Injection mold making1 is a critical process in manufacturing, enabling the production of precise plastic parts for industries like automotive, electronics, and medical devices. The essential tools2 for this process include software for design, machines for shaping, and components for mold functionality. Understanding these tools is key to optimizing the mold-making process and ensuring high-quality results.
Key Points:
-
Essential tools include CAD software, CNC machines, mold bases, inserts, ejector pins, cooling systems, measuring instruments, and mold components3 like core, cavity, gates, runners, and sprue bushes.
-
These tools enable the design, machining, and assembly of molds for high-volume production.
-
Tool selection impacts cost, quality, and efficiency, requiring careful consideration based on production needs.
Injection mold making is vital for precision manufacturing.True
It allows for the creation of complex, high-accuracy plastic parts essential to multiple industries.
All tools are interchangeable in mold making.False
Each tool has a specific role, and substitutions can compromise quality or efficiency.
- 1. What Are the Key Tools in the Design Phase of Injection Mold Making?
- 2. What Tools Are Used in the Machining Phase of Injection Mold Making?
- 3. What Are the Essential Components in the Assembly Phase of Injection Mold Making?
- 4. How Do Measuring Instruments Ensure Quality in Injection Mold Making?
- 5. What Are the Core Components of an Injection Mold?
- 6. How Do You Choose the Right Tools for Injection Mold Making?
- 7. Conclusion
What Are the Key Tools in the Design Phase of Injection Mold Making?
The design phase lays the groundwork for a successful mold, relying on advanced software to create precise models.
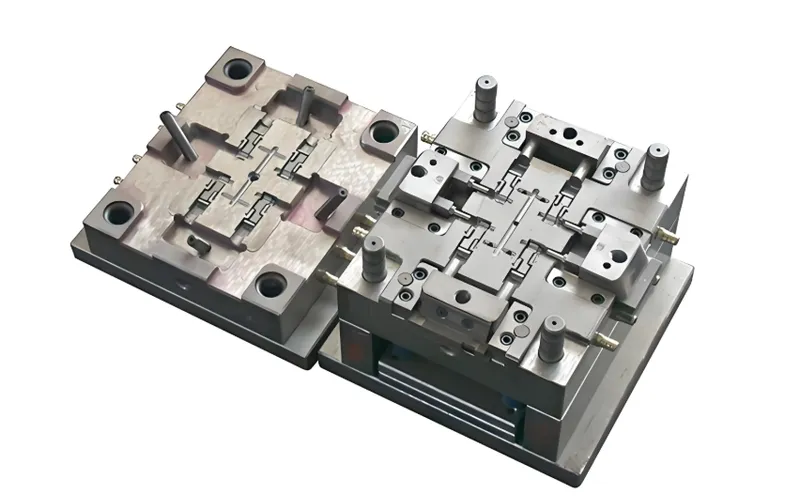
CAD software4 is the backbone of mold design, allowing engineers to create detailed 3D models and simulate the molding process.
Tool | Purpose | Notes |
---|---|---|
CAD Software | Design and simulation | Essential for precision |
Moldflow Analysis5 | Predicts material flow | Enhances mold performance |
CAD Software
CAD (Computer-Aided Design) software enables engineers to craft detailed 3D models of molds, including the core, cavity, runners, and gates. It facilitates simulation of the injection process, helping to identify issues like air traps or weld lines before production. Popular options include SolidWorks, AutoCAD, and Moldflow.
CAD software reduces design errors and improves efficiency.True
Simulations and visualizations allow engineers to address issues early, saving time and resources.
For more on CAD in mold design, see this article.
What Tools Are Used in the Machining Phase of Injection Mold Making?
The machining phase transforms designs into physical components, demanding high precision and reliability.
CNC machines are essential for shaping mold components with accuracy and consistency.
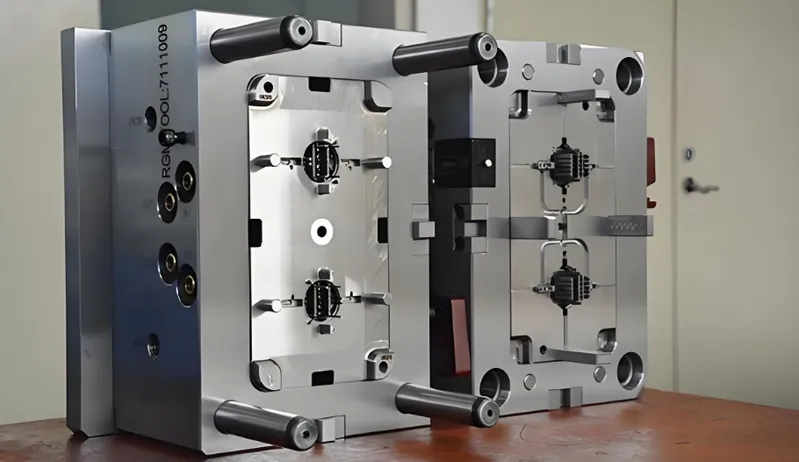
CNC Machines
CNC (Computer Numerical Control) machines cut and shape metal—typically steel or aluminum—to exact specifications based on CAD designs. They achieve tight tolerances (e.g., ±0.002 mm), ensuring components fit perfectly and endure injection molding pressures.
