Have you ever felt the frustration of inspecting a product only to find it marred by incomplete fills? It’s a common challenge in injection molding—short shots. Let’s dive into understanding this issue and uncover effective solutions together.
Short shots occur when the plastic melt does not fully fill the mold cavity, often due to poor plastic fluidity, insufficient drying, or improper machine settings. Solutions include selecting better materials, optimizing mold design, and adjusting process parameters like temperature and pressure.
But don’t worry! While it may seem daunting, addressing short shots requires a balance of different factors. Let’s explore expert recommendations and best practices that can elevate your injection molding operations.
Short shots occur due to poor plastic fluidity.True
Poor fluidity restricts melt flow, causing incomplete mold filling.
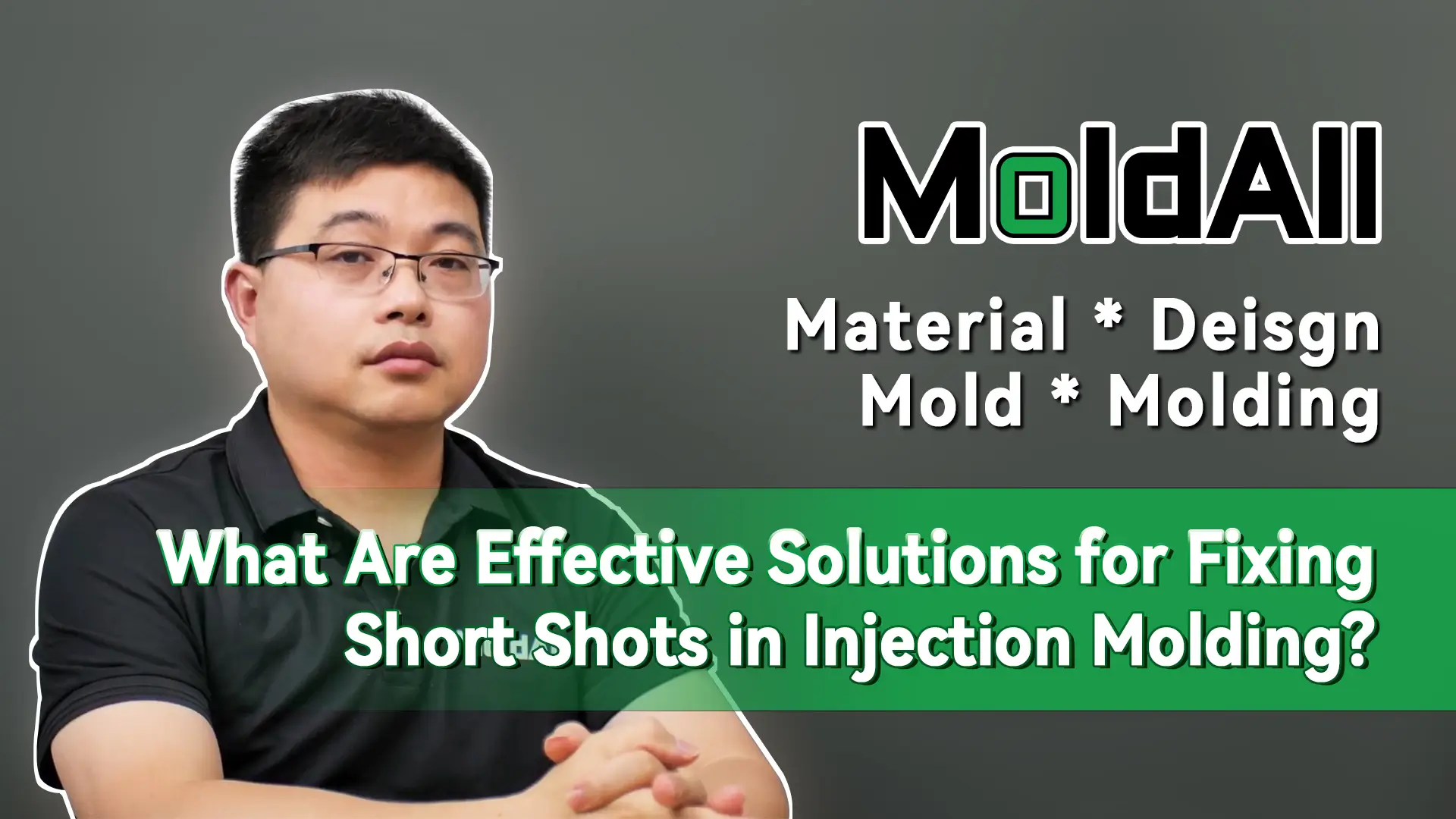
How Do Material Properties Affect Short Shots?
