All Posts
blog & article
read our latest newsletter
Whether you’re curious about material selection, product design, mold design, mold making and injection molding, feel free to ask us anything. Our team is ready to provide the guidance and insights you need.
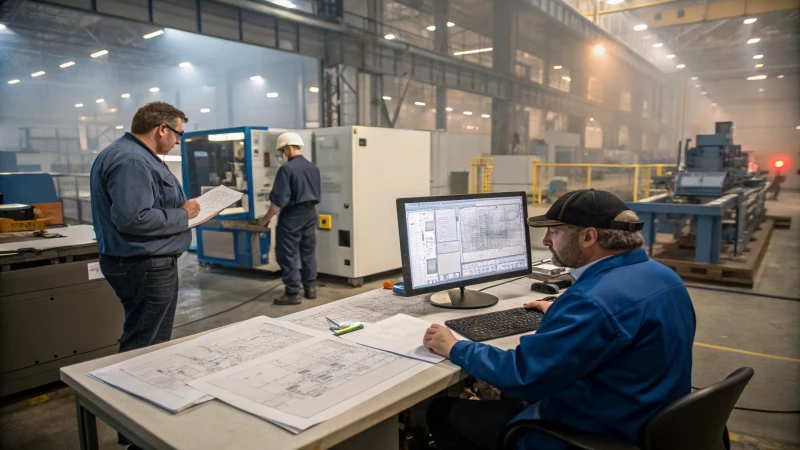
How Is the Standard Development Process for Injection Molds Defined?
This article outlines the standard development process for injection molds, detailing essential steps such as product analysis, design planning, mold structure considerations, manufacturing techniques, trial testing procedures, and the importance of data organization. Each phase is crucial for ensuring high-quality ...
MANUFACTURING
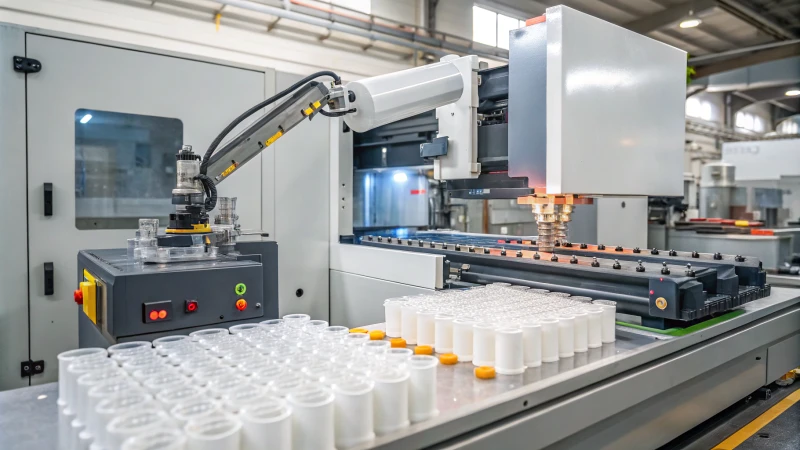
How Does Injection Speed Affect the Productivity of Injection Molds?
This article explores the critical role of injection speed in the productivity of injection molds. It highlights how adjusting injection speed can reduce cycle times, enhance product quality, and improve demolding efficiency. However, it also addresses the potential risks associated ...
MANUFACTURING
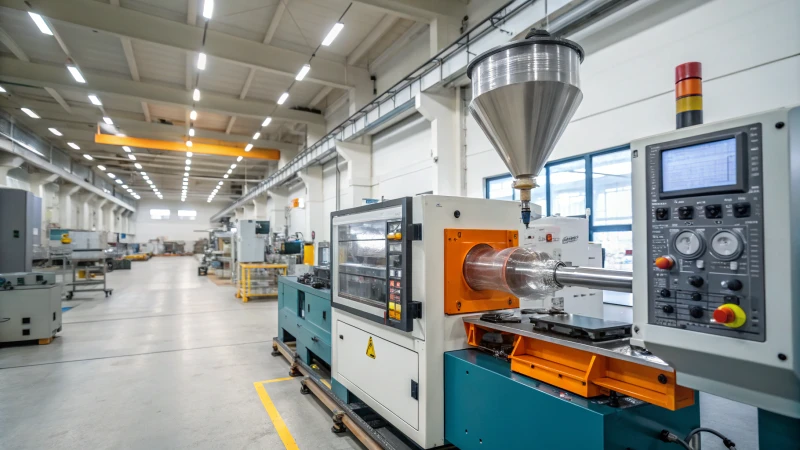
How Quickly Can Injection Molds Be Filled?
The speed at which injection molds are filled is influenced by various factors including the type of injection molding machine, the viscosity of the plastic materials used, and the size and shape of the products being manufactured. Ordinary small machines ...
MANUFACTURING
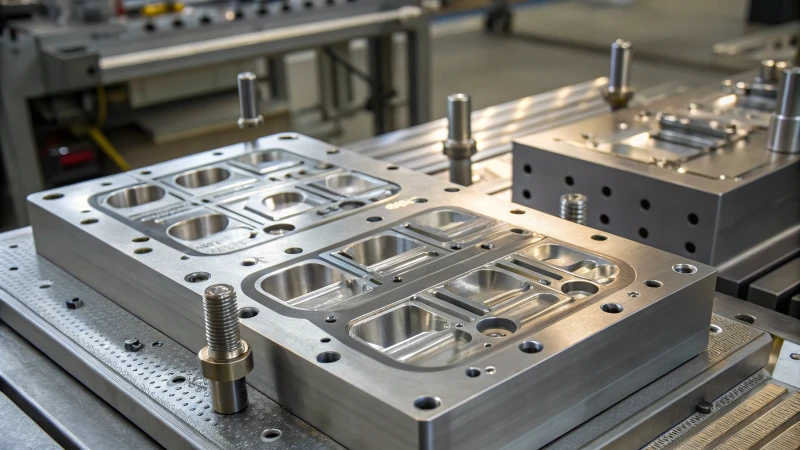
What Are Effective Solutions for Underfill Problems in Mold Design?
Underfill issues in mold design can be frustrating, but with the right strategies, they can be effectively addressed. Key solutions include optimizing gate placement to enhance melt flow, adjusting runner systems for reduced resistance and heat loss, and improving exhaust ...
DESIGN
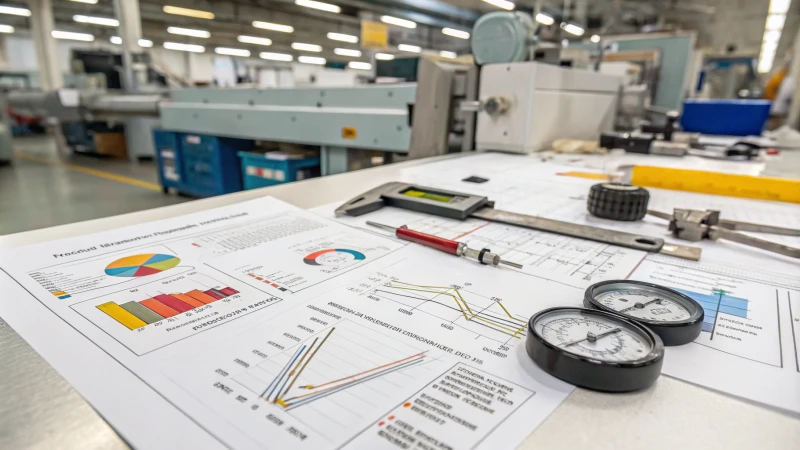
How Can You Identify If Mold Underfilling Is Due to Injection Parameters or Mold Design Issues?
