Do you wonder about the energy efficiency of extrusion compared to injection molding? I want to tell you what I know from my time in the manufacturing industry.
Extrusion is generally more energy-efficient than injection molding due to its continuous process and lower operating pressures, making it ideal for simple, high-volume products like pipes and sheets.
My journey through the complex world of manufacturing often leads me to think about energy use in extrusion and injection molding. Extrusion probably uses energy more steadily because it runs continuously. Injection molding really feels like a rollercoaster. Its energy needs go up and down with each cycle. These differences are not just theories. They directly affect our production decisions. These choices impact our sustainability goals too.
Extrusion is generally more energy efficient than injection molding.True
Extrusion shows stable energy consumption due to continuous production, unlike the variable demands of injection molding.
Injection molding has lower energy consumption than extrusion.False
Injection molding's cyclical process leads to variable energy demands, making it less efficient compared to extrusion.
- 1. How do extrusion and injection molding differ in energy consumption?
- 2. How do heating processes impact energy efficiency in manufacturing methods?
- 3. How Does Energy Consumption Affect Production Costs?
- 4. How can manufacturers optimize energy use in extrusion and injection molding processes?
- 5. Conclusion
How do extrusion and injection molding differ in energy consumption?
Exploring extrusion and injection molding might feel like walking on a thin rope. Energy use in these areas is very important. It is not just about complex words or technical language. Decisions in this field probably save money. These choices also really cut down on waste during production.
The main differences between extrusion and injection molding in using energy involve heating stability, production cycles and waste creation. Extrusion usually uses less energy. It provides really stable heating power. Lower overall energy costs usually result from this compared to injection molding. Injection molding involves changing cycles and more waste.
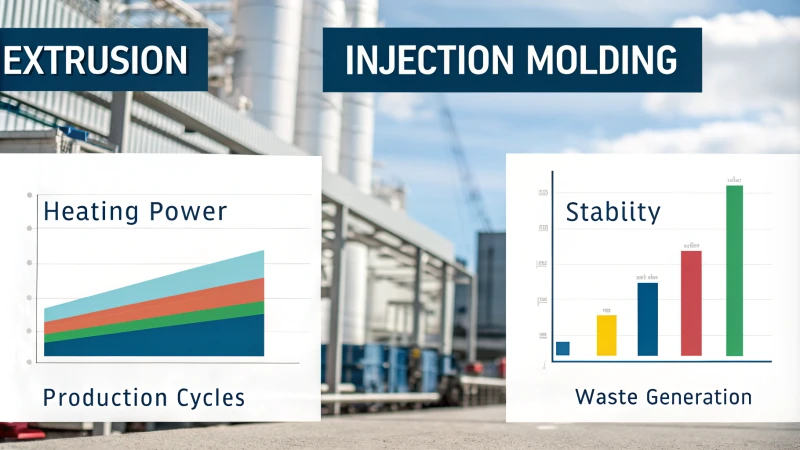
Energy Consumption Characteristics of Extrusion Molding
Extrusion molding uses a lot of energy for heating. Machines heat the barrel to melt plastic materials. Small machines use around 3 kW, while large industrial machines may need as much as 50 kW. Once the plastic is warm, the system maintains the temperature, mainly replacing any lost heat. This process runs very efficiently.
Power Requirements
- Heating Power: Typically ranges from a few kW to tens of kW.
- Motor Power: Generally falls between 7-15 kW for motors in standard pipe extruders.
Energy use stays stable if the screw speed does not change. Everything operates smoothly this way.
Energy Consumption Characteristics of Injection Molding
Injection molding has unpredictable energy use. Like extrusion, it needs varying heating power from several kW to tens of kW. The injection process constantly alters barrel temperature during cycles, making energy use erratic. Once, I saw our energy bills soar during production due to adjusting temperatures causing these ups and downs.
Key Aspects
- Injection Process: Requires high pressure, up to 200 MPa, leading to big energy needs.
- Clamping Force: Needs power from tens to thousands of tons.
This cyclical nature results in noticeable peaks and troughs in energy usage, particularly during injection and mold opening stages.
Comparison of Energy Usage Over Time
Process Type | Energy Stability | Typical Power Consumption | Energy Utilization Rate |
---|---|---|---|
Extrusion Molding | Continuous and stable | 3-50 kW (Heating), 7-15 kW (Motor) | High due to continuous flow |
Injection Molding | Cyclical with peaks | Several kW (Heating), significant for injection and clamping | Lower due to waste production |
Experience shows average energy use per time unit favors extrusion as it maintains a steady flow. Injection molding has energy spikes that increase costs.
