In injection molding, keeping your materials in top shape isn’t just important—it’s everything! Let me share how I ensure my products shine.
To prevent material degradation in injection molding, it is essential to focus on selecting suitable raw materials with good thermal stability, optimizing process parameters like temperature and pressure, and maintaining equipment regularly. These steps help ensure consistent product quality and performance.
Now that we understand the importance of these foundational elements, let’s dive deeper into effective strategies that can transform your injection molding process!
Proper storage prevents raw material degradation.True
Storing materials in cool, dry environments maintains their integrity.
What Are the Best Practices for Raw Material Storage?
Proper storage of raw materials is crucial in preventing material degradation during injection molding. Implementing best practices can significantly extend the shelf life and maintain the quality of materials.
Store raw materials in a dry, cool, well-ventilated environment away from direct sunlight and chemicals to prevent degradation. Maintain suitable temperature and humidity levels, and ensure safety from fire hazards and flammable materials.
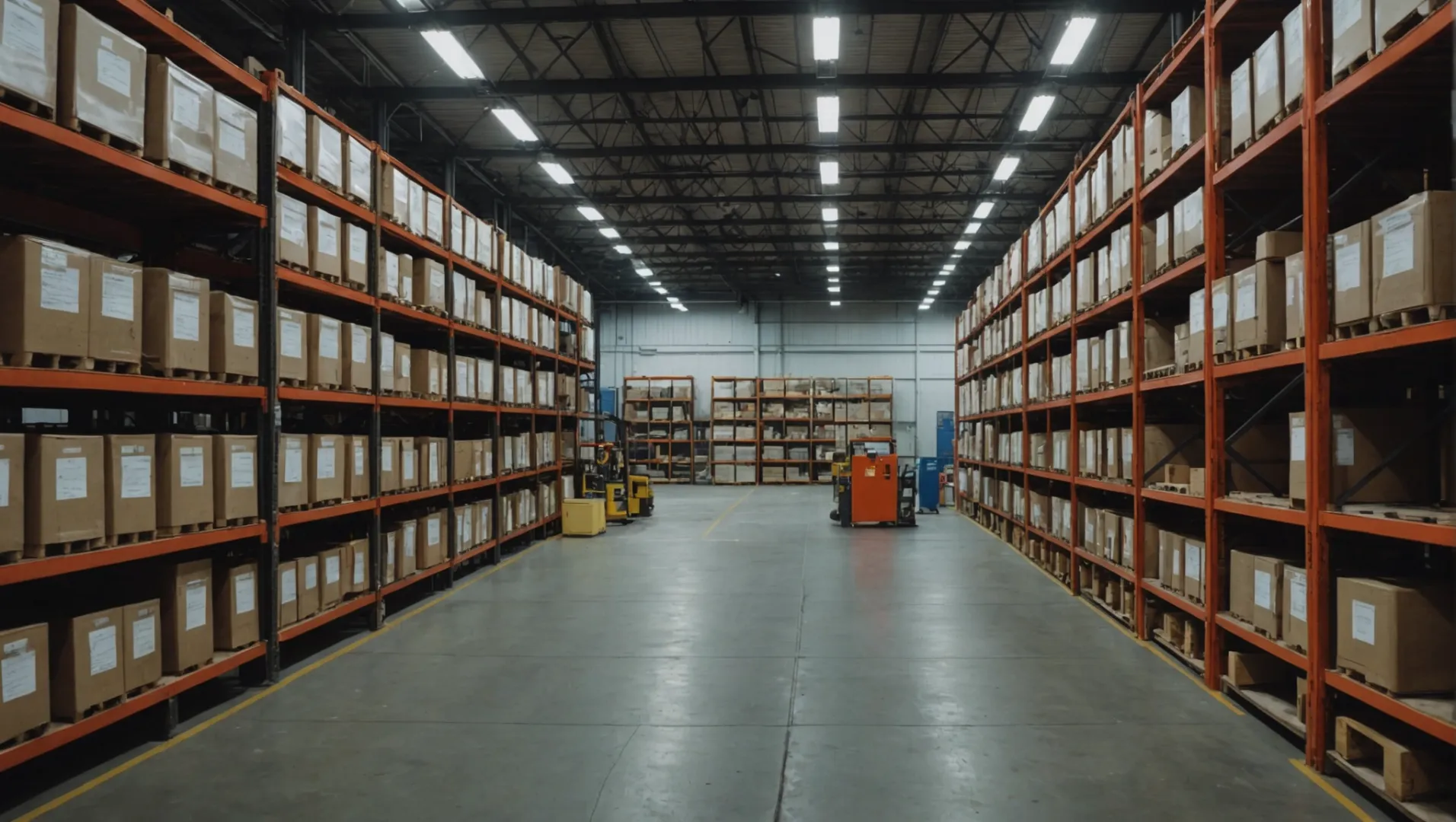
Importance of Environment Control
Storing raw materials in an environment that is dry, cool, and well-ventilated is critical for preserving their integrity. High temperatures and humidity can accelerate degradation. Therefore, facilities should aim to maintain optimal conditions.
