Injection molding is more than just a manufacturing technique; it’s an art form that transforms raw plastic into functional products we use daily.
The seven essential components of injection molding are molding parts, gating system, guide mechanism, ejector device, lateral parting and core pulling mechanism, cooling and heating system, and exhaust system. These components work together to form and shape plastic parts efficiently.
While this brief overview provides a snapshot of the key components, a deeper dive into each reveals their unique roles and interdependencies. Continue reading to discover how these components contribute to the efficiency and precision of injection molding.
The gating system manages plastic flow into the mold cavity.True
It directs molten plastic using channels and gates for optimal flow.
How Do Molding Parts Shape Plastic Components?
Molding parts play a crucial role in defining the shape and structure of plastic components during the injection molding process.
Molding parts shape plastic components by forming the mold cavity, including elements like punches, concave molds, and cores, which determine the precise dimensions and features of the final product.
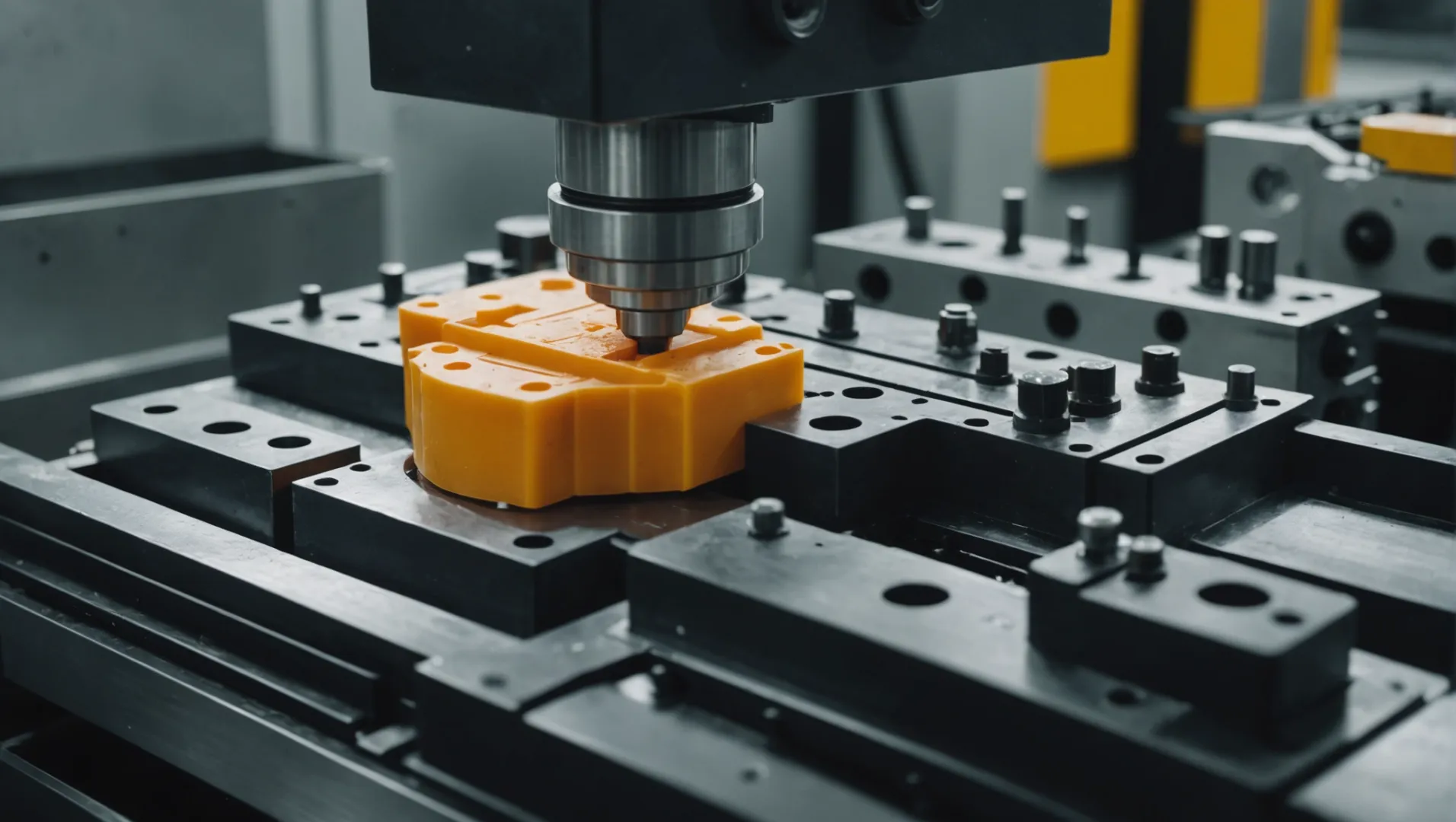
The Role of Molding Parts in Shaping Plastics
In the realm of injection molding1, molding parts are the unsung heroes, acting as the primary influencers of a product’s design. These components form the mold cavity where molten plastic is injected and solidified. Let’s delve into how these elements come together to craft precise plastic parts.
