Injection molding is a widely used manufacturing process for creating plastic parts, but when it comes to materials like glass-filled nylon, there are unique considerations and benefits. Glass-filled nylon, a type of nylon reinforced with glass fibers, offers enhanced strength, rigidity, and heat resistance1, making it ideal for demanding applications. But is injection molding2 possible with this material? The answer is yes, and in this article, we’ll explore everything you need to know about the process, from its basic principles to its practical applications and technical challenges.
Overview
Injection molding with glass-filled nylon3 is a proven method for creating strong, heat-resistant parts used in demanding applications. This guide explores the process, its applications, and key considerations for successful implementation.
- 1. Is Injection Molding Possible with Glass-Filled Nylon?
- 2. What is Glass-Filled Nylon?
- 3. What are the Benefits of Using Glass-Filled Nylon in Injection Molding?
- 4. What are the Typical Applications of Glass-Filled Nylon Parts?
- 5. How Does the Injection Molding Process Work with Glass-Filled Nylon?
- 6. What are the Challenges and Considerations in Molding Glass-Filled Nylon?
- 7. How to Design Parts for Injection Molding with Glass-Filled Nylon?
- 8. When Should You Choose Injection Molding with Glass-Filled Nylon?
- 9. What are Related Technologies and Materials?
- 10. Conclusion
Is Injection Molding Possible with Glass-Filled Nylon?
Yes, injection molding is not only possible but also widely practiced with glass-filled nylon. This process involves injecting molten nylon, reinforced with glass fibers, into a mold to create parts with superior mechanical properties. The addition of glass fibers, typically ranging from 15% to 40% by weight, significantly enhances the strength, stiffness, and thermal stability of the nylon, making it suitable for high-performance applications (FOW Mould).
Injection molding with glass-filled nylon is possible.True
The process is widely used in various industries for producing high-strength parts.
What is Glass-Filled Nylon?
Glass-filled nylon is a composite material where nylon (polyamide) is reinforced with short glass fibers. These fibers improve the material’s tensile strength, rigidity, and dimensional stability, while also increasing its resistance to heat and chemicals. Common variants include glass-filled nylon 6 (PA6) and nylon 66 (PA66), each offering slightly different properties based on the nylon type and glass fiber content (Protolabs).

Key Properties:
-
Tensile Strength: 170–230 MPa (vs. 60–80 MPa for unfilled nylon).
-
Heat Deflection Temperature: Up to 250°C–280°C.
-
Modulus of Elasticity: 7,000–10,000 MPa.
-
Shrinkage: Anisotropic, typically 0.03% in flow direction and 1.9% in cross-flow direction (Fictiv).
What are the Benefits of Using Glass-Filled Nylon in Injection Molding?
The addition of glass fibers to nylon provides several advantages, making it a preferred choice for parts that must endure mechanical stress, high temperatures, or harsh environments.

Benefits:
-
Enhanced Strength4: Up to 70% stronger than unfilled nylon, with tensile strength close to some metals.
-
Improved Heat Resistance5: Performs well in high-temperature environments (up to 280°C).
-
Dimensional Stability: Lower thermal expansion and moisture absorption.
-
Wear Resistance6: Ideal for parts subject to friction or impact.
-
Lightweight: High strength-to-weight ratio, a cost-effective alternative to metals.
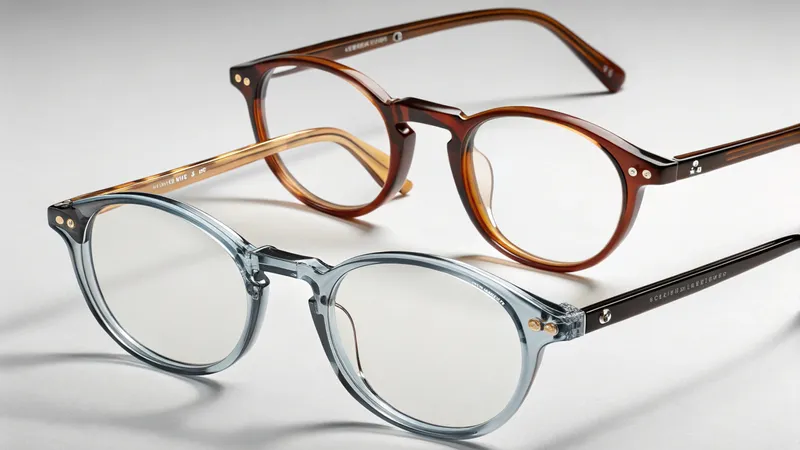
Trade-offs:
-
Abrasiveness: Wears down molds and machinery, increasing maintenance costs.
