Moving through the world of mold acceptance feels like starting a trip toward flawlessness.
The standard steps in the injection mold acceptance process include mold inspection, trial runs, sample evaluation, quality testing, and final approval to ensure the mold meets design specifications and quality standards.
This overview offers the basics. Learning more shows each stage is crucial for shaping success. Picture each step as a puzzle piece. When finished, we get a perfect product ready for production. These procedures not only improve skills. They also create a strong base for making flawless molded parts.
Surface quality inspection is the first step.True
Surface quality inspection typically precedes other checks to ensure defects are absent.
Assembly precision verification comes before dimensional accuracy checks.False
Dimensional accuracy checks usually occur before verifying assembly precision.
- 1. How is Surface Quality Inspected in Mold Acceptance?
- 2. What Tools Are Used for Measuring Mold Size Accuracy?
- 3. How Do We Verify Precision in Mold Assembly?
- 4. What Performance Checks Are Conducted During Mold Acceptance?
- 5. Why are mold trials crucial before production?
- 6. How Can Mold Acceptance Impact Product Quality?
- 7. Conclusion
How is Surface Quality Inspected in Mold Acceptance?
Ever thought about what creates the perfect surface of molds? Discover the detailed process that delivers flawless products every time.
To inspect mold surface quality, focus on surface roughness. Look for defects like scratches or rust. Check for damage on parting surfaces. These steps help avoid defects in molded products. Molded products probably benefit from careful inspection.
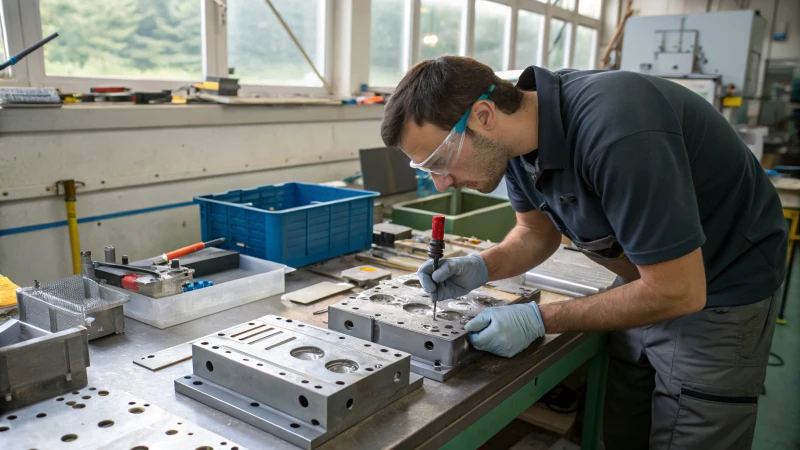
Surface Roughness Assessment
When I began working in the mold industry, I felt very surprised by the detailed work involved in checking molds. Surface quality is not just about looks; it’s about the strength and function of the final product. Every scratch or bump might cause big problems later, so paying close attention to details is necessary.
I remember my first time using a roughness meter1. It felt like a special moment. We used it to measure the roughness of the mold cavity and core, trying to reach a precision range between Ra0.2 to Ra0.8μm. Achieving this level of precision helps the molded parts look good and work perfectly. We always added a visual inspection to find any tiny scratches or defects that the meter might miss.
Parting Surface Inspection
The flatness of the parting surface is also really important. We used a knife edge gauge and a feeler gauge to check the flatness error, which should generally remain within 0.01 to 0.03mm for high-precision molds. This prevented problems such as loose mold closures or unwanted flash.
Rust and Corrosion Checks
I learned that rust is a sneaky enemy of molds, especially for those stored long-term or in humid places. Rust spots harm a mold’s accuracy and life; minor rust can be treated, but severe rust needs serious actions. Detailed guidelines on rust management are linked here2.
Visual Inspection for Defects
Checking visually for scratches, bumps, or pits on the mold surface is very important since even small imperfections can grow in the final product, leading to expensive defects.
Mold Identification Verification
Checking for correct and clear identification marks on molds is key for managing and tracing production. I always look for details like mold number, part number, and production date—this makes mold management3 more reliable and smooth.
