The manufacturing of Lego bricks involves a precise and highly automated process called injection molding1, where molten plastic is injected into molds to create the iconic, interlocking bricks. This method ensures each brick meets strict quality standards for durability, precision, and color consistency.
Legos are made using injection molding, a process that injects molten plastic into precise molds to create durable, interlocking bricks with tight tolerances, primarily using Acrylonitrile Butadiene Styrene (ABS)2 for its strength and color retention.
Understanding the injection molding process and the materials used in Lego production3 is essential for appreciating the precision and sustainability behind these beloved toys. Explore further to see how this process ensures every brick fits perfectly, regardless of when or where it was made.
Injection molding is the only method used to make Legos.True
Lego bricks are exclusively produced using injection molding due to the need for precision and consistency.
Legos are made from biodegradable materials.False
While Lego is exploring sustainable options, the primary material remains ABS, which is not biodegradable.
- 1. What is Injection Molding and How Does It Work for Legos?
- 2. What Materials Are Used in Lego Production?
- 3. What Are the Steps in the Lego Injection Molding Process?
- 4. What Are the Key Factors in the Lego Injection Molding Process?
- 5. What Are the Applications of Injection Molding Beyond Legos?
- 6. How Has Lego’s Manufacturing Process Evolved Over Time?
- 7. Conclusion
What is Injection Molding and How Does It Work for Legos?
Injection molding is a manufacturing process that creates precise plastic parts by injecting molten plastic into a mold. For Legos, this process ensures each brick is identical and can interlock seamlessly with others.
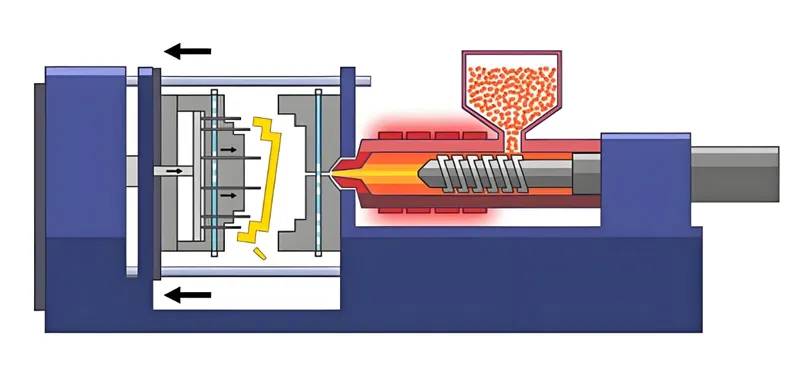
Injection molding for Legos involves melting ABS plastic4, injecting it into high-precision molds5, and cooling it to form durable bricks with tolerances as tight as 0.0005 inches, ensuring perfect fit and consistency.
Process Step | Description |
---|---|
Material Preparation | ABS granules are stored in silos and fed into molding machines. |
Heating | Granules are heated to 450°F (230°C) to become molten plastic. |
Injection | Molten plastic is injected into molds under 25-150 tons of pressure. |
Cooling and Ejection | Plastic cools and solidifies in the mold, then is ejected. |
Automation | Robots and conveyor belts handle the bricks for further processing. |
Why Injection Molding is Ideal for Legos
Injection molding allows for the mass production of complex shapes with high precision, making it perfect for Lego bricks. The process is efficient, scalable, and minimizes waste, aligning with Lego’s commitment to quality and sustainability.
