Injection molding is a cornerstone of modern manufacturing, enabling the production of intricate plastic parts with high precision and efficiency. When it comes to creating complex structures1—such as parts with undercuts, thin walls, or integrated components—specialized techniques are essential to achieve the desired results without compromising quality. This blog post delves into the best techniques for creating complex structures in injection molding, offering insights into their applications, advantages, and considerations.
Mastering advanced injection molding techniques2 like overmolding3, insert molding, and gas-assisted molding is crucial for producing complex structures efficiently and cost-effectively, especially in industries demanding high precision and functionality.
Understanding these techniques can help manufacturers and designers make informed decisions, ensuring that their products meet both functional and aesthetic requirements. Explore the following sections to learn how these methods can be applied to your projects.
Injection molding is the most efficient method for producing complex plastic parts.True
Injection molding allows for high-volume production of intricate parts with tight tolerances, making it ideal for complex structures.
Complex structures in injection molding are limited to simple geometries.False
Advanced techniques enable the creation of highly intricate parts with features like undercuts, thin walls, and multi-material components.
- 1. What Is Injection Molding and Why Is It Used for Complex Structures?
- 2. Where Are These Techniques Commonly Applied?
- 3. How Do These Techniques Work in the Injection Molding Process?
- 4. What Are the Practical Tools for Designing Complex Structures?
- 5. How Do These Techniques Relate to Other Manufacturing Technologies?
- 6. Conclusion
What Is Injection Molding and Why Is It Used for Complex Structures?
Injection molding is a manufacturing process where molten plastic is injected into a mold cavity under high pressure. Once cooled, the plastic solidifies into the shape of the mold, creating a precise part. This method is ideal for mass production4 due to its speed, consistency, and ability to produce complex geometries.
Complex structures in injection molding refer to parts with challenging features such as:
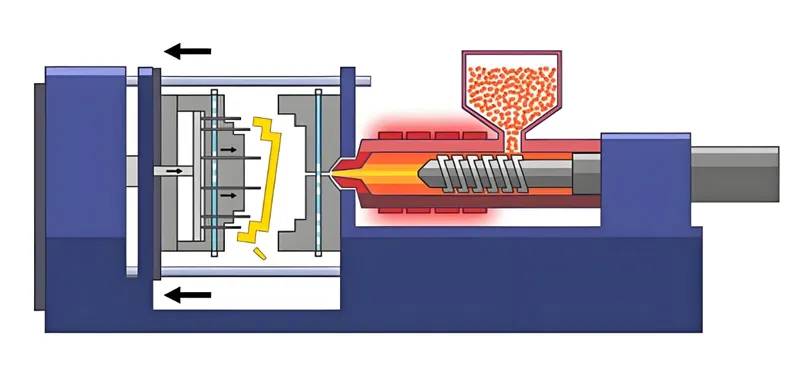
-
Undercuts (features that prevent straightforward ejection from the mold)
-
Thin-walled sections
-
Integrated components (e.g., metal inserts or multiple materials)
-
Hollow sections or varying wall thicknesses
To achieve these features, manufacturers rely on advanced techniques5 that enhance the standard injection molding process.