Table: Tools Used in Surface Quality Inspection | Tool | Purpose | Precision |
---|---|---|---|
Roughness Meter | Measures surface texture | Ra0.2 – Ra0.8μm | |
Knife Edge Gauge | Checks parting surface flatness | 0.01 – 0.03mm | |
Feeler Gauge | Measures gaps | Highly precise |
All these methods together offer a complete inspection of mold surface quality, which is vital for maintaining top product manufacturing standards. It’s a precise dance between tools and careful eyes that I’ve grown to really appreciate in my career.
Surface roughness for molds is Ra0.2 to Ra0.8μm.True
This range ensures the final product's appearance and functionality meet expectations.
Mold parting surface error should be within 0.1mm.False
The correct flatness error range is 0.01 to 0.03mm for high-precision molds.
What Tools Are Used for Measuring Mold Size Accuracy?
Have you ever tried to put something together and discovered that the parts don’t fit? This is why accurate mold size measurement is necessary. Let’s explore the tools that help everything fit perfectly together.
Calipers, micrometers and Coordinate Measuring Machines (CMM) are important tools for checking mold size accuracy. They give very exact measurements of straight lengths and geometric limits. These measurements are crucial for producing high-quality molds.
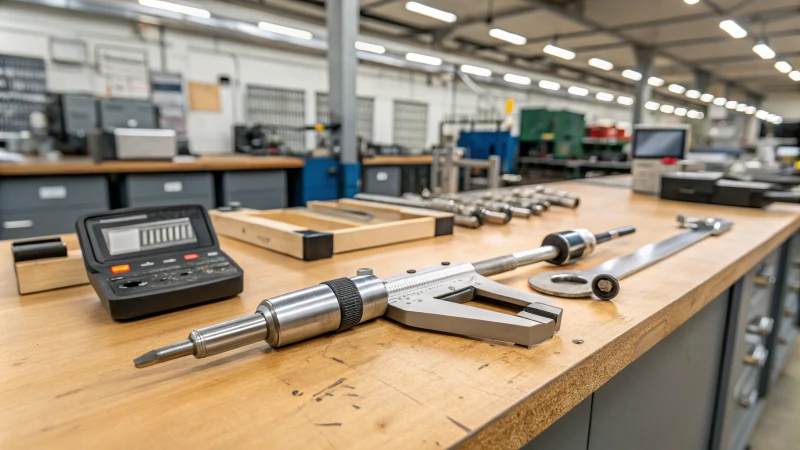
Essential Tools for Measuring Mold Size
-
Calipers and Micrometers
Calipers reminded me of a high-tech ruler. They gave quick readings. When I needed more detailed measurements, micrometers helped a lot. They offered extra precision for crucial design details. Micrometers were my best friends for fine measurements.
Tool Precision Best For Calipers ±0.02 mm Quick measurements Micrometers ±0.01 mm Fine details -
Coordinate Measuring Machine (CMM)
The CMM felt like magic. It collected 3D data from different mold surface points with great accuracy, ideal for high-precision requirements, capable of reaching micron-level accuracy.
-
Roughness Meter
Surface quality required a roughness meter, which was very important for precision injection molds4. Achieving the right surface texture between Ra0.2 – Ra0.8μm was essential to meet design specifications.
Techniques for Accurate Measurements
-
Geometric Tolerance Detection
Detecting geometric tolerances like roundness and cylindricity was crucial—it was like fitting puzzle pieces together accurately. Tools like roundness meters helped align everything properly.
-
Parting Surface Inspection
Knife edge gauges with feeler gauges checked flatness, maintaining a flatness error within 0.01 – 0.03mm is critical for high-precision molds.
-
Hole Spacing and Wall Thickness Measurement
Precision was very important here; exact cooling channel dimensions mattered significantly as they influenced the quality and efficiency of the final product.
Mold Appearance Acceptance
-
Surface Quality Inspection
Surface issues like scratches or rust were problematic; even tiny blemishes led to costly rejections, making thorough inspection necessary to avoid issues.
-
Mold Identification Inspection
Clear mold identification was important for traceability during production processes, serving as a very detailed roadmap.
These tools and techniques changed my work significantly by allowing my designs to reach high aesthetic and functional standards while controlling costs.
Calipers measure mold surface roughness.False
Calipers measure linear dimensions, not surface roughness.
CMM provides micron-level accuracy in measurements.True
CMMs capture precise 3D data, achieving micron-level accuracy.