1. Punches and Concave Molds
Punches and concave molds are essential in creating detailed features on plastic products. Punches are male molds that help shape the internal features, while concave molds are female molds that shape external contours.
- Example: In a water bottle cap, punches create the threads inside, allowing it to screw onto a bottle securely.
2. Cores and Molding Rods
Cores are central to forming hollow sections within a part, whereas molding rods contribute to complex geometries.
- Example: The core helps form the hollow section of a pipe, ensuring uniform wall thickness.
3. Molding Rings and Inserts
Molding rings are used to secure the mold components, ensuring they remain stable during the molding process. Inserts are used to add strength or allow for additional functionalities like threading or fastening.
- Example: Inserts can be embedded within automotive parts to provide metal reinforcements in areas that require high strength.
How Molding Parts Affect Precision
The precision of molding parts directly influences the final product’s quality. With advanced CNC machining2 technologies, creating intricate and precise molds has become possible, allowing for high-quality, consistent production.
-
Material Selection: The choice of material for molding parts impacts durability and precision. Common materials include hardened steel for its strength and aluminum for rapid prototyping.
-
Maintenance: Regular maintenance of molding parts is vital for ensuring long-term accuracy and efficiency. This includes cleaning to prevent buildup and wear checks to avoid defects in molded products.
Challenges and Considerations
While molding parts are pivotal in shaping plastic components, challenges such as mold wear, temperature fluctuations, and material shrinkage must be addressed to maintain product integrity.
Understanding these nuances helps manufacturers optimize their processes for better efficiency and product quality. As technology advances, the precision and capabilities of molding parts continue to expand, opening new avenues in manufacturing innovation.
Punches create internal features in plastic parts.True
Punches are male molds that shape internal features like threads.
Cores form solid sections within plastic components.False
Cores are used to create hollow sections, not solid ones.
What Role Does the Gating System Play in Injection Molding?
In the world of injection molding, the gating system is crucial for controlling material flow and ensuring high-quality parts.
The gating system in injection molding directs the flow of molten plastic from the machine nozzle into the mold cavity. It consists of components like main channels, branch channels, gates, and cold wells, all designed to manage the speed, pressure, and direction of the plastic flow.

Understanding the Gating System’s Functionality
The gating system3 is an integral part of the injection molding process, acting as the passageway through which molten plastic flows into the mold cavity. This system is composed of several components:
- Main Channels: These are the primary pathways that carry plastic from the injection machine’s nozzle to the mold.
- Branch Channels: These distribute plastic evenly to different parts of the mold.
- Gates: Small openings that control the entry of plastic into the cavity, influencing factors like flow rate and pressure.
- Cold Wells: These catch any cold material that might solidify before reaching the cavity, preventing defects.
Each component is meticulously designed to ensure optimal flow characteristics, minimize turbulence, and maintain uniform temperature throughout the material’s journey.
