Two-plate molds are the backbone of injection molding1, offering a straightforward and cost-effective solution for producing a wide range of plastic parts2. In this blog post, we’ll explore how these molds work, their applications, and why they remain a popular choice in manufacturing.
A two-plate mold is the simplest type of injection mold, consisting of two main parts: the cavity plate and the core plate, separated by a single parting plane. It is widely used for producing plastic parts by injecting molten plastic into the mold cavity, allowing it to cool and solidify, and then ejecting the part.
Understanding the functionality and applications of two-plate molds3 is essential for anyone involved in manufacturing, from product designers to engineers. This post will delve into the details of how two-plate molds operate, their advantages, limitations, and how they stack up against other mold types.
Two-plate molds are the most commonly used molds in injection molding.True
Due to their simplicity and cost-effectiveness, two-plate molds are the go-to choice for many injection molding applications, especially for high-volume production of simple parts.
Two-plate molds can only be used for small parts.False
While they are ideal for smaller, simpler parts, two-plate molds can also be designed for larger components, though they may face challenges with complex geometries or multi-cavity setups.
- 1. What is a Two-Plate Mold?
- 2. How Does a Two-Plate Mold Function?
- 3. What are the Applications of Two-Plate Molds?
- 4. What are the Advantages and Disadvantages of Two-Plate Molds?
- 5. How Do Two-Plate Molds Compare to Other Mold Types?
- 6. What are the Key Considerations in Designing Two-Plate Molds?
- 7. Conclusion
What is a Two-Plate Mold?
A two-plate mold, also known as a two-plate injection mold, is the most basic and widely used type of mold in injection molding. It consists of two primary plates: the cavity plate and the core plate, which separate at a single parting plane. The mold is designed to create plastic parts by injecting molten plastic into the cavity, where it cools and solidifies into the desired shape.
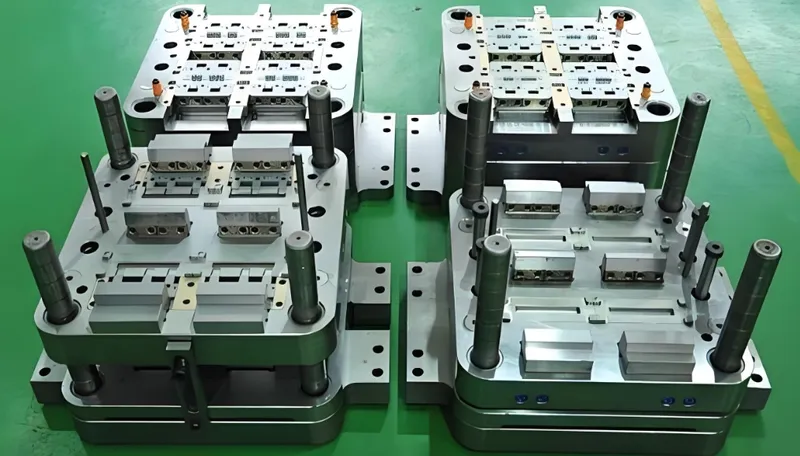
Two-plate molds are characterized by their simplicity, with the runner and gate located at the parting plane, allowing for easy ejection of both the part and the runner system.
Mold Type | Parting Planes | Complexity | Cost |
---|---|---|---|
Two-Plate Mold | 1 | Low | Low |
Three-Plate Mold | 2 | Medium | Medium |
Hot Runner Mold | Varies | High | High |
Key Components of a Two-Plate Mold
-
Cavity Plate: Contains the cavity that forms the outer shape of the part.
-
Core Plate: Contains the core that forms the inner shape of the part.
-
Sprue and Runner System: Channels through which molten plastic is injected into the cavity.
-
Ejection System: Typically ejector pins that push the solidified part out of the mold.
Two-plate molds are ideal for parts with simple geometries and are commonly used in industries like packaging, consumer goods, and automotive for high-volume production.
Two-plate molds are only used for basic plastic parts.False
While they are ideal for simple parts, two-plate molds can also handle more complex designs with careful planning, though they may not be the best choice for highly intricate parts.
