As a product designer, have you ever asked yourself which materials work best for injection molding? I have faced this question too. This often happens when I hoped to develop something truly special.
Injection molding commonly utilizes materials like polyethylene, polypropylene, and polystyrene for general plastics, while ABS and polycarbonate are preferred for engineering plastics, offering versatility and suitability for various applications.
Exploring materials feels overwhelming, but it’s also very exciting! I recall my first time choosing the right material for a project. The pressure was intense. Understanding these options changed everything. This article discusses common materials like polyethylene, polypropylene and polystyrene. Each has unique qualities. These qualities elevate your designs.
The potential of engineering plastics like ABS and polycarbonate will be revealed. You will confidently select the best fit for your next big project.
Polyethylene is commonly used in injection molding processes.True
Polyethylene is a widely utilized material in injection molding due to its versatility and cost-effectiveness, making it suitable for various applications.
ABS is not an engineering plastic used in injection molding.False
ABS is indeed classified as an engineering plastic, commonly used in injection molding for its strength and impact resistance, contrary to the claim.
What Are the Key Properties of Injection Molding Materials?
Ever been confused about choosing materials for your next project? I definitely have! Let’s explore the interesting world of injection molding materials. Their properties truly influence our designs. They really do.
Grasping injection molding materials is crucial for good design. Important qualities include mechanical strength, thermal stability, chemical resistance and impact resistance. Each property impacts how materials perform during manufacturing. Common plastics such as ABS and PC have strengths suited to specific needs.
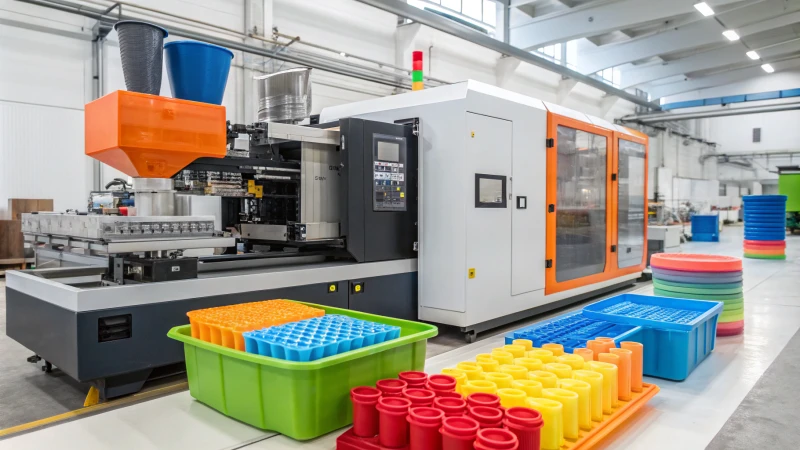
Understanding Injection Molding Materials
When I began working in product design, the impact of material choice amazed me. It affected both the production process and the final product’s quality. It felt like choosing the right ingredients for a recipe. Each material had unique traits affecting everything from durability to looks. Understanding these properties became very important. This was especially true for intricate consumer electronics where every detail mattered.
Injection molding is a widely used manufacturing process that relies heavily on the properties of its materials. Selecting the right material can drastically affect production efficiency and the quality of the final product. Here, we’ll delve into the key properties of injection molding materials, focusing on several common types and their specific characteristics.
Common Properties of Injection Molding Materials
Talking about injection molding materials involves different properties. I first learned about them as hidden treasures. They could either help or ruin my designs:
-
Mechanical Strength: This property tells us how well a material withstands forces without breaking. Polyamide (PA) impressed me with its strong nature. It’s ideal for tough applications.
-
Thermal Stability: Picture a part that survives high temperatures without changing shape! Thermal stability provides this benefit. Polycarbonate (PC) stands out here. It resists heat efficiently. I used PC in projects with unavoidable heat exposure and it worked flawlessly.
-
Chemical Resistance: This property matters in harsh environments. Polyvinyl Chloride (PVC) is my preferred choice for resisting corrosion. Knowing it withstands tough conditions, especially in pipes, is reassuring.