Importance of Design in Gating Systems
A well-designed gating system can significantly impact the quality and efficiency4 of the final product. The design considerations include:
- Gate Location: Determines how well the cavity fills and can affect the part’s mechanical properties.
- Gate Size: Balances between filling speed and pressure requirements.
- Channel Layout: Affects pressure drop and cooling rates.
Engineers often use simulation software to predict how these factors will interact during molding, allowing them to optimize designs before production begins.
Challenges and Solutions in Gating System Design
Designing a gating system can present challenges such as:
- Warpage and Shrinkage: Uneven filling can lead to warpage or shrinkage defects.
- Flow Marks: High-speed flow might cause visible marks on parts.
- Material Wastage: Inefficient designs lead to excess material usage.
To mitigate these issues, engineers may employ techniques such as adjusting gate sizes, altering channel paths, or using multiple gates to ensure even distribution. Advanced computer simulations5 also help in predicting potential issues and optimizing designs effectively.
The gating system controls material flow in injection molding.True
It directs molten plastic flow, influencing speed and pressure.
Cold wells prevent defects by catching cold material.True
They catch solidified material, ensuring it doesn't enter the cavity.
How Does the Guide Mechanism Ensure Precise Mold Clamping?
Discover how the guide mechanism plays a crucial role in ensuring precision and efficiency in mold clamping.
The guide mechanism in injection molding ensures precise clamping by positioning, guiding, and bearing side pressure. It consists of guide pins, sleeves, and positioning cones, which align the dynamic and fixed molds accurately, preventing misalignment and ensuring uniform pressure distribution during the molding process.
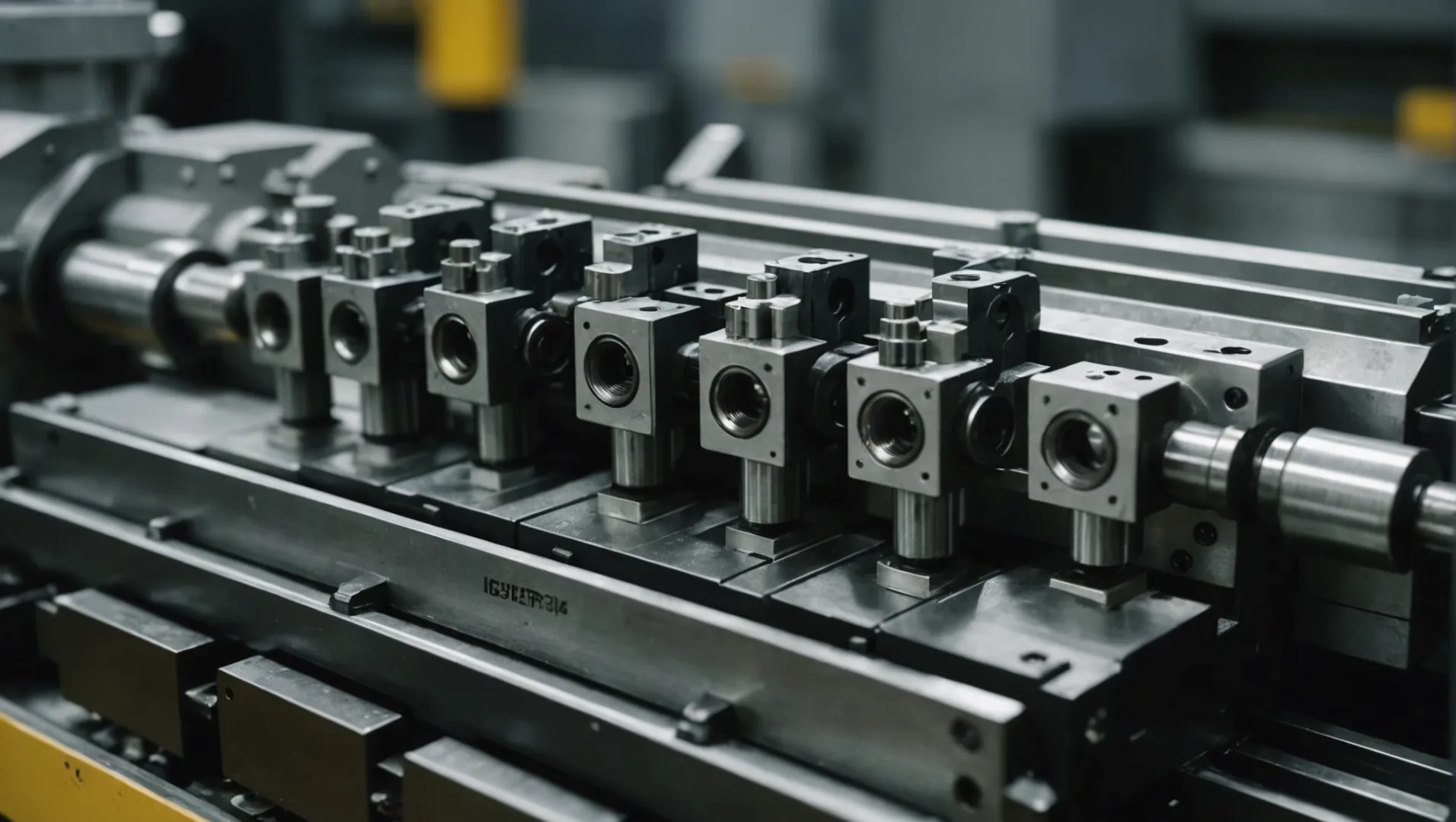
The Functionality of the Guide Mechanism
In the world of injection molding, precision is paramount. The guide mechanism is pivotal in achieving this precision by performing three critical functions: positioning, guiding, and bearing side pressure.
Positioning: Achieving Accurate Alignment
The guide mechanism employs guide pins and sleeves6, or guide holes directly opened on the template, to ensure the dynamic and fixed molds align perfectly. This alignment is crucial for achieving consistent product quality and minimizing defects like flash or mismatch.
