Injection molding is not just a technical process; it’s an art that blends precision with creativity. With the right strategies, you can elevate efficiency and product quality to new heights.
To optimize an injection molding process, focus on selecting suitable materials, designing efficient molds, adjusting process parameters like pressure and temperature, implementing robust quality control, and ensuring thorough personnel training.
But this overview is just the tip of the iceberg! Join me as we dive deeper into these strategies to unlock unparalleled efficiencies and quality improvements.
Material selection impacts injection molding efficiency.True
Choosing the right materials ensures optimal flow and reduces defects.

How Does Material Selection Impact Injection Molding Efficiency?
Material selection is a pivotal factor in the injection molding process, significantly influencing efficiency and product quality.
Choosing the right material for injection molding enhances efficiency by ensuring optimal flow, reducing defects, and aligning with performance and cost requirements. Proper material selection minimizes waste and energy consumption, leading to improved productivity.
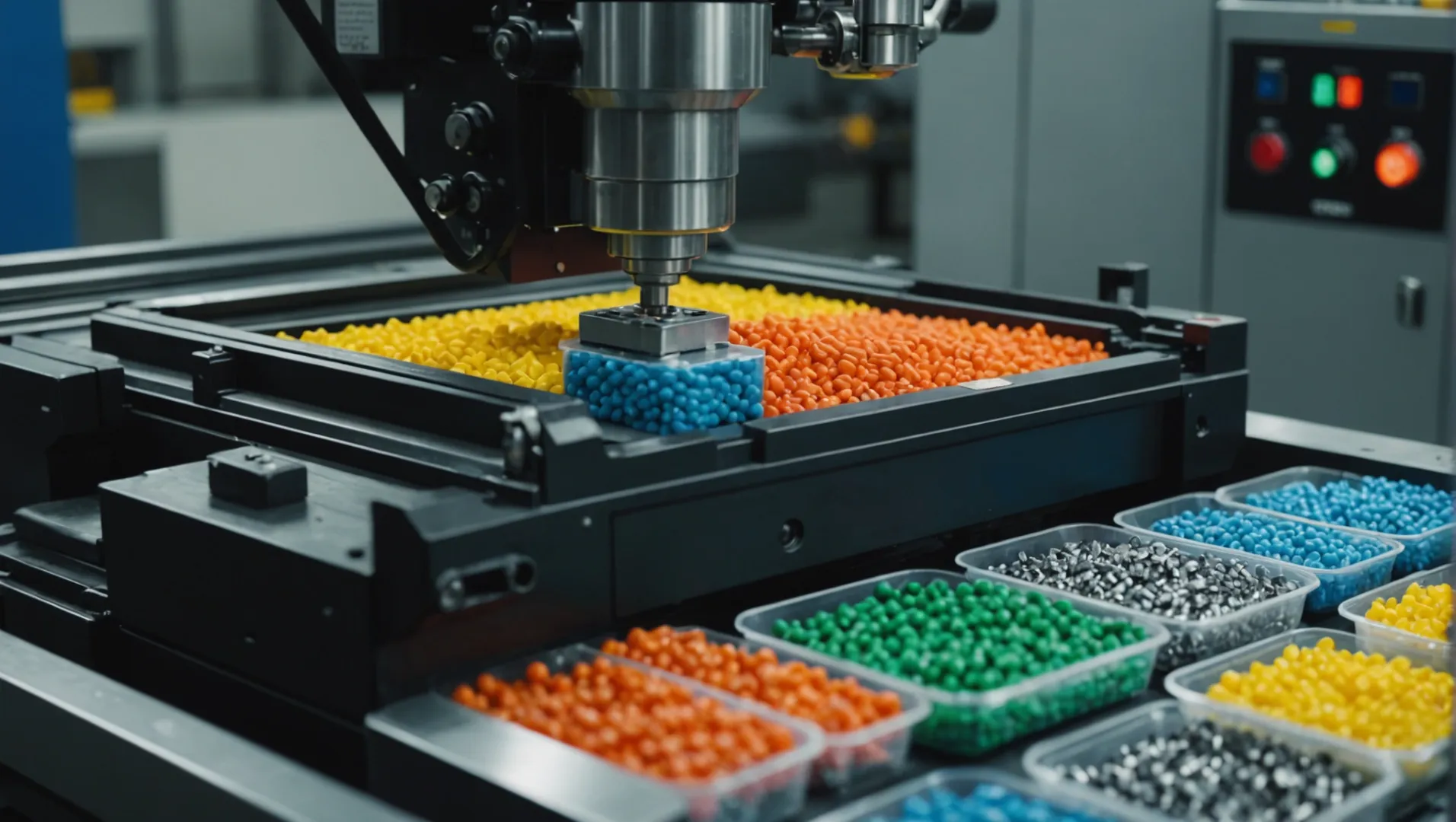
The Importance of Selecting Suitable Plastic Raw Materials
Choosing the right plastic material is the cornerstone of an efficient injection molding process1. The selected material must meet performance requirements, environmental conditions, and cost considerations. Each type of plastic offers unique properties like fluidity, shrinkage, and heat resistance, all of which play critical roles in the molding process.