-
Impact Resistance: Getting dropped doesn’t easily damage a product with good impact resistance. I admire Acrylonitrile-butadiene-styrene (ABS) for this property. It’s a reliable pick for electronics and toys.
Material Types and Their Properties
Let’s explore the common materials used in injection molding:
Below is a comparison table of some common injection molding materials and their key properties:
Material Type | Key Properties | Common Applications |
---|---|---|
Polyethylene (PE) | Low temperature resistance, high ductility | Plastic bags, films, wire coatings |
Polypropylene (PP) | Excellent heat resistance, good fluidity | Automotive parts, household goods |
Polystyrene (PS) | Good optical properties, easy processing | Packaging, household items |
Acrylonitrile Butadiene Styrene (ABS) | High mechanical strength, good impact resistance | Electronic housings, toys |
Polycarbonate (PC) | Best impact strength, high dimensional stability | Optical lenses, medical devices |
Polyamide (PA) | High mechanical strength, good toughness | Medical equipment, bearings |
Thermoplastic Polyurethane (TPU) | Flexibility, chemical resistance | Sports equipment, automotive parts |
Styrene-butadiene-styrene (SBS) | Good elasticity, low temperature resistance | Adhesives, soles |
Factors Influencing Material Selection
Choosing the right material involves more than knowing properties; various factors play a role:
-
Cost-effectiveness: I learned the importance of comparing cost and performance. Sometimes spending more initially saves a lot later.
-
Production Volume: From my experience, Polypropylene (PP) suits high-volume runs well due to its affordability and flow characteristics hitting the perfect balance between cost and function.
-
End-use Requirements: Knowing our product’s environmental exposure is crucial; in projects with UV light exposure like Polyethylene (PE), were essential.
With these insights into selecting appropriate materials for injection molding processes becomes easier; it’s about optimizing our designs for both function and manufacturing! This journey is truly rewarding!
Polycarbonate has excellent heat resistance for high-temperature use.True
Polycarbonate is known for its thermal stability, making it suitable for components exposed to elevated temperatures during operation.
Polyvinyl Chloride is the best material for high-impact applications.False
While PVC has good chemical resistance, it does not excel in impact resistance compared to materials like ABS.
How Do Material Choices Affect Product Design and Performance?
Did you ever think about how the materials we pick could change a product’s look and use completely? Believe me, knowing this link might really change our design plans!
Material choices greatly impact product design. They affect how things look, work and last. Choosing the right materials is important for how well the item performs and appeals. This choice is crucial in many uses.
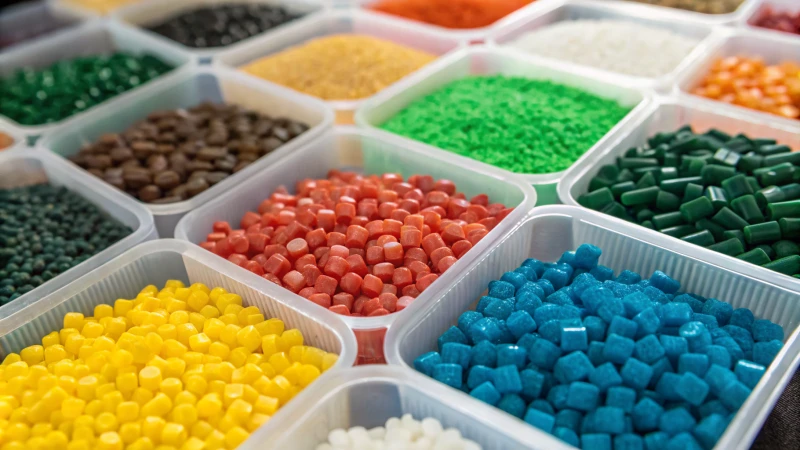
The Role of Material Properties in Design
Selecting materials involves more than just technical details; they define our products’ core. I remember choosing my first material for a project. My heart raced thinking about how it affected everything, from strength to looks. It was eye-opening and taught me how important material properties are in design.
