In plastic part design, screw bosses1 are essential features that provide secure fastening points for screws, ensuring sturdy and reliable assemblies. These cylindrical protrusions are widely used in industries like electronics, automotive, and consumer goods.
A screw boss is a cylindrical protrusion on a plastic part designed to accept a screw, offering a reinforced fastening point for assembly. Effective design enhances strength, manufacturability, and compatibility with the material and screw type.
Mastering the design of screw bosses can improve product durability2 and streamline manufacturing. This guide outlines the key steps to creating an effective screw boss, from material selection to reinforcement techniques.
Screw bosses are only used in plastic parts.False
While prevalent in plastics, screw bosses can also be designed in metal or composite parts, though with different considerations.
A well-designed screw boss can improve assembly efficiency.True
Proper design reduces defects and ensures smooth screw insertion, speeding up assembly processes.
What is a Screw Boss and Why is it Important?
A screw boss is a raised, cylindrical feature molded into a plastic part to serve as a mounting point for screws. It reinforces the area around the screw, preventing the material from cracking or deforming under stress. Screw bosses are critical in applications like enclosures, brackets, and panels where secure fastening is required.
Screw bosses strengthen fastening points in plastic assemblies3, ensuring durability and preventing damage during screw insertion.
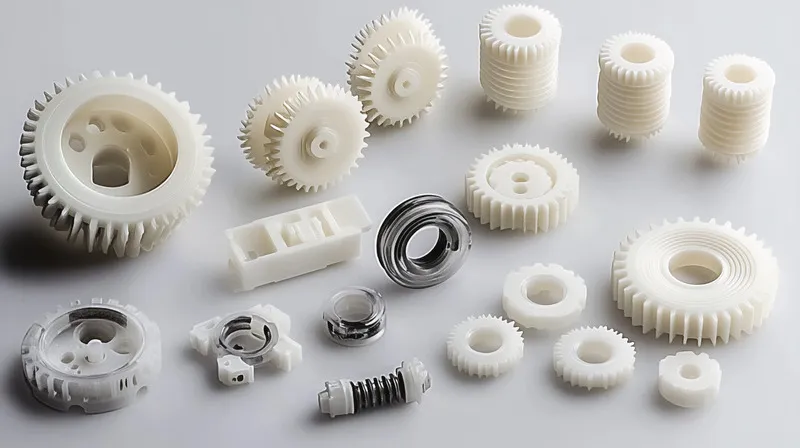
A poorly designed screw boss can lead to manufacturing issues4 like sink marks or assembly failures like cracking. Conversely, a well-designed boss enhances both the part’s performance and production efficiency.
Screw bosses are only needed for large screws.False
Screw bosses accommodate screws of all sizes, ensuring a secure fit tailored to the application’s needs.
What Are the Key Steps to Designing an Effective Screw Boss?
Designing a screw boss involves balancing material properties5, screw specifications, and manufacturing constraints to achieve a robust and practical feature.
Key steps include selecting the material, sizing the boss for the screw, placing it strategically, adding draft angles, sizing the hole accurately, and reinforcing it as needed.
Below, we break down these steps with practical insights and guidelines.
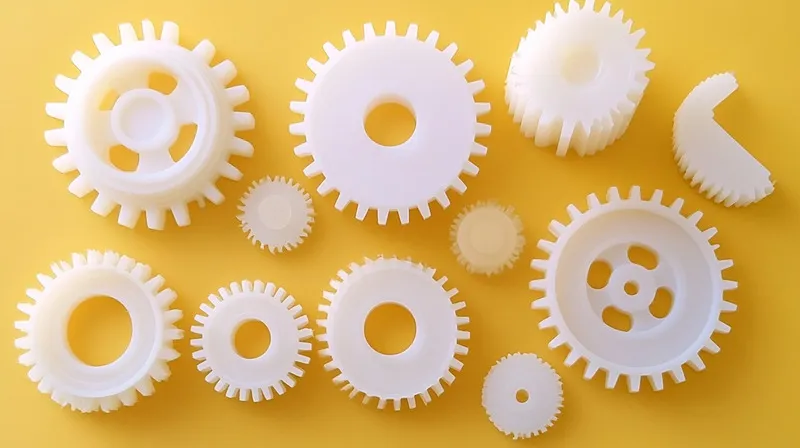
1. Material Consideration
The material of the plastic part dictates many aspects of screw boss design6. Different plastics have unique properties that affect strength, flexibility, and brittleness.
