You know, sometimes the smallest things can have the biggest impact, like venting in injection molding.
Venting in injection molds allows trapped air to escape, reducing defects, improving material flow, and optimizing cycle times, thus enhancing product quality and production efficiency.
I remember the first time I really grasped the importance of venting. It was one of those ‘aha!’ moments. By strategically placing vents, I could almost see the invisible air escaping, like a sigh of relief from the mold. This wasn’t just about reducing defects or improving flow; it was about creating something that worked seamlessly. The sense of accomplishment when those first perfect pieces came out was indescribable.
Implementing effective venting isn’t just a technical tweak—it’s a game-changer. It’s like opening a window in a stuffy room; suddenly, everything breathes easier. So, dive deeper into these techniques and watch how they transform your mold designs into high-efficiency masterpieces.
Venting reduces burn marks in injection molding.True
Venting allows gases to escape, preventing burn marks.
Venting increases cycle times in mold design.False
Effective venting optimizes cycle times, reducing them.
Why is Venting in Injection Molding Crucial?
Ever noticed how some plastic gadgets are just perfect while others fall short? The magic often lies in the invisible art of venting during injection molding. Let me take you on a journey to uncover this secret.
Venting in injection molding is all about carving out little pathways for air and gases to escape from the mold cavity. This step is essential to avoid flaws like burn marks and incomplete fills, ensuring both quality and efficiency in the final product.
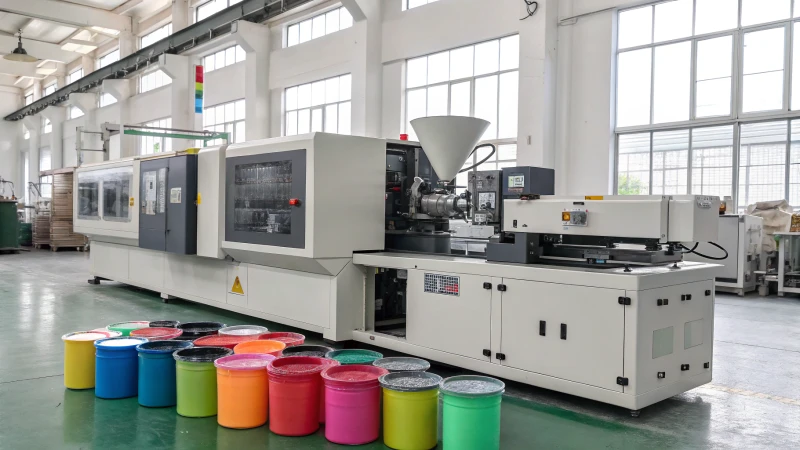
Understanding Venting in Injection Molding
Imagine this: I was working on a project where everything seemed to be going smoothly, but the final product had these pesky burn marks. That’s when I realized venting was the key player I’d been missing. You see, when molten plastic is injected into a mold, it fills up the space, and any trapped air or gases need an escape route. Without these venting paths, you’d end up with those imperfections we dread—burn marks or, worse, parts that don’t fully form.
Types of Venting Techniques
In my experience, experimenting with different venting techniques is like choosing the right tool for the job:
- Parting Line Vents: These are straightforward and budget-friendly, with thin channels at the mold’s parting line letting air out during injection.
- Valve Vents: Picture this as a more sophisticated solution where valves open just in time to release trapped air but then shut tight to keep the plastic in check.
- Porous Metals: These are like the unsung heroes—metal inserts that let air pass through without compromising strength.
Here’s a quick comparison:
Venting Technique | Advantages | Disadvantages |
---|---|---|
Parting Line Vents | Simple, cost-effective | Limited effectiveness |
Valve Vents | High precision | Higher complexity |
Porous Metals | Uniform venting | Costly |
Importance of Proper Venting
Venting isn’t just a technicality; it’s a game-changer for ensuring product quality and consistency. I’ve learned that proper venting can:
- Prevent Defects: By giving gases an exit strategy, venting keeps defects like burns or short shots at bay.
- Reduce Cycle Time: Efficient venting speeds up filling and cooling, cutting down cycle times.
- Improve Surface Finish: A well-vented mold is your best bet for a pristine surface, free from gas entrapment marks.
I remember one time when poor venting led to visible burn marks on transparent parts, resulting in a spike in rejections and waste. To avoid such pitfalls, diving into vent design guidelines1 can be incredibly enlightening. A well-thought-out vent design can truly elevate both the quality and efficiency of your production line.
