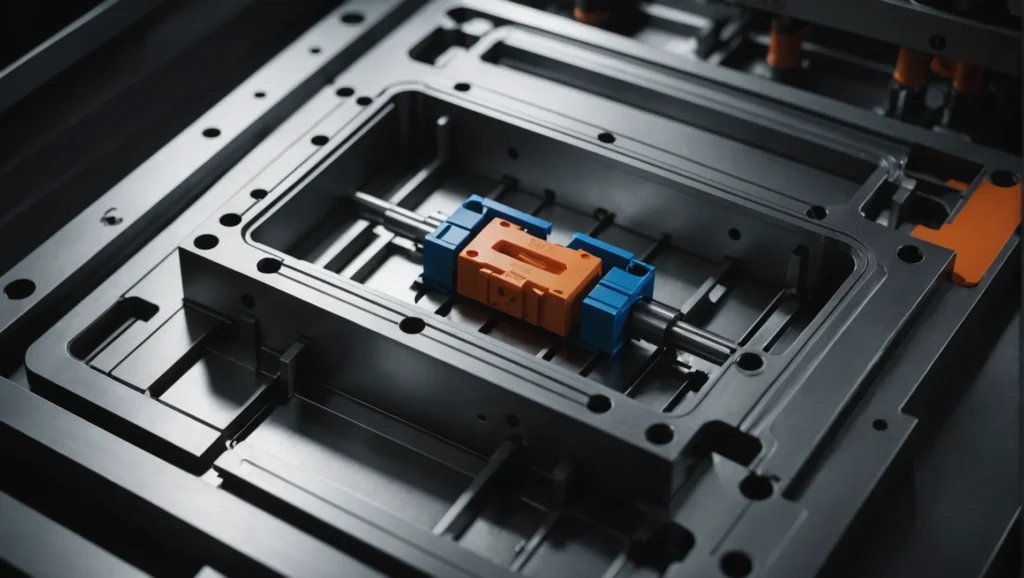
What Are the Best Optimization Techniques for Runner Layout in Injection Molds?
If you're grappling with defects in your injection molded parts, optimizing your runner layout might just be the game changer you need. Discover expert techniques for enhancing product quality and production efficiency, ensuring your molds operate at their best. Let's ...
DEVELOPMENT
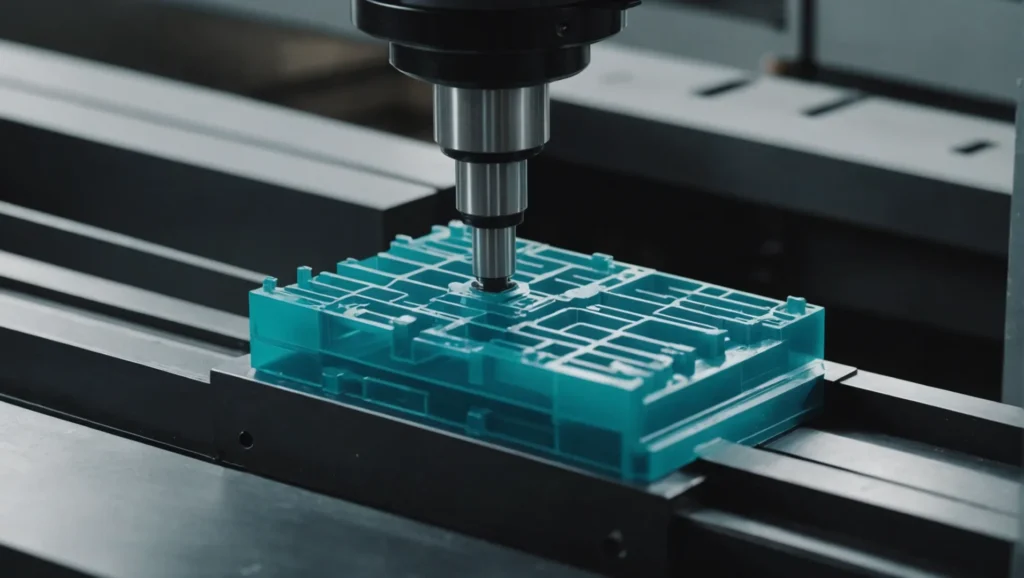
What Are the Best Strategies to Optimize Wall Thickness Distribution in Injection Molded Products?
In the intricate world of injection molding, achieving the perfect wall thickness distribution is crucial for both product quality and efficiency. This article explores essential strategies, from product design to material selection, that can significantly enhance your results. Discover how ...
DEVELOPMENT
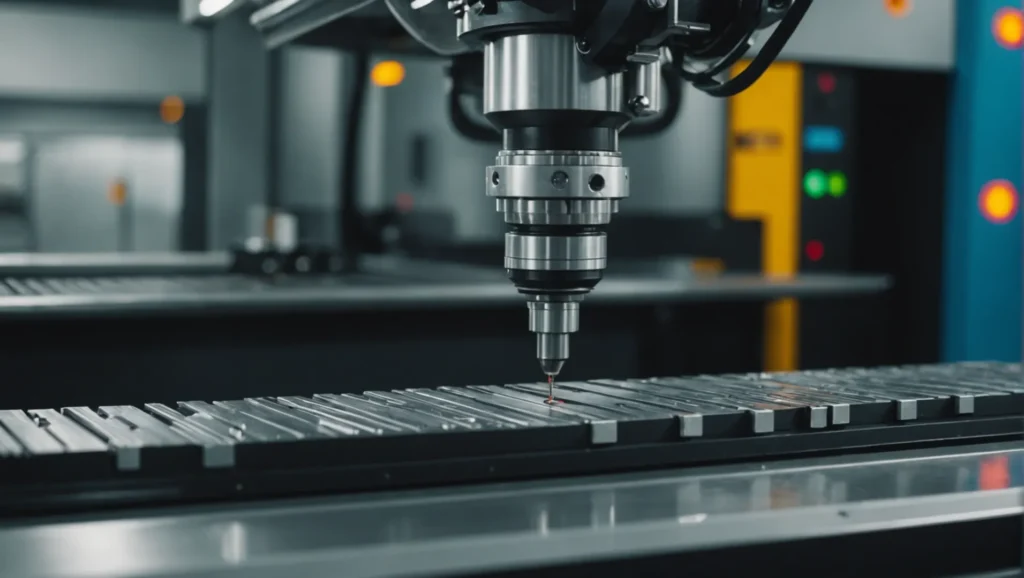
What Are the Key Factors for Achieving High Precision in Injection Molding?
Achieving high precision in injection molding is essential for ensuring product quality across various industries. This article delves into the critical factors influencing precision, including mold design, material selection, process parameters, and equipment maintenance. By understanding these aspects, manufacturers can ...
