Injection molding is a cornerstone of modern manufacturing, enabling the production of complex plastic parts with high precision and efficiency. However, one of the most critical yet often overlooked aspects of this process is cooling time—the period during which the molten plastic cools and solidifies inside the mold before ejection. Cooling time typically accounts for 80-85% of the total cycle time, making it a key factor in both production efficiency and part quality 1. Mismanaging this phase can lead to defects like warping or sink marks, while optimizing it can significantly boost productivity without compromising quality.
In this guide, we’ll explore the intricacies of cooling time, from the factors that influence it to practical strategies for optimization. Whether you’re a designer, engineer, or manufacturer, understanding cooling time is essential for mastering injection molding.
Cooling time is the most time-consuming part of the injection molding cycle.True
Cooling time typically accounts for 80-85% of the total cycle time, making it a critical factor in production efficiency.
Optimizing cooling time can improve production efficiency without affecting part quality.True
When done correctly, reducing cooling time enhances productivity while maintaining or even improving part integrity.
- 1. What Is Cooling Time in Injection Molding?
- 2. What Factors Influence Cooling Time in Injection Molding?
- 3. How Can Cooling Time Be Optimized in Injection Molding?
- 4. What Are the Practical Considerations for Managing Cooling Time?
- 5. What Technologies Are Related to Cooling Time in Injection Molding?
- 6. Conclusion
What Is Cooling Time in Injection Molding?
Cooling time in injection molding refers to the duration required for the injected molten plastic to cool and solidify sufficiently to withstand ejection forces without deforming. This phase is crucial because it ensures the part achieves the desired strength, dimensional accuracy, and surface finish. However, it also represents the longest portion of the molding cycle, directly impacting production rates and costs 2.

Cooling time is the period during which molten plastic solidifies in the mold, typically accounting for 80-85% of the cycle time, and is critical for part quality and production efficiency.
Factor | Impact on Cooling Time |
---|---|
Part Thickness | Increases with thickness |
Material Properties | Varies with thermal conductivity |
Mold Design | Efficient cooling channels reduce time |
Mold Temperature | Lower temperatures speed up cooling |
Why Is Cooling Time Important?
Proper cooling ensures that parts are free from defects such as warping, shrinkage, or incomplete solidification. However, excessive cooling time can slow down production, while insufficient cooling can compromise part integrity. Striking the right balance is essential for efficient and high-quality manufacturing 3.
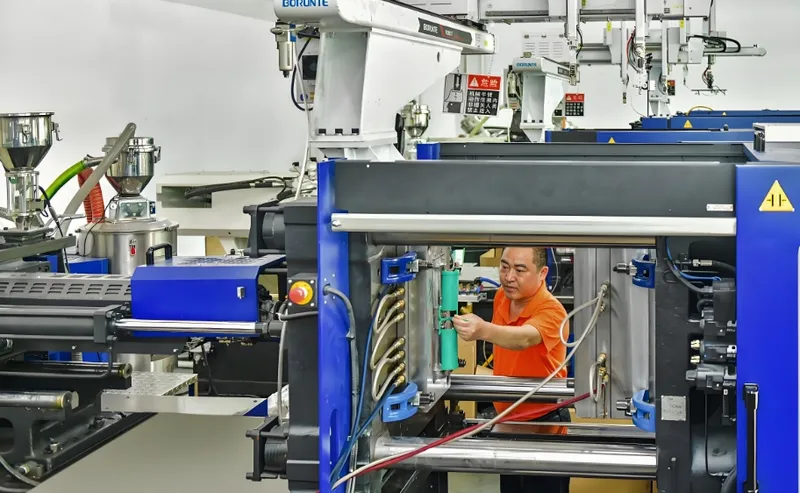
Cooling time directly affects the dimensional accuracy of molded parts.True
Adequate cooling ensures the part solidifies correctly, maintaining precise dimensions and preventing defects.