Venting prevents burn marks in injection molding.True
Venting allows trapped gases to escape, preventing burn marks.
Porous metals are the cheapest venting technique.False
Porous metals are costly due to their material and manufacturing.
How Does Venting Reduce Defects in Molded Parts?
Ever wonder why some molded parts look flawless while others just miss the mark? It’s all about the art of venting.
Venting in molding lets trapped gases escape, curbing defects like short shots, burn marks, and voids. This ensures higher quality parts by maintaining consistent mold cavity pressure and flow dynamics.
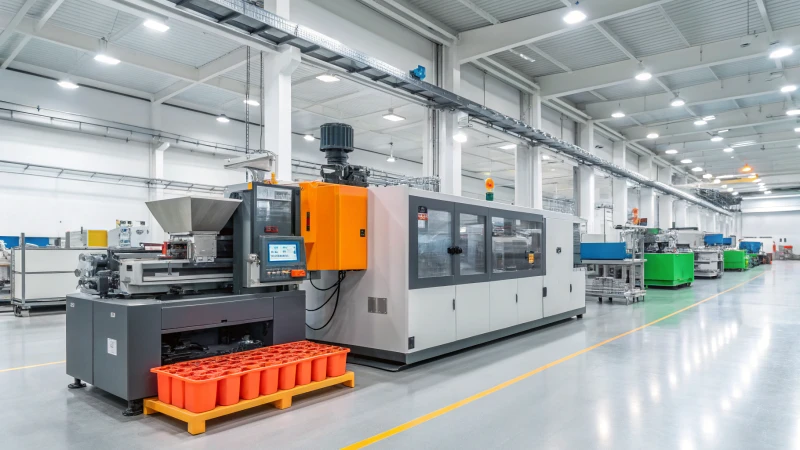
The Role of Venting in Molded Parts
Imagine you’re trying to pour a perfect cup of coffee, but an air bubble keeps splattering hot liquid everywhere—frustrating, right? That’s how it feels when I’m working on injection molding, and venting2 isn’t up to par. Venting involves creating tiny passages within the mold to let trapped air and gases escape, much like giving that stubborn bubble a way out of my morning brew. Without proper venting, these gases can wreak havoc, causing defects from minor surface blemishes to incomplete fillings—known as short shots.
Types of Defects Prevented by Proper Venting
-
Short Shots: I’ve faced the disappointment of a short shot more times than I’d like to admit. It’s when the mold cavity isn’t fully filled, often because trapped air blocks the flow of molten material. Venting helps by expelling that air so the material can fill the mold completely.
-
Burn Marks: Picture this—unwanted black streaks across a pristine white part. That’s what happens when trapped gases ignite. Effective venting reduces this risk significantly, making sure our parts look as good as they function.
-
Voids: These sneaky little air pockets can ruin the integrity of a part. By allowing gases to escape, venting minimizes void formation, much like letting air out of a balloon slowly rather than popping it.
Strategies for Effective Venting
Every time I dive into mold design, understanding venting strategies is crucial. It’s like knowing how to navigate a maze. Consider these methods:
- Venting Channels: Placing channels strategically in high-pressure areas is key. I’ve seen it make or break the quality of the output.
- Use of Porous Materials: Using materials that naturally allow gas passage enhances venting efficiency. It’s like using breathable fabric on a hot day—it just makes sense.
Analyzing Mold Design for Venting
Designing molds with venting in mind is something I’ve learned to approach like planning a road trip route—every exit counts. A poorly designed mold can lead to excessive gas buildup and defects, much like getting stuck in traffic with no way out.
Venting Considerations | Impact on Quality |
---|---|
Channel Placement | Reduces short shots and burn marks |
Material Permeability | Prevents voids and enhances part finish |
Cavity Pressure | Ensures consistent flow dynamics |
For further insights into optimizing venting, I often consult with experts or dive into industry standards on mold design guidelines3. Proper venting not only enhances the quality of molded parts but also boosts production efficiency, cutting down waste and cost. Understanding these principles has been game-changing in making informed decisions during mold design4 and production processes.
Venting prevents short shots in molded parts.True
Venting allows air to escape, ensuring the mold cavity fills completely.
Poor venting increases production efficiency.False
Poor venting leads to defects, reducing efficiency and increasing waste.