Materials open up a world of possibilities. Each type has its unique traits that may improve or limit our designs. For example, Polyethylene (PE) is my staple due to its strong impact resistance and low friction. It acts like a reliable workhorse in moisture-safe packaging. However, UV light can make it brittle, limiting outdoor use. Conversely, Polycarbonate (PC) is my choice for safety glasses because it is very tough and resists impact well.
Knowing these properties goes beyond technical facts; it’s about storytelling through design! Every material influences how people use our products. Explore more about the impact of materials on design1.
Aesthetic Considerations
Materials breathe life into our designs. I remember using Polystyrene (PS) for a consumer product for its clear look. It made our packaging eye-catching! However, its brittleness reminded me that practicality is essential too. Thermoplastic polyurethane (TPU) was ideal for sports gear with its soft touch and flexibility, blending style and function.
Choosing materials that add visual charm and meet functional needs is vital. For more tips, see this guide on aesthetic material selection2.
Performance and Functionality
Performance matters! A material’s mechanical traits affect a product’s success. Once I had to pick materials for high heat.
Material | Key Properties | Common Applications |
---|---|---|
Polyvinyl chloride (PVC) | Great thermal stability | High heat applications |
Polypropylene (PP) | Good heat resistance, high yield strength | Automotive parts, household goods |
Acrylonitrile-butadiene-styrene (ABS) | High impact resistance, good surface finish | Toys, electronic housing |
Nylon (PA) | High toughness, excellent wear resistance | Medical equipment, mechanical parts |
Knowing performance features is key in guiding material choices in product design3.
Environmental Impact and Sustainability
Designers today must think about the environment. I often choose sustainable materials that reduce ecological damage and attract eco-conscious consumers. The first time I used recycled plastics in a project, it felt great knowing my design could help the planet! Bioplastics are now my top choice – they blend performance and sustainability beautifully.
Considering a material’s entire lifecycle – from creation to disposal – can significantly influence design choices and align with eco-friendly goals. For more on sustainable materials, visit sustainability in product development4.
In summary, material choices are crucial in product design and performance. By understanding different materials’ properties and effects, we create innovative products that meet style, function and sustainability needs. Each decision tells a design story, one that speaks to users and elevates our work.
Polycarbonate is suitable for outdoor products due to UV resistance.False
Polycarbonate's high impact resistance makes it ideal for safety glasses, but it is not UV resistant, limiting its outdoor use.
Sustainable materials can enhance product appeal to consumers.True
Using sustainable materials not only reduces environmental impact but also attracts eco-conscious consumers, enhancing overall product appeal.
What Safety Considerations Should Be Taken When Using Certain Plastics?
Understanding plastics might feel confusing. This is especially true when considering health and safety. I often wondered if something was safe. Let’s learn the important points together. Let’s find the best ways to stay safe.
When using certain plastics, focus on your health. Avoid harmful chemicals like BPA and phthalates. Choose safe materials such as polyethylene (PE) and polypropylene (PP). Keep these plastics away from high temperatures and sunlight. Proper handling really minimizes exposure.
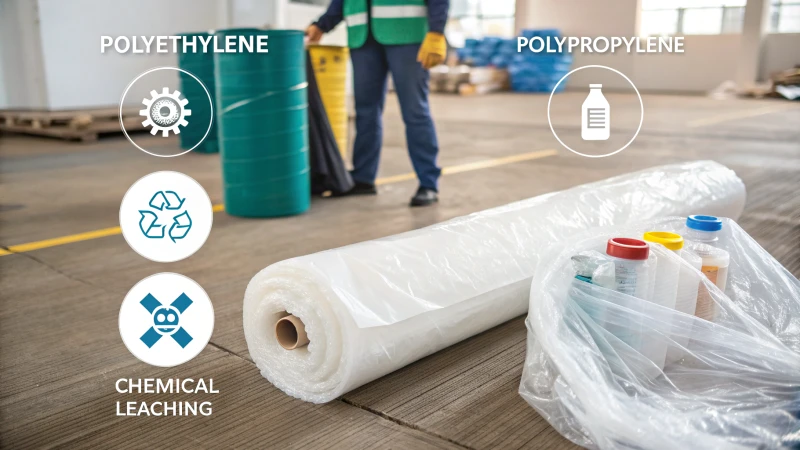
Understanding the Risks of Plastics
When I first began learning about plastics, I discovered surprising health risks. Some common plastics hide dangers. Hearing about chemical leaks shocked me. It was like a wake-up moment. Certain plastics such as Polyvinyl Chloride (PVC) release toxic gases when processed, raising significant safety concerns.
