In manufacturing, every decision counts. A single choice can lead to either triumph or failure.
To enhance the mechanical properties of injection molded parts, focus on selecting appropriate raw materials, optimizing the injection molding process, refining mold design, and implementing effective post-processing techniques. These strategies can significantly improve strength and durability.
While these initial insights provide a solid foundation, diving deeper into each aspect can unlock advanced techniques and optimization methods. Continue reading to discover detailed strategies and expert tips for enhancing your injection molded parts.
Annealing improves the strength of injection molded parts.True
Annealing reduces residual stress, enhancing mechanical properties and stability.
What Are the Key Factors in Selecting Resins for Injection Molding?
Choosing the right resin is crucial for achieving optimal performance in injection molded parts.
Key factors in selecting resins for injection molding include mechanical properties, resin type, molecular weight distribution, and the addition of reinforcement materials. These elements determine the strength, stiffness, and overall quality of the final product.
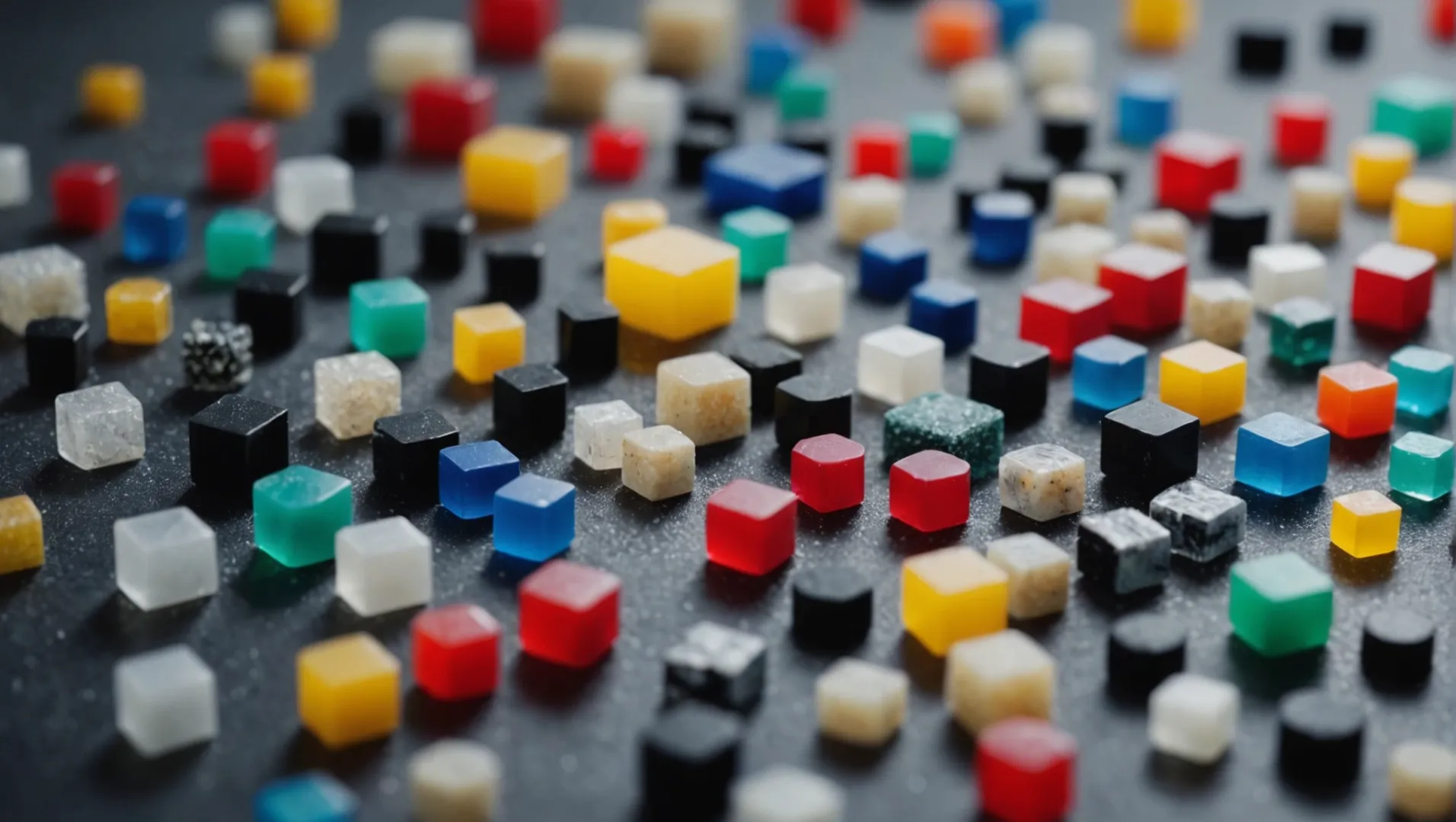
Understanding Resin Types
Selecting the right resin starts with understanding the wide array of resin types available1 for injection molding. Engineering plastics such as polycarbonate (PC) and polyamide (PA) are favored for their high strength and stiffness. The choice of resin should align with the specific performance requirements of the part being molded.