Cooling time is only critical for large, thick parts.False
Even thin parts require precise cooling to avoid defects like warping or poor surface finish.
What Factors Influence Cooling Time in Injection Molding?
Several factors determine how quickly a part cools in the mold, and understanding these can help manufacturers optimize the process.
Key factors affecting cooling time include part thickness, material properties, mold design, and mold temperature, each playing a significant role in heat transfer and solidification.
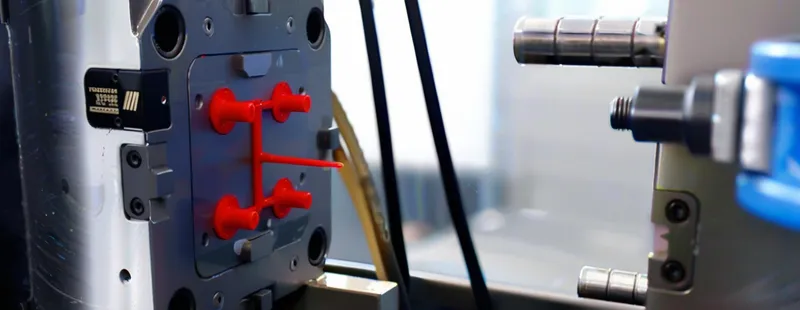
Part Thickness
Part thickness is the most significant factor, as cooling time increases with the square of the thickness. This means even small increases in thickness can lead to disproportionately longer cooling times 4. For example, a part twice as thick may take four times longer to cool.
Material Properties
Different plastics have varying thermal properties, such as thermal conductivity and specific heat, which affect cooling rates. Materials like nylon, with higher thermal conductivity, cool faster than those like polypropylene 5.
Material | Thermal Conductivity (W/m·K) | Specific Heat (J/kg·K) | Cooling Time Impact |
---|---|---|---|
ABS | 0.2 – 0.3 | 1400 – 1600 | Moderate |
Polypropylene | 0.1 – 0.2 | 1800 – 2000 | Longer |
Polycarbonate | 0.2 – 0.25 | 1200 – 1300 | Moderate to longer |
Nylon | 0.25 – 0.35 | 1600 – 1700 | Shorter |
Mold Design
The design of cooling channels within the mold is crucial. Efficiently placed channels, especially near thick sections, can significantly reduce cooling time. Advanced techniques like conformal cooling, where channels follow the part’s geometry, can further enhance heat removal 6.
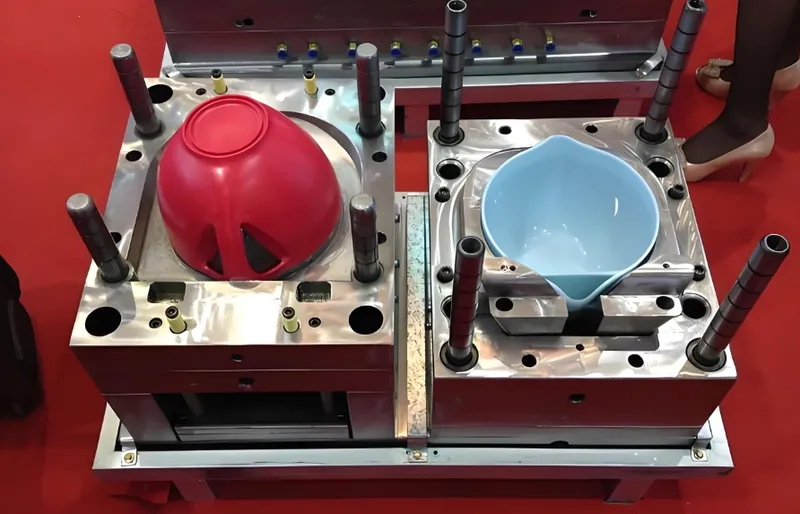
Mold Temperature
Lower mold temperatures accelerate cooling by increasing the temperature gradient between the plastic and the mold. However, this can affect surface finish and may introduce residual stresses, so it must be balanced with part quality requirements 7.