For instance, materials with high fluidity can fill molds more quickly and completely, reducing cycle times and increasing productivity. On the other hand, a material with a high shrinkage rate might lead to dimensional inaccuracies and defects.
A detailed table below illustrates common plastics used in injection molding and their properties:
Material | Fluidity | Shrinkage | Heat Resistance |
---|---|---|---|
Polyethylene | High | Medium | Low |
Polypropylene | Medium | Low | Medium |
ABS | Low | Low | High |
Ensuring Quality Stability with Reliable Suppliers
The stability of raw materials across batches is crucial for maintaining consistent product quality. Partnering with reliable suppliers who provide quality assurance can help ensure that each batch of material performs as expected, thus preventing unexpected downtimes and defects.
The Role of Raw Material Pretreatment
Before entering the molding machine, raw materials often require pretreatment to remove moisture, which can otherwise affect their fluidity and lead to defects like bubbles or silver streaks. Additionally, additives can be incorporated to tailor the properties of the plastic to specific product requirements. This includes color matching or enhancing thermal stability.
Case Study: Material Selection in High-Performance Applications
Consider the automotive industry, where injection-molded parts must withstand high temperatures and mechanical stress. Using a polymer such as polyamide (nylon) can significantly boost efficiency by reducing the need for post-processing and enhancing durability. This choice also aligns with cost-effectiveness2 when compared to metals.
Conclusion
Optimizing material selection in injection molding not only improves efficiency but also reduces waste, energy consumption, and overall production costs. By understanding and leveraging the unique properties of different plastics, manufacturers can achieve superior product quality and operational efficiency.
Polyethylene has high fluidity in injection molding.True
Polyethylene is known for its high fluidity, aiding mold filling.
ABS has a high shrinkage rate in injection molding.False
ABS is characterized by low shrinkage, ensuring dimensional accuracy.
What Role Does Mold Design Play in Product Quality?
Mold design is a pivotal factor in injection molding, directly influencing product quality and manufacturing efficiency. Without a well-conceived mold, even the best materials and parameters can’t achieve optimal results.
Mold design plays a critical role in product quality by ensuring uniform material flow, reducing defects, and facilitating efficient cooling. A well-designed mold leads to improved structural integrity and aesthetic precision in the final product.
