Have you ever felt frustrated with shrinkage in injection molded items? Many manufacturers experience this challenge. It affects the quality and size of the final product.
Optimize process settings, redesign molds, or use alternative materials to manage shrinkage in injection molded products, enhancing dimensional stability and minimizing defects effectively.
These first tips give a good beginning for controlling shrinkage. Exploring each method more closely could uncover additional techniques to improve your production line. This deeper look probably allows you to obtain great results from your manufacturing process.
Changing plastic materials reduces shrinkage in molded products.True
Using different plastics can affect shrinkage due to varying thermal properties.
Ignoring mold structure has no effect on shrinkage issues.False
Mold design impacts material flow and cooling, affecting shrinkage.
How Can You Reduce Shrinkage in Injection Molding?
Have you ever experienced the irritation when shrinkage in injection molding ruins your precise designs?
Reducing shrinkage in injection molding involves adjusting important settings. These include holding pressure, injection speed, melt temperature and mold temperature. Mold structure should be improved. Selecting low-shrinkage materials really helps product quality. This step is important.
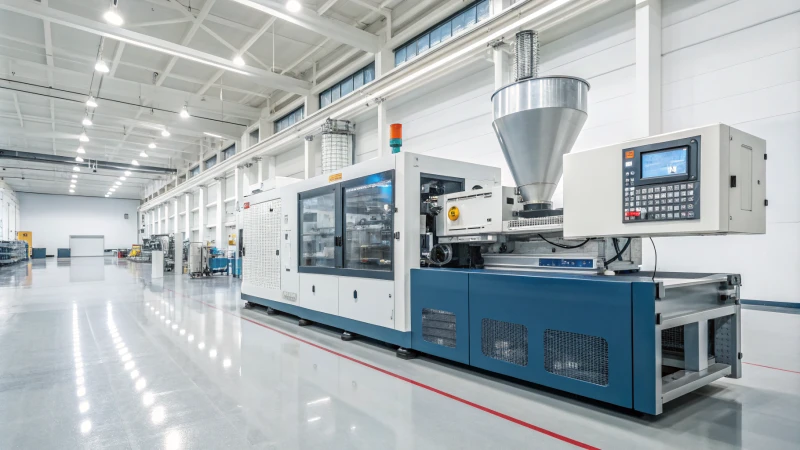
Adjust Injection Molding Process Settings
Increase Holding Pressure and Time
Early in my career, a batch of products shrank more than I expected. The holding pressure was too low. I increased it from 50% to about 60% of the injection pressure. Adding a few more seconds helped too. This small change greatly improved the product’s size. It was a minor adjustment but had a big impact.
Adjust Injection Speed and Melt Temperature
I thought faster injection was better until I learned it wasn’t. Slowing down helped the melt fill the cavity smoothly, reducing pressure differences and shrinkage. Raising the melt temperature1 a bit also helped, especially for crystalline plastics. Learning this balance took trial and error.
Optimize Mold Temperature
Mold temperature is important. If it’s too hot or too cold, it’s not good. For thin-walled designs, increasing the temperature from 30℃ to 40℃-50℃ really controlled shrinkage without reducing efficiency. It took experimenting to find the perfect spot where everything worked well.
Modify Mold Structure
Increase Gate Size or Number
I redesigned a mold for a difficult part by increasing the gate size from 0.8mm to about 1.2mm and adding more gates for larger sections improved flow dramatically, ensuring even distribution and reduced shrinkage.
Parameter | Initial Setting | Optimized Setting |
---|---|---|
Gate Diameter | 0.8mm | 1.2mm |
Optimize the Cooling System
Uneven cooling was a problem in my projects. I changed the cooling channel layout, bringing them closer in thick-walled sections. Conformal cooling technology2 helped a lot by keeping everything consistently cool and reducing inconsistencies.
Change Plastic Materials or Adjust the Formula
Choose Materials with Low Shrinkage
Switching materials was daunting but moving from polypropylene to polystyrene (PS) for some precise parts reduced shrinkage significantly. Sometimes, adjusting filler content or adding glass beads was transformative, turning shrinkage challenges into success.
