Injection molding and compression molding are two widely used manufacturing processes1 for producing plastic parts, each with its own strengths and ideal applications. Understanding the key differences between them is crucial for selecting the right method for your project.
Injection molding2 injects molten plastic into a closed mold under high pressure, creating precise, complex parts quickly, ideal for high-volume production. Compression molding places pre-measured material into an open mold, then closes and heats it, suitable for simpler, larger parts or specific materials like thermosets.
Knowing when to use each process can save costs and ensure product quality. Injection molding excels in efficiency and precision, while compression molding3 is cost-effective for certain materials and production scales.
Injection molding is only for small, intricate parts.False
While ideal for complex parts, injection molding can also produce larger components, though it may be less cost-effective for very large or simple shapes.
Compression molding is always cheaper than injection molding.False
Compression molding has lower tooling costs, making it cheaper for small production runs, but injection molding is more cost-effective for large volumes due to faster cycle times.
- 1. What are the Common Materials Used in Injection Molding and Compression Molding?
- 2. What are the Steps in the Injection Molding and Compression Molding Processes?
- 3. What are the Key Factors Influencing Injection Molding and Compression Molding?
- 4. What are the Applications of Injection Molding and Compression Molding?
- 5. What are the Differences Between Injection Molding and Compression Molding?
- 6. Conclusion
What are the Common Materials Used in Injection Molding and Compression Molding?
Material selection is pivotal in determining the success of the molding process, as each method is suited to different types of plastics and composites.

Injection molding primarily uses thermoplastics like Nylon, Polypropylene, and PEEK, while compression molding is ideal for thermosets such as Epoxy and Phenolic resins, rubber, and composites.
Molding Process | Common Materials | Notes |
---|---|---|
Injection Molding | Thermoplastics (e.g., Nylon, PEEK, ABS) | Best for materials that flow well under pressure. |
Compression Molding | Thermosets (e.g., Epoxy, Phenolic), rubber, composites | Suitable for materials requiring curing under heat and pressure. |
Thermoplastics in Injection Molding
Thermoplastics are the go-to materials for injection molding due to their ability to melt and flow into intricate mold cavities. Common examples include:
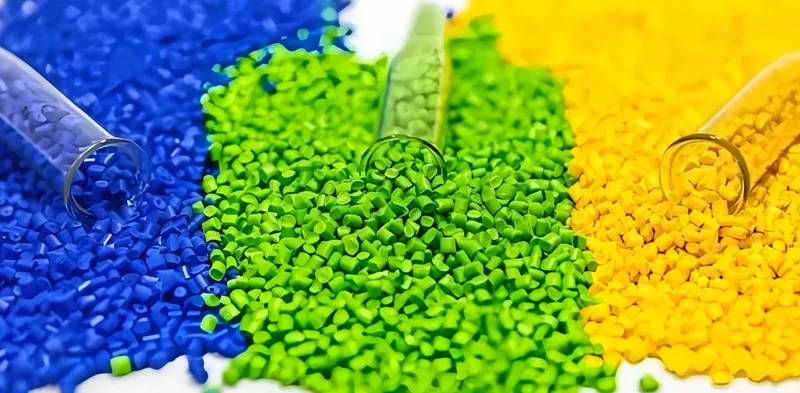
-
Nylon: Used for its strength and durability in automotive and consumer goods.
-
Polypropylene: Popular for its chemical resistance and low cost, used in packaging and medical devices.
-
PEEK: A high-performance plastic for aerospace and medical implants due to its heat resistance.
Injection molding can also handle some thermosets and liquid silicone rubber (LSR), but specialized equipment is required.