In injection molding, identifying the root cause of mold underfilling is crucial for product quality. This article discusses methods to analyze injection parameters such as speed, pressure, and volume alongside evaluating mold design elements like gate position and runner systems. ...
DESIGN
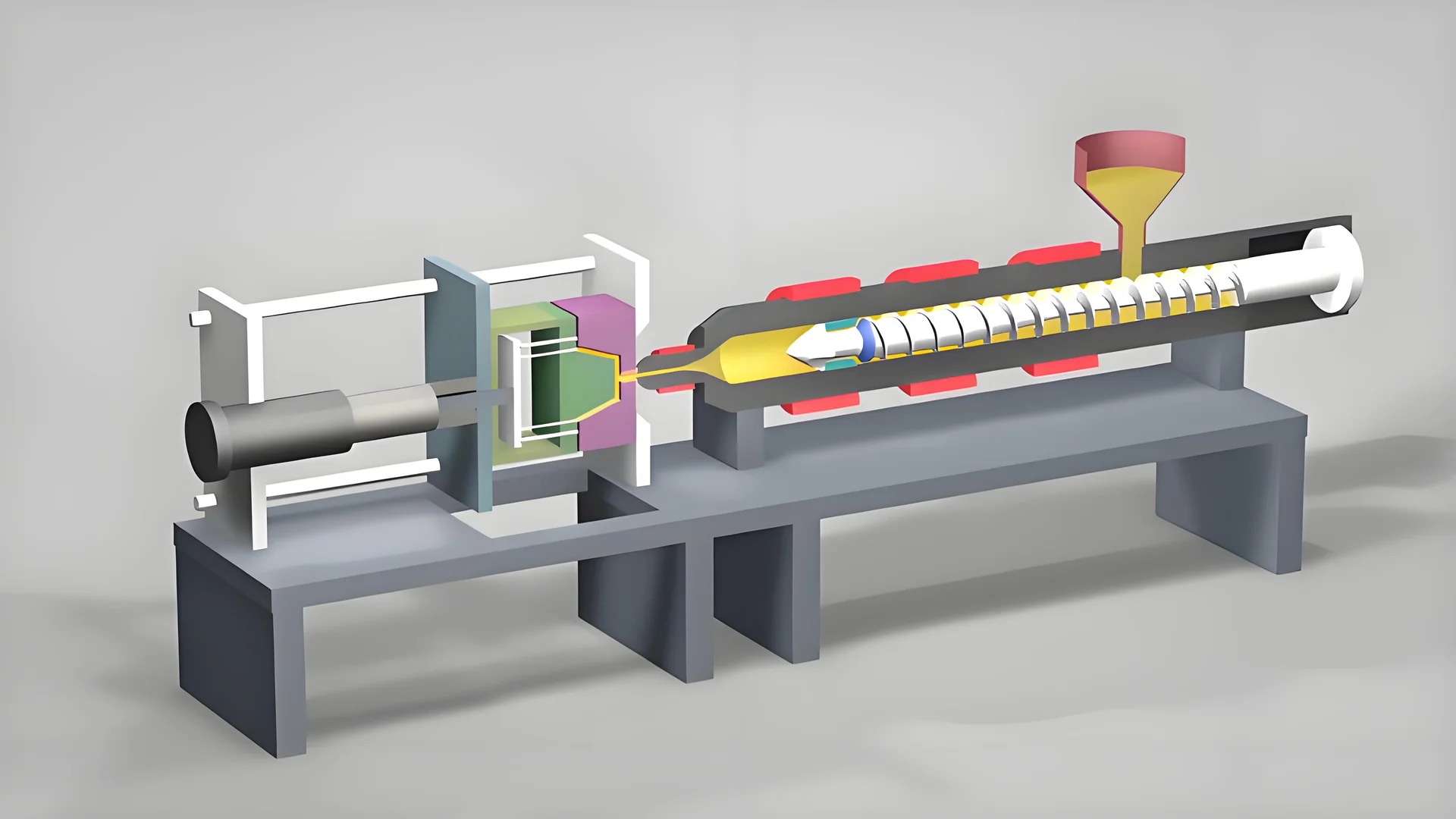
How Does the Tonnage of an Injection Molding Machine Affect Injection Volume?
This article explores how the tonnage of an injection molding machine impacts injection volume. It discusses the relationship between clamping force, mold size, and injection pressure while emphasizing that higher tonnage allows for larger molds and better filling of complex ...
MANUFACTURING

How Does Mold Thickness Impact the Quality of Injection Molded Products?
The thickness of a mold plays a crucial role in the quality of injection molded products. It affects cooling speed, which in turn impacts dimensional accuracy; thicker molds cool more slowly, potentially leading to shrinkage and warping. Additionally, thicker molds ...
MANUFACTURING
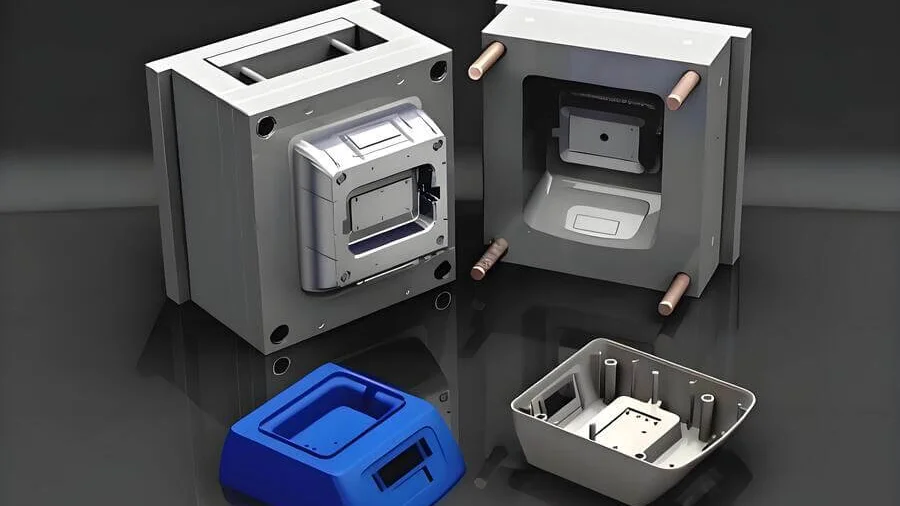
How Does Standard Mold Thickness Affect Injection Molding Process Parameters?
The thickness of a mold plays a critical role in the injection molding process, impacting various parameters such as mold opening stroke, injection pressure, cooling time, and overall product quality. Thicker molds require careful adjustments to ensure smooth operation and ...