How Does a Two-Plate Mold Function?
The functionality of a two-plate mold is straightforward yet highly efficient. The process involves several key steps that ensure the production of consistent, high-quality plastic parts.
The two-plate mold functions by closing the mold, injecting molten plastic into the cavity, cooling the plastic to solidify it, opening the mold, and ejecting the part along with the runner system.
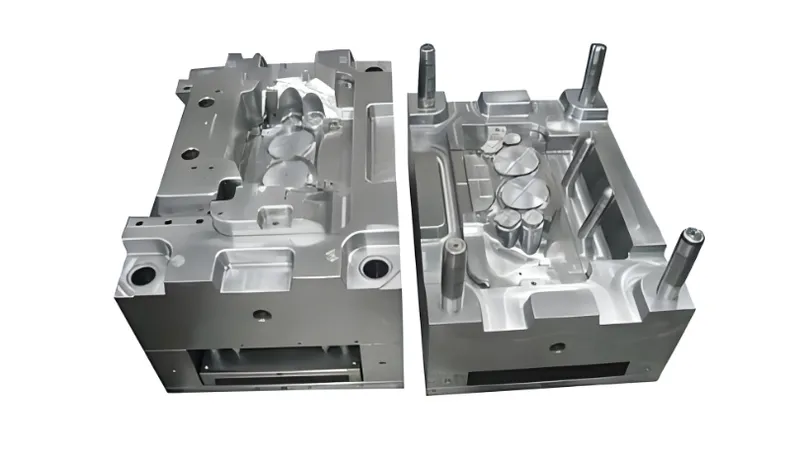
Step-by-Step Process
-
Mold Closing: The cavity and core plates come together at the parting plane, forming a sealed cavity.
-
Injection: Molten plastic is injected through the sprue and runner system into the cavity under high pressure.
-
Cooling: The plastic cools and solidifies inside the mold, taking the shape of the cavity.
-
Mold Opening: The mold splits at the parting plane, separating the cavity and core plates.
-
Ejection: Ejector pins push the solidified part and the attached runner system out of the mold.
Step | Key Parameters | Notes |
---|---|---|
Injection | Pressure: High for filling | Depends on material and part size |
Cooling | Time: 10-60 seconds | Influenced by part thickness |
Ejection | Draft Angles: 1-2° | Ensures smooth part release |
The simplicity of this process allows for shorter cycle times, making two-plate molds ideal for high-volume production.
Two-plate molds require manual removal of the runner system.False
In most cases, the runner system is ejected along with the part and can be automatically separated in post-processing, though some setups may require manual intervention.
What are the Applications of Two-Plate Molds?
Two-plate molds are versatile and find applications across various industries due to their cost-effectiveness and efficiency.
Two-plate molds are commonly used in the packaging, consumer goods, and automotive industries for producing items like bottle caps, containers, and interior car components.

Industry Examples
-
Packaging: Bottle caps, lids, and containers.
-
Consumer Goods: Toys, household items, and disposable cutlery.
-
Automotive: Interior trim pieces and dashboard components.
These molds are particularly suited for parts that are flat or have simple geometries, where the runner system can be easily managed.
Two-plate molds are unsuitable for complex parts.True
While they can be used for some complex parts, two-plate molds are less efficient for designs requiring multiple gates or intricate geometries, where three-plate or hot runner molds are preferred.
What are the Advantages and Disadvantages of Two-Plate Molds?
Understanding the pros and cons of two-plate molds is crucial for deciding when to use them in manufacturing.
Two-plate molds offer simplicity, lower cost, and faster cycle times but are limited by their inability to handle complex geometries without flow balancing issues.

Advantages
-
Cost-Effective4: Fewer components and simpler design reduce manufacturing costs.
-
Faster Cycle Times5: The single parting plane allows for quicker mold opening and closing.
-
Ease of Maintenance: Simpler structure makes repairs and adjustments easier.
Disadvantages
- Limited to Simpler Parts: Not ideal for parts requiring multiple gates or complex shapes.
