Painting injection molded products enhances their aesthetics, durability, and functionality, making it a vital post-processing step in industries like automotive, electronics, and consumer goods.
Painting injection molded products involves surface preparation and coating techniques1 like spray painting and powder coating, improving appearance and durability for applications in automotive, electronics, and daily goods.
Mastering the techniques for painting injection molded products can elevate your manufacturing process, ensuring high-quality finishes tailored to specific needs. This article explores the best methods, from basic concepts to advanced workflows, offering practical insights for professionals and enthusiasts alike.
Painting injection molded products enhances both aesthetics and durability.True
It provides a uniform finish and protects against UV, chemicals, and scratches, extending product life.
Painting is the only way to finish injection molded products.False
Alternatives like in-mold coloring and powder coating also exist, offering different benefits depending on the application.
- 1. What Are the Common Techniques for Painting Injection Molded Products?
- 2. What Are the Steps in Painting Injection Molded Products?
- 3. What Are the Key Factors in Painting Injection Molded Products?
- 4. What Are the Applications of Painting Injection Molded Products?
- 5. How Does Painting Compare to Other Finishing Methods?
- 6. Conclusion
What Are the Common Techniques for Painting Injection Molded Products?
Painting techniques for injection molded products vary by process and application, offering solutions for aesthetic enhancement and functional improvement across industries.
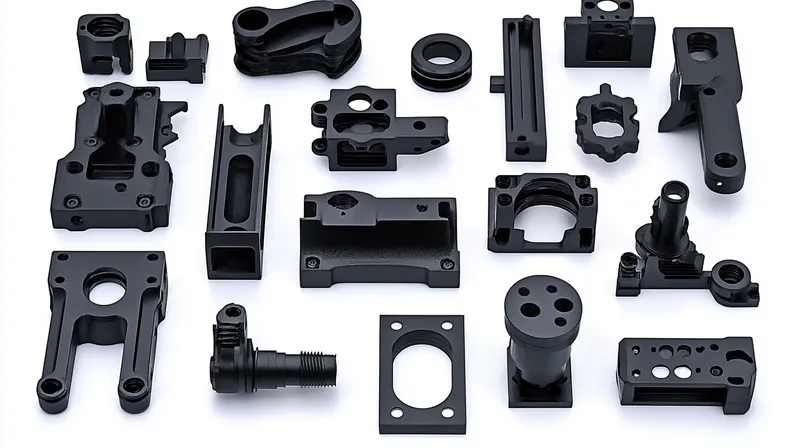
Spray painting and powder coating2 are top techniques for painting injection molded products, providing cost-effective aesthetics and durable finishes for automotive, electronics, and consumer goods.
Technique | Typical Finish Thickness | Notes |
---|---|---|
Spray Painting | 0.025 – 0.075 mm | Thin, uniform, cost-effective |
Powder Coating | 0.05 – 0.2 mm | Thicker, durable, UV-cured |
Spray Painting
Spray painting is a widely used method due to its simplicity and affordability. According to ICOMold Painting Processes3, it involves applying paint via a spray gun, often with UV or self-curing options, to achieve finishes from matte to high gloss. It’s ideal for covering molding imperfections and ensuring color uniformity, commonly used in automotive dashboards and consumer electronics.
Powder Coating
Powder coating offers a tougher, more durable finish. This technique, detailed in ICOMold Painting Processes, uses electrostatically charged powder cured under UV light, making it suitable for parts needing UV and chemical resistance, like outdoor furniture or appliance covers. It’s less flexible in finish options but excels in longevity.