With these changes and some experimentation, shrinkage was reduced significantly, improving product quality while bringing satisfaction in mastering the craft.
Increasing holding pressure reduces shrinkage.True
Higher holding pressure allows more plastic into the cavity, reducing shrinkage.
Lower mold temperature increases shrinkage.True
Lower mold temperatures speed up cooling, leading to increased shrinkage.
How Can Modifying Mold Structure Help Minimize Shrinkage?
Have you ever thought about how a tiny alteration in mold design might completely change your production line? Let’s explore the magic in reducing shrinkage.
By adjusting mold structures, like enlarging the gate size or refining the cooling system, shrinkage is reduced effectively. A more uniform pressure distribution and efficient cooling result. Products gain better accuracy and quality. Better accuracy is really important.
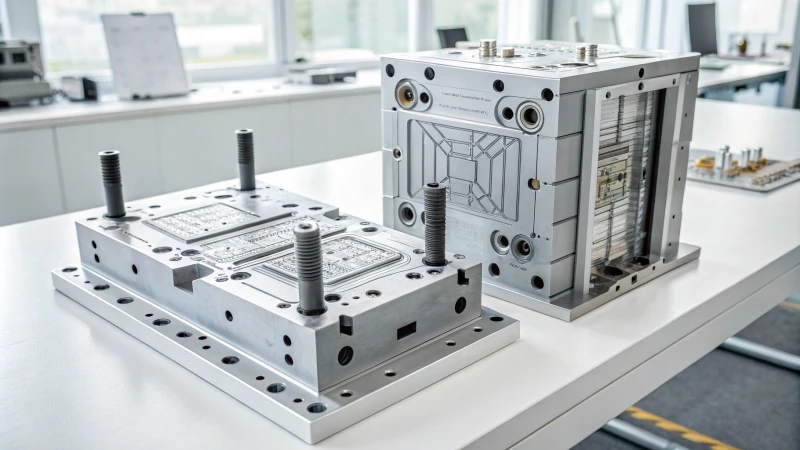
Simple Mold Structure Changes
I remember when I first experimented with mold structures. I spent many hours thinking about the gate sizes. Increasing the gate size or number changed everything. More plastic melt filled the cavity, compensating for shrinkage effectively3. This change fixed the shrinkage issues. It really worked.
Table: Gate Size Impact on Shrinkage
Gate Size (mm) | Effect on Shrinkage |
---|---|
0.8 | High |
1.0 – 1.2 | Reduced |
Optimizing the cooling system is important. During my trials, ensuring even cooling across the mold stopped uneven shrinkage, which can lead to defects. Utilizing conformal cooling technology helped a lot by aligning the cooling channels with the product shape and improving4 uniformity.
Cooling System Changes
Checking the cooling channels’ efficiency is key. For thick parts, more channel density reduces shrinkage differences. Channel diameters must allow enough cooling capacity; this is very important.
Designers should explore new conformal cooling technologies as these advancements are worth considering to explore more5.
Choosing Materials
Choosing materials with lower shrinkage rates is another option. Switching from polypropylene to polystyrene helped due to different properties, significantly reducing shrinkage rates effectively.
Modifying fillers in composite materials adjusted shrinkage rates well, which was an effective adjustment.
Understanding these changes with process parameters is crucial. Adjusting injection speeds, melt temperatures, and holding pressures improves mold changes and really helps in reducing shrinkage.
Increasing gate size reduces shrinkage.True
A larger gate allows more plastic melt, compensating for shrinkage.
Polypropylene has lower shrinkage than polystyrene.False
Polystyrene has lower shrinkage rates compared to polypropylene.
When is it Time to Change Plastic Materials to Tackle Shrinkage?
Shrinkage in plastic parts seems like an unseen problem haunting the production line. This issue can disrupt progress. Changing materials at the right time probably solves this problem.
Think about using different plastics if your current ones don’t meet size accuracy or shrink too much. Polystyrene might be a good choice. This material often shrinks less. It probably helps keep product quality stable.
