Do you ever think about why some products seem wrong? Products sometimes seem off. Design plays a big role. A strange shape or awkward color might cause confusion. Sometimes designers forget about the small details. These details truly matter. Bad lighting or strange textures can also create problems. People notice these issues. These things are important. Customers really deserve better designs.
Not enough mold filling damages products. Defects include short shots, rough surfaces and size problems. Adjustments solve these issues. Change the runner system. Modify injection settings. Pick suitable materials. This approach helps mold filling. Perfect mold fill is important.
I’ve experienced many headaches with this. Frustration hits when a product comes out of the mold and looks incomplete. Discovering the main reasons and exploring the details truly changes how you manufacture things. This journey really leads to perfect molded parts. Perfect parts.
Optimizing the runner system prevents short shots.True
Improving runner design enhances material flow, reducing short shots.
Surface roughness increases with higher injection pressure.False
Higher injection pressure generally reduces surface roughness by improving fill.
How does insufficient mold filling impact product appearance?
Have you ever thought about how a small problem in mold filling might change your smooth design into something less attractive? Some details show why these flaws happen and how to solve them.
Not enough mold filling results in defects. Short shots, rough surfaces and size changes often occur. These problems spoil the look. They also weaken the product’s function.
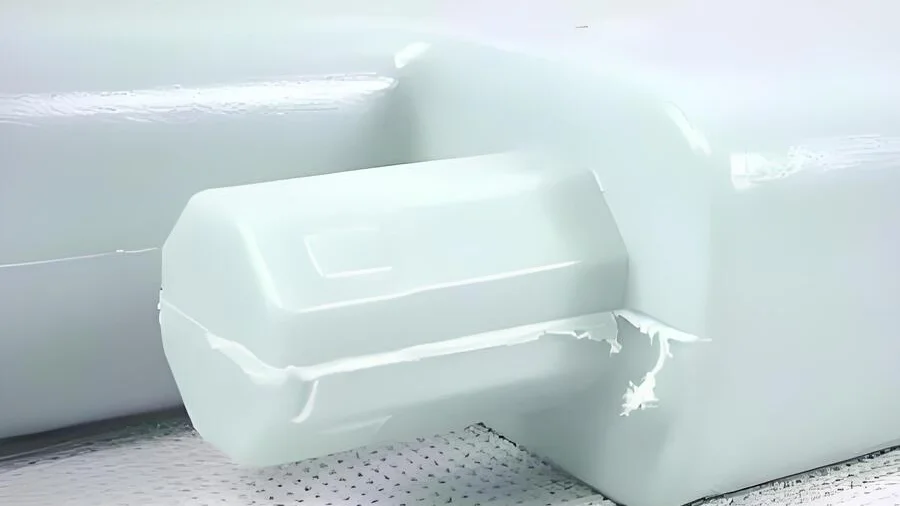
The Effect on Looks
When mold cavities aren’t completely filled, several aesthetic problems can arise. The most notable is the short shot phenomenon, where sections of the product remain visibly incomplete. This often occurs in areas with complex shapes or thin walls, such as narrow handles. Parts of your creation end up incomplete, spoiling its smooth look.
Another common defect is increased surface roughness. Imagine expecting a smooth finish but getting texture like sandpaper. This happens when plastic doesn’t move well, leaving bad marks and ripples. In transparent products, this defect can significantly reduce transparency and gloss, making it a critical issue to address.
Moreover, insufficient mold filling can cause dimension deviation, where products end up smaller than their intended size. Have you ever dealt with parts that won’t fit, no matter how you twist them? This deviation is particularly problematic for parts that need to fit precisely with others.
Defect | Description |
---|---|
Short Shot Phenomenon | Incomplete filling in complex or thin-walled areas. |
Increased Surface Roughness | Unstable flow leading to marks and reduced gloss, especially in transparent items. |
Dimension Deviation | Smaller-than-designed size affecting fit and functionality. |
Fixing Flaws
Optimizing Mold Design: Changing the runner system1 greatly helps alleviate filling issues. Making the main and branch runners bigger enhances the flow of plastic melt into the cavity, reducing pressure loss and ensuring proper filling.
Adjusting gate design is also key. Picking the right gate type and positioning it appropriately allows for even filling. For instance, pin-point gates work well for thin-walled products due to their high-speed and high-pressure capabilities.