To mitigate these risks, always check the resin codes on plastic products for understanding. It’s like reading food labels; this tells me what I’m actually using.
Safe Practices for Food Storage
With food storage, I became very careful. Not all plastics safely touch food. The following table outlines common plastics used in food containers and their safety ratings:
Plastic Type | Resin Code | Safety Considerations |
---|---|---|
Polyethylene Terephthalate (PET) | 1 | Generally safe; low risk of leaching. |
Polypropylene (PP) | 5 | Safe for food storage; resistant to high temperatures. |
Polystyrene (PS) | 6 | Not recommended for hot foods; may leach chemicals. |
Polyvinyl Chloride (PVC) | 3 | Avoid for food contact due to potential toxins. |
I now trust certain plastics for keeping food safe and always use PE or PP containers for leftovers or meal preps. It is a simple change that gives peace of mind.
Best Practices for Handling Plastics
Handling plastics needs care. I follow these steps:
- Avoid high temperatures: Never expose plastics to high heat; it risks chemical leaks.
- Keep away from sunlight: Sunlight breaks down containers faster; store them in cool, dark spots.
- Use BPA-free products: BPA has links to health issues; choose products labeled BPA-free.
These steps reduce my contact with harmful substances from plastics.
Awareness of Chemical Additives
Knowing about chemical additives in plastics is crucial. Phthalates, often found in PVC products, worry about health impacts. I choose products that are free from harmful additives because small actions can have a big impact on overall well-being.
Check out safety tips5 for more advice on handling plastics in daily life.
Conclusion on Material Selection
Understanding which plastics we use helps keep us healthy. Choose safe plastics and follow good practices—it makes life healthier! It is not just about containers; it involves making thoughtful choices for yourself and loved ones.
Polyvinyl Chloride (PVC) is safe for food contact.False
PVC can release harmful toxins, making it unsafe for food storage. Avoid using PVC for food-related purposes.
Polyethylene (PE) is generally safe for food storage.True
PE has a low risk of leaching, making it a safe choice for storing food and beverages.
How Do I Choose the Right Material for My Injection Molding Project?
Selecting the correct material for injection molding seems like a big challenge. I have experienced this and I know it’s not only about selecting a material. It’s about understanding how it aligns with your vision. Let’s explore this together!
Choose the best material for your injection molding job by looking at the material’s strength and heat resistance. Think about what the project needs and how much money is available. Find a balance between cost and how well the material works. The end product should meet quality standards. It should also not cost too much. Quality is really important.
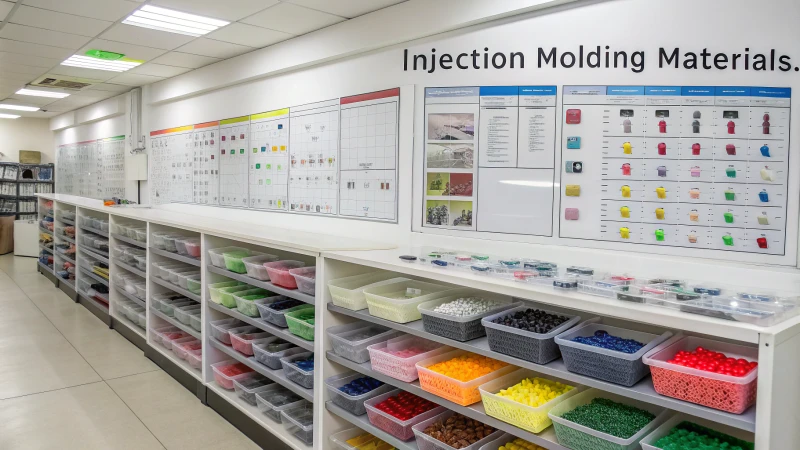
Understanding Material Properties
When I began in product design, choosing materials for my injection molding projects felt very daunting. Each material seemed unique, with its own strengths and shortcomings. Understanding these traits was crucial to making sure my designs were both attractive and functional. How do you choose wisely?