How Do We Verify Precision in Mold Assembly?
Did you ever think about how each molded piece turns out perfect? Precision is the key.
Precision in mold assembly is verified through detailed surface checks, careful measurements and strict trials. These steps guarantee that molds consistently follow design standards. Meeting design standards is crucial for high-quality production. High-quality production is very important.
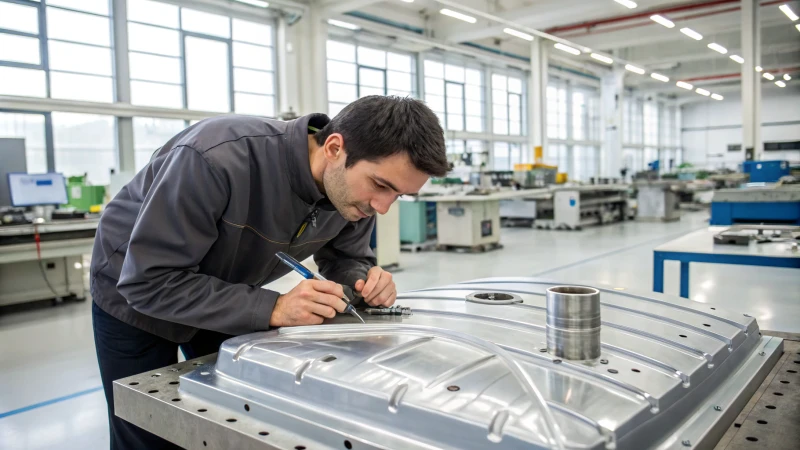
Surface Quality Inspection
Think of holding a shiny, polished gem. That is the detail we need for our molds. I remember my first project where I learned about surface roughness. Using a roughness meter, I checked important areas like the mold cavity and core. They needed to meet our design standards – usually between Ra0.2 and Ra0.8μm for precision injection molds5. Visual checks are really important too. Even a tiny scratch can cause problems later.
Linear Dimension Measurement
Accuracy cannot be guessed. Calipers and micrometers are my main tools for measuring dimensions such as length, width, and depth of the cavity. For very precise accuracy, the three-coordinate measuring machine (CMM) is invaluable. It measures feature points with micron-level precision, ensuring that cavity dimensions and cooling channels match the design specifications6.
Tool | Application | Accuracy Level |
---|---|---|
Calipers | Basic measurements | Millimeter |
Micrometers | Fine measurements | Micrometer |
CMM | High-precision tasks | Sub-micron |
Geometric Tolerance Detection
Checking geometric tolerances is crucial, even if it seems tedious. I learned this when a guide pin issue nearly ruined a project. Tools like roundness meters help find errors in cylindricity and flatness using instruments such as a flatness measuring instrument7. These checks ensure each part fits perfectly when the mold closes.
Mold Closing Accuracy Inspection
Mold closing accuracy is essential. I use feeler gauges to measure gaps, ideally under 0.03-0.05mm for high-precision molds. Misalignments or gaps are checked using feeler gauges or gap gauges to ensure proper mold closure8. Numbers are important, but watching manual operations also confirms smooth movement between guide pins and sleeves.
Ejector Mechanism Accuracy Inspection
I once faced a jamming ejector mechanism due to a small alignment issue that caused it to jam or skew during manual operations. Ensuring smooth movement of ejector pins is vital to avoid product deformation; their extension length must align with design specifications.
Mold Trial Acceptance
The trial phase brings everything together like a dress rehearsal for the final product before full-scale production begins. Watching this process helps find defects early, such as flash or short shots, so dimensions and quality meet expectations and adhere to design requirements.
Inspecting each aspect of mold assembly precision is essential to maintaining quality and meeting industry standards by incorporating these thorough inspections and measurements.
Surface roughness in molds should be Ra0.2 - Ra0.8μm.True
The specified range for surface roughness ensures precision and quality.
Calipers provide sub-micron level accuracy for measurements.False
Calipers offer millimeter-level accuracy, not sub-micron.
What Performance Checks Are Conducted During Mold Acceptance?
Ever wondered what prepares a mold for production? It’s like a symphony of checks and balances. Everything must work perfectly together.
