Have you ever wondered what it takes to produce high-quality plastic products? Understanding the four stages of quality control in plastic injection molding is your first step toward mastery.
The four stages of quality control in plastic injection molding are: design stage, material preparation stage, injection molding stage, and quality inspection stage. Each stage plays a crucial role in ensuring the final product meets the required standards and specifications.
But that’s just the tip of the iceberg! Let’s journey through each stage, uncovering the intricacies that guarantee superior products.
Design stage is the first step in quality control.True
The design stage initiates quality control, setting product specifications.
How Does Product Design Affect Quality in Injection Molding?
Product design is pivotal in injection molding, influencing quality from the outset. A well-thought-out design can preemptively solve potential issues, ensuring a smoother production process and superior end product.
Product design impacts injection molding quality by determining functional requirements, optimizing wall thickness, ensuring manufacturability, and perfecting mold design. Effective design minimizes defects, ensures structural integrity, and enhances manufacturability.
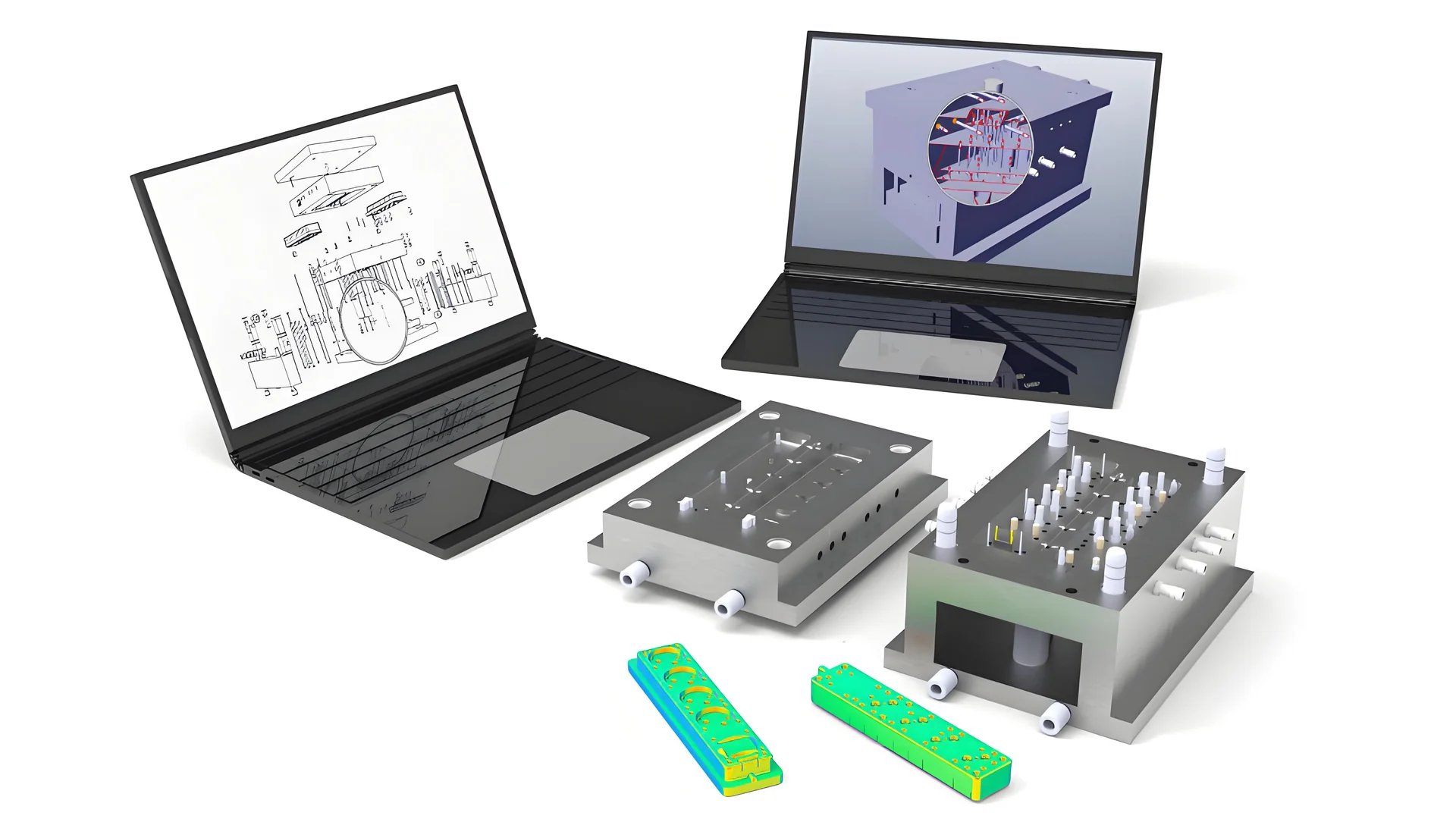
The Significance of Functional Requirements
In injection molding, understanding the functional requirements1 of a product is crucial. This involves considering the product’s use environment, durability needs, and aesthetic expectations. For instance, a product used outdoors requires materials resistant to UV exposure and temperature fluctuations. By addressing these needs during the design phase, you can avoid costly revisions later.