Selecting the right material for injection molding starts with understanding the properties of different materials. Each type has unique characteristics that determine its suitability for specific applications. For instance, you might consider factors such as:
- Strength: Does it withstand stress without breaking?
- Heat Resistance: Does it endure heat without losing quality?
- Chemical Resistance: Does it remain stable when exposed to chemicals?
Evaluating these properties helps narrow down choices to those that fit your project’s needs. For more details, see material property charts6.
Commonly Used Materials in Injection Molding
Here’s a quick list of materials I often consider for injection molding:
Material | Properties | Common Applications |
---|---|---|
Polyethylene (PE) | Low water absorption, excellent electrical insulation | Plastic bags, films, wire coatings |
Polypropylene (PP) | High yield strength, good heat resistance | Automotive parts, consumer goods |
Polystyrene (PS) | Good optical and electrical properties | Product packaging, household goods |
Polyvinyl Chloride (PVC) | High temperature resistance | Water pipes, door seals |
ABS | High mechanical strength, good impact resistance | Electronic housings, toys |
Polycarbonate (PC) | Excellent impact strength | Optical lenses, medical equipment |
Polyamide (PA) | High tensile strength, good toughness | Medical equipment, mechanical parts |
Polyoxymethylene (POM) | Excellent wear resistance | Precision parts, gears |
Thermoplastic Polyurethane (TPU) | Good flexibility and wear resistance | Sports equipment, automotive parts |
Styrene-butadiene-styrene (SBS) | Good elasticity | Soles, adhesives |
This table is just a starting point. I remember deciding between ABS and polycarbonate. It felt like choosing between two good friends! Each had positives and negatives. Understanding them helped me choose the right one.
Assessing Project Requirements
Once I know material properties, I evaluate my project’s specific needs. I ask myself:
- What will the product be used for?
This helps identify the best material. - What conditions will the product face?
Will it meet chemicals or extreme temperatures? - Are there regulatory or safety requirements?
Some materials have restrictions in certain industries.
These questions create a clearer picture of what I need. For more on this process, see project requirement guidelines7.
Cost vs. Performance
Lastly, I balance cost and performance. High-performance materials can be expensive! I evaluate:
- My budget limits.
- How material choices affect production costs.
- Long-term benefits of investing in durable, quality materials.
Considering these factors aids in finding a cost-effective solution without sacrificing quality. For detailed cost analysis, see cost-benefit analysis resources8.
With this approach, I usually make decisions that match both my creative vision and practical needs.
Polycarbonate (PC) offers excellent impact strength for products.True
PC is known for its durability and is commonly used in applications requiring high impact resistance, such as optical lenses and medical equipment.
PVC is the best choice for high-temperature applications.False
While PVC has good temperature resistance, materials like Polypropylene (PP) are often better suited for high-temperature applications, making this claim false.
Conclusion
Explore common materials used in injection molding, their properties, applications, and how to select the right one for your product design needs.
-
Clicking this link provides in-depth analysis on how material selection impacts design decisions and product outcomes. ↩
-
Explore this resource for strategies on selecting materials that enhance aesthetic appeal in designs. ↩
-
Discover how mechanical properties of materials influence product performance in this insightful article. ↩
-
Learn about sustainable material options for eco-friendly designs through this valuable link. ↩
-
Explore essential safety considerations when using various types of plastics to protect your health effectively. ↩
-
Discover comprehensive guidelines on selecting materials tailored to your specific injection molding needs. ↩
-
Explore detailed resources that explain the properties of various materials used in injection molding. ↩
-
Learn about cost analysis techniques that can help you balance budget constraints with performance needs. ↩