- Temperature: Ensure the storage area is cool. High temperatures can cause thermal degradation in plastics.
- Humidity: A dry environment prevents moisture from interacting with raw materials, which could lead to chemical reactions.
Safety Precautions
To prevent potential hazards, storage areas must be clear of fire sources and flammable materials. Implementing fire safety measures can protect both the material and the facility.
- Fire Safety: Equip storage areas with fire extinguishers and smoke detectors.
- Chemical Safety: Avoid storing raw materials near chemicals that could induce unwanted reactions.
Ensuring Raw Material Purity
Raw material purity is essential to avoid triggering degradation reactions. Collaborate with reputable suppliers and verify purity through certificates or test reports.
- Supplier Verification: Choose suppliers with proven track records and quality certifications.
- Regular Testing: Conduct routine checks on material batches for impurities.
Organizing Storage Facilities
Efficient organization within storage facilities can prevent cross-contamination and maintain easy access.
Storage Factor | Best Practice |
---|---|
Labeling | Clearly label all material types |
Segregation | Separate by type and batch |
Accessibility | Keep frequently used materials handy |
Implementing these best practices ensures that raw materials remain stable and ready for use in injection molding processes1.
Raw materials should be stored away from direct sunlight.True
Direct sunlight can degrade materials, reducing their quality and lifespan.
High humidity is beneficial for raw material storage.False
High humidity can cause chemical reactions, degrading raw materials.
How Do You Optimize Injection Molding Process Parameters?
Optimizing injection molding parameters is crucial for enhancing product quality and preventing material degradation. Mastering the control of temperature, pressure, and timing can significantly improve the efficiency and outcomes of the molding process.
Optimizing injection molding process parameters involves adjusting temperature, pressure, and cooling times to match material characteristics and product requirements, thereby minimizing material degradation and enhancing product quality.
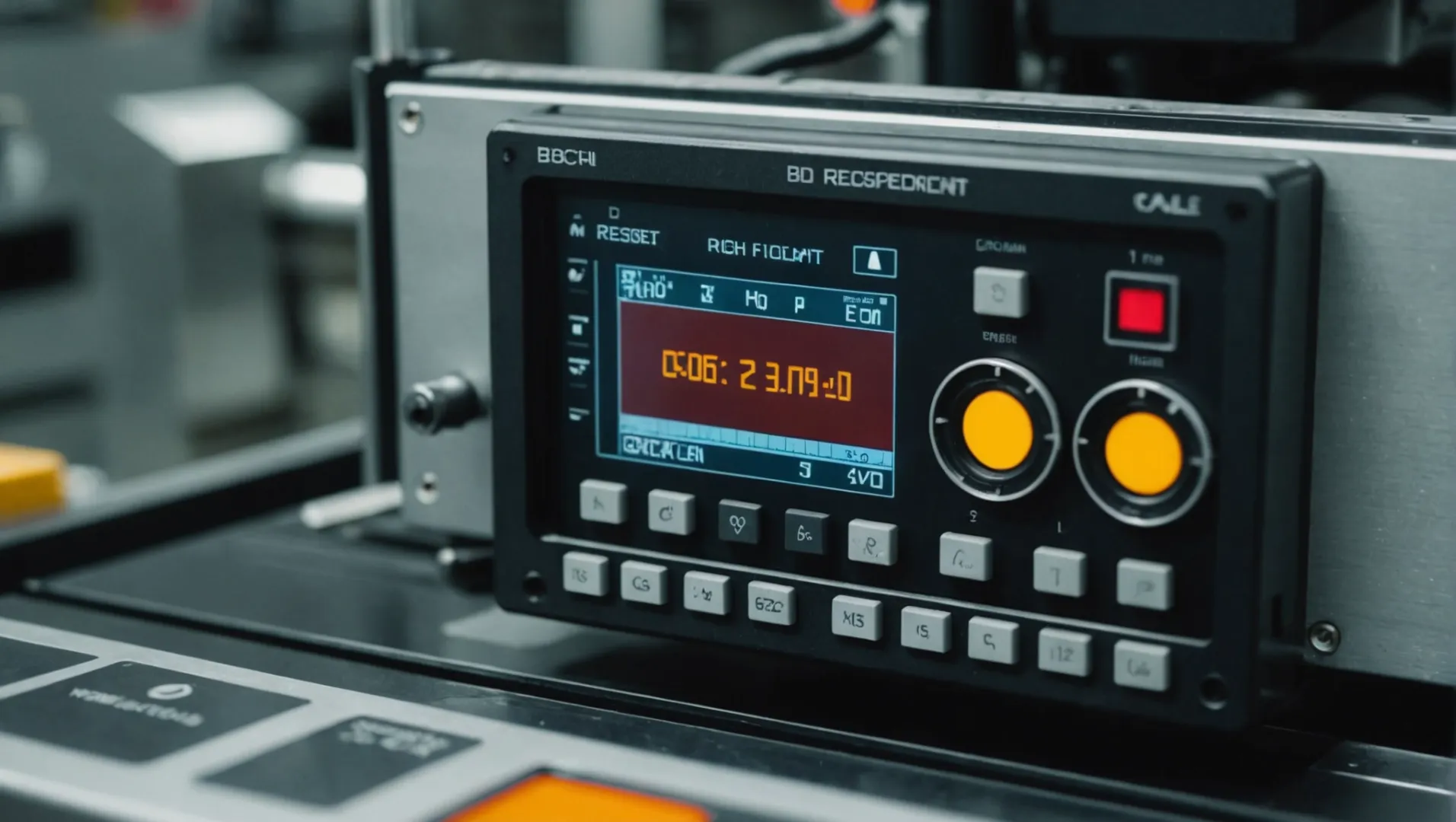
Control Temperature for Material Stability
Temperature control is pivotal in the injection molding process. Begin by setting the barrel temperature to align with the plastic material’s specific characteristics. An excessively high temperature can lead to material decomposition, while a low temperature might cause poor plasticization.