-
Surface Finish: Rougher due to visible glass fibers.
-
Brittleness: More prone to fracturing under high stress.
Property | Glass-Filled Nylon | Unfilled Nylon | Metal (e.g., Aluminum) |
---|---|---|---|
Strength | High | Moderate | Very High |
Heat Resistance | Excellent | Good | Excellent |
Cost | Higher | Lower | High |
Weight | Light | Light | Heavy |
Flexibility | Less Flexible | More Flexible | Rigid |
Glass-filled nylon is less expensive than unfilled nylon.False
The addition of glass fibers and the need for specialized equipment make it more costly.
What are the Typical Applications of Glass-Filled Nylon Parts?
Glass-filled nylon is used across various industries for parts requiring durability, heat resistance, and mechanical strength.
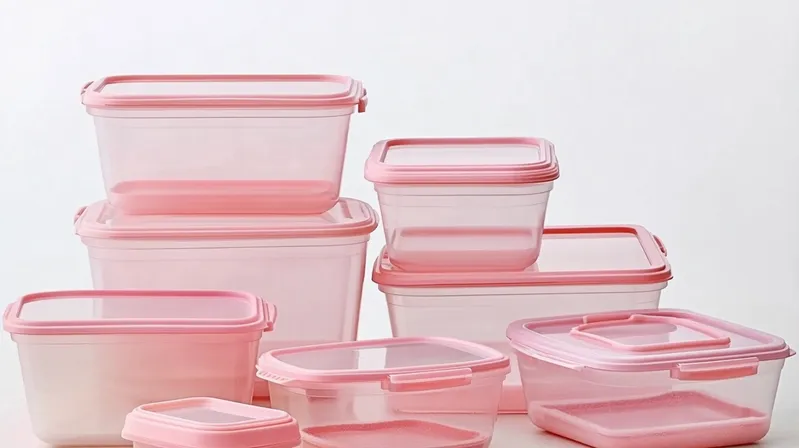
Applications:
-
Automotive: Gears, bearings, engine components, and under-hood parts.
-
Electrical: Connectors, insulators, and housings for electronics.
-
Consumer Goods: Power tool components, sporting equipment, and appliances.
-
Industrial: Pumps, valves, and wear strips in machinery.
These applications leverage the material’s ability to withstand harsh conditions while maintaining dimensional accuracy (PMC Plastics).
How Does the Injection Molding Process Work with Glass-Filled Nylon?
The injection molding process for glass-filled nylon7 involves several critical steps, each requiring precise control to ensure part quality.
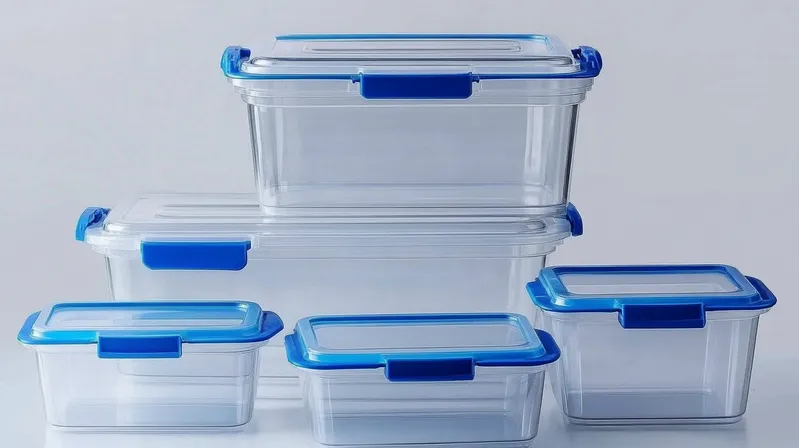
Process Steps:
-
Material Preparation: Pellets are dried to remove moisture (nylon is hygroscopic, absorbing 1.2%–2.5% water).