MANUFACTURING
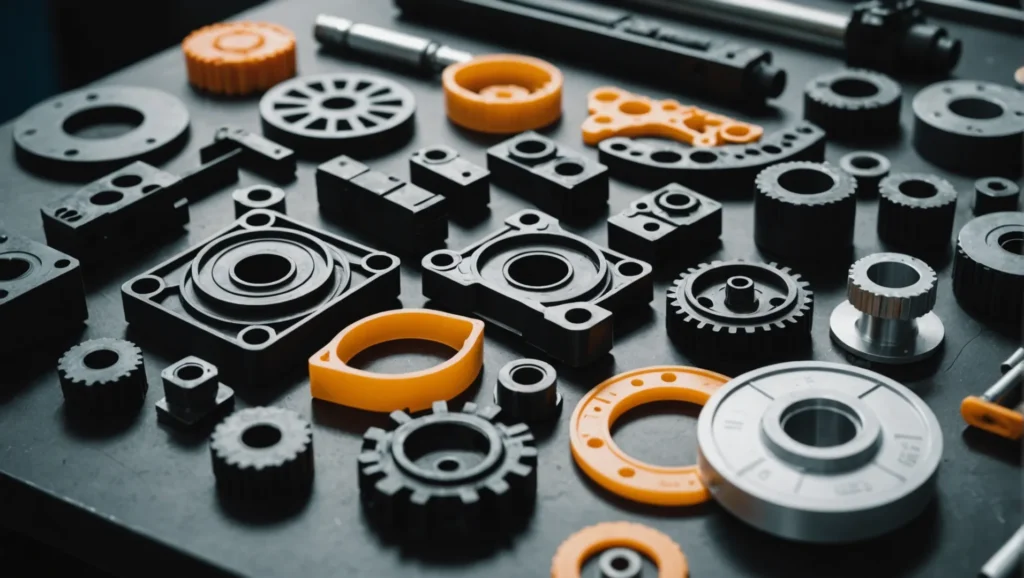
How Can You Balance Rigidity and Toughness in Plastic Injection Molded Parts?
Crafting the perfect plastic injection molded part requires a delicate balance between rigidity and toughness. Achieving this equilibrium ensures durability and performance in demanding applications. In this article, we will explore essential strategies for material selection, structural design, and process ...
DEVELOPMENT
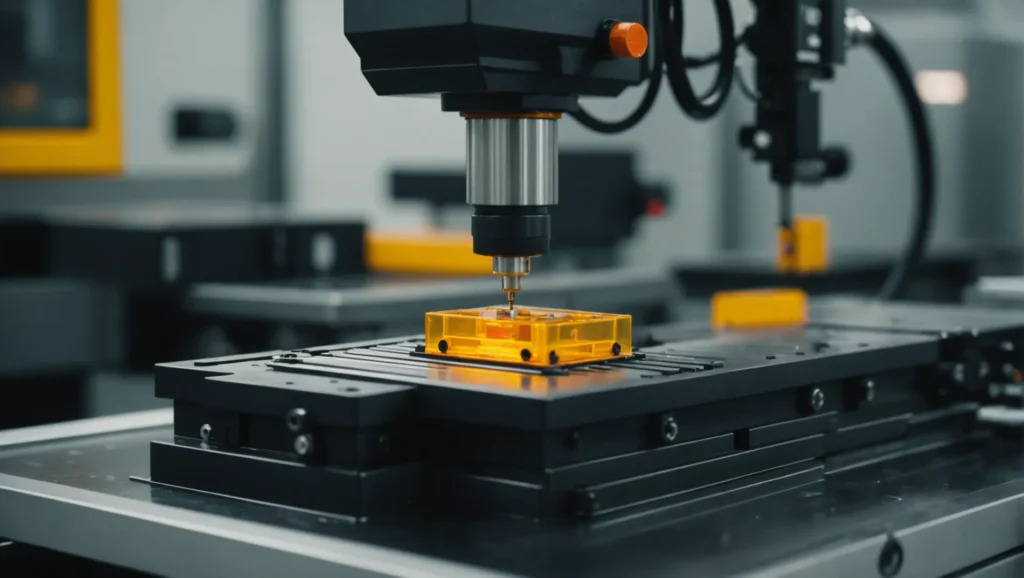
How Can You Prevent Residual Stress Problems in the Injection Molding Process?
Residual stress can severely impact the quality of injection-molded plastic products. Understanding its causes and effects is crucial for manufacturers aiming to improve product performance. This article explores effective strategies for preventing residual stress, including material selection, cooling rates, and ...
OPTIMIZATION
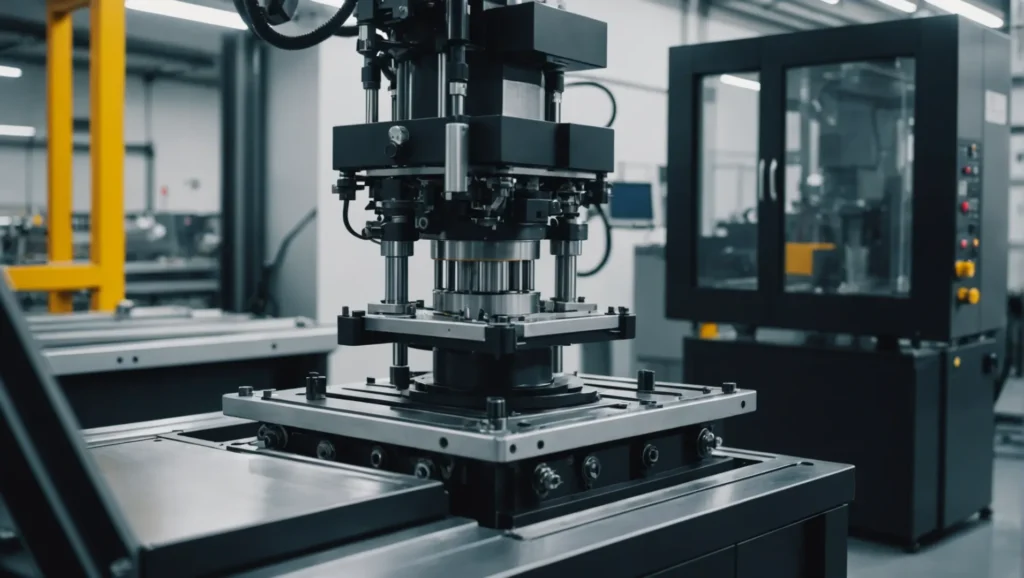
How Can You Optimize Clamping Accuracy in Injection Molds?
Clamping accuracy is a cornerstone of successful injection molding, directly impacting product quality and operational efficiency. By focusing on mold design, manufacturing techniques, proper operation, and maintenance, manufacturers can enhance their processes and ensure top-notch outputs.
DEVELOPMENT
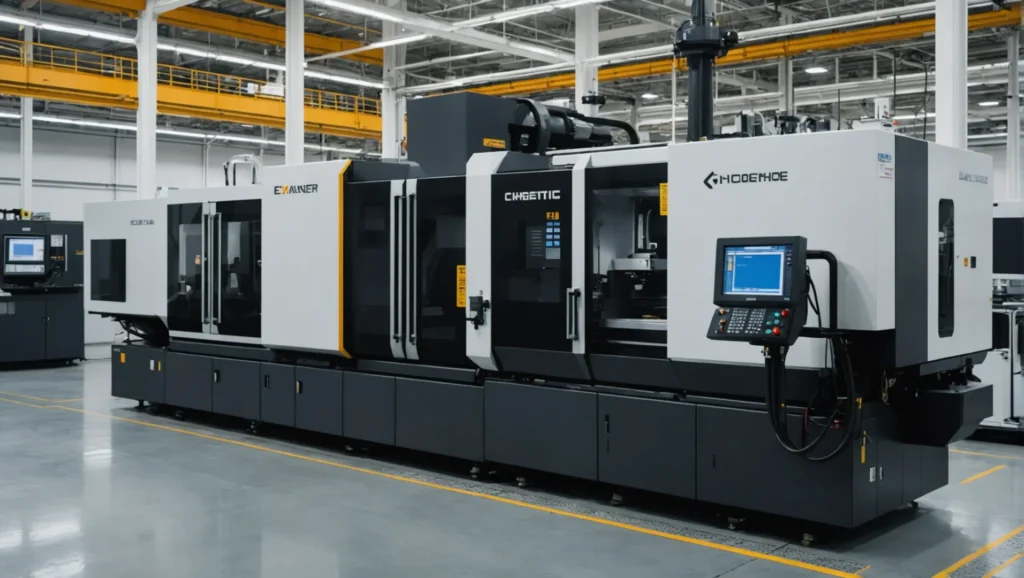
How Does Rapid Cooling Technology Enhance Injection Molding Efficiency?