During mold acceptance, we perform important checks. These include surface quality inspection. We also verify size accuracy. Assembly accuracy testing follows next. Then, we evaluate action performance. Finally, we conduct trial acceptance. Each step checks molds properly. It confirms they meet industry standards. High-quality production needs this process.
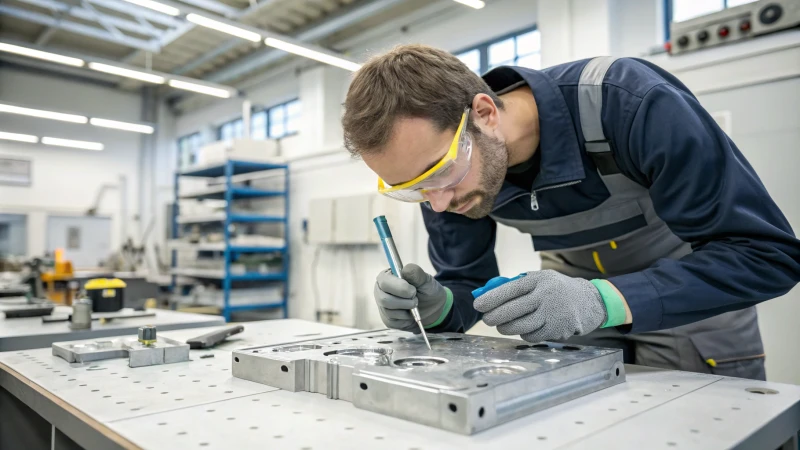
Surface Quality Inspection
I remember the first time I had to check a mold’s surface quality. Anxiety filled me as I tried not to miss even a small scratch. The surface quality inspection9 ensures that the mold’s appearance meets design specifications. Key factors include:
- Surface Roughness: Measured using a roughness meter. For precision molds, the cavity roughness typically ranges between Ra0.2 – Ra0.8μm.
- Rust Check: Rust is a major concern, especially if the mold sits in storage. Look for rust and address minor rust promptly to prevent dimensional inaccuracies.
- Parting Surface Inspection: Use a knife edge gauge and feeler gauge to measure flatness errors, usually kept within 0.01 – 0.03mm.
Size Accuracy Verification
Inspecting size accuracy feels like solving a puzzle. Size accuracy involves measuring the linear dimensions10 of the mold:
Measurement Tool | Purpose |
---|---|
Calipers & Micrometers | Measure basic dimensions like cavity depth |
CMM | High-precision dimensions |
Geometric Tolerances: Ensure aspects like cylindricity and flatness adhere to stringent standards to avoid production issues.
Assembly Accuracy Testing
Imagine putting together furniture from scratch. In assembly accuracy, focus on the mold closing11 accuracy:
- Mold Closing Gap: Should be minimal (less than 0.03-0.05mm) to prevent product flash.
- Guide Pin & Sleeve Fit: Smooth operation without jamming ensures long-term functionality.
- Ejector Mechanism Accuracy: Ejector pins should move smoothly without skewing to prevent product deformation.
Action Performance Evaluation
Evaluating action performance is like checking the mold’s heartbeat:
- Opening/Closing Actions: The opening and closing actions should be noiseless and smooth, resembling a well-oiled machine without noise or vibration.
- Demolding Action: Watching the demolding action work seamlessly is satisfying; ensure lifters/sliders work properly during demolding for smooth product ejection.
Trial Acceptance
Trial acceptance is where everything comes together in real-world performance:
- Preparation & Observation: Adjusting machine settings and choosing materials feel like preparing for a great performance; select appropriate materials and adjust injection molding machine settings.
- Test Product Inspection: During test runs, measuring dimensions is crucial; measure dimensions and conduct performance tests to ensure compliance with design requirements.
These checks are not just simple steps but stories of careful work and strong attention to detail with the goal of producing quality molds for production.
Surface roughness for precision molds is Ra0.2 - Ra0.8μm.True
Precision molds require smooth surfaces, hence the specified roughness range.
Mold closing gap should exceed 0.05mm to prevent flash.False
A smaller gap under 0.03-0.05mm is needed to avoid product flash.
Why are mold trials crucial before production?
Do you ever ask yourself why mold trials matter so much in manufacturing? These test runs hold high importance before the real production begins.