Importance of Molecular Weight Distribution
Molecular weight distribution (MWD) significantly impacts the mechanical properties of resins. A narrower MWD often results in better strength and durability. This is because resins with a higher molecular weight and uniform distribution tend to exhibit improved mechanical properties. Understanding MWD can guide you in selecting a resin that meets your performance criteria.
Reinforcement Materials: Glass and Carbon Fibers
Adding reinforcement materials like glass or carbon fibers can dramatically enhance the mechanical attributes of injection molded parts.
- Glass Fiber: Commonly used to increase strength, stiffness, and heat resistance. The content of glass fiber reinforced resin generally varies between 10% and 40%.
- Carbon Fiber: Offers high strength and stiffness with reduced weight but comes at a higher cost. It’s suitable for applications demanding superior mechanical properties.
Comparison Table: Glass Fiber vs Carbon Fiber
Material | Benefits | Drawbacks |
---|---|---|
Glass Fiber | Cost-effective, enhances strength | Heavier than carbon |
Carbon Fiber | Lightweight, excellent strength | Expensive |
Role of Mineral Fillers
Mineral fillers like talcum powder and calcium carbonate can enhance hardness and dimensional stability but are less effective in improving strength compared to glass or carbon fibers. These fillers are ideal when slight improvements in hardness are needed without significantly altering other properties.
Aligning Resin Selection with Application Needs
Ultimately, selecting the appropriate resin involves balancing mechanical performance with cost-effectiveness and manufacturing considerations. Analyze the application requirements carefully to decide on the best resin type and reinforcements. This process ensures that the final product not only meets but exceeds performance expectations.
Polycarbonate is a type of engineering plastic.True
Polycarbonate is known for its high strength and stiffness, ideal for engineering.
Mineral fillers improve strength more than glass fibers.False
Glass fibers enhance strength significantly more than mineral fillers.
How Can Process Optimization Improve Part Durability?
Unlocking the full potential of injection molded parts hinges on process optimization, which directly impacts durability.
Optimizing the injection molding process enhances part durability by fine-tuning temperature, pressure, and cooling rates. This reduces defects and internal stresses, leading to stronger, longer-lasting parts.