Material properties play a crucial role in determining the success of the injection molding process, impacting both fluidity and defect rates.
Material properties influence short shots primarily through fluidity and moisture content. Poor fluidity restricts the melt flow, while excess moisture leads to bubbles, both resulting in incomplete mold filling. Opting for materials with superior fluidity and ensuring thorough drying can significantly reduce short shots.
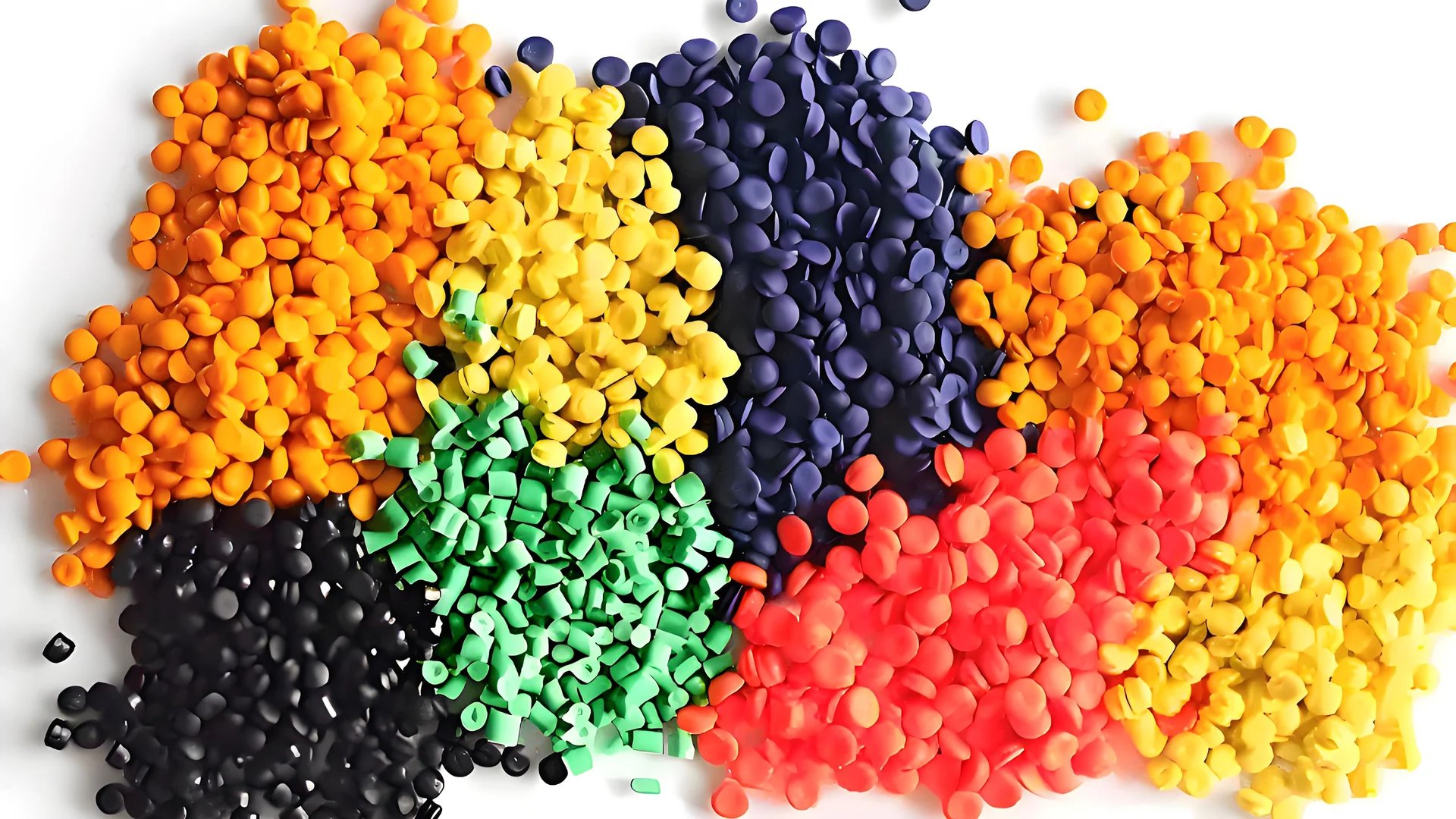
The Role of Material Fluidity
Material fluidity is a critical factor in the injection molding process, dictating how well a plastic can fill a mold cavity. Poor fluidity means that the plastic melt struggles to reach all areas of the mold, often leading to short shots. Materials like Polypropylene (PP) and Acrylonitrile Butadiene Styrene (ABS) offer varying fluidity levels, affecting their suitability for complex molds.
- Example: A high-fluidity material, such as PP, can effortlessly fill intricate molds without requiring excessive pressure or temperature adjustments.
Choosing a plastic with adequate fluidity ensures that the melt flows uniformly, reducing the chances of short shots. For products with detailed geometries, selecting materials with higher fluidity can prevent defects and improve overall quality.
Importance of Material Drying
Material drying is essential for removing excess moisture from plastics before they undergo the injection molding process. Moisture trapped in the material can turn into steam during heating, creating bubbles and voids that disrupt the flow of the melt, causing short shots.
- Solution: Utilize specialized drying equipment to maintain ideal moisture levels and prevent flow interruptions.
