- 1. I. Basic Cognitive Level: Establishing Conceptual Framework
- 2. II. Application Analysis Level: Solving User Decision-Making Problems
- 3. III. Technical Deep Dive Level: Meeting Professional Reader Needs
- 4. IV. Practical Tools Level: Enhancing Content Operability
- 5. V. Extension Level: Building a Knowledge Network
- 6. Conclusion: Mastering Cooling Time with ZetarMold
I. Basic Cognitive Level: Establishing Conceptual Framework
Before we optimize, we must understand.
Clear Definitions
- Injection Molding Cooling Time:
- Full Technical Name: Cooling Phase Duration in Injection Molding Cycle.
- Common Aliases: Cooling time1, solidification time2, cure time (less common for thermoplastics, more for thermosets/silicone).
- Core Principle: Cooling time is the period within the injection molding cycle, starting after the mold cavity is filled and packed with molten plastic, during which the plastic material solidifies to a point where it’s rigid enough to be ejected from the mold without deformation or damage. This occurs through heat transfer from the molten plastic to the cooler mold.
- Significance: It typically constitutes the largest portion (often 50-80%) of the overall injection molding cycle time.
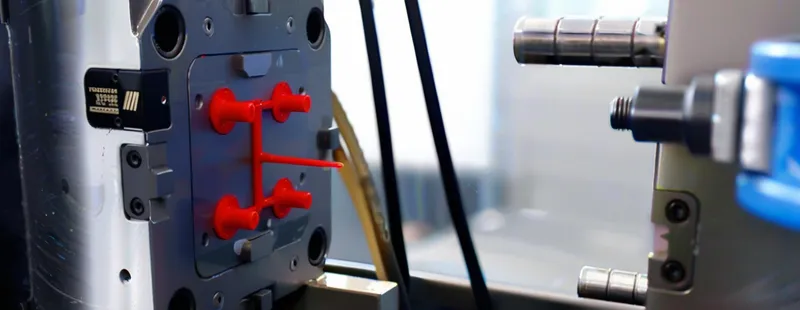
- Injection Molding Cycle3: The complete sequence of events for producing one part (or set of parts), comprising:
- Mold Closing
- Injection (Filling)
- Packing (Holding)
- Cooling
- Mold Opening
- Ejection
Classification (Factors Influencing Cooling Time)
Cooling time isn’t a fixed value; it’s influenced by a confluence of factors that can be broadly classified:
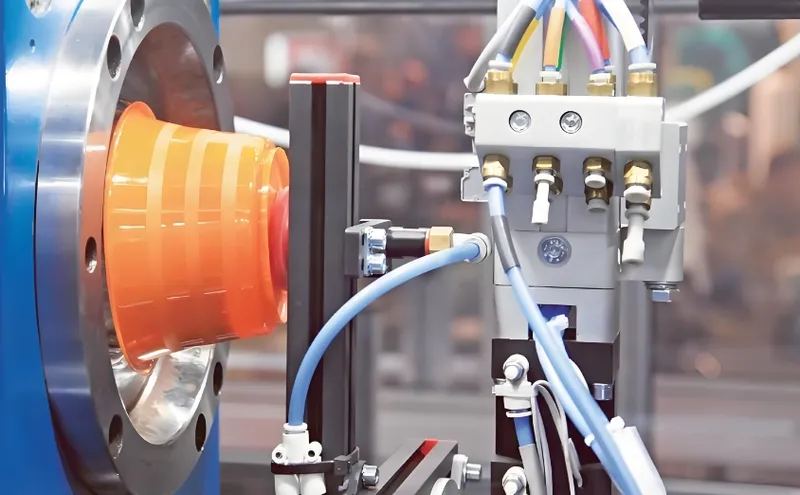
-
Material-Centric:
- Type of Polymer4: Amorphous (e.g., PC, PS) vs. Semi-crystalline (e.g., PP, PA, POM). Semi-crystalline materials often require more precise cooling control due to latent heat of fusion and crystallization shrinkage.
- Thermal Properties: Thermal conductivity, specific heat capacity, thermal diffusivity, and glass transition temperature (Tg) or melting temperature (Tm) of the polymer.
- Ejection Temperature: The maximum temperature at which the part can be ejected without issues like warpage or sticking.
-
Part Design-Centric:
- Wall Thickness: The most dominant factor. Cooling time is approximately proportional to the square of the thickest wall section.
- Part Geometry: Complex geometries, ribs, bosses, and non-uniform wall thicknesses can create hot spots and differential cooling.