- Popular Choices: Common thermoplastics7 include ABS (good strength and flexibility), polycarbonate (brittle, needs thicker walls), and nylon (wear-resistant but prone to deformation).
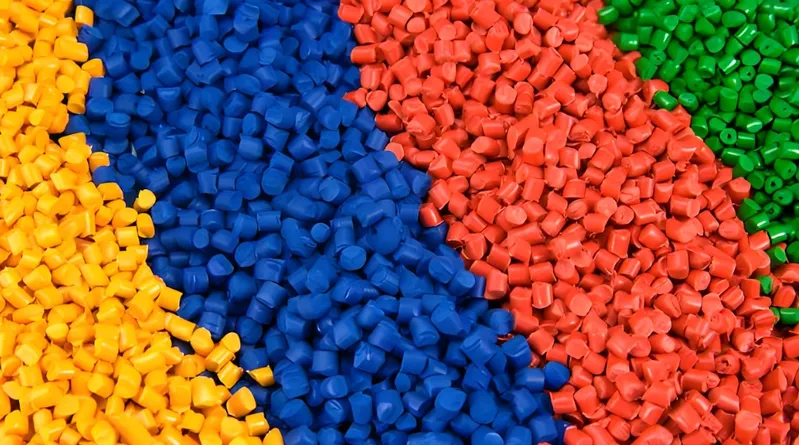
- Design Adjustments: Brittle materials like polycarbonate may require a thicker boss to avoid cracking, while flexible materials like nylon need careful sizing to prevent stretching.
For detailed material properties, explore MatWeb.
ABS is the best material for all screw boss applications.False
ABS is versatile, but the ideal material varies by application, depending on factors like temperature or chemical exposure.
2. Screw Size and Boss Dimensions
The screw boss must be sized to match the screw it will hold, ensuring sufficient material for strength without excess bulk.
-
Diameter: The boss’s outer diameter should be 2-3 times the screw’s diameter.
-
Height: The boss height should at least equal the screw’s engagement length for a secure hold.
Screw Size | Recommended Boss Diameter (mm) |
---|---|
#4 | 5.0 – 7.5 |
#6 | 7.0 – 10.5 |
#8 | 9.0 – 13.5 |
#10 | 11.0 – 16.5 |
Adjust these dimensions based on material strength and specific needs.
The boss height must equal the screw’s full length.False
The height should match the screw’s engagement length, not its total length, to ensure proper thread engagement.
3. Strategic Placement
Where the screw boss is placed affects both its performance and the part’s manufacturability.
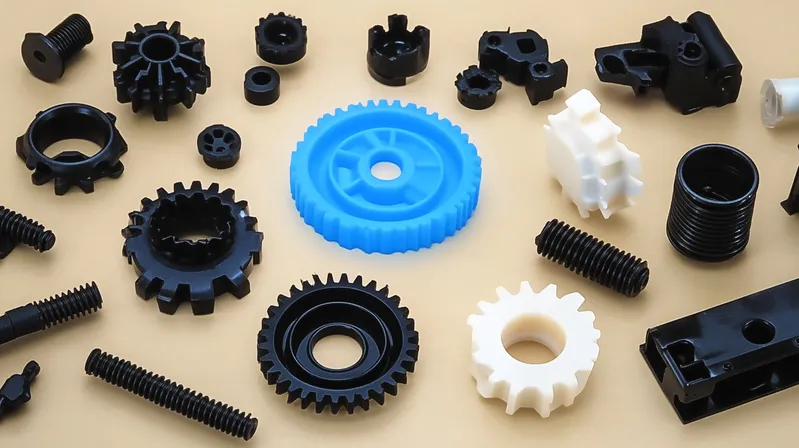
-
Support Structures: Position the boss near walls or ribs for added strength.
-
Avoid Weak Spots: Steer clear of thin areas to prevent sink marks or warping.
