Ever wondered how you can make your injection mold designs not just good, but great?
Integrating DFM principles in injection mold design streamlines production, reduces costs, and enhances quality by addressing manufacturing constraints early, resulting in easier-to-produce molds, efficient cycles, and superior products.
I remember when I first discovered the power of Design for Manufacturing (DFM) principles in my own projects. It was like finding the secret sauce that took my designs from mediocre to masterpieces. Imagine creating molds that not only meet functional needs but also glide through production without a hitch. This is the real magic of DFM—it’s about foresight, planning, and making informed choices that pay off big time in the long run.
Let me walk you through some strategies and share stories from the field where DFM turned challenges into triumphs, revealing how it can be a game-changer for your mold design process.
DFM reduces injection mold production costs.True
By considering manufacturing constraints, DFM minimizes waste and inefficiencies.
Ignoring DFM principles enhances product quality.False
Neglecting DFM often leads to design flaws and increased production errors.
- 1. What Are the Core Principles of Design for Manufacturing?
- 2. How Does DFM Reduce Production Costs in Mold Design?
- 3. How Does Design for Manufacturing Enhance Product Quality?
- 4. How Can Designers Implement DFM in the Early Stages of Mold Design?
- 5. What Are Common Mistakes to Avoid When Applying DFM Principles?
- 6. How Do Real-World Case Studies Illustrate the Benefits of DFM?
- 7. Conclusion
What Are the Core Principles of Design for Manufacturing?
Ever had that moment when everything just clicks? That’s what DFM principles do for product design—making everything fit seamlessly together. Let’s dive into these game-changing principles.
Core principles of Design for Manufacturing include simplicity, standardization, minimizing parts, and ease of assembly to enhance efficiency, reduce costs, and improve product quality in the manufacturing process.

Simplification of Design
I’ve often found that simplifying a design can feel like solving a puzzle, where each piece fits perfectly to form a coherent whole. It’s like when I streamlined a gadget design1, reducing its parts and complexities, which not only sped up production but also minimized errors. With fewer components, assembly time shrinks, making the entire process more efficient.
Standardization of Components
I once faced a situation where we needed a part that wasn’t readily available, leading to costly delays. That’s when I realized the power of standardization2. By using common parts across different products, we cut down on wait times and saved money. It’s like having a universal charger for all your devices—it just makes life easier.
Benefit | Description |
---|---|
Cost Savings | Reduces custom parts costs |
Consistency | Ensures uniform quality |
Minimizing the Number of Parts
Imagine piecing together a complex jigsaw puzzle with fewer pieces—it’s quicker and less likely to fall apart over time. That’s the idea behind minimizing parts in a product. During one of my projects, combining functionalities into single components reduced potential points of failure, enhancing durability and reliability. This principle requires thoughtful consideration during the design phase3.
Ease of Assembly
Nothing’s more satisfying than watching a team breeze through assembling a product I designed. By ensuring ease of assembly, I focus on creating parts that are intuitive to handle and fit seamlessly without force. It’s like building with Lego bricks—smooth and straightforward. Ensuring that designs are intuitive to assemble4 can save time and reduce errors on the production line.
Designing for Quality Control
Incorporating quality control into the design process has been a game-changer for me. It’s about adding features that allow quick checks during assembly. I remember implementing a simple alignment feature that dramatically reduced inspection times and caught issues early, saving headaches down the line. This involves creating designs that are easy to inspect and test during production processes such as assembly processes5.
Simplification reduces manufacturing errors.True
Simplifying designs minimizes complexity, reducing potential errors and time spent.
Standardized components increase custom part costs.False
Standardization cuts costs by using common parts, reducing the need for custom parts.
How Does DFM Reduce Production Costs in Mold Design?
Ever wondered how some companies manage to slash costs without compromising quality? It’s like finding the secret ingredient to a successful recipe. Let’s explore how DFM works this magic in mold design.
DFM reduces mold design costs by optimizing component geometry, simplifying assembly, and eliminating unnecessary features, resulting in less material waste, faster production, and reduced errors.

