Ever wondered how to make your injection molding process both cost-effective and efficient? Family molds might be your answer!
Family molds offer a cost-effective way to produce multiple different parts in a single cycle of injection molding. By enhancing efficiency and cutting down production costs, they are perfect for projects needing various components with unique designs.
Reflecting on my early days in mold design, I remember the constant struggle with balancing cost and efficiency. That’s when I stumbled upon the concept of family molds, which felt like uncovering a hidden gem. Not only did they simplify production by allowing me to mold multiple parts in one go, but they also slashed the costs significantly. Whether you’re designing intricate components for consumer electronics or working on a new product line, the advantages of family molds are worth considering. They don’t just save money; they streamline operations, making them an invaluable asset in the competitive world of manufacturing. Dive deeper into how these molds can transform your production line with practical insights and real-world applications.
Family molds reduce production costs by 50%.False
Family molds reduce costs but not specifically by 50% universally.
Family molds can produce multiple parts in one cycle.True
Family molds are designed to create various parts simultaneously.
- 1. What Are Family Molds and How Do They Work?
- 2. How Do Family Molds Compare to Traditional Molds?
- 3. How Can Family Molds Save You Money?
- 4. How Can Family Molds Boost Production Efficiency?
- 5. What Challenges Might Arise with Family Molds?
- 6. Are Family Molds Suitable for Your Manufacturing Needs?
- 7. Conclusion
What Are Family Molds and How Do They Work?
Imagine crafting several puzzle pieces at once, each fitting together perfectly—this is the magic of family molds.
Family molds are injection molds designed to produce multiple, distinct parts in one cycle, optimizing efficiency and reducing costs in manufacturing processes.
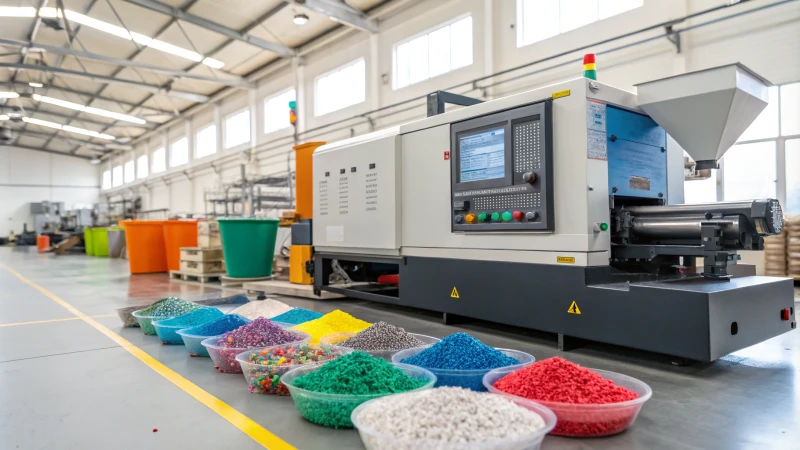
Understanding Family Molds
When I first heard about family molds, it felt like discovering a hidden gem in the world of manufacturing. Picture a single mold housing several cavities, each diligently working to produce a different part simultaneously. Unlike multi-cavity molds1 that churn out identical parts, family molds are like a Swiss Army knife for industries needing diverse components, such as consumer electronics. Imagine designing the casing, buttons, and internal components of a gadget all in one go!
How Family Molds Work
Here’s where the magic happens. You inject molten material into these precisely crafted cavities, each tailored to form a unique piece. The process might sound complex, but it’s quite fascinating—like orchestrating a well-tuned symphony where each instrument plays its part. Once the parts cool down, the mold opens up to reveal a set of finished components. It’s crucial to get this synchronization spot on to maintain high-quality standards.
Advantages of Family Molds
- Cost Efficiency: By making multiple parts at once, you cut down production time and labor expenses—a huge plus when you’re managing a budget.
- Material Savings: It’s like baking the perfect batch of cookies with just the right amount of dough, ensuring no waste.
