Ever been confused by injection molding? Figuring out the size limits might seem like solving a mystery. Maybe it feels that way to you too.
The size limits for injection-molded parts are influenced by machine specifications, mold manufacturing capabilities, and material performance, all of which are crucial in determining the feasibility of producing large-scale items.
As someone with years of experience in product design, I know that size limitations in injection molding are very important. These limitations shape our projects. For example, the maximum injection volume and clamping force of a machine restrict what we create. I remember designing a part too large for the machine. What a learning experience that was! Each factor is critical. Machine specs and material performance matter. They play roles in what’s possible. Let’s explore these limitations together. They can significantly impact your designs.
Injection molding size limits depend on machine specifications.True
The size limitations of injection molded parts are primarily determined by the specifications of the injection molding machine used.
All plastic materials allow for large-scale injection molding.False
Not all plastic materials are suitable for large-scale production due to their performance characteristics and processing constraints.
What are the key specifications of injection molding machines?
Did you ever think about how those shiny plastic parts in our gadgets get created? Injection molding machines play a vital role in manufacturing. Let’s explore their important details and understand why they are significant!
Key features of injection molding machines involve clamping force, injection volume and injection pressure. These factors directly impact the size and quality of molded parts. Designers must really grasp their importance for successful production. It is very important.
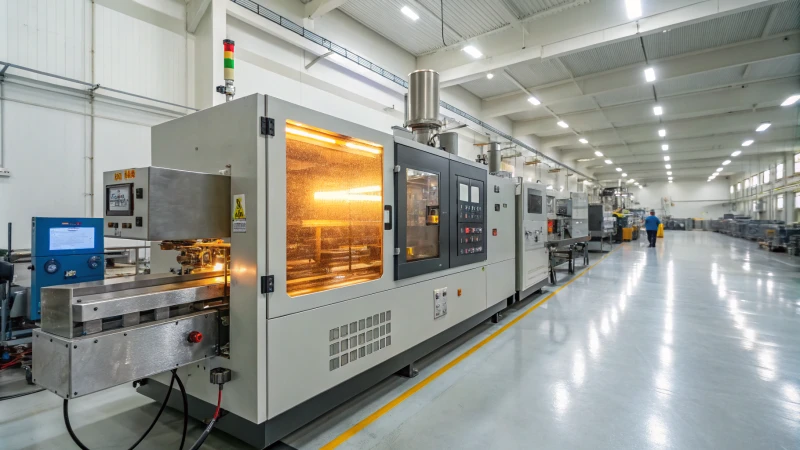
Understanding Key Specifications of Injection Molding Machines
Injection molding machines are pivotal in manufacturing processes, particularly for producing plastic parts. The specifications of these machines play a critical role in determining the feasibility and quality of the molded products. Key specifications include:
-
Clamping Force: Imagine holding a lid tightly while someone pushes from inside. That is clamping force. It is very important as it keeps the mold secure during injection. Once, I underestimated this and we had a costly problem with defects like flash.
-
Injection Volume: This shows how much plastic goes into the mold. When I created a larger part, I saw that passing this volume brought problems. It taught me to match part design with machine limits.
-
Injection Pressure: This pushes plastic into the mold cavity. High pressure is often needed for complex shapes. I’ve seen how low pressure causes incomplete parts and wastes materials.
Size Limits for Parts Produced by Injection Molding
The size of parts produced is directly influenced by several factors, including:
Specification | Description |
---|---|
Max Injection Volume | Determines the largest volume of plastic that can be used for molding. |
Max Clamping Force | The force required to keep the mold closed against high injection pressures. |
Mold Complexity | Affects the maximum dimensions and precision achievable in molded parts. |
For example, if a part exceeds the maximum injection volume, it cannot be molded properly, leading to potential waste and inefficiency. Furthermore, larger parts require more significant clamping force to counteract the expansion forces generated during injection.
Limitations of Mold Manufacturing and Precision
Mold specifications also impose limitations:
- Dimensional Tolerances: I’ve dealt with large molds that were hard to make accurately. Tolerance build-up reduces part accuracy. It’s frustrating when parts don’t fit as expected.
- Cooling Systems: A good cooling system is like a well-timed show. If one part is off, it causes deformations or inaccuracies. Uneven cooling affects size accuracy, especially with thick parts.
Understanding these aspects helps designers ensure that their molds will produce parts that meet quality standards.
Material Performance Considerations
The type of plastic material used can significantly affect part size and quality:
- Shrinkage Rates: Every designer should know how materials shrink when cooling. Once, crystalline plastics surprised me and messed up our dimensions.
- Fluidity: Picking materials that flow well is crucial. In one large part project, the flow length was too much, causing incomplete parts.