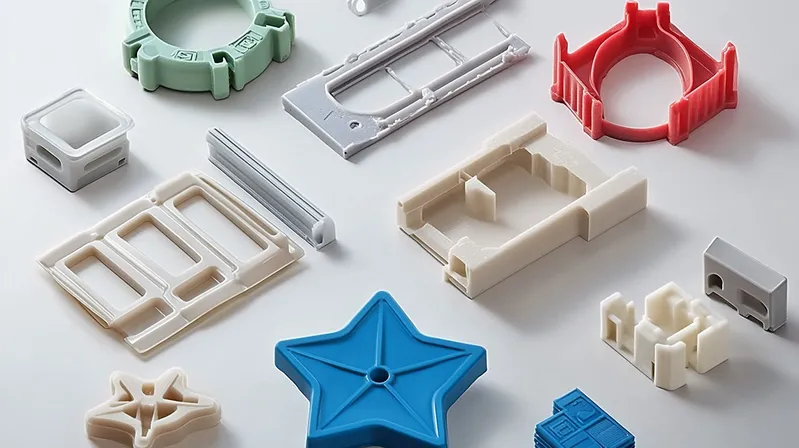
Silk Screening
Silk screening is perfect for detailed designs on flat surfaces. As noted in ICOMold Painting Processes, it uses separate screens per color, making it a go-to for logos on electronics housings or appliance panels, though it’s less versatile for complex shapes.
Stamping
Stamping, or pad printing, is quick and precise, using a pad to transfer paint onto raised designs. Per ICOMold Painting Processes, it’s cost-effective for small, detailed parts like buttons or toy components, offering versatility across industries.
Spray painting is the most cost-effective technique for injection molded products.True
It requires minimal equipment and provides a quick, uniform finish, reducing labor and material costs.
Powder coating is unsuitable for indoor applications.False
While durable for outdoor use, powder coating is also effective indoors, especially for appliances needing scratch resistance.
What Are the Steps in Painting Injection Molded Products?
The painting process for injection molded products is a detailed workflow that ensures adhesion and quality, critical for industries requiring robust finishes.
Painting injection molded products involves cleaning, etching, applying paint, and testing adhesion, ensuring durable, attractive finishes for automotive and consumer goods.
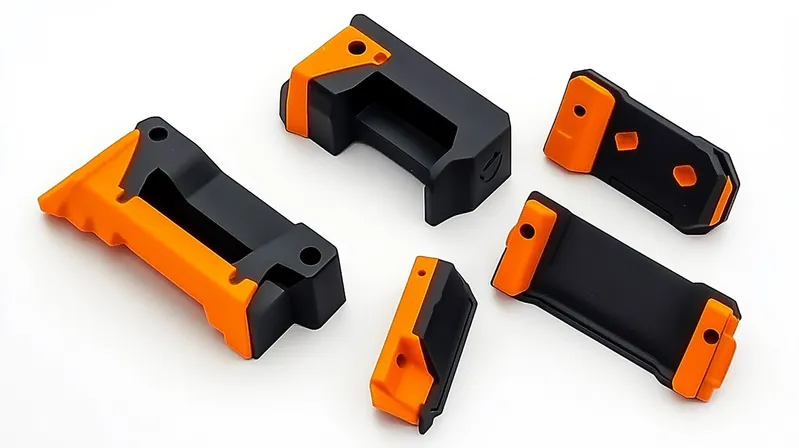
Surface Preparation
Start with a clean surface, free of soil, residue, and debris, at 50% humidity, as recommended by ICOMold Painting Processes. Use water-soluble mold releases removable with detergent to avoid adhesion issues, addressing plasticizers that can interfere.
Surface Etching
Etch the surface to enhance adhesion, especially for low-polarity plastics like polypropylene. Techniques include chemical etching, brief gas burner exposure, or plasma conditioning, as outlined in Star Rapid Injection Molding Materials4, increasing surface energy for better paint bonding.
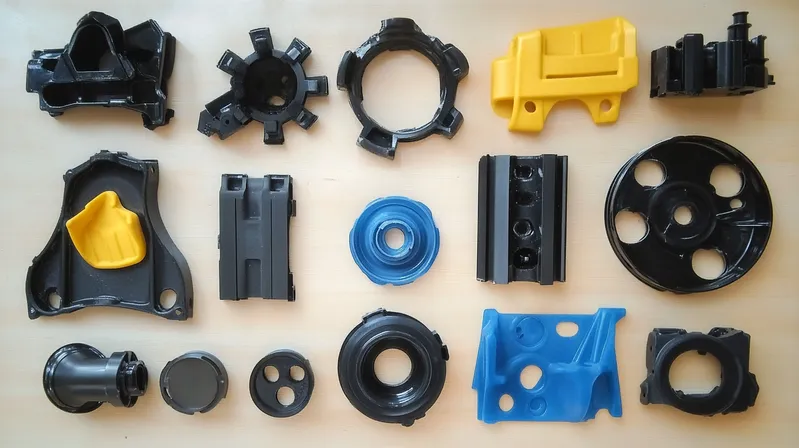
Painting Application
Apply paint using the chosen method—spray painting for simplicity, powder coating5 for durability, silk screening6 for details, or stamping for precision. Per ICOMold Painting Processes, match the technique to the part’s use, like UV resistance for outdoor applications.