- Reduced Setup Time: With fewer mold changes needed, you minimize those dreaded downtimes.
- Versatility: Perfect for projects requiring varied parts, like electronic casings and buttons.
Feature | Family Molds | Multi-Cavity Molds |
---|---|---|
Parts Produced | Different parts per cycle | Identical parts per cycle |
Efficiency | High due to varied output | High for mass production |
Material Waste | Reduced | Potentially more waste |
Challenges with Family Molds
Of course, it’s not all smooth sailing. Designing family molds demands precision akin to a watchmaker’s attention to detail. Balancing production can be tricky since each part might have different cooling or ejection needs—it’s like juggling flaming torches while walking a tightrope. And let’s not forget the initial tooling costs can give you sticker shock, but the savings over time make it worthwhile.
Applications of Family Molds
Beyond electronics, family molds stretch their utility to automotive industries—think dashboards composed of various distinct elements. They’re also gaining traction in consumer goods manufacturing2, crafting everything from multi-part toys to kitchen tools.
Understanding how family molds operate can significantly boost efficiency and productivity in manufacturing settings. With well-thought-out designs and applications, these molds can lead to substantial savings and streamlined production cycles. Exploring real-world case studies can offer deeper insights into their effectiveness across diverse industries.
For those keen on staying ahead in this fast-paced market, investigating how top companies optimize their family mold designs is a must. It’s a treasure trove of knowledge about future trends and innovations in injection molding technology.
Discover more about how companies innovate using family molds3 to maintain their edge in the industry.
Family molds produce identical parts per cycle.False
Family molds produce different parts per cycle, unlike multi-cavity molds.
Family molds reduce material waste in production.True
Optimized material use in family molds lowers waste compared to other methods.
How Do Family Molds Compare to Traditional Molds?
Ever wondered how to choose the best mold for your project? Let’s dive into the fascinating world of family molds versus traditional molds.
Family molds, unlike traditional multi-cavity molds, produce different parts in a single cycle. They’re perfect for creating varied components with similar production needs, making them efficient and cost-effective.
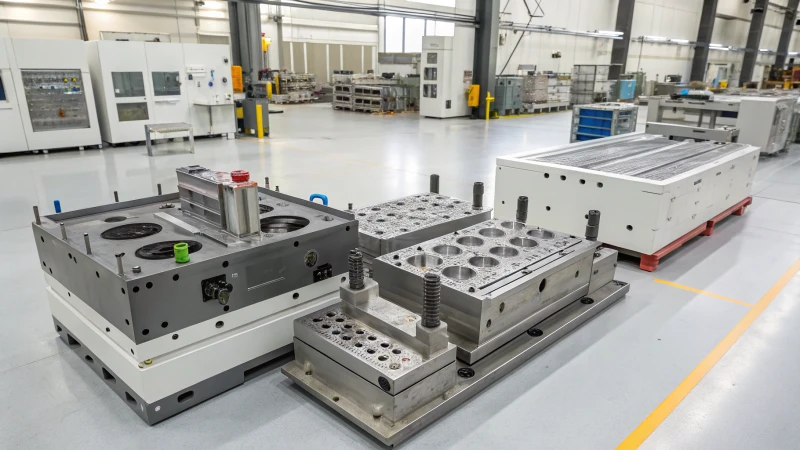
Understanding Family Molds
I’ve always been fascinated by the ingenuity behind family molds. Imagine you’re working on a project that requires multiple distinct parts, like assembling a toy with different colored pieces or an intricate electronic device. Family molds come to the rescue by allowing all these different parts to be produced simultaneously. They shine in industries where assembling different components into a single product is key, such as electronics. It’s like having a Swiss Army knife in your production line—versatile and efficient.
