The three-plate mold is a cornerstone in injection molding, enabling manufacturers to produce complex plastic parts with precision and efficiency. By using a unique three-plate design, this mold type offers flexible gate placement and automatic degating1, making it ideal for industries like automotive, medical, and consumer goods. Understanding the mechanics behind a three-plate mold is essential for leveraging its benefits in your production process.
A three-plate mold consists of three main plates—cavity, core, and runner—allowing for central or multiple gate placements, automatic runner separation, and enhanced part quality, particularly in complex designs.
Mastering the mechanics of a three-plate mold2 can elevate your manufacturing capabilities. Explore the detailed breakdown below to see how this technology can optimize your production.
Three-plate molds reduce production costs.False
While they offer design flexibility, three-plate molds are more complex and costly than simpler alternatives like two-plate molds.
Three-plate molds are only used in high-volume production.False
They are also used in low to medium volumes when specific gate placements or automatic degating are required.
What Is a Three-Plate Mold?
Three-plate molds are a specialized type of injection mold used in plastic manufacturing, offering unique advantages in gate placement and runner separation. Below, we explore their definitions, classifications, and key characteristics.
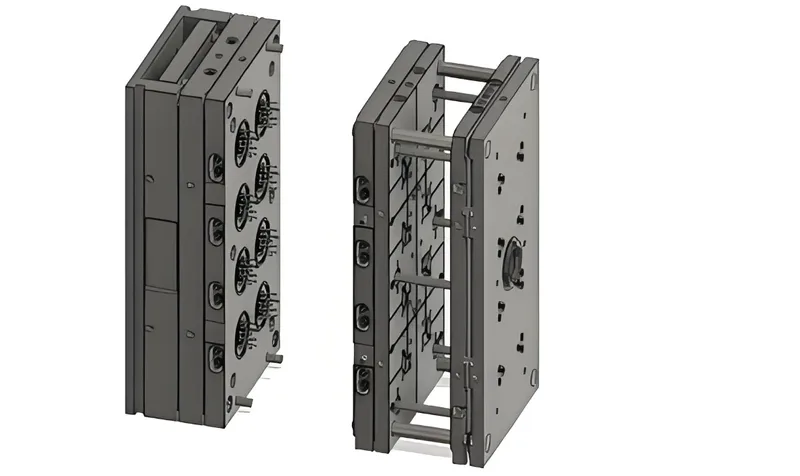
A three-plate mold, also known as a triple plate mold or T-Series mold, consists of three plates—cavity, core, and runner—enabling flexible gate placement3 and automatic degating for complex plastic parts.
Aspect | Details |
---|---|
Full Technical Name | Three-plate injection mold4 |
Common Aliases | Triple plate mold, small gate mold, T-Series mold base |
Core Principle | Uses two parting lines to separate the runner and eject the part automatically |
Classification | – Process: Injection molding – Materials: Thermoplastics (e.g., ABS, polypropylene) – Applications: Automotive, medical, consumer goods |
Key Features
-
Flexible Gate Placement: Allows central or multiple gates, reducing defects like weld lines.
-
Automatic Degating: Separates the runner from the part during the mold opening, minimizing manual labor.
-
Complexity: More intricate than two-plate molds, requiring precise alignment and maintenance.
Three-plate molds are ideal for parts where gate marks on sidewalls are undesirable, such as in medical devices or aesthetic consumer products Plastics Technology.
Three-plate molds are essential for all injection molding projects.False
They are best suited for specific applications requiring flexible gating or automatic degating, not for all projects.
Three-plate molds enhance part quality in complex designs.True
Their flexible gate placement reduces defects and improves surface finish.
When Should You Use a Three-Plate Mold?
Choosing the right mold type is crucial for optimizing production. Three-plate molds offer distinct advantages but also come with trade-offs. Below, we explore typical application scenarios and compare their pros and cons with other mold types.
Three-plate molds are ideal for parts requiring central or multiple gates, automatic degating, or high-quality surface finishes, commonly used in automotive, medical, and consumer goods industries.

