Injection molding is a cornerstone of modern manufacturing, producing plastic parts for industries ranging from automotive to medical devices. However, the molded parts often require additional operations—known as post-processing1—to meet the desired quality, appearance, and functionality. These steps, which include trimming excess material, applying surface finishes, assembling components, and conducting inspections, are critical for ensuring the final product meets industry standards.
While post-processing enhances the value of injection molded parts2, it can also add time and cost to production. Therefore, understanding and managing post-processing effectively is essential for manufacturers aiming to balance quality with efficiency3. This blog explores the best practices for managing post-processing in injection molding, covering everything from foundational concepts to practical tools and related technologies.
- 1. What is Post-Processing in Injection Molding?
- 2. How is Post-Processing Classified in Injection Molding?
- 3. What are the Typical Application Scenarios for Post-Processing?
- 4. What are the Pros and Cons of Post-Processing Compared to Other Technologies?
- 5. What is the Full Workflow of Post-Processing in Injection Molding?
- 6. How Does Material Compatibility Affect Post-Processing?
- 7. What are the Best Practices for Designing Parts with Post-Processing in Mind?
- 8. How to Select the Right Post-Processing Techniques?
- 9. What Technologies are Related to Post-Processing in Injection Molding?
- 10. Conclusion
What is Post-Processing in Injection Molding?
Post-processing in injection molding refers to the operations performed after the molding process to improve the quality, appearance, and functionality of plastic parts. These operations address limitations of the molding process, such as surface defects, and add value through aesthetic or functional enhancements.
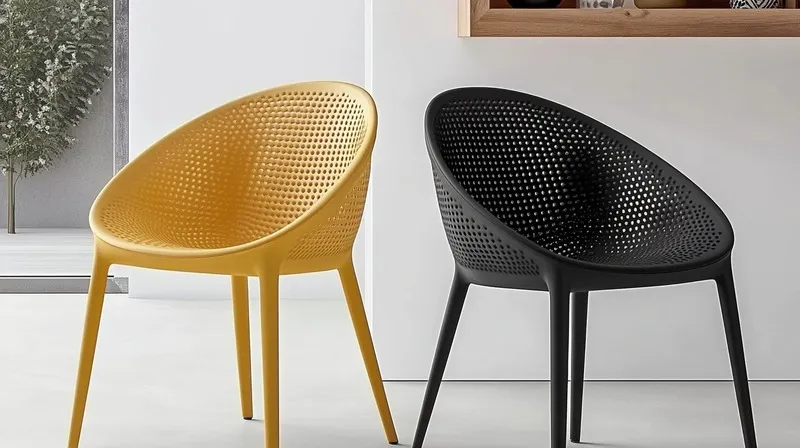
-
Technical Names and Aliases: Post-processing is often called "secondary operations4" or "finishing operations5." Specific techniques include gate trimming, deburring, spray painting, powder coating, pad printing, laser marking, UV printing, heat staking, ultrasonic welding, and mold texturing.
-
Core Principles: The primary goal is to ensure parts meet aesthetic, functional, and regulatory requirements. Post-processing corrects molding imperfections, enhances durability or visual appeal, and enables complex assemblies. It adds cost but can be more economical than using expensive tooling or materials during molding.
How is Post-Processing Classified in Injection Molding?
Post-processing techniques can be categorized based on process type, material considerations, and application areas:
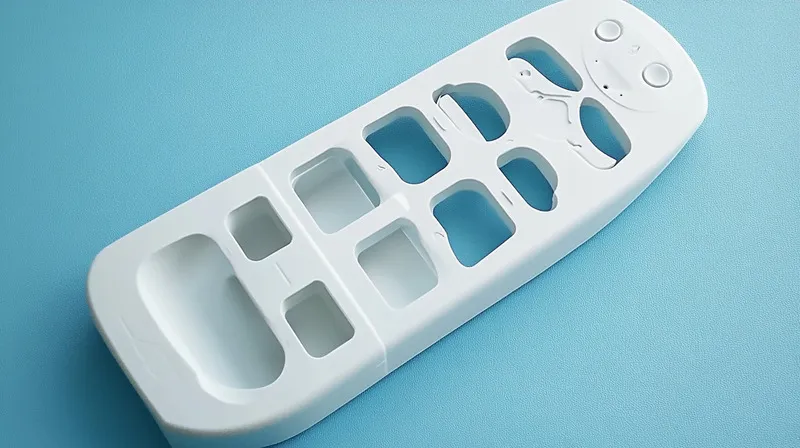
- By Process:
- Corrective Processes6: Gate trimming, deburring, flash removal to eliminate molding imperfections.