Cooling time is directly proportional to the square of the part thickness.True
The cooling time formula shows that thickness has a squared effect, making thicker parts much slower to cool.
Using a higher mold temperature reduces cooling time.False
Higher mold temperatures actually increase cooling time by reducing the temperature difference between the plastic and the mold.
How Can Cooling Time Be Optimized in Injection Molding?
Optimizing cooling time involves reducing it without sacrificing part quality. This requires a strategic approach to material selection, mold design, and process control.
Cooling time can be optimized through material selection, efficient mold design, process adjustments, and simulation tools, balancing speed and quality.
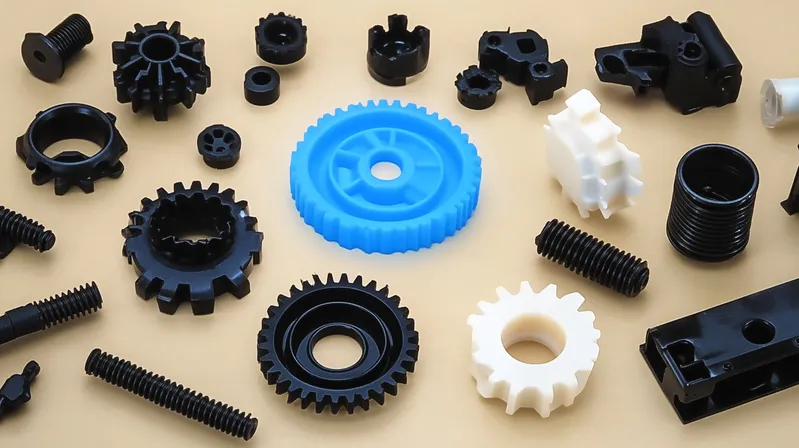
Material Selection
Choosing materials with higher thermal conductivity, such as nylon over polypropylene, can reduce cooling time. However, material choice must align with the part’s functional requirements 8.
Mold Design Improvements
Implementing conformal cooling channels or using high-conductivity mold materials like aluminum can enhance heat transfer. Conformal cooling, in particular, can reduce cooling time by up to 30% compared to traditional methods 9.
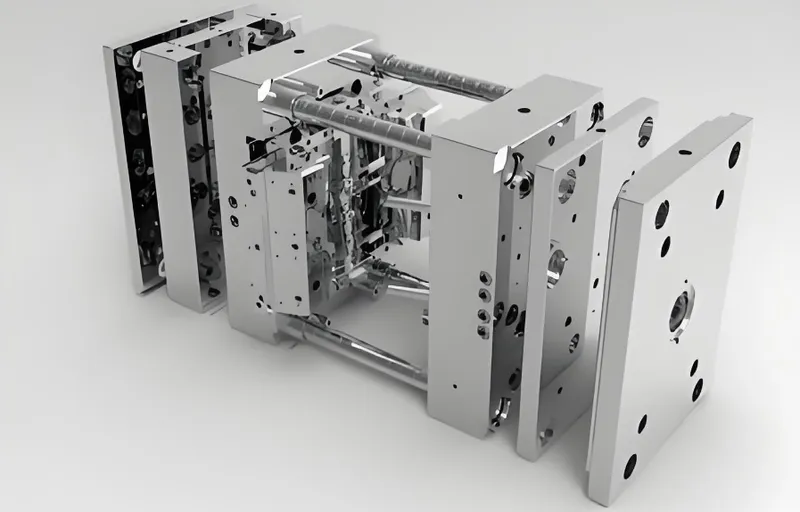
Process Parameter Adjustments
Fine-tuning parameters like mold temperature, coolant flow rate, and injection speed can optimize cooling. For example, increasing coolant flow improves heat removal but must be managed to avoid issues like mold condensation 10.