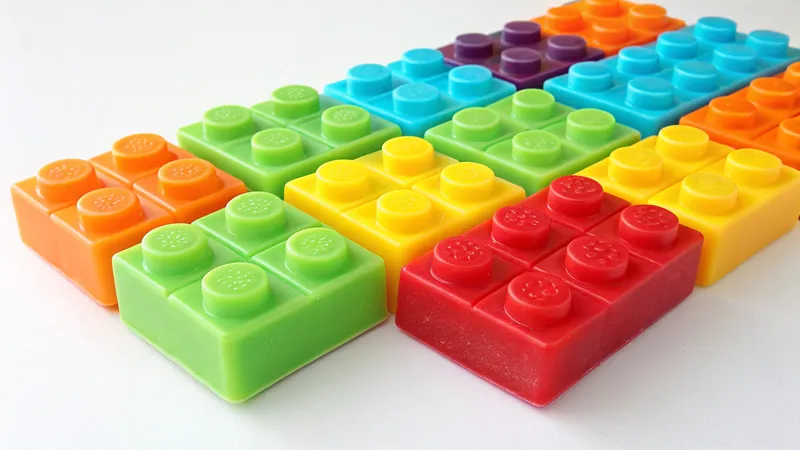
Injection molding is the most cost-effective method for producing Legos.True
Despite high initial mold costs, injection molding enables mass production with minimal waste, reducing long-term costs.
Injection molding cannot produce complex shapes like Lego bricks.False
Injection molding is specifically chosen for its ability to create intricate designs with tight tolerances.
What Materials Are Used in Lego Production?
The choice of materials in Lego production is critical for ensuring the bricks’ durability, safety, and vibrant colors. Lego primarily uses ABS plastic but is also exploring sustainable alternatives.
Legos are primarily made from Acrylonitrile Butadiene Styrene (ABS), chosen for its strength, color retention, and safety, with bio-polyethylene being introduced for eco-friendly sets.
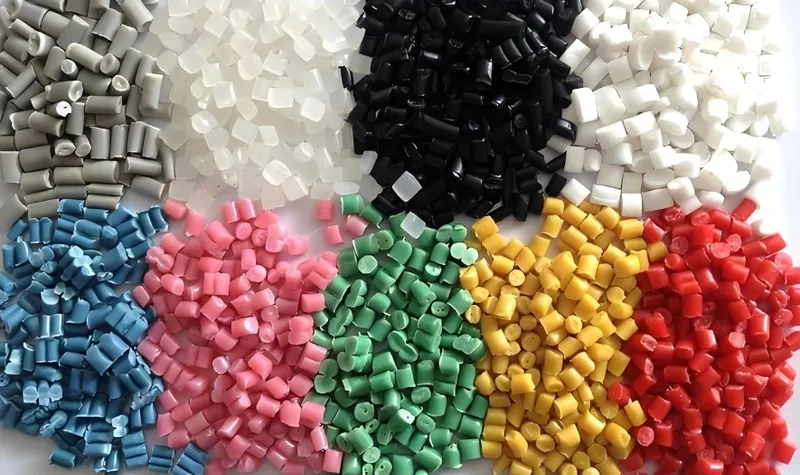
Acrylonitrile Butadiene Styrene (ABS)
ABS is a thermoplastic polymer known for its toughness and impact resistance. It is ideal for Lego bricks because it maintains its shape and color over time, even after extensive use. ABS also allows for precise molding, ensuring each brick fits perfectly with others.
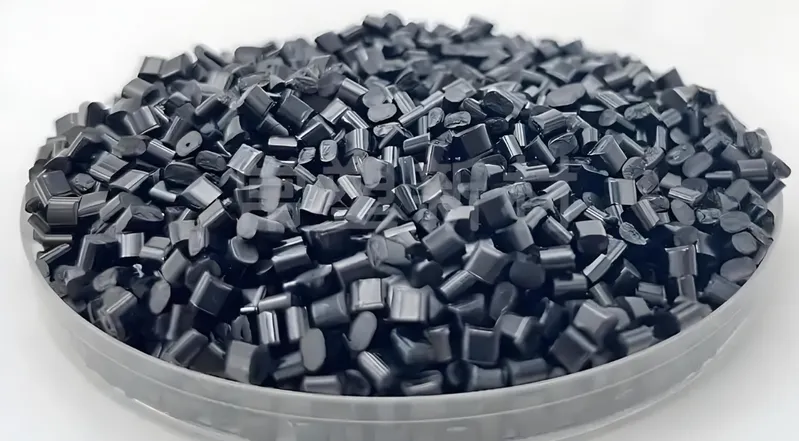
Bio-Polyethylene
Lego is committed to sustainability and has begun using bio-polyethylene, a plant-based plastic derived from sugarcane, in some sets. This material offers similar properties to traditional plastics but with a reduced environmental footprint. Lego aims to use only sustainable materials by 2030 (Lego Sustainability).