-
Melting and Injection: Melted at 260°C–280°C and injected at 100–150 MPa.
-
Cooling: Cooled in the mold, managing anisotropic shrinkage.
-
Ejection: Part is ejected, avoiding damage due to brittleness.
Key Parameters:
-
Melt Temperature8: 260°C–280°C.
-
Mold Temperature: 80°C–120°C.
-
Injection Speed9: Optimized to reduce defects like "floating fibers."
Molds must be made from wear-resistant materials like hardened steel (VEM Tooling).
Glass-filled nylon requires special molds due to its abrasiveness.True
The glass fibers can cause significant wear on standard molds, necessitating hardened materials.
What are the Challenges and Considerations in Molding Glass-Filled Nylon?
Glass-filled nylon presents unique challenges that must be addressed during molding.
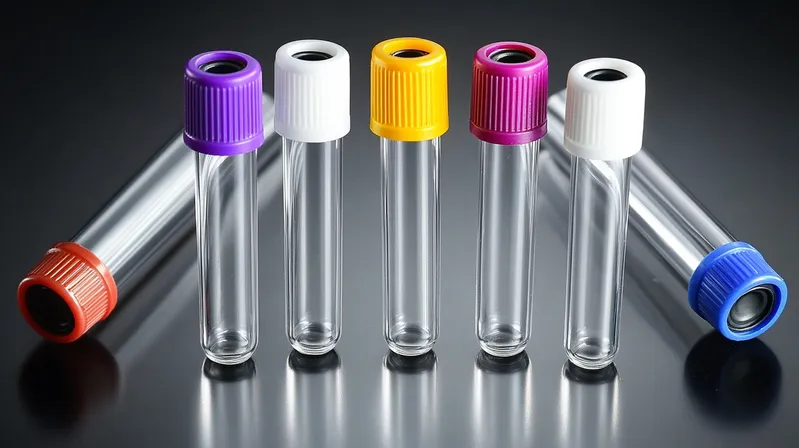
Challenges:
-
Abrasiveness10: Reduces mold life by 30–50%.
-
Surface Finish11: Visible fibers limit aesthetic applications.
-
Anisotropic Shrinkage: Varies by flow direction, requiring precise mold design.
-
Moisture Sensitivity12: Requires thorough drying to avoid defects.
Solutions:
-
Use wear-resistant molds.
-
Optimize injection parameters.
-
Design with fiber orientation in mind.
How to Design Parts for Injection Molding with Glass-Filled Nylon?
Designing for glass-filled nylon requires specific guidelines to ensure manufacturability and performance.
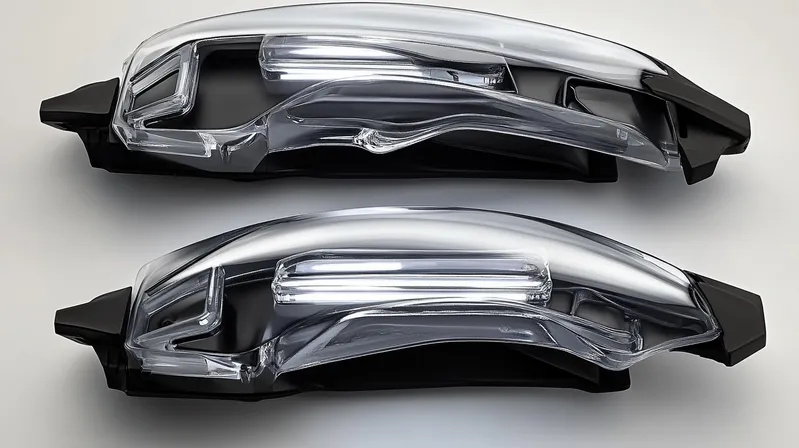
Design Checklist:
-
Wall Thickness: Uniform, minimum 3.175 mm to prevent warping.