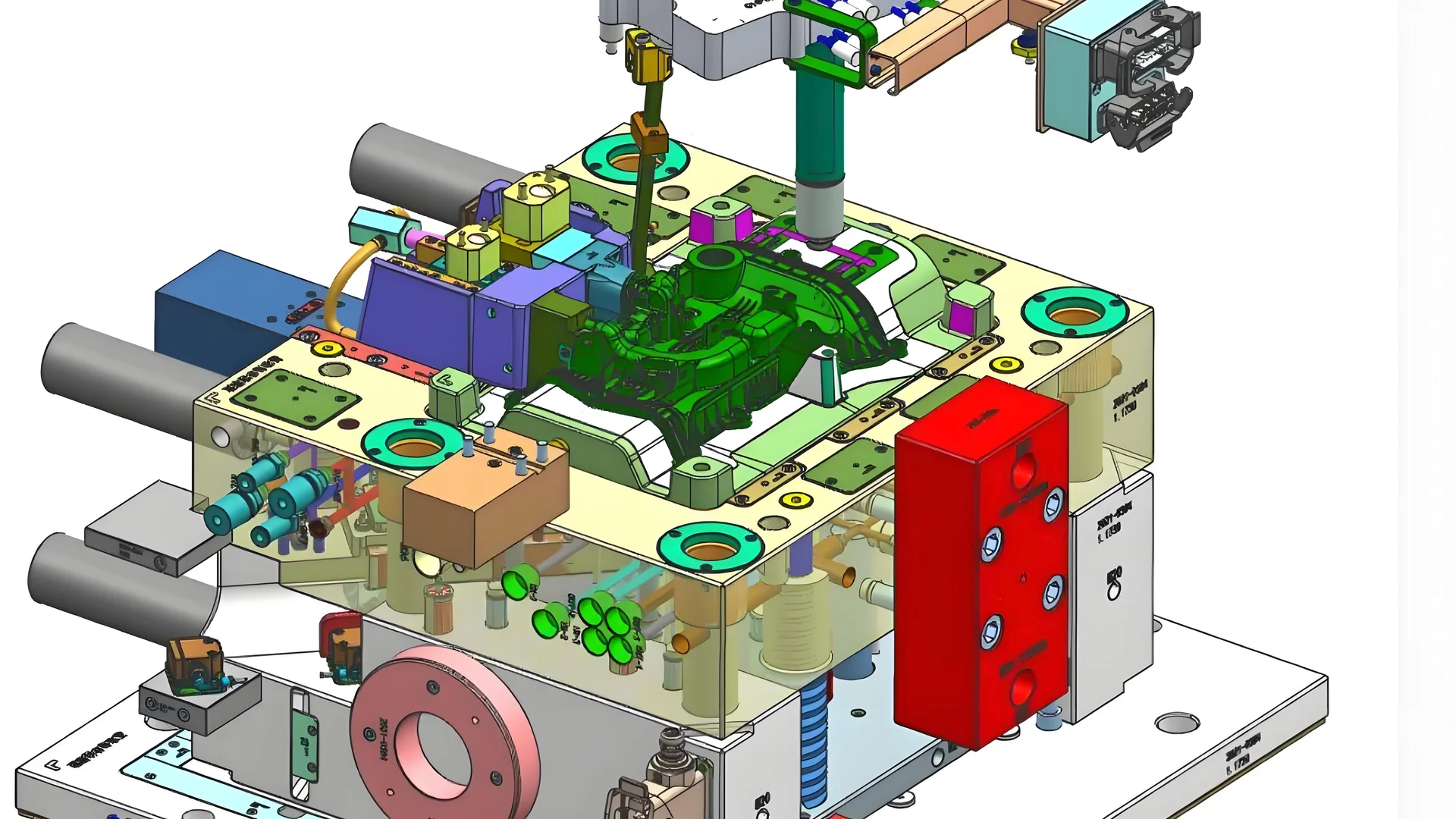
The Importance of Structural Integrity
A well-designed mold3 ensures that the plastic flows evenly, preventing common issues such as stagnation and short shots. The structural design should accommodate the product’s specific requirements, enabling consistent quality across each unit.
-
Uniform Flow: By facilitating a smooth flow of material, the mold minimizes defects like weld lines and voids. Uniform flow also reduces internal stresses, which can compromise product strength.
-
Gate Design: Proper gate placement and sizing are crucial for filling the mold cavity efficiently. A strategically designed gate optimizes material distribution, directly affecting the product’s mechanical properties.