MANUFACTURING
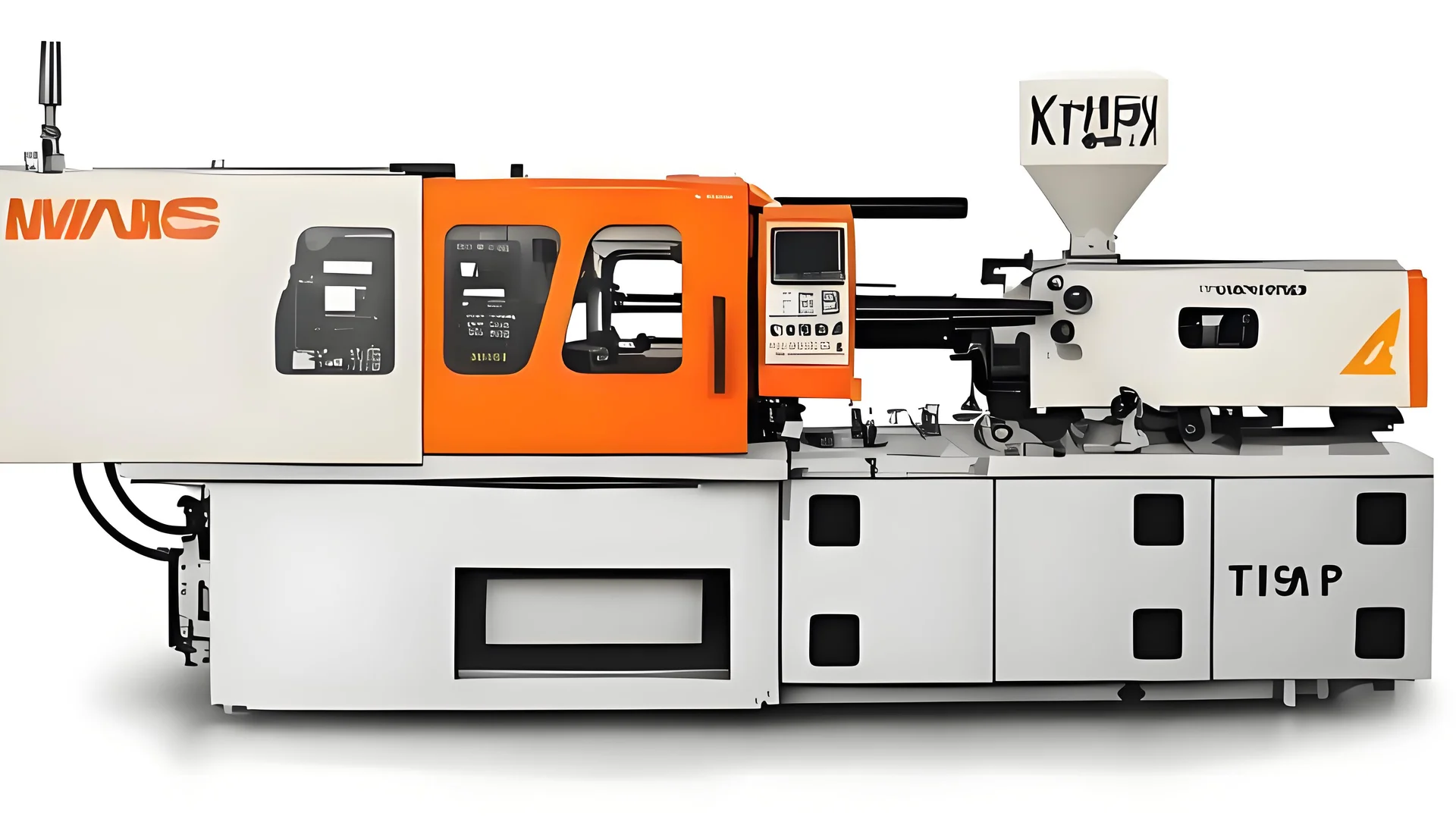
How Does the Tonnage of an Injection Molding Machine Influence the Product Molding Cycle?
This article explores how the tonnage of injection molding machines affects various stages of the molding cycle. It discusses the influence on mold clamping force, opening and closing speeds, injection pressure during filling, holding pressure stability during cooling, and considerations ...
Quality Inspection
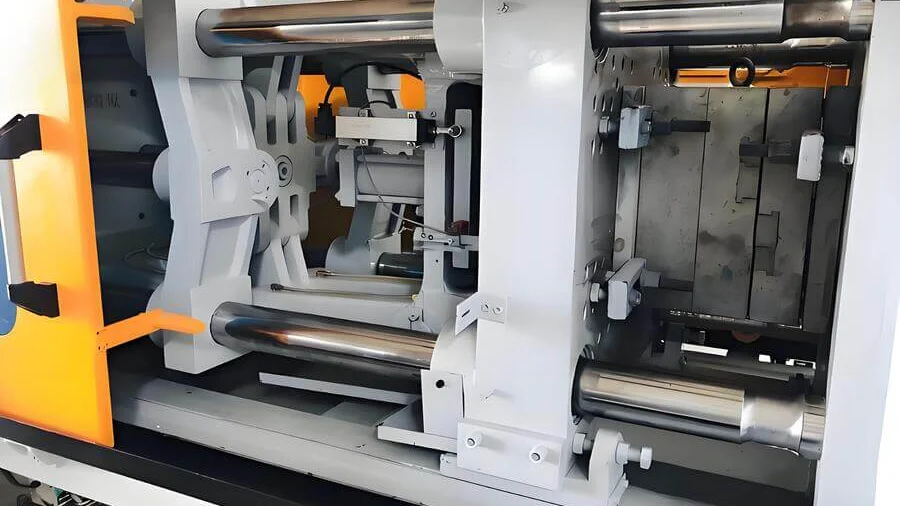
What Are the Key Criteria for Mold Opening Stroke and Mold Thickness Range in Injection Molding Machines?
Selecting the right injection molding machine involves understanding mold opening stroke and thickness ranges. Small machines typically have strokes between 150mm to 650mm and thicknesses from 100mm to 400mm. Medium-sized machines range from 600mm to 1500mm in stroke and can ...
MANUFACTURING
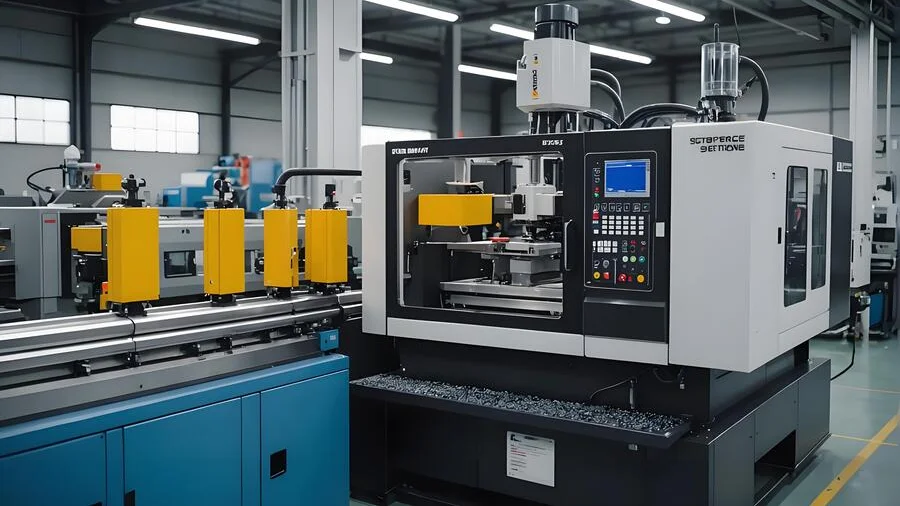
How Can You Enhance Machining Accuracy for Parting Surfaces in Mold Design?
Achieving precision in machining parting surfaces is essential for successful mold design. This article discusses methods to enhance machining accuracy through the use of high-precision CNC machines, appropriate tools such as carbide cutters, and optimization of cutting parameters. Advanced techniques ...