Waste and Energy Efficiency
Another big difference is energy efficiency. Extrusion minimizes waste by producing continuous products, enhancing energy efficiency. Injection molding creates waste like gates and runners each cycle, raising total energy consumption. I often wish to get rid of those waste parts!
Frequent temperature changes in injection molding reduce its energy efficiency; each change feels like a mini rollercoaster—one I don’t enjoy!
Overall, understanding these differences helps me choose better energy-saving practices. Anyone keen to explore energy use optimization should look into energy efficiency in manufacturing1. Knowing these details helps save money and benefits the environment.
Extrusion molding has lower average energy consumption than injection molding.True
Extrusion molding maintains a steady energy output, making it more energy-efficient compared to the cyclical peaks of injection molding.
Injection molding requires higher instantaneous power than extrusion molding.True
The need for high pressure during injection cycles increases the energy demands of injection molding compared to extrusion processes.
How do heating processes impact energy efficiency in manufacturing methods?
Have you ever thought about how heating materials in factories affects energy use? It is an interesting path through extrusion and injection molding. I am very eager to explore this topic with you.
Heating processes strongly affect energy efficiency in manufacturing by changing power use in processes like extrusion and injection molding. Extrusion uses stable energy, while injection uses varying energy due to its operation style. Grasping this concept allows manufacturers to improve processes and cut costs.
Understanding Heating in Manufacturing
Heating is very important for energy efficiency in methods like extrusion and injection molding. Each method uses different heating ways that affect energy use and how well the process works.
Energy Use in Extrusion Molding
In extrusion molding, heating melts the plastic raw materials with electric or oil heating. Different extruder types need different heating levels.
Extrusion is a continuous process where, once the correct temperature is reached, energy usage stays stable during production. This stability comes because energy is only compensating for heat loss.
Power Use in Extrusion Molding
Extrusion molding requires significant power to move material through the barrel using a screw. As long as screw speed stays the same, power usage remains constant. This consistency is really attractive in times of uncertainty.
Energy Use in Injection Molding
Injection molding is a complex process. It also melts plastic raw materials, but the intermittent operation requires constant temperature adjustments. This leads to unpredictable energy use.
Heating Power: Similar to extrusion but varies due to cycles.
Power Need: High pressure is needed during injection, causing sudden energy peaks.
Watching an injection molding machine shows peaks during injection and mold stages. Energy management is crucial in injection molding compared to extrusion.
Comparing Energy Efficiency: Extrusion vs Injection Molding
Examining energy use per time unit, extrusion stands out. Its continuous method results in stable energy use. Injection molding’s cycles create peaks.
Producing similar plastic products highlights the difference. Injection uses a lot of energy in short bursts, while extrusion remains steady.
Extrusion continuously melts and moves materials, maximizing energy use. Injection molding’s waste from gates and runners worsens its energy efficiency.
Understanding these heating processes and their impact on energy efficiency is vital for manufacturers aiming to optimize production and minimize costs. Techniques such as energy recovery or new heating solutions can truly improve operational performance in these settings.
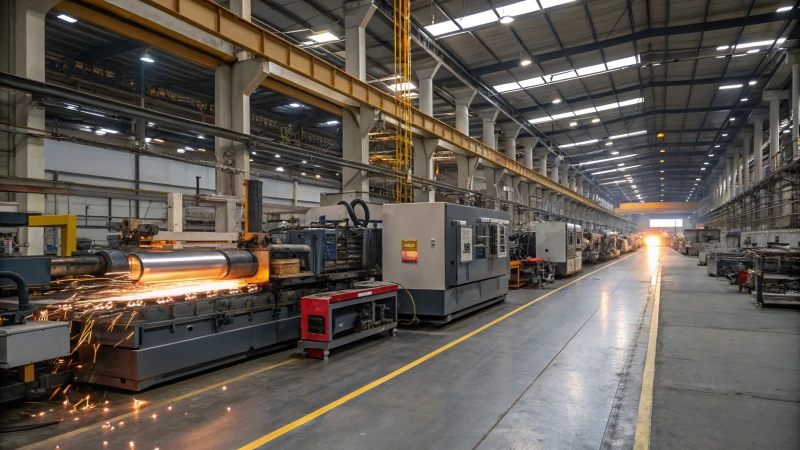
Understanding Heating Processes in Manufacturing
Heating processes have a big impact on energy efficiency in manufacturing methods like extrusion and injection molding. I still recall my first deep dive into these ideas. It was really eye-opening to see how various techniques shape not only production but also the environment where we work. These processes differ in important ways. Understanding these differences affects energy consumption.