ABS is the only material used in Lego bricks.False
While ABS is the primary material, Lego is incorporating bio-based plastics for sustainability.
Bio-polyethylene is used in all Lego sets.False
Bio-polyethylene is currently used in select sets as part of Lego’s sustainability initiatives.
What Are the Steps in the Lego Injection Molding Process?
The injection molding process6 for Lego bricks is a highly automated and precise workflow that ensures each brick meets strict quality standards.
The Lego injection molding process involves material preparation, heating, injection, cooling, ejection, and automation, with each step carefully controlled to maintain precision and efficiency.
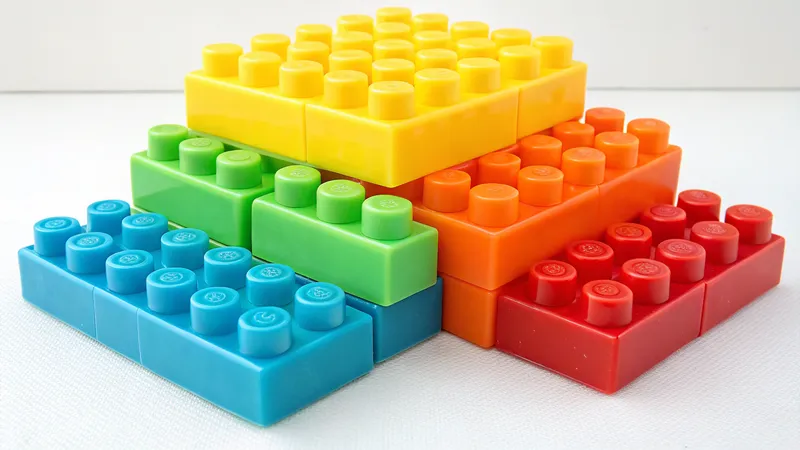
Material Preparation
ABS granules7 are delivered to factories and stored in large silos, each holding up to 33 tons of plastic. These granules are then fed into molding machines for processing.
Heating
The ABS granules are heated to 450°F (230°C) in the molding machines, turning them into a molten state ready for injection.
Injection
The molten plastic is injected into high-precision molds under pressures ranging from 25 to 150 tons. The molds are designed with Hot Runner systems8 to reduce waste by injecting plastic directly into individual cavities.
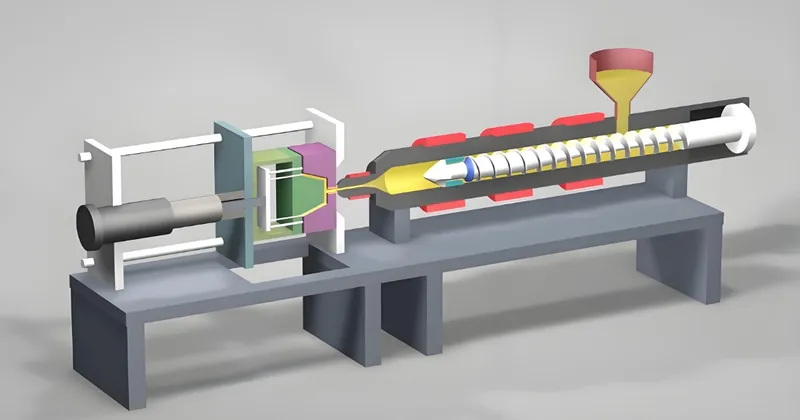
Cooling and Ejection
Once injected, the plastic cools and solidifies in the mold. The entire cycle, from injection to ejection, takes about 10 seconds per brick.
Automation
After ejection, the bricks roll down conveyor belts into boxes. Robot trucks, guided by floor grooves, transport the boxes to the next stage for decoration, assembly, and packaging.
The injection molding process for Legos takes several minutes per brick.False
The cycle time is approximately 10 seconds per brick, making it highly efficient.
Lego molds are designed to minimize plastic waste.True
Hot Runner molds reduce waste by injecting plastic directly into individual cavities.