-
Accessibility: Ensure the boss is reachable for screw insertion during assembly.
For example, in a plastic housing, corner placement can evenly distribute stress.
Screw bosses must always be near a wall for support.False
While often helpful, freestanding bosses can work if reinforced properly.
4. Incorporating Draft Angles
draft angles8 are vital for injection-molded parts, allowing easy removal from the mold.
-
Angle Range: A draft of 0.5 to 1 degree is typically sufficient for screw bosses.
-
Application: Apply to both the outer surface and the inner hole (if present).
5. Hole Sizing
The hole in the boss must be tailored to the screw type and material properties.
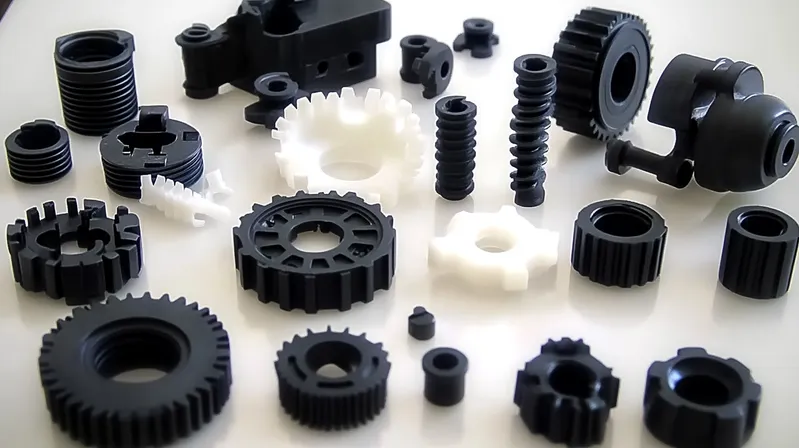
-
Self-Tapping Screws: Size the hole slightly smaller than the screw’s outer diameter for thread cutting.
-
Machine Screws: Match the hole to the screw’s minor diameter for pre-threaded fits.
Check screw manufacturer specs, like those from Fastenal, for precise dimensions.
The hole for self-tapping screws should match the screw’s outer diameter.False
It should be smaller to allow the screw to cut threads effectively.
6. Reinforcement Techniques
For high-stress applications, reinforcing the boss enhances its durability.
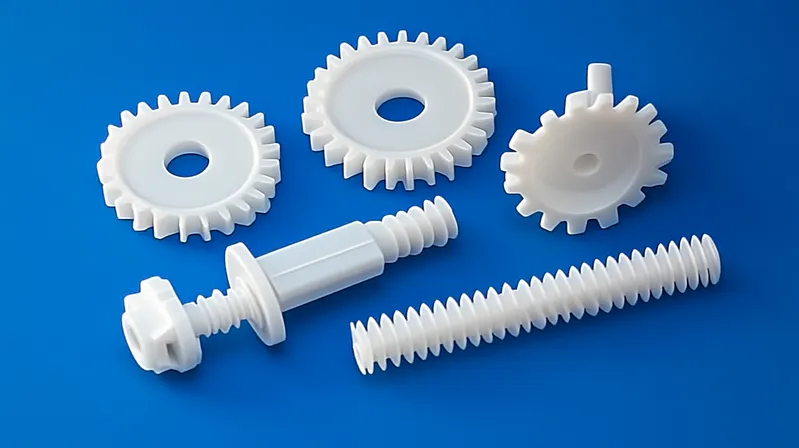
-
Ribs: Add 3-4 ribs radiating from the boss to spread the load.
-
Gussets: Use triangular supports to connect the boss to nearby walls.
Ribs always improve a screw boss’s strength.True
Well-designed ribs distribute stress, boosting the boss’s load capacity.
How Do Screw Bosses Compare to Other Fastening Methods?
Screw bosses aren’t the only way to join plastic parts. Here’s how they stack up against alternatives:
Screw bosses offer secure, removable fastening, while snap-fits provide quick assembly, and adhesives deliver permanent bonds. The best choice depends on the application.