- Decorative Processes: Painting, pad printing, laser marking, UV printing, and surface texturing for aesthetic enhancement.
- Functional Processes: Heat staking, ultrasonic welding, and threaded insert installation for structural or operational purposes.
- Quality Control: Visual inspection, dimensional measurement, and non-destructive testing (NDT) to ensure compliance.
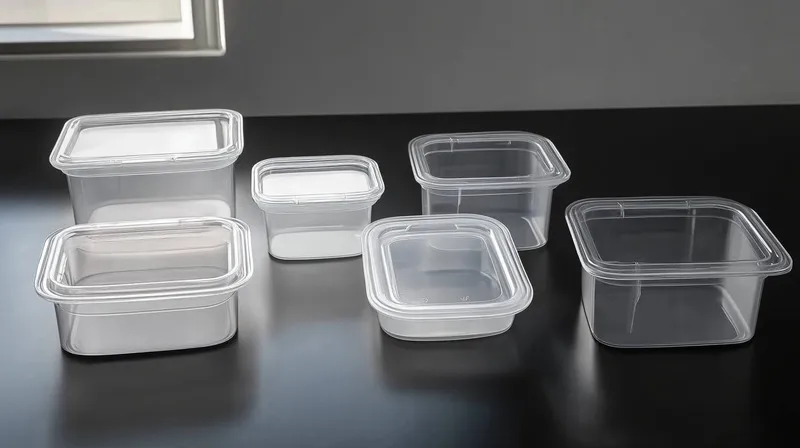
-
By Materials: Techniques vary depending on the plastic’s properties, such as surface energy or heat resistance. For instance, low surface energy plastics like polyethylene require plasma treatment7 for paint adhesion.
-
By Applications: Tailored to industry needs, such as automotive (durable coatings), medical devices (biocompatible finishes8), consumer electronics (branding), and aerospace (precision machining).
What are the Typical Application Scenarios for Post-Processing?
Post-processing is critical in industries where part quality, aesthetics, or regulatory compliance are paramount. Key scenarios include:
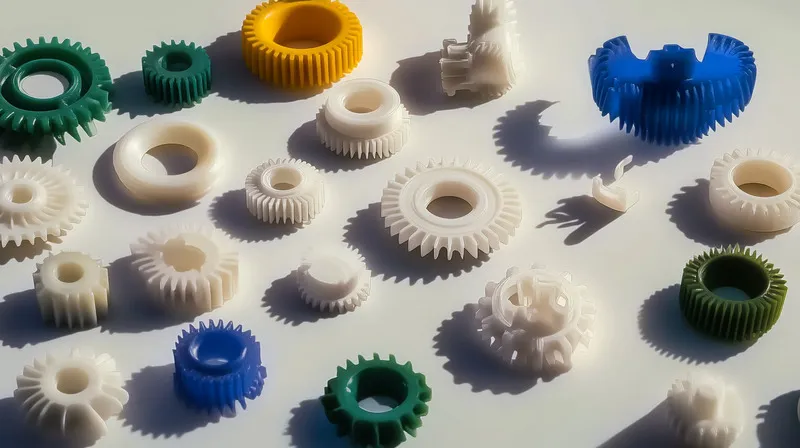
-
Automotive: Aesthetic finishes like painting or texturing for interior and exterior components, functional assemblies via welding, and UV-resistant coatings for durability.
-
Medical Devices: Precision finishing, sterilization, and biocompatible processes like ultrasonic welding for solvent-free assembly and laser marking for traceability.