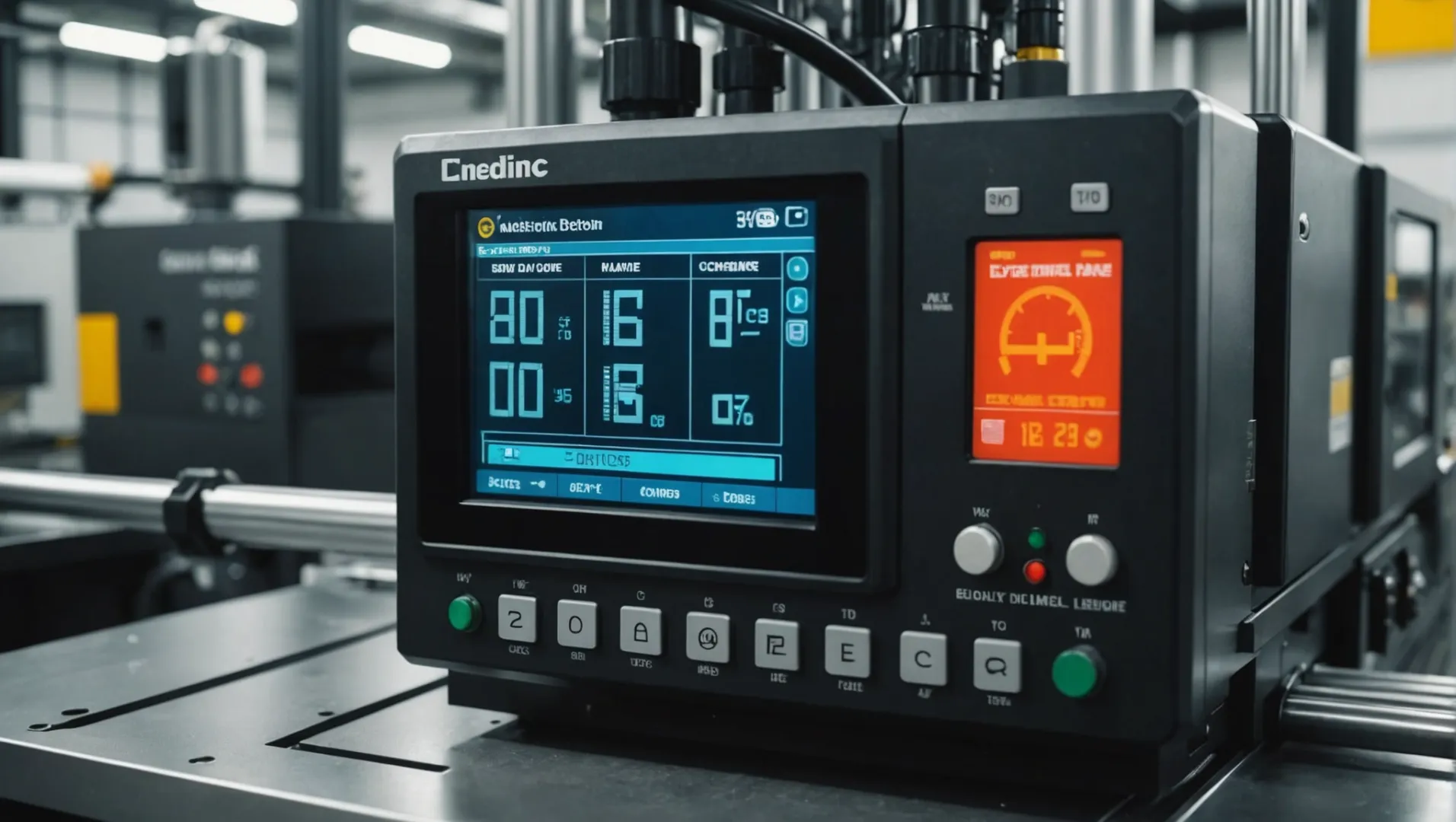
Temperature Control: A Crucial Variable
The temperature at which injection molding is carried out can greatly influence the final product’s durability. By increasing the molding temperature appropriately, the viscosity of the resin decreases. This improved flow allows for better cavity filling, minimizing internal defects such as voids or incomplete sections. However, it’s vital to strike a balance; excessive heat can cause resin decomposition or bubbles. Each resin type, like polycarbonate (PC) or polyamide (PA), has an optimal temperature range that needs to be respected for maximum efficiency.
Pressure and Speed Adjustments
Adjusting the pressure and speed during the injection process can lead to significant improvements in part strength. Higher injection pressures ensure the resin fills the mold cavity completely and tightly, reducing issues like pores and shrinkage holes. Likewise, controlling the speed can prevent defects such as flow marks. An initial high speed helps quickly fill the cavity, while a slower speed towards the end prevents excessive pressure that might damage the mold.