DESIGN

How Does Tonnage Size Impact the Properties of Injection Molded Products?
The tonnage size of injection molding machines plays a vital role in determining the quality of molded products. High tonnage ensures strong clamping force, which is essential for maintaining dimensional accuracy by preventing mold expansion during the injection process. This ...
MANUFACTURING

What Factors Determine the Best Injection Molding Machine for Your Product Size and Weight?
Choosing the right injection molding machine is crucial for manufacturing success. Key factors include product size and weight, which influence clamping force calculations using projected area. Mold size must match machine capacity to ensure smooth production. Additionally, understanding injection volume ...
MANUFACTURING
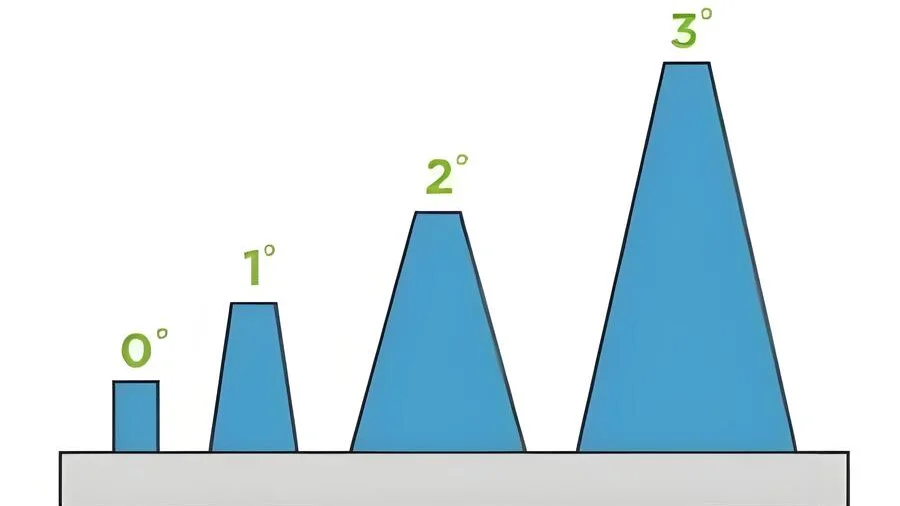
How Can You Ensure Accurate Draft Angles in Mold Design?
This article discusses the importance of accurate draft angles in mold design, emphasizing the use of 3D modeling software like SolidWorks for precise product geometry. It highlights how simulation tools such as Moldflow can predict demolding challenges and optimize draft ...
DESIGN
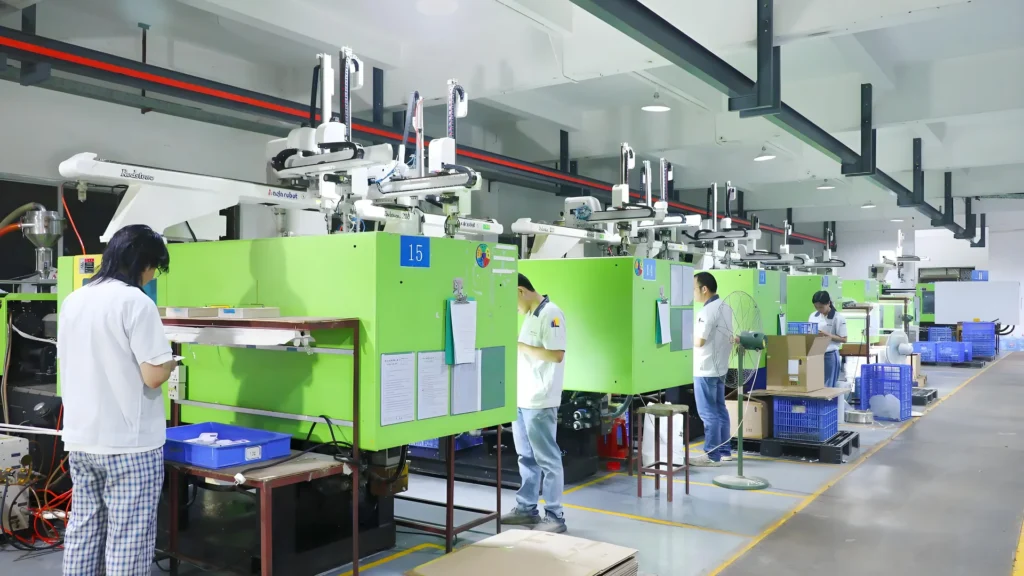
How Do You Select the Right Tonnage for an Injection Molding Machine?
Choosing the correct tonnage for an injection molding machine is crucial for producing high-quality plastic products. Key factors include calculating the projected area of the product to determine necessary clamping force using the formula F = p × A, where ...
MANUFACTURING
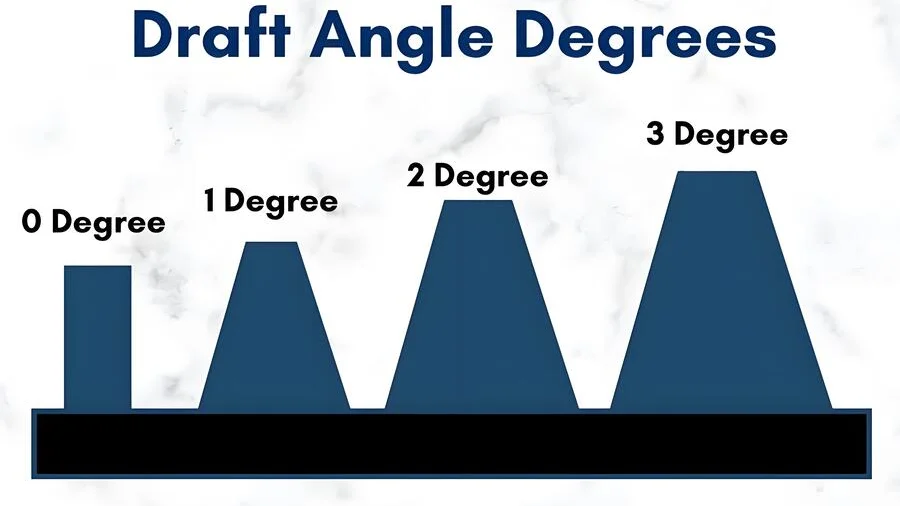
What Factors Determine the Ideal Draft Angle for an Injection Mold?
Determining the ideal draw slope for injection molds involves understanding various factors such as plastic material properties (shrinkage rates and elasticity), product shape complexity, height, and mold structure. Materials like polypropylene require larger slopes due to higher shrinkage rates compared ...