Improving Exhaust System: A well-designed exhaust is crucial for preventing defects. Adding exhaust grooves in places filled last helps air and gases escape, stopping back pressure that disrupts filling.
Solution Area | Strategy |
---|---|
Mold Design | Optimize runner and gate design for better flow distribution. |
Exhaust System | Implement strategic exhaust grooves to release air and prevent defects. |
Process Tweaks
Injection Molding Settings: Raising injection pressure and speed helps overcome flow resistance, achieving full cavity fill; however, balance is key as too much speed might create issues like flashing.
Adjusting holding parameters by extending time and changing pressure ensures that the melt settles properly in the cavity, balancing cooling shrinkage.
Finally, adjusting barrel and mold temperatures2 improves melt flow significantly aiding hard-to-handle plastics.
These strategies collectively enhance product appearance by ensuring consistent mold filling which reduces surface defects and dimensional inconsistencies.
Short shot phenomenon affects product appearance.True
Short shots occur due to incomplete mold filling, affecting aesthetics.
Increased surface roughness improves transparency.False
Surface roughness reduces transparency and gloss in products.
How Does Mold Design Ensure Complete Filling in Injection Molding?
Have you ever thought about how mold design affects the quality of your plastic products? It’s more important than you might realize!
Mold design is very important for full filling in injection molding. Good design reduces errors like short shots and size errors. It focuses on things like runner systems, gate location and exhaust features. This approach gives high-quality plastic parts.
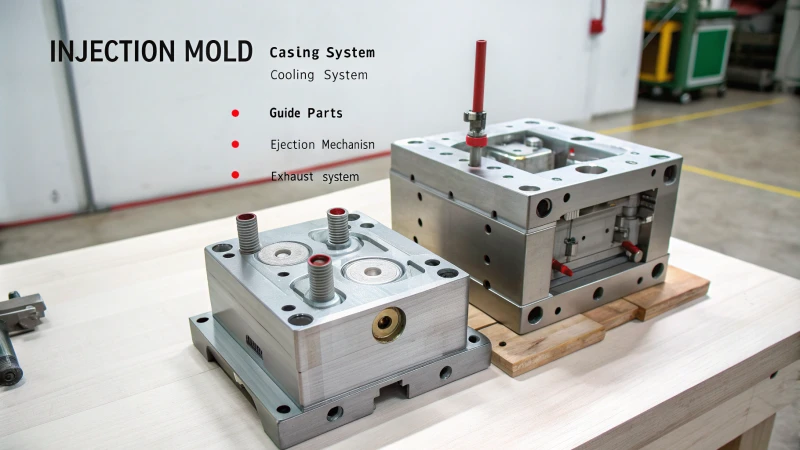
Importance of Optimized Runner Systems
I remember my first struggle with bad mold filling – complete chaos. The problem? A bad runner system. A well-planned runner system allows plastic to flow smoothly into the mold. Changing the runner’s size and shape helps spread material evenly. I discovered increasing the main runner diameter from 3mm to 5mm really boosted flow efficiency.
Runner System | Adjustment | Outcome |
---|---|---|
Main Runner | Diameter 3mm to 5mm | Smoother Flow |
Learn more about runner system adjustments3.
Strategic Gate Design
Designing gates is like planning a chess game. For thin products, a pin-point gate is best, moving material quickly and evenly. Big flat items might need side or fan gates, like your trusty rook or bishop.
- Gate Placement: Put them in thicker parts to use flow power.
- Number of Gates: Add more for tricky shapes.
Explore gate design strategies4 for top results.
Improving the Exhaust System
A good exhaust system feels like a breath of fresh air for your mold. It stops back pressure that slows down filling. Add exhaust grooves or use breathable materials, such as breathable steel, for great results.
- Exhaust Groove Depth: 0.02-0.04mm
- Positioning: At corners or ends of ribs
Find tips on exhaust system improvements5.
Impact on Product Appearance and Performance
I’ve seen poor mold filling cause problems like short shots and rough surfaces. Proper mold design reduces these issues, helping products meet dimensions. These designs very much matter for assembly.
Consider the consequences of insufficient mold filling6 to improve quality control.
Good mold design not only improves appearance but also product strength. Changing designs and parameters is crucial for injection molding success.