Adhesion Testing
Test adhesion to ensure long-term durability, considering plastic chemistry and surface energy. ICOMold Painting Processes emphasizes this step to confirm paint withstands environmental stresses like UV or chemical exposure.
Surface preparation is optional in painting injection molded products.False
Proper cleaning and etching are essential for adhesion, especially with challenging plastics like polypropylene.
Adhesion testing ensures painted products last longer.True
It verifies paint bonds well, preventing peeling or fading under use.
What Are the Key Factors in Painting Injection Molded Products?
Success in painting injection molded products hinges on material choice, surface prep, and process control, impacting finish quality and durability.
Material compatibility7, surface preparation, and painting technique are key factors in painting injection molded products, determining adhesion and finish quality.
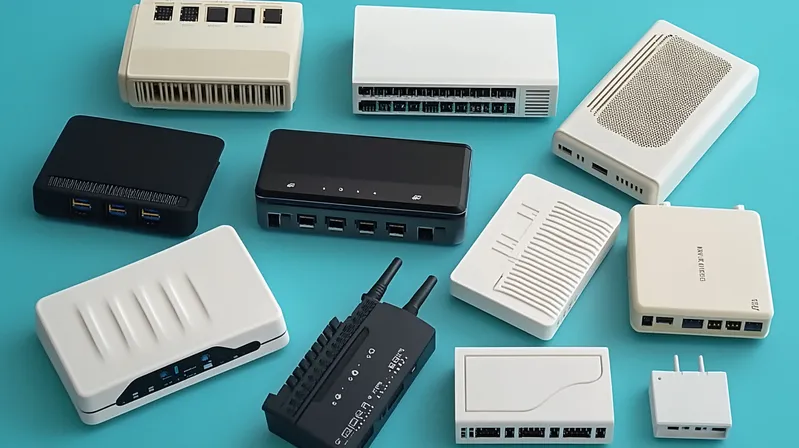
Material Compatibility
Plastic type affects painting success. Polypropylene and polyethylene need etching due to low polarity, while ABS requires plasticizer management, per Star Rapid Injection Molding Materials. Acrylics and nylon also vary in adhesion needs due to dye uptake and water absorption.
Surface Preparation
Effective prep involves cleaning at 50% humidity and etching for adhesion, as noted in ICOMold Painting Processes. Skipping this risks poor bonding, especially with plastics containing plasticizers or low surface energy.
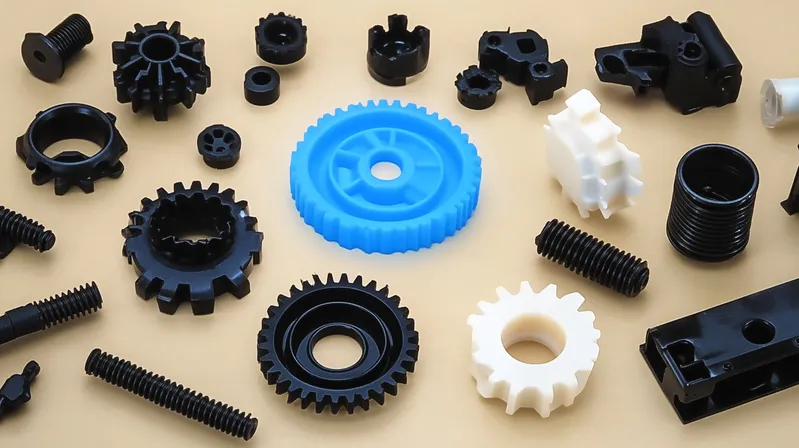
Painting Technique Selection
Choose based on needs: spray for cost, powder for durability, silk screening for flat designs, or stamping for precision. ICOMold Painting Processes highlights matching technique to application, like UV curing for outdoor parts.