Wall Thickness and Structural Integrity
Determining the appropriate wall thickness is essential for maintaining the structural integrity of molded parts. Insufficient wall thickness can lead to weak points and potential failure under stress. Conversely, excessive thickness can cause issues like sink marks or warping. Designers must balance these factors to ensure that the final product remains robust and functional.
Wall Thickness Considerations | Potential Issues |
---|---|
Too Thin | Weakness, Breakage |
Too Thick | Warping, Sink Marks |
Ensuring Manufacturability
Manufacturability refers to designing products that can be easily and cost-effectively manufactured. This means avoiding overly complex geometries that are difficult to mold or demold. Designers should aim for simplicity where possible, as intricate designs can lead to increased cycle times and higher production costs.
Mold Design: The Heart of Quality
Mold design is arguably the most critical factor influencing injection molding quality. A well-designed mold ensures consistent and defect-free parts. Key considerations include:
- Runner System: Efficient runner systems ensure uniform filling of the mold cavity, reducing issues like voids or air traps.
- Cooling System: Proper cooling is vital to minimize internal stresses and prevent warping. Uniform cooling channels help achieve this by maintaining consistent cooling rates across the part.
- Parting Surface and Ejection Mechanism: These elements must be meticulously planned to allow smooth demolding without damage.
Understanding the impact of mold design2 on production efficiency and product quality highlights the interconnected nature of product design and manufacturing outcomes.
Proper wall thickness ensures structural integrity.True
Correct wall thickness prevents weak points and maintains strength.
Complex geometries reduce manufacturability in molding.True
Intricate designs increase cycle times and production costs.
Why Is Material Preparation Crucial for Injection Molding?
The success of injection molding relies heavily on meticulous material preparation, ensuring both the quality and consistency of the final product.
Material preparation is crucial in injection molding as it involves selecting appropriate raw materials and pre-treating them for optimal performance. This step ensures material consistency, reduces defects, and enhances the quality of the final product, thereby meeting the required specifications and standards.
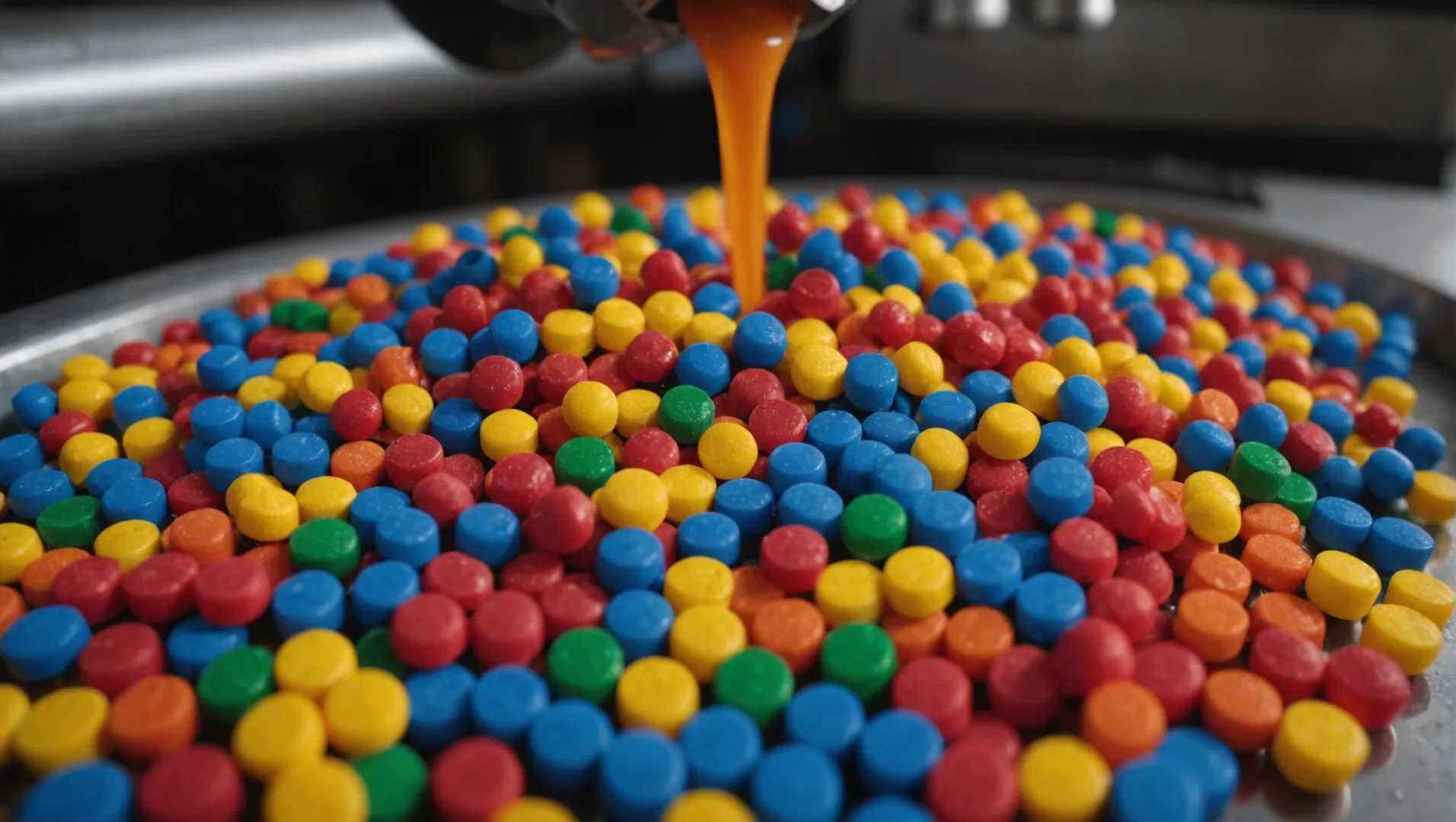
The Importance of Raw Material Selection
Selecting the right raw materials is the foundation of successful injection molding3. Different plastics offer unique properties such as strength, heat resistance, and flexibility, making them suitable for specific applications. For instance, while polypropylene is chosen for its flexibility, polycarbonate is preferred for its impact resistance.