Thermosets and Composites in Compression Molding
Compression molding excels with materials that require curing, such as:
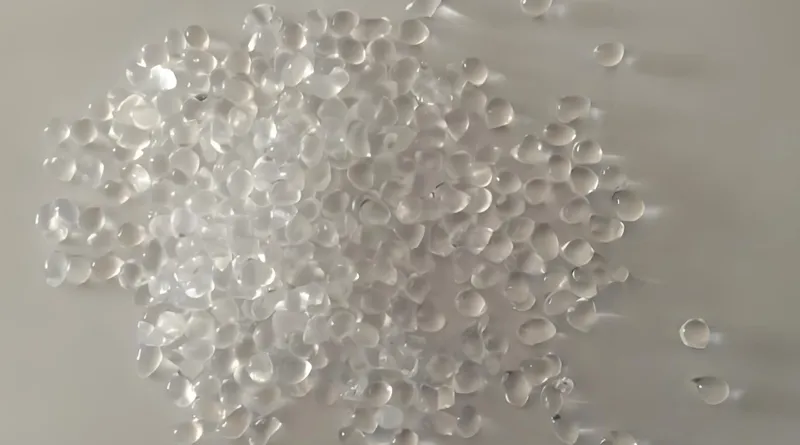
-
Epoxy Resins: Used in electrical insulators and aerospace components for their heat resistance.
-
Phenolic Resins: Ideal for high-temperature applications like circuit breakers.
-
Rubber and Composites: Common in gaskets, seals, and large panels due to their durability.
These materials are less suited for injection molding due to their viscosity and curing requirements.
Injection molding can only process thermoplastics.False
While primarily used for thermoplastics, injection molding can also process some thermosets and silicone rubber with specialized equipment.
Compression molding is limited to simple shapes.True
Compression molding is best for simpler, larger parts, as complex geometries can be challenging due to the open mold process.
What are the Steps in the Injection Molding and Compression Molding Processes?
Understanding the step-by-step workflows of each process is key to appreciating their differences and applications.
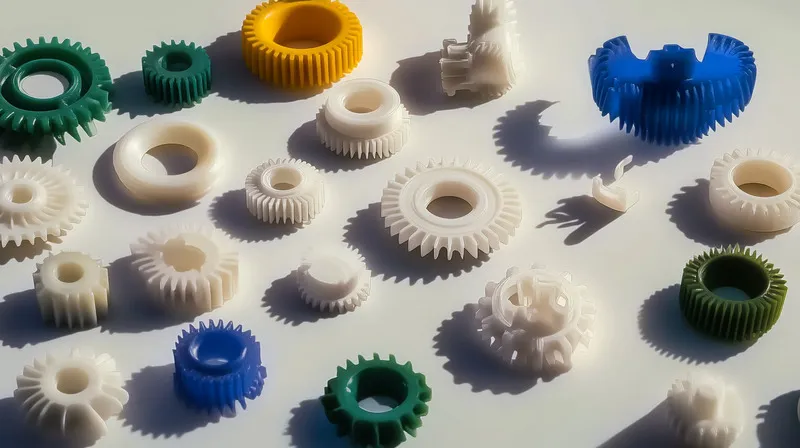
Injection Molding Process
-
Material Preparation: Thermoplastic pellets are fed into a hopper and melted in a heated barrel.
-
Injection: Molten material is injected into a closed mold under high pressure (typically 30,000–40,000 psi).
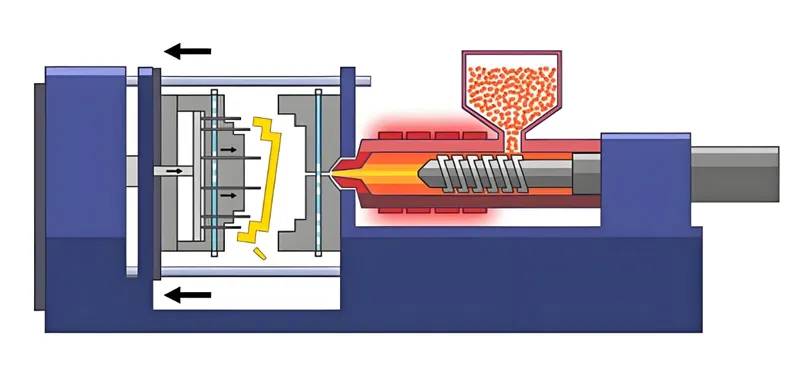
-
Clamping: The mold is clamped to withstand the injection forces.