Energy Consumption Characteristics of Extrusion Molding
In extrusion molding, the heating process is primarily focused on melting plastic raw materials, utilizing either electric or oil heating. The heating power varies significantly based on the extruder type:
Extruder Type | Heating Power (kW) |
---|---|
Small Experimental Extruder | 3-5 kW |
Large Industrial Production | 30-50 kW |
Once the material reaches the required temperature, energy consumption stabilizes during continuous production stages. This is crucial as it means that the power consumption primarily compensates for heat loss rather than fluctuating with production rates.
Power Consumption in Extrusion Molding
Alongside heating, extrusion molding requires substantial power to drive the screw, which moves the material through the barrel. Typical power ratings for screw drive motors are:
Screw Drive Motor Power (kW) | Typical Applications |
---|---|
7-15 kW | Ordinary Plastic Pipe Extruders |
Here, the power consumption remains relatively constant if the screw speed does not change, leading to predictable energy usage in continuous processes.
Energy Consumption Characteristics of Injection Molding
Conversely, injection molding’s heating process involves more complexity due to its intermittent production cycles. The barrel temperature must be adjusted frequently, impacting energy stability:
- Heating Power: Similar to extrusion, but fluctuating due to cycle requirements.
- Power Demand: High pressure is necessary during injection, leading to peak energy demands. For instance:
Injection Pressure (MPa) | Power Consumption |
---|---|
100-200 MPa | Significant for injection and clamping systems |
This leads to noticeable peaks in energy consumption, particularly during injection and mold opening/closing stages, making energy management more complex compared to extrusion molding.
Comparative Energy Efficiency: Extrusion vs Injection Molding
When analyzing energy consumption per unit time, extrusion molding stands out due to its continuous production method. In contrast, injection molding experiences peaks during operational cycles:
Method | Energy Utilization Rate | Comments |
---|---|---|
Extrusion Molding | Generally higher | Continuous and stable operation |
Injection Molding | Lower | Waste generation and cyclical peaks |
For example, when producing similar quality plastic products, injection molding’s energy consumption may spike during short cycles while extrusion maintains a steady rate.
Additionally, while extrusion maximizes energy utilization by continuously melting and transporting materials, injection molding incurs waste in the form of gates and runners, further complicating its energy efficiency profile.
Understanding these heating processes and their implications on energy efficiency is vital for manufacturers looking to optimize production while minimizing costs. Exploring techniques such as energy recovery2 or innovative heating solutions3 can further enhance operational effectiveness in these manufacturing settings.
Extrusion molding has stable energy consumption during production.True
Extrusion molding maintains consistent energy usage as it compensates for heat loss, unlike injection molding's fluctuating power demands.
Injection molding is more energy efficient than extrusion molding.False
Injection molding experiences peaks in energy consumption, making it less efficient compared to the steady energy use of extrusion molding.
How Does Energy Consumption Affect Production Costs?
Do you ever stop to consider the large amount of energy used in manufacturing? This energy use greatly impacts production costs. It influences budgeting and affects sustainability practices. The relationship is really complex. Let’s look closer at this interesting topic.
Energy consumption strongly impacts production costs. It affects cost efficiency, operational stability and environmental impact. Different processes, such as extrusion and injection molding, have unique energy needs. These variations in energy use can cause large changes in overall expenses.