-
Mold Design-Centric:
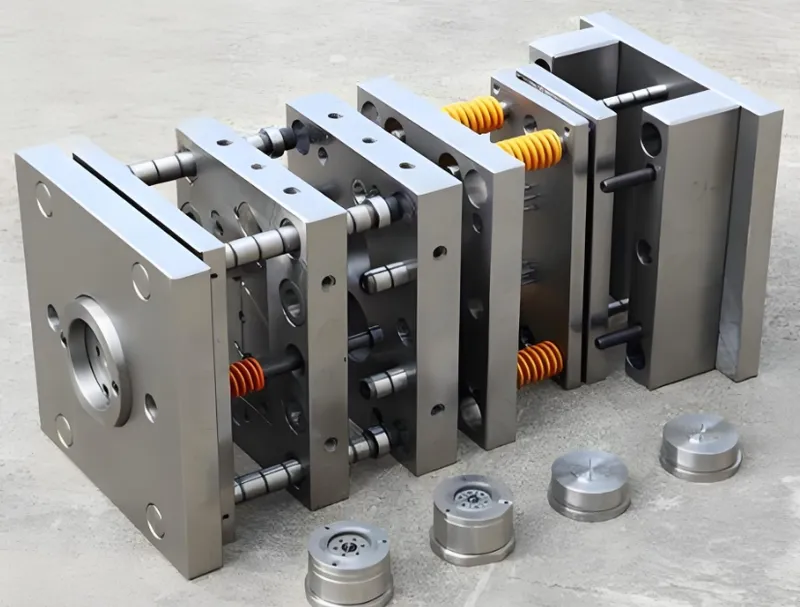
- Cooling Channel Design5: Layout, diameter, proximity to the cavity, and type (e.g., conventional drilled lines, conformal cooling channels).
- Mold Material: Higher thermal conductivity mold materials (e.g., beryllium copper inserts vs. P20 steel) can reduce cooling time.
- Venting: Proper venting allows trapped air to escape, preventing insulation effects that can prolong cooling.
- Process Parameter-Centric:
- Melt Temperature6: Higher melt temperature means more heat to remove.
- Mold Temperature: Lower mold temperature generally means faster cooling, but can affect surface finish, stresses, and filling.
- Coolant Temperature & Flow Rate: Colder coolant and higher flow rates enhance heat removal efficiency.
II. Application Analysis Level: Solving User Decision-Making Problems
Understanding cooling time helps in making informed decisions for various applications.
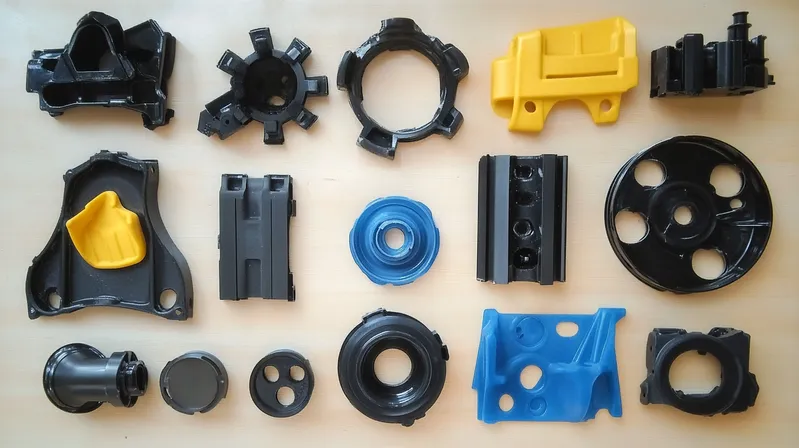
Typical Application Scenarios
- High-Volume, Thin-Walled Packaging (e.g., food containers, caps – often PP, PE):
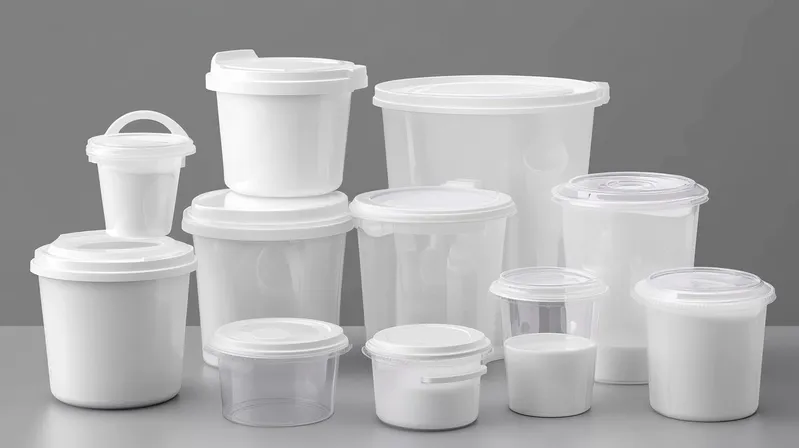
- Suggestion: Cooling time is paramount for cycle time. Optimize for rapid cooling using highly conductive mold materials, efficient cooling channel design, and potentially lower (but controlled) mold temperatures. Material choice favors fast-cycling grades.