Holding Time and Pressure Optimization
An extended holding time and increased pressure compensate for resin shrinkage as it cools, which is crucial in reducing internal stress and shrinkage defects. However, care must be taken to avoid over-holding, which can introduce additional stresses or deformations. The key is to find the sweet spot where these parameters are balanced.
Cooling Rate Considerations
Controlling the cooling rate is essential for ensuring even shrinkage and minimizing stress-induced warping or brittleness. Fast cooling may lead to increased brittleness, while slow cooling might hamper production efficiency. By adjusting mold temperature and optimizing the cooling water channel layout, manufacturers can achieve an ideal cooling speed.
The table below summarizes key process optimizations and their effects:
Process Optimization | Benefit |
---|---|
Temperature Control | Enhances flow, reduces defects |
Pressure Adjustment | Improves fill quality |
Speed Control | Minimizes flow marks |
Holding Time/Pressure | Compensates for shrinkage |
Cooling Rate | Ensures uniform shrinkage |
By refining these parameters, manufacturers can significantly enhance part durability and performance. For further insights into how temperature control2 affects mechanical properties, explore expert recommendations on achieving optimal conditions.
Higher molding temperatures reduce resin viscosity.True
Higher temperatures decrease viscosity, enhancing flow and cavity filling.
Excessive cooling rates improve part durability.False
Fast cooling increases brittleness, compromising part durability.
What Role Does Mold Design Play in Mechanical Performance?
Mold design significantly impacts the mechanical performance of injection molded parts, influencing factors such as strength, durability, and dimensional accuracy.
A well-designed mold ensures optimal resin flow, reduces stress concentration, and maintains precision, thereby enhancing mechanical performance. Key aspects include optimizing mold structure, improving mold accuracy, and employing balanced gating systems.
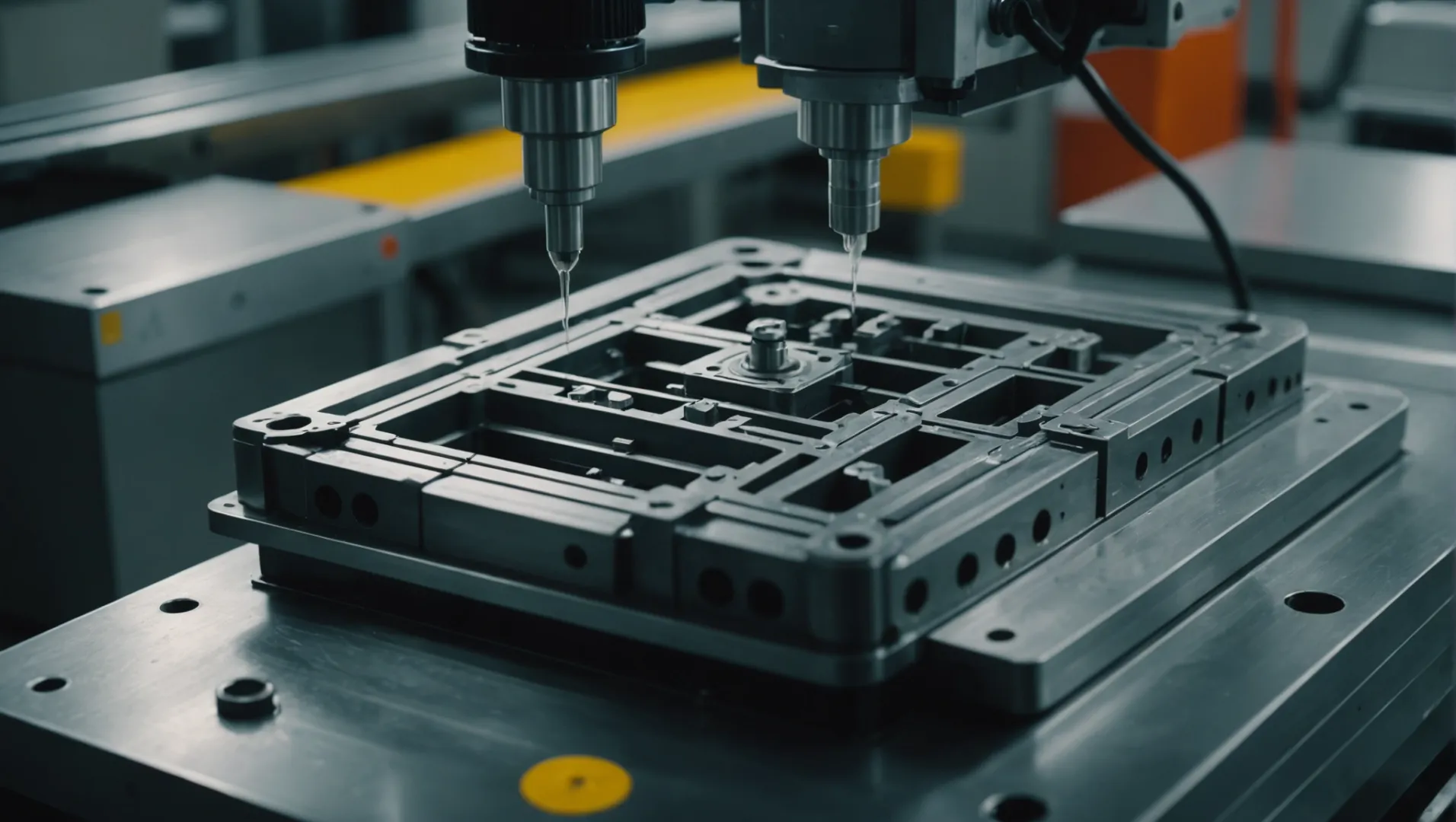
Optimizing Mold Structure
A critical aspect of mold design is structuring the mold to facilitate uniform resin flow and minimize potential defects. This involves:
- Balanced Pouring System: Ensures uniform resin distribution across the mold. A well-balanced system reduces localized stress concentrations, preventing weak spots.
- Gate Positioning and Number: Strategically placing gates reduces flow resistance and prevents overheating. This balance is crucial in avoiding issues like warping and distortion.
- Avoidance of Complex Structures: Overly intricate designs may lead to stress concentration points or dead corners where resin flow is restricted, compromising mechanical properties.
Improving Mold Accuracy
The precision of the mold directly impacts the dimensional accuracy and surface finish of the injection molded parts:
- Dimensional Accuracy: High-precision molds ensure parts are produced to exact specifications, reducing variance that could affect part performance.
- Surface Quality: A smooth mold surface reduces friction during resin flow, enhancing the finish and strength of the final product.
- Regular Maintenance: Routine upkeep of molds prevents wear and tear, ensuring consistent part quality and extending mold lifespan.
Employing Advanced Gating Systems
Utilizing sophisticated gating techniques can significantly enhance mechanical performance:
- Submarine Gates: These enable automatic part ejection and improve the aesthetic quality of the molded parts by eliminating gate marks.
- Hot Runner Systems: These systems reduce cycle time and material wastage, leading to cost-effective production while maintaining high quality.
Case Study: Balanced Mold Design Impact
Aspect | Traditional Design | Optimized Design |
---|---|---|
Resin Flow | Uneven | Uniform |
Stress Concentration | High | Low |
Mechanical Properties | Compromised | Enhanced |
The table above illustrates how an optimized mold design can improve mechanical properties by ensuring uniform resin flow and minimizing stress concentrations.
In summary, effective mold design3 is crucial in enhancing the mechanical performance of injection molded parts by ensuring precise structure, accurate dimensions, and advanced gating systems.
Balanced pouring reduces stress in molded parts.True
A balanced system ensures even resin distribution, reducing stress.
Complex mold designs enhance mechanical properties.False
Complex designs can create stress points, weakening the part.