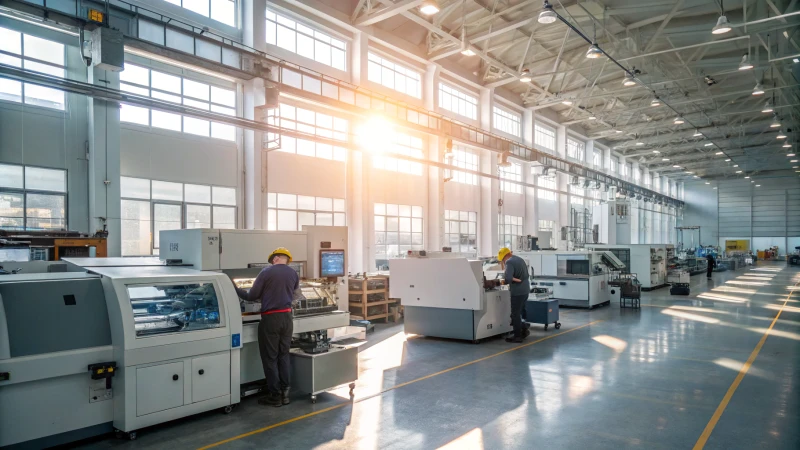
Understanding Energy Consumption in Production
Energy consumption plays a critical role in determining the overall production costs across various manufacturing processes. The implications of energy usage can be divided into key areas: cost efficiency, production stability, and environmental impact.
Cost Efficiency
Energy costs contribute significantly to the total production expenses. In processes like extrusion molding, energy is primarily consumed during the heating phase of the barrel. Typically, the heating power for an extruder ranges from 3-50kW, depending on the size and type of the equipment. The stable power consumption during the production stage can lead to predictable cost structures, allowing manufacturers to budget effectively.
Process Type | Typical Heating Power (kW) | Stability of Power Consumption |
---|---|---|
Extrusion Molding | 3 – 50 | Stable |
Injection Molding | 5 – 40 | Cyclical |
In contrast, injection molding involves intermittent energy consumption. The barrel must frequently adjust its temperature during cycles, which can lead to spikes in energy costs at various stages of the injection process. The injection and clamping systems require high energy, especially when applying pressures between 100-200MPa. This cyclical nature can make budgeting more complex and unpredictable, affecting overall cost efficiency.
Production Stability and Efficiency
The stability of energy consumption in extrusion molding means manufacturers can expect a consistent energy expense over time. This is especially beneficial in high-volume production settings where maintaining a steady output is crucial. For instance, while producing plastic products, extrusion molding’s continuous operation often results in lower average energy consumption compared to injection molding for similar outputs.
On the other hand, injection molding’s peaks in energy use during mold cycles can lead to inefficiencies. Manufacturers must account for these fluctuations in their production planning and operational strategies to minimize costs. By implementing energy-efficient practices, manufacturers can mitigate these spikes. For more insights on enhancing production efficiency, check out energy optimization strategies4.
Environmental Considerations
Beyond immediate financial implications, energy consumption has broader environmental impacts that can indirectly influence production costs. Higher energy consumption often correlates with increased carbon emissions, which can lead to regulatory costs and pressures for companies to adopt sustainable practices.
For example, extrusion molding typically has a higher energy utilization rate because it maintains constant production without significant waste material. In contrast, injection molding generates scrap materials such as gates and runners during each cycle, which not only increases waste but also affects overall energy utilization rates. This discrepancy underscores the importance of evaluating both production methods and energy strategies in the context of sustainability.
To explore how energy consumption influences long-term sustainability practices, see sustainable manufacturing practices5.
Extrusion molding has more stable energy costs than injection molding.True
Extrusion molding's consistent energy consumption leads to predictable production costs, unlike the cyclical nature of injection molding that causes fluctuations.
Higher energy consumption always leads to lower production efficiency.False
While higher energy use can indicate inefficiencies, it depends on the process; extrusion may utilize energy better than injection despite higher usage.
How can manufacturers optimize energy use in extrusion and injection molding processes?
As a manufacturer, I discovered that lowering energy use in extrusion and injection molding is not just good business. It is essential for sustainability. This is very important. Reducing energy helps both costs and the planet. Let’s explore improving our processes for efficiency. They become more efficient and really help in saving both money and the environment.
Manufacturers need to study heating processes to use energy better in extrusion and injection molding. They should use efficient technologies, such as Variable Frequency Drives (VFDs). Manufacturers should also reduce waste. Simple changes can really refine production processes. These actions probably lead to lower costs. They also increase sustainability significantly.