How Can Venting Optimize Cycle Times in Production?
Ever felt like your production line is stuck in slow motion? Venting might just be the hidden gem you’re missing.
Venting optimizes cycle times by eliminating defects caused by trapped gases, ensuring molds fill and cool faster. This not only boosts efficiency but also reduces downtime, significantly enhancing productivity.
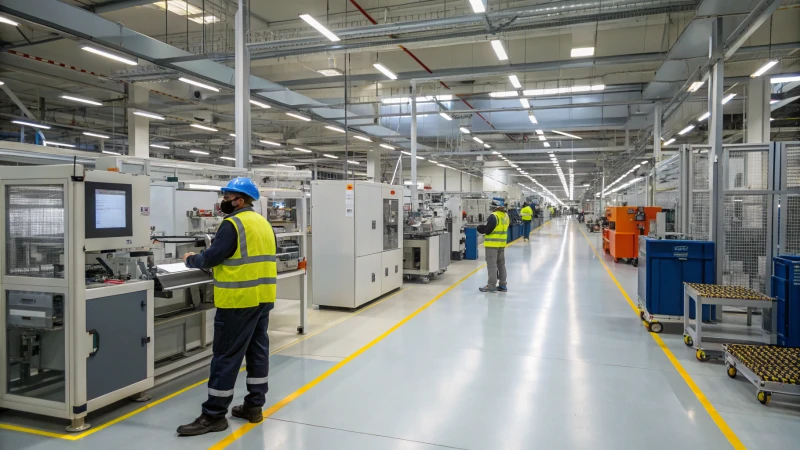
Understanding Venting in Production
Back when I first started in the industry, I remember being puzzled by how something as simple as venting could impact production so profoundly. Venting involves creating passages in molds to let trapped gases escape, a process crucial in manufacturing environments5 that use molten materials. Without adequate venting, gas trapped inside molds can lead to pesky defects like short shots or burns, which I learned the hard way when a project nearly derailed.
Benefits of Proper Venting
-
Reduced Defects: I’ve seen firsthand how proper venting minimizes common defects like burn marks and voids, leading to higher-quality products. Imagine the relief when a defect-free batch rolls out!
-
Improved Mold Filling: Allowing air to escape ensures the material fills the mold cavities completely, saving me countless hours of rework.
-
Faster Cooling: Venting facilitates quicker cooling of parts, crucial for reducing cycle time and getting products out the door faster than ever.
Techniques for Optimizing Venting
-
Venting Channels: These small grooves or openings are designed to release trapped air. The placement and sizing of these channels are everything. It’s like finding the perfect path for water to flow through a maze.
-
Pin Vents: Small pins in the mold aid air escape without affecting part integrity. Picture it like a little secret passageway that makes everything run smoothly.
-
Vacuum Venting: Using a vacuum system to actively remove gases from the mold during production can enhance efficiency even further. It’s a game-changer!
Practical Application in Mold Design
When designing molds, incorporating effective venting strategies is essential. I’ve learned to consider material flow and where gases might accumulate, using CAD software to simulate gas flow and identify potential issues before they become costly mistakes.
Technique | Description | Advantages |
---|---|---|
Venting Channels | Grooves/openings for gas escape | Minimize defects |
Pin Vents | Small pins aiding in air escape | Maintain part integrity |
Vacuum Venting | System actively removes gases | Enhances mold efficiency |
By focusing on these elements, manufacturers can ensure that venting contributes effectively to reducing cycle times, thus optimizing production efficiency. Explore more about effective mold design strategies6 to integrate comprehensive venting solutions into your processes. This approach not only boosts production rates but also improves overall product quality, aligning with strategic manufacturing goals. It’s amazing how something as seemingly simple as venting can make such a difference!
Proper venting reduces production defects.True
Proper venting allows trapped gases to escape, minimizing defects.
Vacuum venting slows down cycle times.False
Vacuum venting actively removes gases, enhancing efficiency and speed.
How Do Material Properties Affect Venting Requirements?
Navigating the world of injection molding can feel like an adventure, especially when it comes to understanding how material properties affect venting. For folks like me, ensuring we get it right is key to creating flawless products.
In injection molding, material properties such as viscosity, thermal conductivity, and shrinkage dictate venting requirements. These characteristics determine how vents are sized and placed, ensuring optimal airflow and preventing common defects.