Guiding: Smooth Mold Operation
By providing a steady path for the molds to follow, the guide mechanism facilitates smooth operation during the clamping process. This involves components like positioning cones, which help maintain mold integrity during repeated cycles.
Bearing Side Pressure: Ensuring Stability
During the injection molding process, side pressures are inevitable. The guide mechanism’s ability to withstand these pressures without compromising alignment is vital. The structural design of the guide pins and sleeves ensures that side pressures are absorbed effectively, maintaining the stability of the mold setup.
Components of the Guide Mechanism
Let’s take a closer look at the components that make up this essential mechanism:
Component | Description |
---|---|
Guide Pins | Facilitate alignment and movement between mold halves. |
Guide Sleeves | Work in tandem with pins to prevent lateral shifts. |
Positioning Cones | Ensure precise initial alignment during mold closure. |
Understanding these components’ roles helps us appreciate the meticulous design considerations that go into creating a reliable guide mechanism.
The Impact on Production Quality
The precision offered by the guide mechanism directly influences production quality. A well-aligned mold ensures uniform pressure distribution, leading to parts with consistent dimensions and surface finishes.
Without an effective guide mechanism, issues such as misalignment can cause defects that necessitate costly rework or lead to rejected batches. Thus, investing in a robust guide system is not just about operational efficiency but also about safeguarding product quality.
By ensuring precise mold clamping, the guide mechanism plays an indispensable role in achieving high-quality injection molded parts7.
Guide pins prevent mold misalignment.True
Guide pins ensure accurate alignment of dynamic and fixed molds.
Positioning cones are unnecessary in mold clamping.False
Positioning cones ensure precise initial alignment during mold closure.
Why Is the Cooling and Heating System Vital for Injection Molding?
A consistent and precise temperature is crucial in injection molding, impacting both product quality and production efficiency.
The cooling and heating system in injection molding controls mold temperature, ensuring dimensional stability, surface quality, and efficient cycle times. It involves cooling water channels and heating elements to regulate the mold’s thermal conditions, preventing defects and improving the overall quality of the molded parts.