Optimizing Component Geometry
I remember the first time I got my hands on a complex mold design. The sheer volume of material involved was staggering. But then, applying DFM principles, I learned how focusing on optimizing component geometry could trim down the material used without sacrificing quality. It’s not just about savings on materials—less weight also means lower tooling costs, which is always a win in my book.
Simplifying Assembly Processes
There was this one project where the assembly process felt like a never-ending jigsaw puzzle. By redesigning the molds with fewer parts and using standardized components, we managed to streamline the entire process. The production lines6 suddenly felt like well-oiled machines, reducing assembly time and minimizing errors. It’s amazing what simplicity can achieve!
Reducing Unnecessary Features
Once, I spent days trying to figure out why a certain mold was costing so much. Turned out, it was overloaded with unnecessary features. DFM taught me to strip these down, which not only simplified the manufacturing process7 but also slashed those extra machining costs. Less really can be more.
Leveraging Advanced Technology
Incorporating advanced technologies like CAD and CAM has been a game-changer for me. The precision with which we can simulate and model now means we catch potential issues early on. This foresight saves us from costly post-production adjustments and keeps projects on budget.
DFM Benefits | Impact on Costs |
---|---|
Optimized Geometry | Reduced material use |
Simplified Assembly | Faster production cycles |
Eliminated Unnecessary Features | Lower tooling costs |
Advanced Technology Use | Fewer post-production errors |
By embracing these principles, I’ve seen firsthand how manufacturers can trim down production costs while still meeting high-quality standards. It’s all about working smarter, not harder.
DFM reduces material use by optimizing component geometry.True
DFM focuses on efficient design, minimizing material use without compromising quality.
Simplifying assembly processes increases production errors.False
Simplifying assembly processes reduces the likelihood of errors, leading to smoother operations.
How Does Design for Manufacturing Enhance Product Quality?
I remember my first encounter with Design for Manufacturing (DFM) and how it transformed my approach to product quality and reliability.
Design for Manufacturing (DFM) improves product quality by aligning design with manufacturing capabilities, reducing errors, and boosting efficiency.
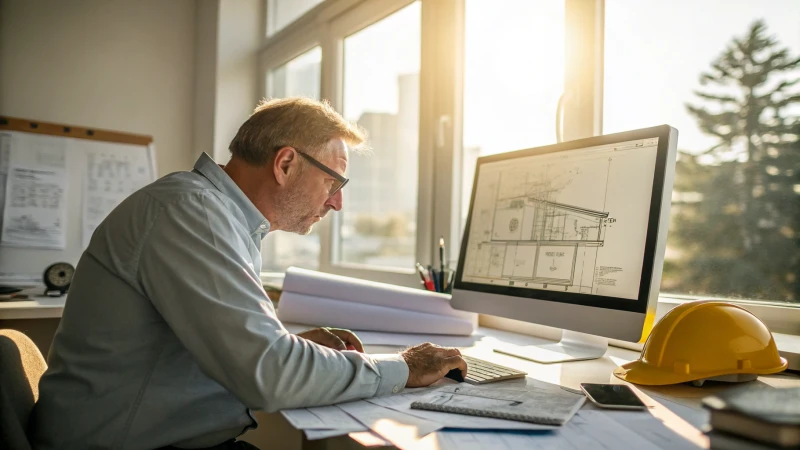
Understanding DFM Principles
The journey into Design for Manufacturing (DFM) was eye-opening for me. I realized how crucial it was to adapt my designs to fit the manufacturing process. It wasn’t just about creating something that looked good on paper; it was about ensuring that the design was practical and could be manufactured without a hitch. By considering manufacturing constraints8, I could streamline production, which was a game-changer.
Benefits of DFM
One of the most satisfying parts of adopting DFM has been the noticeable reduction in manufacturing costs and defects. Designing products that are simple to manufacture means there’s less room for error, which has drastically reduced production delays9. The consistency in product quality has been remarkable.
Examples of DFM Implementation
- Material Selection: I once selected a specific plastic for a project because it had uniform properties that reduced shrinkage and warping. It was a small change, but the impact on product quality was significant.