Enhancing Aesthetic Precision
Product appearance is equally crucial, especially for consumer-facing items. Mold design significantly impacts surface finish and color consistency.
-
Surface Finish: The mold’s surface texture translates directly onto the product. A polished mold surface yields a smoother finish, enhancing the product’s appeal.
-
Color Consistency: A well-engineered mold can aid in maintaining consistent color across batches by ensuring even temperature distribution and material flow.
Cooling System Efficiency
Efficient cooling is vital for maintaining production speed without sacrificing quality. A mold’s cooling system should be tailored to the product’s dimensions and material.
-
Cooling Channels: Strategically placed cooling channels ensure even cooling, preventing warping and dimensional inaccuracies.
-
Material Selection for Molds: Using materials with high thermal conductivity for the mold can expedite cooling, further boosting production efficiency.
The Role of Maintenance in Mold Longevity
Regular mold maintenance4 is essential to uphold quality standards and prolong mold life. This involves cleaning to remove residues that can affect surface quality, as well as inspecting for wear and tear.
-
Routine Checks: Implementing a maintenance schedule helps identify issues before they escalate, ensuring consistent production quality.
-
Replacement of Worn Parts: Timely replacement of worn components prevents defects and maintains the integrity of the mold design.
By focusing on these critical aspects of mold design and maintenance, manufacturers can significantly enhance both the efficiency of their processes and the quality of their products.
Mold design affects product's structural integrity.True
Proper mold design ensures even material flow, reducing defects.
Gate placement has no effect on product quality.False
Incorrect gate placement can lead to poor material distribution.
Why Is Precise Parameter Adjustment Crucial for Injection Molding?
In injection molding, even minor parameter tweaks can drastically alter the final product’s quality. Precision is key.
Precise parameter adjustment in injection molding ensures dimensional accuracy, surface quality, and production efficiency, reducing defects like warping and flash.
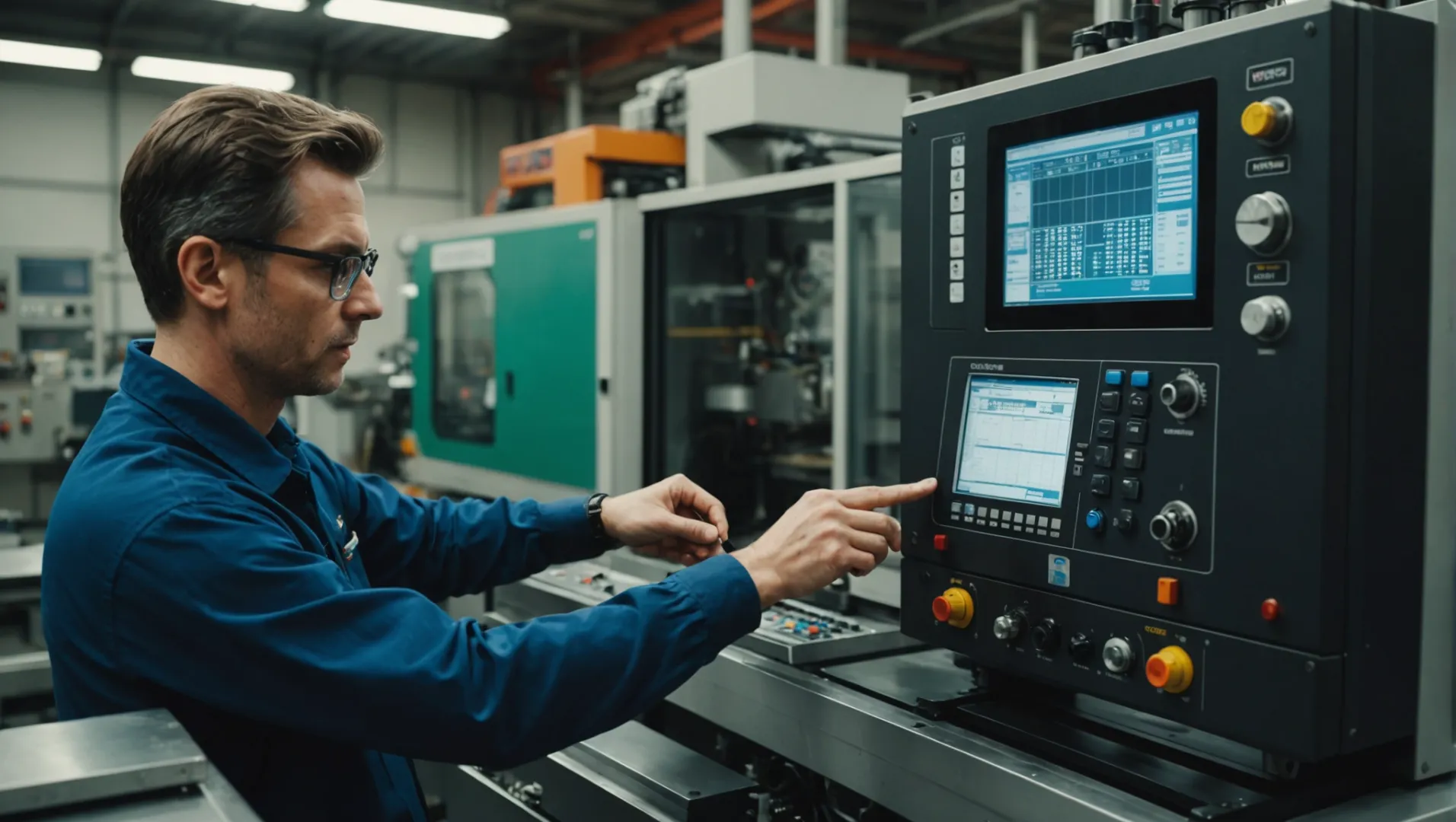
Understanding the Role of Injection Parameters