What Are the Key Factors in the Lego Injection Molding Process?
Several factors influence the quality and consistency of Lego bricks during the injection molding process, including temperature, pressure, and material flow9.
Key factors in Lego injection molding include precise temperature control10, injection pressure, and material flow, all of which ensure the bricks meet tight tolerances and quality standards.
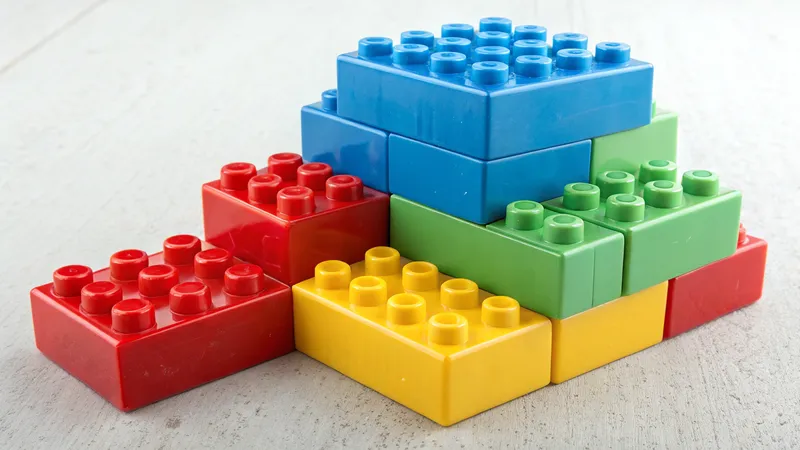
Temperature Control
The temperature must be carefully controlled to ensure the ABS plastic melts evenly and flows properly into the mold. Lego maintains a heating temperature of 450°F (230°C) for optimal results.
Injection Pressure
The pressure during injection (25-150 tons) ensures the molten plastic fills the mold completely and uniformly, preventing defects like warping or incomplete filling.
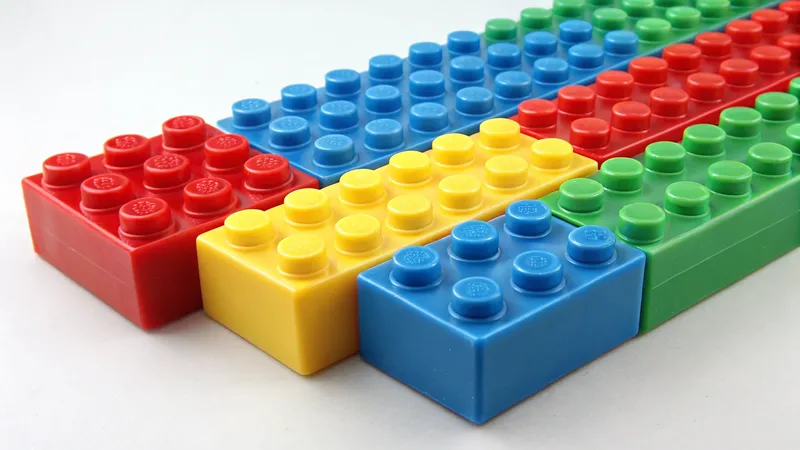
Material Flow
Even material flow is critical to avoid inconsistencies in the brick’s structure. Lego’s Hot Runner molds help achieve this by directing plastic precisely into each cavity.
Temperature control is crucial for preventing defects in Lego bricks.True
Precise temperature ensures even melting and flow, reducing the risk of warping or incomplete filling.
Injection pressure has no impact on the quality of Lego bricks.False
Proper injection pressure is essential for filling the mold completely and maintaining brick integrity.
What Are the Applications of Injection Molding Beyond Legos?
Injection molding is a versatile manufacturing process used in various industries beyond toy production, thanks to its ability to create precise, complex parts efficiently.
Injection molding is used in automotive, medical, and consumer goods industries for producing precise, high-volume plastic parts, from car components to medical devices.
