The ejector system in injection molding is a crucial mechanism that ensures the efficient removal of molded parts from the mold cavity. This system plays a vital role in maintaining production speed and part quality1, making it essential for manufacturers to understand its operation and design considerations.
The ejector system in injection molding2 uses pins, blades, or air to push or pull solidified plastic parts out of the mold, ensuring efficient, damage-free removal for continuous production.
Mastering the ejector system’s intricacies can optimize your injection molding process, reducing defects and downtime. Explore further to learn how different ejector types and designs3 impact part quality and production efficiency.
The ejector system is essential for all injection molding processes.True
Without an ejector system, parts would remain stuck in the mold, halting production and potentially damaging both the part and the mold.
Ejector systems are only necessary for complex part geometries.False
Even simple parts require an ejector system to ensure consistent and efficient removal from the mold cavity.
What Is the Ejector System in Injection Molding?
The ejector system is a fundamental component of injection molding machines, designed to remove finished plastic parts from the mold after they have cooled and solidified.

The ejector system, also known as the ejection or part removal system, uses mechanical or pneumatic mechanisms to extract molded parts, ensuring smooth production cycles and preventing part damage.
Ejector Type | Common Applications | Notes |
---|---|---|
Pin Ejection | Standard parts | Widely used, cost-effective |
Blade Ejection | Large, flat surfaces | Ideal for automotive parts |
Air Ejection | Delicate or sticky parts | Prevents surface damage |
Definition and Core Principles
The ejector system operates by applying controlled force to release the part from the mold cavity. This is achieved through various mechanisms such as ejector pins, blades, sleeves, or air jets. The system must overcome the adhesion and shrinkage forces that hold the part in place, requiring precise timing and force application to avoid damaging the part or leaving marks.
Common aliases for the ejector system include "ejection system," "mold ejector," and "part release mechanism."
Classification of Ejector Systems
Ejector systems can be classified based on several criteria:

-
By Type of Ejector:
- Pin Ejection: Uses cylindrical pins to push the part out.
- Blade Ejection: Employs flat blades for larger surfaces.
- Sleeve Ejection: Utilizes hollow pins for parts with through-holes.
- Stripper Plate Ejection: Involves a plate that slides to push the part out.
- Air Ejection: Uses compressed air to blow the part out.
- Lifter Ejection: Employs lifters for parts with undercuts.
-
By Driving Force:
- Mechanical: Powered by the molding machine’s hydraulic or mechanical systems.
- Pneumatic: Driven by compressed air.
- Hybrid: Combines mechanical and pneumatic mechanisms.
-
By Application:
- Standard Molds: For simple parts.
- Complex Molds: For parts with undercuts or intricate features.
Pin ejection is the most common type of ejector system.True
Pin ejection is widely used due to its simplicity, cost-effectiveness, and suitability for most standard parts.
Air ejection is only used for very specific applications.False
While specialized, air ejection is increasingly popular for delicate or sticky materials to prevent surface damage.
How Does the Ejector System Work?
Understanding the operation of the ejector system is key to optimizing the injection molding process and ensuring high-quality parts.
The ejector system activates after the mold opens, using pins, blades, or air to apply force and release the part, then resets for the next cycle.

Process Workflow
The ejection process is integrated into the injection molding cycle:
-
Mold Opening: After cooling, the mold separates.
-
Ejector Activation: The ejector system is triggered, moving the ejector plate forward.
-
Force Application: Ejector mechanisms contact and push the part out.
-
Part Removal: The part is fully released and removed.
-
System Reset: The ejector system retracts, and the mold closes for the next cycle.