Injection molding, a staple in manufacturing, relies heavily on parameter adjustment5 to ensure product quality and efficiency. Parameters like injection pressure, speed, holding pressure, and temperature dictate how material flows into molds, affecting everything from structural integrity to aesthetics.
-
Injection Pressure and Speed: Higher injection pressures and speeds can enhance fluidity but risk issues like flash or warping. Tailoring these to the product’s shape and material characteristics is crucial for optimal results.
-
Holding Pressure and Time: These settings are pivotal for maintaining the product’s dimensional stability. Proper holding pressure compensates for shrinkage during cooling, while the right holding time prevents internal stress buildup.
The Impact of Temperature Control
Temperature variations across the machine—whether in the barrel, nozzle, or mold—play a crucial role in material behavior. Each plastic type requires specific temperature ranges to maintain flow and form.
- Barrel Temperature: This should exceed the plastic’s melting point for optimal flow.
- Nozzle Temperature: Slightly higher than the barrel to prevent premature solidification.
- Mold Temperature: Tailored to product requirements to aid efficient cooling and minimize defects.
Cooling Time Considerations
Cooling time directly influences both production speed and product quality. Insufficient cooling can lead to deformation post-demolding, whereas excessive cooling extends cycle times unnecessarily.
- Determining Cooling Time: Factors include product thickness and material thermal properties. Balancing these ensures efficient production without sacrificing quality.
Integrating Quality Control
Advanced quality control measures6 like online testing and sampling inspections are vital. They not only catch defects early but also inform necessary parameter adjustments.
- Online Testing: Real-time monitoring of size and appearance can preempt batch-wide defects.
- Sampling Inspection: Regular checks on dimensional accuracy and mechanical properties guide ongoing parameter refinements.
Through meticulous parameter adjustment, manufacturers can significantly enhance product quality and operational efficiency. Continual monitoring and adaptation are essential to stay ahead in this dynamic field.
Injection pressure affects product fluidity.True
Higher injection pressures enhance fluidity but can cause defects.
Mold temperature is irrelevant to cooling efficiency.False
Mold temperature must be tailored for efficient cooling and quality.