Typical Application Scenarios
-
Central Gating: Essential for parts like caps or medical devices to avoid weld lines and ensure uniform filling.
-
Multiple Gates: Used in large or complex parts (e.g., automotive components) for balanced material flow.
-
Automatic Degating: Reduces labor in high-volume production, such as packaging components General Plastic.
Pros and Cons Comparison
Mold Type | Pros | Cons |
---|---|---|
Three-Plate Mold | – Flexible gate placement – Automatic degating – Better surface finish |
– Higher cost – Longer cycle times – More complex maintenance |
Two-Plate Mold | – Lower cost – Simpler design – Shorter cycle times |
– Limited gate placement – Manual runner removal |
Hot Runner Mold | – No cold runner waste – Flexible gating |
– High cost – Complex heating systems |
Three-plate molds strike a balance between flexibility and cost, making them a middle-ground option for manufacturers needing specific design features without the expense of hot runner systems Prototool.
Three-plate molds are more cost-effective than two-plate molds.False
They are generally more expensive due to their complexity and additional components.
Three-plate molds reduce manual labor in production.True
Automatic degating eliminates the need for manual runner removal.
How Does a Three-Plate Mold Work?
Understanding the workflow of a three-plate mold is key to leveraging its benefits. Below, we break down the process and discuss material compatibility5.
The three-plate mold process involves clamping, injection, cooling, and a two-stage opening for automatic runner separation and part ejection, with key parameters like injection pressure6 and cooling time7.

Process Workflow Breakdown
-
Clamping: The three plates (cavity, core, runner) are closed, forming a sealed cavity. Clamping force8 is critical (e.g., 500 tons for large molds).
-
Injection: Molten plastic is injected through the runner plate. Injection pressure (e.g., 1000-2000 psi) and temperature (e.g., 200-300°C for ABS) must be optimized.
-
Cooling: The plastic cools and solidifies. Cooling time (e.g., 10-30 seconds for polypropylene) is controlled by cooling channels.
-
First Opening: The runner plate separates, stripping the cold runner.
-
Second Opening: The core plate separates, ejecting the part via ejector pins Mechanicaleng Blog.
Material Compatibility
Three-plate molds work with various thermoplastics, but material properties impact the process:
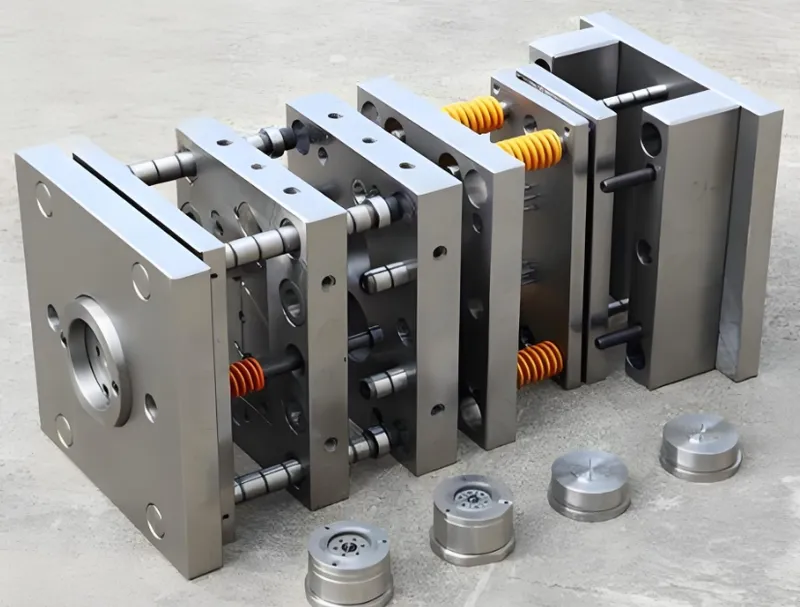
-
Flow Properties: High-viscosity materials (e.g., polycarbonate) may require higher injection pressure.
-
Shrinkage Rates: Materials like polypropylene (1-2% shrinkage) need precise cooling to prevent warpage Boyan Manufacturing Solutions.