For example, when working with high-temperature engineering plastics2, selecting materials with superior thermal stability is crucial. Consult the technical data sheets from material suppliers or conduct experimental trials to identify the optimal temperature range.
Additionally, managing the nozzle temperature helps prevent degradation at the nozzle. If the nozzle is too hot, it risks degrading the material; too cold, it affects fluidity and raises injection pressure. Meanwhile, mold temperature influences material stability—keeping it within a reasonable range reduces risks for temperature-sensitive plastics.
Adjust Injection Pressure and Speed
Injection pressure and speed are critical factors that need careful adjustment. Excessive pressure or speed can subject materials to high shear forces, causing degradation.
To optimize these parameters, trial molding is recommended. Start with a lower pressure and speed, then gradually increase if product defects arise, ensuring not to exceed material tolerance. Here’s a simple table illustrating potential adjustments:
Parameter | Initial Setting | Adjustment Strategy |
---|---|---|
Injection Pressure | Low | Increase until optimal |
Injection Speed | Low | Increase until optimal |
Fine-tune Injection and Cooling Times
Both injection and cooling times impact the final product’s integrity. Prolonged injection time can increase degradation risk by leaving materials in the barrel or mold longer than necessary. Cooling time should be enough to stabilize product dimensions but not so long that it impedes production efficiency.
Optimize cooling time by tweaking cooling water channel flow or using effective coolants to find a balance between quality and efficiency.
By focusing on these detailed aspects of the injection molding process parameters, manufacturers can ensure minimal material degradation while maximizing product quality and consistency. Understanding the nuances of each parameter offers a robust approach to achieving superior outcomes in injection molding.
High nozzle temperature degrades material.True
Excessive heat at the nozzle can cause material breakdown.
Long cooling times always improve product quality.False
Overly long cooling times can reduce production efficiency without quality gains.
Why Is Equipment Maintenance Critical in Injection Molding?
Equipment maintenance is vital in injection molding to ensure the machinery operates efficiently, reducing the risk of material degradation and production downtime.
Equipment maintenance in injection molding prevents material degradation by ensuring optimal machine performance, reducing downtime, and maintaining product quality. Regular checks and cleaning of components like screws and barrels are essential.