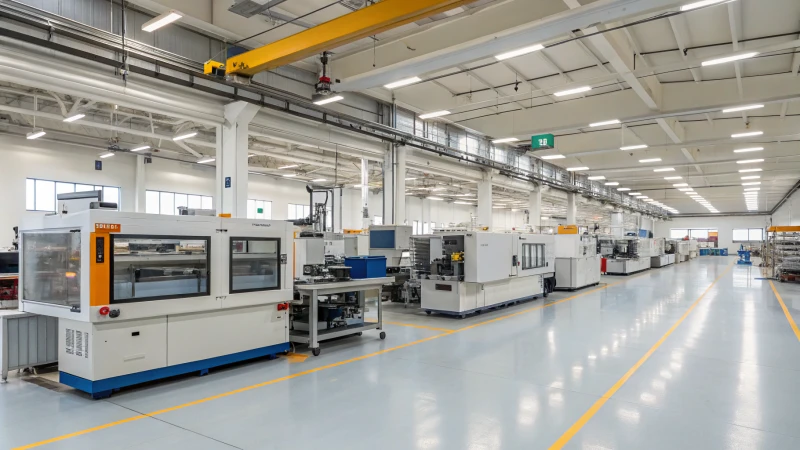
Understanding Energy Consumption Characteristics
To improve energy use in extrusion and injection molding, understanding each process’s unique energy patterns is crucial. Knowing these details enables strategies that lower energy expenses and increase overall efficiency.
Energy Consumption in Extrusion Molding
In extrusion molding, most energy goes to heating the barrel to melt plastic materials. The power needed varies by extruder size, ranging from 3-50 kW depending on the size of the extruder.
- Heating Process:
- Continuous Production: Once everything is hot, energy use balances to counter heat loss in my work.
- Power Consumption: The screw motor typically needs 7-15 kW. As long as the screw speed stays the same, energy use stays steady.
This stability in power consumption allows for better monitoring6 of energy use, enabling manufacturers to optimize their processes effectively.
Energy Consumption in Injection Molding
Injection molding is more complex due to its stop-and-start nature. Here are key points:
Aspect | Description |
---|---|
Heating Power | Ranges from several kW to tens of kW. |
Intermittent Production | Requires constant adjustments in barrel temperature during injection cycles. |
Power Requirements | High instantaneous power needed for injection and clamping, often reaching 100-200 MPa. |
Energy peaks during injection and mold operations in my experience. Understanding this helps me schedule production better, saving on energy costs.
More insights on optimizing injection processes can be found here7.
Strategies for Optimization
-
Using Energy-Efficient Technologies
Investing in new technologies focused on saving energy brought big changes:- Variable Frequency Drives (VFDs): These let motors change speed based on need, cutting unnecessary energy.
- Energy Monitoring Systems: Real-time data helped spot energy spikes for quick cost-saving adjustments.
-
Process Improvements
Improving both extrusion and injection processes saved my team a lot of energy:- For extrusion, keeping temperatures just right and cutting downtime was crucial.
- In injection molding, better cycle times and shorter cooling periods reduced peak energy demand.
-
Waste Reduction Strategies
Waste management was a surprising area of energy waste. Injection molding makes extra materials that waste energy:- Designing molds to cut waste (like smaller gates and runners) made a big difference.
- Recycling scrap materials in our production line allowed effective reuse.
These actions not only saved energy but also improved material efficiency. For more information on waste reduction practices, click here8.
Conclusion
By understanding energy consumption in extrusion and injection molding, I developed strategies that improved efficiency and cut costs. It has been satisfying to see my profits rise alongside better sustainability efforts.
Extrusion molding primarily consumes energy during heating.True
Energy consumption in extrusion molding is mainly due to the heating process of the barrel, crucial for melting plastic materials.
Injection molding requires constant energy levels throughout production.False
Due to its intermittent nature, injection molding has variable energy demands, leading to peaks during specific operations rather than constant usage.
Conclusion
Extrusion is generally more energy efficient than injection molding due to its stable power consumption, while injection molding experiences fluctuating energy demands leading to higher costs.
-
Discover practical strategies for enhancing energy efficiency in your manufacturing processes with these valuable resources. ↩
-
Discover effective heating techniques that can optimize energy efficiency in manufacturing. This resource provides insights into innovative solutions tailored for your industry. ↩
-
Learn more about energy recovery systems that can significantly reduce operational costs in manufacturing. This information is essential for sustainable practices. ↩
-
Discover comprehensive insights on how energy consumption affects manufacturing costs, helping you make informed decisions in your business. ↩
-
Learn about sustainable practices that can reduce energy consumption and improve profitability in manufacturing processes. ↩
-
Discover practical methods for improving energy efficiency in your manufacturing processes by clicking this link. ↩
-
Learn about advanced technologies that can help reduce energy consumption in manufacturing. ↩
-
Find out how to effectively minimize waste in your production process to save on energy costs. ↩