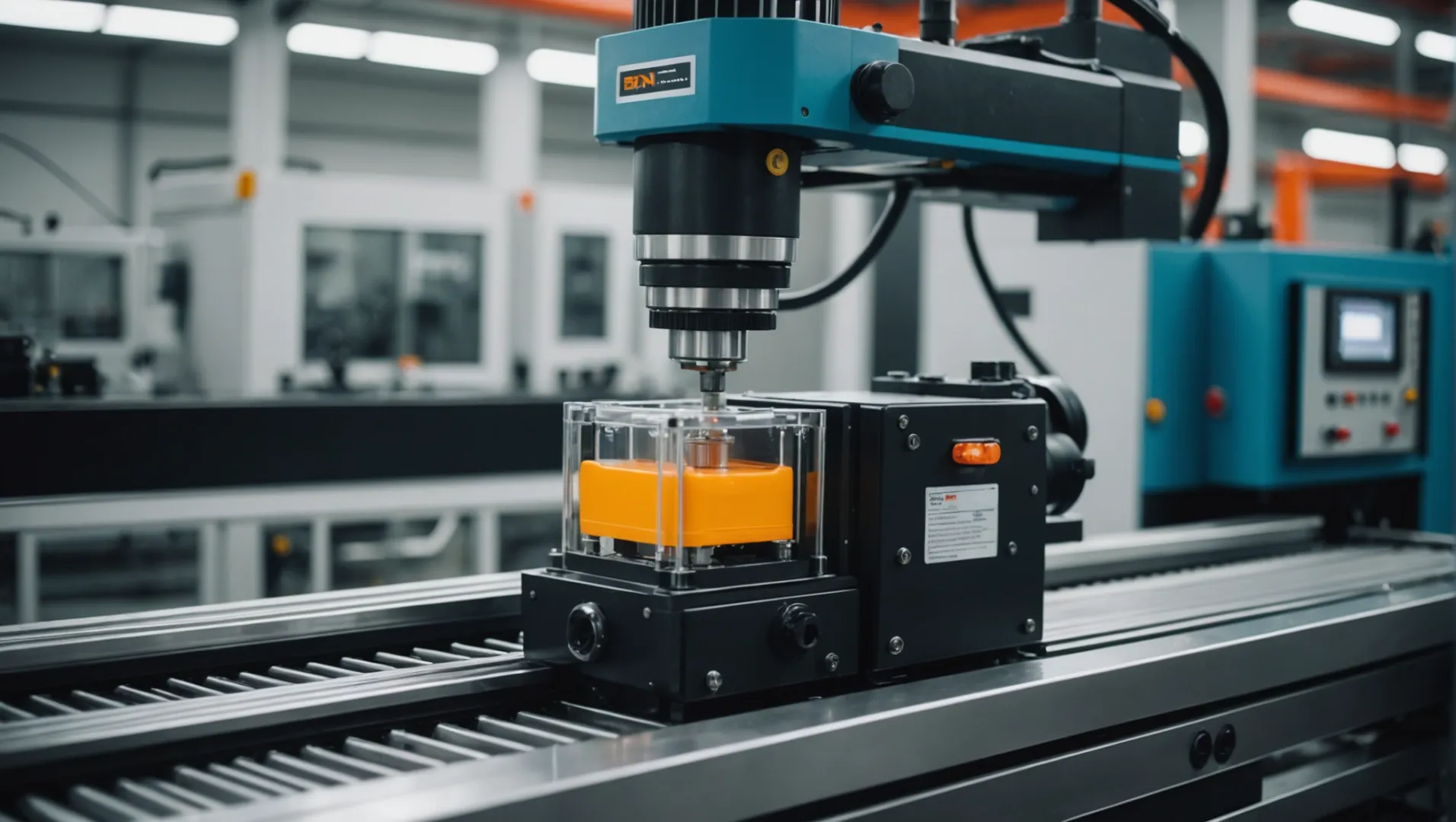
Understanding Temperature Control in Injection Molding
Temperature control is a critical aspect8 of injection molding that influences not only the cycle time but also the mechanical properties of the molded parts. By maintaining an optimal temperature, manufacturers can ensure that the plastic flows correctly within the mold cavities, minimizing defects such as warping, shrinkage, and poor surface finish.