-
Radii: ≥50% of wall thickness to reduce stress.
-
Draft Angle: 0.5%–1% for ejection.
-
Shrinkage: Account for 0.03% (flow) and 1.9% (cross-flow).
-
Gates: Large enough for filling, minimal visible marks.
Uniform wall thickness is crucial for glass-filled nylon parts.True
It prevents warping and ensures even cooling during the molding process.
When Should You Choose Injection Molding with Glass-Filled Nylon?
Choose When:
-
High strength and heat resistance are needed.
-
Weight reduction is key, but metal is impractical.
-
High-volume production is required.
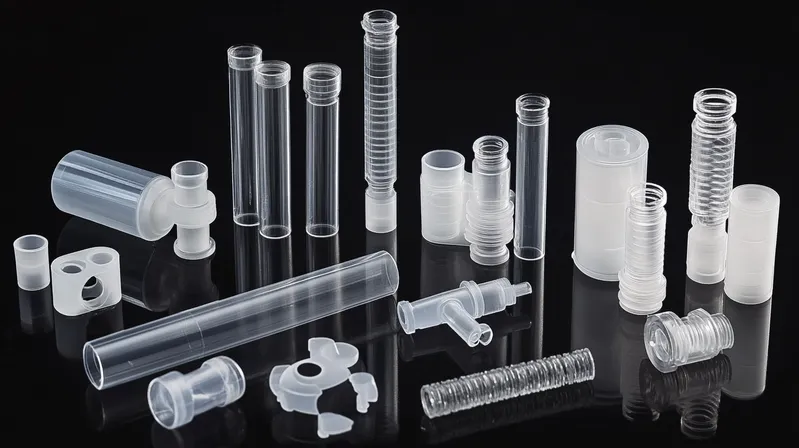
Alternatives When:
-
Smooth finishes are critical.
-
Cost is a priority.
-
Enhanced properties aren’t necessary.
Options include unfilled nylon or ABS for less demanding applications.
Related Materials:
-
Carbon-Filled Nylon: Higher strength, more expensive.
-
Mineral-Filled Nylon: Better stability, less strength.

Alternative Processes:
-
Compression Molding: For simpler shapes.
-
3D Printing: For prototypes, lower strength.
Conclusion
Injection molding with glass-filled nylon is a powerful technique for producing high-performance parts. While it offers significant benefits like enhanced strength and heat resistance, it requires careful design and process control due to challenges like abrasiveness and shrinkage. By understanding its applications and requirements, manufacturers can leverage this technology effectively.
-
Discover materials with superior heat resistance to enhance your manufacturing processes and product durability. ↩
-
Learn about the injection molding process to grasp how it creates durable plastic parts efficiently. ↩
-
Explore the advantages of glass-filled nylon in injection molding to understand its unique properties and applications. ↩
-
Explore how Enhanced Strength in glass-filled nylon can significantly improve performance in demanding applications. ↩
-
Learn about the superior heat resistance of glass-filled nylon and its applications in high-temperature environments. ↩
-
Discover why wear resistance is a crucial factor for choosing glass-filled nylon in parts subject to friction and impact. ↩
-
Explore the advantages of glass-filled nylon, including its strength and durability, which are crucial for high-quality molded parts. ↩
-
Understanding melt temperature is vital for optimizing the injection molding process and ensuring part quality. ↩
-
Learn how injection speed impacts defect rates and overall part quality in the injection molding process. ↩
-
Understanding the impact of abrasiveness can help in selecting the right materials and processes to enhance mold durability. ↩
-
Exploring this topic can provide insights into improving aesthetic quality in manufacturing glass-filled nylon items. ↩
-
Learning about moisture sensitivity can help ensure high-quality production and reduce defects in glass-filled nylon components. ↩