In today's fast-paced manufacturing landscape, efficiency is not just a goal; it’s a necessity. Rapid cooling technology is at the forefront of revolutionizing injection molding processes. By optimizing cooling, it not only accelerates production but also enhances the quality of ...
DEVELOPMENT
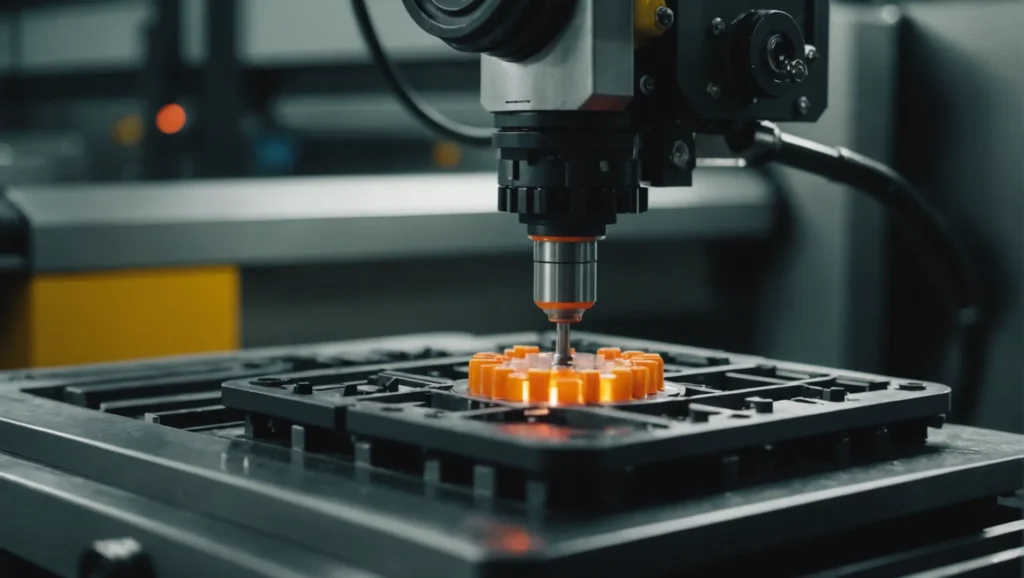
What Causes Debonding and Cracks in Injection Molded Products, and How Can They Be Prevented?
Injection molding is fundamental to modern manufacturing, but defects like debonding and cracks can jeopardize product quality. Understanding the causes of these issues is essential for manufacturers looking to optimize their processes. This article delves into the key factors contributing ...
Quality Inspection
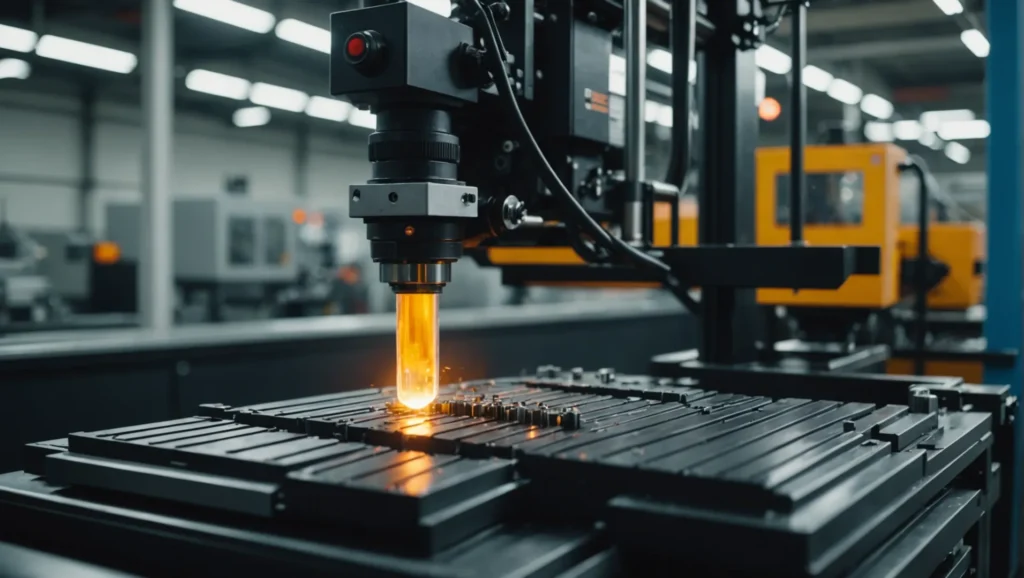
How Does the Injection Molding Process Affect the Thickness of Plastic Parts?
Injection molding is a pivotal process in manufacturing high-quality plastic parts with precise thickness. Understanding its impact is essential for optimal design. This article delves into key factors such as injection pressure, holding pressure, and mold temperature that influence thickness ...
MANUFACTURING
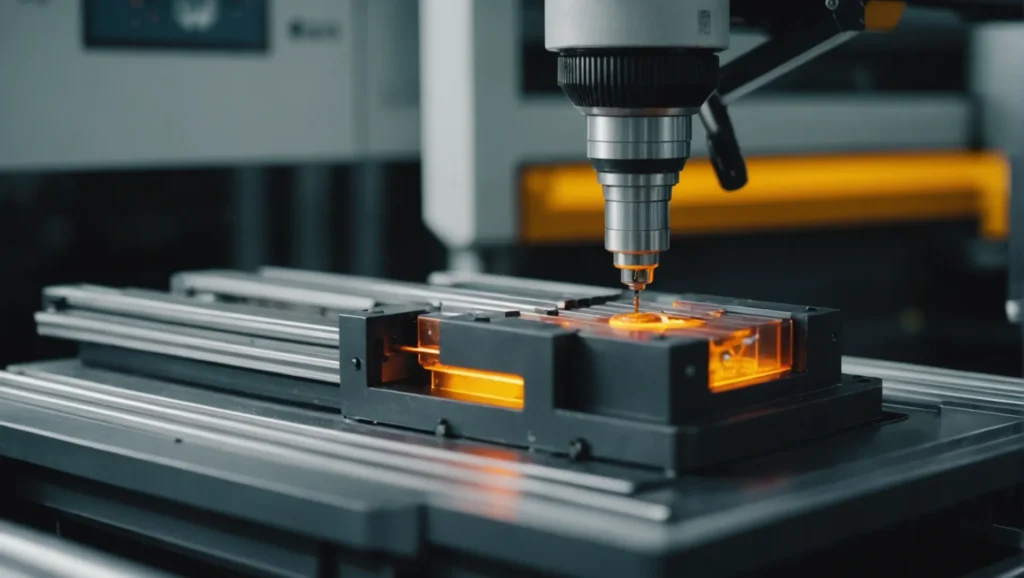
What Are the Solutions to High-Temperature Deformation in Plastic Injection Molded Parts?
High-temperature deformation is a common challenge in the plastic injection molding industry that can significantly impact product quality and reliability. This article explores effective strategies to tackle this issue, including material selection, process optimization, design improvements, and post-processing techniques. By ...