Traditional Mold Overview
On the flip side, traditional molds are like your trusty old hammer, steadfast and reliable for specific tasks. These molds create identical parts in each cycle, making them ideal for large-scale production where consistency is king. I remember working on a project with these molds for automotive components, where speed and uniformity were crucial. Traditional molds excel in environments that demand high-volume output of single components, like bottle caps or car parts.
Efficiency and Cost Considerations
Aspect | Family Molds | Traditional Molds |
---|---|---|
Production Speed | Moderate – Multiple components in one cycle | High – Identical parts produced quickly |
Cost-Effectiveness | Cost-effective for varied low-to-medium volume | More efficient for high-volume single component |
Tooling Complexity | More complex due to varied cavity design | Less complex with uniform cavities |
Family molds can be a game-changer when you need to cut down on tooling costs and lead times for projects involving multiple components. However, I have also found that designing these molds requires a keen eye for detail to ensure materials flow evenly across different cavities.
Suitability for Applications
Family molds are particularly suited for creating products that demand various types of components simultaneously, like toys or home appliances. In contrast, traditional molds are your go-to choice when the goal is to churn out large quantities of the same part efficiently—think of them as the bread and butter of industries like packaging and automotive.
Challenges and Limitations
Despite their versatility, family molds can sometimes be tricky. Balancing mold fill time across different cavities can lead to inefficiencies if not managed well. However, traditional molds, with their focus on single-part production, offer streamlined processes that are hard to beat when it comes to repeatability and precision.
Understanding these differences has often helped me make informed decisions tailored to specific production goals4 and product types. Each mold type brings its own set of advantages and challenges, making the selection process both critical and exciting in the world of manufacturing.
Family molds are less complex than traditional molds.False
Family molds are more complex due to varied cavity designs.
Traditional molds are ideal for high-volume single parts.True
They produce identical parts quickly, perfect for high-volume needs.
How Can Family Molds Save You Money?
Ever wondered how to cut costs while boosting production efficiency? Let’s dive into the world of family molds and uncover some impressive benefits.
Family molds offer cost advantages by producing multiple parts in one cycle, reducing setup time and material waste, which leads to significant savings in manufacturing and operational expenses.
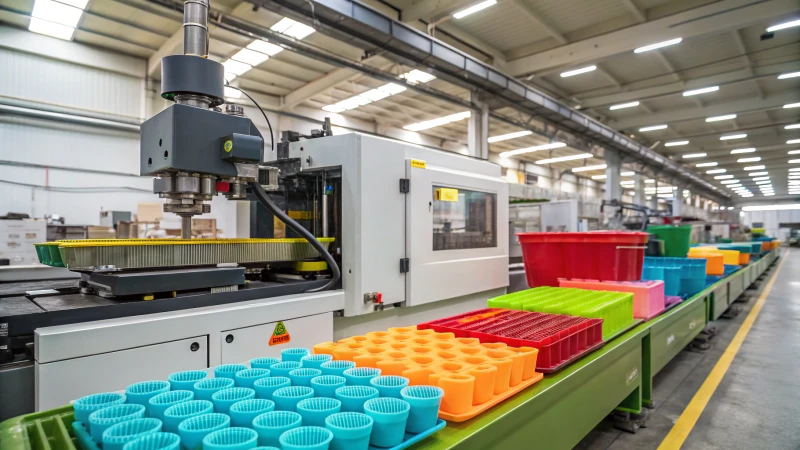
Understanding Family Molds
Imagine being able to produce a whole set of different parts at once, like baking an entire batch of cookies rather than one at a time. Family molds do just that! They’re designed to craft two or more different pieces in a single go, particularly when these parts share similar material needs and production volumes. I remember my first encounter with family molds; it was like discovering a secret recipe that shaved hours off my work week.
Cost Efficiency Through Reduced Setup Times
Setting up a new mold feels like setting up camp — it takes time, effort, and resources. Every setup has costs tied to labor and machine downtime. Family molds help minimize these occurrences, akin to packing all your camping gear into one efficient bag. This means smoother, more continuous production flows, leading to lower operational expenses. It’s like having a magic wand that keeps everything moving seamlessly.