Thorough drying not only minimizes defects but also enhances the mechanical properties of the final product. Incorporating pre-molding drying processes is particularly crucial for hygroscopic materials like Nylon and Polycarbonate.
Selecting the Right Material
The choice of material significantly affects short shots. Selecting plastics known for their excellent flow characteristics can reduce the occurrence of these defects.
Material Type | Fluidity Level | Suitability for Complex Molds |
---|---|---|
Polypropylene (PP) | High | Excellent |
Acrylonitrile Butadiene Styrene (ABS) | Medium | Good |
Nylon | Low | Moderate |
Ensuring that your selected material aligns with the product’s requirements and design complexities is crucial. Consideration of both fluidity and drying needs will lead to fewer short shots and higher production efficiency.
By understanding how material properties impact short shots, manufacturers can make informed decisions that lead to superior product quality and reduced defect rates. For further guidance on material selection, consult resources on choosing materials for injection molding1.
Polypropylene has high fluidity for injection molding.True
Polypropylene (PP) is known for its excellent flow characteristics.
Moisture in plastics doesn't affect short shots.False
Excess moisture creates bubbles, leading to incomplete mold filling.
What Mold Design Changes Can Prevent Short Shots?
Mold design plays a crucial role in preventing short shots, a common defect in injection molding. What are the key design changes to consider?
To prevent short shots, mold design should focus on enlarging gate sizes, optimizing runner design, and improving exhaust systems. These changes facilitate better plastic flow, reduce resistance, and ensure proper venting, which collectively prevent incomplete filling of mold cavities.