Key Techniques for Creating Complex Structures
Several specialized techniques are employed to create complex structures in injection molding. These include:
Technique | Description | Common Applications |
---|---|---|
Overmolding6 | Molding one material over another to combine properties or aesthetics. | Ergonomic grips, multi-material parts |
Insert Molding | Incorporating pre-formed parts (e.g., metal inserts) into the plastic part. | Reinforced structures, electronics |
Multi-Shot Molding | Using multiple injections to create parts with different materials or colors. | Seals, aesthetic components |
Gas-Assisted Injection Molding7 | Injecting gas to create hollow sections and reduce weight. | Lightweight parts, automotive components |
Microcellular Foam Injection Molding | Creating a foam structure to reduce weight and material usage. | Packaging, insulation |
In-Mold Labeling/Decoration | Applying labels or decorations during molding for complex designs. | Consumer goods, packaging |
Hot Runner Systems | Maintaining molten plastic in the runner system for efficiency and complexity. | High-volume production |
Mold Flow Analysis8 | Simulating plastic flow to optimize mold design. | All complex parts |
These techniques can be classified based on their primary benefits:
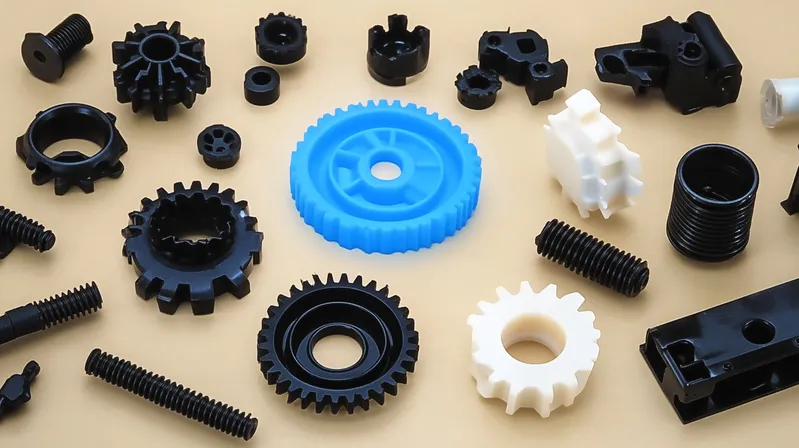
-
Material Combination: Overmolding, Insert Molding, Multi-Shot Molding
-
Weight Reduction: Gas-Assisted Molding, Microcellular Foam Molding
-
Aesthetic Enhancement: In-Mold Labeling/Decoration
-
Efficiency and Complexity: Hot Runner Systems, Mold Flow Analysis
Overmolding is essential for creating parts with both rigid and flexible components.True
By molding a soft material over a rigid base, overmolding allows for ergonomic designs and improved functionality.
Gas-assisted injection molding is only used for aesthetic purposes.False
While it can improve surface finish, its primary purpose is to create hollow sections and reduce material usage.
Where Are These Techniques Commonly Applied?
Injection molding techniques for complex structures are widely used across various industries:
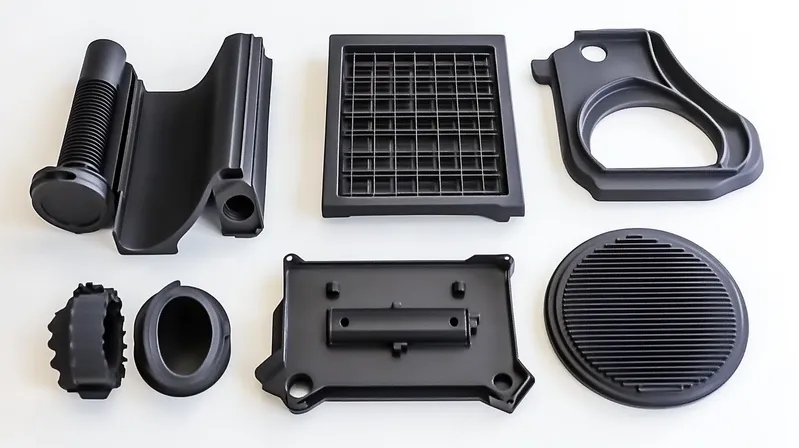
-
Automotive Industry: Complex parts like dashboards, bumpers, and interior components often require overmolding for soft-touch surfaces or insert molding for reinforced structures.
-
Medical Devices: Precision and biocompatibility are crucial, making insert molding9 ideal for embedded electronics or multi-shot molding10 for multi-material components.
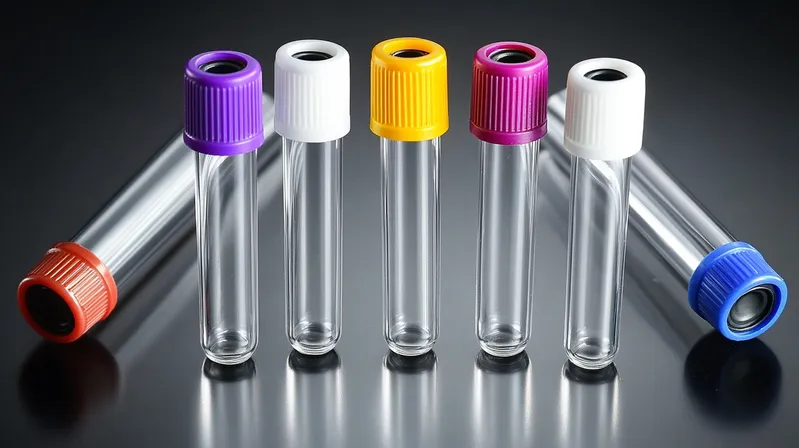
-
Consumer Electronics: Devices like smartphones and laptops use in-mold decoration for aesthetic appeal and gas-assisted molding for lightweight yet strong casings.