- Medical Devices (e.g., syringes, diagnostic components – often PC, PEEK, COC):
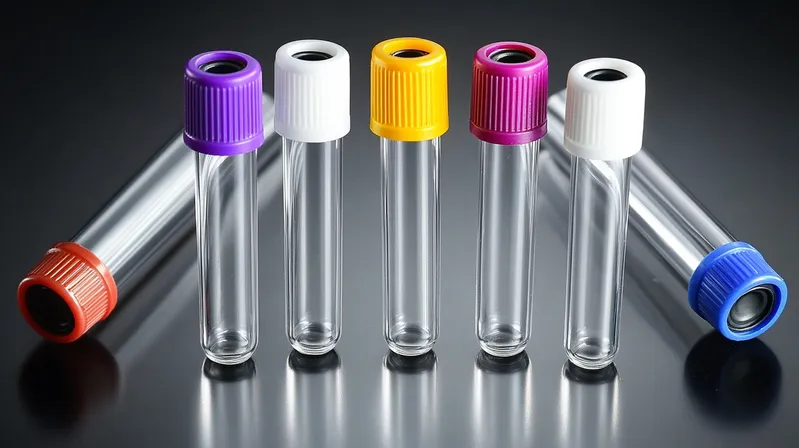
- Suggestion: Precision and material integrity are key. Cooling must be uniform to minimize internal stresses and ensure dimensional accuracy. Longer, more controlled cooling might be acceptable to achieve critical tolerances.
- Consumer Electronics Housings (e.g., phone cases, remote controls – often ABS, PC):
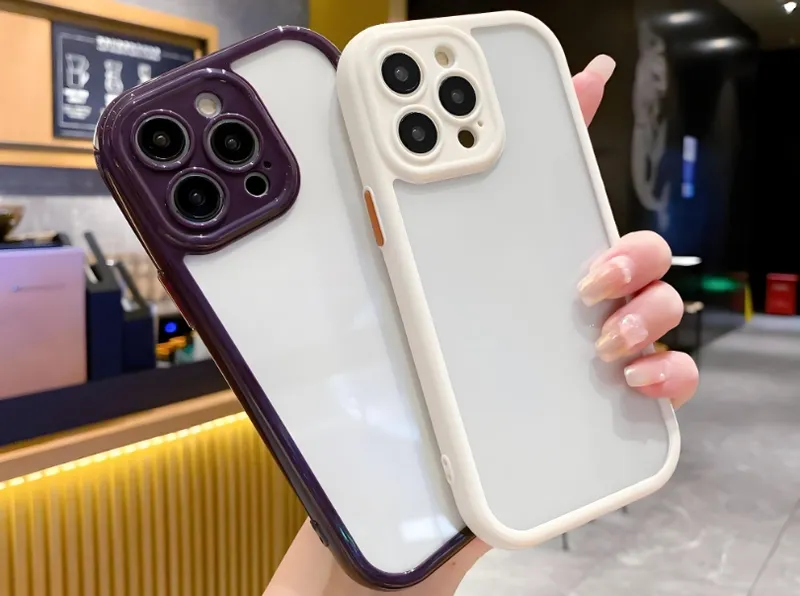
- Suggestion: Aesthetics (surface finish) and structural integrity are important. Cooling needs to be managed to avoid sink marks and ensure good fit and feel. Optimized cooling channel design is crucial.
- Silicone Rubber Products (LSR Molding):
- Suggestion: While ZetarMold also handles silicone, its "cooling" is actually "curing" via heat. The mold is hot, and the "cooling" equivalent is the time taken for the cross-linking reaction to complete. The principles of heat transfer and uniformity still apply, but the objective is to maintain heat for curing rather than remove it for solidification.
Pros and Cons Comparison (Impact of Cooling Time Duration)
Feature | Shorter Cooling Time | Longer Cooling Time |
---|---|---|
Pros | – Reduced cycle time | – Better dimensional stability |
– Increased productivity | – Improved part quality (fewer sink marks, less warpage) | |
– Lower per-part cost | – Reduced internal stresses | |
Cons | – Risk of defects (warpage, sink marks, short shots) | – Increased cycle time |
– Potential for parts sticking or deforming on ejection | – Lower productivity | |
– Higher internal stresses if cooled too rapidly/unevenly | – Higher per-part cost | |
– May require more robust ejection system | – Possible over-packing issues if holding pressure is maintained too long into cooling |
III. Technical Deep Dive Level: Meeting Professional Reader Needs
Let’s get into the nitty-gritty.