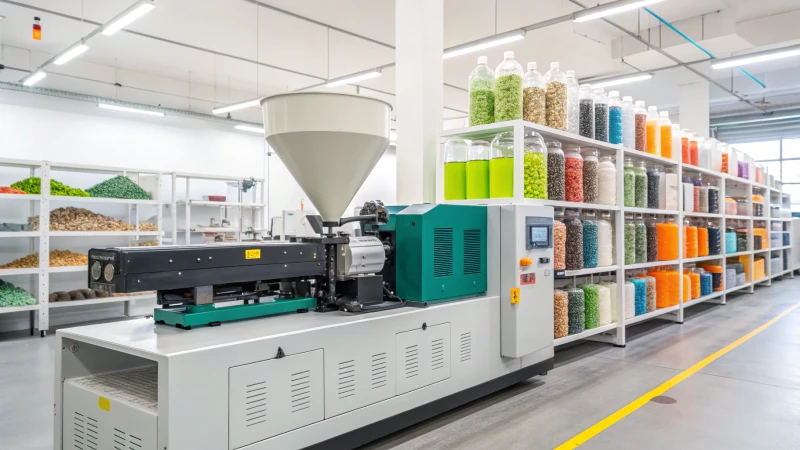
Understanding Material Properties
Having spent years in product design, I’ve come to appreciate just how unique each material can be. It’s not just about picking a material that looks good; it’s about understanding how it will behave when molded. Here are a few properties that often keep me up at night:
- Viscosity: It’s all about how smoothly the material flows.
- Thermal Conductivity: This impacts how quickly the material cools.
- Shrinkage: It’s crucial for determining the final size of a part.
Viscosity and Venting
Let me share a story: early in my career, I underestimated how a high-viscosity material would perform. The result? A nightmare of trapped gases and defects! I quickly learned that such materials require more extensive venting to allow gases to escape smoothly.
Material Type | Viscosity Level | Venting Requirement |
---|---|---|
Low Viscosity | Easy Flow | Minimal Venting Needed |
High Viscosity | Difficult Flow | Extensive Venting Needed |
Exploring viscosity’s role7 can help optimize mold design.
Thermal Conductivity and Cooling
One time, I was working with a material that had low thermal conductivity. I remember how frustrating it was to deal with uneven cooling and warping issues. Proper vent placement became my best friend in achieving uniform cooling.
Understanding thermal effects8 helps in better material selection.
Shrinkage and Mold Design
I’ve learned the hard way that ignoring shrinkage can lead to significant dimensional inaccuracies. With high-shrinkage materials, precise vent placement is not just beneficial—it’s essential. Sometimes, additional supports or post-processing are necessary to meet specifications.
Referencing shrinkage characteristics9 provides insights into managing dimensional changes.
Importance of Proper Venting
Getting venting right is like finding the perfect rhythm in music; it ensures everything flows without a hitch. Proper venting prevents those pesky defects like air traps and burn marks. Aligning vent design with material properties has become a cornerstone of my approach to smoother production.
Exploring venting techniques10 offers guidance on effective mold design strategies.
Higher viscosity materials need larger vents.True
High viscosity hinders flow, requiring larger vents for gas escape.
Low thermal conductivity materials cool faster.False
Low thermal conductivity slows heat dissipation, leading to slower cooling.
Conclusion
Venting in injection molding is crucial for enhancing efficiency by allowing trapped gases to escape, reducing defects, improving material flow, and optimizing cycle times for higher quality products.
-
These guidelines are vital for designing effective vent systems, crucial for improving product quality and efficiency. ↩
-
This link explains the significance of venting in injection molding, highlighting its role in preventing defects and ensuring product quality. ↩
-
Explore established guidelines and standards for mold design that help optimize venting and improve production outcomes. ↩
-
This resource provides insights into enhancing mold design to achieve effective venting and minimize defects. ↩
-
Understand why venting is critical in manufacturing processes and its role in quality control. ↩
-
Learn strategies for integrating efficient venting solutions in mold design to enhance production cycles. ↩
-
Learn about the impact of viscosity on mold flow and how it influences venting strategies. ↩
-
Explore how thermal properties determine cooling rates and influence vent design. ↩
-
Understand how shrinkage affects mold design and vent placement. ↩
-
Discover various techniques to optimize venting and improve product quality. ↩