Which Post-Processing Techniques Enhance Part Quality?
Unlocking the potential of injection molded parts lies in effective post-processing techniques.
Key post-processing techniques to enhance part quality include annealing and humidity adjustment. These methods improve dimensional stability, mechanical properties, and overall part performance by reducing internal stress and optimizing material characteristics after molding.
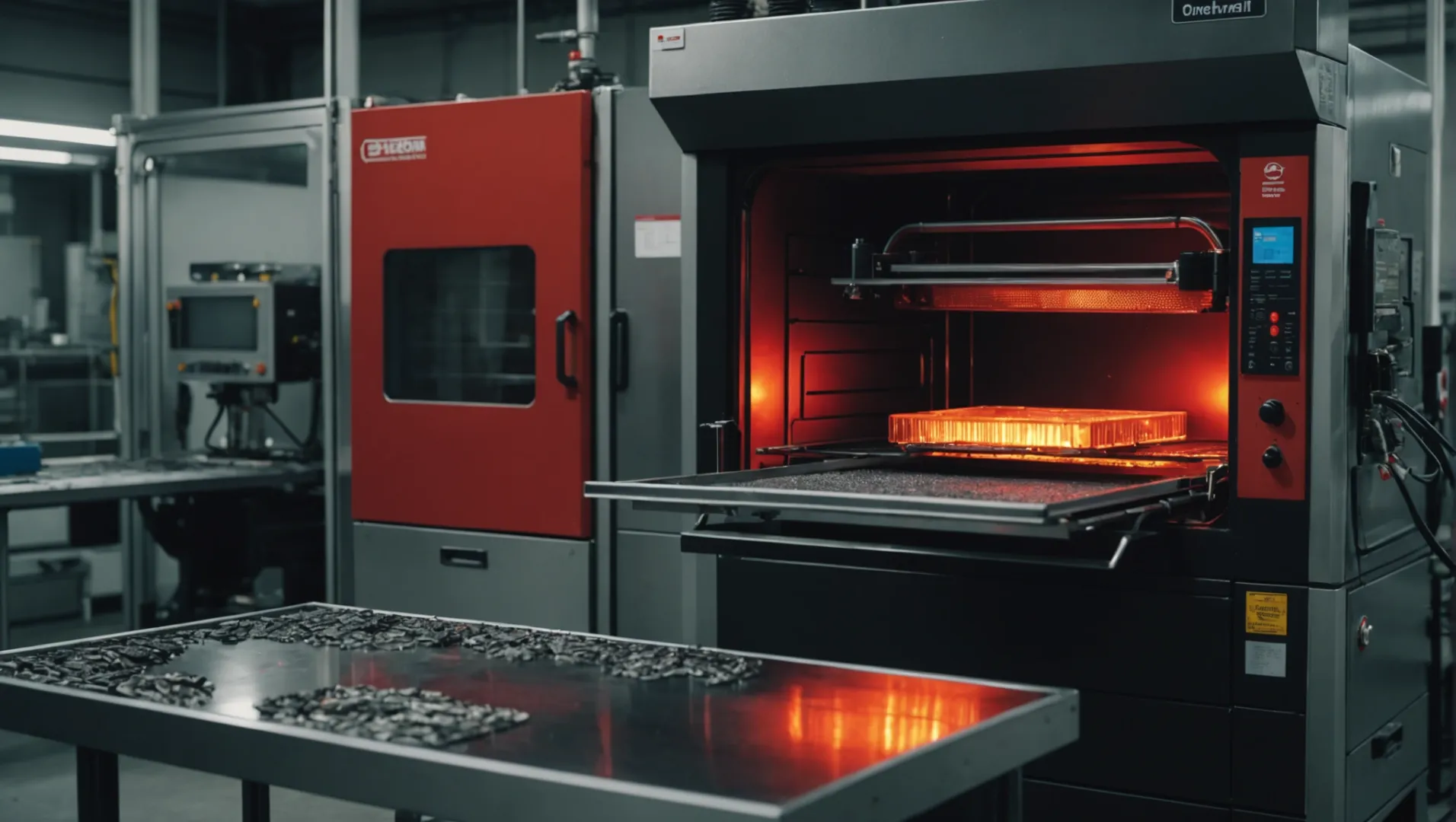
Annealing: Reducing Stress for Better Performance
Annealing is a thermal treatment process that involves heating the injection molded parts to a specific temperature and then cooling them at a controlled rate. This method effectively reduces residual stresses within the parts, which often arise during the rapid cooling phase in the molding process. By relieving these stresses, annealing improves dimensional stability and mechanical properties.