DESIGN
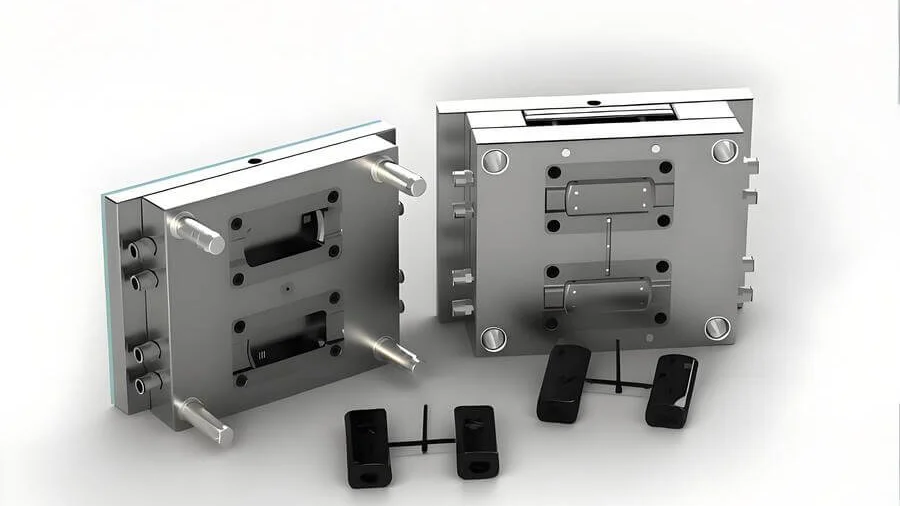
How Does the Angle of the Parting Surface Influence Mold Longevity in Injection Mold Design?
This article explores how the angle of the parting surface in injection molding impacts mold longevity. It highlights the significance of proper fit to minimize wear and fatigue damage caused by uneven pressure distribution and friction during demolding. By optimizing ...
DESIGN
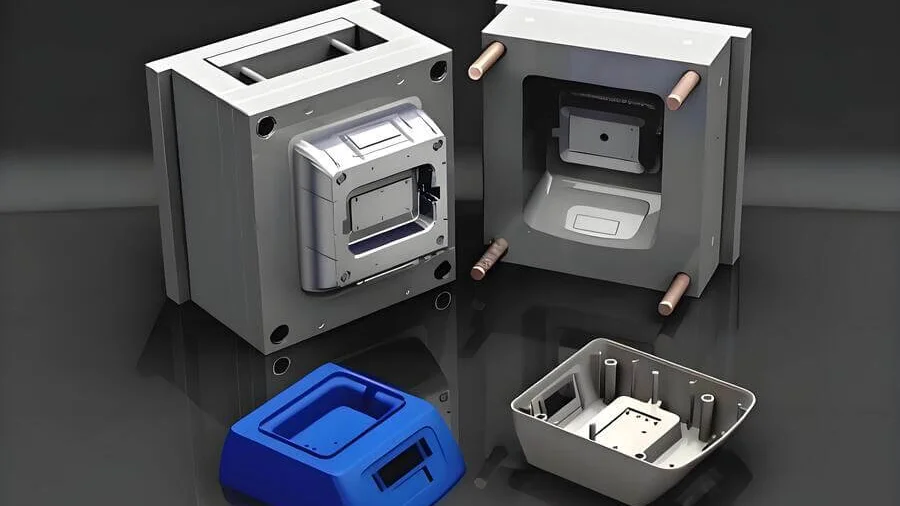
What Is the Best Parting Surface Angle for Optimal Injection Mold Design?
The selection of parting surface angles in injection molding significantly influences product quality and processing efficiency. For simple shapes like flat or cylindrical products, a 0° angle is ideal as it simplifies mold design and ensures easy demolding. In contrast, ...
DESIGN
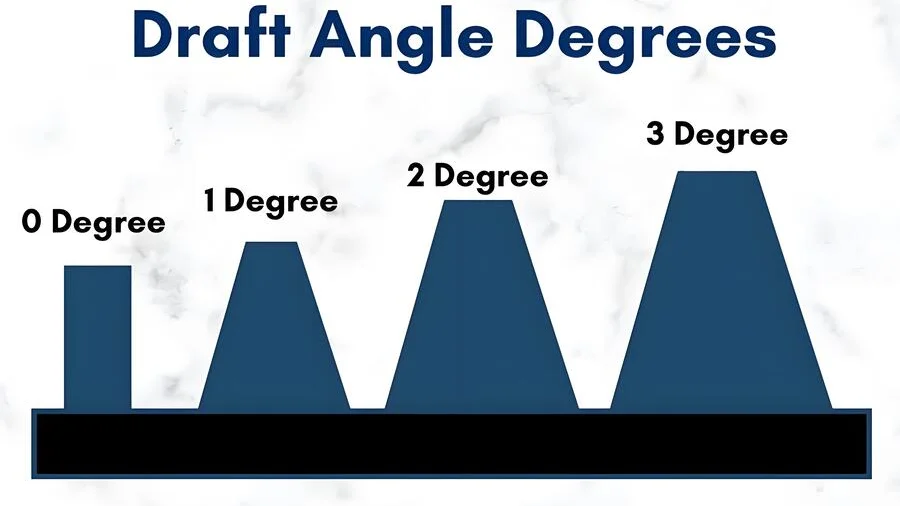
How Do You Measure the Draft Angle of an Injection Mold?
Accurate measurement of the draw slope in injection molds is crucial for producing high-quality parts. This article explores three primary methods: using an angle ruler, trigonometric calculations, and coordinate measuring machines (CMM). Each method varies in precision and suitability depending ...
DESIGN
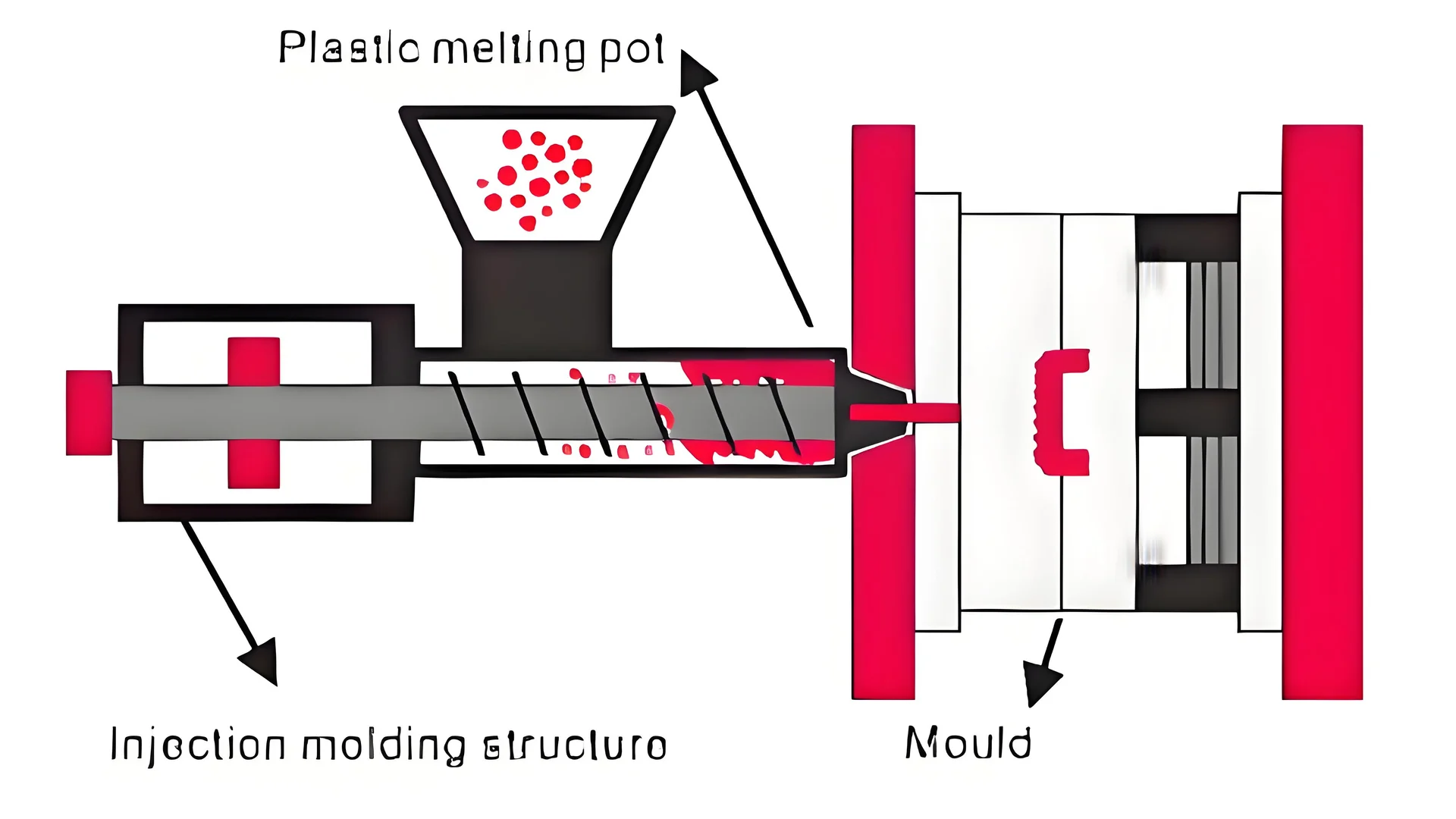
How Do You Choose the Right Injection Molding Machine for Your Product’s Size and Weight?