-
Cooling: The material cools and solidifies in the mold.
-
Ejection: The part is ejected using pins or sliders for complex geometries.
- Key Parameters: Injection pressure, mold temperature, cooling time, clamping force (Fictiv).
Compression Molding Process
-
Charging: A pre-measured amount of material is placed into an open mold cavity.
-
Closing: The mold is closed, applying pressure.
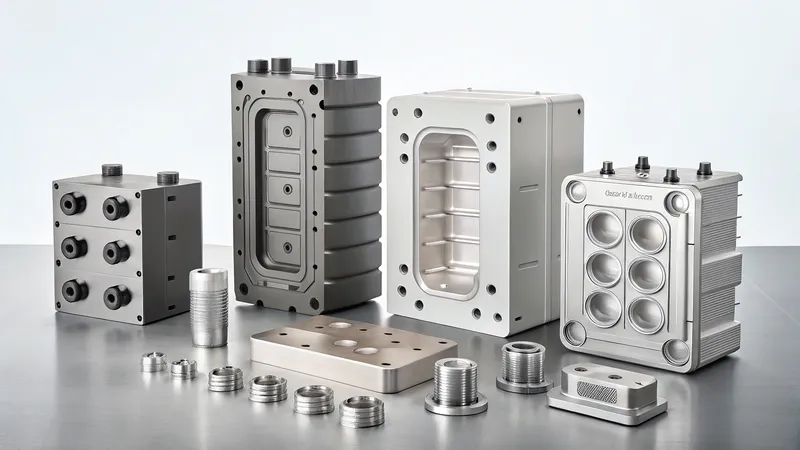
-
Heating and Curing: Heat cures the material under pressure.
-
Opening: The mold is opened, and the part is removed.
-
Post-Processing: Flash (excess material) is trimmed manually or via cryogenic deflashing.
- Key Parameters: Mold temperature, curing time, pressure.
Injection molding requires less manual intervention than compression molding.True
Injection molding is highly automated, while compression molding often involves manual steps like material placement and flash trimming.
Both processes can produce parts with the same level of precision.False
Injection molding generally offers higher precision due to the closed mold and high-pressure injection.
What are the Key Factors Influencing Injection Molding and Compression Molding?
Several critical parameters affect the quality and efficiency of each molding process.
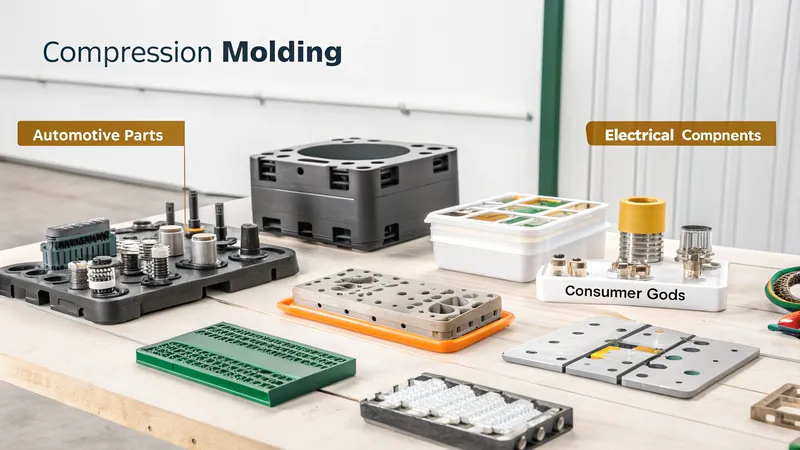
Injection Molding Factors
-
Injection Pressure4: Higher pressure ensures the material fills intricate mold details but requires stronger molds.
-
Mold Temperature5: Affects cooling time and part quality; too hot can cause warping.