- Tolerance Optimization: Setting realistic tolerances has always been a priority. Ensuring parts fit together well not only reduces assembly time but also improves reliability. It’s like putting together a puzzle where every piece fits perfectly.
- Simplicity in Design: Simplifying designs has become second nature to me. Focusing on core functionality and eliminating unnecessary features has lowered the risk of defects.
DFM Practice | Impact on Quality |
---|---|
Material Selection | Reduces defects such as warping and cracking |
Tolerance Optimization | Ensures better fitting parts |
Simplicity in Design | Lowers complexity and potential errors |
Challenges in Implementing DFM
Despite all these benefits, implementing DFM isn’t without its challenges. Finding that sweet spot between cost savings and design flexibility is tough. Sometimes, I find myself wrestling with the need for innovative features versus sticking with tried-and-true methods that don’t require advanced tooling10.
Ultimately, DFM has become an integral part of my work, helping me align designs with manufacturing capabilities to enhance product quality. For someone like me, who thrives on precision and efficiency, understanding and applying DFM principles has been incredibly rewarding.
DFM reduces manufacturing costs and defects.True
Designing for manufacturability minimizes errors and production delays.
Complex designs improve product reliability in DFM.False
Simplifying designs reduces errors, enhancing reliability and functionality.
How Can Designers Implement DFM in the Early Stages of Mold Design?
Ever felt the rush of nailing a design that perfectly marries beauty and functionality? That’s the magic of Design for Manufacturability (DFM), especially in mold design. Let’s explore how to weave DFM into your early design stages seamlessly.
To implement DFM in the early stages of mold design, focus on material selection, geometric simplicity, and collaborative feedback. Use CAD tools for simulations to foresee production issues and enhance manufacturability.

Understanding the Role of Material Selection
Material selection became my foundation stone. It’s incredible how picking the right material can change everything. I realized I had to consider factors like shrinkage rates and thermal properties right from the start to ensure the mold’s durability and performance wouldn’t suffer.
Material Type | Key Considerations |
---|---|
Plastic | Shrinkage, Heat Resistance |
Metal | Durability, Machinability |
Analyzing Geometric Complexity
Initially, I was drawn to intricate designs, but I quickly learned that simplicity is key. By reducing unnecessary geometric complexity, I could prevent countless production headaches and cut costs dramatically. CAD tools became my best friend, helping me simulate potential issues before they became problems. Utilize CAD tools to simulate and identify potential production challenges11.
Leveraging Feedback Loops
Working closely with cross-functional teams12 taught me so much. Regular feedback sessions with engineers and production specialists helped align my designs with manufacturing realities. It’s like having a safety net that catches potential issues early on.
Optimizing Production Processes
Collaboration with suppliers and manufacturers was crucial. Understanding their capabilities allowed me to fine-tune my designs to fit seamlessly into existing production processes. This collaboration often came down to small details, documented in a process checklist:
- Tooling Specifications: Compatibility with machines
- Cycle Time: Target production speeds
- Quality Control: Standards and checks
Utilizing Advanced CAD Tools
Advanced CAD tools were a game-changer for me. They offered simulations that could predict mold behavior13 under various conditions, saving time and resources by reducing trial-and-error during production. Whether it was thermal analysis or stress testing, these tools provided insights that informed every decision.
- Simulation Types:
- Thermal Analysis
- Stress Testing
- Flow Dynamics
Each project taught me something new about incorporating DFM in the early stages of mold design, ensuring efficiency and quality from the outset.
Material selection impacts mold's thermal properties.True
Choosing the right material affects the mold's heat resistance.
Ignoring geometric complexity reduces production costs.False
Reducing, not ignoring, complexity improves manufacturability and cost.
What Are Common Mistakes to Avoid When Applying DFM Principles?
Navigating the world of Design for Manufacturing (DFM) can be a bit like walking a tightrope—one wrong step, and you might find yourself in a costly redesign spiral.
Avoid common DFM mistakes by considering manufacturability, material constraints, and cost implications early in the design process, and collaborate with manufacturing teams to streamline production and reduce costs.