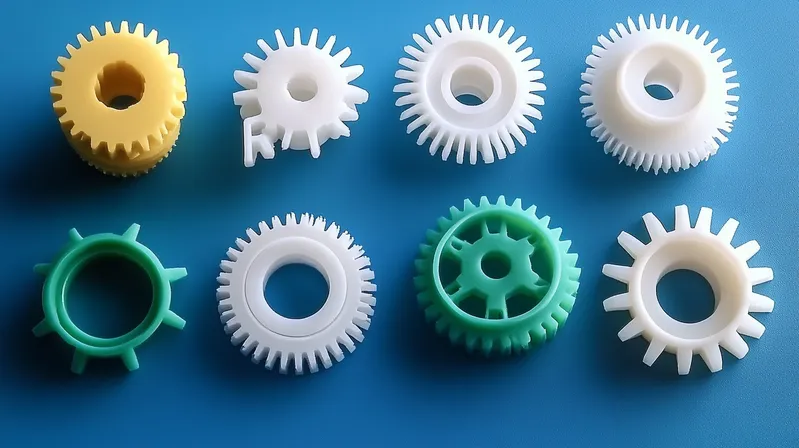
-
Screw Bosses: Strong and detachable, ideal for frequent disassembly.
-
Snap-Fits: Fast and tool-free, suited for lightweight, permanent joins.
-
Adhesives: Permanent and hardware-free, but messy and slow to apply.
Screw bosses are the cheapest fastening option.False
Cost varies by design and process; snap-fits may be more economical for simple parts.
What Are Common Mistakes to Avoid?
Avoid these pitfalls to ensure a successful screw boss design:
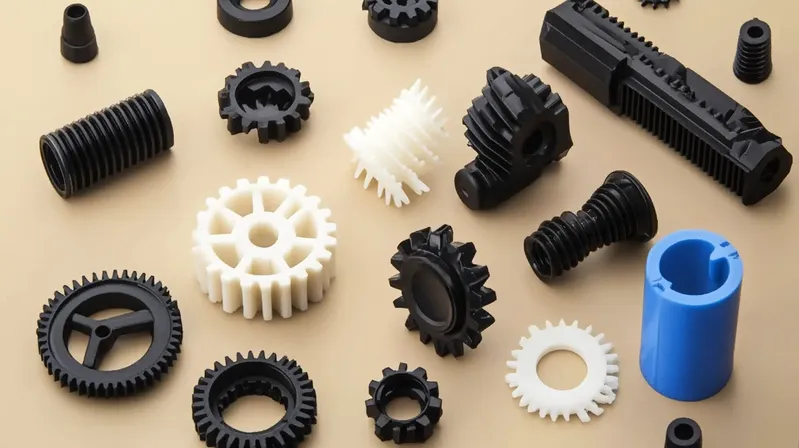
-
Too Thin: A thin boss risks cracking or stripping.
-
Wrong Hole Size: Too large reduces grip; too small causes binding.
-
No Draft Angle: Complicates mold release and damages the boss.
-
Poor Placement: Weak areas lead to deformation or sink marks.
A poorly designed screw boss can cause assembly issues.True
Defects like cracking or stripping can weaken the entire assembly.
Conclusion
Designing an effective screw boss is a blend of science and strategy, requiring careful attention to material, screw size, placement, draft angles, hole sizing, and reinforcement. By following these steps, you can create screw bosses that enhance product reliability and simplify manufacturing. Prototyping or simulation tools can further refine your design, catching issues before production.
-
Understanding screw bosses is crucial for effective plastic part design, ensuring strong and reliable assemblies. ↩
-
Learning about product durability can help you create long-lasting and reliable plastic components. ↩
-
Explore how screw bosses enhance the durability and performance of plastic assemblies in various applications. ↩
-
Learn about potential pitfalls in screw boss design to avoid costly manufacturing errors. ↩
-
Material properties are crucial in design; learn how they influence strength and flexibility for better outcomes. ↩
-
Understanding screw boss design can enhance your product’s durability and functionality. Explore expert insights and guidelines. ↩
-
Discover the various thermoplastics and their unique properties to make informed material choices for your designs. ↩
-
Understanding draft angles is crucial for ensuring smooth mold release and high-quality injection-molded parts. Explore this resource for detailed insights. ↩