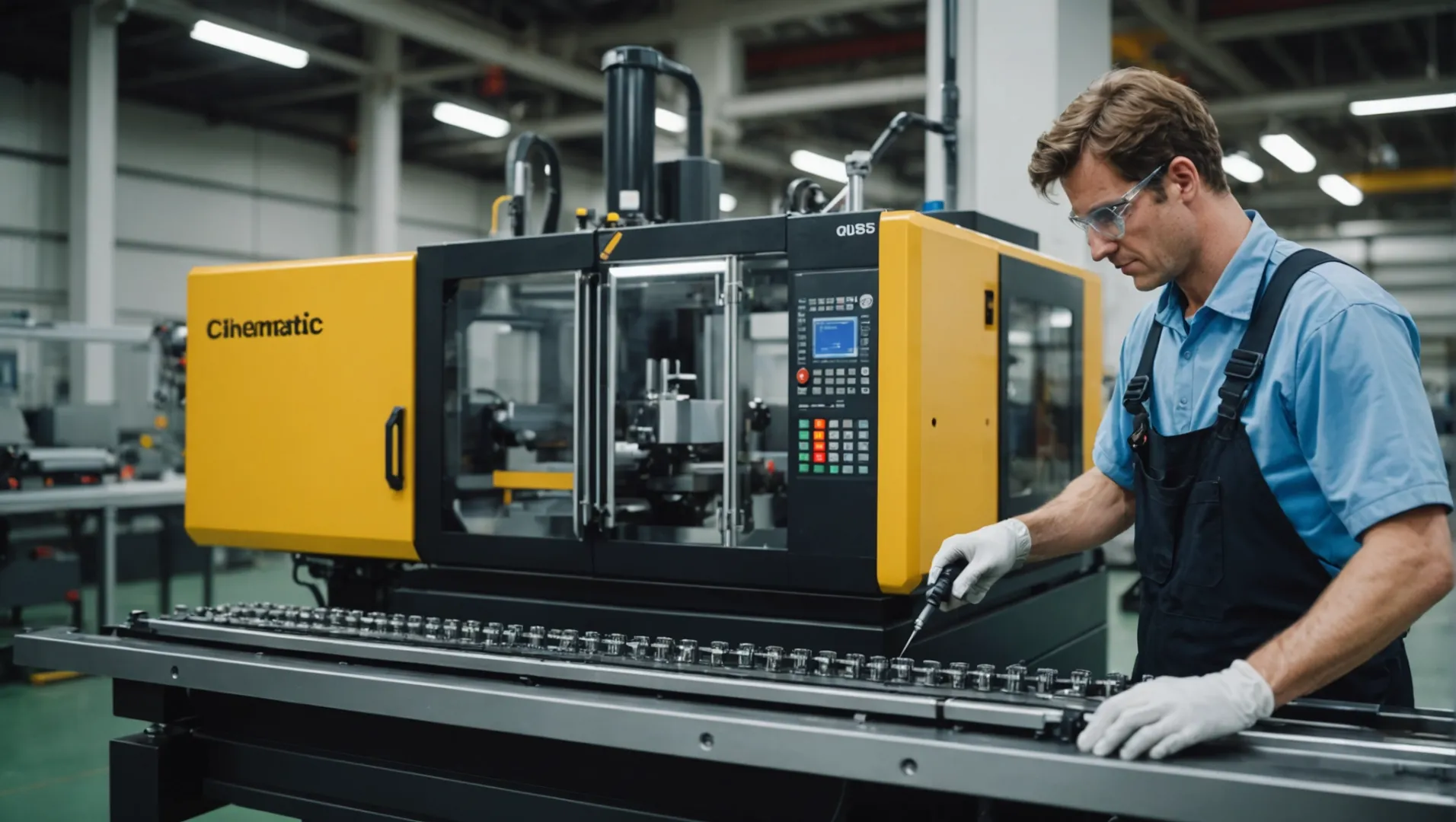
The Role of Equipment Maintenance in Injection Molding
In the injection molding process3, machinery efficiency directly impacts the quality of the final product. Regular maintenance ensures that machines run smoothly, reducing the likelihood of defects caused by equipment-related issues. A well-maintained machine also optimizes energy use, saving costs in the long run.
-
Regular Inspections: Conducting routine checks on key components such as the heating system, cooling system, and hydraulic system is crucial. These inspections can help identify wear and tear early, preventing unexpected breakdowns that could halt production.
-
Component Wear and Tear: The screw and barrel of an injection molding machine are subject to significant stress during operation. Wear in these areas can lead to uneven material shear, which increases the risk of degradation. Regular assessments can determine when replacements or repairs are necessary.