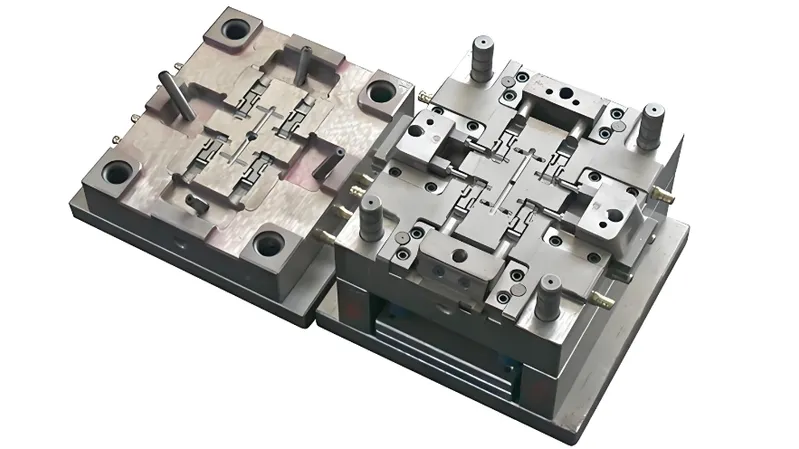
-
Runner Waste: The runner system must be ejected with the part, leading to material waste.
-
Flow Balancing Issues: In multi-cavity molds, ensuring even filling can be challenging.
Advantage | Disadvantage |
---|---|
Low cost | Limited to simple geometries |
Fast cycle times | Runner waste |
Easy maintenance | Flow balancing in multi-cavity molds |
Two-plate molds are the most cost-effective option for all injection molding projects.False
While they are cost-effective for simple, high-volume parts, more complex projects may benefit from the precision and material savings of hot runner molds, despite higher initial costs.
How Do Two-Plate Molds Compare to Other Mold Types?
Comparing two-plate molds with other common mold types, such as three-plate and hot runner molds, helps in selecting the right mold for specific applications.
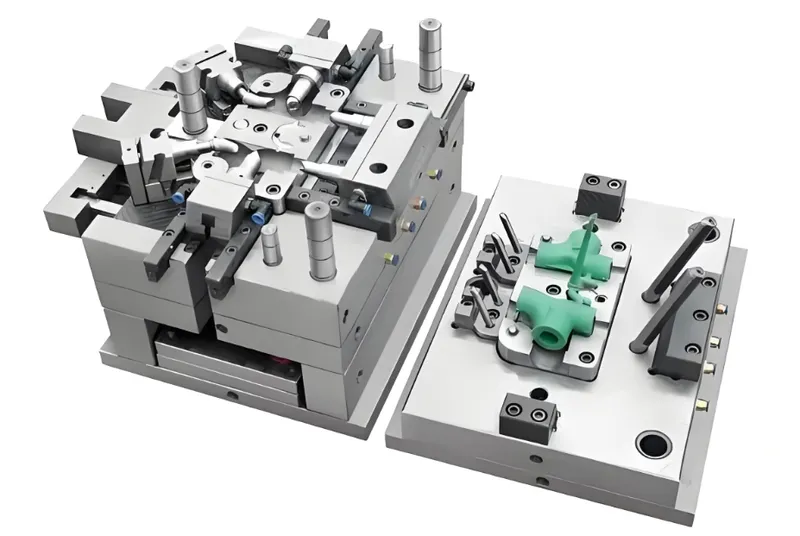
Two-plate molds are simpler and cheaper than three-plate and hot runner molds but lack the flexibility for complex parts or material efficiency.
Comparison Table
Mold Type | Parting Planes | Runner System | Best For |
---|---|---|---|
Two-Plate Mold | 1 | Cold runner | Simple, high-volume parts |
Three-Plate Mold | 2 | Cold runner, separate | Parts needing multiple gates |
Hot Runner Mold | Varies | No runner waste | Complex, high-precision parts |
-
Three-Plate Molds: Feature an additional plate that separates the runner system from the part, allowing for more precise gate placement but increasing complexity and cycle times.