To enhance understanding, refer to detailed studies on plastic material performance1.
By grasping these specifications and their implications, engineers and designers can optimize their designs for injection molding processes, ensuring high-quality outcomes without compromising production efficiency.
Injection molding machines require high clamping force for large parts.True
High clamping force is necessary to keep molds closed during injection, especially for larger components, preventing defects like flash.
Injection volume limits the size of parts in injection molding.True
The maximum injection volume determines the largest plastic part that can be molded, affecting production feasibility and efficiency.
How does mold design impact part size limitations?
Have you ever thought about how the details of mold design shape the products we build? Let us explore this topic and see why it is important for designers like us. Mold design really matters a lot.
Mold design affects how big parts can be. It involves factors like the maximum injection volume and clamping force. If the part volume is bigger than what the machine can handle, molding does not succeed. Knowing these limits is important. It leads to effective design and production. It allows for bigger parts without defects.
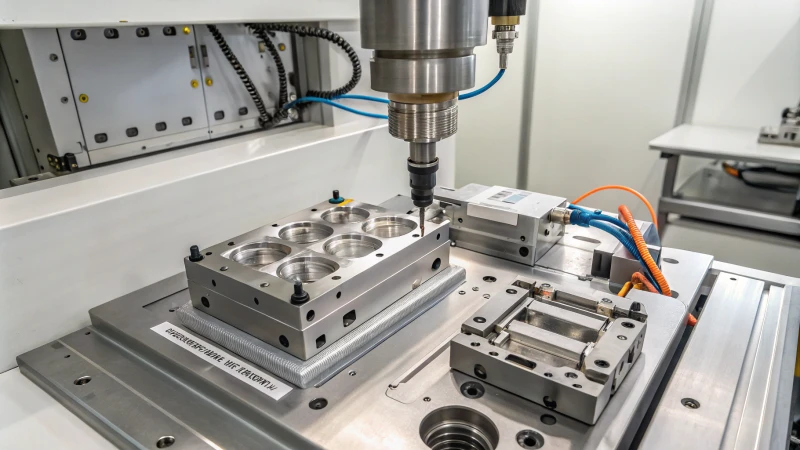
Limitations of Injection Molding Machine Specifications
The capacity of injection molding machines significantly influences the size of parts that can be produced. Key parameters include the maximum injection volume and clamping force.
For instance, if a part’s volume exceeds the injection volume of the machine, it will not mold properly.
Similarly, clamping force is crucial to counteract the pressure exerted by the melted plastic during injection.
Parameter | Impact on Part Size |
---|---|
Maximum Injection Volume | Limits the total volume of plastic injected. |
Clamping Force | Prevents mold separation during injection. |
When large parts are molded, they generate greater expansion forces, which can lead to defects like flash if they exceed the machine’s clamping force. Understanding these limits is essential for effective design.
Limitations of Mold Manufacturing and Precision
The complexity and size of the mold itself impose restrictions on part dimensions.
Larger molds present challenges in maintaining processing accuracy due to dimensional tolerances that become more pronounced with size.
For example, as the cavity increases in size, the potential for errors during manufacturing grows.
Additionally, mold deformation during clamping is a risk factor for large parts:
- Weight of the mold can affect stability.
- Cooling systems must be designed carefully to maintain dimensional accuracy.
Factor | Consequences |
---|---|
Mold Size | Increased tolerance issues in manufacturing. |
Cooling Time | Longer cooling can lead to size deviations. |
If large parts have uneven cooling, they might experience significant shrinkage, potentially leading to non-compliance with design specifications.
Limitations of Plastic Material Performance
The characteristics of plastic materials are also critical in determining part size limits.
For example, different plastics exhibit varying shrinkage rates during cooling:
- Crystalline plastics may shrink due to crystallization, affecting larger parts more significantly.
- The fluidity of materials can hinder the molding process if the part’s dimensions exceed acceptable limits.
Material Property | Effect on Part Size |
---|---|
Shrinkage Rate | Larger parts may not meet dimensional requirements due to increased shrinkage. |
Flow Length Ratio | Excessive ratios can lead to incomplete filling of cavities. |
These factors highlight the importance of selecting appropriate materials based on the desired part sizes and shapes.
Advancements in Injection Molding Technology
As technology evolves, methods to overcome these limitations are emerging.
For instance, advancements in larger injection molding machines and optimized mold designs enhance manufacturing capabilities.
improvements in plastic formulations also contribute to expanding the size range of molded parts.
Investing in technology and material science can mitigate some constraints, allowing designers like Jacky to explore new dimensions in product design while adhering to the limits imposed by mold specifications.
Injection volume limits part size in injection molding.True
The maximum injection volume of a machine restricts the overall volume of plastic that can be molded, affecting part size capabilities.