Selecting the appropriate injection molding machine is crucial for manufacturing efficiency and product quality. Key factors include understanding the projected area for clamping force calculations, ensuring mold size compatibility with machine specifications, and determining injection volume based on product weight ...
MANUFACTURING
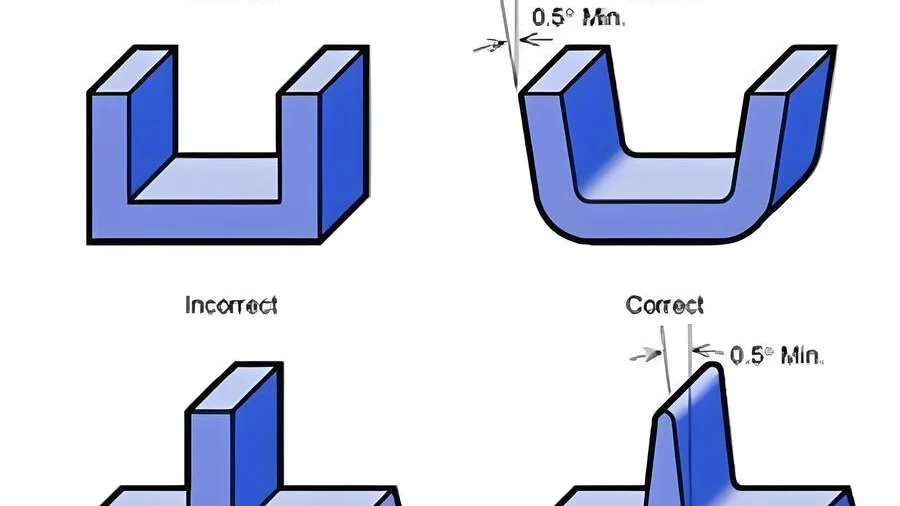
How Does the Parting Surface Angle Influence the Draft Angle in Mold Design?
Understanding the relationship between parting surface angles and draft angles is crucial for effective mold design. The parting surface angle determines the starting direction and effective range of the draft angle, which is essential for ensuring smooth demolding. A well-calculated ...
DESIGN
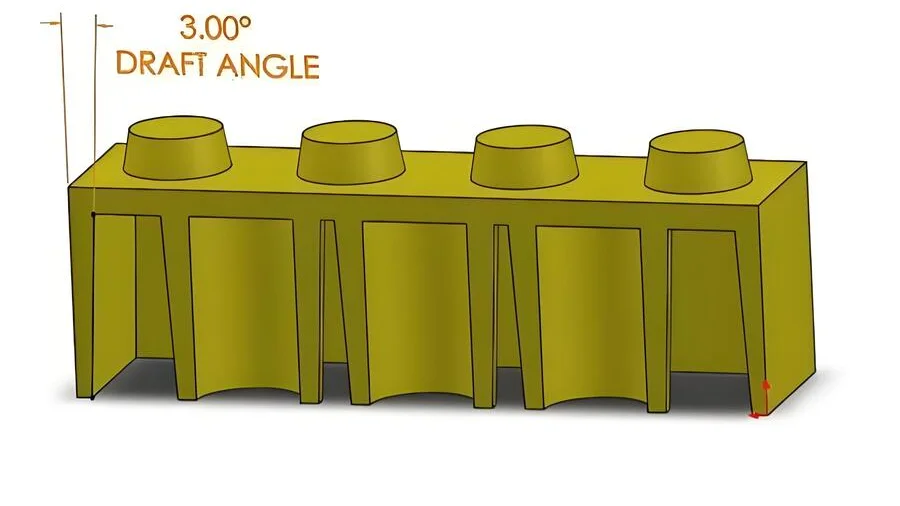
What Are the Standard Specifications for Injection Mold Draft Angle?
Understanding injection mold pullout slopes is crucial in manufacturing. Industry standards dictate specific angles to ensure smooth demolding: ISO suggests 0.5°-1.5° for outer surfaces and 1°-3° for inner surfaces, while the automotive sector mandates stricter requirements of 1°-2° and 2°-4°, ...
DESIGN
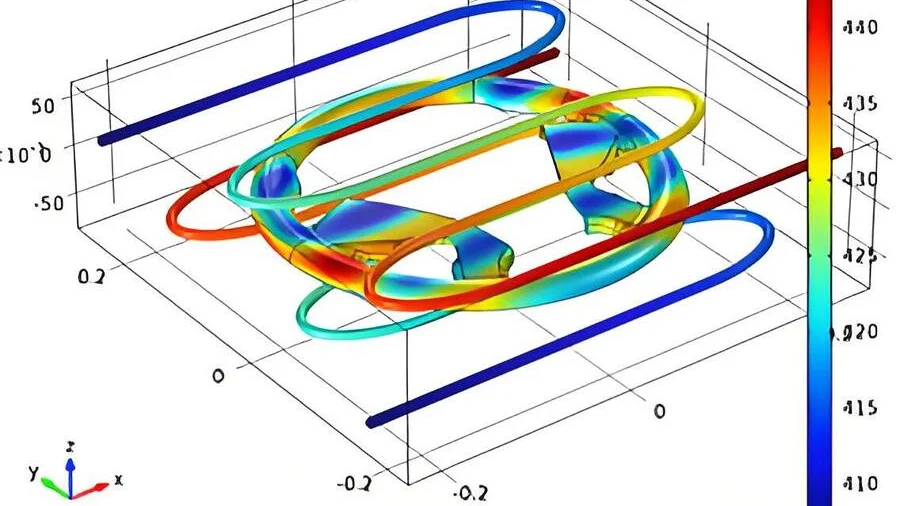
What Factors Determine Excessive Cooling Time in Injection Molds?
This article explores the critical factors affecting excessive cooling times in injection molds. It highlights how product thickness and material type influence cooling duration, which can lead to decreased production efficiency and compromised product quality. For instance, thin-walled parts should ...