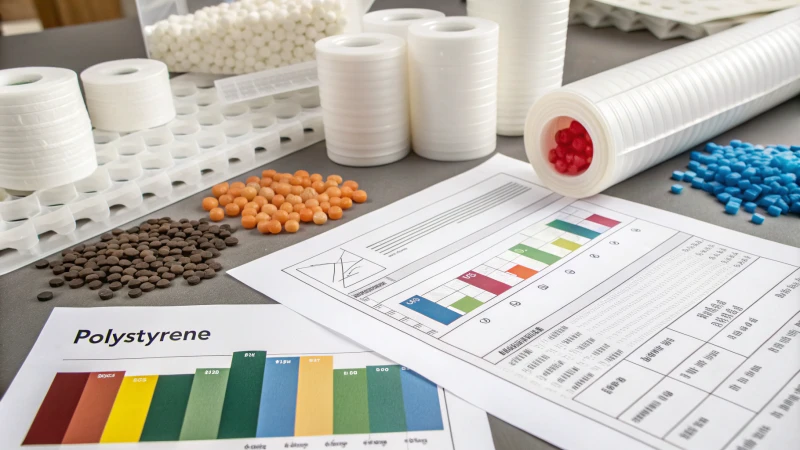
Understanding Material Shrinkage
Imagine watching a plastic part cool down. It seems to shrink like a balloon losing air. This happens because the material contracts during cooling, which might change your product’s final size.
Evaluating Material Properties
When your material performs poorly, it’s time to find another option. Think about using polypropylene (PP), which shrinks a lot. This feels like building a sandcastle with waves coming in. Using polystyrene (PS) could really help you.
Comparison Table: Common Plastics and Shrinkage Rates
Material | Typical Shrinkage (%) |
---|---|
Polypropylene (PP) | 1.5 – 2.0 |
Polystyrene (PS) | 0.4 – 0.7 |
Polyethylene (PE) | 1.5 – 3.0 |
Adjusting Formulations
At the beginning of my work with composites, I noticed a crucial insight: changing filler content really reduces shrinkage problems. Try using fewer organic fibers or adding some glass beads.
Process Optimization
Optimizing injection molding settings6 is very useful before changing materials. Adjusting the holding pressure, injection speed, or mold temperature might solve shrinkage problems without needing to change materials.
Material-Specific Considerations
Not all plastics act the same with heat and pressure:
- For crystalline plastics, adjusting melt temperature was crucial for even crystallization.
- For amorphous plastics, keeping cooling rates steady is very important.
The Role of Mold Design
Look at your mold design before choosing new materials. A small change, like making the gate size larger or optimizing cooling channels, might fix shrinkage problems and avoid the need for a full material change.
Considering these factors helps you decide when to change a material and which alternative really tackles shrinkage best in your production process7. Remember, each adjustment helps improve your work.
Polypropylene has higher shrinkage than polystyrene.True
Polypropylene's shrinkage rate is 1.5-2.0%, while polystyrene's is 0.4-0.7%.
Changing mold design can't reduce shrinkage issues.False
Modifying mold design, like gate size, can resolve shrinkage problems.
How Does Cooling System Optimization Help Manage Shrinkage?
Did you ever feel that a tiny detail might completely change a project’s result? That’s my exact thought about cooling systems in injection molding. Cooling systems play a crucial role.
Optimizing the cooling system in injection molding is important for managing shrinkage effectively. Uniform cooling is essential. Manufacturers adjust the layout and density of channels. These adjustments probably help in reducing different levels of shrinkage. High-quality, defect-free products result from this process.