Larger molds always improve manufacturing accuracy.False
Larger molds can lead to increased tolerance issues, making it harder to maintain processing accuracy during manufacturing.
How Does Material Selection Affect the Size of Parts in Manufacturing?
In the beginning of my manufacturing career, I discovered that choosing the right material really changes part size. This knowledge truly matters for reaching the ideal design. Believe me, this path deserves your time.
Choosing the right material is essential for setting the size of parts in injection molding. Materials influence how much the part shrinks and flows. Different materials cause changes in the final size and quality of the piece. These are important aspects. Every designer needs to understand these to achieve successful production.
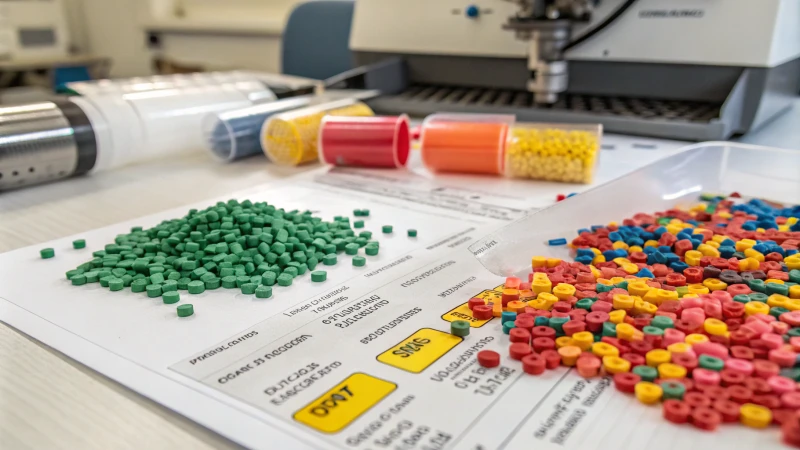
Understanding Material Selection in Injection Molding
Material selection is very important for defining part size in injection molding. It affects shrinkage rates, flow, and how materials work with machine specifications. These factors impact the final size and quality of the molded part. Every choice about materials feels like an adventure. This adventure can either create a wonderful product or cause a setback if not done correctly.
For instance, thermoplastics and thermosetting plastics shrink differently when cooling, which can significantly affect the final dimensions of larger components. Larger parts experience greater absolute shrinkage, potentially leading to dimensional inaccuracies.
Shrinkage Rates and Their Implications
The following table illustrates common plastic materials used in injection molding along with their typical shrinkage rates:
Material Type | Typical Shrinkage Rate (%) | Comments |
---|---|---|
Polypropylene (PP) | 1.0 – 2.5 | Good fluidity, suitable for large parts |
Acrylonitrile Butadiene Styrene (ABS) | 0.5 – 1.5 | Balanced properties, moderate shrinkage |
Nylon (PA) | 1.5 – 3.0 | Higher moisture absorption affects size |
Polycarbonate (PC) | 0.5 – 1.0 | Good strength, lower shrinkage |
Designers need to understand these rates well as they influence how much a part might shrink from its original size during production. I remember working with ABS on a project, constantly adjusting dimensions due to shrinkage; it felt like solving an endless puzzle!
Fluidity and Part Size
Besides shrinking, a material’s fluidity is also very important. Fluidity affects how well a material fills the mold:
- High Fluidity Materials: Fill intricate designs and thin walls well, reducing the chance of incomplete molds.
- Low Fluidity Materials: Have more trouble with larger or complex molds, possibly causing defects.
I’ve faced challenges with this! I worked on a detailed design with thin walls where I needed high fluidity material to succeed. Balancing these properties with the size and complexity of the part is key.
Impact of Machine Specifications
Material selection must consider the specifications of the injection molding machine. Important machine parameters include:
- Maximum Injection Volume: If a part’s volume is too high, the molding process fails.
- Clamping Force: Big parts create a lot of pressure during injection; machines need strong clamping to prevent defects like flash.
These factors let me choose materials and size parts correctly, improving production efficiency. I’ve learned that even little details have big impacts!
Conclusion
Understanding how material traits, machine specs, and design needs interact helps us decide for successful manufacturing outcomes. My journey in this field is very educational; each project is a chance to learn and grow step by step! For further insights into material selection processes, explore more about material properties2 or consult resources on injection molding techniques3.
Material choice impacts the final size of injection molded parts.True
The selected material directly affects shrinkage rates and fluidity, influencing the dimensions of the molded components during production.
Larger parts have lower shrinkage rates than smaller parts.False
In reality, larger parts experience greater absolute shrinkage, leading to more significant dimensional inaccuracies compared to smaller components.