CNC machining ensures high precision in mold components.True
Automation allows repeatable, accurate cuts critical for mold durability and part quality.
Learn more about CNC machining in mold making at this guide.
What Are the Essential Components in the Assembly Phase of Injection Mold Making?
The assembly phase integrates components into a functional mold, each contributing to stability and performance.
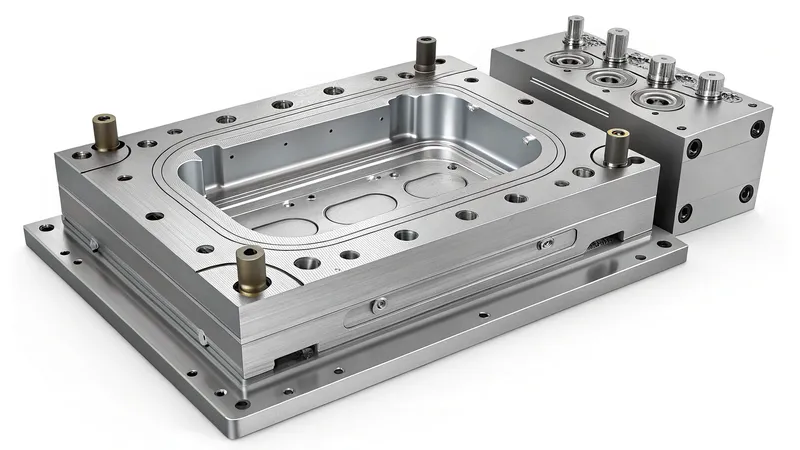
The mold base6, inserts, ejector pins7, and cooling systems8 are key to assembling a reliable mold.
Component | Function | Notes |
---|---|---|
Mold Base | Structural support | Steel or aluminum |
Inserts | Customization and maintenance9 | Reduces setup time |
Ejector Pins | Part removal | Hardened materials |
Cooling Systems | Temperature regulation | Prevents defects |
Mold Base
The mold base provides a sturdy foundation, typically made from steel for durability in high-volume production or aluminum for cost-effective prototyping.
Steel mold bases excel in high-volume production.True
Their durability withstands repeated use, making them cost-effective for large runs.
Inserts
Inserts allow customization and simplify maintenance, ideal for molds needing frequent adjustments or multiple part designs.
Ejector Pins
Ejector pins, often made from hardened steel, eject finished parts without damage, ensuring smooth production cycles.
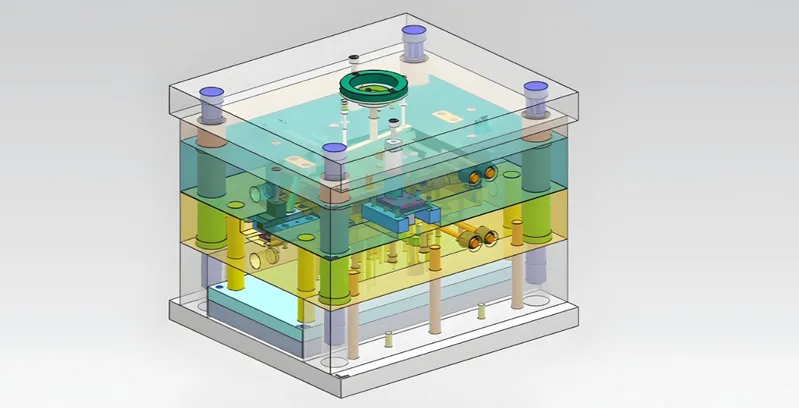
Cooling Systems
Cooling systems regulate mold temperature to prevent defects like warping. Options include water-based10 (efficient, cost-effective), oil-based11 (precise control), or hybrid systems.
Cooling System | Pros | Cons |
---|---|---|
Water-based | Efficient, cost-effective | Less precise control |
Oil-based | Precise, stable | Expensive, slower |
Hybrid | Flexible, combined benefits | Complex, costly |
Cooling systems prevent defects in molded parts.True
Proper temperature control ensures uniform cooling, reducing risks like shrinkage.
How Do Measuring Instruments Ensure Quality in Injection Mold Making?
Measuring instruments verify that molds meet exact specifications, ensuring quality and consistency.
Coordinate Measuring Machines (CMM) and laser scanners are critical for precision and quality control.