Key parameters include:
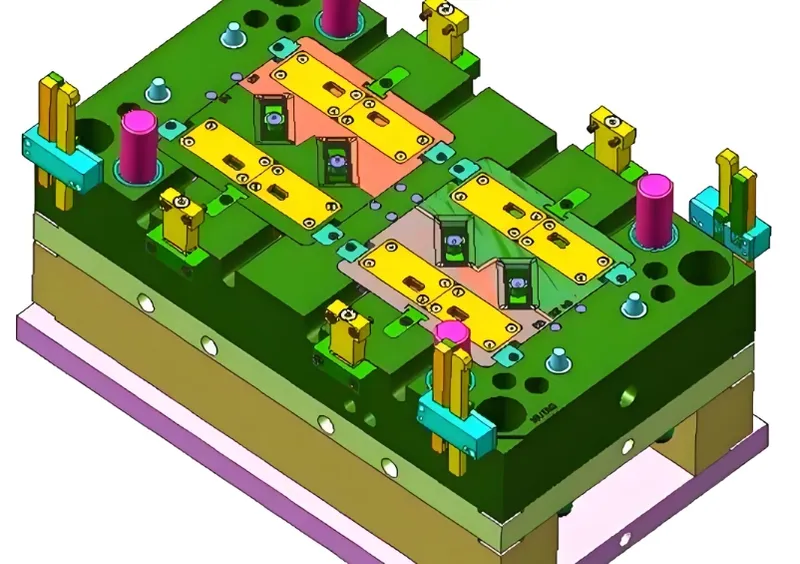
-
Ejector Stroke: Typically 5-10mm or 2/3 of the part’s depth.
-
Ejection Force: Must exceed the holding force due to shrinkage.
-
Timing and Speed: Controlled to prevent part damage.
Material Compatibility
Different materials require tailored ejector approaches:
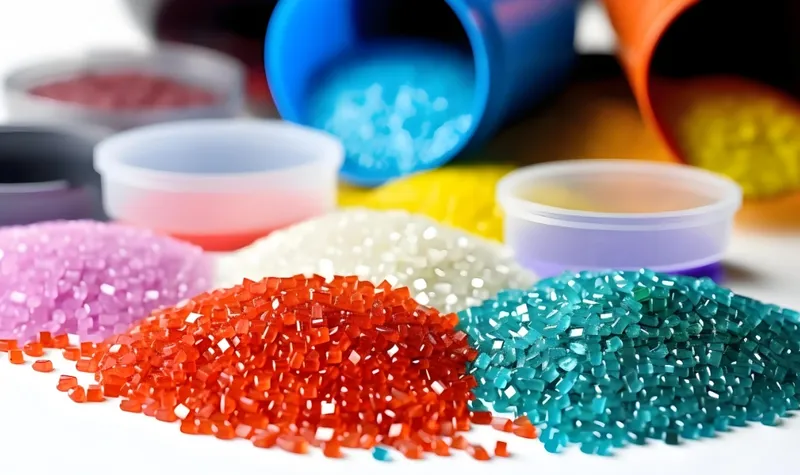
-
Hard Plastics (e.g., ABS): Suitable for mechanical ejection.
-
Soft or Sticky Materials (e.g., TPE): Benefit from air or stripper plate ejection.
-
High-Shrinkage Materials: May need higher ejection forces.
Material Type | Recommended Ejection Method | Notes |
---|---|---|
Hard Plastics | Pin, Blade | Can handle high forces |
Soft/Sticky Plastics | Air, Stripper Plate | Requires gentle ejection |
High-Shrinkage | Pin with High Force | Needs strong force |
The ejector system operates independently of the molding cycle.False
The ejector system is synchronized with the mold’s opening and closing to ensure seamless operation.
Material properties significantly influence ejector system design.True
Factors like shrinkage and adhesion dictate the choice of ejector type and force required.
What Are the Applications of the Ejector System?
The ejector system is indispensable across various industries, ensuring efficient part removal and maintaining production flow.
The ejector system is used in automotive, medical, consumer goods, and electronics industries for removing parts like dashboards, syringe barrels, and device housings.
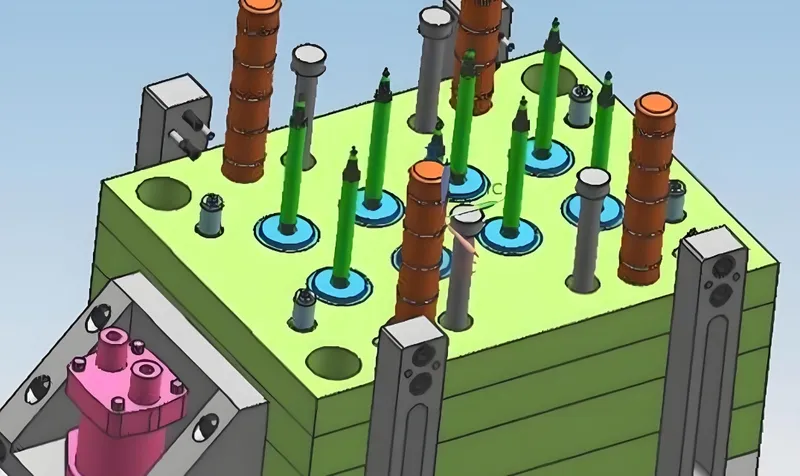
Typical Application Scenarios
-
High-Volume Production: Essential for rapid cycle times in consumer goods.