Type of Mold | Setup Time | Efficiency |
---|---|---|
Single Cavity | High | Low |
Family Mold | Low | High |
Material Waste Reduction
If you’ve ever felt the sting of tossing out good material, you’ll appreciate how family molds work. They use shared runners and gates, which ensures more material goes into products instead of the trash. This not only cuts material costs but also aligns with sustainability goals — something close to my heart as I strive to leave a smaller carbon footprint.
Streamlining Production Processes
Integrating family molds into production lines is like tidying up a cluttered desk; suddenly, everything becomes more straightforward. With fewer molds to juggle, scheduling and inventory control become simpler. This streamlining boosts efficiency and reduces the chance of errors — a lifesaver in my hectic production schedule.
Practical Application Scenarios
Picture a company needing to churn out diverse plastic components5 for electronics. With a family mold, all parts get made simultaneously, slashing both time and costs. I recall one project where switching to family molds felt like moving from dial-up to high-speed internet — everything just clicked faster.
Family molds shine brightest in industries requiring large volumes of varied yet related components, like automotive, consumer goods, and electronics. For more insights on optimizing production with family molds6, delve into case studies that reveal real-world applications and outcomes. These stories offer a glimpse into how others have harnessed the power of family molds to achieve remarkable results.
Family molds reduce setup time costs significantly.True
Family molds consolidate production, minimizing the frequency of costly setup processes.
Family molds increase material waste in production.False
They reduce waste by sharing runners and gates, optimizing material usage.
How Can Family Molds Boost Production Efficiency?
Let me take you on a journey into the world of family molds and how they might just be the secret to skyrocketing your production efficiency.
Family molds boost production efficiency by allowing multiple parts to be created in a single cycle, cutting down setup times, and reducing material waste. They’re perfect for parts that have similar design and material needs.
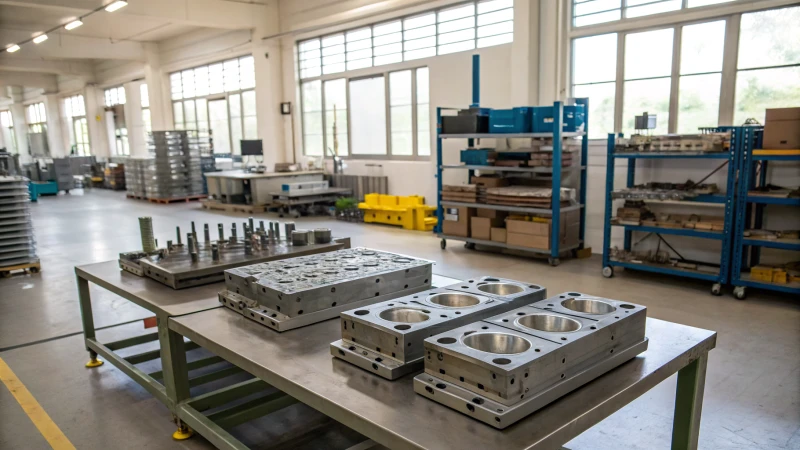
Understanding Family Molds
Imagine walking into a workshop and seeing a mold that can produce different parts of a product all at once—pretty cool, right? That’s the magic of family molds. They come equipped with cavities for various parts of a product family, helping manufacturers like us produce multiple components in one go. I remember the first time I saw one in action; it was like watching a well-choreographed dance, with every piece falling perfectly into place.
Family molds, a type of injection mold, contain cavities for different parts of the same product family. This allows manufacturers to produce multiple parts in one shot, enhancing production efficiency7. The key advantage is the ability to streamline the manufacturing process, as it eliminates the need for separate setups for each part.