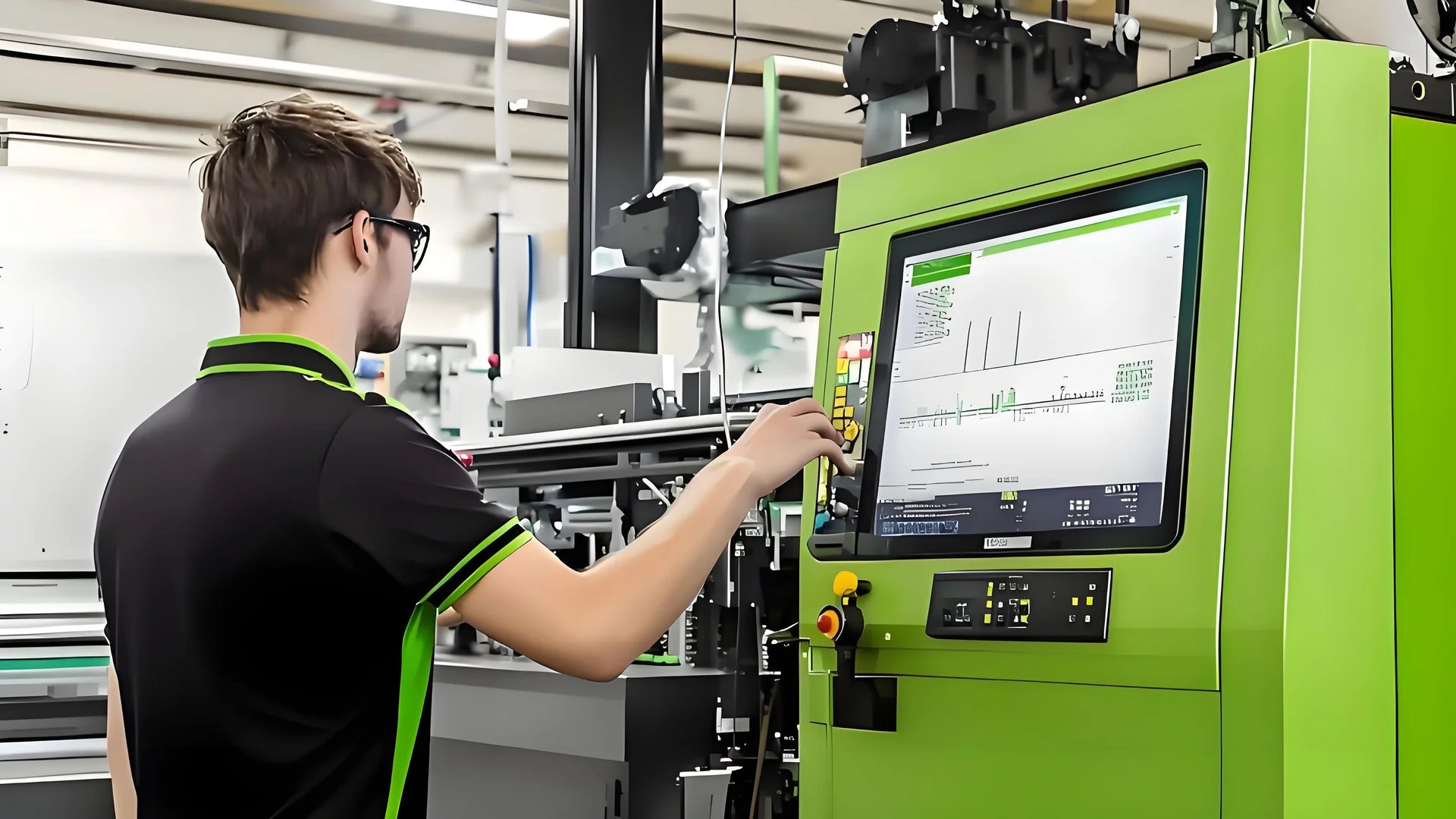
Importance of Gate Size
A critical aspect of mold design is the gate size, which determines the flow speed and volume of the plastic entering the cavity. Small gate sizes can restrict this flow, leading to short shots. By increasing the gate size, manufacturers can ensure more efficient filling of the mold, reducing the chances of defects.