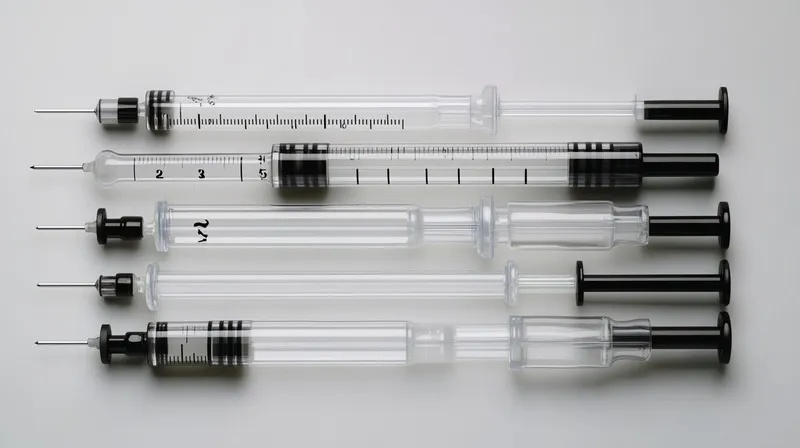
-
Consumer Electronics: Surface finishes for branding (e.g., pad printing logos), assembly for functionality (e.g., heat staking), and compact designs for miniaturization.
-
Aerospace: High-precision machining, specialized coatings for environmental resistance, and rigorous inspection to meet stringent standards.
What are the Pros and Cons of Post-Processing Compared to Other Technologies?
Post-processing in injection molding is often compared to other manufacturing methods like CNC machining or 3D printing. Here’s a simple comparison:
Aspect | Injection Molding Post-Processing | CNC Machining9 | 3D Printing10 |
---|---|---|---|
Cost | Cost-effective for high-volume production but adds post-processing costs. | Higher cost for low-volume or complex parts. | Cost-effective for prototypes but expensive for scaling. |
Precision | Moderate precision; post-processing enhances accuracy. | High precision for complex features. | Varies; often requires extensive post-processing for finish. |
Scalability | Highly scalable for mass production. | Limited scalability due to time and cost. | Best for low-volume or custom parts. |
Post-Processing Needs | Required for defects, aesthetics, or assembly. | Minimal, as parts are often finished. | Extensive for surface quality and strength. |
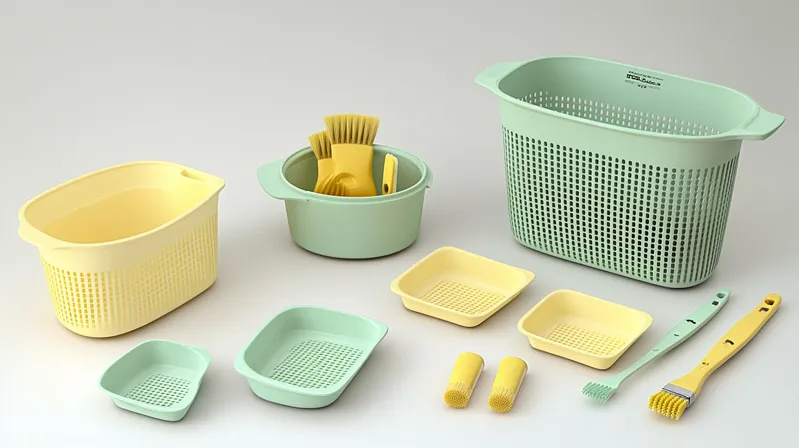
- Enhances aesthetics, functionality, and durability.
- Enables customization (e.g., logos, colors) and branding.
- Often more cost-effective than modifying molds or using premium materials.
- Cons:
- Increases production time and cost.
- Requires careful planning to avoid variability.
- May need specialized equipment or expertise.
What is the Full Workflow of Post-Processing in Injection Molding?