OPTIMIZATION
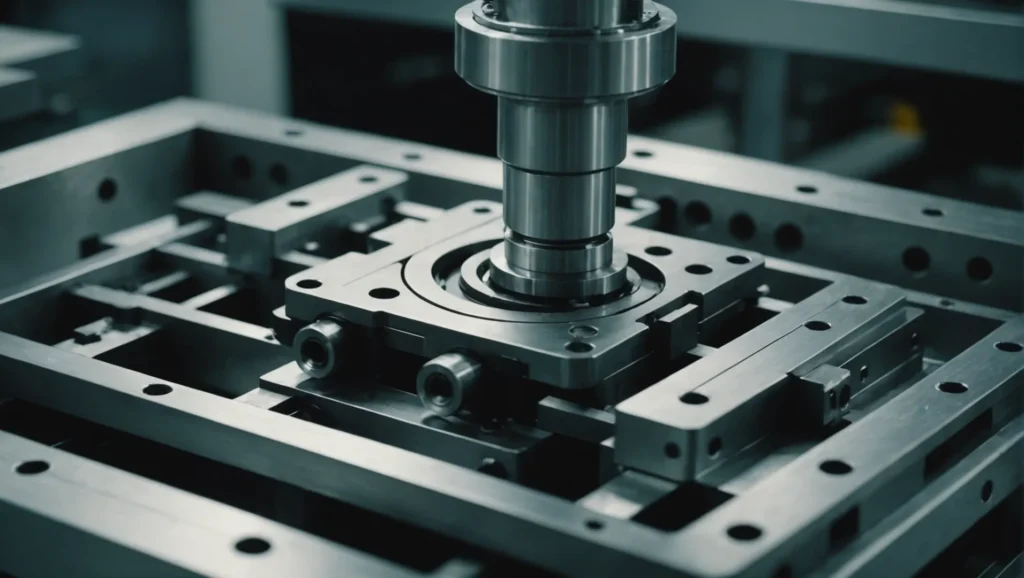
How Can You Design and Optimize the Guide Mechanism of Injection Molds?
The guide mechanism is crucial in injection molding, affecting precision and efficiency. Understanding its design, functions, and optimization techniques can greatly enhance your molding projects. Dive deep into the essential elements that ensure your molds operate at their best, delivering ...
DESIGN
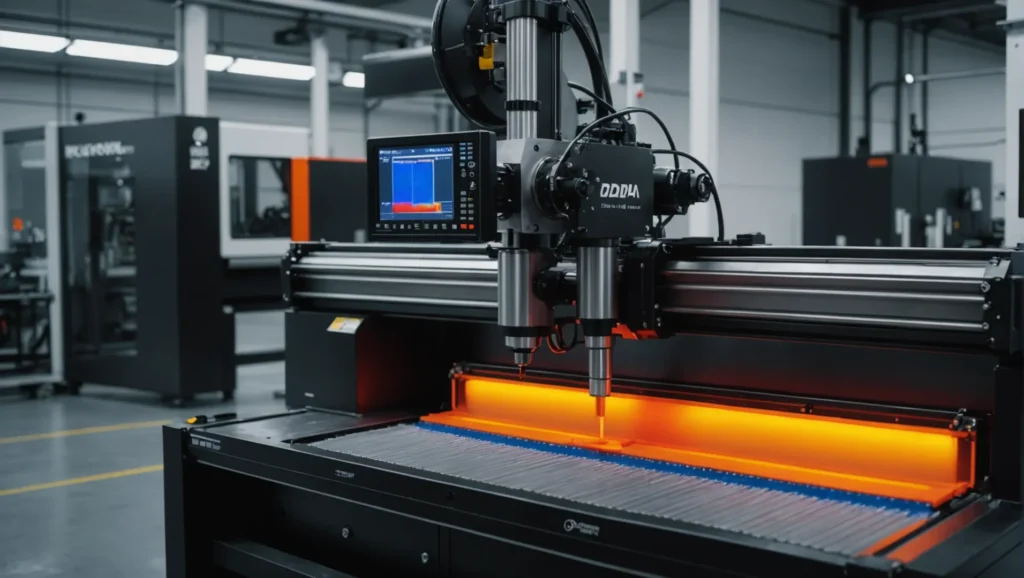
How Can You Effectively Control Heat Loss During Injection Molding?
In the world of manufacturing, particularly in injection molding, controlling heat loss is vital. By optimizing equipment design, ensuring proper insulation, and managing environmental factors, manufacturers can enhance energy efficiency and product quality. Dive into the details of effective heat ...
DEVELOPMENT
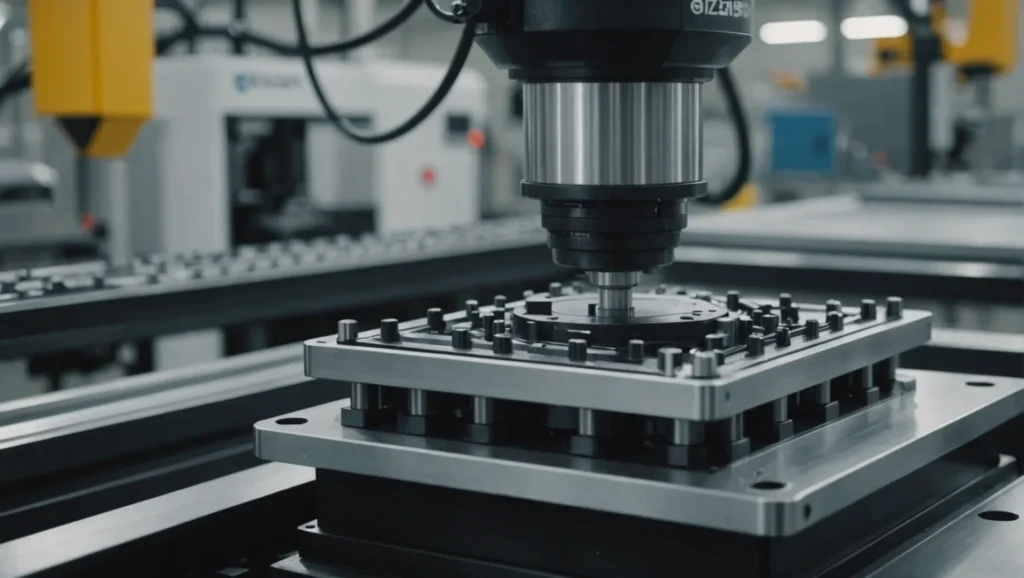
What Are the Best Techniques for Controlling Thickness Tolerance in Injection Molded Products?
Maintaining precise thickness in injection molded products is a challenge that manufacturers often face. This article explores essential techniques to control thickness tolerance, including mold design, process parameter adjustments, material selection, and quality inspection. Discover how these strategies can enhance ...
DEVELOPMENT
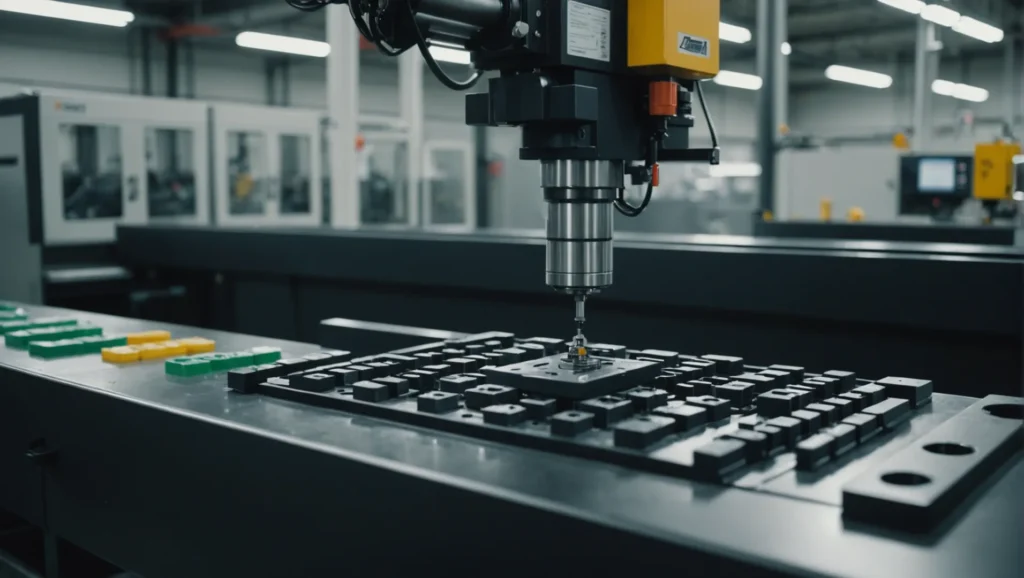
What Are the Benefits of Using Antioxidants in Injection Molding Production?