-
Complex Geometries: Necessary for parts with undercuts or thin walls.
-
Delicate Materials: Crucial for preventing damage to sticky or soft parts.
-
Large Parts: Vital for robust removal of heavy components.
Industry examples include:
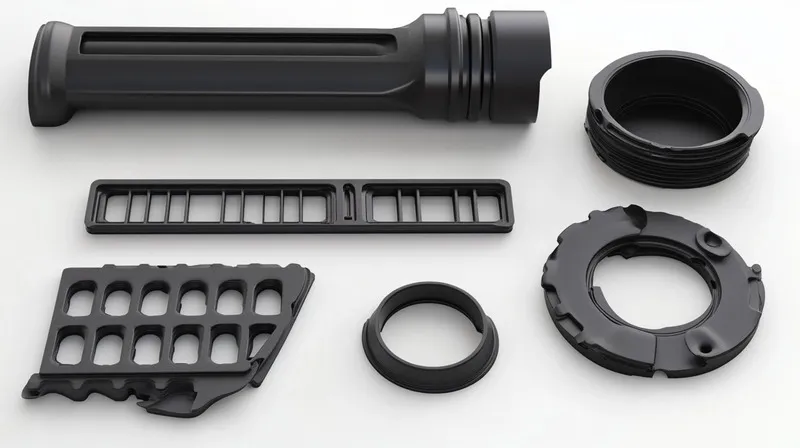
-
Automotive: Trim components and structural elements.
-
Medical: Precision parts like syringe barrels.
-
Consumer Electronics: Device housings requiring flawless finishes.
Pros and Cons Comparison
Comparing the ejector system to alternative methods:
Method | Pros | Cons |
---|---|---|
Ejector System | Automated, efficient, integrated | Potential marks, requires precise design |
Manual Removal | Flexible, no equipment cost | Labor-intensive, inconsistent, slow |
Robotic Removal | Precise, handles complex parts | High cost, requires additional systems |
The ejector system reduces production costs by automating part removal.True
Automation minimizes labor and increases consistency, leading to cost savings.
Manual removal is a viable alternative for high-volume production.False
Manual removal is too slow and inconsistent for large-scale manufacturing.
How to Design an Effective Ejector System?
Designing an ejector system requires careful consideration of part geometry, material properties, and production requirements.
An effective ejector system design4 involves selecting the right ejector type, calculating stroke and force, and positioning ejectors to avoid part damage.
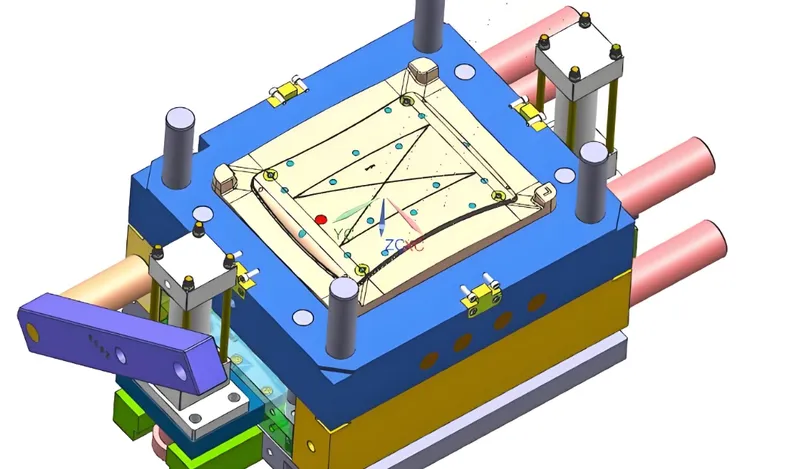
Design Checklist
-
Identify Ejection Points: Place on rigid areas like ribs or flanges.