Gate Feature | Impact on Mold Filling |
---|---|
Small Gate | Increased resistance, prone to short shots |
Large Gate | Improved flow, reduced risk of short shots |
Optimizing Runner Design
The runner system is like a highway for plastic melt. If it’s too narrow, long, or curved, it can significantly increase resistance against the flowing plastic. An optimized runner design minimizes this resistance by ensuring that the path is as direct and smooth as possible. This not only helps in achieving complete mold filling but also enhances overall cycle time.
For further insights on runner design optimization2, you may want to explore how engineering best practices can be applied to improve production efficiency.
Enhancing Exhaust Systems
Proper venting is essential in mold design to prevent air traps which can cause short shots. Implementing effective exhaust grooves or holes helps in releasing trapped gases during the injection process. This improvement ensures that air does not block the path of the plastic melt, allowing for complete filling of the cavity.
To delve deeper into exhaust system improvements3, understanding various techniques for optimizing air release can prove beneficial.
Integrating Advanced Features
Some advanced molds incorporate features like collapsible cores and hot runner systems that further refine the molding process by enhancing plastic flow and reducing cooling time. These technologies can be particularly useful when dealing with complex part geometries or high-volume production requirements.
Learning more about advanced mold features4 can provide innovative solutions that address short shot issues effectively.
By focusing on these key aspects of mold design—gate size, runner optimization, and effective venting—manufacturers can significantly reduce the occurrence of short shots, leading to improved product quality and operational efficiency.
Increasing gate size reduces short shot risk.True
Larger gates improve plastic flow, ensuring complete mold filling.
Narrow runners enhance mold filling efficiency.False
Narrow runners increase resistance, hindering efficient mold filling.
How Can Adjusting Machine Settings Reduce Short Shots?
Fine-tuning machine settings can play a crucial role in eliminating short shot defects in injection molding.
Adjusting machine settings such as injection pressure, speed, and temperature can significantly reduce short shots by ensuring the plastic melt flows smoothly and fills the mold cavity completely.
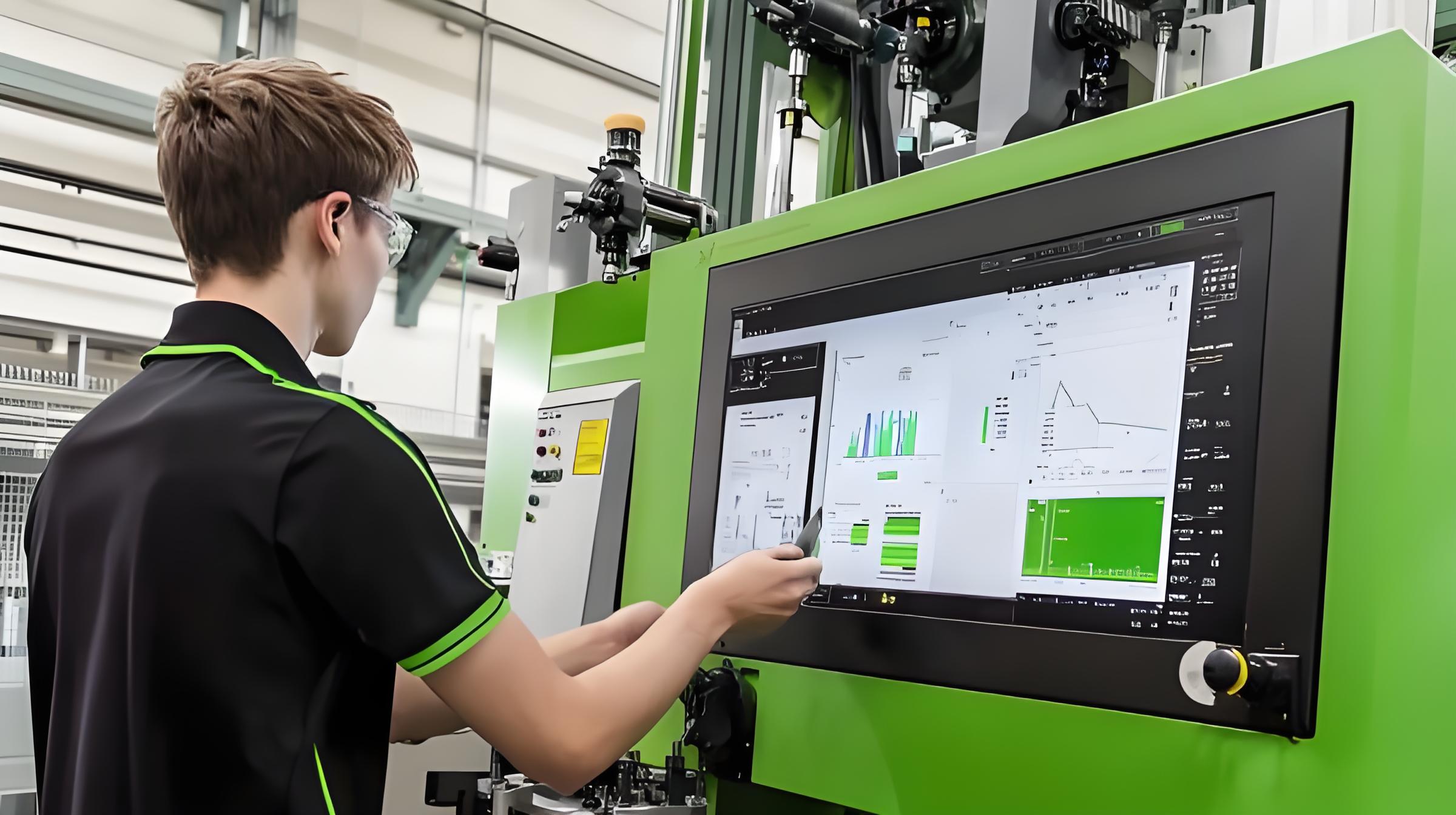
Understanding the Role of Machine Settings