Injection molding is a complex process that demands precision and resilience in materials. Antioxidants offer a solution to many common challenges faced during production. They play a crucial role in improving product quality, longevity, and manufacturing efficiency. This article explores ...
MANUFACTURING
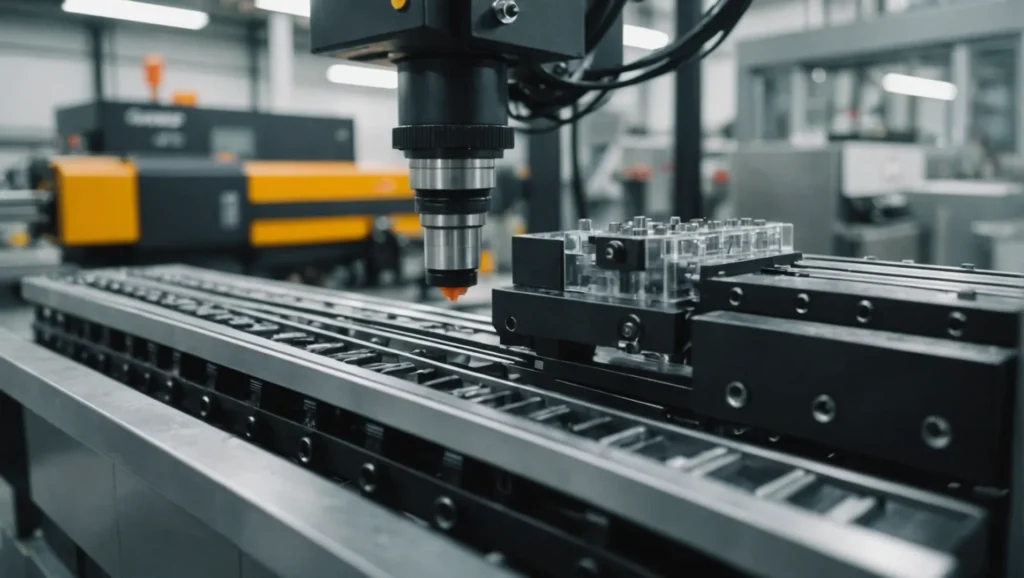
How Can You Optimize the Filling and Holding Stages in Plastic Injection Molding?
Optimizing the filling and holding stages in plastic injection molding is essential for achieving high-quality products. This article explores the critical parameters involved, including injection speed, pressure, and temperature. By understanding how these factors interact, you can significantly enhance your ...
DEVELOPMENT
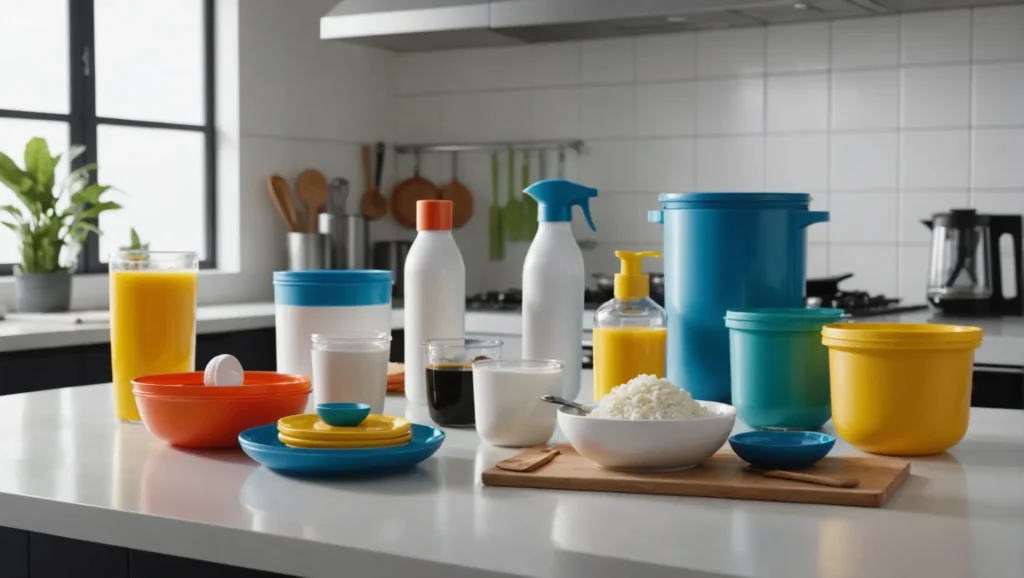
What Are the Latest Market Trends and Design Directions for Injection Molded Household Products?
In a world where our homes reflect our identities, injection molded household products are evolving to meet our diverse needs. From sustainability to smart technology, let's explore the latest trends shaping these essential items in our lives. Join me as ...
DESIGN
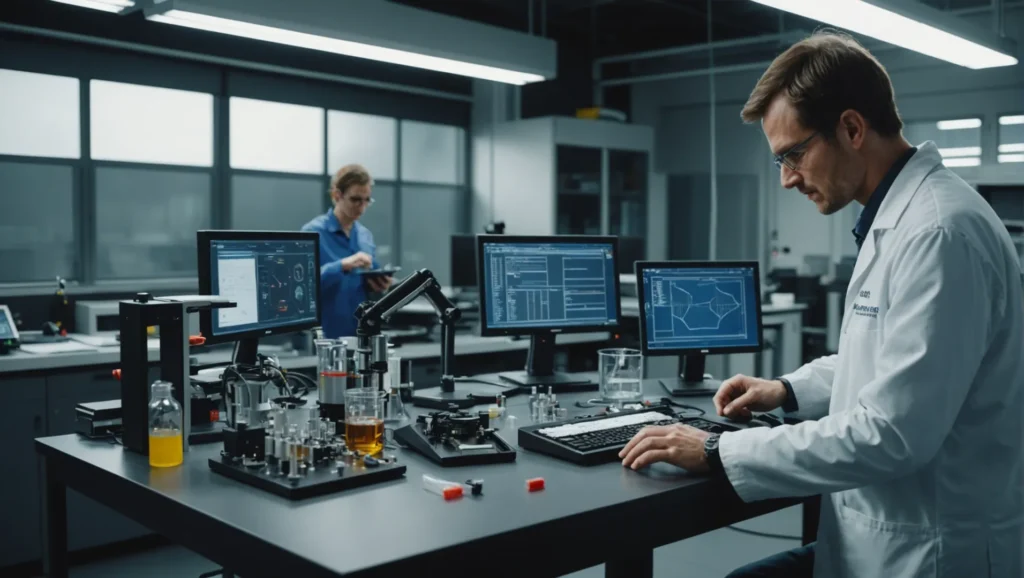
How Can Anti-Deformation Design Improve Injection Molded Parts in High Humidity Environments?