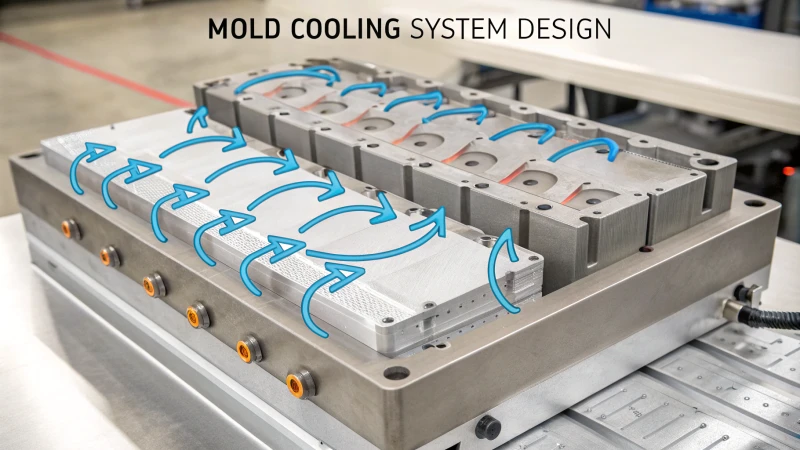
Understanding Cooling System Optimization
When I first started learning about injection molding, I quickly realized that cooling system optimization really changes how we handle shrinkage. Molded parts cool and shrink, and this shrinkage creates size errors, which nobody wants. The role of the cooling system is to make this shrinking happen evenly.
Key Aspects of Cooling System Optimization:
-
Uniform Temperature Distribution:
Imagine those moments when you want everything perfect. That’s this task. Ensuring an even temperature across the mold prevents different shrinkage in different spots. Cooling channels8 must cover every important part of the mold. -
Channel Density and Layout:
It’s like arranging furniture in a room for best comfort. For thick parts, adding more channels speeds cooling, reducing shrinkage differences. But be careful – not too many channels in thinner areas.Factors Thin-Walled Products Thick-Walled Products Mold Temperature Higher Moderate Channel Density Lower Higher -
Conformal Cooling Technology:
This modern approach is like tailoring a suit to fit perfectly. It matches cooling channels to the product’s shape, reducing cycle time and improving evenness. By using conformal cooling9, manufacturers can significantly reduce shrinkage-related defects.
Practical Adjustments
To use cooling optimization effectively, adjusting process settings is vital:
-
Injection Speed and Melt Temperature:
Adjusting these is like perfecting a recipe. Too much or too little ruins balance. Proper adjustments help fill the cavity smoothly, reducing shrinkage. Balancing this without high melt temperature is very important. -
Holding Pressure and Time:
Increasing these lets more melt fill the cavity, compensating for volume shrinkage during cooling—like watering a plant just right. Gradual changes based on the product are probably best.
For more insights, exploring injection speed effects10 and melt temperature control11 could be helpful. By optimizing these elements, we find a balance between fast production and high quality, tackling shrinkage directly.
Uniform cooling reduces shrinkage variance.True
Even temperature distribution minimizes local shrinkage differences.
Conformal cooling increases cycle time.False
Conformal cooling reduces cycle time by enhancing uniformity.
Conclusion
Effective management of shrinkage in injection molded products involves adjusting process parameters, optimizing mold design, and selecting low-shrinkage materials to enhance product quality and accuracy.
-
Adjusting melt temperature ensures even crystallization, reducing shrinkage and enhancing product quality. ↩
-
Conformal cooling improves cooling uniformity, reducing shrinkage inconsistencies in molded products. ↩
-
Learn how varying gate sizes affect pressure distribution and minimize shrinkage in molded products. ↩
-
Discover how conformal cooling enhances uniformity and reduces shrinkage in injection molding. ↩
-
Find cutting-edge cooling methods that optimize mold performance and reduce defects. ↩
-
Learn detailed methods to optimize injection molding parameters, which may reduce the need for changing materials. ↩
-
Discover strategies for enhancing production processes that can mitigate shrinkage without changing materials. ↩
-
Learn how to design effective cooling channels to ensure even temperature distribution in molds. ↩
-
Discover how conformal cooling technology reduces cycle time and improves cooling uniformity. ↩
-
Understand how adjusting injection speed can minimize shrinkage in molded products. ↩
-
Explore how controlling melt temperature influences product quality and shrinkage. ↩