Benefits of Family Molds
-
Cost Savings: I’ve seen firsthand how producing multiple parts simultaneously can cut down on labor and machine costs. It’s like buying in bulk—more bang for your buck! By producing multiple parts simultaneously, family molds can significantly reduce labor and machine costs. This efficiency results from minimizing idle time between setups and consolidating material usage.
-
Reduced Setup Time: One of my favorite perks is less time spent on setups. Imagine how much more we can accomplish when we don’t have to pause every few hours to change molds. A major advantage of using family molds is the reduction in setup times. With a single mold capable of producing various components, manufacturers can avoid frequent mold changes, boosting overall productivity.
-
Material Optimization: These molds are pros at minimizing waste, which makes production not just efficient but also eco-friendly—a win-win! Family molds help in minimizing material waste by optimizing the flow and distribution of plastic within the mold. This leads to more sustainable production processes and cost reductions.
Feature | Benefit |
---|---|
Multi-part Cycle | Reduced time and labor costs |
Single Setup | Minimizes machine downtime |
Material Flow | Decreases waste and enhances quality |
Challenges and Considerations
While the benefits are plenty, family molds aren’t without their quirks. Ensuring each part meets quality standards can be tricky. I once faced a challenge where balancing injection speed and pressure became a game of precision to avoid defects—think of it like juggling with different weights.
Ensuring uniform quality across different parts can be difficult. Manufacturers must carefully design these molds to account for variations in part size, weight, and material properties.
Moreover, balancing the injection speed and pressure for different cavity sizes is crucial to avoid defects. For example, an imbalance might lead to overfilling one cavity while underfilling another.
Comparative Analysis with Multi-Cavity Molds
Multi-cavity molds stick to making identical parts each time, which is fantastic for high-volume production but lacks the adaptability of family molds. It’s like choosing between a one-size-fits-all outfit versus a custom-tailored suit.
In contrast, multi-cavity molds produce identical parts in each cycle. While they excel in high-volume production of single parts, they lack the versatility of family molds for complex assemblies.
To decide which type is more suitable, manufacturers should evaluate factors such as production volume, part complexity, and cost constraints. Analyzing these elements can guide whether family molds are the right choice for their manufacturing strategy.
For further insights on how family molds compare with other mold types explore industry best practices8 that can guide decision-making.
Real-World Applications
In industries like automotive and electronics, family molds are game-changers. I’ve read about companies that have leveraged these molds to ramp up efficiency while keeping costs in check.
Many industries have successfully implemented family molds to boost production efficiency. Automotive and consumer electronics sectors frequently use them due to their capability to produce complex assemblies quickly and cost-effectively.
Review case studies of companies that have benefited from family molds gaining insights into their implementation strategies and outcomes.This approach9 can help you understand potential impacts on production and how to mitigate common challenges in your projects.
Consider tapping into these strategies as you shape your manufacturing approach aiming for optimal efficiency and quality across your product line.
Family molds reduce machine downtime.True
Family molds require a single setup for multiple parts, reducing downtime.
Multi-cavity molds are ideal for complex assemblies.False
Family molds, not multi-cavity molds, are suited for complex assemblies.
What Challenges Might Arise with Family Molds?
Ever tried fitting a square peg into a round hole? That’s how it feels working with family molds sometimes. Join me as I dive into the complexities of these multi-part molds, revealing the behind-the-scenes challenges we face in keeping production smooth.
Family molds can lead to uneven cooling, material waste, and increased design complexity. Tackling these issues requires meticulous planning and expertise in mold design, ensuring quality and efficiency are maintained.