How Can Effective Quality Control Improve Production Outcomes?
Quality control in production isn’t just about meeting standards; it’s a strategic tool that significantly enhances product reliability and efficiency. Discover how implementing robust quality control practices can transform your production outcomes.
Effective quality control improves production outcomes by reducing defects, optimizing processes, and ensuring consistent product quality. It involves real-time monitoring, regular sampling, and comprehensive operator training to swiftly identify and rectify issues, thereby enhancing efficiency and customer satisfaction.
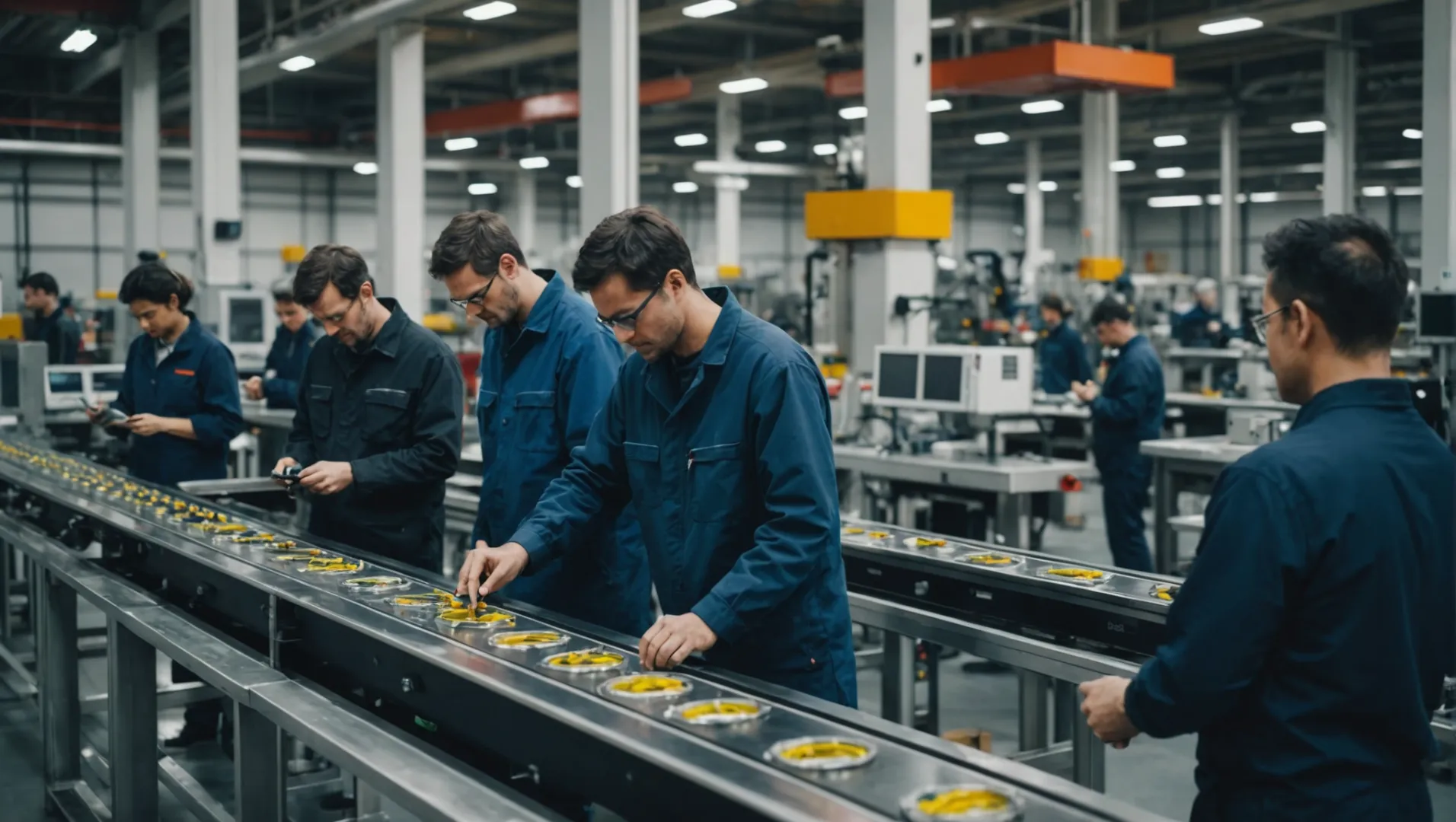
Real-Time Monitoring: Proactive Issue Detection
Utilizing advanced technology like sensors and cameras for online testing7 allows for real-time detection of defects or deviations during production. This proactive approach helps in immediate process adjustments, preventing defective batches from accumulating and ensuring consistent product quality.