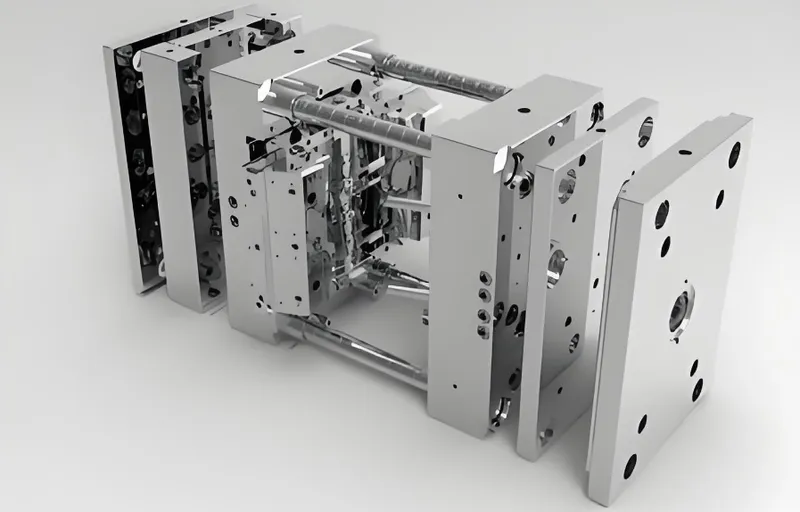
Coordinate Measuring Machines (CMM)
CMMs measure component dimensions with high accuracy (e.g., ±0.002 mm), detecting deviations for pre-production corrections.
Laser Scanners
Laser scanners assess surface details and complex geometries with precision up to ±0.01 mm, ensuring mold accuracy.
Measuring instruments are crucial for quality control.True
They verify dimensions and detect errors, maintaining high-quality standards.
Explore measuring tools further at this resource.
What Are the Core Components of an Injection Mold?
Core mold components shape the plastic part and manage material flow, directly affecting part quality.
The mold core and cavity, gates, runners, and sprue bushes form and guide the plastic during injection.
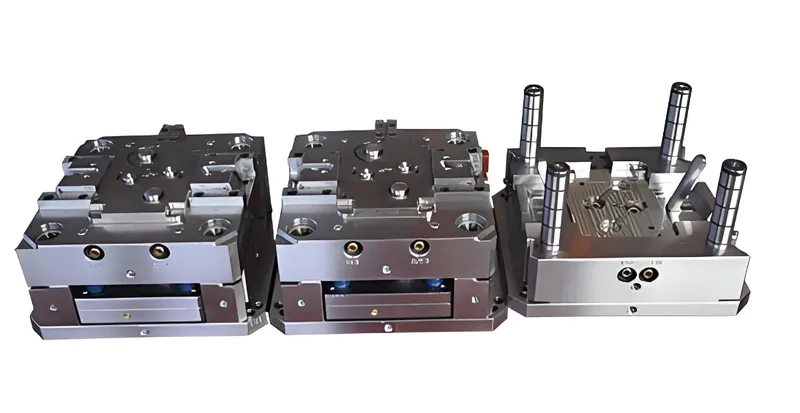
Mold Core and Cavity
The core shapes internal features, while the cavity defines the external form, together creating the part’s geometry.
Gates, Runners, and Sprue Bushes
-
Gates: Control plastic flow into the cavity, designed for easy removal.
-
Runners: Channels directing plastic from sprue to gates; hot runners reduce waste, cold runners are simpler.
-
Sprue Bushes: Link the nozzle to runners, available as hot or cold tip variants.
Gate and runner design impacts part quality.True
Proper configuration ensures even filling and minimizes defects like short shots.
How Do You Choose the Right Tools for Injection Mold Making?
Tool selection balances production goals, part complexity, and budget for optimal outcomes.

Material choice, durability, and design needs guide tool selection.
Factor | Options | Guidance |
---|---|---|
Mold Material | Steel vs. Aluminum | Steel for volume, aluminum for prototypes |
Runner Type | Hot vs. Cold | Hot for efficiency, cold for simplicity |
Cooling System | Water, Oil, Hybrid | Match to precision and cost needs |
Tool selection affects cost and quality.True
The right tools optimize efficiency and ensure mold performance.
For a detailed guide, see this article.
Conclusion
The essential tools for injection mold making—from CAD software and CNC machines to mold bases and cooling systems—are vital for producing high-quality molds. By understanding their roles and benefits, manufacturers can streamline processes, cut costs, and achieve consistent results. To dive deeper, explore how mold materials influence part quality or how CAD advancements are shaping mold design’s future.
-
Explore this link to understand the significance of injection mold making in various industries and its impact on production efficiency. ↩
-
Discover the critical tools used in injection mold making to enhance your knowledge and improve your manufacturing processes. ↩
-
Understanding essential mold components can significantly impact your production quality and efficiency. Check this out! ↩
-
Explore this link to discover top CAD software that enhances precision in mold design, crucial for successful outcomes. ↩
-
Learn how Moldflow Analysis can predict material flow and enhance mold performance, making it a vital tool for engineers. ↩
-
Understanding the mold base’s role can enhance your knowledge of manufacturing processes and improve production efficiency. ↩
-
Learning about ejector pins will provide insights into their essential function in part removal and overall mold efficiency. ↩
-
Exploring cooling systems will reveal their critical role in preventing defects and ensuring product quality in mold production. ↩
-
Exploring the impact of customization on maintenance can lead to improved efficiency and reduced downtime in manufacturing. ↩
-
Explore the benefits of water-based systems to see how they can be efficient and cost-effective for your needs. ↩
-
Learn about oil-based cooling systems to understand their precise control and potential drawbacks for your applications. ↩