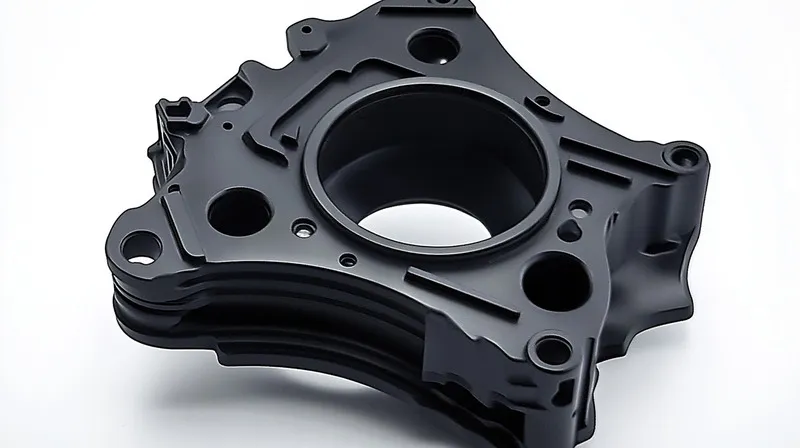
Automotive Industry
Injection molding is used to produce lightweight, durable parts like dashboards, bumpers, and interior panels, reducing vehicle weight and improving fuel efficiency.
Medical Devices
The process is ideal for creating sterile, precise components like syringes, surgical tools, and diagnostic equipment, where consistency and safety are paramount.
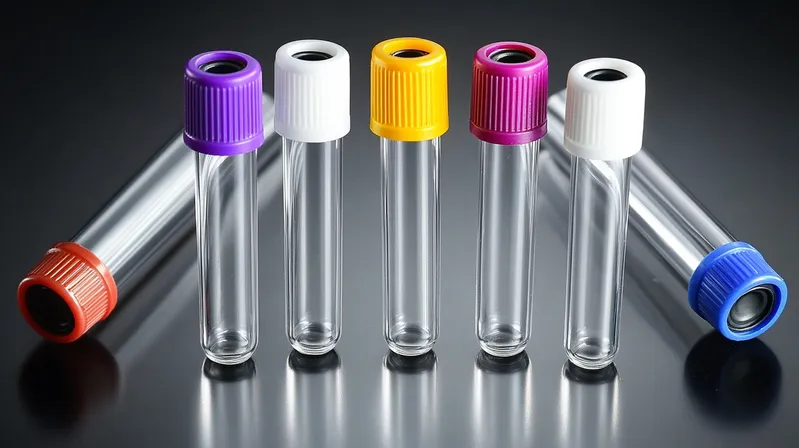
Consumer Goods
From electronics housings to kitchenware, injection molding enables the mass production of everyday items with complex designs and tight tolerances.
Injection molding is only used for small plastic parts.False
While it excels at small parts, injection molding can also produce larger components like car panels.
Injection molding is cost-effective for low-volume production.False
The high initial mold costs make injection molding more suitable for high-volume production.
How Has Lego’s Manufacturing Process Evolved Over Time?
Lego’s manufacturing process has evolved significantly since its inception, with key innovations in materials and molding techniques enhancing precision and sustainability.
Lego’s manufacturing has evolved from using cellulose acetate to ABS plastic and introducing Hot Runner molds for precision, with a recent focus on sustainable materials like bio-polyethylene.
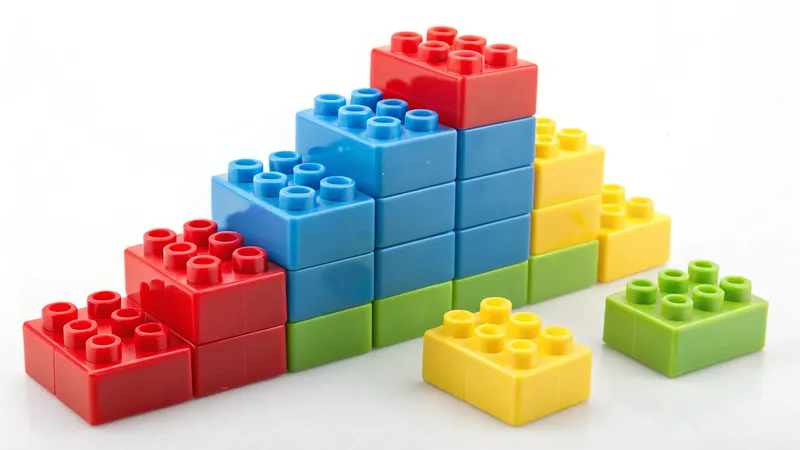
Switch to ABS Plastic
In 1963, Lego switched from cellulose acetate to ABS plastic for better stability, color retention, and durability, under the supervision of Hans Schiess (Lego Molding Philosophy).