The Role of Cooling Systems
Cooling systems in injection molds typically consist of channels through which cooling water circulates. These channels are strategically placed within the mold to efficiently remove heat from the molten plastic after it has been injected. The key objectives here are:
- Rapid Cooling: To reduce cycle time and increase productivity.
- Uniform Temperature Distribution: To prevent hot spots that can lead to inconsistent part dimensions.
For instance, a mold with well-designed cooling channels can significantly decrease cycle times, thereby enhancing throughput without compromising quality.
Heating Systems: When and Why?
Heating systems, on the other hand, are used when certain polymers require specific temperatures to maintain fluidity and ensure complete cavity filling. Electric heaters or oil circuits are commonly employed to maintain or raise the mold temperature to desired levels. This is particularly essential for:
- Thermoplastic Elastomers: Which need precise temperature control for optimal viscosity.
- High-Performance Polymers: That demand higher mold temperatures to achieve desired mechanical properties.
A well-calibrated heating system helps in minimizing stresses and improving the crystalline structure of polymers, which is crucial for applications demanding high-performance characteristics.
Balancing Both Systems for Optimal Results
The symbiotic relationship between cooling and heating systems in an injection mold cannot be overstated. These systems must work harmoniously to provide consistent temperature control throughout the molding process. Here’s a simple table illustrating the impact of both systems:
Aspect | Cooling System Impact | Heating System Impact |
---|---|---|
Cycle Time | Decreases with efficient cooling | May increase if heating is excessive |
Surface Finish | Improves with uniform cooling | Enhanced by precise heating |
Dimensional Stability | Ensures stability through rapid cooling | Ensures precision with consistent heating |
Conclusion: Why Temperature Control is Paramount
In conclusion, an effective cooling and heating system is essential for optimizing the injection molding process. It not only ensures that products meet stringent quality standards but also enhances production efficiency. Thus, understanding and implementing an effective temperature control strategy is paramount for any manufacturer aiming to leverage injection molding’s full potential.
Cooling systems reduce cycle time in injection molding.True
Efficient cooling channels decrease cycle times, boosting productivity.
Heating systems are unnecessary for thermoplastic elastomers.False
Precise heating is crucial for optimal viscosity in thermoplastic elastomers.
Conclusion
Understanding these components empowers professionals to optimize injection molding processes, ensuring quality and efficiency. Reflect on how mastering these elements can enhance your projects or career.
-
Learn about the fundamental process behind shaping plastic components.: With injection molding, molten plastic is injected into a mold cavity under high pressure, creating a part all at once. Both processes are … ↩
-
Discover how CNC machining improves mold precision and quality.: Injection mold making is the go-to method for mass-producing plastic parts. The process is streamlined to maximize cost savings and part … ↩
-
Explore the intricate role of gating systems in shaping injection-molded parts.: The “gate” is the opening in a mold through which the molten plastic is injected into the final part. It is the boundary between part and scrap. ↩
-
Learn how design impacts efficiency and quality in injection molding.: The gate dimensions have to be such that they permit the mold to be correctly filled. Shear heating rates are higher in gates with a smaller cross-section. ↩
-
Understand how simulations enhance gating system design accuracy.: Injection molding simulation software is used to make better molded parts and reduce defects. It does this by digitally simulating virtually every aspect of … ↩
-
Understand how these components aid in precise mold alignment.: A guide pin secures the plastic injection molding process against such damage by ensuring precise mold alignment. By preventing misalignment or collisions … ↩
-
Explore how precision impacts overall product quality.: It’s ideal for consistent, affordable production of a wide range of high-quality, complex plastic parts suitable for nearly any application and environment. ↩
-
Explore why temperature control is crucial in reducing defects.: When the temperatures are too low during the injection-molding process, it can bring about wavy lines or flow marks that damage the surface of … ↩