The post-processing workflow in injection molding involves several key steps, each with specific techniques and parameters:
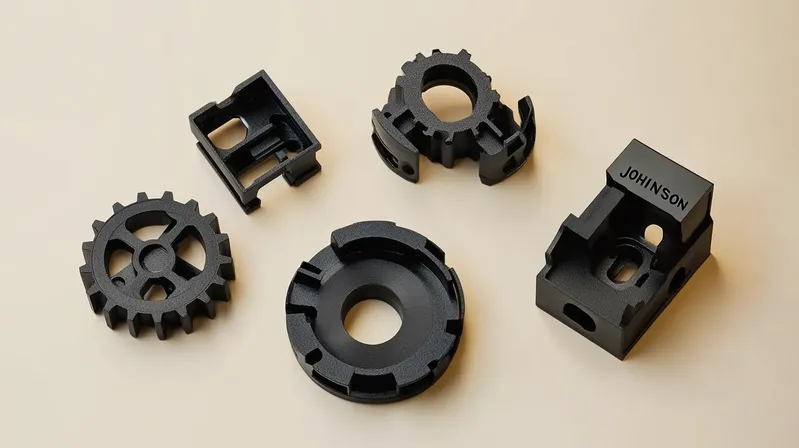
- Cooling:
- Purpose: Ensures uniform solidification to minimize warping, shrinkage, and defects.
- Key Parameters: Cooling time (up to 80% of cycle time), mold temperature, and material thermal conductivity.
- Best Practices: Use conformal cooling channels, maintain uniform wall thickness, and employ advanced techniques like variotherm or pulsed cooling for precise temperature control.
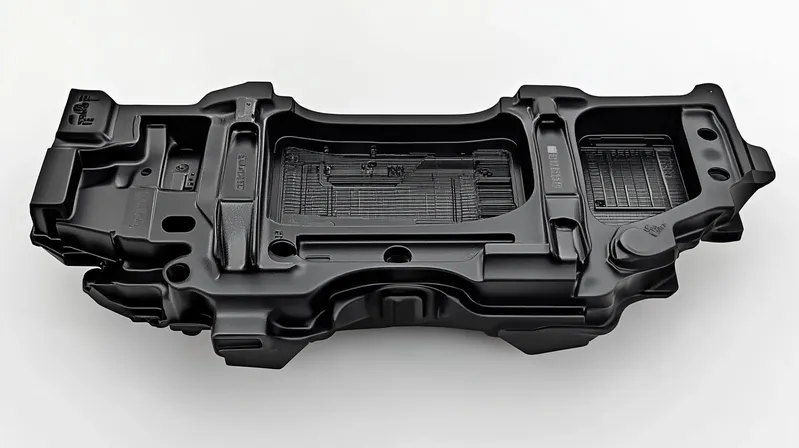
-
Ejection:
- Purpose: Removes parts from the mold without damage.
- Key Parameters: Ejection force, mold release agents, and automation settings.
- Best Practices: Use automated ejection systems to ensure consistency and prevent surface damage.
-
Trimming/Deburring:
- Purpose: Removes excess material (flash, gates) and smooths edges.
- Techniques: Manual scraping, tumbling, thermal energy deburring (TED), precision grinding.
- Key Parameters: Tool precision, material hardness, and safety protocols.
- Best Practices: Use TED for inaccessible areas and ensure proper personal protective equipment (PPE).
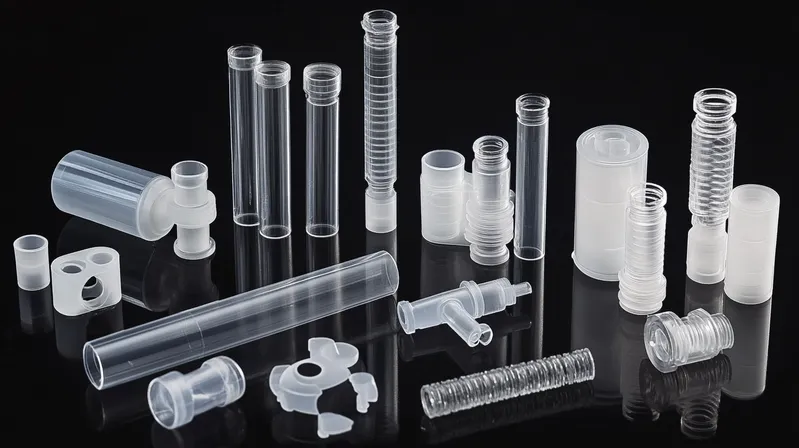
-
Surface Finishing:
- Purpose: Enhances aesthetics, durability, and functionality (e.g., grip, UV resistance).
- Techniques: Spray painting (self-curing or UV-curing), powder coating, pad printing, laser engraving, UV printing.
- Key Parameters: Surface preparation (cleaning, sanding, plasma treatment), coating thickness, and curing time.