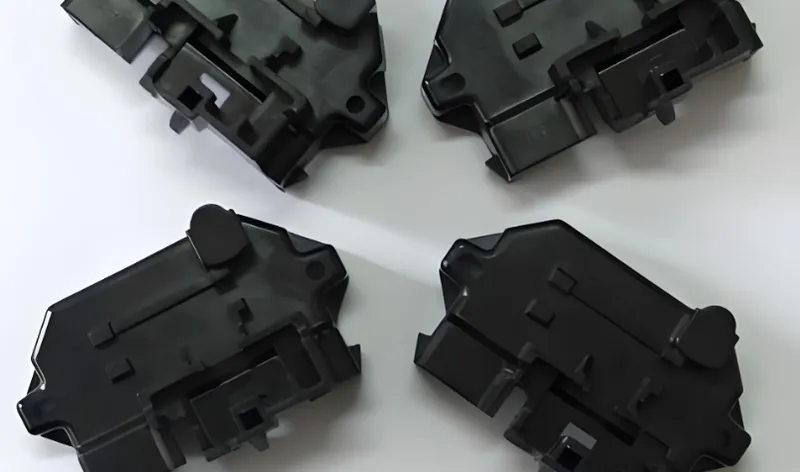
Process Full Workflow Breakdown (Focus on Cooling)
-
Mold Closure & Clamping: The two halves of the mold are securely closed and clamped.
-
Injection: Molten plastic is injected into the mold cavity under high pressure.
-
Packing/Holding: After the cavity is mostly filled, additional material is packed in under pressure to compensate for shrinkage as the material begins to cool and solidify near the mold walls.
- Key Parameter: Packing pressure, packing time.
-
Cooling Phase:
- Heat Transfer: This is the core of cooling. Heat from the molten plastic (at melt temperature) is transferred primarily through conduction to the cooler mold steel, and then carried away by the coolant (usually water) circulating through the mold’s cooling channels.
- Solidification Front: Solidification starts at the mold walls and progresses inwards towards the center of the part.
- Shrinkage Compensation7: Continues initially from packing pressure, then volumetric shrinkage occurs as the bulk material cools further.
- Duration Determinants: Material’s ejection temperature, thermal properties, part’s thickest section, mold temperature, and cooling system efficiency.
- Key Parameters: Mold temperature, coolant temperature, coolant flow rate, desired part ejection temperature.
-
Mold Opening: Once the set cooling time has elapsed and the part is sufficiently rigid, the clamp opens the mold.
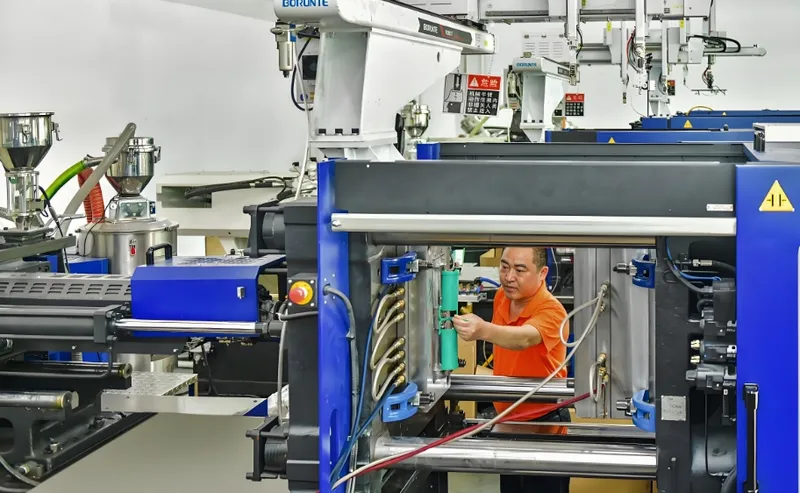
- Ejection: The solidified part is pushed out of the mold cavity by an ejector system (pins, sleeves, plates).
Key Cooling Parameters to Monitor & Control:
-
Mold Surface Temperature8: Critical for controlling the rate of heat extraction and influencing surface finish and crystallization (for semi-crystalline polymers).
-
Coolant Inlet/Outlet Temperature Difference (Delta T): Indicates the amount of heat being removed. A very small Delta T might suggest insufficient flow or poor thermal contact.