A mold trial before production is essential. This confirms that the mold works well. It checks the quality of the product. The trial catches problems early. It delivers accuracy. Costs decrease. Product reliability is really important and increases.
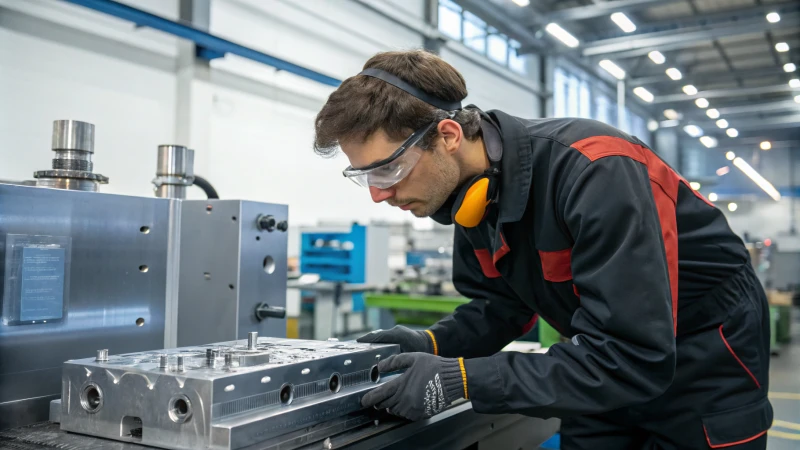
Understanding Mold Trials
When I first began in manufacturing, I saw mold trials as just another task on a long list of pre-production duties. Later, I discovered their real importance. A mold trial is more than a simple test. Here, theory meets practice. It helps prove that a detailed design turns into a real product. This step fixes any problems before full production starts.
Important Parts of a Mold Trial
1. Surface Quality Check
I recall my first time with a roughness meter, standing with my mentor, checking the mold cavity’s surface. Our goal was the perfect Ra0.2 – Ra0.8μm range. Even a tiny error could change the product’s appearance and texture. We examined each piece under light, searching for any scratches or rust from storage.
Aspect | Requirement |
---|---|
Surface Roughness | Ra0.2 – Ra0.8μm |
Flatness Error | ≤ 0.03mm |
2. Mold Size Precision
Precision matters greatly. We spent hours with calipers and CMMs, making sure every millimeter matched the blueprints—crucial for the mold’s functionality12. My heart would race a bit when the numbers lined up exactly; this meant we succeeded with the mold’s precision.
Reasons for Mold Trials
Avoiding Expensive Mistakes
Mold trials help catch mistakes early, saving us trouble later by allowing adjustments to mold design13 or process settings—vital for smooth production.
Guaranteeing Product Excellence
We have all experienced those bad moments—spotting short shots or weld marks in the wrong places during trials guarantees each part meets top standards in both look and function because high standards matter.
Mold Trial Challenges
Honestly, mold trials can feel overwhelming; they need time and resources and sometimes several attempts are necessary to achieve the best results. However, these efforts are valuable to confirm the final product’s quality.
Reviewing trial outcomes involves watching how well the plastic fills the cavity and looking closely for insufficient fill, flash or weld marks—defects indicating issues with injection pressure or gate layout but understanding them helps improve.
Mastering mold trials advances production methods and confirms that every product made is something we can really be proud of.
Mold trials ensure mold size accuracy.True
Mold trials verify dimensions with calipers or CMM to meet design specs.
Surface quality is not checked during mold trials.False
Inspectors measure surface roughness to ensure it meets design standards.
How Can Mold Acceptance Impact Product Quality?
Do you ever think about how the hidden process of mold approval influences the quality of everyday products? Let’s explore this process and see how it functions.
Mold acceptance affects product quality by checking the surface and size of the mold. This makes sure they match design plans. Good molds reduce defects like flashes and misalignments. Products then become reliable and appealing.