-
Packaging: Complex closures and containers benefit from multi-shot molding for integrated seals or overmolding for ergonomic grips.
Pros and Cons of Injection Molding vs. Other Methods
When deciding on a manufacturing method for complex structures, it’s essential to compare injection molding with alternatives like 3D printing and CNC machining.
Method | Pros | Cons |
---|---|---|
Injection Molding | High production speed, low cost per part for large volumes, precise complex geometries | High upfront tooling costs, less flexible for design changes |
3D Printing | Flexible for prototyping, no tooling required, complex geometries possible | Slower production, higher cost per part, limited material properties |
CNC Machining | High precision, suitable for low volumes, wide material options | Limited to simpler geometries, higher cost for complex parts |
When to Choose Injection Molding: For high-volume production of complex parts where precision, material performance, and cost-efficiency are critical.
Injection molding is more cost-effective than 3D printing for large-scale production.True
While 3D printing is excellent for prototypes, injection molding offers lower per-part costs for mass production.
CNC machining can produce parts with the same complexity as injection molding.False
CNC machining is limited by tool access and cannot easily produce undercuts or hollow sections without additional steps.
How Do These Techniques Work in the Injection Molding Process?
While the basic injection molding process involves melting plastic, injecting it into a mold, cooling, and ejecting the part, advanced techniques modify this workflow to accommodate complex structures.
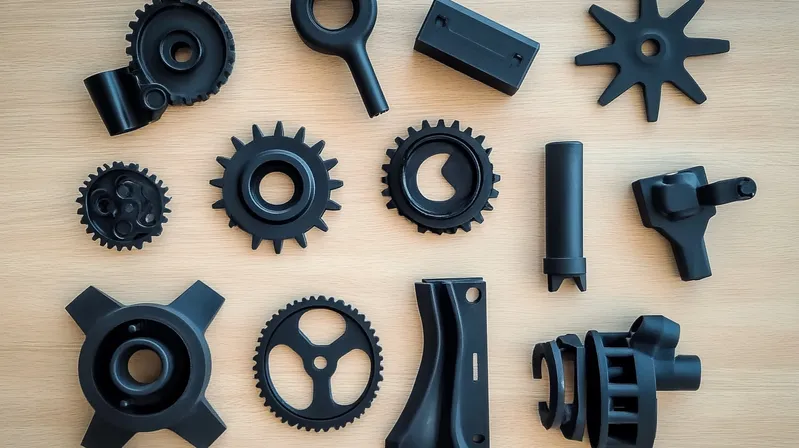
Technique-Specific Workflows
-
Overmolding: Involves two or more shots of material. The first material is molded, then the mold is rotated or transferred to another cavity for the second material.
-
Insert Molding: The insert (e.g., a metal part) is placed into the mold manually or robotically before injection. The plastic is then injected around it.
-
Gas-Assisted Molding: After partially filling the mold with plastic, gas is injected to push the plastic to the mold walls, creating hollow sections.
-
Multi-Shot Molding: Multiple injections are performed in sequence, often using different materials or colors, to build up the part.
-
Microcellular Foam Molding: A blowing agent is introduced to create a foam structure within the plastic, reducing weight.
-
In-Mold Labeling/Decoration: Labels or decorative films are placed in the mold before injection, bonding to the part during molding.
-
Hot Runner Systems: These systems keep the plastic molten in the runner channels, allowing for more complex mold designs and reduced waste.
-
Mold Flow Analysis: This simulation tool predicts how the plastic will flow into the mold, helping to optimize gate placement, cooling, and part design.
Material Considerations for Each Technique
Material selection is critical for the success of these techniques:

-
Overmolding: Requires materials that bond well, such as thermoplastic elastomers (TPE) over rigid plastics like ABS or polycarbonate.
-
Insert Molding: The insert material must withstand molding temperatures and pressures without deforming (e.g., metals, ceramics).
-
Microcellular Foam Molding: Works best with polymers that can be foamed, like polypropylene or polystyrene.
-
Multi-Shot Molding: Materials must be compatible in terms of melting points and adhesion properties.