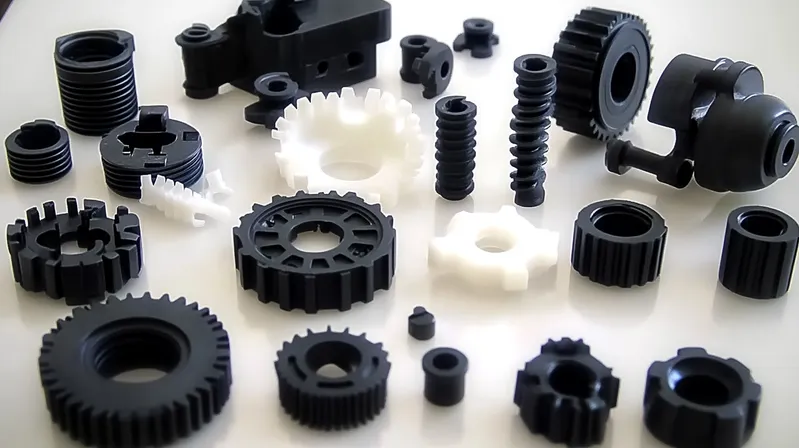
-
Coolant Flow Rate9: Turbulent flow is generally preferred for efficient heat transfer.
-
Melt Temperature: Sets the initial heat load.
Material Compatibility Explanation
The thermal properties of the plastic material are fundamental to its cooling behavior:
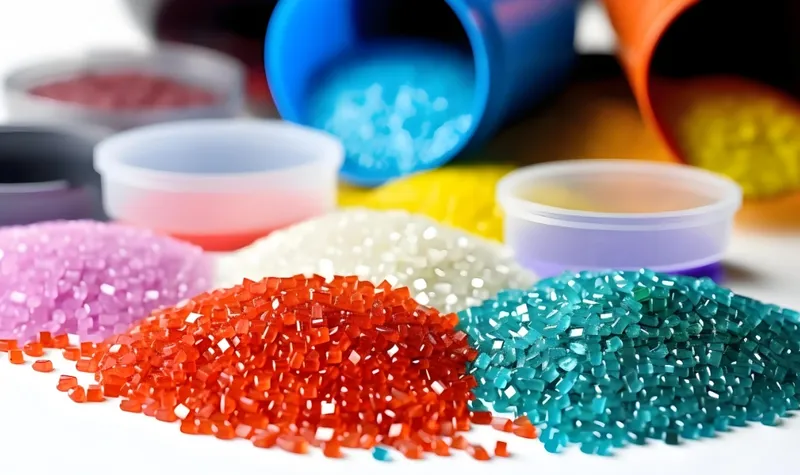
-
Amorphous Polymers (e.g., Polystyrene (PS), Polycarbonate (PC), ABS):
- No sharp melting point; they soften over a temperature range.
- Generally lower shrinkage than semi-crystalline.
- Cooling is about bringing the material below its Glass Transition Temperature (Tg) to achieve rigidity.
- Can be more prone to internal stresses if cooled too rapidly.
-
Semi-crystalline Polymers (e.g., Polypropylene (PP), Polyethylene (PE), Nylon (PA), PET, PBT):
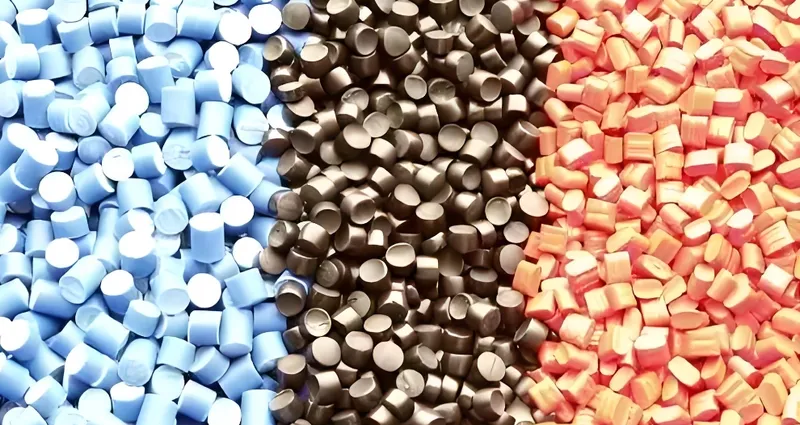
- Sharp melting point (Tm).
- Higher shrinkage due to the formation of ordered crystalline structures; this process also releases latent heat of fusion, which must be removed.
- Cooling rate can affect the degree of crystallinity, influencing mechanical properties. Rapid cooling can lead to smaller spherulites and sometimes improved toughness but potentially more warpage.
- Require careful cooling control to manage warpage and dimensional stability.
- Liquid Silicone Rubber (LSR – for comparison):
- Thermoset material. The mold is heated (typically 170-210°C).
- "Cooling time" is actually "curing time" where the material cross-links. The part is ejected hot. Heat transfer is still key, but for maintaining curing temperature uniformly.
IV. Practical Tools Level: Enhancing Content Operability
Actionable insights for your projects.