Increasing runner diameter improves flow efficiency.True
Larger diameters reduce resistance, allowing smoother material flow.
Pin-point gates are ideal for large flat products.False
Large flat products benefit more from side or fan gates.
How Can Injection Molding Process Parameters Be Optimized?
Entering the world of injection molding resembles opening a complicated puzzle of factors. These factors affect product quality and efficiency. Product quality and efficiency depend on these factors.
To improve injection molding, I adjust settings such as pressure, speed and temperature. These alterations greatly help mold filling. They really decrease problems like incomplete parts and rough surfaces.
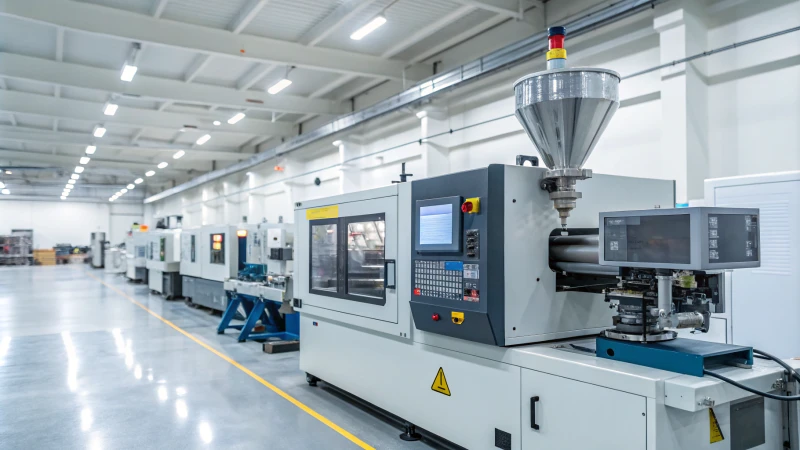
Optimizing Injection Pressure and Speed
When I first worked on improving injection molding, changing the injection pressure and speed really changed everything. Higher pressure helps the plastic liquid move smoothly, overcoming any blockage. Too much pressure, however, brings new issues. It’s all about balance.
Parameter | Adjustment | Example |
---|---|---|
Pressure | Increase within machine limits | From 70 MPa to 80-90 MPa |
Speed | Increment cautiously | Enhances flow but avoid defects |
For thin-walled products, higher speeds may be beneficial. However, for complex shapes, a moderate pace might be preferable. Testing variations is key to finding the optimal balance.
Adjusting Holding Parameters
Adjusting holding time and pressure was another lesson in patience. Extending the holding time from 5-10 seconds to 10-15 seconds let my plastic fit tightly in the mold, compensating for any shrinkage during cooling. Lowering the holding pressure to around half of the injection pressure kept the density uniform.
- Holding Time: Extend from 5-10s to 10-15s.
- Holding Pressure: Set at 40%-60% of injection pressure.
These changes really matter when I work on parts that need a perfect fit, like gears or buckles.
Temperature Control in Molding
Temperature changes were a big discovery. Raising barrel temperature improved melt fluidity, but too much heat leads to decomposition.
- ABS: Raise from 200°C to 220°C -240°C made a big difference.
For difficult materials like polycarbonate, changing mold temperatures from 80°C to 100°C -120°C makes them fill more cooperatively during molding.
Material Selection and Additives
Choosing the right materials or additives is like picking the right gear for a climb. Selecting materials with better fluidity, like switching from HDPE to PP, improved results significantly.
Material | Alternative | Benefit |
---|---|---|
HDPE | Switch to PP | Better flow |
Adding zinc stearate to lower melt thickness was a trick I learned, though it’s really important to use the right amount – usually between 0.1%-0.5% of material weight.
By constantly trying these adjustments, I improved product quality while reducing defects. Monitoring systems became my helpers, providing real-time feedback that lets me shift dynamically, keeping the molding process accurate. Injection molding methods are complex but rewarding. With persistence and precision, reaching superior mold filling and high-quality products is entirely achievable.
Increasing injection pressure reduces mold defects.False
Excessive pressure can cause defects like flashing, not reduce them.
Higher mold temperatures improve polycarbonate filling.True
Raising mold temperature lowers viscosity, aiding cavity filling.
How Can I Improve Mold Filling Efficiency Through Material Choices?