-
System Calibration: Ensuring that all systems are correctly calibrated is another critical aspect. Miscalibrated machines can lead to improper heating and cooling cycles, resulting in defective products or wasted materials.
Cleaning Protocols and Their Importance
Maintaining cleanliness is not just about aesthetics; it plays a pivotal role in preventing degradation.
-
Residual Material Buildup: Leftover plastic or impurities in the hopper, screw, or mold can initiate degradation reactions. Regular cleaning schedules help remove these residues, maintaining the integrity of the molded products.
-
Use of Suitable Cleaning Agents: It’s important to select cleaning solutions that are non-corrosive to the materials being processed. Safety should also be prioritized during cleaning to prevent accidents.
Cost Implications of Poor Maintenance
Neglecting equipment maintenance not only leads to quality issues but also escalates operational costs.
-
Increased Downtime: Unplanned maintenance due to equipment failure can lead to significant production delays. This downtime can disrupt delivery schedules and incur additional costs from idle labor and machinery.
-
Long-term Equipment Damage: Without proper maintenance, machines may suffer from irreversible damage, leading to costly replacements rather than repairs.
Incorporating systematic maintenance routines and adhering to recommended practices ensures not only the longevity of your equipment but also consistency in product quality, ultimately safeguarding your business’s reputation and bottom line.
Regular maintenance reduces injection molding downtime.True
Routine checks prevent unexpected breakdowns, minimizing production delays.
Neglecting maintenance saves costs in injection molding.False
Poor maintenance leads to increased downtime and equipment damage, raising costs.
What Role Does Operator Training Play in Preventing Degradation?
Operator training is a crucial yet often underestimated aspect of preventing material degradation in injection molding.
Operator training plays a pivotal role in preventing degradation by equipping personnel with the knowledge and skills needed to manage raw materials, optimize machine parameters, and maintain equipment efficiently. Well-trained operators can significantly reduce the risk of errors that lead to material degradation.
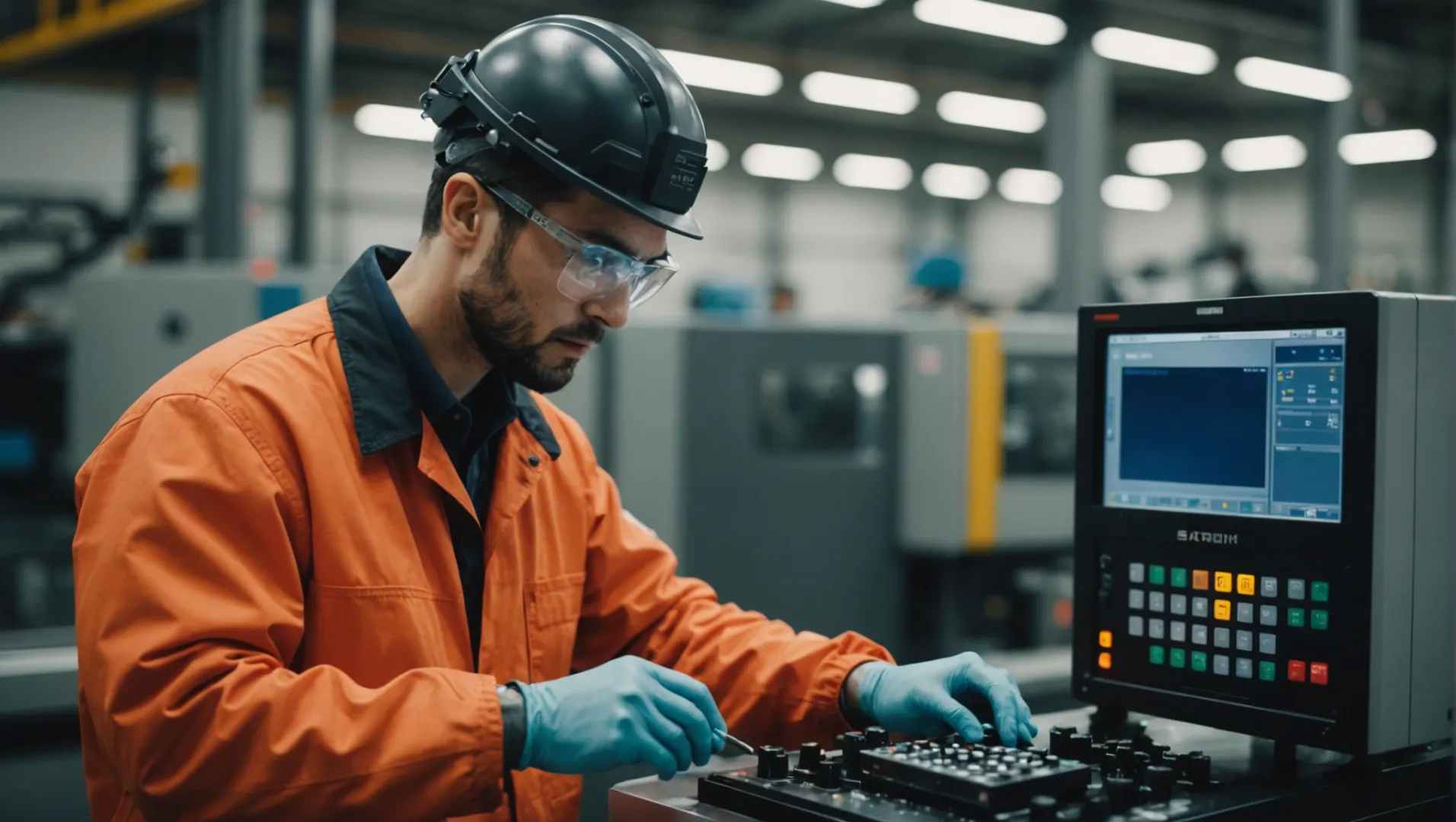
Understanding Material Properties and Degradation
Operators need comprehensive training on the properties of the materials they handle. By understanding the thermal stability and degradation mechanisms of various plastics, operators can make informed decisions about process parameters. This knowledge empowers them to identify and mitigate potential risks during production.
For instance, knowing that certain materials degrade at high temperatures allows operators to adjust machine settings accordingly. They can monitor for signs of degradation, such as discoloration or unusual odors, and take proactive steps to correct these issues.
Mastering Process Parameters
Training should focus on optimizing process parameters4 like temperature, pressure, and speed. Operators learn to set these parameters based on material characteristics and product requirements.
