Gas marks are a prevalent defect in injection molding, manifesting as streaks, burns, or focal points on the surface of molded parts. These defects arise from trapped gases—such as air, water vapor, or decomposition gases—that fail to escape the mold during the injection process. The presence of gas marks1 not only mars the aesthetic quality of the part but can also compromise its structural integrity, making it a critical concern for manufacturers.
In industries where surface finish and part strength are paramount, such as automotive, consumer goods, and medical devices, gas marks can lead to increased production costs due to the need for rework or scrapping of defective parts. Understanding the causes and effects of gas marks is essential for optimizing the injection molding process2 and ensuring high-quality outputs.
Gas marks are a significant defect in injection molding.True
They affect both the appearance and strength of molded parts, leading to potential product failures.
In this article, we will explore the causes of gas marks, their impact on the injection molding process, and effective strategies to mitigate them. We will also examine how gas-assisted injection molding3 compares to traditional methods in addressing these challenges.
- 1. What are Gas Marks in Injection Molding?
- 2. What Causes Gas Marks in Injection Molding?
- 3. How Do Gas Marks Affect the Injection Molding Process?
- 4. What are the Mitigation Strategies for Gas Marks?
- 5. What are the Applications and Industries Affected by Gas Marks?
- 6. How Does Gas-Assisted Injection Molding Compare?
- 7. Conclusion
What are Gas Marks in Injection Molding?
Gas marks are surface defects that occur during the injection molding process when gases become trapped in the mold cavity. These gases can originate from various sources, including air trapped in the mold, moisture in the plastic material, or gases produced by the decomposition of the plastic during heating. As the molten plastic is injected into the mold, these gases are compressed and can create visible streaks or burns on the part’s surface.
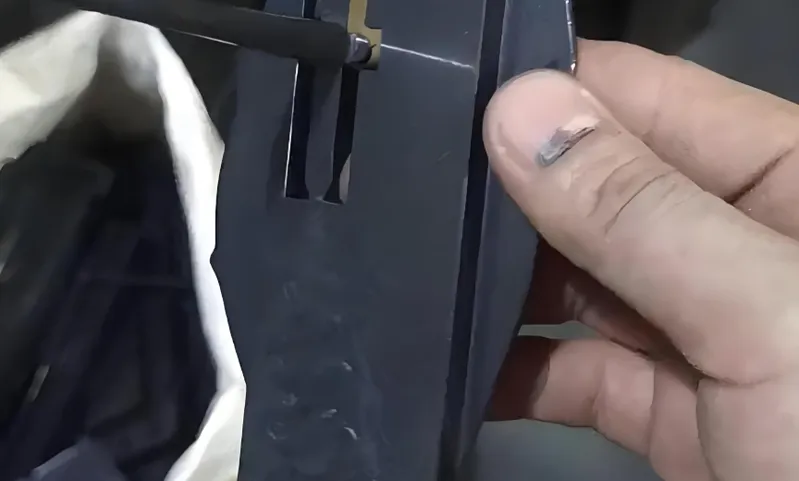
Gas marks are a common defect in injection molding.True
They occur due to trapped gases during the molding process, affecting many industries.
Gas marks are particularly problematic because they not only affect the visual appeal of the part but can also indicate underlying issues in the molding process that may compromise the part’s mechanical properties.
What Causes Gas Marks in Injection Molding?
Several factors can contribute to the formation of gas marks in injection molding. These causes can be categorized based on equipment, mold design4, production processes5, materials, environmental conditions, and melt flow characteristics.
Cause Category | Description | Example Issues |
---|---|---|
Equipment | Mismatch in machine capacity or design | Small nozzle holes, improper screw design |
Mold Exhaust | Poor venting design or maintenance | Clogged vents, misplaced inserts |
Production Process | Incorrect injection parameters | High pressure/speed, low speed causing cooling |
Material-Related | Moisture or thermal decomposition | Wet materials, overheating PC/ABS |
Environmental | External conditions affecting mold | High humidity causing vapor |
Melt Flow | Gas entrapment in melt or mold | Poor gas escape during filling |
Proper mold venting is crucial to prevent gas marks.True
Inadequate venting traps gases, leading to defects.