MANUFACTURING
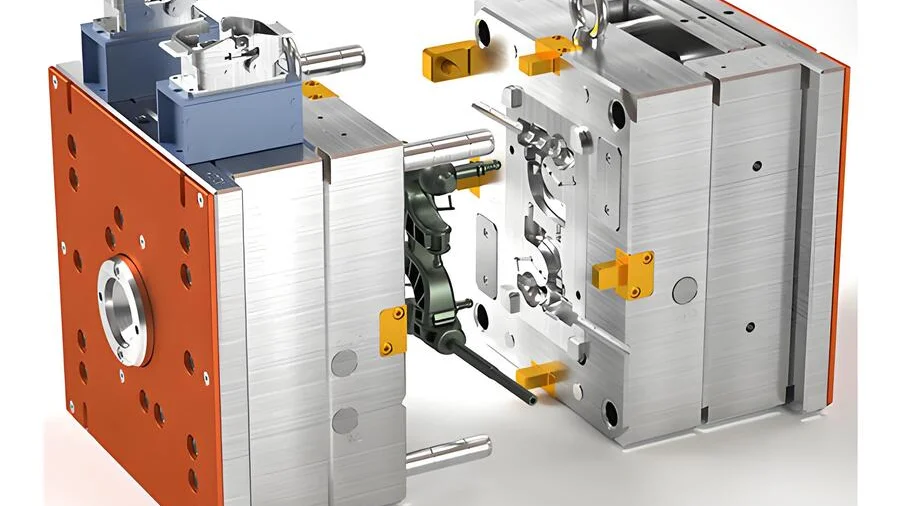
What Factors Should You Consider When Choosing a Mold Surface Treatment Process?
When selecting a mold surface treatment process, several factors must be considered to ensure optimal performance. Key considerations include the wear resistance needed for high-filler materials like glass fiber-reinforced plastics, corrosion resistance for molds used with corrosive plastics such as ...
MANUFACTURING
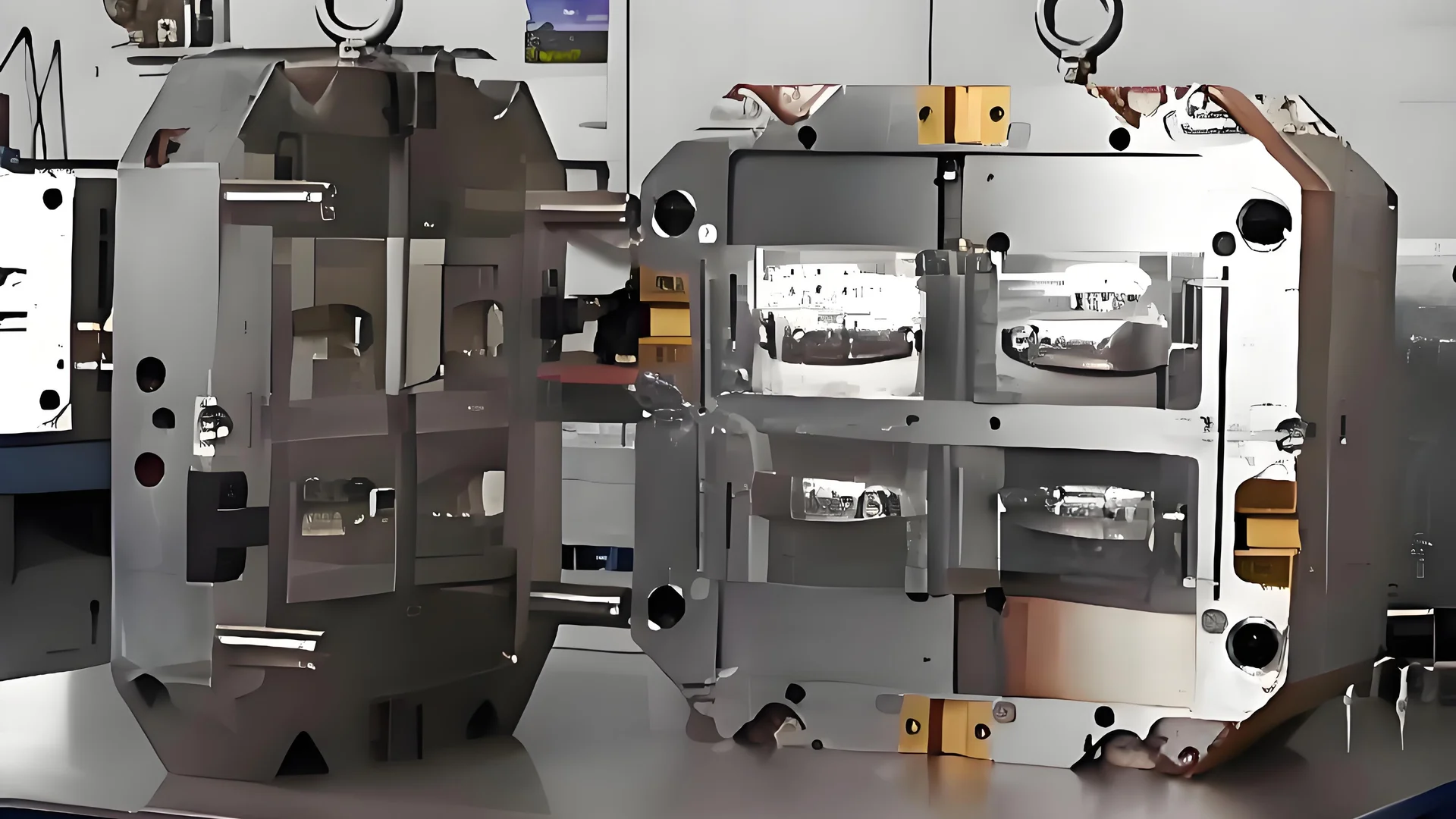
How Much Does Mold Surface Treatment Process Cost?
This article explores the costs associated with various mold surface treatment processes including hand polishing, mechanical polishing, nitriding, chrome plating, titanium plating, and chemical nickel plating. Each method has distinct cost factors such as labor rates for skilled workers in ...
Price Evaluation

What Are the Pros and Cons of Nitriding Injection Molds?
Nitriding is a surface heat treatment process that significantly increases the hardness and wear resistance of injection molds. With surface hardness reaching HV1000-1200 (HRC70), nitrided molds exhibit improved fatigue strength and anti-seize performance while also enhancing corrosion resistance. However, the ...
MANUFACTURING

How Does Nitriding Treatment Enhance Mold Durability?
Nitriding treatment significantly improves mold durability by adding nitrogen to the surface layer, resulting in increased hardness, reduced wear, and enhanced fatigue resistance. The process involves careful preparation of molds through inspection, cleaning, pre-treatment like tempering and de-stressing, followed by ...