For instance, in cases involving polycarbonate4, annealing can increase impact resistance and enhance optical clarity. The process parameters such as temperature and time should be tailored to the specific resin and part size to avoid distortion while maximizing benefits.
Humidity Adjustment: Enhancing Toughness in Hygroscopic Resins
Certain resins like polyamide (PA) are hygroscopic, meaning they absorb moisture from their surroundings. Humidity adjustment treatment is a targeted post-processing technique where parts are exposed to controlled humidity levels to reach equilibrium moisture content.
This process significantly improves toughness and dimensional stability, particularly in applications where parts may be exposed to varying humidity levels. For example, treating nylon parts5 can optimize their performance in environments prone to moisture fluctuations, ensuring consistent function and longevity.
Surface Treatments: Improving Aesthetics and Functionality
Various surface treatments can enhance both the aesthetic appeal and functional attributes of injection molded parts. Techniques such as painting, plating, and coating add protective layers that can resist wear, corrosion, and UV degradation.
Moreover, applying advanced coatings6 can create smoother surfaces or add specific features like anti-fogging or anti-scratch properties. These treatments not only improve the visual quality but also extend the operational life of the parts.
Mechanical Treatments: Refining Surface Finish
Mechanical treatments like sanding, polishing, or tumbling help achieve desired surface finishes on injection molded parts. These processes are crucial for applications requiring high precision or specific texture characteristics.
Using vibratory finishing or abrasive blasting can effectively remove burrs or rough edges, enhancing both the look and performance of the final product. Understanding the right techniques7 for different materials ensures optimal results without compromising part integrity.
Annealing increases impact resistance of polycarbonate parts.True
Annealing relieves stresses, enhancing impact resistance and clarity.
Humidity adjustment decreases toughness in nylon parts.False
Humidity adjustment improves toughness by achieving moisture equilibrium.
Conclusion
By integrating these strategies into your production process, you can achieve superior mechanical properties in injection molded parts.
-
Explore various resin types and their unique properties for informed decision-making.: Common Applications for Plastic Resin Injection Molding · ABS · Celson® (Acetal) · Polypropylene · HIPS · LDPE. ↩
-
Explore expert advice on optimal molding temperatures for durability.: Temperature is naturally a very important factor in the plastic injection molding process, and two particular temperature types hold an especially vital role. ↩
-
Discover detailed insights into how mold design affects mechanical performance.: Mike Baranoski, a Design Engineer at Rodon, discusses how his role and having a solid design are critical to the plastic injection molding process. ↩
-
Explore how annealing boosts polycarbonate’s impact resistance and clarity.: BENEFITS OF POST-MACHINING ANNEALING ; Polycarbonate (unfilled), 4 hours to 275°F, 30 minutes per 1/4” thickness ; Polycarbonate (glass-filled), 4 hours to 290°F … ↩
-
Learn how humidity control enhances nylon part toughness.: Most nylon manufacturers will recommend drying nylon to below 0.2% moisture content. This will typically yield acceptable parts but reducing … ↩
-
Discover coatings that enhance durability and aesthetics.: PVD coatings will reduce friction on the components and in the cavities of your plastic injection mold. This helps the process in a number of ways. ↩
-
Find out which finishing methods suit various materials.: Injection molding finish options include SPI, VDI, MT, and YS standards. Learn about mold polish and mold texture standards for injection molded plastic … ↩