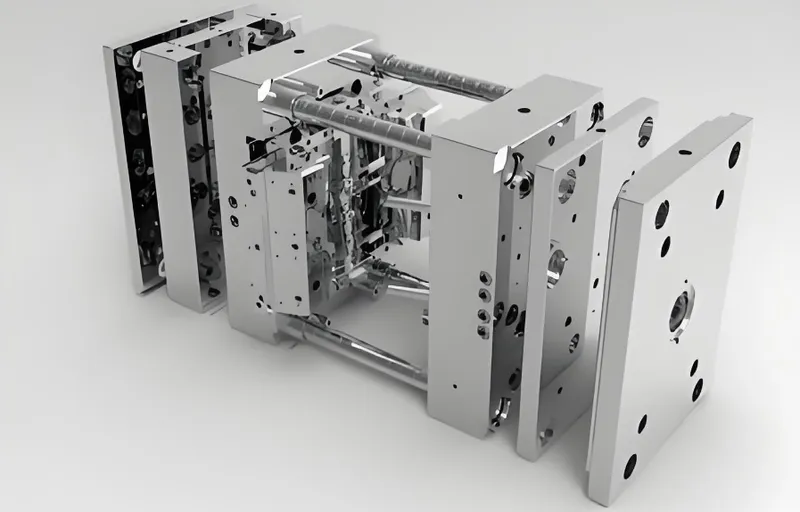
-
Cooling Time: Longer cooling ensures part stability but slows production.
-
Clamping Force: Must be sufficient to keep the mold closed during injection.
Compression Molding Factors
- Mold Temperature: Critical for curing thermosets; too low can lead to incomplete curing.
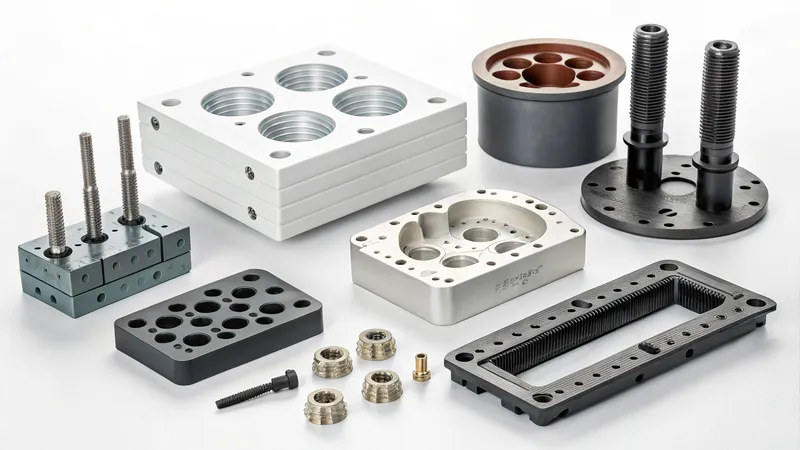
-
Curing Time6: Longer times ensure full curing but reduce production speed.
-
Pressure: Must be uniform to avoid defects like air pockets or incomplete filling.
Higher injection pressure always improves part quality in injection molding.False
Excessive pressure can cause mold damage or part defects like flash.
Compression molding requires precise temperature control for thermosets.True
Temperature directly affects the curing process, impacting part strength and durability.
What are the Applications of Injection Molding and Compression Molding?
Each molding process is suited to specific industries and product types based on their capabilities.

Injection Molding Applications
-
Industries: Automotive (dashboards, bumpers), medical (surgical tools), consumer goods (kitchenware), electronics.
-
Characteristics: High-volume production of complex, precise parts with fine details and thin walls (Reliant Plastics).
Compression Molding Applications
- Industries: Automotive (acoustic parts), aerospace, electrical (insulators), rubber products (gaskets).