Design Checklist (Reminders of Process Limitations for Cooling)
When designing parts for injection molding, consider these to optimize cooling:
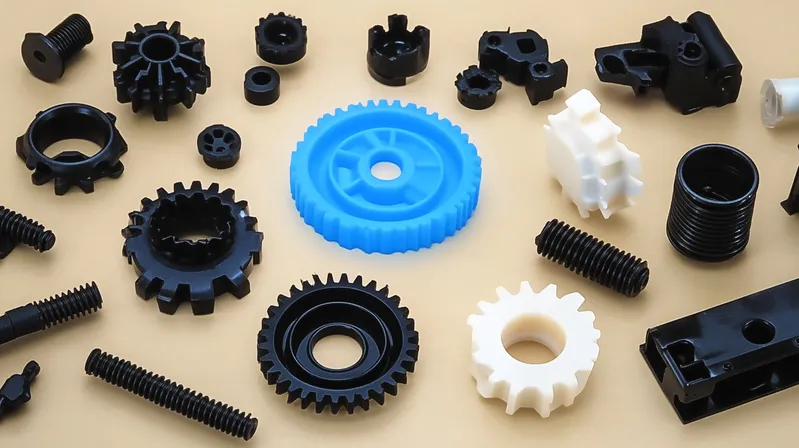
-
Uniform Wall Thickness: Aim for consistent wall thickness throughout the part. This is the #1 rule for manageable cooling.
-
Avoid Thick Sections: If unavoidable, core them out or use features like gas assist.
-
Generous Radii: Use radii on inside and outside corners instead of sharp edges to prevent stress concentrations and improve flow/cooling.
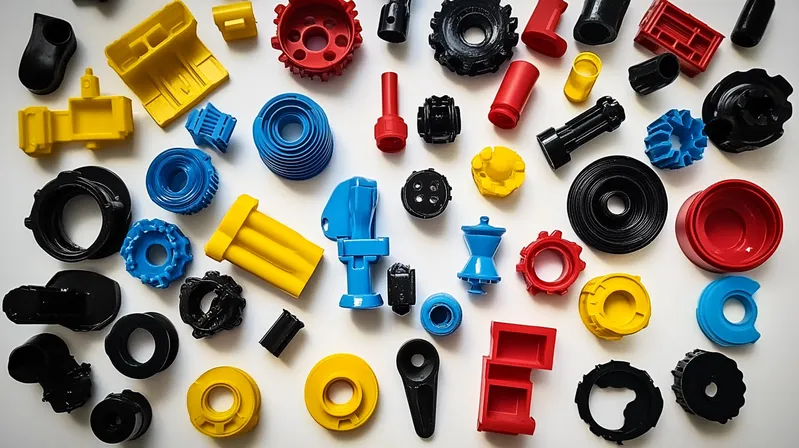
-
Gradual Transitions: If thickness changes are necessary, make them gradual.
-
Ribs/Bosses Design: Rib thickness should be ~50-70% of the nominal wall to prevent sink marks. Bosses should be cored.
-
Material Selection: Consider materials with better thermal conductivity or lower processing temperatures if cycle time is critical.
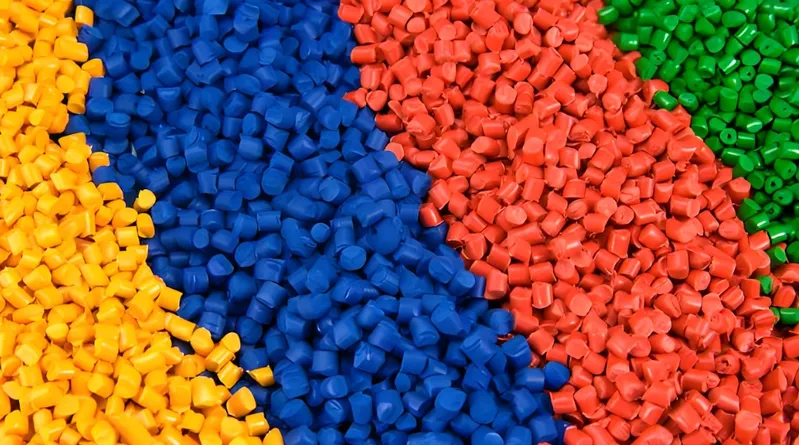
-
Gate Location: Place gates to fill thick sections first, or to minimize temperature variations.
-
Consider Mold Cooling Feasibility: Is the part design so complex that effective cooling channels are impossible to implement conventionally? (This might push towards conformal cooling).
