Have you ever thought about why multi-stage injection molding feels so confusing?
The main technical difficulties in multi-stage injection molding involve complicated setting of parameters. High accuracy in process control is required. The method must adapt to different material properties and mold designs. Strong equipment performance and stability are crucial. Robust performance is important.
I remember the first time I learned about multi-stage injection molding – it felt like solving a Rubik’s Cube with closed eyes. Each step needed accuracy, from adjusting the injection speed to changing the pressure. Every tiny detail mattered. The material’s peculiarities and the mold’s complexities seemed very important. Each of them could succeed or spoil the process. Now, let’s explore these challenges more and look at ways to handle them well.
Multi-stage injection molding requires precise parameter settings.True
Complex parameter settings are crucial for quality in multi-stage processes.
Material properties have no impact on injection molding.False
Material properties significantly affect the molding process and outcomes.
How Do I Accurately Determine Injection Speed and Position?
Do you ever think about how small details, such as how fast we inject and where we inject, lead to perfect molding? Join me on this journey to understand this complex process.
Accurately determining injection speed and position requires evaluating the product’s shape, size and the mold runner system. Material properties are also important. Use actual data and simulations. Rely on personal experience. Establish the best settings for each injection stage.
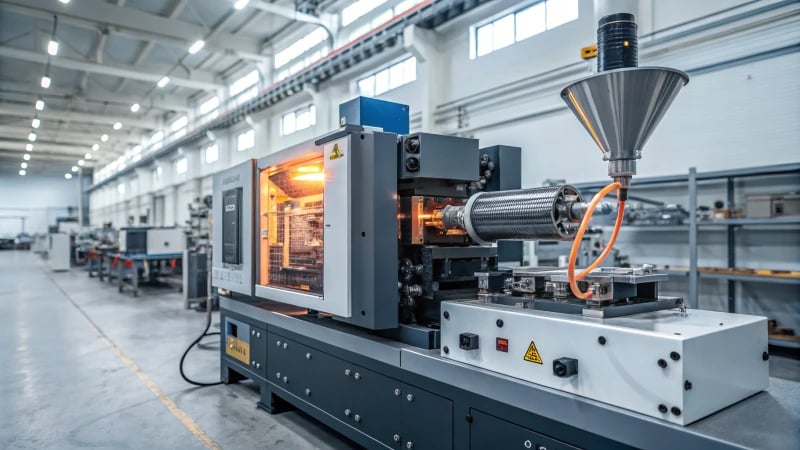
Factors that Change Injection Speed and Position
Molding needs the right injection speed and position. It is similar to creating a beautiful artwork. The process starts by knowing the shape and size of your product. I once worked on a hard project with a tricky inner cavity. The secret was in the small details – adjusting settings meant perfect results.
The mold’s runner system is also very important. Hot runners1 and cold runners have different flow styles that control speed and position. Also, material characteristics must be considered. Some time ago, I dealt with thick polycarbonate, where controlling speed was necessary to stop material damage.
Technical Problems in Setting Parameters
Choosing these settings is like walking on a tight wire. One choice must fit perfectly with the next. High injection speed or pressure might cause extra flash, while low values could mean incomplete filling. In one project, abrupt speed changes left visible marks. It taught me the value of smooth transitions.
Parameter | Challenge |
---|---|
Injection Speed | Ensures smooth filling |
Pressure Matching | Prevents defects like flash |
Speed Switching | Avoids flow marks |
Tools and Methods for Better Performance
Luckily, modern tools really help. Simulation software2 is my favorite for guessing outcomes. Examining different speeds and positions with simulations refines my methods before actual production.
Testing is also very useful. Past test results are full of useful information. They help decide the best current settings.
Effect of Equipment on Performance
If the equipment is too weak, nothing else matters. A quick injection molding machine is key for precise work. Consistent quality during long runs is vital, without any problems.