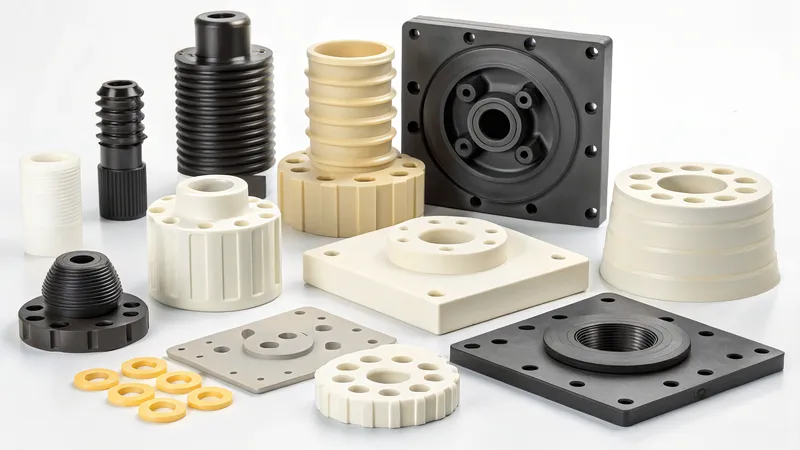
- Characteristics: Low-to-medium volume production of durable, simpler parts with uniform thickness, such as large panels or seals.
Injection molding is unsuitable for large parts.False
While typically used for smaller parts, injection molding can produce larger components, though it may be less efficient than compression molding.
Compression molding is ideal for high-volume production.False
Compression molding has slower cycle times, making it better for smaller production runs or specialized materials.
What are the Differences Between Injection Molding and Compression Molding?
A direct comparison highlights the strengths and limitations of each process.
Aspect | Injection Molding | Compression Molding |
---|---|---|
Tooling Cost | High (complex molds) | Lower (simpler molds) |
Production Volume | High (efficient for large runs) | Low to medium (slower cycle times) |
Part Complexity | High (intricate details, thin walls) | Low to medium (simpler shapes) |
Material Waste | Low (precise material use) | Higher (flash requires trimming) |
Cycle Time | Fast (seconds to minutes) | Slower (minutes per part) |
Material Compatibility | Thermoplastics, some thermosets | Thermosets, rubber, composites |
Advantages and Disadvantages
-
Injection Molding:
- Advantages: Rapid production, high precision, low waste, suitable for complex parts.
- Disadvantages: High tooling costs, less suitable for very large parts or thermosets.
-
Compression Molding:

- Advantages: Lower tooling costs, ideal for thermosets and large parts, cost-effective for small runs.
- Disadvantages: Slower production, higher waste, limited to simpler shapes.
Injection molding is always more expensive than compression molding.False
While tooling costs are higher, injection molding becomes more cost-effective for large production volumes due to faster cycle times.
Compression molding cannot produce parts with fine details.True
The open mold process limits the ability to achieve intricate details compared to injection molding.
Conclusion
Choosing between injection molding and compression molding depends on factors like part complexity, production volume, material type, and budget. Injection molding is ideal for high-volume, precise, and complex parts, especially with thermoplastics. Compression molding is better for simpler, larger parts or when using thermosets, rubber, or composites, particularly in smaller production runs.
Consider the following when deciding:
- For intricate, high-volume parts: Choose injection molding.
- For large, simple parts or thermosets: Opt for compression molding.
- For cost-sensitive, small runs: Compression molding may be more economical.
Understanding these differences ensures you select the most efficient and cost-effective process for your manufacturing needs.
-
Discover various manufacturing processes to make informed decisions for your project and understand their strengths and weaknesses. ↩
-
Explore the benefits of Injection molding to understand its efficiency and precision in producing complex plastic parts. ↩
-
Learn about the applications of compression molding to see how it can be cost-effective for larger parts and specific materials. ↩
-
Understanding injection pressure is crucial for optimizing mold design and ensuring product quality. Explore this link to learn more. ↩
-
Mold temperature plays a vital role in the curing and quality of molded parts. Discover insights on managing this parameter effectively. ↩
-
Curing time is essential for achieving the desired properties in molded products. Learn about its impact on production efficiency and quality. ↩