- Best Practices: Prepare low surface energy plastics with plasma treatment for better adhesion (Plasma Treatment).
-
Assembly:
- Purpose: Joins parts for functional or structural purposes.
- Techniques: Ultrasonic welding (20,000–40,000 Hz vibrations), heat staking (softening plastic for inserts), threaded insert installation.
- Key Parameters: Welding frequency, insertion force, and material compatibility.
- Best Practices: Use ultrasonic welding for biocompatible medical devices to avoid solvents.
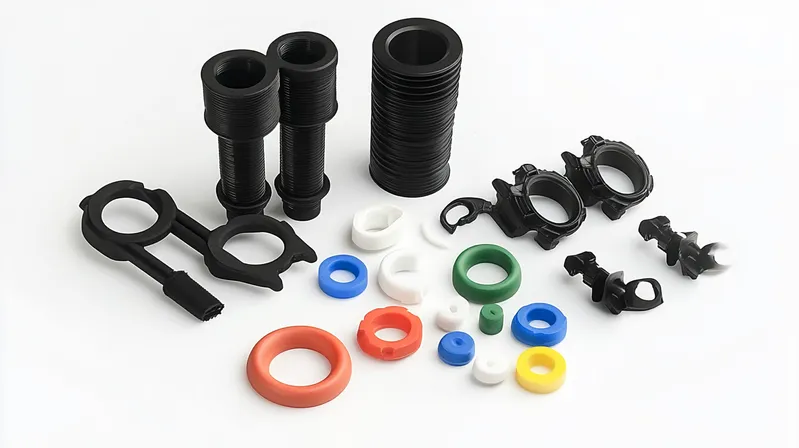
- Inspection:
- Purpose: Ensures parts meet quality and regulatory standards.
- Techniques: Visual inspection (surface defects), dimensional measurement (accuracy), NDT (internal integrity).
- Key Parameters: Inspection frequency, automation level, and tolerance limits.
- Best Practices: Implement automated inspection systems for efficiency and consistency.
How Does Material Compatibility Affect Post-Processing?
The choice of post-processing technique depends on the plastic’s properties:

-
Thermoplastics: Most common in injection molding (e.g., ABS, polycarbonate, polyethylene). Low surface energy thermoplastics (e.g., polyethylene, polypropylene) require plasma treatment for painting or coating adhesion. High-temperature thermoplastics (e.g., PEEK) may need specialized welding techniques.
-
Thermosets: Used for high-temperature applications (e.g., epoxy, phenolic). Their cross-linked structure limits re-melting, requiring unique finishing methods like precision grinding or specialized coatings.
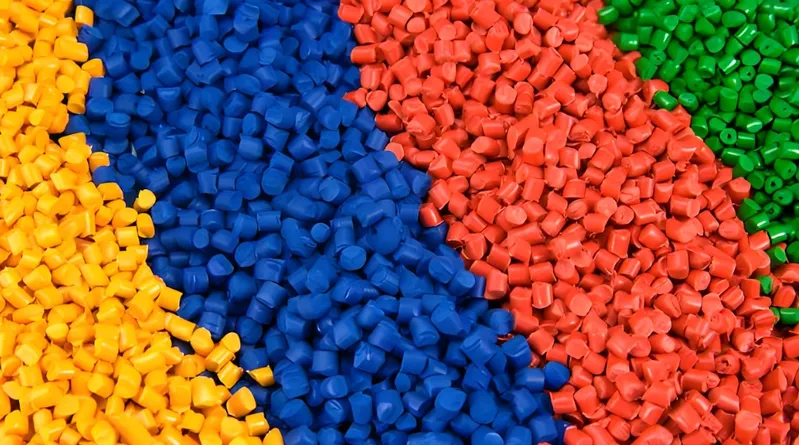
- Elastomers: Used for flexible parts (e.g., TPE, silicone). Post-processing must preserve elasticity, using gentle deburring or compatible coatings.
What are the Best Practices for Designing Parts with Post-Processing in Mind?