High humidity can pose a significant challenge to injection molded parts, leading to deformation and compromised performance. This article explores anti-deformation design strategies, focusing on material selection, structural integrity, and mold design, providing insights into creating robust components that withstand ...
MANUFACTURING
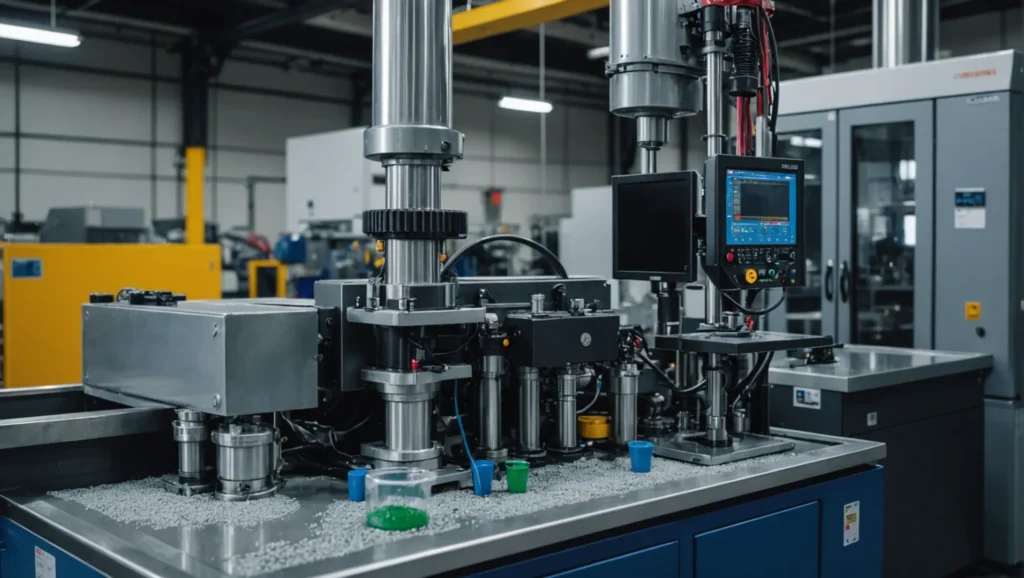
What Are the Common Colorant Mixing Technologies in Injection Molding?
Color consistency in injection molding can significantly impact the quality of the final product. Understanding various colorant mixing technologies is essential for achieving desired results. This article explores methods like dry mixing, masterbatch coloring, paste colorant coloring, and pigment pre-dispersion, ...
MANUFACTURING
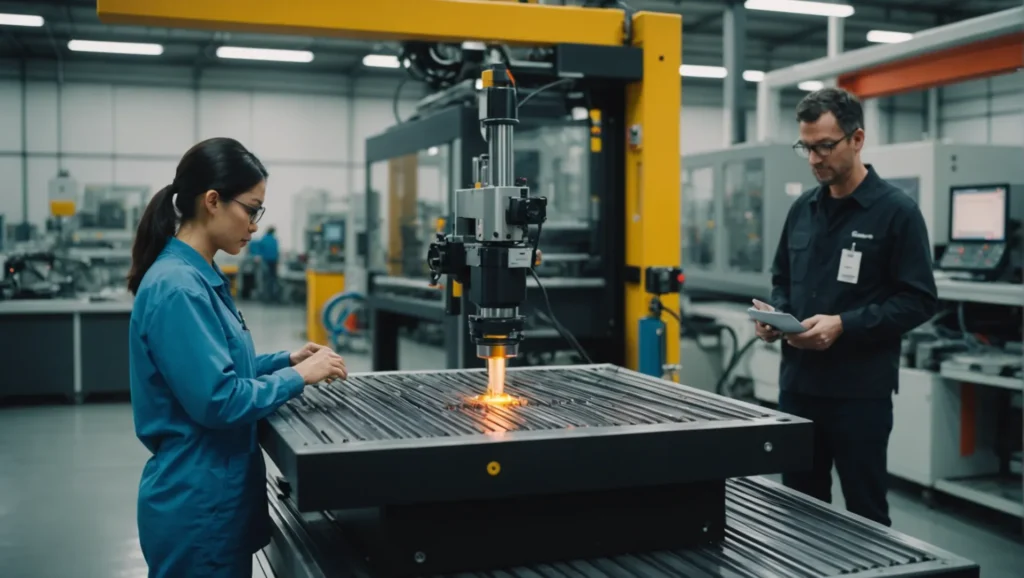
How Can You Ensure Impact Resistance in Products During Injection Molding?
Injection molding is a vital process for creating durable plastic products, but impact resistance is key for their performance and longevity. This article explores how to enhance impact resistance through careful material selection, precise process parameters, thoughtful mold design, and ...
OPTIMIZATION
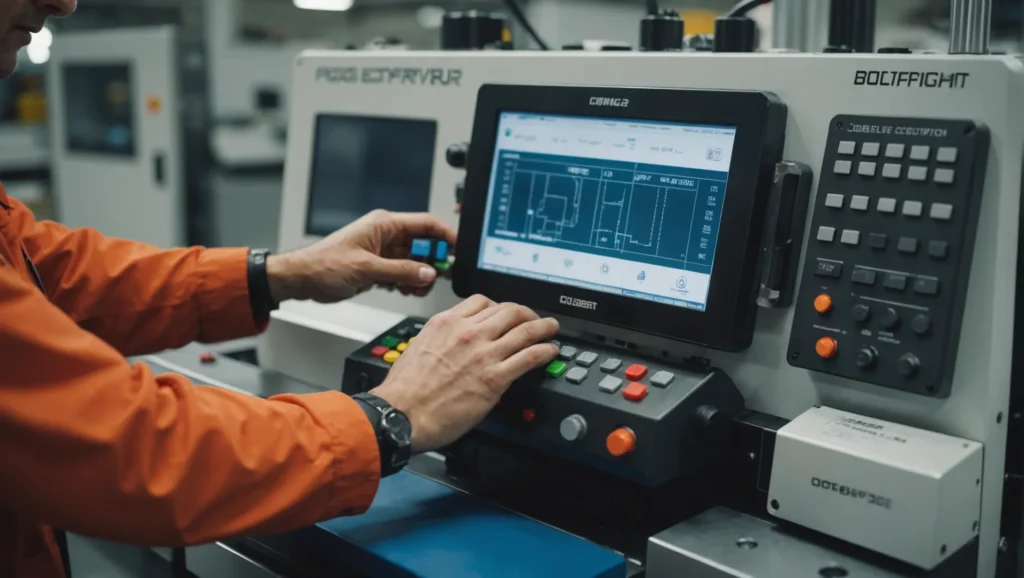
How Can You Adjust Back Pressure in Injection Molding for Better Quality?
Injection molding is a precise science, where even minor adjustments can significantly impact the final product's quality. Understanding back pressure is key to achieving optimal product consistency and minimizing defects. Let's explore effective strategies to adjust back pressure and improve ...