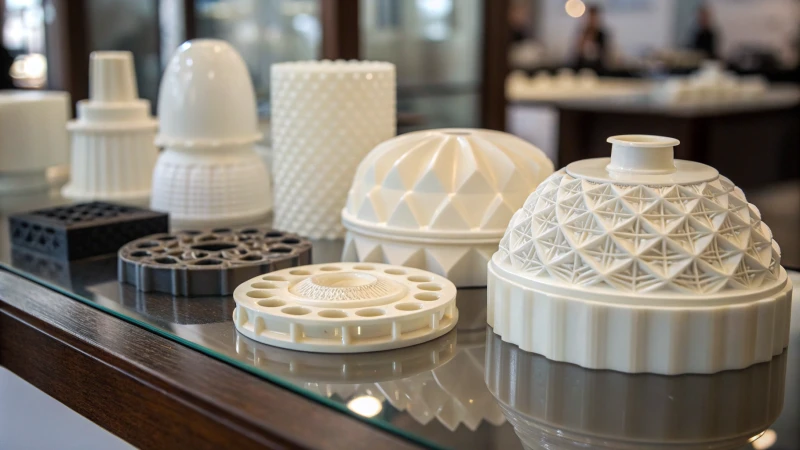
The Importance of Surface Quality Inspection
When I began working with molds, I noticed how surface quality greatly improves product appearance. Imagine holding a newly molded piece. It looks perfect – no scratches, no rust. This perfection results from careful surface inspections. We use a roughness meter to verify every cavity and core meet specific standards, usually Ra0.2 – Ra0.8μm for high-precision jobs. Even a tiny defect could ruin not only the look but also the product’s lifespan. It’s really important.
Precision in Dimensional Accuracy
Precision matters greatly in mold making. I remember seeing a three-coordinate measuring machine14 (CMM) for the first time. This machine was amazing, like something from a sci-fi film. Its ability to measure down to microns is invaluable. We use it with calipers and micrometers to check every dimension, from cavity depth to hole spacing.
Measurement Tool | Application | Precision |
---|---|---|
Calipers | Basic linear dimensions | ±0.02mm |
Micrometers | Diameter measurements | ±0.01mm |
CMM | High precision features | ±0.005mm |
It’s like solving a complex puzzle where every piece must fit perfectly.
Evaluating Mold Assembly Accuracy
Assembling molds is like directing an orchestra; every part must work in harmony. I’ve seen how a perfectly fitted guide pin can mean the difference between smooth operations and frustrating misalignments. The key is fitting every part seamlessly so all parts close tightly without gaps.
Performance of Mold Action
Running mold action poorly feels like running a marathon with a stone in your shoe. The opening and closing should be very smooth, with no unexpected sounds or vibrations. Testing at multiple speeds helps confirm everything works well, preventing expensive delays or defects.
Conducting a Successful Mold Trial
There is nothing like the crucial moment during a mold trial; it tests all our efforts. I watch carefully for problems like short shots or flashes, as they signify issues with pressure or clamping.
Precise adjustments here greatly improve product quality.
Adjustments matter a lot.
For more on how these factors connect, see injection molding parameters15. Every step we take shows our very strong commitment to quality and reliability in everything we produce.
A roughness meter checks mold surface quality.True
Roughness meters measure surface texture, ensuring quality standards are met.
Calipers measure high precision features with ±0.005mm accuracy.False
Calipers measure basic dimensions with ±0.02mm precision, not high precision.
Conclusion
The injection mold acceptance process involves thorough inspections of surface quality, size accuracy, assembly precision, and performance evaluation to ensure molds meet design specifications for high-quality production.
-
Learn how roughness meters assess mold surfaces to ensure product quality. ↩
-
Discover effective methods for handling rust on stored molds. ↩
-
Understand how proper identification aids in mold management and traceability. ↩
-
Understand the specific surface roughness standards essential for precision injection molds. ↩
-
Explore how surface roughness impacts mold quality and precision. ↩
-
Learn why cooling channels are crucial for effective mold performance. ↩
-
Understand methods and tools used to ensure flatness in mold components. ↩
-
Discover techniques to verify accurate mold closure to prevent defects. ↩
-
Learn how surface quality inspection ensures molds meet aesthetic and functional standards. ↩
-
Discover tools and techniques used to verify the precise dimensions of molds. ↩
-
Explore how checking mold closing accuracy prevents production defects. ↩
-
Details on how precise measurements ensure mold functionality. ↩
-
Explores why verifying mold performance is crucial before mass production. ↩
-
Learn how a CMM enhances precision in measuring mold dimensions, ensuring high-quality product outcomes. ↩
-
Discover how adjusting injection molding parameters can optimize product quality and reduce defects. ↩