To optimize post-processing, consider the following during part design:
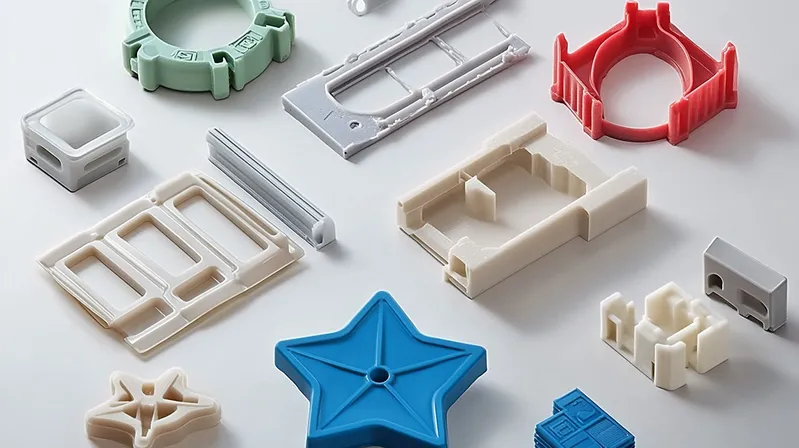
-
Material Selection: Choose plastics compatible with desired post-processing (e.g., paintable ABS, weldable polycarbonate).
-
Part Design: Ensure uniform wall thickness to simplify cooling and trimming, and design accessible gates for easy flash removal.
-
Tolerance and Fit: Account for post-processing tolerances to avoid fit issues during assembly.
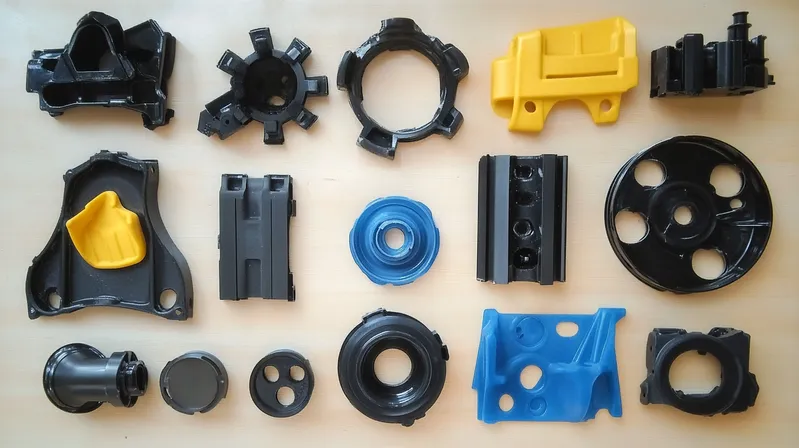
-
Cost and Time: Balance post-processing needs with production budgets and timelines.
-
Process Limitations: Recognize technique constraints (e.g., painting may require surface treatment for certain plastics).
How to Select the Right Post-Processing Techniques?
Selecting the right post-processing techniques involves a structured approach:
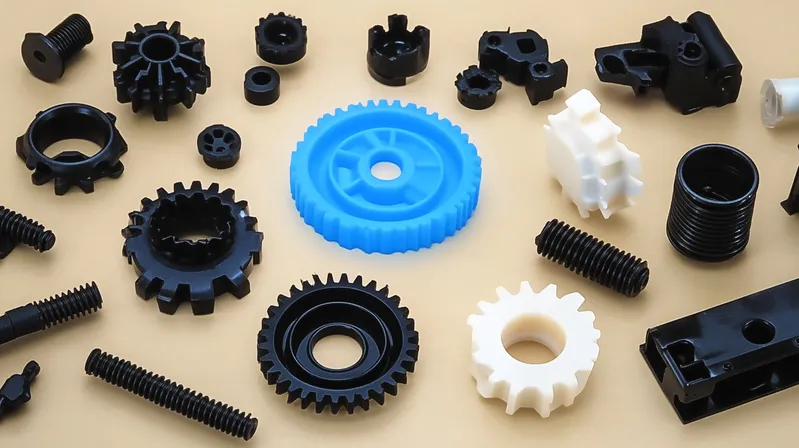
-
Identify Requirements: Determine the part’s functional (e.g., strength), aesthetic (e.g., color), and regulatory (e.g., biocompatibility) needs.