Simulation and Modeling
Using software like Moldflow or SolidWorks Plastics to simulate the cooling process allows engineers to predict and optimize cooling time before production, reducing trial-and-error costs 11.
Conformal cooling can significantly reduce cooling time in injection molding.True
By following the part’s geometry, conformal cooling channels improve heat transfer efficiency, cutting cooling time by up to 30%.
Simulation tools are unnecessary for optimizing cooling time.False
Simulation software helps predict cooling behavior, allowing for optimized mold design and process settings before physical trials.
What Are the Practical Considerations for Managing Cooling Time?
To effectively manage cooling time, designers and manufacturers should follow best practices in part design, mold design, and process control.
Practical considerations include minimizing wall thickness variations, optimizing cooling channel placement, selecting appropriate materials, and monitoring process parameters.
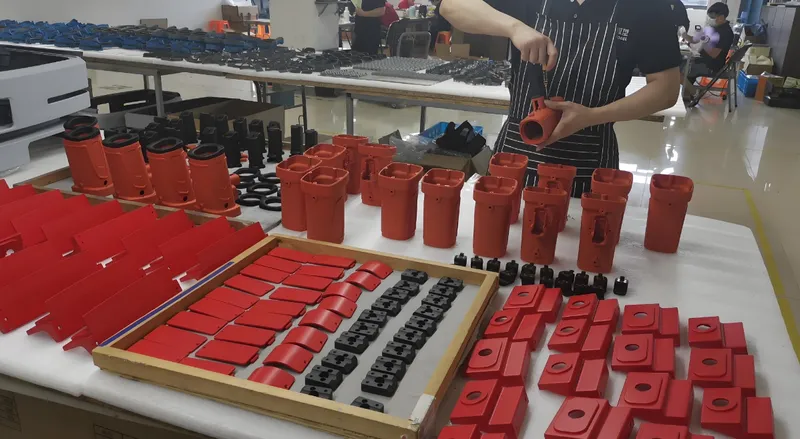
Part Design
-
Uniform Wall Thickness: Ensures even cooling and prevents defects like warping.
-
Avoid Thick Sections: Use ribs or other features to maintain strength without increasing thickness.
-
Draft Angles: Facilitate ejection and reduce stress during cooling.
Mold Design
- Cooling Channel Placement: Position channels near thick sections for efficient heat removal.
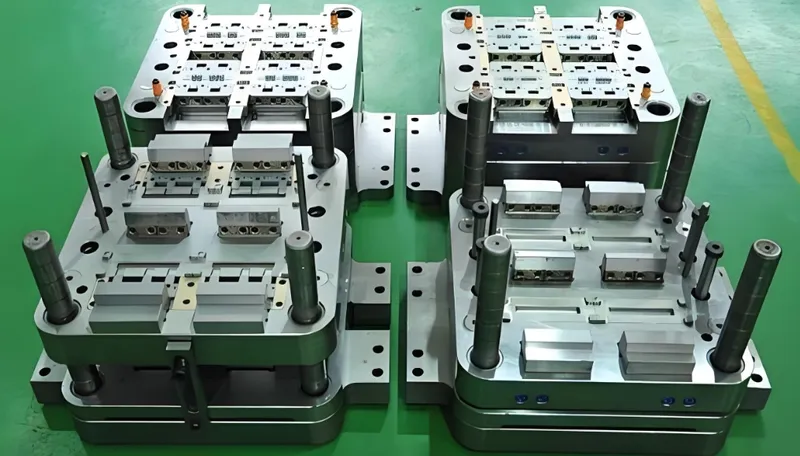
-
Conformal Cooling: Consider for complex parts to enhance cooling uniformity.
-
Venting: Ensure adequate venting to prevent air traps that cause uneven cooling.
Material Selection
- Thermal Properties: Choose materials with higher thermal diffusivity for faster cooling.