Each of these categories encompasses specific issues that can lead to gas entrapment. For instance, equipment-related causes might include using a machine with insufficient capacity, while material-related causes could involve using plastics that are not adequately dried.
How Do Gas Marks Affect the Injection Molding Process?
Gas marks have a multifaceted impact on the injection molding process, affecting both the quality of the final product and the efficiency of production.
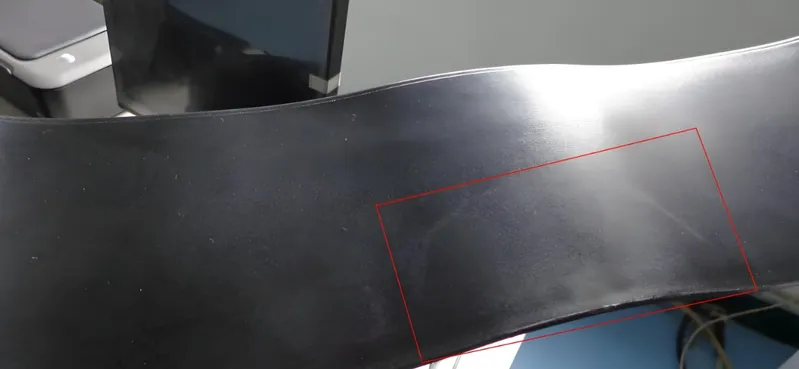
-
Product Quality6: Gas marks7 can weaken the structural integrity of the part, making it more susceptible to failure under stress. Additionally, the visual defects can render the part unsuitable for applications where appearance is critical.
-
Production Efficiency8: The occurrence of gas marks often necessitates adjustments to the molding process, such as modifying injection parameters or improving mold venting. In severe cases, defective parts may need to be reworked or scrapped, leading to increased material waste and production costs.
Gas marks can lead to increased production costs.True
Defective parts may require rework or scrapping, wasting time and materials.
Furthermore, gas marks can be indicative of broader process issues, such as improper material handling or suboptimal machine settings, which can have a cascading effect on overall production quality.
What are the Mitigation Strategies for Gas Marks?
To minimize or eliminate gas marks, manufacturers can employ several strategies focused on improving mold design, optimizing process parameters, and ensuring material quality.
Strategy | Description |
---|---|
Improve Mold Venting9 | Add or clear venting channels to allow gas to escape from the mold cavity. |
Optimize Injection Parameters10 | Adjust injection speed and pressure to prevent gas compression and ensure smooth flow. |
Dry Materials | Remove moisture from plastics before molding to prevent vapor formation. |
Use Gas-Assisted Injection Molding11 | Inject gas to push molten plastic, reducing defects like sink marks and warping. |
Proper process adjustments can minimize gas marks.True
By optimizing venting, injection parameters, and material preparation, manufacturers can reduce the occurrence of gas marks.
These strategies require a thorough understanding of the specific molding setup and the materials being used. For example, moisture-sensitive materials like nylon may require extended drying times, while complex part geometries might necessitate additional venting channels.
What are the Applications and Industries Affected by Gas Marks?
Gas marks are a critical issue in several industries where injection molding is used to produce parts with high aesthetic and functional requirements.