Three-plate molds require longer cycle times than two-plate molds.True
The two-stage opening process increases cycle time compared to single-stage molds.
Material choice does not affect three-plate mold performance.False
Different materials require adjustments in parameters like injection pressure and cooling time.
What Are the Key Considerations for Designing a Three-Plate Mold?
Designing a three-plate mold requires careful planning to ensure efficiency and cost-effectiveness. Below, we provide a design checklist and a decision-making guide.
Key considerations include gate placement, runner design, ejection system, and production volume, with a checklist to avoid common pitfalls and a decision tree for mold selection.
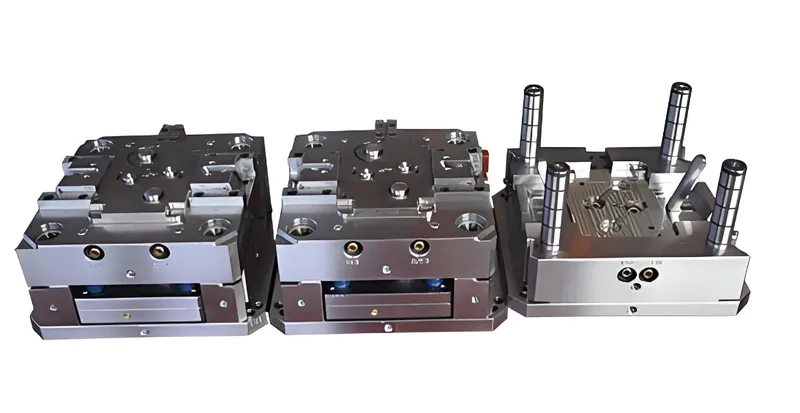
Design Checklist
-
Necessity Check: Confirm if flexible gating or automatic degating is required; otherwise, use a two-plate mold.
-
Mold Base: Select a T-Series mold base for the runner stripper plate.
-
Parting Lines: Define two parting lines for runner stripping and part ejection.
-
Runner System: Design for clean stripping; typical runner diameter: 3-6 mm.
-
Gating: Use pin-point gates (0.5-2 mm) for small parts.
-
Ejection: Ensure robust ejection with pins (2-5 mm diameter).
-
Cooling: Design efficient channels (10-15 mm spacing) to reduce cycle time.
-
Maintenance: Use wear-resistant materials (e.g., SKD61) for pins.
-
Cost vs. Volume: Evaluate if production volume justifies the mold’s complexity.
Process Selection Decision-Making
Use this decision tree to choose the right mold:
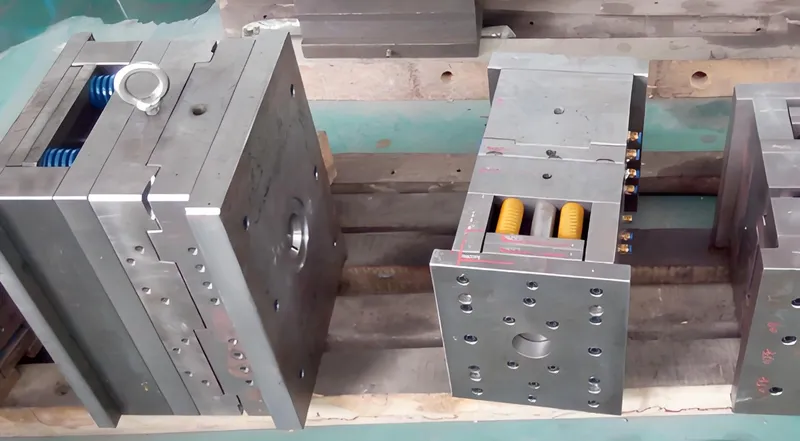
-
Step 1: Does the part require specific gate placement? If yes, consider three-plate or hot runner mold.
-
Step 2: Is production volume high? If yes, three-plate mold may be cost-effective.
-
Step 3: Can you afford higher upfront costs? If no, consider two-plate mold.
-
Step 4: Do you need automatic degating? If yes, three-plate mold is ideal FOW Mould.