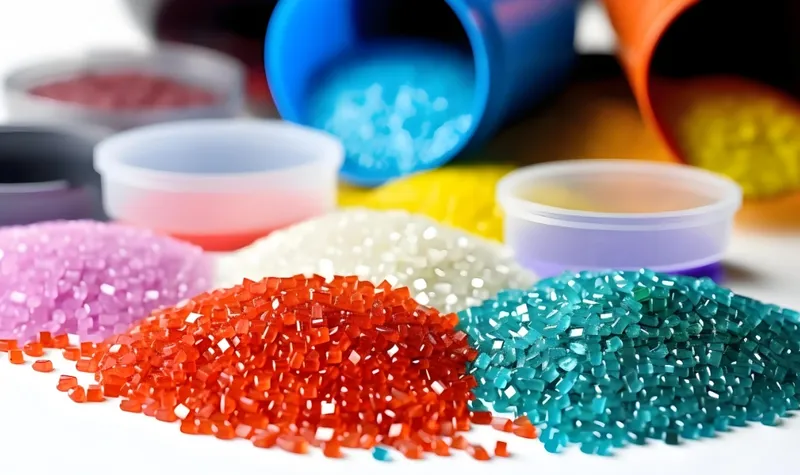
- Verify Specifications: Use reliable data from manufacturers, not third-party sources.
Process Control
- Mold Temperature: Set appropriately for the material and part requirements.
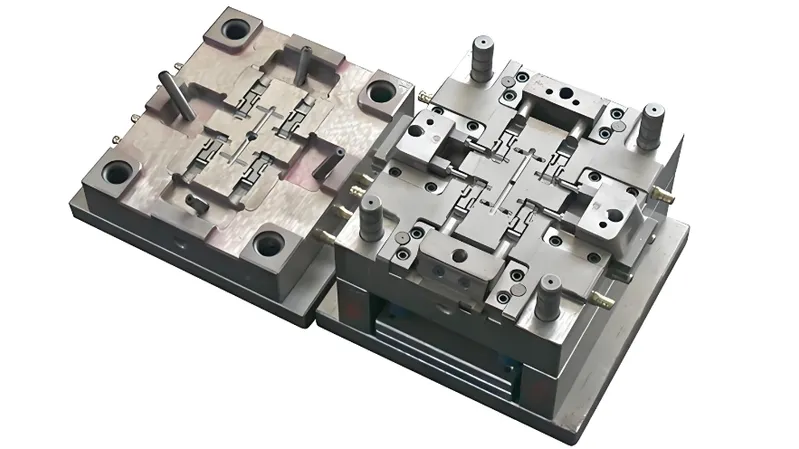
-
Coolant Flow: Adjust flow rates to maintain consistent mold temperature.
-
Monitoring: Use sensors to track cooling performance in real-time.
Uniform wall thickness is critical for even cooling in injection molding.True
Variations in thickness can lead to uneven cooling, causing defects like warping or sink marks.
Cooling time optimization is only relevant for high-volume production.False
Even in smaller batches, optimizing cooling time improves part quality and reduces energy consumption.
Several advanced technologies and processes can further enhance cooling efficiency and overall molding performance.
Related technologies include conformal cooling, multi-material molding, alternative molding processes, 3D-printed molds, and simulation software.
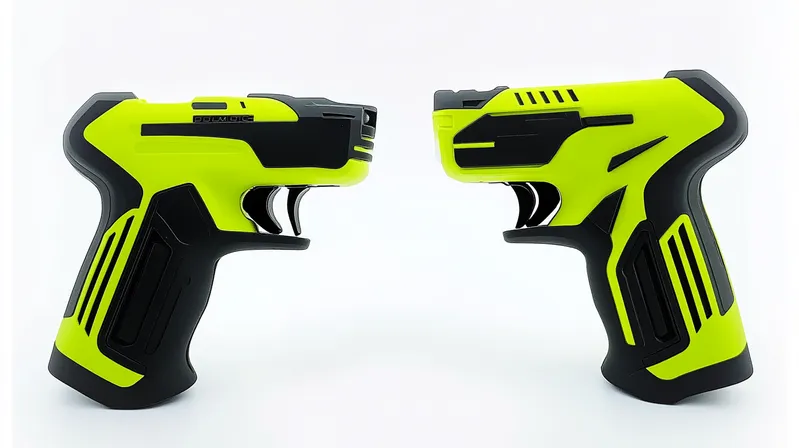
Conformal Cooling
This technique uses cooling channels that conform to the part’s shape, improving heat transfer and reducing cooling time significantly 12.