Choosing inappropriate materials can lead to defects such as warping or brittleness, which compromise the product’s functionality. Therefore, understanding the performance requirements and environmental conditions of the final product is essential for selecting the most suitable raw materials.
Material Pretreatment: A Necessity
Before the injection process begins, some plastic materials require pretreatment to enhance their properties. For example, plastics like nylon and polycarbonate are hygroscopic, meaning they absorb moisture from the environment. This moisture can lead to defects like bubbles in the finished product if not removed through drying.
Preheating materials can also improve flow characteristics during injection, reducing the required pressure and minimizing internal stress. This step is crucial in producing a defect-free, high-quality product.
Ensuring Quality Through Consistency
Consistent material quality is a non-negotiable aspect of successful injection molding. Variations in material properties can lead to unpredictable results and defects in the final product. Therefore, sourcing raw materials from reputable suppliers and conducting thorough inspections are necessary steps to ensure uniformity.
Regular checks and balances in material preparation help prevent issues during production, saving time and resources by reducing the likelihood of defects emerging later in the process.
Conclusion: Setting the Stage for Success
While raw material selection and pretreatment are just parts of the larger injection molding process, they lay a critical foundation. By emphasizing material preparation, manufacturers set themselves up for success, ensuring that subsequent stages such as molding and inspection proceed smoothly, resulting in superior products.
Material pretreatment reduces injection molding defects.True
Pretreating materials like drying hygroscopic plastics prevents defects.
Polycarbonate is unsuitable for impact-resistant products.False
Polycarbonate is chosen for its excellent impact resistance properties.
What Role Do Process Parameters Play in Injection Molding Quality?
In injection molding, precise control of process parameters is critical to achieving high-quality products with minimal defects.
Process parameters such as injection temperature, pressure, speed, and cooling time are vital in determining the quality of injection molded products. Proper settings ensure optimal material flow, reduce defects like warping or flash, and maintain dimensional stability.

Understanding Key Process Parameters
In the world of injection molding4, process parameters are the levers that adjust the quality and consistency of molded parts. By fine-tuning these settings, manufacturers can ensure that each product meets stringent quality standards. Here’s a closer look at the key parameters:
1. Injection Temperature
The injection temperature is set based on the specific material being used. For instance, thermoplastics require precise temperature settings to melt adequately without degrading. An incorrect temperature can lead to issues such as incomplete filling or material degradation.