Three-plate molds are always the best choice for complex parts.False
They are ideal for specific needs but may be overkill for simpler designs.
Proper design can minimize maintenance issues in three-plate molds.True
Using wear-resistant materials and efficient cooling systems reduces downtime.
Three-plate molds are part of a broader ecosystem of injection molding technologies. Below, we explore related upstream and downstream technologies.
Related technologies include material development, part design software9, hot runner molds10, stack molds, and insert molding, each enhancing or complementing three-plate mold capabilities.
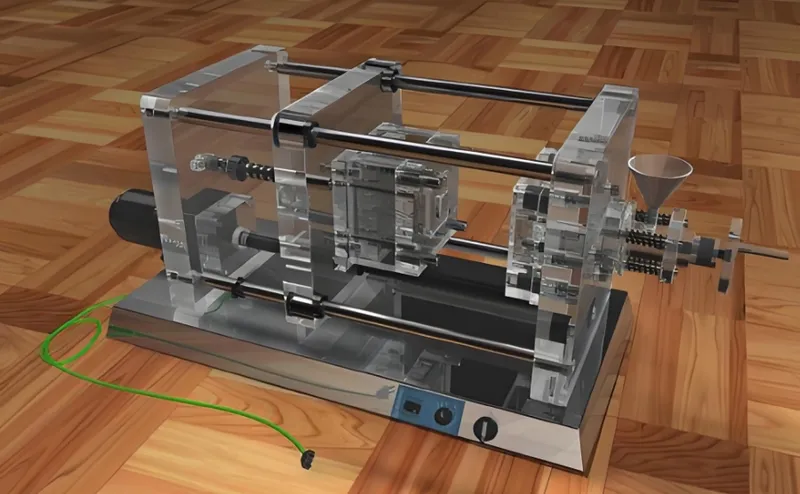
Upstream Technologies
-
Material Development: Innovations in bio-based plastics impact mold compatibility.
-
Part Design Software: Tools like Moldflow optimize designs for three-plate molds.
Downstream Technologies
-
Hot Runner Molds: Offer flexible gating without cold runners, ideal for high-volume production.
-
Stack Molds: Increase output by using multiple levels, complementing three-plate designs.
-
Insert Molding: Allows molding around inserts, often requiring specific gate placements ACO Mold.
Three-plate molds are obsolete due to newer technologies.False
They remain relevant for specific applications where cost and design flexibility are balanced.
Understanding related technologies enhances three-plate mold efficiency.True
Integrating upstream and downstream technologies optimizes production.
Conclusion
Three-plate molds are a powerful tool in injection molding11, offering unparalleled flexibility in gate placement and automatic degating for complex parts. While they come with higher costs and complexity, their benefits in part quality12 and labor reduction make them indispensable in industries like automotive, medical, and consumer goods. By understanding their mechanics and applications, manufacturers can make informed decisions to optimize production.
-
Explore the concept of automatic degating to understand its role in minimizing manual labor and enhancing production efficiency. ↩
-
Discover the unique benefits of three-plate molds in injection molding, enhancing production efficiency and part quality. ↩
-
Learn how flexible gate placement can reduce defects and improve the quality of molded parts in manufacturing. ↩
-
Explore the benefits of three-plate injection molds to understand their applications and advantages in manufacturing. ↩
-
Discover the types of materials that work best with three-plate molds for optimal production results. ↩
-
Understanding injection pressure is crucial for optimizing the molding process and ensuring quality parts. Explore this link for detailed insights. ↩
-
Cooling time directly influences the final product’s quality. Discover more about its impact and optimization techniques in this resource. ↩
-
Understanding clamping force is essential for optimizing the injection molding process and ensuring product quality. ↩
-
Discover top software tools that can enhance your mold design process and improve production outcomes. ↩
-
Learn how hot runner molds can streamline your production process and reduce waste in manufacturing. ↩
-
Discover cutting-edge techniques and innovations in injection molding that can enhance your production efficiency and part quality. ↩
-
Explore the critical elements that affect part quality in injection molding to ensure optimal production outcomes. ↩