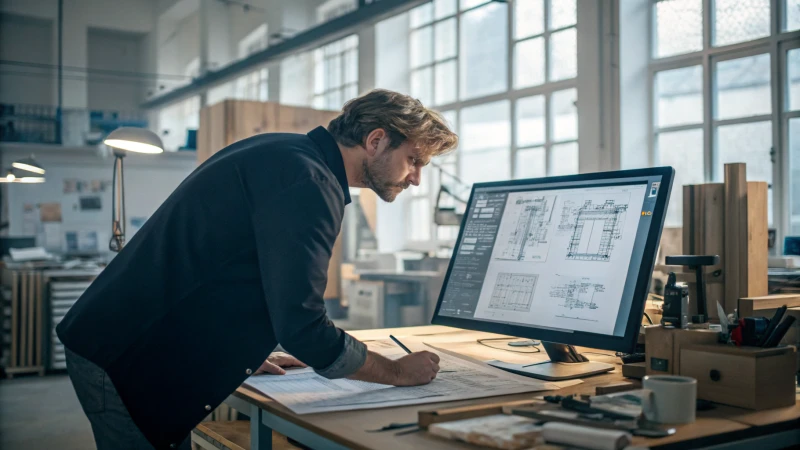
Overlooking Manufacturability in Design Phase
Ignoring manufacturability early in the design process often results in costly redesigns or delays. Ensure your design meets manufacturing capabilities by consulting engineers and using design tools14 that simulate production processes.
Design Aspect | Potential Mistake | Solution |
---|---|---|
Tolerances | Too tight or loose | Balance precision & cost |
Component Size | Ignoring machine limits | Match with equipment specs |
Neglecting Material Constraints
Choosing the right materials can feel like navigating a maze. In my early days, I overlooked how material properties like thermal resistance or tensile strength could affect the final product. Selecting inappropriate materials can lead to unexpected failures15 or unnecessary expense. Consider material properties and always align them with the product’s intended use and manufacturing method.
Ignoring Cost Implications
There was this one intricate design I was really proud of—until I realized the tooling costs were skyrocketing. That was a tough lesson in how design intricacies can inflate production costs. Conducting a cost analysis16 during the design phase is a non-negotiable step for me to ensure simplicity and identify potential savings.
Lack of Early Collaboration
I’ve found that getting the manufacturing team involved early is like having a secret weapon. Their insights have saved me countless times from design pitfalls. Regular meetings and feedback loops are now part of my workflow, facilitated by collaboration platforms17 that keep everyone on the same page.
By embracing these lessons and focusing on collaboration, I’ve been able to significantly enhance the manufacturability of my designs, staying true to DFM principles and ensuring smoother production workflows.
Ignoring manufacturability leads to costly redesigns.True
Neglecting manufacturability in design often results in expensive delays.
Selecting any material is fine for manufacturing.False
Materials must match product use and manufacturing needs to avoid failures.
How Do Real-World Case Studies Illustrate the Benefits of DFM?
Ever wonder how some companies manage to save millions and improve efficiency just by tweaking their designs?
Real-world case studies show that DFM can lead to major cost savings, better product quality, and more efficient manufacturing. These examples offer real insights into optimizing designs for large-scale production.
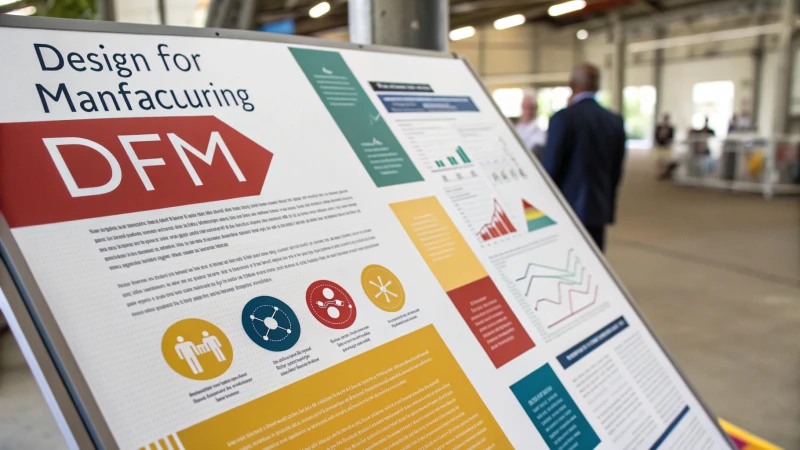
The Role of DFM in Cost Reduction
Let me share a story about a consumer electronics company that took a bold step with DFM to tackle material waste issues. Imagine being part of a team where each product run felt like watching money slip through your fingers. By applying DFM principles, they managed to trim down material use by a whopping 20%, translating into millions in savings. It’s like finding a secret stash of cash you didn’t know you had! This case truly highlights how significant cost savings18 can be achieved when strategic design adjustments are made.