- Too High: Can cause decomposition and discoloration.
- Too Low: Results in poor material flow and incomplete cavity filling.
2. Injection Pressure and Speed
These parameters work hand-in-hand to drive molten plastic into the mold cavities efficiently.
- High Pressure/Speed: May cause flashes or increased internal stresses.
- Low Pressure/Speed: Leads to insufficient filling and surface defects.
Parameter | High Setting Issues | Low Setting Issues |
---|---|---|
Pressure | Flash, stress | Poor fill |
Speed | Stress, defects | Surface issues |
3. Holding and Cooling Time
The holding time allows the material to solidify under pressure, while cooling time ensures the part is stable before ejection.
- Extended Holding: Might induce high internal stress and deformation.
- Shortened Cooling: Can result in shrinkage or warping.
Properly managing these times ensures parts maintain dimensional stability and performance characteristics.
The Impact on Product Quality
Adjusting these parameters influences the final product’s appearance, strength, and durability. For example, maintaining an optimal cooling rate minimizes internal stresses5 that could compromise product integrity.
Regular Equipment Maintenance
Ensuring that all equipment components, such as heaters and coolers, are functioning optimally is crucial. Regular maintenance checks prevent deviations in process parameters that could lead to quality issues.
Proper control of process parameters ensures each molded part meets the desired specifications and functions as intended in its application. By understanding these variables, manufacturers can enhance productivity while reducing waste and rework.
High injection speed causes increased internal stresses.True
High injection speed can lead to increased internal stresses in molded parts.
Low cooling time results in better dimensional stability.False
Short cooling time can cause shrinkage or warping, reducing stability.
How Is Quality Inspection Conducted in Injection Molding?
Quality inspection in injection molding is a meticulous process ensuring products meet strict standards. Here’s how it’s done.
Quality inspection in injection molding involves appearance inspection, performance testing, and sampling inspection. These steps ensure that each product meets the desired specifications and performance criteria, maintaining high standards and consistency throughout production.
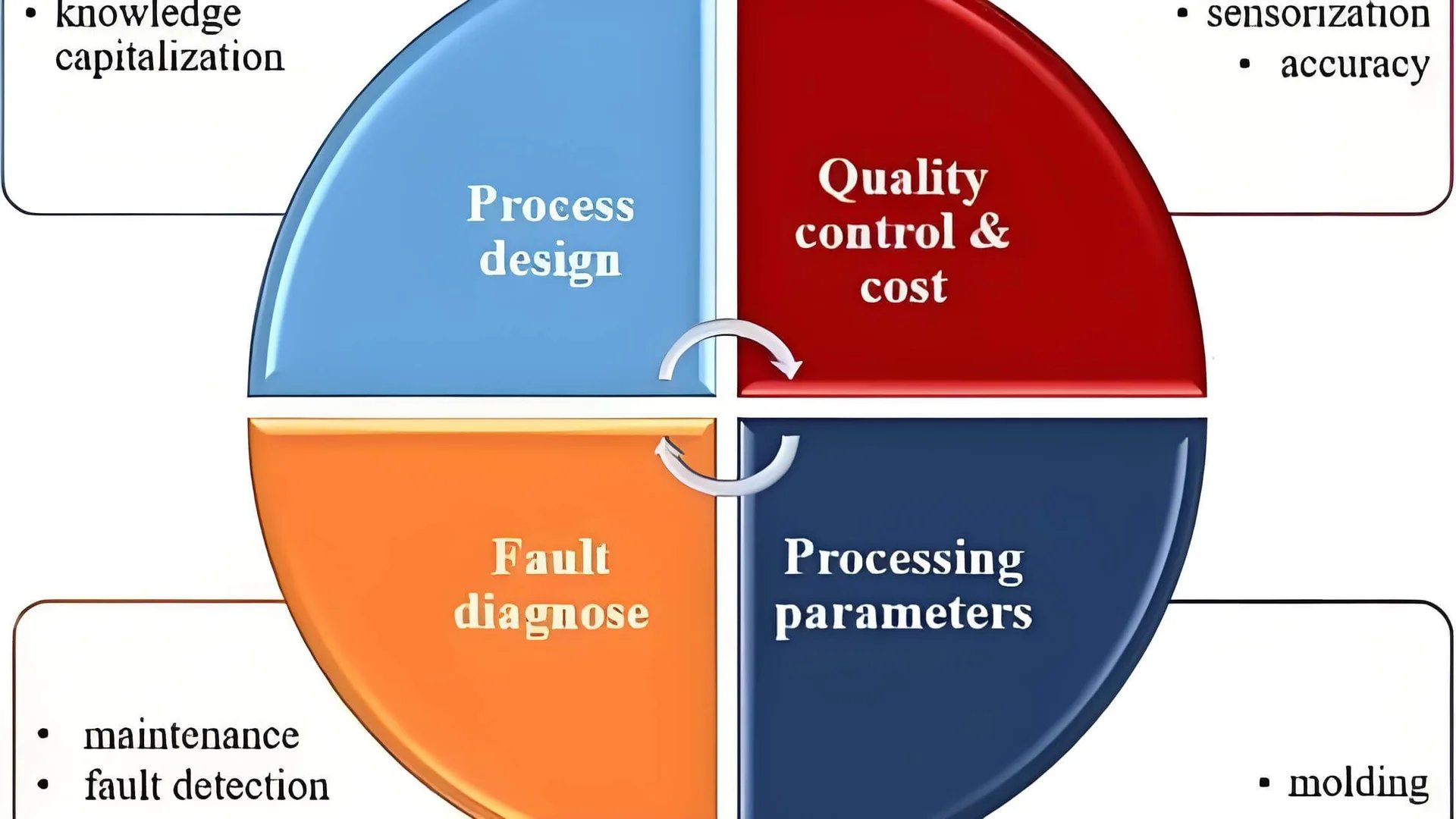
Appearance Inspection: Ensuring Aesthetic Excellence
The first step in the quality inspection process is appearance inspection6. This involves scrutinizing the product for any visible defects such as bubbles, silver wires, flash, or scratches. The color must be uniform and the dimensions should adhere to specified tolerances to guarantee proper assembly performance. A thorough appearance inspection is crucial as even minor defects can affect the product’s functionality and marketability.
Key Points for Appearance Inspection:
- Surface Quality: Check for blemishes or surface imperfections.
- Color Consistency: Ensure the color matches the required standard across all products.
- Dimensional Accuracy: Verify that dimensions fall within acceptable tolerance levels.