Ever wondered if there’s something missing in your injection molding?
Selecting materials with high flowability, such as polypropylene (PP), improves mold filling efficiency in injection molding. Additives like zinc stearate help. These choices lower melt viscosity. Complete cavity filling occurs. Defects decrease.
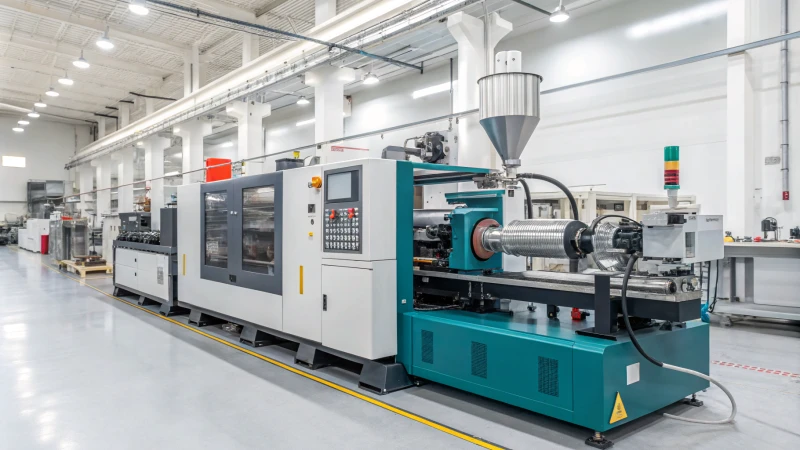
Understanding Material Flow Properties
I recall when I first understood the importance of material flow properties in my work. It felt like wearing glasses for the first time, seeing everything clearly. Materials that flow well fill mold spaces more efficiently, reducing the chance of defects like the short shot phenomenon7. I often picked polypropylene (PP) over high-density polyethylene (HDPE) because PP flows better.
The Role of Additives
Adding the right additives is like adding a special ingredient to a dish. Suddenly, everything works better. For example, zinc stearate changes melt viscosity. This discovery was a turning point. Adding 0.1%-0.5% by weight allows the plastic to flow really well into complex molds, minimizing issues like increased surface roughness8. It really helps.
Additive | Effect on Mold Filling Efficiency |
---|---|
Zinc Stearate | Reduces viscosity, improves fluidity |
Silicone Oil | Enhances lubrication, reduces friction |
Calcium Carbonate | Increases thermal conductivity, aids cooling |
Impact on Product Appearance
Efficient mold filling significantly impacts product appearance. I have faced many troubles with molds not filling properly; incomplete products were always a reminder of mistakes. Filling molds efficiently uses less material and greatly improves how a product looks. Choosing the right material ensures that even intricate parts of the design are fully formed, avoiding dimension deviation9 and improving aesthetics.
Moreover, consistent quality in production batches is vital. Matching thermal properties with molding conditions leads to better outcomes; it’s important.
Exploring Material Innovations
Discovering new materials in polymer science brings unique excitement. Bio-based polymers improve material flow and offer environmental benefits—a win for both performance and nature. These insights into choosing and improving materials have led to big improvements in mold filling efficiency, resulting in higher product quality and lower production costs.
Polypropylene has better flow than HDPE for mold filling.True
Polypropylene's superior flow characteristics make it more efficient in mold filling.
Zinc stearate increases melt viscosity in plastics.False
Zinc stearate actually decreases melt viscosity, enhancing fluidity.
Conclusion
Insufficient mold filling leads to defects like short shots, rough surfaces, and dimension deviations. Optimizing design and process parameters can enhance product quality in injection molding.
-
Learn more about optimizing runner systems to improve plastic flow in molds. ↩
-
Discover how adjusting temperatures can enhance plastic fluidity during molding. ↩
-
Discover how optimizing runner systems can enhance plastic flow and reduce defects. ↩
-
Uncover strategic gate design techniques that improve mold filling efficiency. ↩
-
Learn effective ways to enhance exhaust systems, preventing back pressure issues. ↩
-
Understand the impact of insufficient filling on product quality and performance. ↩
-
Learn how choosing materials with better flow properties can prevent short shot defects. ↩
-
Discover how additives improve fluidity and reduce surface roughness. ↩
-
Explore how proper material choices prevent dimensional deviations. ↩