DEVELOPMENT
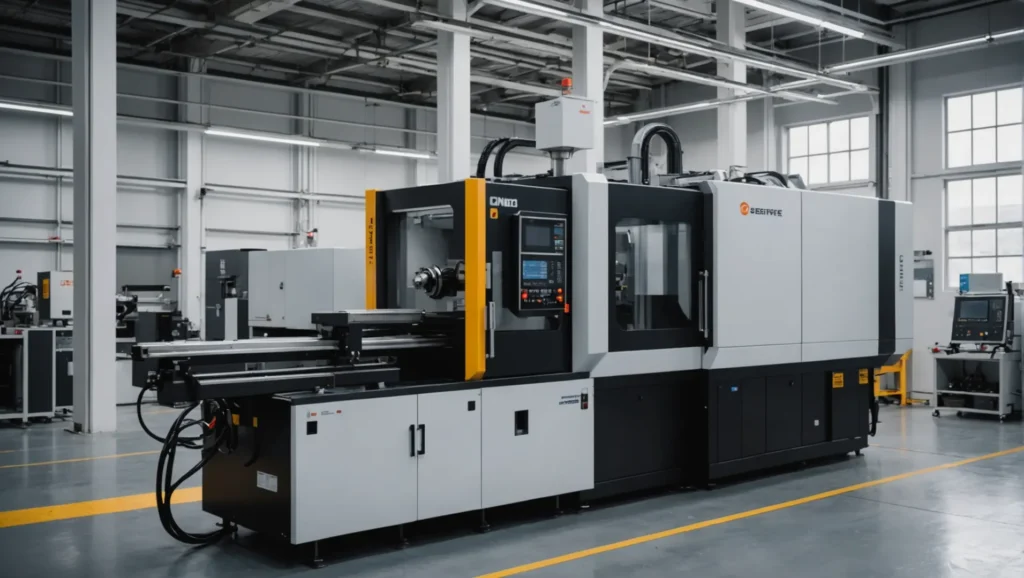
How Can You Solve Static Problems in Injection Molding Production?
Static electricity can be a silent disruptor in injection molding production, impacting product quality and safety. To tackle these issues, strategies such as using antistatic agents, optimizing humidity levels, employing static elimination equipment, and improving design can be effective. Let’s ...
OPTIMIZATION
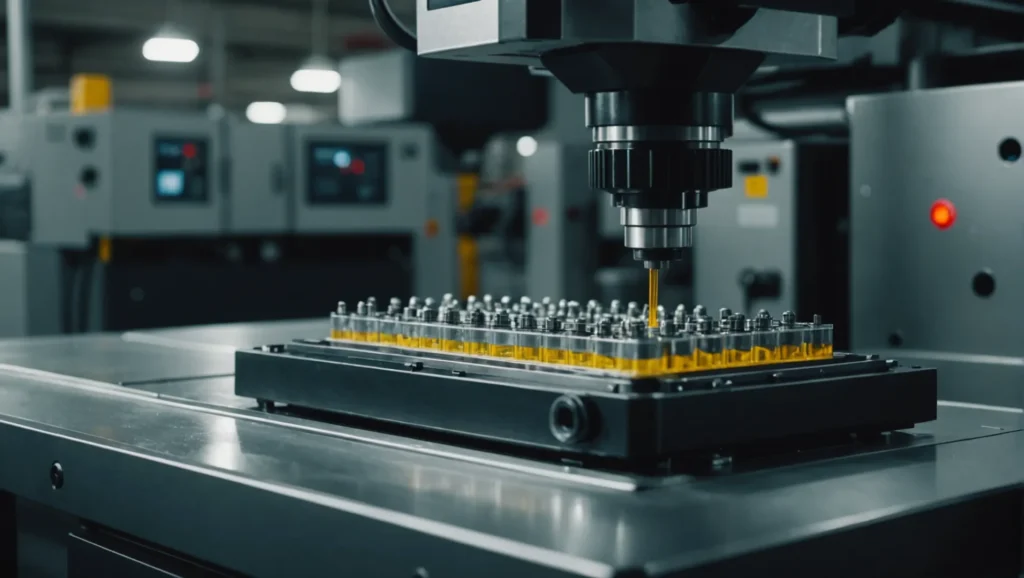
What Are Effective Strategies to Reduce Molding Stress in Injection Molding?
Injection molding is a critical process in manufacturing, but managing stress within the mold is vital to avoid defects like warpage and cracking. By implementing effective strategies, manufacturers can enhance product quality and durability. This article explores various methods including ...
DEVELOPMENT
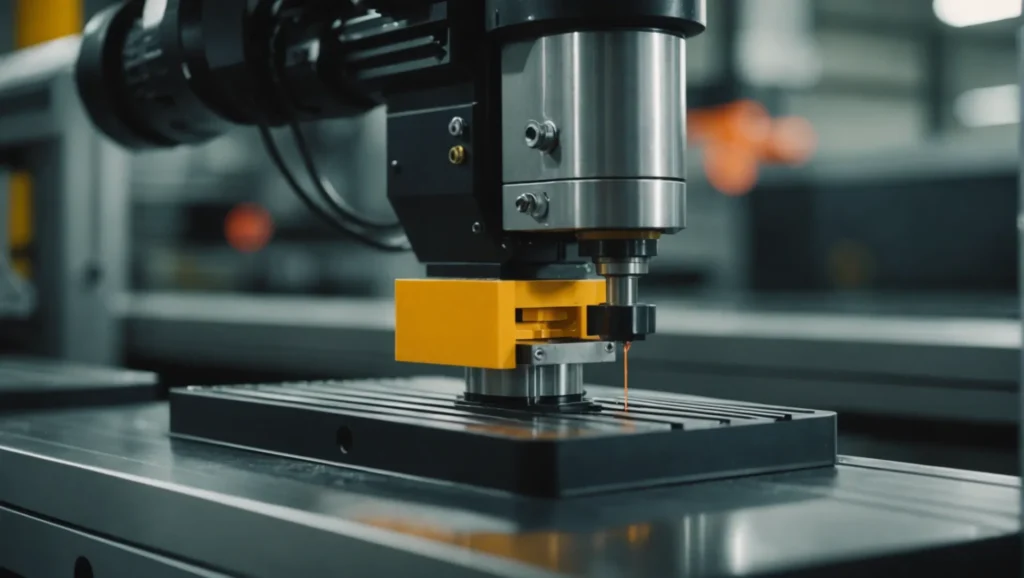
What Are the Common Technical Difficulties in Ultra-Thin Injection Molding?
Ultra-thin injection molding is a cutting-edge technique that allows manufacturers to create incredibly thin and precise plastic parts. However, this innovative process is not without its challenges. In this article, I explore the common technical difficulties faced in ultra-thin injection ...
OPTIMIZATION
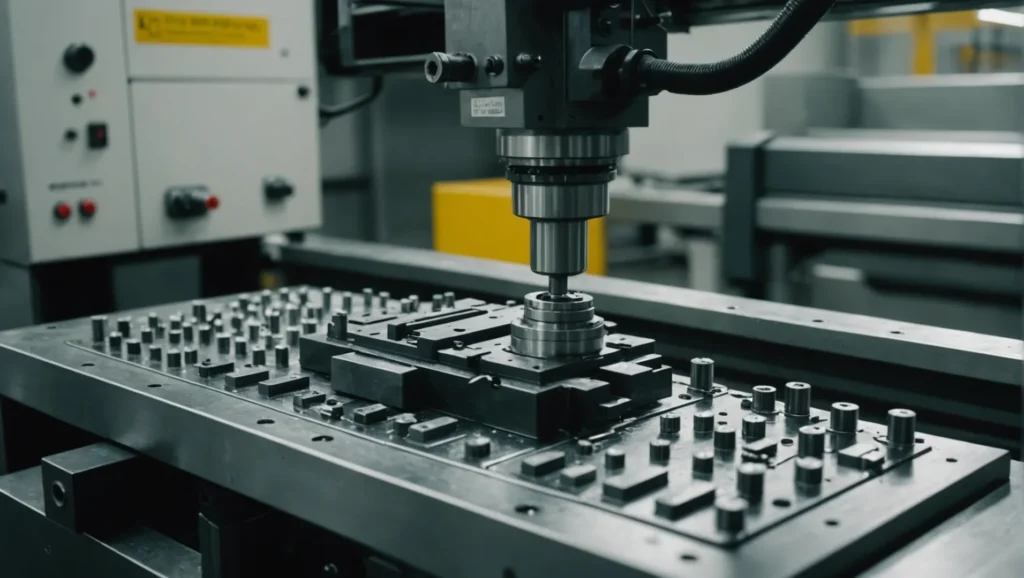
What Factors Determine the Best Mold Opening Time in Injection Molding?