Machine settings are pivotal in determining how efficiently the plastic melt flows into and fills the mold cavity. By modifying specific parameters, you can effectively address the issues leading to short shots.
Injection Pressure
One of the primary factors contributing to short shots is insufficient injection pressure. The pressure needs to be adequately high to push the plastic melt through the mold cavity completely. Increasing the injection pressure5 helps in overcoming resistance within the mold and ensures that even intricate areas are filled.
Injection Speed
Speed plays a crucial role, particularly when dealing with complex molds. A low injection speed can cause the plastic melt to cool down prematurely, which reduces its fluidity and results in short shots. By increasing the injection speed6, the melt remains at a high enough temperature to fill the cavity more efficiently.
Temperature Settings
Both mold and barrel temperatures are significant contributors to the occurrence of short shots. A lower-than-optimal mold temperature can cause rapid cooling of the melt, whereas a low barrel temperature may result in improper melting. Adjusting these temperatures to suit the specific plastic material used can enhance fluidity and reduce short shot occurrences. Check and adjust the mold temperature7 and barrel temperature8 according to the material’s properties and desired product specifications.
Machine Setting | Problem Addressed | Recommended Adjustment |
---|---|---|
Injection Pressure | Insufficient filling | Increase pressure as needed |
Injection Speed | Premature cooling | Raise speed for improved flow |
Mold Temperature | Rapid cooling | Adjust to maintain optimal fluidity |
Barrel Temperature | Improper melting | Set to ensure complete plastic melt |
By focusing on these critical settings, manufacturers can significantly reduce instances of short shots and improve overall product quality. Balancing these factors requires careful analysis and adjustments tailored to each specific situation.
Increasing injection pressure reduces short shots.True
Higher pressure ensures complete mold filling, preventing short shots.
Lowering mold temperature decreases short shots.False
Lower temperatures cause rapid cooling, increasing short shot risk.
Are There Innovative Technologies Addressing Short Shot Issues?
Emerging technologies are revolutionizing how manufacturers tackle short shot issues in injection molding, offering innovative solutions to enhance product quality.
Innovative technologies such as advanced simulation software, smart sensors, and AI-driven predictive maintenance are transforming how short shot issues are identified and resolved in injection molding processes.