Material compatibility is crucial in multi-shot molding.True
Incompatible materials may not bond properly, leading to delamination or weak joints.
All plastics can be used in gas-assisted injection molding.False
Only certain polymers with appropriate viscosity and flow characteristics are suitable for gas-assisted molding.
What Are the Practical Tools for Designing Complex Structures?
To ensure that complex structures are moldable and meet quality standards, designers should follow best practices and use decision-making tools.
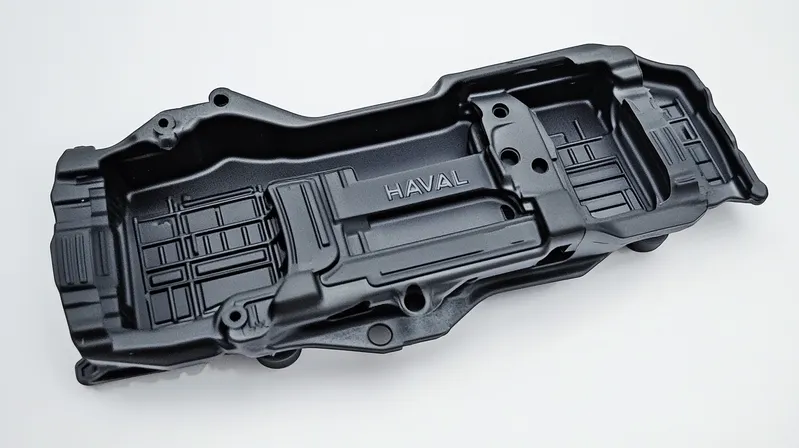
Design Checklist for Complex Structures
-
Draft Angles: Apply a draft angle of 1-2 degrees to all vertical walls to facilitate ejection.
-
Wall Thickness: Maintain uniform wall thickness (typically 1-3 mm) to prevent warping and sink marks. For thin walls, ensure the material’s flow characteristics allow for complete filling.
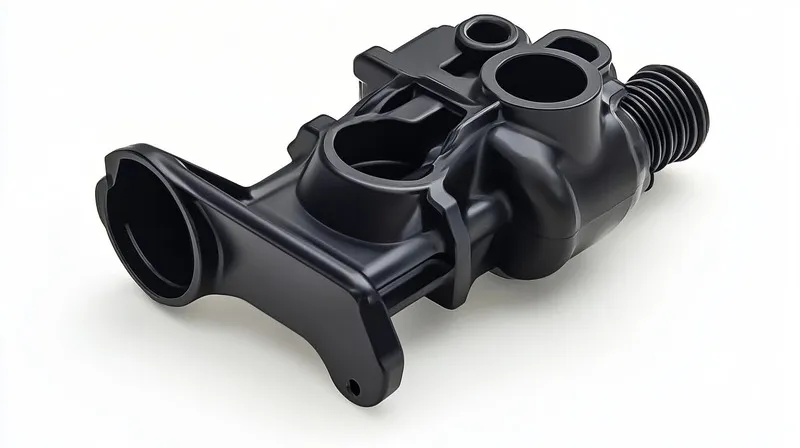
-
Undercuts: Minimize undercuts or design them with collapsible cores or side actions to avoid mold complexity.
-
Gate Location: Place gates in non-critical areas, considering flow patterns to avoid weld lines or air traps.
-
Venting: Include vents, especially in deep ribs or bosses, to allow air to escape and prevent burn marks.
-
Ribs and Bosses: Design ribs with a thickness of 50-60% of the wall thickness and bosses with adequate draft for ejection.
Process Selection Decision-Making Guide
When choosing the right technique for your project, consider the following:
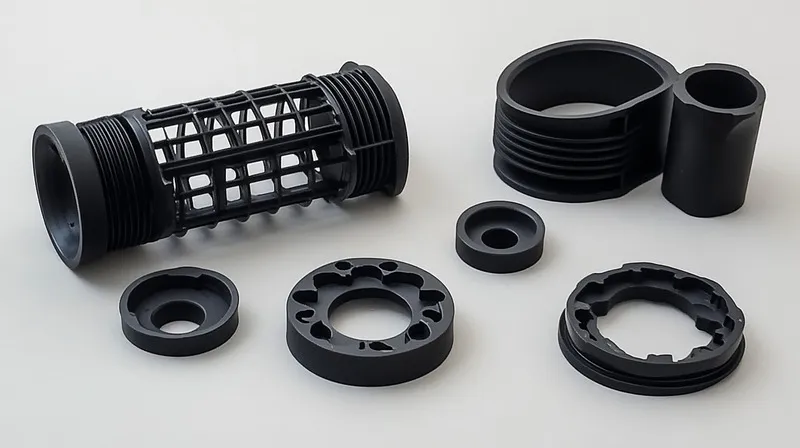
-
For Multi-Material Parts: Use overmolding or multi-shot molding.