Performance Inspection: Assessing Functional Integrity
Performance inspection tests the strength, hardness, heat resistance, and corrosion resistance of the product. Various methods and standards are used depending on the product’s intended use. If a product fails to meet these performance standards, it’s crucial to analyze the root cause and implement corrective measures.
Performance Inspection Techniques:
- Tensile Testing: Evaluates strength and flexibility.
- Thermal Analysis: Assesses heat resistance and stability.
- Hardness Testing: Measures resistance to deformation.
Sampling Inspection: Monitoring Quality Consistency
Sampling inspection is conducted during production to ensure ongoing quality stability. The frequency and sample size are determined by the product’s quality requirements and production scale. Early detection of quality issues through sampling allows for timely adjustments in the manufacturing process, reducing waste and improving efficiency.
Sampling Inspection Strategies:
- Random Sampling: Helps detect sporadic defects.
- Statistical Process Control (SPC): Monitors and controls production quality.
- Corrective Actions: Adjusts processes based on sampling results to enhance quality.
In conclusion, each of these inspection stages plays a vital role in maintaining the high standards expected in injection molding, ensuring that every product not only meets but exceeds customer expectations in terms of quality and performance.
Appearance inspection checks for surface blemishes.True
Appearance inspection involves checking for visible defects like blemishes.
Sampling inspection occurs at the end of production.False
Sampling inspection is conducted during production to ensure quality.
Conclusion
Mastering these four stages is essential for producing high-quality plastic products. Reflect on these practices to enhance your production processes.
-
Learn how functional requirements shape effective product designs.: They assess the part design and make modifications and recommendations based on key product requirements including product usage and function. ↩
-
Discover how mold design influences quality in injection molding.: The quality of your injection-molded product can be influenced by the design of the mold, the wall thickness of the end-product, type of runner, and even the … ↩
-
Explores why choosing correct materials is vital for product integrity.: Materials such as thermoplastic, polypropylene, polystyrene, and others play a vital role in determining the final product’s quality, durability, and … ↩
-
Learn why process parameters are vital for molding precision.: By fine-tuning temperature, pressure, speed, and other key factors, you can achieve consistent, high-quality results while minimizing defects … ↩
-
Discover how cooling rates influence product integrity.: It is displayed this way because as the plastic resin cools, it shrinks, which reduces the mold cavity pressure. ↩
-
Understand how surface defects affect product quality and corrections needed.: In this blog post, we will guide you through why dimensional inspections matter and the key steps and best practices for conducting dimensional inspections. ↩