All plastics are equally easy to paint.False
Low-polarity plastics like polypropylene require extra prep, unlike ABS or acrylics.
Technique choice impacts both cost and durability.True
Spray painting saves money, while powder coating offers a tougher finish.
What Are the Applications of Painting Injection Molded Products?
Painting injection molded products8 serves diverse industries, enhancing both function and appeal with tailored finishes.
Painting injection molded products is used in automotive, electronics, and consumer goods for aesthetics, durability, and environmental resistance.
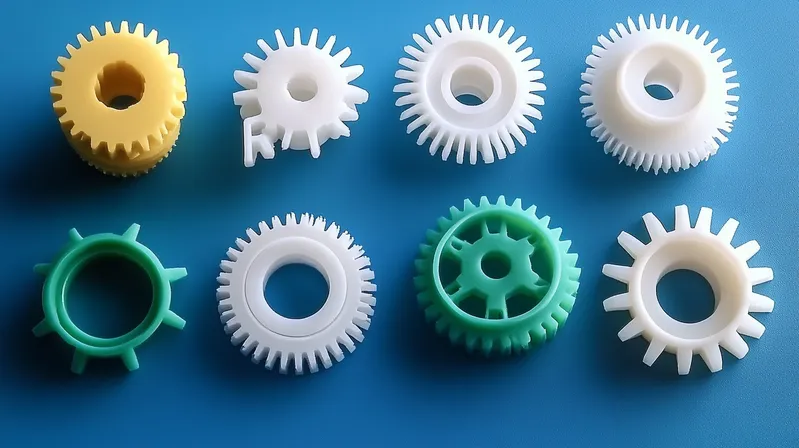
Automotive Industry
Painting enhances dashboards, bumpers, and trim for UV resistance and uniform color, as seen in ICOMold Painting Processes. It covers imperfections and boosts durability for exterior parts.
Electronics
Housings for smartwatches and sensors benefit from painting for scratch resistance and aesthetics, per ICOMold Painting Processes. Silk screening adds detailed logos or labels.
Consumer Goods
Appliance covers and furniture use painting for stain resistance and visual appeal, with powder coating9 offering durability for outdoor items, according to ICOMold Painting Processes.
Painting reduces manufacturing costs in all applications.False
It adds post-processing costs, though it can offset expenses by covering flaws.
Painted injection molded products resist environmental damage.True
Coatings protect against UV, chemicals, and scratches, enhancing longevity.
How Does Painting Compare to Other Finishing Methods?
Process Flow
Painting is a post-process involving cleaning, etching, and coating, per ICOMold Painting Processes. In-mold coloring integrates color during molding, while powder coating applies a dry finish cured separately.
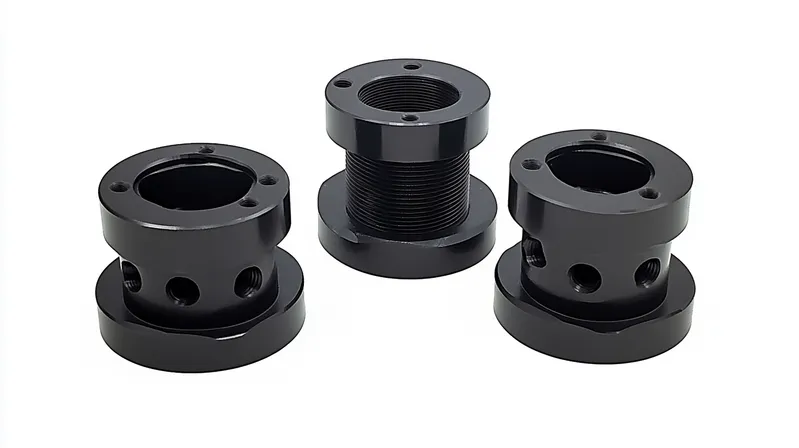
Principle
Painting applies liquid or powder post-molding, requiring adhesion prep. In-mold coloring embeds color in the resin, per Post-Processing for Plastic Injection Molding10, reducing steps but limiting flexibility.
Finish Characteristics
Painting offers matte to gloss finishes with versatility, while in-mold coloring11 depends on mold texture, and powder coating provides a tough, uniform layer, as noted in ICOMold Painting Processes.