-
Check for Undercuts: Use lifters or angle pins if necessary.
-
Ensure Draft Angles: Typically 1-2° for easy ejection.
-
Select Ejector Type: Based on part complexity5 and material.
-
Calculate Stroke and Force: Ensure sufficient but not excessive.
-
Protect Surface Finish: Position ejectors on non-visible surfaces.
-
Match Material Properties: Consider shrinkage and adhesion.
Process Selection Decision-Making
Consider:
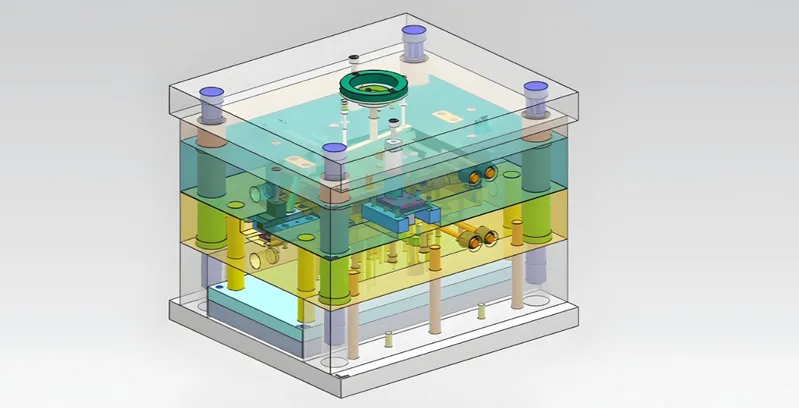
-
Production Volume: High volume requires durable, automated systems.
-
Part Complexity: Complex parts may need specialized ejectors.
-
Material Type: Soft materials favor gentle ejection methods.
-
Cost: Balance design complexity with budget constraints.
Decision Tree:
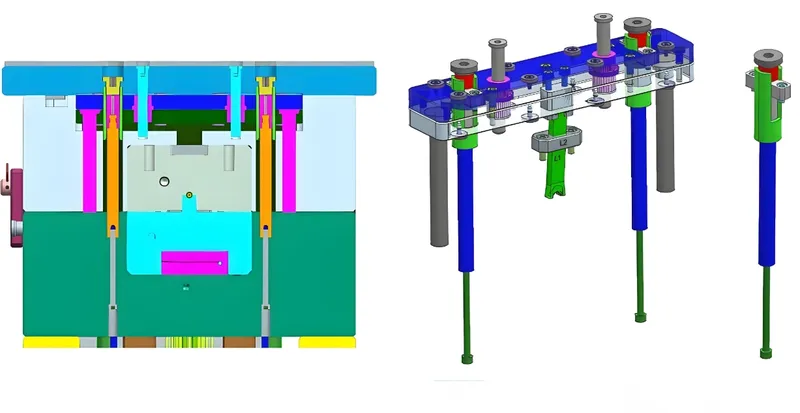
-
Assess Geometry: Simple (pins) vs. complex (lifters).
-
Evaluate Material: Hard (mechanical) vs. soft (air).
-
Determine Volume: High (automated) vs. low (simpler systems).
-
Select Type: Based on the above and cost.
Proper ejector system design can eliminate part defects.True
Correct design prevents issues like deformation, cracking, or surface marks.
All ejector systems require the same design considerations.False
Design must be tailored to specific part geometries and material properties.
The ejector system is part of a broader ecosystem in injection molding, connected to various upstream and downstream technologies.
Related technologies include mold design software, material science, automation, and quality control systems, all enhancing the ejector system’s effectiveness.