Process Selection Decision-Making (Optimizing Cooling Time)
Here’s a basic thought process for optimizing cooling time:
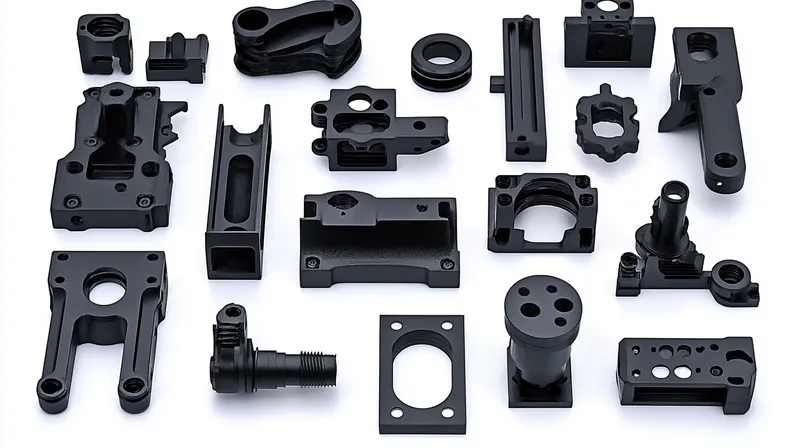
-
Is current cooling time excessive, leading to high costs or low output?
- YES: Proceed to analyze.
- NO: Is part quality (warpage, sinks, dimensions) an issue?
- YES: Cooling might be too short or uneven. Proceed to analyze.
- NO: Current cooling is likely adequate. Monitor periodically.
-
Analyze Part Design:
- Is wall thickness non-uniform? Action: Advise customer on DFM for uniform walls.
- Are there avoidable thick sections? Action: Advise coring out.
-
Analyze Material:
- Is the material appropriate for the cycle time target? Action: Explore alternative grades or materials if feasible.
- Note the material’s recommended ejection temperature and thermal properties.
-
Analyze Mold Design & Condition:
- Are cooling channels adequate (size, number, placement)? Action: Use mold flow simulation. Consider conformal cooling for complex parts or critical applications.
- Are channels clear and free of scale? Action: Implement regular mold maintenance.
- Is the mold material appropriate for heat transfer needs? Action: Consider inserts of higher conductivity material in hot spot areas.
-
Analyze Process Parameters:
- Is melt temperature higher than necessary? Action: Reduce gradually, monitoring fill.
- Is mold temperature set optimally? (Too low can cause other issues). Action: Experiment within material supplier’s recommended range.
- Is coolant flow rate and temperature optimized? Action: Ensure turbulent flow; use chilled water if appropriate and cost-effective.
Decision Tree Snippet:
-
IF part has thick sections AND cooling is long THEN consider coring out OR using gas-assist.
-
IF part shows warpage AND cooling is short THEN increase cooling time OR improve cooling uniformity (e.g., conformal cooling).
-
IF cycle time is critical AND part quality allows THEN explore options to reduce cooling (optimized mold, parameters) cautiously.
V. Extension Level: Building a Knowledge Network
Cooling time doesn’t exist in a vacuum.
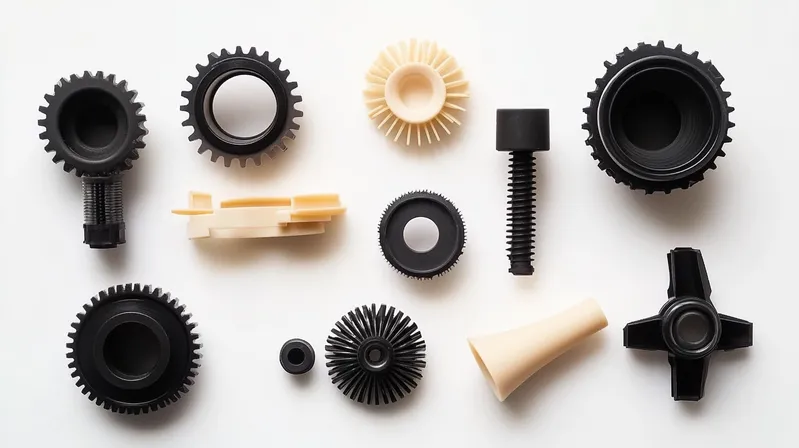
Related Technology Navigation
- Upstream Technologies:
- Part Design (DFM – Design for Manufacturability): Decisions made here heavily influence cooling.
- Material Selection: Thermal properties are intrinsic to cooling calculations.
- Mold Flow Analysis (Simulation): Software like Moldflow, SolidWorks Plastics, etc., can predict cooling time, identify hot spots, and help optimize cooling channel design before steel is cut. This is invaluable.
- Mold Design: Incorporating efficient cooling channel layouts, using appropriate mold materials.