As I navigate these challenges, it’s clear that balancing design with material and equipment is crucial. Success depends on combining simulations with real data.
Explore more about injection molding equipment3 capabilities to expand your knowledge.
Hot runner systems offer better flow dynamics.True
Hot runner systems maintain material temperature, improving flow consistency.
High-viscosity materials require faster injection speeds.False
High-viscosity materials need controlled speeds to prevent defects.
How Can I Perfect Pressure Matching and Adjustment in Injection Molding?
Exploring how to adjust pressure in injection molding might seem challenging. Small changes sometimes create big differences. Believe me, these tiny adjustments matter a lot.
To become good at handling pressure during injection molding, pay attention to setting the correct injection speeds and positions. Smooth transitions really matter. Control holding pressures with care based on the material and mold details.
%[A high-tech injection molding machine in operation with visible controls and gauges.]https://www.moldall.com/wp-content/uploads/2024/11/industrial-injection-molding-machine-factory-1.webp”High-Tech Injection Molding Machine")
Injection Speed and Position
When determining injection speed and position, it’s essential to account for product shape, size, and mold runner systems. For complex parts like automotive components, precise judgment of melt flow is necessary. This may involve analyzing melt flow dynamics4 across different filling stages. Experience and extensive test data are invaluable here.
Importance of Pressure Matching
Injection pressure must align with speed to ensure smooth cavity filling. Adjust pressures based on wall thickness and material properties. Excessive pressure might cause defects like flash, while inadequate pressure can lead to insufficient filling or weld marks. A balance is crucial for quality outcomes.
Parameter | Effect | Adjustment Required |
---|---|---|
High Pressure | Flashing | Decrease |
Low Pressure | Weld Marks | Increase |
Ensuring Smooth Speed Transitions
In multi-stage injection processes, seamless speed transition prevents defects such as flow marks. This requires precise control to avoid unstable melt flow. Evaluate the equipment’s responsiveness to transitions for improved quality.
Holding Pressure Control
Holding pressure impacts dimensional accuracy and stability. Precisely control parameters like pressure and time to counteract melt shrinkage during cooling. Different materials5 require varied pressure settings, demanding attention to material-specific needs.
Material Properties and Mold Structure Adaptation
Material viscosity and thermal stability dictate process adjustments. For instance, polyethylene allows faster speeds compared to polycarbonate. Additionally, mold structures like gate form and runner layout affect flow behavior. Adapt parameters to accommodate mold characteristics6.
Equipment Performance Requirements
The response speed of injection molding machines is critical. Fast, accurate adjustments to screw speed and injection pressure are necessary for precise control. Stability and repeatability of equipment ensure consistent performance across production runs. Monitor equipment regularly to maintain optimal functionality.
Incorporating these practices enhances the effectiveness of pressure matching and adjustment, leading to superior product quality and consistency in injection molding processes.
High pressure can cause flashing defects.True
Excessive injection pressure leads to material escaping mold cavities, causing flash.
Low pressure reduces the risk of weld marks.False
Inadequate pressure can result in incomplete filling, increasing weld mark occurrence.
How Do Material Properties Influence Multi-Stage Injection Parameters?
Tiny details of material properties really impact the success of your injection molding project. Small characteristics decide the outcome.
Material properties like viscosity, fluidity and thermal stability are important. They impact how we adjust speed, pressure and temperature. These adjustments help in filling molds well and producing high-quality products.