MANUFACTURING
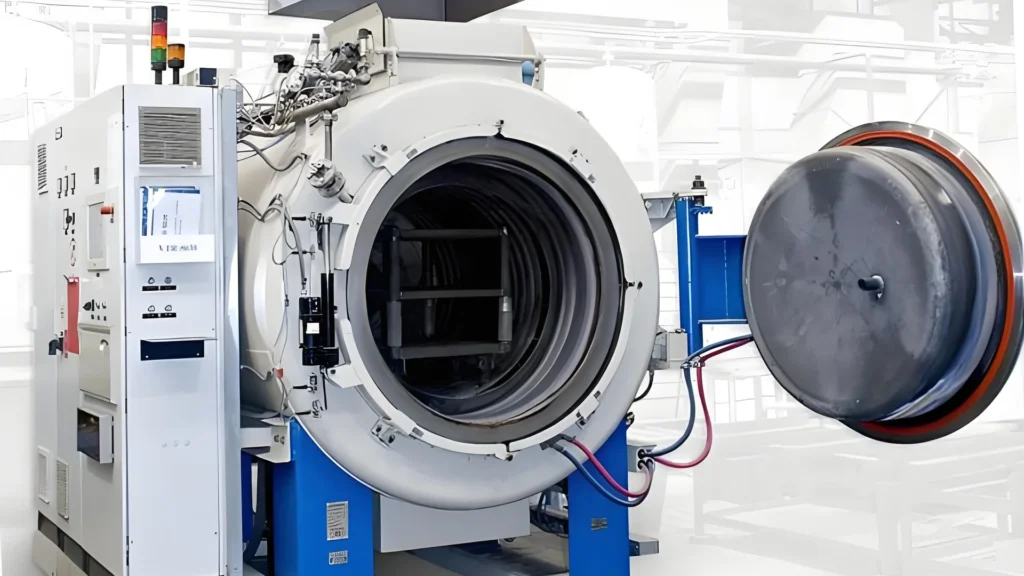
How Expensive is Nitriding for Molds?
Nitriding treatment for molds is costly due to various factors including equipment acquisition and maintenance costs, gas and energy consumption, and skilled labor requirements. Specialized nitriding furnaces can range from thousands to tens of thousands of dollars. Regular maintenance is ...
Price Evaluation
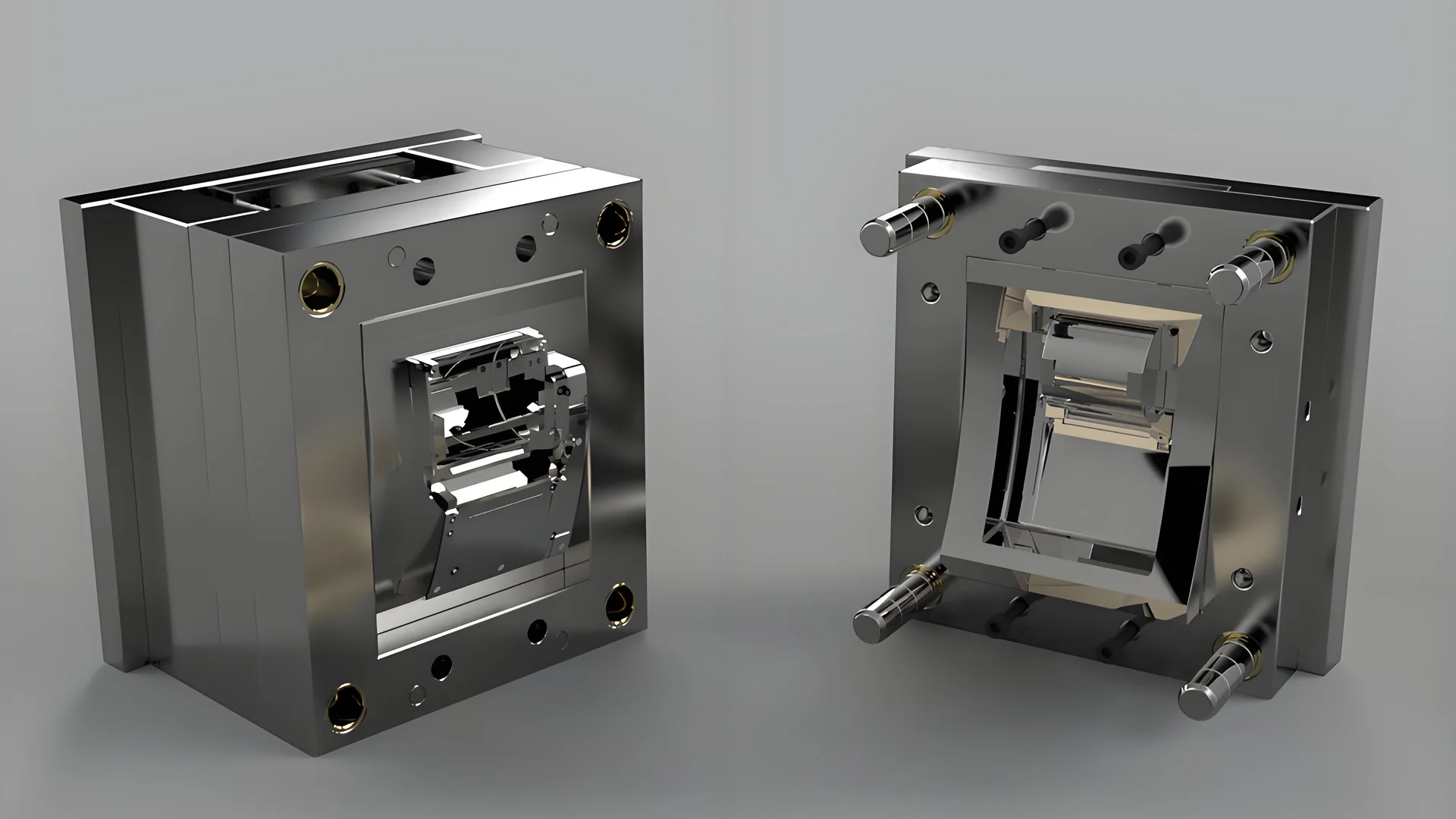
What Are the Applications and Benefits of Nitriding Treatment for Molds?
Nitriding treatment significantly improves the durability and efficiency of molds used in manufacturing. By forming a hard nitride layer on the surface, it enhances wear resistance and extends mold life. This process is particularly beneficial for die-casting aluminum and zinc ...
MANUFACTURING
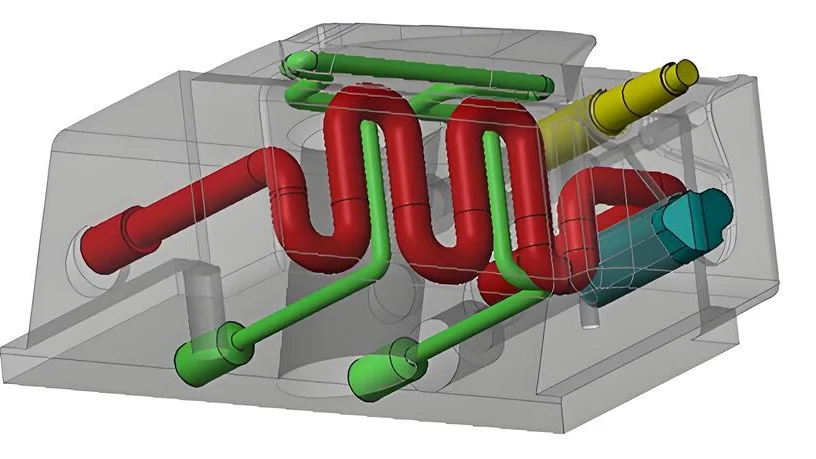
How Do Long Cooling Times Affect Injection Molds?
This article explores the significant impact of long cooling times on injection molding processes. Extended cooling periods lead to reduced production output, increased operational costs, and various quality issues such as dimensional inaccuracies, warping, and surface defects. Additionally, prolonged cooling ...
DESIGN