Can advancements in technology really expand the size limits of injection molded parts?
Imagine a world where injection molding has no limits. New technology opens doors to larger and more detailed parts. This innovation really changes our industry.
Definitely! Larger injection molding machines are advancing technology. Improved mold designs also contribute to this progress. Plastic formulations are getting better. These improvements will probably allow for bigger injection molded parts. Production capabilities are expanding due to these changes. Efficiency is increasing as well. New possibilities are emerging.
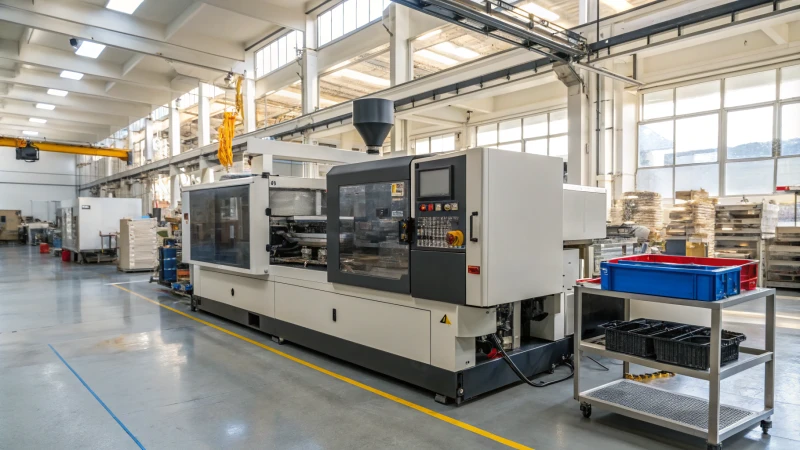
Understanding Size Limits in Injection Molding
Years spent in product design taught me about the challenges of injection molding. Size limits exist due to machine specifications, mold manufacturing capabilities, and plastic performance characteristics.
Limitations of Injection Molding Machines
-
Injection Volume: Many ideas stalled because of our machine’s maximum injection volume. Parts exceeding this volume simply fail in molding. However, new machine designs promise larger volumes soon.
-
Clamping Force: Watching molten plastic fill a mold is tense. Larger parts create more pressure. If the pressure is too much for the system’s clamping force, defects like flash emerge. Machinery improvements for stronger clamping are hopeful for future projects.
Feature | Current Limits | Potential Advances |
---|---|---|
Maximum Injection Volume | Limited by machine design | Development of high-capacity machines |
Clamping Force | Restricts large part molding | Enhanced mechanical systems |
Mold Manufacturing and Precision
-
Dimensional Accuracy: Seeing a well-designed part with precision problems is disheartening. Bigger molds struggle to maintain precision. New methods like 3D printing present hope for better tolerance control.
-
Cooling Systems: Cooling is crucial. Uneven cooling has caused serious size deviations in past projects. Innovations here could help create uniformity, making precision attainable for larger molded parts.
Example: Cooling Time Impact
Part Size | Cooling Time | Potential Improvement |
---|---|---|
Small | Short | Faster cooling systems |
Medium | Moderate | Optimized cooling channels |
Large | Long | Advanced cooling technologies |
Plastic Material Performance
-
Shrinkage Rates: Shrinkage rates matter. Larger parts shrink more. Finding materials to minimize this is vital. Materials science is creating formulations with lower shrinkage.
-
Fluidity of Materials: It’s frustrating when a large component fails to mold due to fluidity issues. Thankfully, polymer advancements are improving material flow, making it easier to fill bigger molds.
Future Directions
The future of injection molding fills me with optimism. The industry nears groundbreaking innovations that could increase size capacities. Important areas to watch include:
- Bigger, more efficient machines designed for large volumes.
- Improved mold designs using new technology for better precision.
- New materials that withstand large part production without losing quality.
Learning about these advancements empowers designers and manufacturers like Jacky. Dreaming big and improving processes for sizable components can become a reality. By embracing change, efficiency and production capabilities can really soar like never before.
Advancements in technology can increase injection volume limits.True
Innovations in machine design may enhance the maximum injection volume, allowing for larger parts to be molded effectively.
Larger injection molded parts always have higher shrinkage rates.False
While larger parts tend to shrink more, advancements in material science can reduce shrinkage rates, improving dimensional accuracy.
Conclusion
Injection molding part sizes are limited by machine specs, mold precision, and material properties. Understanding these constraints is essential for successful design and manufacturing.
-
Explore this resource for an in-depth analysis of how material properties affect injection molding outcomes. ↩
-
This link provides an overview of key material properties that impact size during manufacturing processes. ↩
-
Learn about various injection molding techniques that can influence part dimensions through material choices. ↩