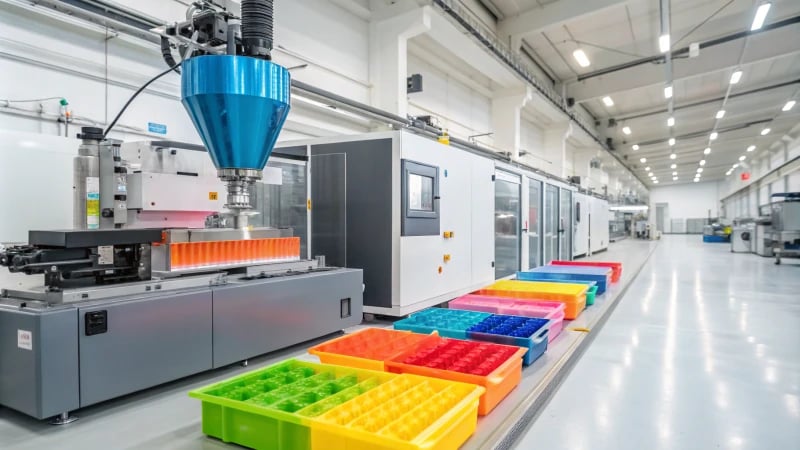
Key Material Properties Affecting Injection Parameters
I recall my early days at the mold factory, facing the challenge of adjusting to various material properties. Different materials have unique viscosity7 characteristics. For instance, low-viscosity materials like polyethylene allow faster injection speeds, speeding up production. Conversely, high-viscosity materials like polycarbonate require slow, controlled speeds to avoid degradation and frustration.
Material Type | Recommended Speed | Reason |
---|---|---|
Polyethylene | High | Low viscosity |
Polycarbonate | Low | High viscosity, heat sensitivity |
Understanding these thermal stability8 traits is crucial. Countless hours went into adjusting temperatures, knowing that one mistake could ruin heat-sensitive materials.
Influence of Mold Structure
The structural design of the mold also affects parameter settings. The mold itself plays a silent but crucial role in determining melt flow behavior through its characteristics such as gate form and runner layout. On one project, I noticed hot runner molds need different settings than cold runner molds due to their unique thermal dynamics.
For instance:
- Hot Runner Molds: Generally maintain consistent temperature, influencing smoother flow and potentially higher speeds.
- Cold Runner Molds: May require slower speeds to accommodate cooling and solidification stages.
Matching Pressure with Material Properties
Matching pressure to material properties was like solving a puzzle. Injection pressure must match the material’s ability to fill the cavity without defects like flash or weld marks. Early experiments showed varying wall thickness needs careful pressure adjustments.
Material Thickness | Pressure Level | Issues to Address |
---|---|---|
Thick | High | Avoid underfilling |
Thin | Lower | Prevent flash and stress marks |
Importance of Accurate Speed Switching
Smooth transition between speeds during multi-stage injection is crucial. Mistakes here cause ugly flow marks. Materials with low viscosity demand precise speed changes to keep both appearance and quality intact.
Ensuring that each stage aligns with the material’s characteristics requires precise adjustment of both speed and holding pressure to manage shrinkage during cooling—a task that varies greatly between different materials9. This complexity necessitates a deep understanding of both material behavior and mold design intricacies learned through trial and error.
Every project taught me something new about balancing these elements. Even small adjustments can truly affect the quality of results.
Polyethylene requires high injection speeds.True
Due to its low viscosity, polyethylene allows faster injection speeds.
Cold runner molds require higher speeds than hot runner molds.False
Cold runner molds generally need slower speeds to manage cooling stages.
How Does Equipment Performance Affect Multi-Stage Injection Success?
Ever thought about how your injection molding machines affect your production? I will share my experiences and insights from the industry.
Equipment performance is key in multi-stage injection molding. It influences precision and stability. Quality depends on it. The machine’s speed is very important. Consistency also plays a vital role. Desired results depend on these factors. They’re essential.