Introduction of Hot Runner Molds
In 1961, Lego adopted Hot Runner molds from Schöttli of Switzerland, which reduced plastic waste by injecting directly into individual cavities. By the early 1970s, Lego developed its own Hot Runner mold design for even greater precision (Lego History).
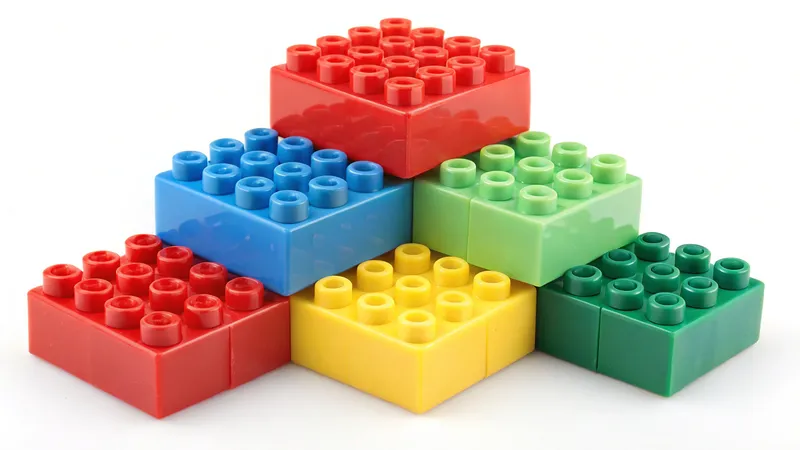
Sustainability Initiatives
Lego is committed to sustainability, aiming to use only bio-based or recycled materials by 2030. The company has already introduced bio-polyethylene in select sets and balanced 100% of its energy use with renewable sources in 2020 (Lego Sustainability).
Lego has always used ABS plastic for its bricks.False
Lego initially used cellulose acetate before switching to ABS in 1963 for better performance.
Lego’s Hot Runner molds were developed in-house from the start.False
Lego initially adopted Hot Runner molds from Schöttli and later developed its own design.
Conclusion
Injection molding is the cornerstone of Lego’s manufacturing process, enabling the production of precise, durable, and consistent bricks that have delighted generations. By using advanced materials like ABS and innovating with sustainable alternatives, Lego continues to set the standard for quality and environmental responsibility in the toy industry.
For more insights into Lego’s production process, explore How LEGO Bricks Are Made or learn about their sustainability efforts at Lego Sustainability.
-
Discover the intricacies of injection molding, the key process behind Lego’s precision and quality, ensuring every brick is perfect. ↩
-
Learn about ABS, the material that gives Lego bricks their strength and color, crucial for understanding their durability. ↩
-
Explore the sustainable practices in Lego production, highlighting their commitment to quality and environmental responsibility. ↩
-
Learn about ABS plastic’s characteristics and why it’s the material of choice for durable products like Lego bricks. ↩
-
Discover the significance of high-precision molds in ensuring product consistency and quality in manufacturing processes. ↩
-
Understanding the injection molding process can provide insights into how precision and efficiency are achieved in manufacturing. ↩
-
Exploring the properties and applications of ABS granules can enhance your knowledge of materials used in production. ↩
-
Learning about Hot Runner systems can reveal how they improve efficiency and reduce waste in the injection molding process. ↩
-
Learning about material flow can help you understand how it impacts the structural integrity and quality of molded products. ↩
-
Exploring temperature control in injection molding reveals its crucial role in ensuring product quality and performance. ↩