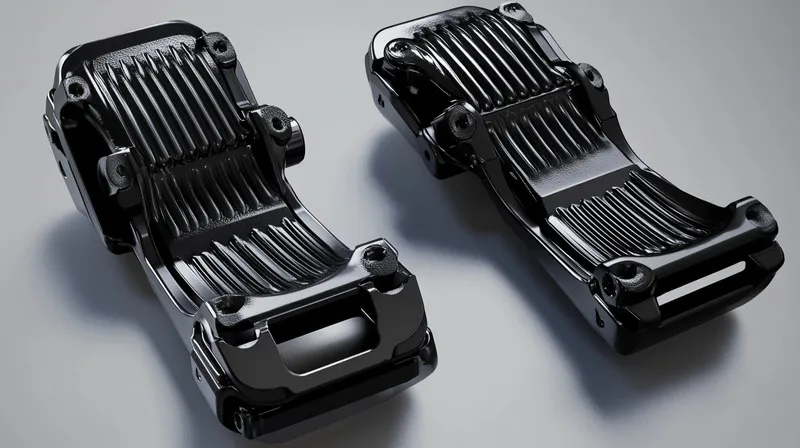
-
Automotive Industry: Components like dashboards and interior panels require flawless surfaces for both aesthetics and durability.
-
Consumer Goods: Electronics casings and household appliances demand high-quality finishes to appeal to consumers.
-
Medical Devices: Parts must meet stringent standards for appearance and strength to ensure safety and functionality.
-
Complex Geometries: Parts with thick sections or intricate designs are particularly prone to gas trapping, increasing the risk of gas marks.
Gas marks are a significant issue in the automotive industry.True
They affect the aesthetic quality of interior components, which is a key selling point.
In these industries, the presence of gas marks can lead to product rejection, increased costs, and potential safety hazards, making their prevention a top priority.
How Does Gas-Assisted Injection Molding Compare?
Gas-assisted injection molding is an alternative technology that can help mitigate some of the issues associated with traditional injection molding, including defects like sink marks and warping. However, its impact on gas marks specifically is less direct.
Technology | Pros | Cons |
---|---|---|
Traditional Injection | Simpler equipment, lower initial costs, suitable for uniform parts | Prone to defects like gas marks, higher material usage, longer cycle times |
Gas-Assisted Injection | Reduces defects like sink marks, saves material, faster cycles, better stability | Higher equipment costs, complex design, limited applicability |
Gas-assisted injection molding can reduce material usage.True
By using gas to hollow out parts, less plastic is needed, reducing costs.
While gas-assisted injection molding offers several advantages, it is not a direct solution for preventing gas marks. Instead, it is more effective for managing other defects and improving part quality in specific applications.
Conclusion
Gas marks are a significant challenge in injection molding, affecting both the quality of the final product and the efficiency of the manufacturing process. By understanding the causes of gas marks and implementing effective mitigation strategies—such as improving mold venting, optimizing injection parameters, and ensuring material dryness—manufacturers can reduce the occurrence of these defects and enhance overall production outcomes.
In industries where precision and appearance are critical, addressing gas marks is essential for maintaining competitiveness and meeting customer expectations. As technology advances, exploring alternative methods like gas-assisted injection molding may offer additional benefits, though it is not a panacea for all molding defects.
-
Understanding gas marks is crucial for manufacturers to improve product quality and reduce costs associated with defects. ↩
-
Optimizing the injection molding process can significantly enhance product quality and reduce waste, making it essential for manufacturers. ↩
-
Discover the benefits of gas-assisted injection molding and how it can enhance production efficiency and quality. ↩
-
Exploring mold design impacts can lead to better designs and fewer defects in production. ↩
-
Learning about best practices in production processes can enhance overall manufacturing effectiveness. ↩
-
Exploring this topic can help manufacturers enhance their product quality and reduce defects caused by gas marks. ↩
-
Understanding gas marks is crucial for improving product quality and production efficiency in injection molding processes. ↩
-
Learning about strategies to enhance production efficiency can lead to cost savings and better resource management in manufacturing. ↩
-
Explore this link to learn effective techniques for enhancing mold venting, which can significantly reduce gas marks in production. ↩
-
Discover how adjusting injection parameters can lead to smoother flows and fewer defects, improving overall product quality. ↩
-
Find out how gas-assisted injection molding can minimize defects like sink marks and warping, enhancing the final product’s integrity.on defects, improving efficiency and product quality. ↩