Multi-Material Injection Molding
In processes like overmolding, different materials may have varying cooling rates, requiring precise mold design to ensure uniform cooling 13.
Alternative Molding Processes
Techniques like blow molding or compression molding have different cooling requirements and may be suitable for specific applications where injection molding’s cooling time is a limitation.
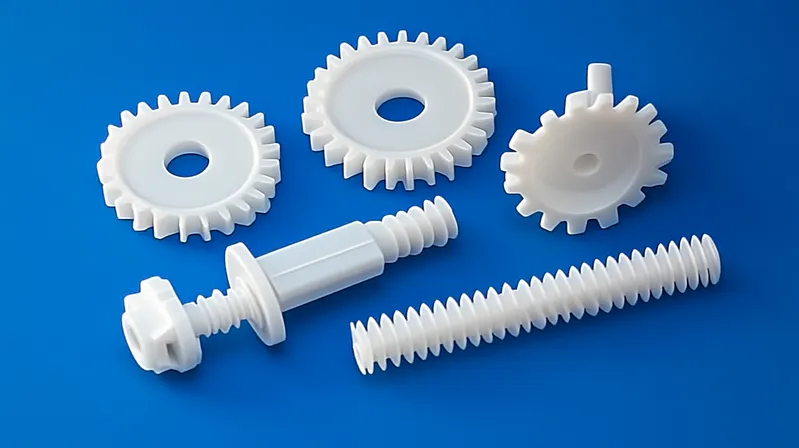
3D-Printed Molds
Additive manufacturing allows for molds with complex, integrated cooling channels, potentially reducing cooling time and improving part quality 14.
Simulation Software
Tools like Moldflow or ANSYS simulate the cooling process, helping engineers optimize mold design and process parameters before production 15.
3D-printed molds can incorporate complex cooling channels for better heat management.True
Additive manufacturing enables the creation of molds with intricate cooling designs that traditional methods cannot achieve.
Multi-material molding simplifies cooling time management.False
Different materials may have varying cooling rates, complicating the process and requiring careful design to ensure uniform cooling.
Conclusion
Cooling time is a pivotal aspect of injection molding, influencing both production efficiency and part quality. By understanding the factors that affect cooling—such as part thickness, material properties, and mold design—manufacturers can implement strategies like conformal cooling, material selection, and process adjustments to optimize this phase. Practical considerations, including uniform part design and precise process control, further enhance outcomes. As injection molding evolves, staying informed about related technologies like 3D-printed molds and simulation tools will be key to maintaining competitive and efficient production.
-
How to Determine Injection Molding Cooling Time – RJG, Inc. ↩
-
The Importance of Cooling Time in Plastic Injection Molding – Midstate ↩
-
Cooling Rate in Injection Molding: A Comprehensive Guide – Hansen Plastics ↩
-
A Comprehensive Overview of Injection Molding Cooling Time – Zhongde ↩
-
Cooling Methods and Design in Injection Molding – Crescent Industries ↩
-
Injection Molding Cooling Time: A Breakdown – Design World ↩
-
What Goes into Injection Molding Cooling Time? – Medical Design and Outsourcing ↩
-
What You Need To Know About Material Compatibility For Multi-Material Injection Molding – SyBridge Technologies ↩
-
8 Recent Innovations in Plastic Injection Molding – Polymer Molding ↩
-
The Science Behind Injection Molding Technology – Seasky Medical ↩