Sampling Inspection: Ensuring Conformance
Regular sampling inspection involves selecting random samples from production runs to evaluate their conformance with desired specifications. This method aids in verifying whether products meet dimensional accuracy, mechanical properties, and appearance standards. Analyzing these results helps in identifying root causes of recurring issues, leading to targeted improvements.
Operator Training: Enhancing Human Capital
Quality control is heavily reliant on the expertise of the operators. Comprehensive training programs are essential to familiarize operators with the nuances of injection molding processes, including equipment operation, mold setup, parameter adjustments, and quality assurance techniques. Well-trained personnel can swiftly identify potential issues and make informed adjustments, thereby minimizing downtime and waste.
Integrated Quality Management Systems
Implementing a cohesive quality management system (QMS) helps in standardizing production processes, ensuring all steps from raw material procurement to final product inspection adhere to predefined quality standards. A robust QMS facilitates traceability, making it easier to pinpoint when and where errors occur.
Case Study: Achieving Excellence Through Quality Control
Consider a manufacturer who integrated an advanced QMS with real-time monitoring8. They observed a 30% reduction in defective products within six months. This improvement was attributed to immediate feedback loops that allowed for quick parameter adjustments and enhanced operator responsiveness. The end result was not only better product quality but also increased customer satisfaction and reduced operational costs.
By embracing a comprehensive approach to quality control, companies can not only meet but exceed production goals, turning quality assurance into a competitive advantage.
Real-time monitoring reduces defective products by 30%.True
A case study showed a 30% reduction in defects with real-time monitoring.
Operator training is unnecessary for quality control.False
Operator training is crucial for identifying issues and minimizing waste.
Conclusion
By mastering these optimization strategies, you can achieve remarkable enhancements in efficiency and product quality, paving the way for success in your injection molding endeavors.
-
Discover why material choice is critical for efficiency and quality.: Learn how to select the right material for your injection molding design with this technical overview of thermoplastic resins. ↩
-
Learn how polymers offer a cost-effective alternative to metals.: The plastic resin mixtures cost between $1 and $10 per pound, and glass fibers starts around $1 per lb compared to only $0.40/lb for steel. Thermoset materials … ↩
-
Explores how structural integrity impacts product quality.: The quality and make of the mold allows injection molders to ensure high tolerance, identify defects, maintain precision, choose the right raw materials, as … ↩
-
Provides tips on regular maintenance for prolonged mold lifespan.: An optimal cooling channel used: Proper cooling of the mold cavity is very important to prevent the mold cavities from warping and cracking. ↩
-
Understand how parameter tweaks affect molding outcomes directly.: By fine-tuning temperature, pressure, speed, and other key factors, you can achieve consistent, high-quality results while minimizing defects … ↩
-
Explore advanced methods for maintaining high product standards.: Tolerance level; Material heating zones; Cavity pressure; Injection time, speed, and rate; Overall production time; Product cooling time. ↩
-
Discover how real-time testing enhances product quality and process efficiency.: Furthermore, improved agility and shorter testing time can reduce lead times for quality control labs by 60 to 70 percent and eventually lead … ↩
-
Learn from real-world examples of successful quality control implementation.: We’ve compiled a collection of 101 case studies on Quality Management. Discover how various organizations are implementing quality initiatives. ↩