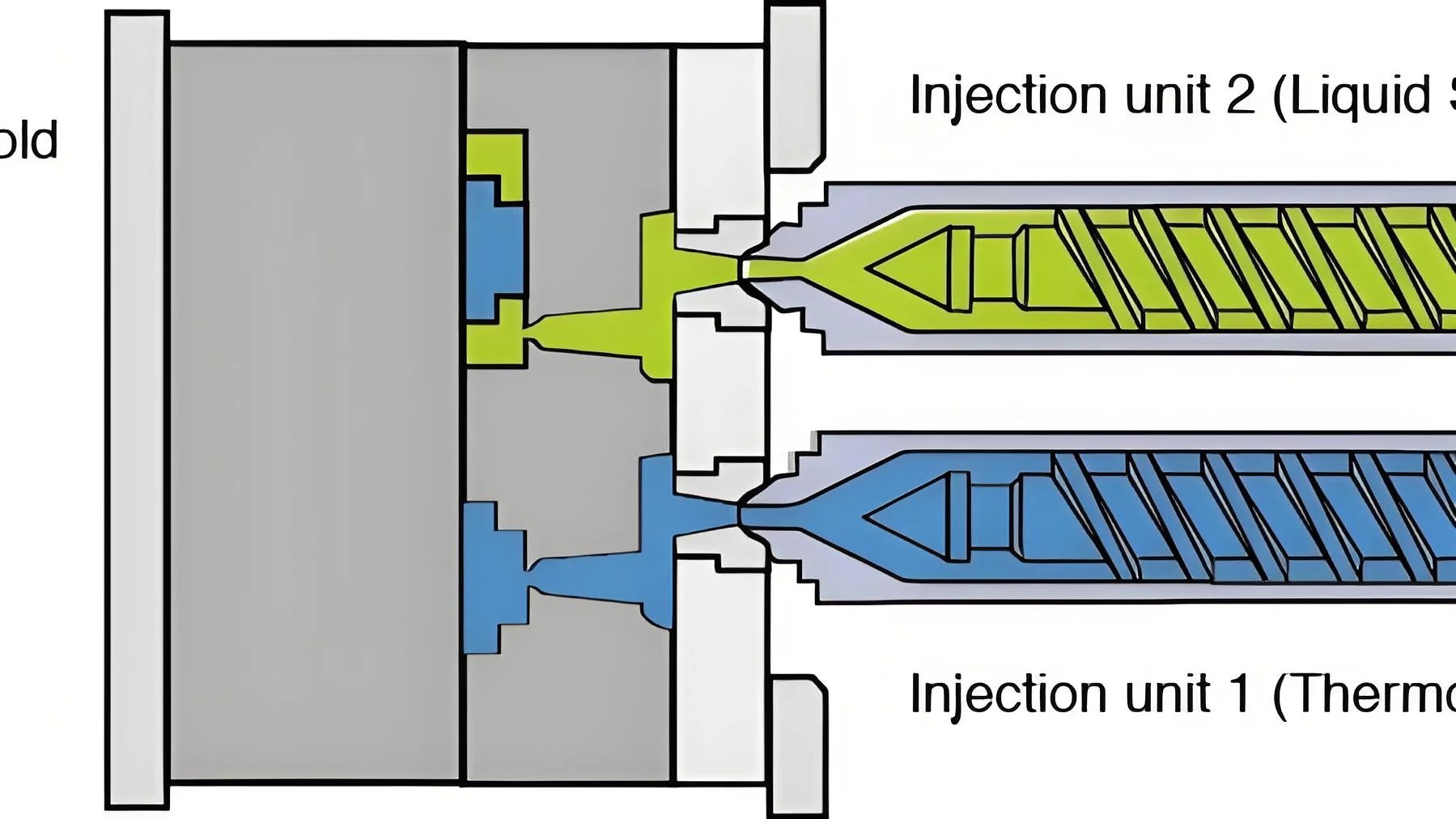
Advanced Simulation Software
The use of advanced simulation software9 enables manufacturers to predict potential short shot issues before production begins. By creating digital twins of molds and processes, these tools can simulate various scenarios to identify optimal settings and design improvements. This proactive approach helps in making necessary adjustments before encountering real-world problems.