-
Evaluate Options: Compare techniques based on cost, time, material compatibility, and production volume. For example, laser marking is tool-less and precise but may be costlier than pad printing.
-
Plan Integration: Ensure post-processing integrates smoothly into the manufacturing workflow, using automation where possible.
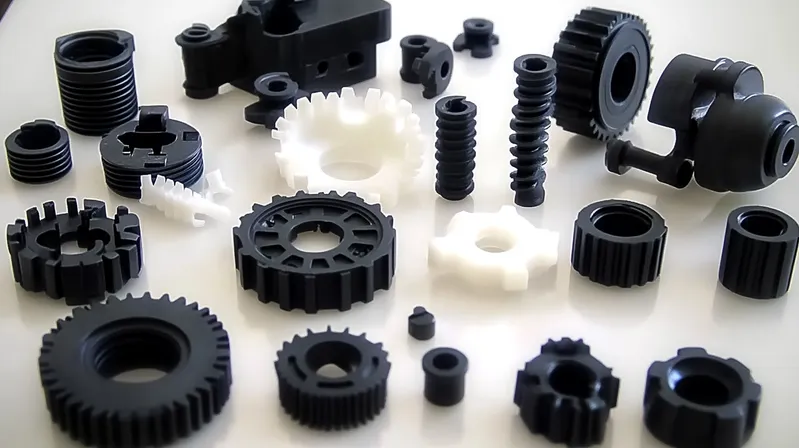
- Decision Tree:
- Aesthetic Needs? → Consider painting, pad printing, or laser marking.
- Functional Assembly? → Evaluate heat staking, ultrasonic welding, or inserts.
- Defect Correction? → Prioritize trimming, deburring, or surface finishing.
- Quality Critical? → Implement visual, dimensional, or NDT inspections.
Decision Factor | Corrective (e.g., Trimming) | Decorative (e.g., Painting) | Functional (e.g., Welding) | Quality Control (e.g., Inspection) |
---|---|---|---|---|
Cost | Low to moderate | Moderate to high | Moderate to high | Low to high (automated systems) |
Time | Fast | Moderate | Moderate | Varies (manual vs. automated) |
Material Impact | Minimal | Requires surface prep | Material-specific | Minimal |
Applications | All industries | Automotive, electronics | Medical, automotive | All industries |
Post-processing in injection molding connects to a broader manufacturing ecosystem:
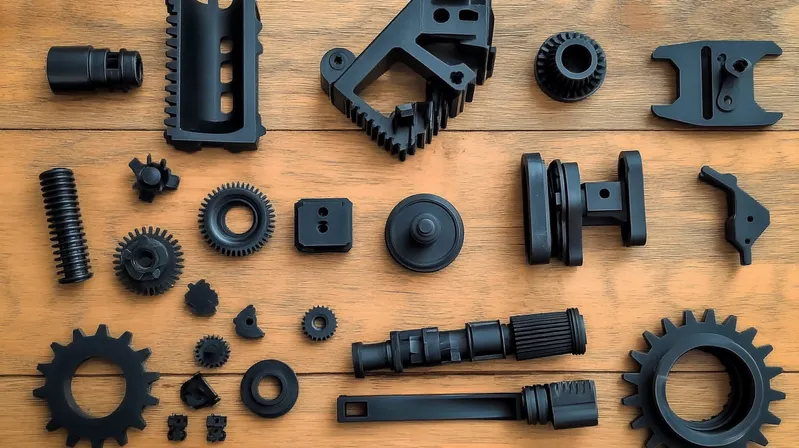
- Upstream Technologies:
- Injection Molding Machines: Advanced machines with precise control reduce defects, minimizing post-processing needs.
- Mold Design Software: Tools like CAD/CAM optimize mold designs for easier ejection and trimming.
- Material Science: Research into plastics with better surface properties or weldability enhances post-processing efficiency.