-
Before DFM Implementation:
- High material waste
- Increased production costs
-
After DFM Implementation:
- Reduced material usage by 20%
- Achieved significant annual savings
Enhancing Product Quality through DFM
I remember reading about a medical device manufacturer who turned to DFM to solve persistent reliability issues. It was like having a lightbulb moment after constant trial and error—realizing that close collaboration with the production team was key. By addressing design flaws that led to assembly errors, they achieved a 15% boost in product reliability. It’s a testament to the power of improved product quality19 through thoughtful design changes.
Boosting Manufacturing Efficiency with DFM
In the automotive industry, there’s an inspiring tale of a manufacturer who decided to optimize their component designs for easier assembly. Imagine shaving 30% off your assembly time—it’s like winning the efficiency lottery! This case study proves that enhanced manufacturing efficiency20 isn’t just a dream when you align designs with production capabilities.
DFM Benefits | Real-World Examples |
---|---|
Cost Reduction | Electronics company saved millions |
Improved Product Quality | Medical devices saw reliability boost |
Manufacturing Efficiency | Automotive reduced assembly time |
These stories from different industries vividly demonstrate the transformative power of DFM, offering concrete examples of how its principles can be applied to achieve remarkable results.
DFM reduces material waste by 20%.True
A consumer electronics company cut material usage by 20% with DFM.
DFM increases product reliability by 30%.False
A medical device manufacturer improved reliability by 15% with DFM.
Conclusion
DFM principles enhance injection mold design by simplifying production, reducing costs, and improving quality through early integration of manufacturing constraints and efficient design strategies.
-
Exploring this link will provide insights into how simplifying design can enhance manufacturability and reduce costs. ↩
-
Learn how standardizing components across products can lead to significant cost reductions and efficiency improvements. ↩
-
Discover strategies for reducing part count in designs to improve reliability and simplify manufacturing. ↩
-
Gain practical tips on designing products that are easy to assemble, saving time and reducing errors. ↩
-
Understand why integrating quality control features in design is essential for successful manufacturing. ↩
-
Discover why streamlined assembly processes are vital for cost efficiency and error reduction in manufacturing. ↩
-
Explore the advantages of removing non-essential features from designs to simplify manufacturing and cut costs. ↩
-
Explore how recognizing manufacturing constraints early can help tailor designs to fit production capabilities, reducing errors. ↩
-
Understand how effective DFM can mitigate typical production delays by addressing potential issues during the design phase. ↩
-
Learn about advanced tooling methods that might be necessary when balancing cost and design flexibility within DFM. ↩
-
This link provides strategies to simplify designs, reducing potential production hurdles and enhancing manufacturability. ↩
-
Feedback loops ensure designs meet manufacturing capabilities, leading to smoother production processes. This link explains how to establish effective feedback systems. ↩
-
Learn about advanced simulations that help foresee mold performance, minimizing errors and improving design accuracy. ↩
-
Explore tools that simulate production processes, enabling designers to foresee manufacturing challenges early. ↩
-
Learn about material failures to choose appropriate materials for your design. ↩
-
Discover methods to analyze costs during the design phase, promoting budget-friendly decisions. ↩
-
Find platforms that enhance teamwork and documentation among design and manufacturing teams. ↩
-
Discover how companies have saved millions by reducing material waste using DFM principles. ↩
-
Learn how DFM principles enhance product reliability and reduce assembly errors in real-world cases. ↩
-
Explore how aligning designs with production capabilities enhances efficiency in manufacturing processes. ↩