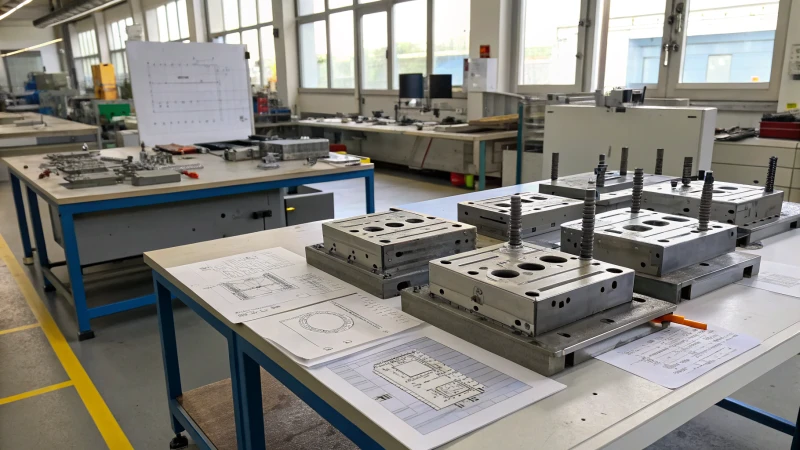
Uneven Cooling and Its Impact
I remember my first project with family molds like it was yesterday. It felt like juggling flaming torches while balancing on a unicycle. The biggest hurdle? Uneven cooling. When you’ve got parts of different shapes and sizes, keeping them cool at the same rate can be like trying to get my kids to eat their veggies—next to impossible. If one part shrinks or warps, it can throw everything out of whack.
- Solution: Over the years, I’ve learned that designing with uniform wall thickness or using advanced cooling techniques can help even things out.
Material Waste Concerns
Early on, I realized that using a shared runner system for different parts was akin to pouring too much syrup on pancakes—wasteful and messy. It quickly became clear that without careful management, material waste could skyrocket, not to mention the inconsistency in part quality.
Issue | Impact | Solution |
---|---|---|
Uneven Material Flow | Part Defects | Optimize Runner Design |
Excessive Waste | Cost Increase | Efficient Gate Balancing |
Increased Complexity in Design
Every time I start designing a family mold, it’s like assembling a jigsaw puzzle where the pieces have to fit perfectly, or they just don’t work. The parts must align just right within the mold to avoid any production hiccups. This adds layers of complexity that can stretch timelines and budgets.
Maintenance and Repair Challenges
The intricate designs of family molds remind me of my grandfather’s old clock—beautiful but complicated. If one component fails, it can bring the whole operation to a halt, just like when that clock stopped ticking.
- Solution: Now, I always ensure regular maintenance and invest in top-notch materials to keep things running smoothly.
Conclusion
By understanding these challenges, I’ve been able to innovate solutions that maintain the efficiency of family molds without sacrificing product quality. It’s all about strategic planning and learning from every hurdle we encounter. If you’re interested in more insights on mold challenges10, there’s plenty more to explore.
Uneven cooling leads to warping in family molds.True
Different shapes in family molds cause uneven cooling, leading to warping.
Family molds reduce material waste significantly.False
Shared runner systems in family molds can increase material waste.
Are Family Molds Suitable for Your Manufacturing Needs?
Considering family molds for your next project? Let’s dive into whether they truly fit your manufacturing puzzle.
Family molds are ideal when you need to produce different parts from similar materials all at once. They offer cost and time savings but can complicate quality control and material usage.
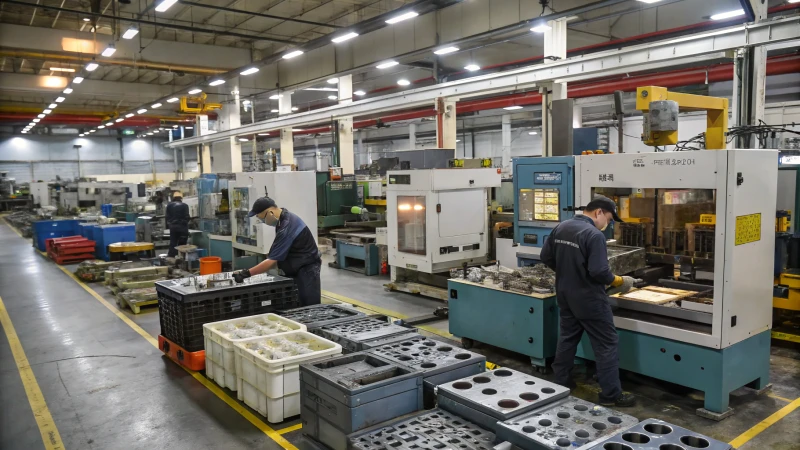
Understanding Family Molds
Let me take you back to a moment in my career when I was knee-deep in designing molds for a new line of electronics. Picture this: I’m at my desk, surrounded by blueprints and coffee cups, trying to figure out how to streamline our production process. That’s when I stumbled upon family molds. These ingenious designs allow multiple parts to be made in one go, each cavity shaping a different component. It’s perfect for items sharing the same material, like when I was tasked with creating various components for a smartphone.