In the world of injection molding, getting the mold opening time just right is crucial. It can significantly impact both production efficiency and product quality. Understanding the various factors that play into determining this timing—like product characteristics, material types, process ...
DEVELOPMENT
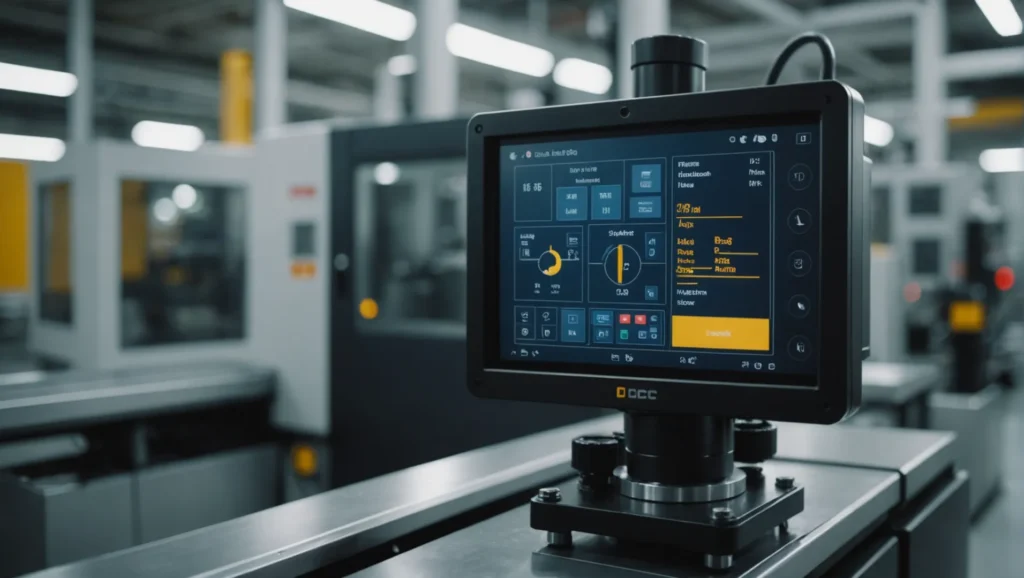
What Are the Best Techniques for Controlling Liquid Plastic Flow Rate in Injection Molding?
Controlling the flow rate of liquid plastic during injection molding is essential for achieving high-quality products. In this article, I'll explore various techniques, including mechanical adjustments, electrical controls, and intelligent systems. Each method has its own strengths and weaknesses, and ...
DEVELOPMENT
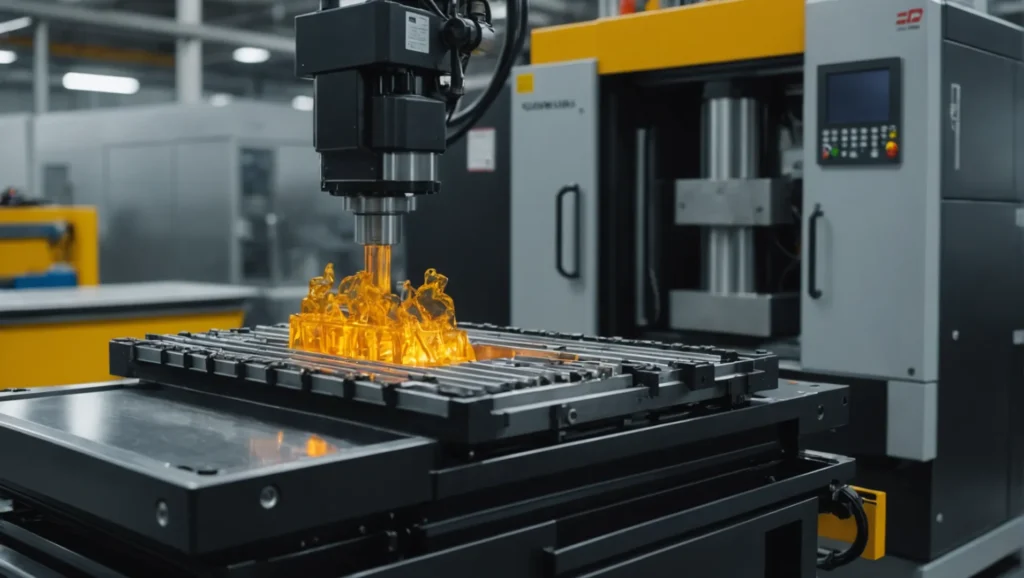
How Can Mold Optimization Enhance the Density of Injection Molded Parts?
In the world of plastics manufacturing, achieving optimal density in injection molded parts is essential for product durability and performance. This article explores how mold optimization can significantly improve the density of these parts through careful design and process adjustments.
OPTIMIZATION
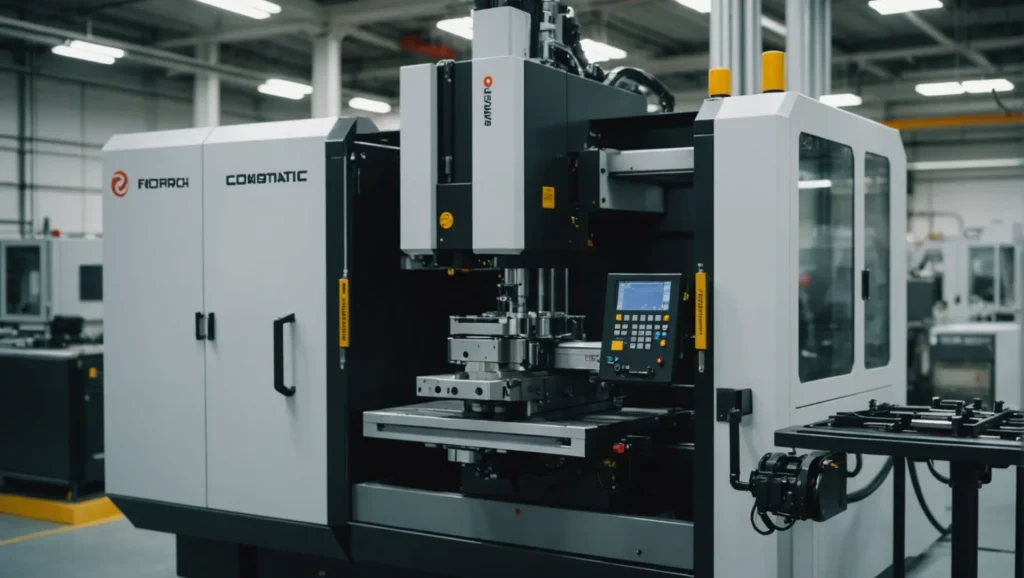
What Are the Best Practices for Achieving High Repeatability in Injection Molding?
Injection molding is essential in manufacturing, where achieving high repeatability is vital for maintaining product quality and consistency. This article explores best practices, including equipment quality, material management, process optimization, and operator training, to enhance repeatability and reduce defects.
DEVELOPMENT