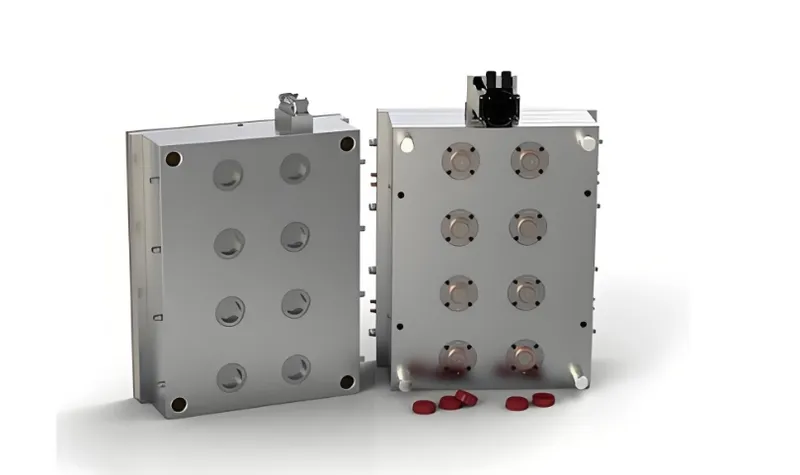
-
Downstream Technologies/Considerations:
- Post-Molding Operations: Annealing might be required for parts with high internal stress, sometimes exacerbated by rapid or uneven cooling.
- Quality Control (QC): Dimensional checks, warpage analysis, and stress testing are influenced by the cooling process.
-
Parallel/Enhancement Technologies:
- Conformal Cooling: Cooling channels that follow the contour of the mold cavity, providing much more uniform and efficient cooling. Often built using additive manufacturing (3D printing of metal).
- Pulsed Cooling/Variotherm (Heat & Cool Molding): Rapidly heating the mold surface during injection for better surface finish and flow, then rapidly cooling it. Complex but can solve specific issues.
- Hot Runner Systems: While not directly cooling, they keep the runner molten, eliminating runner cooling time and material waste, thus impacting overall efficiency.
- Mold Temperature Controllers (TCUs): Essential for maintaining precise coolant temperature and flow.
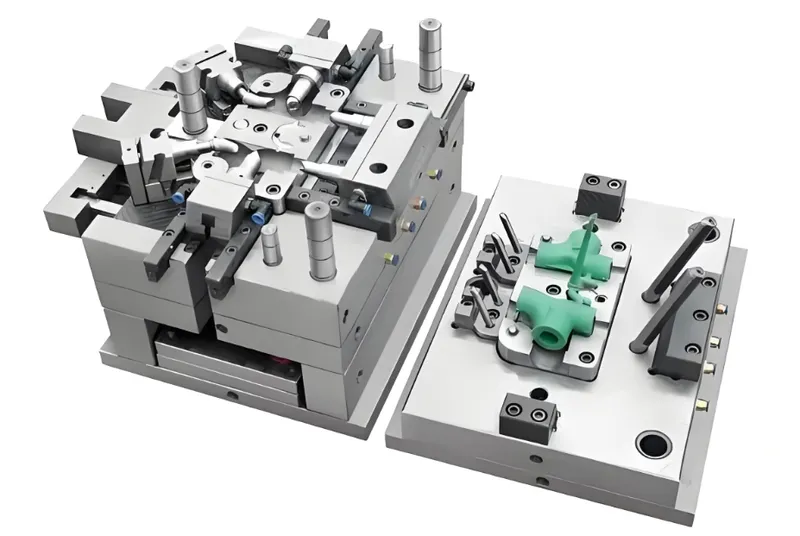
Conclusion: Mastering Cooling Time with ZetarMold
At ZetarMold, we recognize that mastering injection molding cooling time is a blend of science, experience, and cutting-edge technology. It’s a critical factor that we meticulously manage to deliver high-quality, cost-effective injection molded and silicone rubber products to our international clients.
By understanding the fundamentals, analyzing applications, diving into the technical details, and utilizing practical tools, we can collectively optimize cooling processes for superior outcomes.
-
Understanding cooling time is crucial for optimizing the injection molding process and improving product quality. ↩
-
Learning about solidification time can lead to better control over the molding process, ensuring high-quality products. ↩
-
Exploring the injection molding cycle helps in grasping the entire manufacturing process, enhancing efficiency and output. ↩
-
Understanding polymer types is crucial for optimizing cooling times in manufacturing processes. Explore this link for detailed insights. ↩
-
Cooling channel design significantly impacts cooling efficiency. Discover best practices and innovations in this area. ↩
-
Melt temperature plays a vital role in cooling efficiency. Learn more about its effects on production processes. ↩
-
Learning about Shrinkage Compensation is essential for ensuring dimensional accuracy and quality in molded parts, preventing defects during cooling. ↩
-
Understanding Mold Surface Temperature is crucial for optimizing heat extraction and achieving high-quality surface finishes in molded parts. ↩
-
Exploring the impact of Coolant Flow Rate can help improve heat transfer efficiency and overall production quality in injection molding processes. ↩