Family molds allow the production of multiple parts in a single molding cycle, with each cavity dedicated to a different component. This type of mold design11 is ideal for products made from the same material.
Pros | Cons |
---|---|
Cost-efficient | Quality control issues |
Reduced cycle times | Material waste |
Ideal for small runs | Complex setup and maintenance |
Pros and Cons
Advantages: I found that family molds drastically cut costs by consolidating production cycles. This means fewer trips to the factory floor, shorter production timelines, and lower material expenses. It felt like hitting the jackpot every time I saw those numbers drop on our budget sheets.
Disadvantages: But not everything was smooth sailing. Ensuring each part maintained consistent quality, especially when they varied in size or shape, was like juggling flaming torches. Also, maximizing material efficiency proved to be a challenge, akin to solving a complex puzzle.
Applications and Examples
Imagine you’re designing components for consumer electronics, much like I did with phone cases, buttons, and clips. Family molds can work wonders here by producing all these parts simultaneously, provided they share similar materials.
Consider family molds if your products, like consumer electronics parts12, share similar materials. For example, a mobile phone case manufacturer might use family molds to produce buttons, cases, and clips simultaneously.
However, if your project involves different materials or requires post-processing, family molds might not be your best bet. I’ve learned this the hard way when unexpected complexities in setup led to frustrating downtime.
Alternatives to Consider
When family molds don’t quite fit the bill, consider alternatives like multi-cavity molds13. These specialize in creating identical parts with uniform quality, reducing complexity in production cycles. Evaluating your specific needs will guide you to the mold type that best aligns with your manufacturing aspirations. I’ve always found that taking the time to assess options upfront saves countless hours of rework later.
Family molds reduce production cycle times.True
Family molds produce multiple parts simultaneously, decreasing cycle time.
Family molds are ideal for large production runs.False
They are better for small runs due to setup complexity and maintenance.
Conclusion
Family molds enhance injection molding efficiency by producing multiple distinct parts simultaneously, reducing costs and setup times, while also minimizing material waste in manufacturing processes.
-
Discover the key differences between these two mold types to better understand their applications and benefits. ↩
-
Explore how family molds are used in making diverse consumer products efficiently. ↩
-
Learn how top companies leverage family mold designs to enhance competitiveness and efficiency. ↩
-
Discover factors influencing the choice between mold types. ↩
-
Explore how different companies effectively utilize family molds to produce various electronic parts efficiently. ↩
-
Discover detailed examples of how family molds optimize production, featuring case studies from leading manufacturers. ↩
-
This link provides an in-depth understanding of how family molds streamline manufacturing processes. ↩
-
Explore detailed comparisons between family and multi-cavity molds to better understand their respective benefits. ↩
-
Discover real-world examples of successful implementations of family molds across various industries. ↩
-
Explore a comprehensive guide on addressing typical mold-related issues to enhance manufacturing outcomes. ↩
-
Understanding mold design helps you comprehend how family molds work. ↩
-
Knowing typical consumer electronics parts aids in visualizing applications of family molds. ↩
-
Learning about multi-cavity molds provides alternative solutions to family molds. ↩