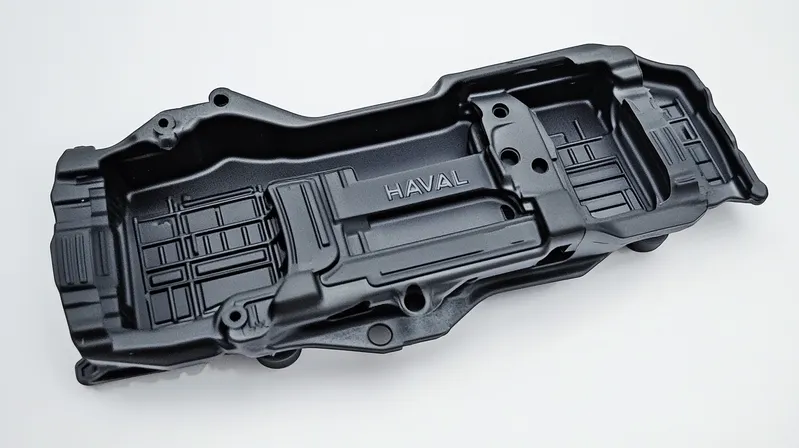
Application Scenarios
Painting suits varied shapes and post-mold adjustments, ideal for automotive and electronics. In-mold coloring fits high-volume, consistent designs, while powder coating excels for durable outdoor parts, per ICOMold Painting Processes.
Advantages and Disadvantages
Painting provides finish options but adds costs; in-mold coloring saves steps but lacks post-flexibility; powder coating is durable but less versatile, per ICOMold Painting Processes.
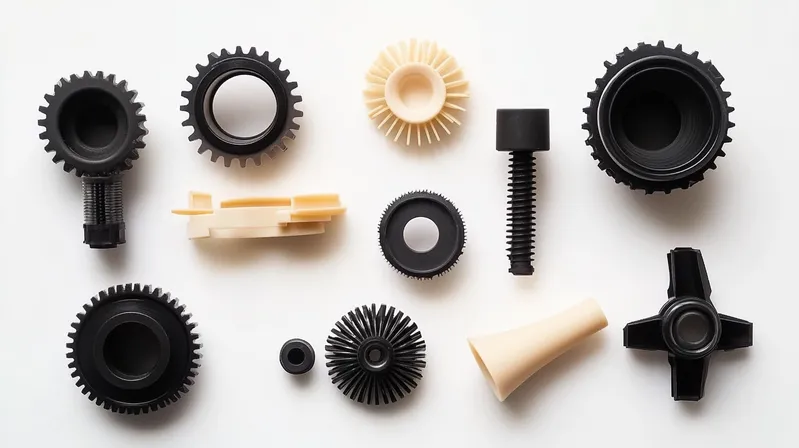
Conclusion
Painting injection molded products, detailed in ICOMold Painting Processes, enhances aesthetics and durability across automotive, electronics, and consumer goods. Techniques like spray painting and powder coating offer tailored solutions, with workflows ensuring adhesion through prep and testing. Compared to in-mold coloring, painting provides flexibility, making it ideal for diverse, high-quality finishes.
-
Learn about effective surface preparation and coating techniques to improve the quality of your injection molded products. ↩
-
Learn about the unique benefits and applications of spray painting and powder coating for superior finishes. ↩
-
Explore ICOMold Painting Processes for insights into painting techniques and workflows. ↩
-
Learn about material challenges in Star Rapid Injection Molding Materials. ↩
-
Explore the advantages of powder coating, especially its durability and UV resistance, ideal for outdoor applications. ↩
-
Learn about silk screening techniques and their effectiveness for creating intricate designs on various surfaces. ↩
-
Understanding material compatibility is crucial for achieving optimal adhesion and finish quality in painted products. Explore this link for detailed insights. ↩
-
Explore the advantages of painting injection molded products for aesthetics and durability across various industries. ↩
-
Learn how powder coating provides a tough, uniform layer that enhances the durability of painted surfaces. ↩
-
Understand finishing alternatives in Post-Processing for Plastic Injection Molding. ↩
-
Discover the differences between in-mold coloring and traditional painting methods for plastic products. ↩