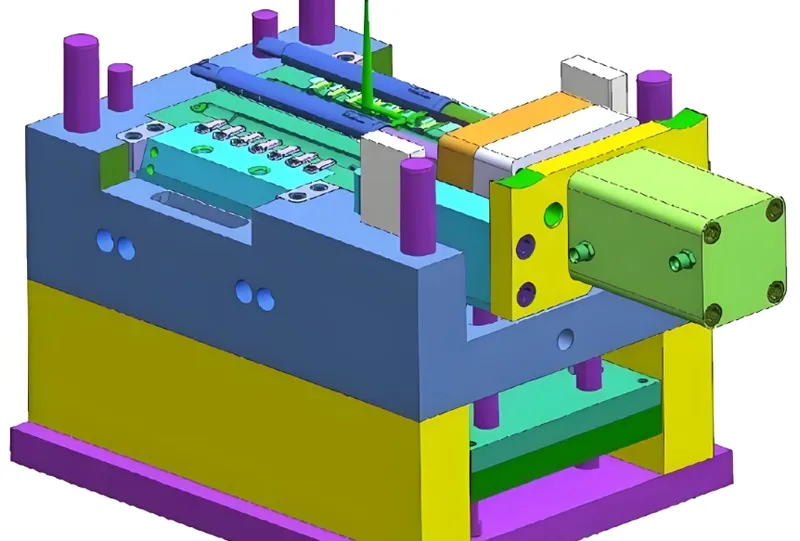
Upstream Technologies
-
Mold Design Software6: Tools like Moldflow simulate ejection for optimized design.
-
Material Science7: Research into plastics informs ejector selection.
-
Machine Technology: Advances in hydraulics or electrics improve control.
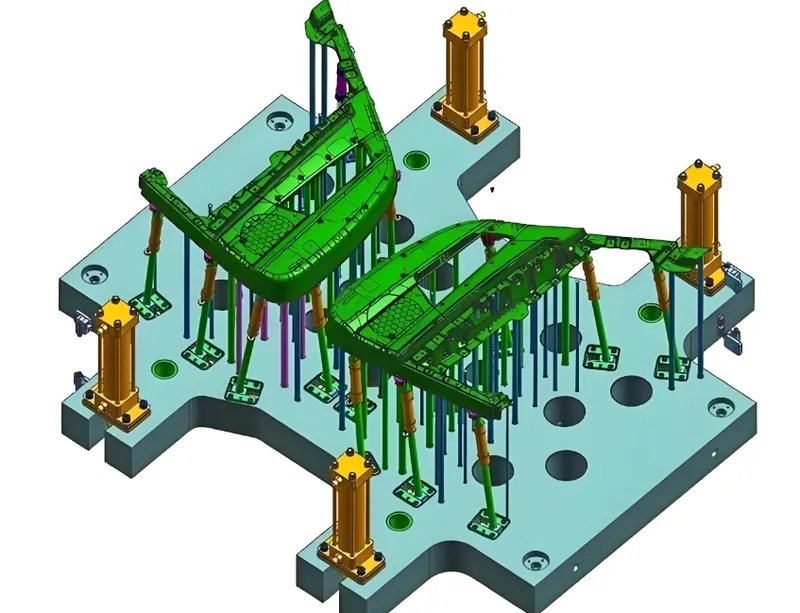
Downstream Technologies
-
Part Finishing: Trimming or polishing to remove ejector marks.
-
Automation: Robotic arms handle ejected parts.
-
Quality Control8: Vision systems ensure part quality.
Advancements in mold design software have improved ejector system efficiency.True
Simulation tools allow for better prediction and optimization of ejection processes.
The ejector system operates in isolation from other molding technologies.False
It is deeply integrated with mold design, material selection, and automation systems.
Conclusion
The ejector system is a critical component in injection molding9, ensuring efficient and damage-free part removal. By understanding its types, operation, and design considerations10, manufacturers can optimize production and maintain high-quality outputs. The system’s integration with related technologies further enhances its role in the broader manufacturing process.
-
Exploring this relationship can help manufacturers enhance efficiency and product standards. ↩
-
Understanding the ejector system is key to optimizing production speed and part quality in injection molding. ↩
-
Learning about various ejector designs can lead to better decision-making for improved production outcomes. ↩
-
Explore this resource to understand the essential practices for designing an effective ejector system, ensuring optimal performance and reliability. ↩
-
Discover how part complexity can dictate the type of ejector system needed, ensuring your design meets all requirements efficiently. ↩
-
Explore the latest mold design software tools to enhance your injection molding process and optimize ejection designs. ↩
-
Understanding material science is crucial for selecting the right ejector system and improving overall molding quality. ↩
-
Learn about effective quality control practices to ensure the highest standards in your injection molded parts. ↩
-
This resource will provide you with comprehensive insights into injection molding processes, enhancing your knowledge of manufacturing techniques. ↩
-
Understanding design considerations is crucial for optimizing production; this link will guide you through essential factors to consider. ↩