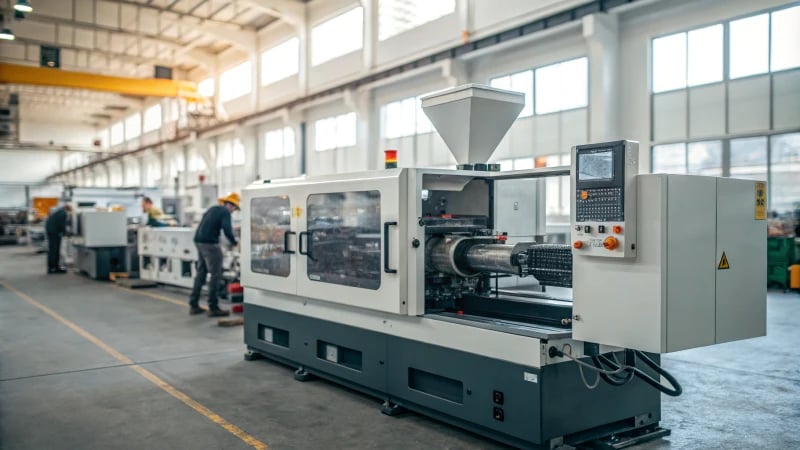
The Effect of Quick Response
Working with multi-stage injection molding, the quick response10 of equipment is absolutely important. Imagine tuning a musical instrument during a show – each moment matters and accuracy rules. Fast, accurate controls let us change screw speed and injection pressure easily. Equipment delay brings uneven mold filling, much like playing a wrong note.
Consistency and Reproducibility
Stable machinery feels like a dependable band rhythm – it produces the same result every time. Keeping output steady during long stretches is crucial. Tiny variations lead to different product quality, impacting production efficiency11. It’s like a drummer missing a beat.
Pressure Coordination and Alteration
Syncing speed and pressure is key, much like instruments harmonizing in an orchestra. Machines must align these to fill molds well. Misaligned settings cause flaws, similar to a wrong note in an orchestra. Proper pressure adjustment is crucial for material compatibility12.
Smooth Speed Change
Moving between injection speeds needs to be smooth as a pianist shifting tunes. Any problem leads to unstable melt flow, causing defects much like static in a recording. The smoothness of these transitions13 directly affects the final product’s appearance and structural integrity.
Parameter | Importance |
---|---|
Quick Response | Ensures timely adjustments during injection stages |
Consistency | Maintains consistent product quality over long productions |
Pressure Coordination | Matches speed and pressure for effective cavity filling |
Speed Transition | Prevents defects by ensuring smooth changes in speed |
Each part of equipment function affects the outcome of multi-stage injections14. It’s like conducting music where all notes count. Quality and efficiency meet precise project needs, highlighting the critical nature of having well-maintained machinery in manufacturing.
Fast response speed prevents mold filling defects.True
A quick response ensures timely adjustments, avoiding defects.
Inconsistent speed transitions improve product quality.False
Unstable transitions cause defects, reducing product quality.
Conclusion
Multi-stage injection molding presents challenges like complex parameter settings, high accuracy requirements, and adaptability to material properties, demanding precise control for optimal production outcomes.
-
Understand how different runner systems affect flow dynamics, influencing injection speed and position. ↩
-
Discover powerful tools that predict outcomes based on different speed and position settings. ↩
-
Learn how advanced machinery ensures precision in multi-stage injections, enhancing product quality. ↩
-
Learn how melt flow dynamics influence injection speeds and positions, aiding in precise parameter settings. ↩
-
Discover how different materials require unique holding pressure settings for optimal molding results. ↩
-
Understand how mold design impacts the flow behavior and parameter settings in injection processes. ↩
-
Learn how varying viscosities of materials influence injection speeds and settings for better mold filling. ↩
-
Discover why maintaining precise temperatures for heat-sensitive materials is crucial in preventing degradation. ↩
-
Gain insights into how different materials dictate specific parameter adjustments in injection molding. ↩
-
Understanding response speed can help ensure precise adjustments during multi-stage injections. ↩
-
Stability guarantees consistent product quality, enhancing overall production efficiency. ↩
-
Proper pressure matching can prevent common defects like flash or weld marks. ↩
-
Smooth speed transitions are vital to prevent surface defects on molded products. ↩
-
Exploring these factors provides insights into achieving high-quality multi-stage injections. ↩