Smart Sensor Technology
Smart sensors are becoming a crucial component in detecting and resolving short shots. These sensors monitor critical parameters such as pressure, temperature, and flow rates in real time. By providing immediate feedback, they help operators make quick adjustments to prevent short shots from occurring.
For instance, pressure sensors installed at key points within the mold can detect deviations that might lead to incomplete filling. Operators can then respond by adjusting injection speed or pressure to ensure complete cavity filling.
AI-Driven Predictive Maintenance
Artificial Intelligence (AI) is playing a pivotal role in minimizing short shot occurrences through predictive maintenance. AI algorithms analyze historical data from injection molding machines to predict when a component might fail or require maintenance. This foresight allows manufacturers to address issues before they affect production quality.
AI can also optimize the injection process by continuously learning from past cycles to adjust parameters dynamically, ensuring consistent product quality and reducing the chances of short shots.
Additive Manufacturing for Prototyping
Additive manufacturing, or 3D printing, assists in prototyping molds quickly and cost-effectively. By testing these prototypes with different materials and designs, manufacturers can identify potential short shot risks and rectify them before committing to expensive, large-scale mold production.
Integrating IoT in Injection Molding
The Internet of Things (IoT)10 provides a connected ecosystem where machines communicate seamlessly. IoT-enabled devices can share data across systems to provide comprehensive insights into the entire production process. This integration allows for real-time adjustments and alerts, significantly reducing the risk of short shots.
These innovative technologies offer promising solutions to the persistent problem of short shots in injection molding. By leveraging advancements such as simulation software, smart sensors, AI, and IoT, manufacturers can not only enhance their production efficiency but also achieve higher quality standards.
Advanced simulation software predicts short shot issues.True
It simulates scenarios to identify potential problems before production.
Smart sensors are irrelevant in injection molding processes.False
They monitor parameters like pressure and temperature to prevent defects.
Conclusion
Understanding short shots is crucial for enhancing product quality. By implementing these solutions, you’ll not only improve efficiency but also reduce defects.
-
Explore material selection to minimize defects and enhance mold performance.: Learn how to select the right material for your injection molding design with this technical overview of thermoplastic resins. ↩
-
Understand engineering practices to improve runner efficiency and production outcomes.: Runner Balance Analysis: Use a runner balance analysis to optimize the runner layout, ensuring an even distribution of plastic flow into the mold cavities. ↩
-
Explore techniques for effective air release in mold designs.: Paulson Training Programs, Inc. This short video clip describes how to improve mold venting … ↩
-
Discover innovative solutions for complex molding challenges.: Create more engaging and efficient parts, plus reduce production costs with these injection molding design tips, including living hinges, bosses, text, … ↩
-
Learn optimal pressure settings for full cavity filling.: One of the first steps in troubleshooting a short shot is to turn off second stage pressure and time, and make what is referred to as a fill-only part. ↩
-
Discover why speed adjustments improve flow efficiency.: Injection speed directly affects filling speed. If injection speed is slow, melt fills slowly, and low-speed flowing melt easily cools, further … ↩
-
Find mold temperature tips for enhanced fluidity.: An optimal setting at 50℃ ensures balanced flow and solidification. … PPS can withstand high temperatures, making it suitable for demanding applications. POM, … ↩
-
Understand how barrel heat affects plastic melting.: An adjustable flow restriction valve after the extruder enables a change in head pressure or a resistance to the screw output and is a much … ↩
-
Discover how simulations help predict and prevent short shot issues.: Injection molding simulation software is used to make better molded parts and reduce defects. It does this by digitally simulating virtually every aspect of … ↩
-
Explore how IoT integration enhances manufacturing efficiency and quality.: By implementing IoT solutions, manufacturers can automate more processes, detect anomalies and reduce errors, and therefore increase operational … ↩