-
For Lightweight Parts: Opt for gas-assisted or microcellular foam molding.
-
For Aesthetic Parts: Choose in-mold labeling/decoration.
-
For High-Volume Production: Implement hot runner systems to reduce waste and cycle time.

- For Complex Geometries: Use mold flow analysis to simulate and optimize the design before production.
A design checklist can prevent common molding defects.True
Following best practices like uniform wall thickness and proper venting reduces the risk of defects such as warping or incomplete filling.
Mold flow analysis is optional for simple parts.True
While beneficial, mold flow analysis is more critical for complex structures to predict and resolve potential issues.
How Do These Techniques Relate to Other Manufacturing Technologies?
Injection molding is part of a broader ecosystem of manufacturing technologies, each with its own strengths:
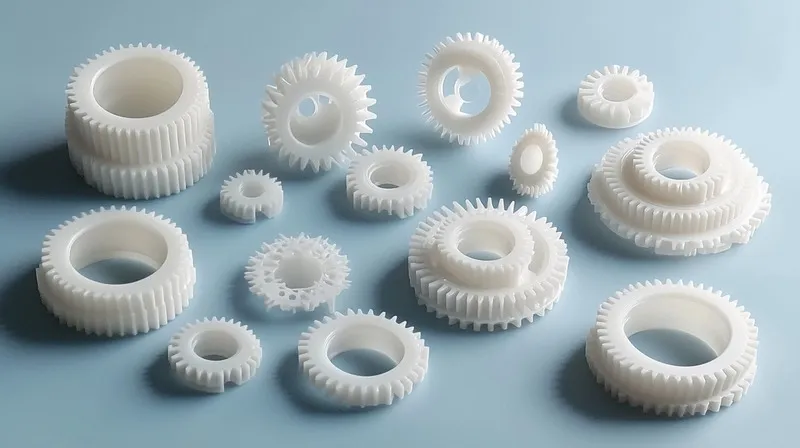
-
Blow Molding: Used for hollow parts like bottles, differing from injection molding’s solid parts.
-
Rotational Molding: Ideal for large, hollow parts like tanks, with slower cycle times but lower tooling costs.
-
Thermoforming: Suitable for sheet-based parts, offering faster production for simpler shapes but less precision.
Understanding these related technologies helps in selecting the most appropriate method for a given application.
Conclusion
Creating complex structures in injection molding requires a deep understanding of advanced techniques like overmolding, insert molding, and gas-assisted molding. By leveraging these methods, manufacturers can produce parts that meet stringent functional and aesthetic requirements across industries such as automotive, medical, and consumer electronics. Additionally, practical tools like design checklists and mold flow analysis ensure that designs are optimized for manufacturability, reducing costs and time to market.
-
Discover essential techniques for producing intricate designs in injection molding, enhancing both functionality and aesthetics. ↩
-
Learn about cutting-edge methods like overmolding and gas-assisted molding to improve efficiency and precision in manufacturing. ↩
-
Explore the benefits of overmolding in creating multi-material parts, enhancing product performance and design flexibility. ↩
-
Learning about mass production in injection molding can help you grasp its advantages in manufacturing and cost-effectiveness. ↩
-
Exploring advanced techniques can provide insights into improving production efficiency and product quality in injection molding. ↩
-
Explore this link to understand how Overmolding enhances product design and functionality, combining materials for better performance. ↩
-
Discover the advantages of Gas-Assisted Injection Molding, including weight reduction and design flexibility, to improve your manufacturing processes. ↩
-
Learn how Mold Flow Analysis can significantly enhance mold design and production efficiency, leading to better quality parts. ↩
-
Explore this link to understand the significance of insert molding in creating complex, durable components across various industries. ↩
-
Discover the benefits of multi-shot molding for creating innovative, multi-material products that enhance functionality and aesthetics. ↩