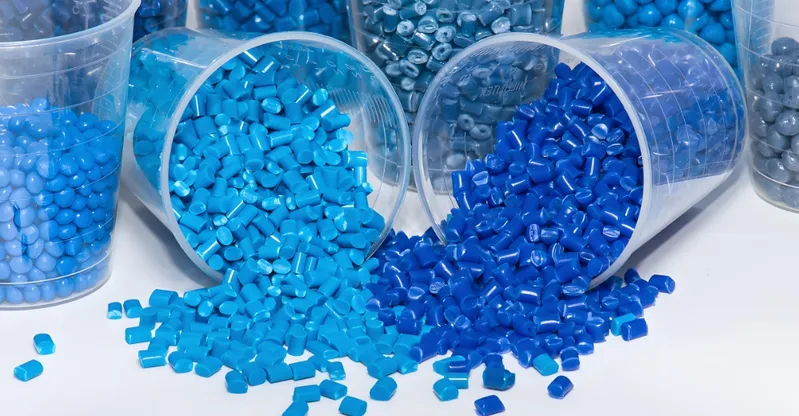
-
Downstream Technologies:
- Automated Assembly Lines: Streamline post-processing tasks like welding or insert installation.
- Packaging Solutions: Custom packaging (e.g., foam, barcodes) protects finished parts during distribution.
- Logistics: Efficient distribution systems ensure timely delivery of post-processed parts.
-
Complementary Technologies:
- CNC Machining: Adds precise features (e.g., holes, threads) post-molding (Protolabs Machining).
- 3D Printing: Useful for prototyping or complex geometries, though it requires different post-processing.
- Robotic Systems: Automate trimming, painting, or inspection for consistency.
- Automated Inspection: Enhances quality control with vision systems or NDT.
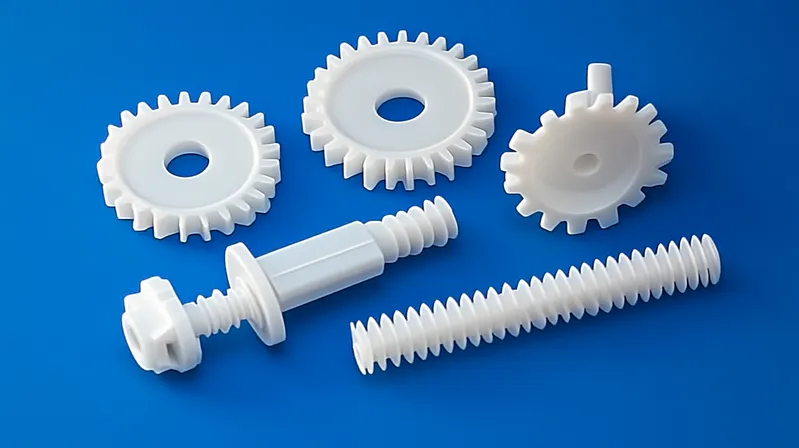
Conclusion
Managing post-processing in injection molding is essential for producing high-quality plastic parts that meet industry standards. By understanding the conceptual framework, application scenarios, technical workflows, and practical tools, manufacturers can optimize their processes and make informed decisions. Early planning, material compatibility, and automation are key to balancing quality with efficiency.
Post-processing is essential for all injection molded parts.False
Some parts may not require post-processing if they meet quality standards directly from the mold.
Automating post-processing can reduce production costs.True
Automation increases efficiency and consistency, potentially lowering overall costs.
-
Exploring best practices for post-processing can help manufacturers enhance quality and efficiency in production. ↩
-
Understanding how post-processing improves injection molded parts can lead to better manufacturing outcomes. ↩
-
Learning strategies for balancing quality and efficiency can significantly improve manufacturing processes and outcomes. ↩
-
Secondary operations play a vital role in enhancing molded parts. Discover more about these techniques and their benefits. ↩
-
Finishing operations are essential for achieving the desired aesthetics and functionality in molded parts. Learn more about these processes. ↩
-
Explore this link to understand various corrective processes that enhance product quality and eliminate imperfections. ↩
-
Learn about plasma treatment’s role in enhancing adhesion for low surface energy plastics, crucial for effective coatings. ↩
-
Discover the importance of biocompatible finishes in medical devices, ensuring safety and compliance in healthcare applications. ↩
-
Exploring CNC machining can provide insights into its precision and efficiency compared to other methods. ↩
-
Learning about 3D printing can reveal its unique advantages for prototyping and custom parts. ↩
-
Understanding post-processing in injection molding can enhance your knowledge of manufacturing techniques and their benefits. ↩