Consider a scenario where the barrel temperature is set too high, leading to overheating and decomposition of the material. A well-trained operator would recognize this risk and adjust the temperature to fall within a safe range, preserving material integrity.
Equipment Maintenance and Troubleshooting
Regular maintenance is vital to preventing equipment-related degradation. Operators should be trained to inspect machines5 for wear and tear, clean components, and troubleshoot common issues.
For example, a worn screw or barrel can cause uneven shear forces during molding, leading to degradation. Operators trained in maintenance can identify such issues early and coordinate timely repairs.
Continuous Improvement through Feedback
Encouraging operators to provide feedback on processes fosters a culture of continuous improvement. Training programs should include mechanisms for operators to report challenges or suggest enhancements.
Operators might observe that specific settings yield better results for certain products. Their insights can be invaluable for refining process parameters and training protocols, ultimately reducing the risk of degradation.
Safety and Compliance Training
Safety training is essential not only for operator well-being but also for material integrity. Proper handling of chemicals and adherence to safety standards prevent accidental contamination or degradation.
By understanding safety protocols, operators can ensure that raw materials remain uncontaminated throughout the molding process, maintaining high product quality.
Operator training reduces material degradation risk.True
Training equips operators to manage materials and machine settings effectively.
Lack of training leads to higher equipment wear.True
Untrained operators may not identify or fix wear issues promptly.
Conclusion
By focusing on strategic practices like careful material selection and diligent equipment maintenance, we can achieve remarkable results in our injection molding endeavors.
-
Explore detailed guidelines on proper storage techniques for injection molding.: 1. A list of raw materials and their basic reaction to atmospheric conditions (read humidity) should be made. · 2. An initial approval of mixing … ↩
-
Explore high-temperature engineering plastics for improved thermal stability.: Polybenzimidazole (PBI) has the highest heat and wear resistance, strength, and mechanical property stability of any engineering thermoplastic … ↩
-
Learn why regular maintenance is crucial for machine efficiency.: However, like any machinery, injection molding equipment requires regular maintenance to ensure optimal performance, longevity, and safety. ↩
-
Discover strategies for setting optimal process parameters.: Steps to INJECTION MOLDING Process Optimization · 1. Tool functionality examination · 2. Short shot testing · 3. Gate seal studies · 4. Sample parts evaluation/data … ↩
-
Learn effective techniques for inspecting and maintaining machines.: 1. Keep Molds and Components Clean and Dry 2. Perform Safety Checks 3. Ensure Your Machine Is Level and Parallel 4. Check Your Oil 5. Check Electrical … ↩