-
Hot Runner Molds: Eliminate the runner system entirely by keeping the plastic molten, reducing waste but significantly increasing cost and complexity.
Hot runner molds are always better than two-plate molds.False
Hot runner molds offer advantages in material savings and precision but are more expensive and complex, making two-plate molds a better choice for simpler, cost-sensitive projects.
What are the Key Considerations in Designing Two-Plate Molds?
Designing a two-plate mold requires careful attention to several factors to ensure optimal performance and part quality.
Key design considerations for two-plate molds include part geometry, material selection, gate placement, and ejection mechanisms.
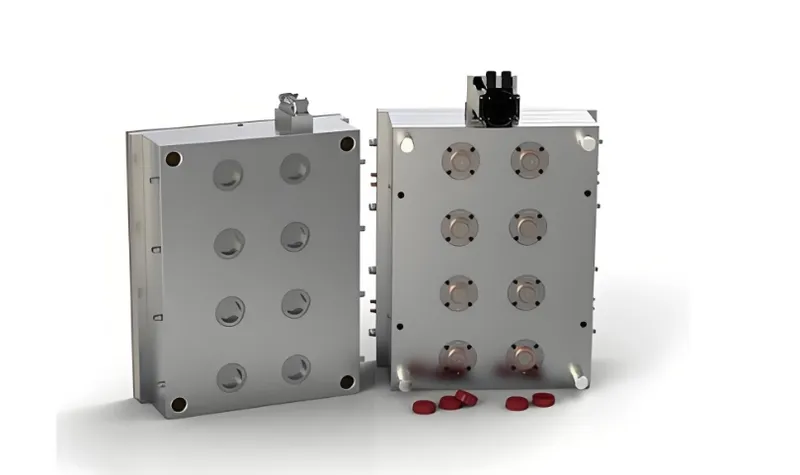
Design Checklist
-
Part Geometry: Ensure the part is simple and flat, avoiding complex features that require multiple gates.
-
Gate Placement6: Align the gate with the parting plane for easy ejection.
-
Draft Angles: Incorporate 1-2° draft angles for smooth part release.
-
Material Selection7: Choose thermoplastics like ABS, PP, or HDPE, considering shrinkage and flow properties.
-
Ejection System: Design an effective ejection system, typically using ejector pins.
Consideration | Importance |
---|---|
Part Geometry | Must be simple for two-plate molds |
Gate Placement | Critical for ejection and flow |
Material | Affects shrinkage and cycle time |
Material selection has no impact on two-plate mold design.False
Different materials have varying shrinkage rates and flow characteristics, which must be accounted for in mold design to ensure part quality.
Conclusion
Two-plate molds are a fundamental tool in injection molding, offering a balance of simplicity, cost-effectiveness, and efficiency for producing a wide range of plastic parts. While they are best suited for simple geometries and high-volume production, their limitations in handling complex parts make it essential to consider project requirements carefully.
By understanding how two-plate molds function, their applications, and how they compare to other mold types, manufacturers can make informed decisions that optimize production and reduce costs.
Two-plate molds are an essential part of the injection molding process, and their role in manufacturing cannot be overstated. Whether you’re producing packaging materials or automotive components, mastering the use of two-plate molds can lead to significant efficiency gains.
-
Learn about injection molding processes and applications to see how they impact various industries and product designs. ↩
-
Discover the diverse applications of plastic parts to appreciate their role in everyday products and industrial uses. ↩
-
Explore the benefits of two-plate molds to understand why they are favored in manufacturing for efficiency and cost-effectiveness. ↩
-
Learn how cost-effective methods can enhance production efficiency and reduce overall manufacturing costs. ↩
-
Discover the key factors that lead to faster cycle times and how they can benefit your production workflow. ↩
-
Discover why gate placement is critical for ejection and flow in Two-Plate Molds, ensuring optimal performance. ↩
-
Learn about the importance of material selection in Two-Plate Molds to enhance part quality and production efficiency. ↩